中信重工RP170120辊压机电气控制系统..pptx
辊压机-电气自动化
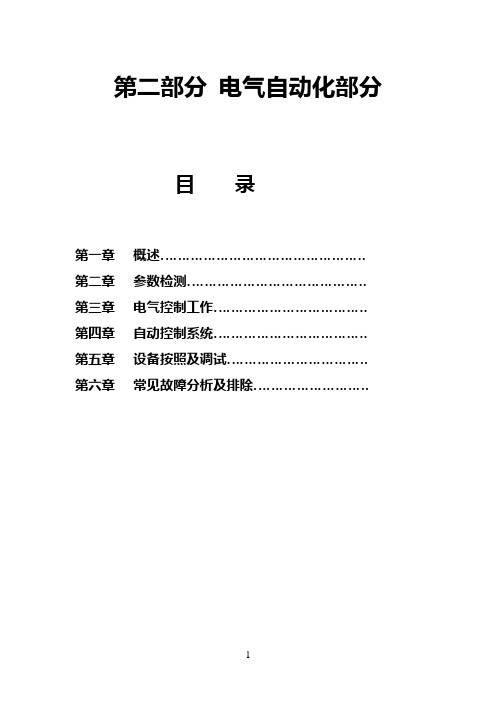
第二部分电气自动化部分目录第一章概述…………………………………………第二章参数检测……………………………………第三章电气控制工作………………………………第四章自动控制系统………………………………第五章设备按照及调试……………………………第六章常见故障分析及排除………………………第一章概述在这一章中,主要描述辊压机的基本特征、特性及其在工艺系统中的作用。
这对于控制是很必要的。
辊压机主体是两个相向转动的辊子。
脆性物料由输送设备,进入装有称重传感器的称量仓,而后通过辊压机的进料装置,进入两大小相同,相对转动的辊子之间,由辊子一面将物料拉入辊隙中,一面以其间的高压将物料压成密实的物料饼,最后从辊隙中落下,经出料斗,由输送设备提出。
再由下一工序对物料进一步的分散或粉磨。
该机应用高压料层粉碎能耗低的原理,采用单颗料粉碎群体化的工作方式。
脆性物料经过高压挤压(该机在压力区的压力约为150Mpa)使物料的细度迅速减小,小于0.08mm的细粉含量达到20~30%,小于2mm的物料达到70%以上,并且在所有经挤压的物料中存在有大量裂纹,使物料在下一个工序中粉磨时,所需的能耗大幅度降低。
更具国外有些资料的报导和我们已取得的实际使用经验,采用此设备的粉磨系统比未采用该设备的粉磨主要系统可增产50~200%,单产电耗可降低20~35%。
并且由于磨辊的磨损小,使得单位磨耗降低,同时设备工作的噪音、粉尘等均较小,改善了工人劳动环境,充分显示出卓越的经济效益和社会效益。
辊压机主要由以下部分组成:1)主轴轴系——是辊压机的核心部件,主要由磨辊主轴、主轴承、可水平移动的轴承及端面热电阻等组成。
其主要功能是向物料输出低速、重负荷的挤压粉碎力。
工作转速为23.75rpm,工作温度<100℃.2)主机架——作为整个辊压机的基础,承受辊压机工作工程中的挤压粉碎力。
3)液压系统——其主要作用是液压弹簧并兼备液压保护功能。
液压系统主要由泵站、阀台和主油缸三大部分组成。
辊压机电气控制系统维护操作指导
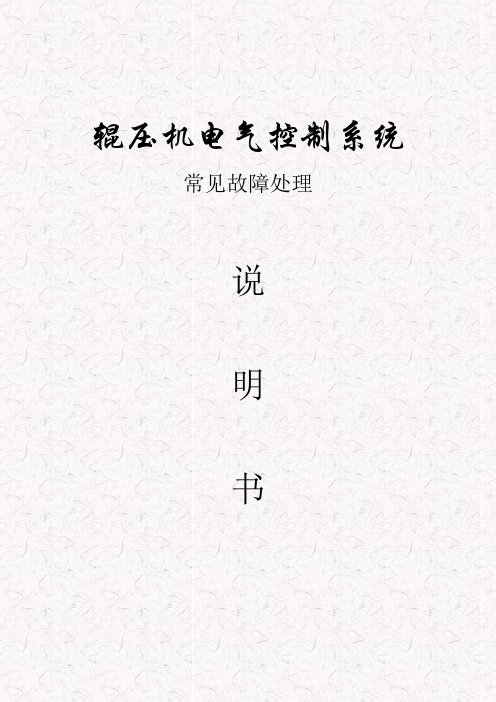
辊压机电气控制系统常见故障处理说明书辊压机电气控制系统主要由一次检测执行元件、PLC模块、上位人机界面计算机组成,控制与联锁关系较多,用户首先应在熟读辊压机《电气控制系统原理图》的基础上,并充分了解辊压机的工作过程,开始着手对辊压机电气部分的维修。
一、基本术语及电量定义1.DI/DO模块是指输入或输出开关量信号,其电压不超过DC+24V/AC15V各点的状态在模块上有相应的指示灯表示,如指示灯亮表示输入或输出状态为1。
2.模拟量模块是指输入信号为DC 4 ~20MA的模拟信号,其电压不超过DC+24V/AC15V,低于4MA或大于20MA的信号均造成不正确显示,甚至产生报警输出。
3.上位人机界面上位机通过以太网与PLC通讯,为用户了解辊压机的运行情况及设置参数提供了良好的人机界面。
PLC的运行与上位机的运行是相对独立的,即在加强设备巡检的条件下,可以暂时脱离上位机运行。
4.辊缝辊缝分左侧辊缝(驱动侧)和右侧辊缝(非驱动侧)。
辊缝是通过位移传感器来检测的,位移传感器的量程为0~60mm,对应输出4~20MA的电流信号。
初始位移值调整时活动辊轴承座应采用液压缸顶至中心机架,位移显示值应通过改变位移传感器安装座位置完成,不得通过调整电气零点偏移方式来改变显示值。
初始间隙大小根据出厂测定数据设定。
5.辊缝差辊缝差是指左右侧辊缝值相减的绝对值。
其值计算由软件完成,辊缝差直接反映了两侧辊缝的偏差程度,为纠偏动作提供了重要参数。
6.压力压力分左侧压力(驱动侧)和右侧压力(非驱动侧)。
压力是通过压力传感器来检测的,压力传感器的量程为0~35Mpa,对应输出4~20MA的电流信号。
压力传感器的零点及量程出厂时已调整好,请不要尝试对它的修改。
6.热电阻及温度变送器热电阻均采用标准的Pt100热电阻,其阻值变化反映了温度的变化(热阻值分度表见附件)。
温度变送器通过测量热电阻的阻值输出4~20MA的信号,其量程为0~150℃。
辊压机电气控制系统调试及操作说明_m.

一、电气控制系统安装1.到达现场后应该立即检查如下内容:对照图纸,核对是否有漏发元件;检查主控制柜、现场控制箱,显示屏等是否有损伤,是否有水侵入痕迹;检查主控制柜、现场控制箱安装位置是否符合图纸上的要求;检查主控制柜接地是否符合图纸上的要求;检查用户配置的气动阀门电磁先导阀电压等级是否为DC24V,如果用户采用电动推杆应立即和公司联系申请解决办法;检查用户配置的高压电机开关柜接口是否符合图纸上规定接口要求(包括电流模拟量、电机驱动和反馈信号开关量);核对主控制柜配置的一次回路元件规格是否和现场实物功率匹配;核对高压电机电压等级是否和用户电压等级一致;检查油站、减速机、电机等设备自带的显示表、热电阻是否有遗漏或损坏;2.安装接线:电气系统在安装接线完成并且检查无误前不得通电,通电前主机柜内PLC模块的接线端子必须拔下来;电气柜就位后即可安装接线,接线前必须和安装单位和业主充分沟通,提请注意图纸上的接线注意事项(如:屏蔽电缆不得用非屏蔽电缆代替;动力电缆和控制电缆不得混敷在一个桥架内,严禁控制电缆同高压电缆和变频器用动力电缆在一个桥架内混敷)现场电缆接线盒根据辊压机规格不同安装方式有所区别,CLF140x30和CLF140x65老式机架的接线盒按照图纸标注位置安装。
CLF140x65H和更大规格辊压机的TB5,TB6接线盒安装在机体附近的墙上或柱上,还可以布置在设备旁不影响交通和检修的地方,电缆穿管暗敷至相应的测点旁引上至测点;电缆管线在设备旁安装时必须和液压管道、润滑油管道、冷却水管道综合协调,保证整齐、美观和检修方便;督促施工单位电缆管线施工必须按照相关规范,严禁不穿钢管和蛇形保护管直接裸电缆引至测点,各测点的蛇形保护管长度不得超过500mm,机架上两个液压阀组(集成块)接线盒TB7、TB8引至电磁阀和压力变送器必须采用公司配置的专用两芯电缆,不得采用普通电线;施工单位在接辊压机电气柜(箱)内接线时必须在旁巡视、检查:⏹电缆标识、线号必须清晰;⏹每根线在端子联接紧固;不得有松动现象;⏹线、缆在柜(箱)内的长度适中,不得因为线缆太长而导致接线完毕后多余的线在柜内和线槽内影响美观和以后的维护;⏹屏蔽线的屏蔽层应在主控柜内联接到专用的屏蔽接地端上;⏹严禁施工单位在控制柜(箱)使用电焊焊接方法固定电缆紧固件;⏹发现接线端子损坏后必须及时更换,不得把该端子的进出线平移至另一个端子上;⏹协助施工单位查线,及时避免接线错误。
RP120-80辊压机更换辊子方案65页PPT
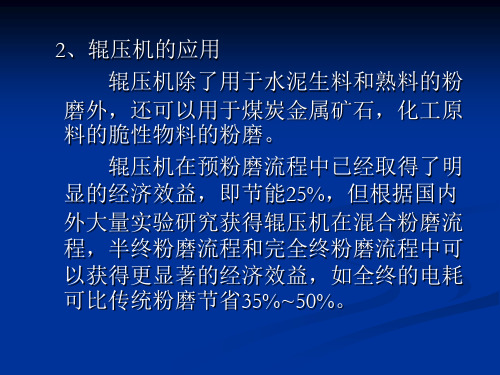
19、修复气动闸板阀,安装复位。 20、调整侧板与辊子端面间隙约:1~2㎜. 21、恢复各冷却水管、回转接头、润滑油管。 22、轴承加油,液压系统加压放气。 23、空转试车。 三、检修时间及工种人员:
1、检修时间:二月十四日到二月二十五日 2、检修人员及工种
卸轴承。
6、拆卸平油缸运至车间清洗。更换机架上磨损的不锈钢滑板。 7、拆卸轴承: ①.拆卸辊子冷却水管各部件。 ②.拆卸轴承压盖。 ③.用液压泵将轴承内径扩张,分离轴承。 8、租用25T车吊,将辊子、轴承吊下,轴承运回车间清洗。 9、清洗轴承:
①.拆卸滚柱、保持架、轴承内圈,清洗各部件。 ②.检查轴承外圈,根据磨损情况决定是否调节安装方向。 ③.清洗J型油封,更换损坏件。 ④.清洗完毕,各部件恢复。 ⑤.更换磨损的特氟龙耐磨板。 10、租用25T吊机,将新辊子、轴承吊至辊压机平面。 11安装辊子端面密封环,结合面打玻璃胶。 12、安装轴承: ①.油泵压力控制在230bar左右。 ②.轴承到位时,内圈压盖外表面至轴颈台阶处为60㎜. 13、各罩壳非标件视情况修复或更换。侧板堆焊处理,侧板顶丝 孔外侧加焊密封圈。
17、吊装上框架压板,恢复进料装置。 18、安装减速机:
①、缩紧盘与胀套清洗干净,用油石去除毛刺。 ②、安装减速机时确保减速机吊平,严禁用葫芦强拉。
③、缩紧套与胀套配合锥面可用二硫化钼喷剂润滑,缩 紧套内表面禁用润滑剂。
④、缩紧套螺栓时,须逐个拧紧,禁止对角拧紧,起 始扭矩300N.m,每二次增加100N.m,最高扭矩1240N.m。
上。 2、拆卸上框架压板,放置到北侧空地上。 注:①.放置上框架压板与进料装置时不要压坏地
面冷却水管。 ②.吊离压板时注意不要和大蓄能器碰撞,必要时
G170-120型辊压机毕业设计说明书

G170-120型辊压机扭力支架设计摘要本次论文进行的是G170-120型辊压机扭力支架的设计。
在这次毕业设计中,首先,论文对辊压机的工作原理及主要构造做了简要说明;其次,对G170-120型辊压机的主要技术参数进行了计算,其中包括辊径、辊宽、最小辊隙、工作压力、生产能力和传动功率等。
然后对G170-120型辊压机的总体方案进行设计,设计中针对系统不同的方案进行了利弊分析,选取了较为合适的方案。
总体方案设计涉及到了主机架结构设计、主机架的装配、进料装置、传动装置、液压与润滑装置、检测系统、扭力支架、电动机的选取等内容。
论文中重点介绍了扭力支架的设计选用。
最后,并对对扭力支撑中连杆上销轴的强度以及连接法兰上螺栓组的强度进行了校核。
此外,本次设计还包括G170-120的总装配图的绘制,扭力支架部装图及其零部件的零件图的绘制。
关键词:辊压机,扭力支架,设计,技术参数。
G170-120 TYPE ROIIER PRESS TORQUE SUPPORT DESIGNABSTRACTThis thesis is G170-120 type roller press torque support design. In this graduation design, Firstly, I Study on roller press the working principle and main structure are briefly described; Secondly. On the G170-120 type roller main technical parameters were calculated, Including the diameter of the roller, roller width, roll gap, minimum working pressure, production capacity and driving power. And then on the G170-120 type roller press the overall scheme design, design for the system of different schemes of the pros and cons, selects the suitable scheme. Overall scheme design involves main frame structure design, a main frame assembly, a feeding device, a transmission device, hydraulic and lubricating device, detection system, the selection of motor torque bracket, etc.. Paper focuses on the torque support design selection. Finally, checking and the torque support rod pin shaft strength and connection flange bolt group strength.In addition, the design also includes the 170-120 type roller press assembly drawing, torque bracket assembly drawing and parts component drawing.KEY WORDS: Roller press, torque support, design, technical parameters.目录前言 (1)第1章辊压机的工作原理及构造 (3)1.1 辊压机的工作原理 (3)1.2 辊压机的主要构造 (4)第2章辊压机主要参数确定 (6)2.1辊径D和辊宽B及最小辊隙S min的确定 (6)2.1.1辊径D (6)2.1.2辊宽B (6)2.1.3 最小辊隙S min (6)2.2辊速n (7)2.3工作压力F m (7)2.4 生产能力Q (7)2.5 传动功率N (8)2.6 辊压机的适宜工艺参数 (8)第3章G170-120辊压机总体方案设计 (9)3.1辊压机主机架结构设计 (9)3.2 挤压辊装配设计 (10)3.2.1挤压辊装配结构选型 (10)3.2.2挤压辊结构处理 (11)3.2.3 挤压辊支撑 (13)3.3 进料装置设计 (14)3.3.1喂料装置 (14)3.3.2侧挡板 (15)3. 4传动装置的选择 (16)3.4.1 传动装置减速器选用 (16)3.4.2传动装置的结构设计 (18)3.5 辊压机的液压与润滑系统设计 (18)3.6 辊压机检测系统 (20)3.7扭力支架设计 (21)3.8电动机的选型 (22)第4章强度校核 (24)4.1 销轴强度校核 (24)4.2 螺栓组强度校核 (26)结论 (30)谢辞 (31)参考文献 (32)外文资料翻译 (33)前言辊压机是八十年代中期问世的新型节能粉磨设备,是水泥粉磨环节中的中间设备之一。
辊压机联合粉磨系统介绍

110
水泥联合粉磨系统(双斗提机方案)
1. 水泥配料和V选的粗粉,用一台斗提机送入中 间仓; 2. 中间仓的物料进入辊压机挤压;挤压后的料 饼,单独用一台斗提机送入送入V型选粉机,进 行分选; 3. 细粉随风带入旋风筒收集入磨,粗粉循环挤 压; 4. 气流经循环风机返回V型选粉机进风口。 5. 进V选的溜子上设溜管除铁器和旁路三通阀; 6. 粉煤灰直接加入磨头或磨尾; 7. 球磨系统采用闭路系统,分选采用高效涡流 选粉机; 8. 磨内通风单独设除尘器和风机,方便调整磨 内通风量。
粉机,系统更简化、更节能; 2. 辊压机料饼中的一部分达到成品粒度的
细粉,经涡流选粉机直接分选为成品,一方面 增加了系统的能力,另一方面减少磨内过粉磨 现象。
3. 选粉风大部分循环,可以减少外排粉尘 总量。
因此,半终粉磨系统更能体现出节能和环保。
1. 系统能力不大时,可以采用单斗提方案,V型选粉机也 可以布置在中间仓顶部。 2. 磨机可以采用单仓磨。
❖ 2. 系统阻力小:
❖ 立磨系统在喷吹环处阻力很大,因此风机全压约10~11kPa;辊压机系
统仅为6~6.5kPa。
❖ 3. 系统节能,烘干能力弱:
❖ 立磨系统主风机装机功率3600~3800kW,辊压机系统循环风机功率
仅1600~1800kW。两者相差2000kW。
❖ 辊压机系统的风量仅为立磨系统的70%~75%,在相同的热源温度情 况下,辊压机系统的烘干能力较弱。在带余热发电情况下,最大烘干水分小 于5%。
❖ 2. 磨得细:
❖ 原料的易磨性、辊压机的选型、入辊压机综合水分等因素。
❖
辊压机的规格起决定作用。
❖ 3. 选得出:
❖ 烘干后细粉的水分、颗粒的分散性、选粉机的选型等因素。
RP120-80辊压机电控系统简介
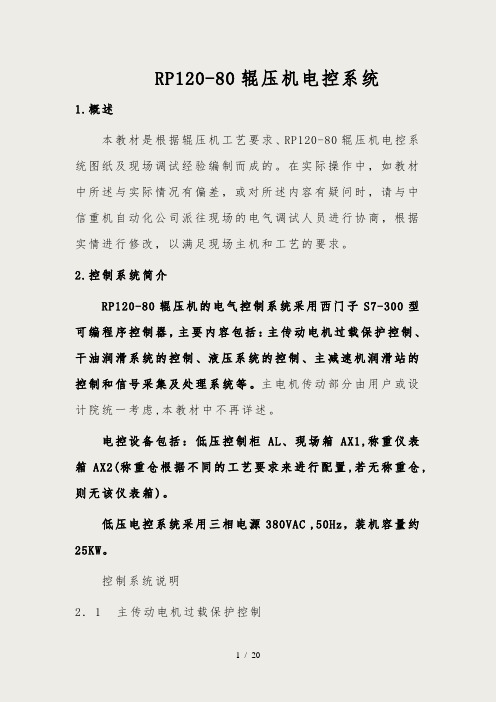
RP120-80辊压机电控系统1.概述本教材是根据辊压机工艺要求、RP120-80辊压机电控系统图纸及现场调试经验编制而成的。
在实际操作中,如教材中所述与实际情况有偏差,或对所述内容有疑问时,请与中信重机自动化公司派往现场的电气调试人员进行协商,根据实情进行修改,以满足现场主机和工艺的要求。
2.控制系统简介RP120-80辊压机的电气控制系统采用西门子S7-300型可编程序控制器,主要内容包括:主传动电机过载保护控制、干油润滑系统的控制、液压系统的控制、主减速机润滑站的控制和信号采集及处理系统等。
主电机传动部分由用户或设计院统一考虑,本教材中不再详述。
电控设备包括:低压控制柜AL、现场箱AX1,称重仪表箱AX2(称重仓根据不同的工艺要求来进行配置,若无称重仓,则无该仪表箱)。
低压电控系统采用三相电源380VAC ,50Hz,装机容量约25KW。
控制系统说明2.1 主传动电机过载保护控制辊压机共有两台主电机,分别作为其固定辊和活动辊的主传动设备。
由于液压系统压力的限制,要求主电机负载不能超过其额定负载的110%,为此,主电机启动时,电机定子电流经过变送器变为模拟量信号后,送入本控制系统PLC 模拟量输入模块中,实现过载控制。
2.2 主传动轴承干油润滑的控制干油润滑专为保证主轴承的长期、可靠运行,正常运行时其油泵工作方式为定时间歇式控制,即工作十分钟,间隔50分钟,如此周期性地重复工作。
油泵工作时,干油左右分配器应动作,如果连续4个周期不动作,则发出声光报警信号,系统停机。
注意:首次运行辊压机前,一定要打足干油。
设备停机期间,应根据设备的实际情况,可人工操作对轴承补充干油。
2.3液压系统的控制液压系统是实现辊压机功能的关键,其工作过程如下:辊压机启动前,应将两辊间料放空,使主电机轻载启动,减少对电网和设备的冲击。
启动主电机后,液压系统向左、右油缸供油的加压电磁阀通电,同时液压油泵电机启动,于是活动辊朝着固定辊方向移动。
海川170-120辊压机常见故障及处理措施

液压系统常见故障及处理措施一、系统加压异常原因分析:1、液压油不足,液位低;2、主油缸内泄;3、油泵损坏导致无法加压;4、加压电磁阀线圈不得电;5、减压阀损坏或卡死;6、安全溢流阀松动或溢流阀组卡死、损坏。
处理措施:1、检查油箱油位,若油位低及时补油;2、在手动加压时检查主油缸是否漏油;3、将控制柜切换到现场模式,现场手动加压,将油站出油口的球阀关死,看出口压力表显示压力是否正常,若没有压力或者压力较小则调整泵出口压力,直到调整到合适的压力,若调整后还后任没有压力,则判定油泵损坏;加压时查看出口压力表显示是否正常4、手动加压检查加压电磁阀线圈是否得电;在手动加压的情况下用内六角缓慢关闭减压调节阀,若此时压力上升,则证明是由于减压阀卡死或损坏造成无法加压的,更换或清洗减压阀即可;关闭减压调节阀,判断减压阀是否卡死或损坏5、用内六角缓慢调节安全溢流阀,若能加压,则说明安全溢流阀松动导致,重新调整溢流安全阀安全压力即可,若无法加压,可能是溢流阀内部卡死或加压阀问题所致,需拆卸溢流阀进行检查,看是否动作灵活;泄压阀阀芯泄压阀内部的氮气囊菌型阀弹簧垫6、在排除上述几种问题的情况下,则有可能是加压阀问题,首先拆卸加压阀,检查是否损坏或者卡死。
二、运行过程中系统不保压原因分析:1、主油缸内泄;2、减压阀卡死或损坏;3、加压阀卡死或损坏;4、液压油脏造成液压元件动作不灵敏。
处理措施:1、检查主油缸在运行时是否有泄漏的情况;2、将控制模式切换到现场手动,手动加压,在加压过程中将减压调节阀缓慢关闭,看压力是否能保的住,若能保压则证明是加压阀问题,清洗或更换即可;3、若上述操作还是不能保压,则在加压到设定值后缓慢关闭加压调节阀,若能保压,则说明是加压阀问题造成无法保压的,清洗或更换即可;4、检查液压油是否脏,若脏需及时过滤液压油或者更换液压油。
液压油污染严重三、运行过程中加减压阀频繁动作原因分析:1、液压系统元件出现磨损,系统无法保压;2、PLC电气控制故障,出现液压元件误动作;3、物料波动大,辊缝波动频繁,导致加减压阀频繁动作(频繁动作造成液压元件损坏),液压系统压力过大,溢流阀动作导致压力过低;损坏的加减压阀断裂的阀芯4、蓄能器充氮压力不合理造成波动较大;液压油清洁度较差,造成液压元件动作不灵敏,导致压力过低。