某压力容器制造企业下料工艺守则
2019年不锈钢压力容器制造工艺守则

奥氏体不锈钢焊制压力容器施工工艺守则1范围1.1本工艺守则规定了奥氏体不锈钢焊制压力容器在制造、检验、试验及供货方面应达到的要求。
1.2本工艺守则适用于奥氏体不锈钢焊制压力容器的制造、检验、包装和运输。
常压不锈钢容器的制造可参照本工艺守则执行。
1.3各种复合板奥氏体不锈钢焊制压力容器除应符合本工艺守则的要求外,还应符合相应的专门技术要求,如 CD 130A3《不锈复合钢板焊制压力容器技术条件》和 JB/T4709-2000《钢制压力容器焊接规程》附录A。
1.4容器的制造、检验等要求除应符合本工艺守则的要求外,还应符合国家技术监督局《压力容器安全技术监察规程》、 GB150《钢制压力容器》和图样的要求。
1.5本工艺守则不适用于衬里奥氏体不锈钢焊制压力容器的制造。
2引用标准GB150 《钢制压力容器》HG20581 《钢制化工容器材料选用规定》HG20584 《钢制化工容器制造技术要求》CD 130A3 《不锈复合钢板焊制压力容器技术条件》JB4708 《钢制压力容器焊接工艺评定》JB4709 《钢制压力容器焊接规程》3制造用原材料3.1奥氏体不锈钢焊制压力容器用原材料应符合下列各项要求:1)设计文件要求;2)GB 150;3)HG 20581;4)国家技术监督局《压力容器安全技术监察规程》;5)本工艺守则的相应要求。
3.2奥氏体不锈钢原材料必须具有质量合格证明书,其内容应包括标准和合同附加项目中规定的检验要求。
材料入厂后或投产前,应按3.1规定进行检查和验收,如有要求或有质疑时,可进行复验。
3.2.1用于制造一、二类压力容器主要受压元件的奥氏体不锈钢材料,其质量证明书中项目不全或实物标识不清时,需进行材料复验,判明其牌号符合相应的质量标准后方可使用。
3.2.2用于制造三类压力容器主要受压元件的奥氏体不锈钢材料,除按有关要求进行必要的化学成分、力学性能和弯曲性能复验外,对有抗晶间腐蚀要求的,应对材料的抗晶间腐蚀性能进行复验。
压力容器下料和坡口加工工艺守则

压力容器下料和坡口加工工艺守则1适用范围适用于制造压力容器受压元件的板材、管子的排料、划线、下料,包括《固定式压力容器安全技术监察规程》和GB 150《压力容器》适用范围内的压力容器;其他产品可参照实施;2引用标准JB/T 4746 钢制压力容器用封头JB 3092 火焰切割面质量技术要求GB 150 压力容器3准备3.1材料3.1.1材料必须经检验合格,办理了入库手续,标识齐全、完整、清晰、牢固;3.1.2材料的材质、规格、型号、执行标准等符合设计图样、有关标准和工艺文件的要求; 3.1.3材料表面无严重锈蚀,表面清洁;3.2设备、机具、量检具3.2.1半自动切割机、等离子切割机、砂轮切割机、剪板机、车床、刨床、空气压缩机、电焊机等设备应完好;3.2.2乙氧焰切割工具、砂轮磨光机、手锤、铲、样冲、粉线、样板、划规、割规、记号笔、划线笔、钢印等工具、机具满足划线、下料和标识移植要求;3.2.3钢直尺、直角尺、钢卷尺、焊缝检测尺、测厚仪、样板等量检具满足检测要求;3.3下料准备3.3.1下料人员已熟知设计文件对受压元件和焊接接头坡口型式的要求,熟知工艺文件的有关规定;3.3.2下料人员熟知所使用设备、机具的性能,并能按安全技术操作规程操作设备和使用机具;3.3.3下料场地等环境条件能满足下料要求;3.3.4材料已按规定搬运至下料地点或垫平,表面清理干净;4筒体下料和坡口加工4.1划线4.1.1下料人员核对和确认钢板的材质、规格和材料标识;钢板的材质、规格按工艺过程卡和图样规定;4.1.2与封头对接的筒体:测量与筒体对接的封头周长;根据封头周长、封头与筒体板厚差值和内齐或外齐或中径对齐的对接方式,确定筒体径向展开下料尺寸;长度方向下料尺寸按工艺工程卡;4.1.3其他筒体:筒体径向展开下料尺寸和长度方向下料尺寸按工艺工程卡;4.1.4对钢板表面及周边进行检查,根据存在的缺陷情况,对钢板进行测量、划线,清除缺陷、齐边,必要时进行再划线;4.1.5下料人员划线后,应进行自检,确认合格后,按规定进行标识移植,标出产品零部件编号;4.1.6检验员对划线质量、标识移植进行检验和确认;操作者和检验员填写工艺过程卡并签字;4.1.7划线排料时应保证每一节筒节长度不小于300mm;当筒节周长方向需拼接时,拼接长度也应不小于300mm;4.1.8在对第一筒节划线的同时,按工艺过程卡和焊接工艺卡的规定,划出两块产品产品焊接试板的下料尺寸线;产品焊接试板的宽度方向应是钢板的轧制方向;4.1.9划线时应从板材或管材无原始标识的一端开始,以保证剩余材料上有原始标识;4.2切割余量4.2.1采用乙氧焰切割或等离子切割:当板厚10~25mm时,每条割口宜留余量5mm;当板厚大于25~36mm时,每条割口宜留余量6mm;当板厚大于36mm时,每条割口宜留余量7mm;4.2.2切割余量的大小,应根据切割方法(手工、半自动)、割嘴大小和切割经验确定;4.3制造和划线公差4.3.1制造公差筒体的长度和直径或周长方向的制造公差应符合以下规定:a所有容器都应符合GB150-《压力容器》的规定;b管壳式换热器应符合GB151-1999《管壳式换热器》第6章的规定;c卧式容器应符合JB/T4731-2005《钢制卧式容器》第8章的规定;d塔式容器应符合JB/T4710-2005《钢制塔式容器》第9章的规定;e人孔筒节应符合HG/T21514-2005《钢制人孔和手孔的类型与技术条件》“4 技术条件”; f其他容器应符合HG20584-1998《钢制化工容器制造技术要求》“7 尺寸公差”的规定; 4.3.2划线公差4.3.2.1 筒节长度划线公差a每一筒节划线长度应根据钢板宽度、钢板质量等具体情况由划线者确定;b筒体总长度、板制接管等零件的划线公差取制造公差的50%,不足2mm时取2mm;固定管板换热器壳程壳体的总长度应根据换热管、管板、膨胀节等零件的实际长度确定;工艺人员应在工艺工程卡中注明或说明;4.3.2.2 每一筒节展开尺寸两对角线尺寸之差值△L = | L1—L2 | 按表1要求;4.3.2.3 每一筒节周长(展开尺寸)的划线公差和同一筒体各筒节间的周长(展开尺寸)划线差值按表2要求;4.4下料4.4.1当板厚小于或等于4mm时,应考虑剪板机下料;当采用剪板机下料时,划线尺寸应为实际用料尺寸,不考虑切割余量;4.4.2当板厚大于4mm时,碳素钢和低合金钢用乙氧焰切割下料,不锈钢用等离子切割机切割下料;4.4.3当采用乙氧焰切割或等离子切割时,割嘴中心的位置应据板厚、切割余量和切割经验确定;4.4.4当直线切割下料时,必须采用半自动切割机切割;当切割圆弧时,能采用半自动切割机切割时,必须用半自动切割机切割;确实不能用半自动切割机切割时,才允许用手工切割下料;手工切割圆弧时应用割规;4.4.5下料后,应用铲清除割口熔渣,用砂轮磨光机磨削割口至平整、光滑;4.4.6下料人员填写工艺过程卡并签字,检验员对下料质量进行检验;4.5下料质量4.5.1下料尺寸公差与划线公差相同;4.5.2乙氧焰和等离子切割表面质量技术要求切割面质量技术要求,应符合JB 3092《火焰切割面质量技术要求》中的乙级要求,摘录如下:a表面粗糙度G:指切割面波纹峰与谷之间的距离(取任意五点的平均值);波纹高度≤160μm;b平面度B:指沿切割方向垂直于切割面上的凹凸程度,按被切割钢板厚度δ计算,其平面度的公差为:当δ<20mm时B≤3%δ,当δ为20~150mm时,B≤1.5%δ(不足0.6mm时按0.6mm); c上边缘熔化程度S:指气割过程中烘塌状况,表现为是否产生塌角及形成间断或连续性的熔滴及熔化条状物;其等级和熔化程度为:上缘有明显圆角塌边宽度≤1.5mm,边缘有熔融金属;d挂渣Z:指切断面的下边缘附着铁的氧化物,其附着多少和剥离难易程度为:有条状挂渣,用铲可清除;e缺陷的极限间距Q:指沿切线方向的切割面上,由于振动或间断等原因,出现沟痕,使表面粗糙度突然下降,其沟痕深度为0.32~1.2mm,沟痕宽度不超过5mm者为缺陷,每个缺陷间的距离≥1m;f直线度P:指切割直线时,沿切割方向将起止两端连成的直线同实际切割面之间的间隙;直线度公差应≤2mm;g垂直度C:指实际切割面与被切割金属表面的垂线之间的最大偏差;按其被切割钢板厚度δ计算,垂直度应≤3%δ;4.6坡口加工4.6.1坡口加工方法4.6.1.1正常情况下,一律采用铣边机加工坡口;4.6.1.2如设备条件允许,可利用数控火焰、数控等离子直接加工出坡口;4.6.1.3单面坡口焊接接头的背面清根和焊缝返修时缺陷的清除,可采用砂轮磨光机或手工碳弧气刨的方法;当采用碳弧气刨清根时,执行《手工碳弧气刨工艺守则》;4.6.2坡口的角度、钝边高度等参数应符合焊接工艺文件的规定;坡口加工完毕后,应用砂轮磨光机清除熔渣、氧化层,不锈钢材料还应清除渗碳层;4.7检验员和操作人员检验下料和坡口加工质量,填写有关工艺文件并签字;5 凸形封头下料5.1凸形封头包括椭圆形封头、碟形封头、球冠形封头和半球形封头;5.2划线5.2.1下料人员核对和确认钢板的材质、规格和材料标识;钢板的材质、规格按工艺过程卡的规定;5.2.2标准椭圆形封头展开直径D按下式计算或按外协成形单位提供的展开尺寸;D=1.2Di+2h+S式中:D —封头展开直径,mm; Di—封头内直径,mm;h —封头直边高度,mm; S —封头名义厚度,mm;封头直边高度h由设计人员根据JB/T 4746—2002《钢制压力容器用封头》中6.3.9的规定,即当封头公称直径DN≤2000mm时,直边高度h宜为25mm;当封头公称直径DN>2000mm时,直边高度h宜为40mm;5.2.3其他形状的凸形封头的展开尺寸由工艺人员计算和确定;5.2.4当板宽满足下料要求时,封头尽可能不拼接,若确需拼接时,应符合JB/T4746的规定;5.2.5每条割口的切割余量按筒体的规定;5.2.6划线后按规定进行材料标识移植,对零部件进行编号;5.2.7检验员对划线质量进行检验确认,并填写《封头检验记录》;5.3下料5.3.1封头下料时,应采用半自动切割机切割,尽量避免采用手工切割;5.3.2用于拼接的切割面表面质量要求,执行4.5.2规定;其他切割面质量的技术要求,执行JB 3092中3级要求;5.3.3检验员检验下料质量,填写《封头检验记录》;5.4坡口加工用于拼接的切割面或非切割面的坡口加工,执行4.6的规定;6锥壳下料6.1锥壳下料前,下料人员同车间技术员一起,按图样对锥壳的下料尺寸进行计算;6.2尺寸计算完毕后,同工艺过程卡中的下料尺寸进行核对,若相符,则按工艺过程卡规定的参数放样,制作样板;带折边锥壳应留出成形后的切边余量;6.3样板制作6.3.1锥壳的拼接块数,由下料人员根据锥壳大小、钢板规格等条件确定;6.3.2当锥壳有折边部分需外协旋压或冲压时,下料人员应考虑运输及旋压等条件,确定外协旋压或冲压部分锥壳的高度尺寸;6.3.3样板实际尺寸中所含切割余量的数值,由下料人员根据切割经验、割嘴大小、钢板厚度等条件,参照4.2确定;6.3.4单件生产的锥壳下料样板,可用油毡或青稞纸制作,多件或批量生产的锥壳下料样板应用0.3~0.5mm镀锌铁皮制作;6.3.5样板制作完毕后,应由检验和工艺人员检查确认合格后方可使用;6.3.6批量生产的锥壳样板,应先进行1~2件锥壳制作试制,确认制作的锥壳符合规定后,方可批量下料;6.3.7不需要拼接的小锥壳划线、下料,可不制作样板,直接在钢板上放样划线;6.4划线6.4.1用样板划线时,应根据钢板规格合理排料,提高钢材利用率;6.4.2划线时至少应由两人操作,以确保样板位置的正确性;6.4.3划线时,应有检验人员跟踪检验,填写《封头检验记录》和工艺文件;6.5下料下料方法、公差要求、切割表面质量技术要求等,执行4.5的相关规定;6.6坡口加工坡口加工执行4.6的规定;7法兰、法兰盖、管板下料7.1划线7.1.1下料人员核对钢板的材质、规格和材料标识;7.1.2对钢板表面和周边进行检查,根据存在缺陷的情况,排料、划线;7.1.3排料划线时,按表5的规定或经验数据留出切割和加工余量(法兰盖和管板厚度方向的加工余量可适当减少);②外径尺寸小于400mm的法兰不应拼接;7.1.4划线后按《标识管理制度》的规定进行材料标识移植;7.1.5下料人员对划线质量自检合格后,填写工艺文件,交检验员检验 ;7.1.6检验员对划线质量进行检验,填写相关检验记录和工艺文件;7.1.7法兰需拼接时,划线前应制作样板,经检验合格的样板,方可使用;7.1.8法兰盖、管板一般不应拼接,确需拼接时,应按规定拼接和热处理;7.2下料和拼接坡口的加工7.2.1碳素钢和低合金钢下料用乙氧焰切割,不锈钢下料用等离子切割机切割;7.2.2下料后应清除割口熔渣,对割口进行适当磨削加工;7.2.3拼接接头坡口加工7.2.3.1坡口加工应采用机械加工的方法,即刨削或铣削法;对较厚的法兰,机械加工之前,允许先用乙氧焰或等离子切割机对坡口进行粗加工;7.2.3.2若采用乙氧焰或等离子切割机加工坡口,应先划线后加工坡口,然后用砂轮磨光机修磨至平整、光滑;7.2.3.3坡口形状、尺寸应符合焊接工艺文件的规定;8管子下料8.1划线8.1.1下料人员核对管子的规格、型号、材质、标准号和材料标识;8.1.2对管端和管子表面质量进行检查确认,必要时去除管端缺陷部分;8.1.3按图样和工艺文件规定尺寸,在管子上划线,划线时应根据不同的切割方法留出切割余量;若批量下料,可采用工装下料,不划线;8.1.4主要受压元件用管子,划线后应按《标识管理制度》的规定,进行标识移植;8.1.5当用乙氧焰或等离子切割机下料时,划线应沿管子圆周方向划全;8.1.6划线后,操作者应自检,填写工艺过程卡并签字;8.1.7检验人员对划线质量进行检查,在工艺过程卡上签字;8.2下料8.2.1管子下料应优先采用磁力管道切割机、砂轮切割机或车床下料的方法;当不能用以上方法下料时,才允许用乙氧焰或等离子切割机切割;下料后应修磨切口或割口;8.2.2管子下料质量应由检验员检查确认,填写《管制接管检验记录》;批量下料时,检验人员必须不定期进行抽查;8.3坡口加工8.3.1凡能够用车床加工坡口的管子,应用车床加工坡口;8.3.2不能用车床加工坡口时,壁厚小于或等于8mm的管子,可用砂轮磨光机加工坡口;壁厚大于8mm的管子,可用磁力管道切割机、乙氧焰或等离子切割机对坡口进行粗加工,用砂轮磨光机进行修磨;8.3.3管子对接满足双面焊条件时,焊接接头背面清根可采用手工碳弧气刨的方法;8.3.4坡口加工质量应有检验员检查确认;9检验和质量标准9.1必须在检验员对划线质量检验确认后,方可下料;9.2坡口表面质量9.2.1坡口表面应平整不得有裂纹、分层、夹杂等缺陷;9.2.2钢板经火焰切割的坡口表面,应用砂轮打磨平滑,并应对加工表面进行磁粉和渗透检测;9.2.3施焊前应清除坡口及母材两侧表面20mm范围内(以离坡口边缘的距离计)的氧化物、油污、熔渣、灰尘、铁粉及其他有害杂质;9.2.4用碳弧气刨加工的不锈钢焊件坡口时,应用专用砂轮磨掉其表面的渗碳层;9.2.5划线、下料、坡口加工质量,应符合各条款和有关标准的要求;10成品保护10.1下料和加工完坡口的零件,应及时拼接、卷制、焊接;10.2当不能及时焊接时,在焊接前,应对坡口进行修磨;10.3不锈钢材料在拼接或组对点固后,应在焊接接头两侧各100mm范围内涂白垩粉,待其干燥后对坡口重新修磨、施焊;10.4在零件卷制或加工过程中,应按规定进行标识移植;11要求和注意事项11.1下料人员必须严格按图样、工艺文件和标准划线、下料;11.2视具体情况,用粉线、记号笔、划线笔等工具划线,必要时打样冲眼(不允许打样冲眼的材料除外);11.3下料人员应按规定佩戴劳保用品,做好施工防护;11.4当吊装、搬运材料和下料完毕的零部件时,应注意安全,吊具应可靠;11.5乙炔、氧气瓶应有足够的安全距离,应有阻火装置;11.6有关人员及时进行标识移植,填写有关工艺文件和质量记录;。
压力容器原材料检验通用工艺守则样本

压力容器原材料检验通用工艺守则样本压力容器是一种经过特殊设计和制造的装置,用于储存和运输高压气体、液体或固体。
由于容器内部承受着高压力,因此其原材料的质量和性能至关重要。
以下是压力容器原材料检验的一般工艺守则样本。
1.原材料选择:选择适用的原材料,如碳钢、合金钢、不锈钢等,根据容器的使用环境和工作条件来确定原材料的类型和规格。
2.原材料验收:接收原材料时,应对其进行质量检验。
检查原材料的化学成分、机械性能、外观等指标是否符合技术要求。
可以使用化学成分分析仪、拉伸试验机等设备进行检测。
3.材料切割:根据设计要求和材料规格,将原材料进行切割。
切割时应确保切割面光滑平整,无裂纹、间隙等缺陷。
4.材料加工:对切割好的材料进行加工,如冷冲压、热冲压、焊接等工艺。
加工过程中应注意避免产生过大的热变形和残余应力。
5.焊接:焊接是压力容器制造中最重要的工艺之一、焊接工艺应符合相关的规范和标准。
在焊接前,应对焊接材料进行质量检验,并选用适当的焊接材料和焊接工艺。
6.焊缝检验:焊接完成后,应对焊缝进行检验。
常用的焊缝检验方法有X射线检测、超声波检测、磁粉检测等。
通过检验,判断焊缝的质量是否符合要求。
7.热处理:对焊接完成的容器进行热处理,以消除焊接产生的残余应力,并提高材料的强度和韧性。
8.表面处理:对容器的表面进行处理,以提高其耐腐蚀性和美观度。
常用的表面处理方法有喷砂、热浸镀锌、电镀等。
9.容器测试:对已制造完成的容器进行压力测试、泄漏测试等。
通过测试,验证容器的密封性和安全性。
10.质量检验:对制造好的容器进行质量检验,包括外观检查、储罐容量测试、材料性能测试等。
以上是压力容器原材料检验的一般工艺守则样本。
严格按照这些守则进行原材料的选择、切割、加工、焊接、热处理和测试,可以确保压力容器的质量和安全性。
压力容器下料工艺守则

压力容器下料工艺守则1 主题内容及适用范围本守则规定了压力容器制造的划线放样、下料和刨坡口的一般要求。
本守则与产品的设计图样、工艺文件同时使用,适用于本厂压力容器制造过程中的划线、下料、刨坡口工序。
2 下料的基本要求使用的材料应符合图样上给定的和相应国家标准的要求。
压力容器受压元件用材料应有本厂的材料标记。
划线放样后经检验员检验认可,按《标识及可追溯性工艺守则》的规定进行标记移植后方可进行切割工序。
3 划线下料3.1 划线前3.1.1 为了充分提高材料的利用率,操作者领料前先根据下料卡将使用相同规格、牌号材料的零件集中在一起,根据板的理论尺寸统筹安排,长短搭配后开具领料单领料。
3.1.2 领料后确认材料规格、牌号、标记移植号与工艺过程卡要求一致,且表面质量不得有分层、裂纹、结疤、折叠等缺陷。
3.1.3 当材料有较大变形影响划线精度时,应先进行矫正,划线前应将材料垫放平整、稳妥,既要利于划线下料和保证精度,又要保证安全和不影响他人工作。
3.2 划线:3.2.1 划线时,板材若没有切边,应留30~50㎜切边量,所用尺寸最大不能超过钢板所标尺寸,根据下料卡合理安排零件划线的先后顺序及零件在材料上的排布位置。
3.2.2 零件划线尺寸根据下料卡(壳体划线尺寸按照封头周长减去板厚×3.1416)决定,工艺过程卡规定带试板的壳体,在同一批材料上横向划上试板(尺寸按L×B=500×150),壳体划线时要求宽度的划线偏差ΔH≤1㎜,长度偏差ΔA≤3㎜,两对角线偏差ΔL=L1-L2≤3㎜,钢板上应注明产品编号、材料标记和零件编号并用白记号笔或白油漆框出,其具体操作按图1。
3.2.3 划线时线条要清晰均匀,测量数据准确,各种线条符号完整,图号、件号、数量和划线尺寸都应与下料卡或工艺过程卡统一,冲眼印相对偏差应不大于0.5㎜。
图13.2.4 零件需拼接时,拼接焊缝按照焊艺的要求焊接,并在拼接矫形后二次划线。
下料工艺守则
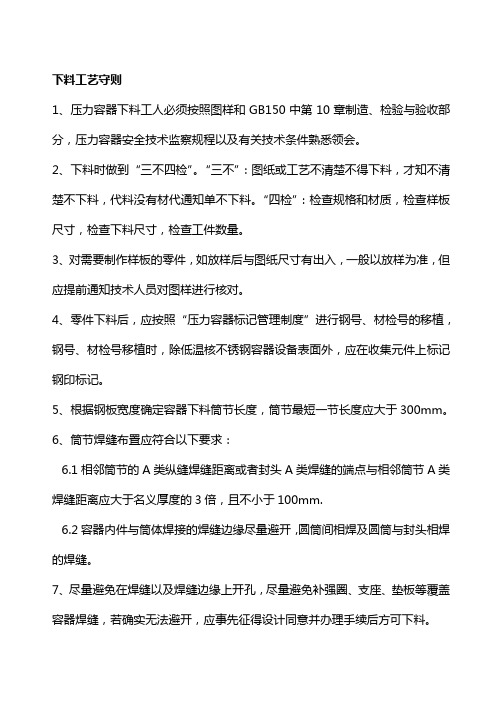
下料工艺守则1、压力容器下料工人必须按照图样和GB150中第10章制造、检验与验收部分,压力容器安全技术监察规程以及有关技术条件熟悉领会。
2、下料时做到“三不四检”。
“三不”:图纸或工艺不清楚不得下料,才知不清楚不下料,代料没有材代通知单不下料。
“四检”:检查规格和材质,检查样板尺寸,检查下料尺寸,检查工件数量。
3、对需要制作样板的零件,如放样后与图纸尺寸有出入,一般以放样为准,但应提前通知技术人员对图样进行核对。
4、零件下料后,应按照“压力容器标记管理制度”进行钢号、材检号的移植,钢号、材检号移植时,除低温核不锈钢容器设备表面外,应在收集元件上标记钢印标记。
5、根据钢板宽度确定容器下料筒节长度,筒节最短一节长度应大于300mm。
6、筒节焊缝布置应符合以下要求:6.1相邻筒节的A类纵缝焊缝距离或者封头A类焊缝的端点与相邻筒节A类焊缝距离应大于名义厚度的3倍,且不小于100mm.6.2容器内件与筒体焊接的焊缝边缘尽量避开,圆筒间相焊及圆筒与封头相焊的焊缝。
7、尽量避免在焊缝以及焊缝边缘上开孔,尽量避免补强圈、支座、垫板等覆盖容器焊缝,若确实无法避开,应事先征得设计同意并办理手续后方可下料。
8、钢板凡需进行超声波探伤者,探伤合格后再进行下料。
9、根据钢板实际宽度,确定好筒节长度,画出拼版图供装配、检查、加工,下料应考虑纵、环焊缝收缩量。
10、所下料的正面拥有其标歇工好(图号)、产品名称、下料尺寸、筒节数量、材质、坡扣型式等内容。
11、筒体剪板必须保证刨边(打磨)时有足够的余量,对不刨边(打磨)的板料,剪板时要特便注意找正。
12、刨边(打磨)坡口必须按检查线找正,刨边(打磨)的尺寸公差必须小于或等于划线的尺寸公差,对刨边(打磨)尺寸有特殊要求者,必须按照图样工艺要求,严格控制坡口型式及尺寸,并用坡口样板检查。
13、按图样和Q/LSJM.G.19-2005《压力容器焊接试板管理制度》下评定试板和产品试板。
压力容器工艺守则

压力容器工艺守则压力容器通用工艺守则汇编目录一、下料通用工艺守则 (1)二、筒体制造通用工艺守则 (7)三、封头、管板、换热器等制造通用工艺守则 (12)四、机械加工通用守则 (19)五、不锈钢产品制造通用工艺守则 (20)六、热处理通用工艺守则 (22)七、奥氏体不锈钢压力容器酸洗钝化工艺守则 (27)八、耐压试验和气密性试验通用工艺守则 (30)九、油漆通用工艺守则 (36)十、包装通用工艺守则 (40)十一、金属材料化学分析通用工艺守则 (42)十二、金属材料机械性能试验通用工艺守则 (45)十三、金相试验通用工艺守则 (47)十四、检验通用工艺守则 (49)十五、无损检测通用工艺手册 (68)一、下料通用工艺守则总则1.1压力容器下料通用工艺守则,以下简称《下料守则》,是压力容器制造中材料、总零部件下料等工序遵照的工艺技术文件。
1.2《下料守则》若与《容规》标准,图样各工艺文件的技术要求不相符时,应以《容规》、标准、图样要求及工艺文件为准。
1.3凡属受压元件的材料<板材、管材、棒材>应有标记。
当钢材需割开前、应按《材料标记移植制度》先进行移植。
1.4下料人员必须熟悉图纸:工艺文件、核对图纸要求的材料与投入使用的材料是否相符,需代用的材料手续是否齐全,严禁使用不合格的材料。
1.5下料人员应根据使用的板材,型材的规格和图纸尺寸,进行排料,并注意下列各项要求。
1.5.1避免支座和接管开孔碰上焊缝。
1.5.2钢管拼接的最短长度;碳素钢不小于300mm,不锈钢不小于400mm。
1.5.3下料时应取钢板的轧制方向与卷园平行。
1.6凡使用气割下料的钢材应垫平,要求切口光滑、平整、垂直,并将熔渣和飞溅必须清除干净。
表面不得有裂纹、分层、夹渣等缺陷。
1.7 奥氏体不锈钢下料划线时不得使用钢针和能引起表面刻痕的工具,应使用无氯无硫记号笔书写划线,标记移植时,不得打钢印,不得使用油漆、等有污染的物料书写。
不锈钢压力容器制造工艺守则

奥氏体不锈钢焊制压力容器施工工艺守则1范围1.1本工艺守则规定了奥氏体不锈钢焊制压力容器在制造、检验、试验及供货方面应达到的要求。
1.2本工艺守则适用于奥氏体不锈钢焊制压力容器的制造、检验、包装和运输。
常压不锈钢容器的制造可参照本工艺守则执行。
1.3各种复合板奥氏体不锈钢焊制压力容器除应符合本工艺守则的要求外,还应符合相应的专门技术要求,如CD130A3《不锈复合钢板焊制压力容器技术条件》和JB/T4709-2000《钢制压力容器焊接规程》附录A。
1.4容器的制造、检验等要求除应符合本工艺守则的要求外,还应符合国家技术监督局《压力容器安全技术监察规程》、GB150《钢制压力容器》和图样的要求。
1.5本工艺守则不适用于衬里奥氏体不锈钢焊制压力容器的制造。
2引用标准GB150《钢制压力容器》HG20581《钢制化工容器材料选用规定》HG20584《钢制化工容器制造技术要求》CD130A3《不锈复合钢板焊制压力容器技术条件》JB4708《钢制压力容器焊接工艺评定》JB4709《钢制压力容器焊接规程》3制造用原材料3.1奥氏体不锈钢焊制压力容器用原材料应符合下列各项要求:1)设计文件要求;2)GB150;3)HG20581;4)国家技术监督局《压力容器安全技术监察规程》;5)本工艺守则的相应要求。
3.2奥氏体不锈钢原材料必须具有质量合格证明书,其内容应包括标准和合同附加项目中规定的检验要求。
材料入厂后或投产前,应按3.1规定进行检查和验收,如有要求或有质疑时,可进行复验。
3.2.1用于制造一、二类压力容器主要受压元件的奥氏体不锈钢材料,其质量证明书中项目不全或实物标识不清时,需进行材料复验,判明其牌号符合相应的质量标准后方可使用。
3.2.2用于制造三类压力容器主要受压元件的奥氏体不锈钢材料,除按有关要求进行必要的化学成分、力学性能和弯曲性能复验外,对有抗晶间腐蚀要求的,应对材料的抗晶间腐蚀性能进行复验。
1下料通用工艺守则(内容)

安徽四汇机械集团有限公司下料通用工艺守则编制:陆玲玲审核:游安军批准:梁永强2014-05-13发布2014-05-28实施1.总则1.1本守则适用于压力容器主要受压元件的下料,其他零部件下料可参照执行。
1.2下料人员必须严格执行产品图样和工艺文件的规定,当图样无特殊要求时,工艺人员在编制下料工艺文件时应遵照本守则的相应规定。
2基本要求2.1下料人员凭领料单办理领料手续。
2.2下料人员必须熟悉产品图样和工艺文件的要求。
2.3切割设备必须完好,现场有足够的下料场地,四周无有碍下料工作的堆积物。
计量器具能满足测量工作的基本要求,且在检定周期内。
2.4主要元件材料必须是经检验合格入库,且经监检确认的材料。
2.5材料上有清晰的出厂标记及入库检验标记,表面质量符合要求、牌号、规格必须与产品设计图样或工艺文件一致。
2.6筒体由若干个筒节拼焊而成时,筒节最小长度不得小于300mm。
2.7压力容器主要元件下料划线结束后应进行材质标记移植,并由专职检验人员进行检验确认,打上确认标记后方可切割下料。
2.8切割方法:碳素钢,低合金钢板材可选用剪板机或气割的方法;管材、棒材可以选用砂轮切割机。
2.9筒体下料尺寸的确定筒节展开长度,可按下式进行估算L=π(Di+δn)+2c式中:L:筒节展开长度Di:筒节内直径δn :壁厚C:边缘加工余量实际下料展开长度,还应以实际周长为准。
3.0划线3.1划线尺寸的依据是产品图样和工艺文件。
3.2划出工件毛坯尺寸线和切割线。
毛坯尺寸线和切割线之间的距离应保证工件切割后毛坯尺寸线不被破坏。
常用下料方法,毛坯尺寸线和切割线之间的距离可按表一推荐的数据选用。
表一mm材料厚度火焰切割等离子切割碳弧气刨剪板机手工自动、半自动手工自动、半自动手工≤10 3 2 9 6 8 010~30 4 3 11 8 10 032~50 5 4 14 10 14 052~65 6 4 16 12 18 03.3工件毛坯尺寸取工件展开尺寸和周边加工余量之和。
- 1、下载文档前请自行甄别文档内容的完整性,平台不提供额外的编辑、内容补充、找答案等附加服务。
- 2、"仅部分预览"的文档,不可在线预览部分如存在完整性等问题,可反馈申请退款(可完整预览的文档不适用该条件!)。
- 3、如文档侵犯您的权益,请联系客服反馈,我们会尽快为您处理(人工客服工作时间:9:00-18:30)。
QB/HT-RQ-03-07 公司企业标准
下料通用工艺守则
编制
审核
批准
发放单位接收单位接收人:
2007年4月5日发布2007年4月15日实施
1 主题内容与适用范围
1.1 本守则规定了压力容器受压元件下料的通用技术要求。
本工艺守则规定了下料工序的操作要点、质量要求和控制的主要内容。
1.2 本守则适用于压力容器制造零部件的下料工序。
2 引用标准
《压力容器安全技术监察规程》
GB150-98《钢制压力容器》(第1、2号修改单)
GB151-99《管壳式换热器》(第1号修改单)
公司《质量手册》及相关程序文件、管理制度
3 材料
3.1 压力容器用材料的质量及规格应符合《压力容器安全技术监察规程》、GB150-1998《钢制压力容器》、GB151-1999《管壳式换热器》及相应国家标准、行业标准的规定。
3.2 制造压力容器受压元件的材料必须具有材料生产单位按照相应标准规定提供的质量证明书(原件)。
质量证明书的内容必须齐全、完整,并应有材料生产单位质量检验部门盖章确认。
如质量证明书为材料生产单位出具的复印件,应由材料销售单位在质量证明书的复印件中加盖销售单位质量检验章和经办人章。
3.3 购进的压力容器受压元件用材,应有明显清晰的标志,且和质量证明书一致,图样及相关标准要求复验及对质量证明书中的某项性能有怀疑时均需复验,没有完成的材料检验,未经材料责任师签署验收入库单的材料不得进入下料现场。
3.4 投入下料现场的材料未种植本单位材料代号标识及检查员见证标识,不允许进行划线下料。
3.5 主要受压元件用材必须进行标记的种植,且应经材料检查员确认。
在使用中始终保留有标识,当制造中需要使用时,应进行标记的移植,并有材料检
验员的确认标记。
主要受压元件包括:压力容器中筒体,封头(端盖),人孔盖、人孔法兰、人孔接管、膨涨节、开孔补强圈、设备法兰、换热器的管板
和换热管、M36mm以上的设备主螺栓及直径大于等于250mm的接管和管法
3.6标记位置
图1筒节钢板拼接标记位置
/
图4管板、法兰标记位置
4划线
4.1划线工人必须熟悉图样和制造卡的要求,划线前应核对材料的品种、规格
是否符合图样和工艺文件的要求。
4.2划线前对受压元件用料应进行表面质量复查。
4.2.1钢板表面仅允许存在深度不超过厚度负偏差之半的划痕、轧痕、麻点、氧化皮脱落后的粗糙等局部缺陷。
4.2.2封头或需要变形的工件下料,应考虑压形工艺减薄量,选用正偏差材料或增加厚度,保证封头或变形件的最小厚度符合设计图样及标准的规定。
4.2.3深度超过钢板负偏差之半时,以及任何裂纹、结疤、折叠、压入氧化皮、夹杂等缺陷时,应打磨消除,打磨面积应不大于钢板面积的30%,打磨的凹
坑应与母材圆滑过渡,否则不得用于受压元件。
4.2.4深度超过钢板负偏差界限的缺陷应和技术人员联系。
4.3筒体下料一般应按轧制方向,当需要横向下料时,应和技术人员联系。
4.4划线应依据图样、制造卡、排版图进行合理划线,充分利用边角余料,提高材料利用率。
4.5拼接焊缝,碳素钢不小于300mm。
不锈钢不小于200mm,最短筒节均不小300mm,且保证容器在组焊时,相邻筒节的A类焊缝的距离大于3倍的板厚,且不大于100mm, A、B类焊缝距开孔边缘的距离应大于3倍的板厚且不小于100m m,同时还应保证容器内件和壳体焊接的焊缝边角尽量避开圆筒间相焊及园筒与封头相焊的焊缝。
4.6卧式容器的B类焊缝应尽量位于支座之外,A类焊缝位于壳体下部的
145°范围之外,支座焊缝与筒体焊缝边缘的距大于筒体壁厚且不小于50mm。
4.7主要受压元件划线后应进行材料标记移植,还应打上主要受压元件编号(不锈钢及小直径管材可用油漆写)待检查员检查划线尺寸和标记移植无误后,打上见证钢印或记录后,方可下料。
一般受压元件可不进行标记移植,但一定要核对材料标记,准确无误,方可下料。
4.8筒体划线
481筒体划线应划出基准线,下料线,需刨边的要留出刨边余量并打上洋冲孔(不锈钢不打洋冲孔,数控切割下料时可不划出基准线,不打洋冲孔),如
图5所示。
4.8.2筒体的展开长度L允差如表1,
表1筒节展开长度L允差
筒体板厚mm3-45-68101214161820-2224-26展开长L允差±mm1 1.5 2.53 3.545 5.5 6.0 6.5
注:管壳式换热器体展开L取正偏差
4.8.3筒体下料长边线应相互平行,对角线误差< 1/1000
4.8.4筒体展开划线
(1)无封头连接的筒体展开下料按图纸名义尺寸展开下料
(2) 有封头时,要根据工艺和图样的要求,封头与筒体外壁对齐或与筒体内壁对齐,或封头与筒体壁厚中心对齐来计算筒体展开长。
4.9产品试板的划线应和筒体同牌号、同规格、同批号、同时下料,并按规定移植标记和编号,一般每台2块(制造卡有特殊要求时,按制造卡规定执定),下料尺寸如图6。
150-200
300 - 500 ______ v__
图6下料尺寸
4.10封头下料划线
4.10.1根据图纸要求,椭圆形封头下料尺寸由下式求得:
下料直径①=(封头内径+ H X1.2 + 2个直边高
下料直径①=(封头外径—5) X.2 + 2个直边高或根据封头压制厂给定尺寸下料。
4.10.2 90°折边封头下料按图纸及工艺给定尺寸下料
4.11其余零件的划线
4.11.1除上述零件外,其余零件下料应按制造卡规定。
4.11.2机加工零件应留出加工余量见表2。
4.11.3对非主要受压元件,采用切割机直接下料时,需保证下料尺寸。
5下料
下料前的准备,气割、裁板机、等离子切割、锯床等设备运转正常,氧气、乙炔等附属材料齐全。
5.1下料工人必须熟悉图样和制造卡,做到五不、四检。
(1) 图纸不清不下料
(2) 制造卡不清下料
(3) 材料代用无代用单不下料
(4) 材料标记不清或不合格不下料
(5) 标记移植无见证钢印不下料。
表2机加工零件加工留量
5.1.2四检
(1) 检查图样和制造卡下料尺寸
(2) 检查材料牌号、规格和标记
(3 )检查样板尺寸几何形状
(4)检查工件数量
5.2剪切下料适用于板材下料。
5.2.1根据被剪切板厚度,调节上下刃间隙,试剪合格后方可进行工件下料,剪切应避免卷边现象。
剪切时,由于对金属的挤压、弯曲和剪切塑性变形,导致切口处产生冷作硬化区,同时,被切开金属发生整体的扭曲塑性变形。
硬化区宽度一般为1.5-2.5m m。
对剪切的质量一般要求切口应与板材表面垂直,斜度不大于1: 10,毛刺高不大于0.5mm。
在采用挡铁切割时,切割尺寸误差为翌.0 —3.0mm,剪切与板材尺寸和厚度有关,执行表3的规定。
5.2.2对于剪板后,不加工焊接坡口的板料,其刨边余量应符合表2的规定。
523剪切后的工件,应进行调平
表3剪切允许误差表
5.3热切割下料
5.3 .1气割下料
将划线检验合格后的坯料置于切割架上,按不同形状和材质选择合适的切割方法及工具。
圆形或环状工件切割应使用割规,符合半自动切割的尽量使用半自动切割机。
切割边缘要求齐整,防止变形。
(1) 被切面应垫平,割嘴应根据板厚选择(包括:仿形切割机),首先选用切割机下料,切口应光滑、平整、垂直。
(2) 切口垂直度为板厚的1/25。
5.3.2等离子切割
(1) 凡剪板机不能剪切的不锈钢材料,均可采用等离子切割下料,切割内圆孔时,应在切割前号钻①8mm的切割工艺孔。
(2) 切割时按线找正,切口应光滑、平整、垂直。
(3) 切割后需进行机加工的零件按表2留加工余量。
其余同气割。
533切割后必须清除飞刺、熔滴、熔瘤等,对标准抗拉强度下限值S b>540Mpa 经火焰切割的坡口应进行磁粉探伤或渗透探伤。
5.3.4检查:
(1) 切割后检查切割表面不得有裂纹、分层、夹渣、夹杂等缺陷。
(2) 切割落料完成后必须检查下料尺寸,批量较大的如换热管下料进行抽查。
5.3.5热切割落料完成后必须检查实际下料尺寸符合下列各表4
5.4锯床下料
5.4.1锯床下料:一般用于圆钢、角钢、钢管等型材的切割落料。
5.4.2单件或小批量的加工用毛坯件(如少量弯头、接管等)应按工艺或图样
给定尺寸测量下料。
543批量较大的螺栓、定距管、换热管等下料,应在锯床一侧设置定距限位装置,并应经过首件验收合格后,方可成批下料,为防止定距移位,造成废品,还应做中间抽查。
表5普通等压式割炬机动气割低碳钢工艺参数
表6气割钢热影响区宽度
表7气割的允许偏差
下料完成后应做好下料尺寸检查,锯床下料尺寸偏差在设计图样或工艺
没有给定情况下按表8和表9规定
表8下料长度允差mm
表9换热管下料长度及管端倾斜允差
5.4.5换热管和圆形棒材的下料采用锯切下料,同一根换热管的拼接焊缝,直管不超过一条,U形管不超过两条,最短管长不小于300mm,不允许在弯曲段拼接。
5.4.6锯切时应注意切口的垂直,偏斜不得大于截面最大尺寸的1/80 (弓字锯
为1/30)。
5.4.7切口毛刺应清理干净。
6自检合格后,按照规定在制造卡中签署名字和日期,并交专职检验员进行检验和记录。
10。