钻削与镗削加工钻削运动与加工范围
机械制造技术基础总结

机械制造技术基础总结机械制造技术基础第一章重点车削加工:工件旋转作主运动,车刀作进给运动的切削加工方法称为车削加工。
铣削加工:铣刀旋转作主运动,工件作进给运动的切削加工方法称为铣削加工。
刨削加工:刀具的往复直线运动为主切削运动,工作台带动工件作间歇的进给运动的切削加工方法称为刨削加工。
钻削加工:钻削是用钻头、铰刀或锪刀等工具在材料上加工孔的工艺过程。
刀具(钻头)是旋转运动为主切削运动,刀具(钻头)的轴向运动是进给运动。
镗削加工:镗削是用镗刀对已经钻出、铸出的孔作进一步加工,通常镗刀旋转做主运动,工件或镗刀直行作进给运动。
磨削加工:用砂轮或涂覆模具以较高的线速度对工件表面进行加工的方法成为磨削加工,主运动是砂轮的旋转。
成形法:成形法是用与被切削齿轮的齿槽线截面形状相符的成型刀具切出齿形的方法,所使用的机床一般为普通机床,刀具为普通铣刀,需要两个简单的成形运动:道具的旋转运动(主切削运动)和直线移动(进给运动)。
展成法:展成法是利用齿轮刀具与被切齿轮保持啮合运动的关系而切出齿形的方法,常用机床有滚齿机、插齿机等,常用加工法有滚齿法、插齿法、磨齿法、剃齿法等。
内传动链:有准确传动比的连接一个执行机构和另一个执行机构之间的传动链。
展成传动链和差动传动链为内联系传动链。
课本P26外传动链:是动力源与执行机构之间或两个执行机构之间没有准确传动比要求的传动链。
速度传动链和轴向进给传动链为外联系传送链。
课本P26表面成型运动:表面成形运动是指在切削加工中刀具与工件的相对运动,可分解为主运动和进给运动。
(来自百度)滚齿原理?滚齿属于展成法加工,用齿轮滚刀在滚齿机上加工齿轮的轮齿,它是按一对螺旋齿轮相啮合的原理进行加工的。
滚齿时的运动主要有:(1)主运动。
主运动是指滚刀的高速旋转。
(2)分齿运动(展成运动)。
分齿运动是指滚刀与被切齿轮之间强制的按速度比保持一对螺旋齿轮啮合关系的运动。
(3)垂直进给运动。
为了在齿轮的全齿宽上切出齿形,齿轮滚刀需要沿工件的轴向作进给运动。
钻削与镗削
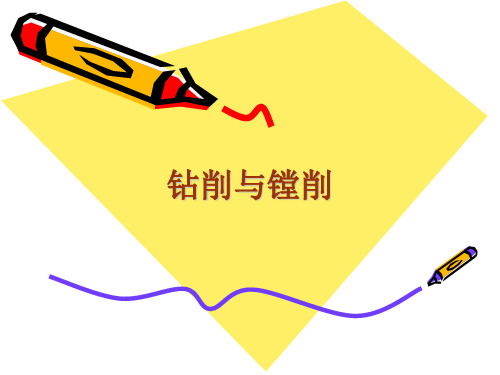
• 三.麻花钻
• 1.麻花钻的组成
• (1)柄部:是钻头夹持,定心,传递 扭矩的部分,有直柄和锥柄两种。
• (2)颈部: • 柄部与工作部的连接部分 • ,上面标准着钻头直径, • 材料牌号,商标。 •
(3)工作部分: 由切削部分和导向部分 组成。导向部分在钻孔 时起引导钻头的作用。
• 2.麻花钻的几何角度
组合机床等进行孔加工。
• 3.车床上钻孔的步骤
• (1)车平端面。便于钻头定心,防止 钻偏。
• (2)预钻中心孔。在工件中心钻出中 心孔或用车刀车出小的定心凹坑。
• (3)装夹钻头。选择与所钻孔直径对 应的钻头,钻头工作部分略长于孔深。 直柄钻头用钻夹头装夹后插入尾座套筒。 锥柄钻头用过度锥套或直接插入尾座套 筒。
钻削与镗削
•
• 教学目的:
•
1.了解钻削和镗削的应用,使用设
备等基础知识
•
2.掌握钻削和镗削的方法。
• 重点,难点:
•
钻削的操作方法。
• 一.概述
• 钻削:用钻头在实体材料上钻削出盲孔 或通孔,并能对已有的孔进行扩孔的加 工方法。
• 钻孔的公差等级:小于等于IT10,表面 粗糙度为 Ra12.5μm。
• (1)基面和切削平面。
• A.基面:指切削刃上任一点的基面Pra 是通过该点,且垂直于该点切削速度方 向的平面。
• B.切削平面:指切削刃任一点的切削平 面Psa是包含该点切削速度方向,而又切 于该点加工表面的平面。
• (2)主切削刃的几何角度。
• A.前角γo。是在正交平面内前刀面与基面的 夹角。主切削刃上的大小不一样,外圆处的角 最大时为正30°。靠近横刃处的前角最小为30°。
• 2.进给量af:钻头每转一转沿自身方向 移动的距离。Mm/r.
孔加工技术

四、铣镗加工中心
铣镗加工中心是一种计算机控制的、具有刀库的、 能自动 换刀的铣镗床。
主要部件: 刀库 主轴箱 机械手 工作台 数控装置
第六 节 镗刀和镗床加工工艺特点
一、镗刀 镗床常用的镗刀有单刃镗刀和双刃镗刀两 种。
1、单刃镗刀安装在镗刀杆上,加工的孔径大小由调整刀头 的伸出长度来保证,多用于单件小批量生产中。
➢横刃斜角Ψ 主切削刃与横刃在钻头端面上投影的夹角。 ➢螺旋角β 最外缘螺旋线切线与轴线的夹角
3.钻头受力分析:
在各切削刃上:
轴向力Ff 径向力Fp 切向力Fc 总的扭矩:
M=M0+M01+M横 轴向力:
F=F0+F01+F横 轴向力主要由横刃产生,
扭矩主要由主刃产生。
4.麻花钻的缺点shortcoming of twist drills
由于内排屑深
孔钻可以避免
切屑划伤孔壁
故加工质量较
高,精度达
IT9-7,Ra值
达3.2μm。
扁钻轴向尺寸小、刚性好,结构简单、制造容易,便 于采用先进刀具材料,换刀方便,适用于数控机床,尤 其在加工大直径孔(D>38mm)时,更是比麻花钻经济。
套料钻:中孔结构,切削刃分布在四周,加工孔时它只 切出一个环形的孔,而中间留下的料芯可二次使用。 适于加工直径大于60mm的深孔及贵重材料。
(3)铰孔的应用:铰孔用于软材料零件孔的精加工,不 能加工硬材料; 铰孔孔径φ1~φ80
铰孔的精度和表面粗糙度主要取决于铰刀的精度、安装方式、切
削用量、切削液等条件。为避免产生积屑瘤,铰孔时应采用较低
的切削速度、较大的进给量并施加适当的切削液。
铰刀分为机用铰刀和手用铰刀。手用铰刀的铰削直径为: ø1~ø50mm机用铰刀为: ø10~ø80mm
机加工工艺种类及介绍

机加工工艺种类及介绍
机加工是一种通过机械设备进行加工的方法,广泛应用于各个制造行业。
下面是一些常见的机加工工艺种类及其介绍:
1.铣削:利用铣床等设备,将刀具旋转并沿着工件表面进行切削,从而形成所需形状。
铣削适用于平面、曲面、开槽、螺纹等不同形状的工件加工。
2.车削:利用车床等设备,将工件固定在旋转的主轴上,通过
刀具的移动将工件表面切削成所需形状。
车削适用于加工圆柱体、圆锥体、球体等旋转对称形状的工件。
3.钻削:利用钻床等设备,通过刀具旋转并沿着工件轴向钻削
孔洞。
钻削适用于加工圆孔、盲孔、连续孔等不同尺寸和深度的孔。
4.磨削:利用磨床等设备,将砂轮或磨具与工件相对快速旋转,并进行相对运动,从而将工件表面切削至所需尺寸和精度。
磨削适用于高精度的表面加工、修正尺寸偏差等工艺。
5.镗削:利用镗床等设备,通过多刀具的轴向运动,将工件内
孔表面进行精细切削,从而得到所需的尺寸和表面精度。
6.车铣复合加工:利用车铣复合加工中心等设备,同时进行车
削和铣削操作,以提高生产效率和工件加工精度。
7.电火花加工:利用电火花机床等设备,在工件表面产生高频
电火花放电,通过电火花腐蚀的方式,将工件材料切割成所需形状。
以上是一些常见的机加工工艺种类,每种工艺都有其特点和适用范围。
企业根据具体加工要求和工件特性选择合适的机加工工艺进行加工。
机械制造技术基础-加工方法

钻孔、扩孔、铰孔
立式钻床
通过移动工件位置 使被加工孔中心与主 轴中心对中,操作不 便,生产率不高。适 于单件小批生产中加 工中小型零件。
摇臂钻床
摇臂可绕立柱回转和升降,主轴箱可在摇臂上作水平移动。 工件固定不动,可方便地移动主轴,使主轴中心对准被加工 孔中心。适于单件小批生产中加工大而重的零件。
2. 车刀的结构形式
整体式(HSS)、焊接式、机械夹固式(重磨式、可转位式)
可转位式车刀的组成:
可转位刀片、刀垫、刀杆、夹紧机构 切削性能好,辅助时间短,生产率高
刀片夹紧方式: 1)上压式 夹紧力大,
定位可靠,阻碍流屑
2)偏心式 结构简单,
不碍流屑,夹紧力不大
3)综合式 夹紧力大,
耐冲击,结构复杂
1. CA6140型卧式车床的组成 (1)主轴箱 (2)进给箱 (3)溜板箱
(4)刀架 (5)尾架 (6)床身
2. CA6140型卧式车床的传动系统分析
为便于了解和分析机床的运动和传动情况, 常用机床的传动系统图。传动系统可分解为主 运动传动链和进给运动传动链。进给运动传动 链又可分为纵向机动和横向机动进给传动链、 螺纹进给传动链,还有刀架快速移动传动链。
车削加工
2.2.2 车床
车床占机床总数的20%~30% 车床种类:卧式、立式、转塔、仿形、自动和半自动、
专门化车床(曲轴、凸轮轴车床、铲齿车床)
CA6140 通用性好,加工范围广,能加工中小型轴类、盘
套类零件内外回转面、端面,加工米制、英制、模数制、径节制四种 标准螺纹及加大螺距、非标准螺距螺纹等。但结构复杂,自动化程度 低,适于单件小批生产及修配车间。
2.4.4 铣削方式
1)端铣和周铣 2)顺铣和逆铣 周铣有顺铣和逆铣两种方式。 顺铣切削厚度大,接触长度 短,铣刀寿命长,加工表面光 洁,但不宜加工带硬皮工件,且进给丝杠与螺母间应消除间 隙。否则,应采用逆铣。
第2章 金属切削机床及各种加工方法

作用力
表面质量 使用情况
周铣
机械工程学院 机械制造基础
34
(2)端铣法 :用端面齿进行铣削加工
端铣法刀杆刚性好,可大用量切削,效率较周铣高;
端铣时有多个切削刃同时切削,切削平稳性好,周铣 只有一个到两个齿切削,切削平稳性较差,加工质量比 端铣低一个等级; 端铣刀齿有修光过渡刃和副刀刃,加工质量较好;
机械工程学院 机械制造基础
36
28 108 120 127
18
36 36 24 24 24 进给量计算 : 1 f 12 36 28 108 120 127
丝杠螺母进给:(S为丝杠导程) 齿轮齿条进给: (m为末级齿轮模数) 机床挂轮的要求: 1) 备用齿轮中应有选用齿轮齿数;
f 1 i主.丝 s
f 1 i主.末 mz末
2) 要防止挂轮互相干涉,要求满足下列条件: za+zb>zc+k zc+zd>zb+k 其中k=15~22 车、铣螺纹时要求进给量应与加工螺纹的螺距或导程相等,齿轮加 工时,滚刀转过1/k转,齿轮转过一个齿或插齿刀转过一个齿,齿轮 也转过一个齿。从而可计算出挂轮的传动比,根据传动比来选配挂 轮齿数。
机械工程学院 机械制造基础 28
2.3 铣削、刨削和拉削
2.3.1 铣削加工范围 平面、直槽、T形槽、燕尾槽、 三维内外形状等
机械工程学院 机械制造基础
29
铣削沟槽
机械工程学院 机械制造基础
30
2.3 铣削、刨削和拉削
2.3.2 铣床:卧式升降台铣床、立式升降台铣床、龙门 铣床、数控铣床等。 2.3.3 铣削加工刀具 立铣刀、盘铣刀、三面刃铣刀、 键槽铣刀、锯片铣刀等。
钻削
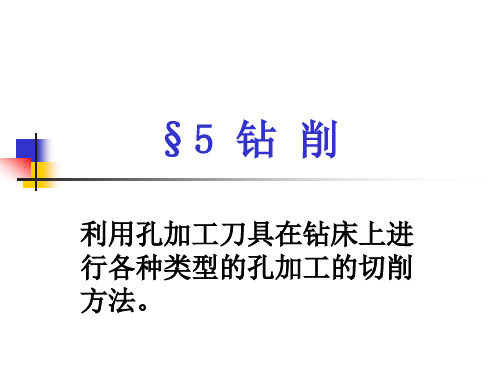
刀具
从实体材料中加工出孔的刀具,如麻花 钻、扁钻、中心钻和深孔钻等; 对工件上的已有的孔进行再加工,如扩 孔钻、锪钻(即埋头钻,一种用以锪锥形 埋头孔的钻)、铰刀及镗刀等。
三、钻削方法
钻孔:利用钻头在实体材料上加工出孔的加 工方法。
扩孔:利用扩孔钻头对已有孔径进行扩大的 切削加工方法。
铰孔:利用铰刀对已有孔的孔壁进行微量切 削加工的方法。
§5 钻 削
利用孔加工刀具在钻床上进 行各种类型的孔加工的切削 方法。
钻削运动
可进行粗加工、半精加工和精加工。
主运动:刀具的旋转运动; 进给运动:刀具或工件的平动。
一、钻削特点与加工范围
特点:钻削加工属于定尺寸切削加工, 孔径尺寸受到刀具直径的限制。
加工范围:主要用于钻孔、扩孔和铰 孔,也可以用来攻螺纹、锪沉头孔及 锪凸台端面。(图6-19)
2)可机械铰孔可手工铰孔; 3)只对孔壁进行精加工,不能校正孔的空间
位置。
钻孔
扩孔
铰孔
钻
削
加
工
攻螺纹
锪端面
锪沉头孔
图6-19 钻削加工
二、钻 床与刀具
钻床分为摇臂钻床、台式钻床、立 式钻床、深孔钻床、中心孔钻床等。
钻床通常用于加工尺寸较小,精度 要求不高的孔。
立式钻床
主轴变速箱
电动机
特点:主轴轴线位置固 进给变速箱
立柱
定,需调整工件位置, 主轴 使被加工孔中心线对准
钻头切削部分组成-“两主两副一横”
存在的问题
由于钻孔使钻头的工作部分大都处于易加工 表面的包围中,从而带来一系列的问题,使 得钻孔比车削外圆复杂得多。
因此,加工过程中要充分考虑并妥善解决钻 头刚度、强度、热硬性及排屑、导向、冷却 润滑等问题。
车削、钻削、铣削、镗削、磨削、的特点及应用范围
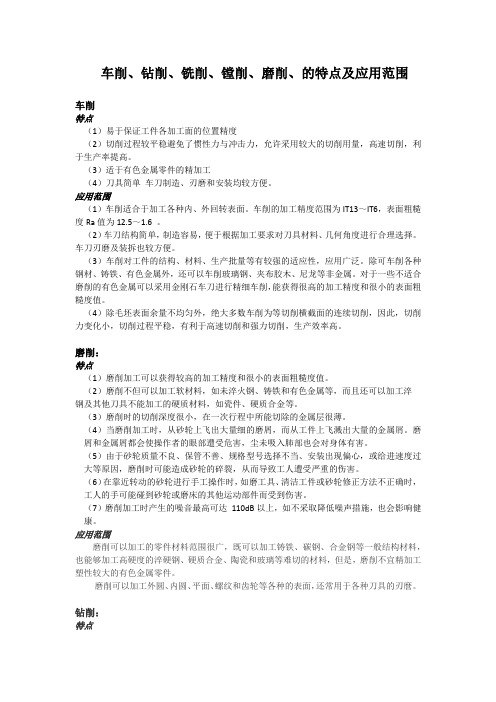
车削、钻削、铣削、镗削、磨削、的特点及应用范围车削特点(1)易于保证工件各加工面的位置精度(2)切削过程较平稳避免了惯性力与冲击力,允许采用较大的切削用量,高速切削,利于生产率提高。
(3)适于有色金属零件的精加工(4)刀具简单车刀制造、刃磨和安装均较方便。
应用范围(1)车削适合于加工各种内、外回转表面。
车削的加工精度范围为IT13~IT6,表面粗糙度Ra值为12.5~1.6 。
(2)车刀结构简单,制造容易,便于根据加工要求对刀具材料、几何角度进行合理选择。
车刀刃磨及装拆也较方便。
(3)车削对工件的结构、材料、生产批量等有较强的适应性,应用广泛。
除可车削各种钢材、铸铁、有色金属外,还可以车削玻璃钢、夹布胶木、尼龙等非金属。
对于一些不适合磨削的有色金属可以采用金刚石车刀进行精细车削,能获得很高的加工精度和很小的表面粗糙度值。
(4)除毛坯表面余量不均匀外,绝大多数车削为等切削横截面的连续切削,因此,切削力变化小,切削过程平稳,有利于高速切削和强力切削,生产效率高。
磨削:特点(1)磨削加工可以获得较高的加工精度和很小的表面粗糙度值。
(2)磨削不但可以加工软材料,如未淬火钢、铸铁和有色金属等,而且还可以加工淬钢及其他刀具不能加工的硬质材料,如瓷件、硬质合金等。
(3)磨削时的切削深度很小,在一次行程中所能切除的金属层很薄。
(4)当磨削加工时,从砂轮上飞出大量细的磨屑,而从工件上飞溅出大量的金属屑。
磨屑和金属屑都会使操作者的眼部遭受危害,尘未吸入肺部也会对身体有害。
(5)由于砂轮质量不良、保管不善、规格型号选择不当、安装出现偏心,或给进速度过大等原因,磨削时可能造成砂轮的碎裂,从而导致工人遭受严重的伤害。
(6)在靠近转动的砂轮进行手工操作时,如磨工具、清洁工件或砂轮修正方法不正确时,工人的手可能碰到砂轮或磨床的其他运动部件而受到伤害。
(7)磨削加工时产生的噪音最高可达110dB以上,如不采取降低噪声措施,也会影响健康。
- 1、下载文档前请自行甄别文档内容的完整性,平台不提供额外的编辑、内容补充、找答案等附加服务。
- 2、"仅部分预览"的文档,不可在线预览部分如存在完整性等问题,可反馈申请退款(可完整预览的文档不适用该条件!)。
- 3、如文档侵犯您的权益,请联系客服反馈,我们会尽快为您处理(人工客服工作时间:9:00-18:30)。
图 6.4 标准型群钻结构
返回目录
其修磨主要特征为: ( 1 )将横刃磨短、磨低,改善横刃处切削条件。 ( 2 )将靠近钻心附近主刃修磨成一段顶角较大的 折线刃和一段圆弧刃 , 以增大该段切削刃前角。同时 ,对称的圆弧刃在钻削过程中起到定心及分屑作用。 ( 3 )在外直刃上磨出分屑槽,改善断屑、排屑情 况。 经过综合修磨而成的群钻 , 切削性能显著 提高。钻削时轴向力下降 35% ~ 50%, 扭矩降低 10% ~ 30% ,刀具使用寿命提高 3 ~ 5 倍 , 生产 率、加工精度都有显著提高 。
两条主切削刃 5 个刀刃 、
两个刀尖
钻头 切削 部分
两条副切削刃 一条横刃、两个刀尖 两个螺旋形前刀面
6 个刀面
Hale Waihona Puke 两个后刀面 两个副后刀面思考题: 1 、麻花钻切削部分的组成如何 ?
2 、麻花钻的主要几何参数。有:
螺旋角 β 、顶角 2Ф 、前角 γo 、后角 α 。和横刃斜角 ψ 等 。
麻花钻的规格:直柄麻花钻( φ0.5~φ20 )
1 、钻削加工的主要问题
1 )导向定心问题:钻头刚性差,易引偏。 采取的措施: P122-123 (例) 2 )排屑问题: 钻孔排屑困难,切屑挤压、摩擦 已加工表面,表面质量差。 采取的措施: P123 3 )冷却问题:冷却困难。 采取的措施:加冷却液,分段钻削,定时 推出的方法来冷却钻头。 故钻孔加工生产效率低。
麻花钻的两个刃瓣可以看作两把对称的车刀。
图
标准高速钢麻花钻
其切削部分的组成为:
前刀面 ---- 螺旋槽的两螺旋面; 主后刀面 ---- 与工件过渡表面(孔底)相对的端部两曲面; 副后刀面 ---- 与工件的加工表面(孔壁)相对的两条棱边; 主切削刃 ---- 螺旋槽与主后刀面的两条交线; 副切削刃 ---- 棱边与螺旋槽的两条交线; 横刃 ---- 两后刀面在钻芯处的交线。 刀尖 ---- 主切削刃与副切削刃的交点(两个)。
锥柄麻花钻( φ8~φ80 ) 钻头材料: 钻头一般为高速钢材料。
麻花钻的角度:
螺旋角 β 最外缘螺旋线切线与轴线的夹角。 25-30º ,右旋 。 前角 γ0 为正交平面内前刀面与基面的夹角,由于钻头的前 刀面为螺旋面,故越靠近中心,前角越小,横刃为负前角。 +30 至 - 30º 后角 α 为轴向剖面内后刀面与切削平面的夹角 。故越靠 近中心,后角越大。 4 - 25º 顶角 2φ 两主切削刃在中心截面上投影的夹角。标准钻头
2 、钻削用量 ( 1 )钻削深度 ap
,
单位: mm
是吃刀深度, ap=d/2 ,当孔径较大时 ,可采用钻—扩加工,这时,钻头直径 取孔径的 70% 左右。
( 2 )进给量 f 和每刃进给量 af : 进给量 f 每刃进给量 af 单位: mm/r 单位: mm/z
af=f/2 ( mm/z)
1 、群钻
经过综合修磨而成的群钻 , 切削性能显著提 高。钻削时轴向力下降 35% ~ 50%, 扭矩降低 10% ~ 30% ,刀具使用寿命提高 3 ~ 5 倍 , 生 产率、加工精度都有显著提高 。
三、其他钻头
1 、群钻 标准麻花钻存在切削刃长、前角变化大、螺 旋槽排屑不畅、横刃部分切削条件很差等结构问 题,生产中为了提高钻孔的精度和效率,常将标 准麻花钻按特定方式刃磨成 “群钻” 使用。 群钻的基本特征为:“三尖七刃锐当先,月 牙弧槽分两边,一侧外刃开屑槽,横刃磨得低窄 尖”。
3 、麻花钻结构上的缺点 ( 1 )横刃处负前角; ( 2 )主切削刃的前角、后角是变化的 ; ( 3 )主切削刃长,切削宽度大,不易 卷曲排屑。
引偏原因:
1) 麻花钻是最常用刀具,由于细长而刚性差 2) 麻花钻上有两条较深的螺旋槽,刚性差 3) 钻头仅有两条很窄二棱边与孔壁接触,接触刚度和导 向作用也 很差。 4) 钻头横刃处前角有很大负值,切削条件极差,钻孔时 一半以上的轴向力由横刃产生,稍有偏斜将产生较大附加力 矩,使钻头弯曲;此外,两切削刃不对称,工件材料不均匀 ,也易引偏
防止钻头引偏的措施: 钻头切削刃刃磨时要尽量对称,使径向力对称 ; 先加工平面,防止表面不平而引偏; 用短而粗的钻头或中心钻先钻一引孔; 采用小进给,减小轴向力; 使用钻套引导,合理使用切削液。
三、其他钻头 1 、群钻 2 、可转位浅孔钻 3 、深孔钻
1 )错齿内排屑深孔钻 2 )单刃外排屑深孔钻
普通麻花钻进给量按 f=(0.01-0.02)d 选择,直径 小于 3-5mm 的小钻头,一般采用手动进给。
( 3 )钻削速度 υc :是钻头外经处的主运
动线速度。单位: m/min 。
vc
dn
1000
d— 钻头直径, mm n— 钻头或工件转速, r/min
钻孔可在钻床上进行,也 可在镗床、车床、铣床上进行。
第6章
钻削、铰削与镗削加工
思考:工件上的孔如何加工出来 ?
钻孔
钻头 钻套 钻模板
工件 钻套:防止钻
扩孔
铰孔
镗孔
孔加工可分为两大类: 一类是从实体材料中钻孔,常用的刀具有麻花 钻、中心钻、深孔钻等。 另一类是对工件上已有孔进行再加工,如扩孔 、铰孔、镗孔,常用的刀具有扩孔钻、铰刀、镗刀 等。 对精度要求高的孔,可根据精度要求采用磨孔、 滚压、珩磨等加工方法。
第一节
一、钻削加工概述
钻削加工与钻头
钻削加工:以钻头或工件的旋转为主运动,两者的相 对运动为进给运动,对实体工件进行加工的切削加工 方法。 钻孔是孔的粗加工方法,孔的尺寸精度一般在 IT13~IT11 , Ra 为 50~12.5μm 。 可加工直径 0.1 ~ 80mm 的孔。钻削中最常用的刀具 是麻花钻。
二、麻花钻的结构
1 、麻花钻结构
加工孔径范围为 0.1--80mm, 以 φ30mm 以下时最 常用。种类:高速钢和硬质合金钻头。
麻花钻由柄部、颈部和工作部分组成。 ① 柄部 ② 颈部 用在与机床或夹具联接,起夹持定位作 位于工作部分和柄部之间,磨削柄部时 由切削部分和导向部分组成。 用 , 并传递扭矩和轴向力。 ,是砂轮的退刀槽。钻头的标记也常标注在这里。 ③ 工作部分
图
标准高速钢麻花钻
麻花钻的工作部分有两个对称的刀刃 ,两条对称的螺旋槽(用于容屑和排屑) ; 导向部分磨有两条棱边(刃带),为 了减少与加工孔壁的摩擦,棱边直径磨有 (0.03 ~ 0.12 ) /100 的倒锥量,形成副 偏角 Kr′ 。
思考题: 1 、麻花钻切削部分有哪几 个主要参数(角度)?