电液锤、液压机、快锻机和精锻机各自的特点
锻压设备概述

锻压设备概述锻压设备具有高效、高精度、高稳定性的特点,能够有效提高金属材料的强度和硬度,并且能够保持工件的内部结构不变。
因此,在航天航空、汽车制造、机械制造等领域都有广泛的应用。
随着科技的发展,现代化的锻压设备通过自动化、智能化等技术的应用,使得生产效率得以提高,质量得以保证,生产成本得以降低。
总的来说,锻压设备在金属加工领域中起着重要的作用,对提高产品质量、促进工业发展具有重要作用。
随着技术的不断进步,锻压设备的生产制造技术和产品性能也将不断提高和改善,这将进一步推动金属加工产业的发展。
锻压是一种常见的金属加工方法,通过锻压设备可以将金属坯料以较高的压力和速度进行塑性变形,使其形成所需的形状和尺寸。
锻压设备的应用范围广泛,可以用于生产汽车零部件、工程机械、航空航天部件、铁路设备等各种领域的产品。
锻压设备可以分为液压锻压机和机械式锻压机两大类。
液压锻压机利用液压传动和液压缸来实现材料的成形加工,具有液压系统压力调节方便、操作灵活等特点,适用于大型复杂构件的锻造。
机械式锻压机则通过机械传动来实现压力和速度的控制,适用于小中型零部件的锻造。
现代化的锻压设备具备自动化控制、数字化操作、智能化监控等功能,能够提高生产效率和产品质量。
在锻压设备的操作中,需要注意保证设备的安全性和稳定性,以防止发生意外事故。
操作人员需要具备针对锻压设备的专业知识和技能,严格按照操作规程进行操作,遵守相关安全操作规定。
另外,锻压设备的维护和保养也是至关重要的,及时检查设备的润滑、密封、电气系统等部件,以保证设备的正常运行。
锻压设备在工业生产中具有重要作用,它能够提高金属件的综合性能,改善内部晶粒组织,提高材料的密度和均匀性。
与其他加工方法相比,锻压设备在提高产品强度、改善材料性能、减少材料损耗等方面具有独特优势。
随着工业化进程的不断推进,锻压设备在国家经济发展中扮演着至关重要的角色。
它不仅是制造业的重要装备,也是实现国家产业升级和技术进步的重要手段。
机械设备四大传动方式优缺点对比,这次终于搞明白了

机械设备四大传动方式优缺点对比,这次终于搞明白了机械设备的种类各种各样,功能和运动方式也是各不相同,有的机构比较小巧,动作灵活,有的机构比较厚重,显得有些笨拙,但是万变不离其宗,我们常用的设备动作方式主要分为四种,机械传动、电气传动、液压传动、气压传动,这四种动作方式各有各的优缺点,都有各自适用的场合。
一、机械传动1.齿轮传动分类:平面齿轮传动、空间齿轮传动。
优点:适用的圆周速度和功率范围广;传动比准确、稳定、效率高;工作可靠性高、寿命长;可实现平行轴、任意角相交轴和任意角交错轴之间的传动。
缺点:要求较高的制造和安装精度、成本较高;不适宜远距离两轴之间的传动。
渐开线标准齿轮基本尺寸的名称有:齿顶圆、齿根圆、分度圆、摸数、压力角等。
2.涡轮涡杆传动适用于空间垂直而不相交的两轴间的运动和动力。
优点:传动比大,结构尺寸紧凑。
缺点:轴向力大、易发热、效率低。
只能单向传动。
涡轮涡杆传动的主要参数有:模数、压力角、蜗轮分度圆、蜗杆分度圆、导程、蜗轮齿数、蜗杆头数、传动比等。
3.链传动包括:主动链、从动链、环形链条。
链传动与齿轮传动相比,其主要特点:制造和安装精度要求较低;中心距较大时,其传动结构简单;瞬时链速和瞬时传动比不是常数,传动平稳性较差。
4.带传动包括:主动轮、从动轮、环形带。
1)用于两轴平行回转方向相同的场合,称为开口运动,中心距和包角的概念。
2)带的型式按横截面形状可分为平带、V带和特殊带三大类。
3)应用时重点是:传动比的计算;结构简单、成本低廉。
缺点:传动的外廓尺寸较大;需张紧装置;由于打滑,不能保证固定不变的传动比带的寿命较短;传动效率较低。
5.轮系1)轮系分为定轴轮系和周转轮系两种类型。
2)轮系中的输入轴与输出轴的角速度(或转速)之比称为轮系的传动比。
等于各对啮合齿轮中所有从动齿轮齿数的乘积与所有主动齿轮齿数乘积之比。
3)在周转轮系中,轴线位置变动的齿轮,即既作自转,又作公转的齿轮,称为行星轮,轴线位置固定的齿轮则称为中心轮或太阳轮。
锻压设备及控制

第二章 锻锤●锻锤:利用气压或液压等传动机构使落下部分(活塞、锤杆、锤头、上砧(或上模块),产生运动并积累动能,在极短的时间施加给锻件,使之获得塑性变形能,完成各种锻压工艺的锻压机械称为锻锤。
● 锻锤的分类 1、机械锤(夹板锤、钢丝锤、弹簧锤) 2、空气锤 3、蒸汽—空气锤(自由锻、模锻锤 )4、蒸汽—空气对击锤 5、高速锤 6、液压模锻锤 7、螺旋压力机● 锻锤的主要特点1、打击速度高:锻锤是一种冲击成形设备,打击速度高,一为7~9m/s ,因此金属流动性好,成形工艺性好。
2、行程次数高:空气锤打击次数在100~250 min-1之间,蒸汽—空气锤全行程打击次数一般也大于70min-1,因而有较高的生产率。
3、操作灵活:工艺万能性强,作为模锻设备时,在一台锤上以完成拔长、滚挤、预锻、终锻等各种工序的操作。
4、定能量设备:没有固定的下死点。
其锻造能力不受吨位限制,当锻锤的有效打击能量小于锻件变形所需能量时,可以多打几锤。
另外当锻件变形量较小时,可以产生很大的打击力。
5、结构简单:制造容易,安装方便,价格便宜。
● 锻锤的打击特性锻锤以很大的砧座或可动的下锤头作为打击的支承面,在工作行程时,锤头的打击速度瞬间降至零,工作是冲击性的,能产生很大的打击力,通常会引起很大的振动和噪音。
●锻锤的打击能量表现为锤头下落行程终了(工件变形前)所具有的动能,对于有砧座式: E h =221mv (2—27)式中:E h —锻锤打击能量,单位为J 或KJ ,它表示锻锤的有效工作能力,是锻锤主参数; m —落下部分质量;v —下落行程终了(工件变形前)锤头速度。
●锻锤的打击过程 在千分之几秒内完成,对有砖座式锤,锤头将打击能量传递给锻件和固定砖座,对于对击式锤,上下两锤头完成等行程撞击或等能量撞击。
打击过程中锻件在锤头与砖座上下两锤头间完成塑性变形。
过程分为两个阶段,第一阶段为加载阶段,在此阶段,随着锤头与砖座彼此接近而致使锻件成形。
锻造起重机的分类和特点分析

锻造起重机的分类和特点分析起重机作为现代工程施工和物流运输领域中不可或缺的设备,发挥着举升、装载和搬运重物的重要作用。
锻造起重机作为一种特殊的起重设备,在钢铁、冶金、船舶等领域中广泛应用。
本文将对锻造起重机的分类和特点进行分析,以帮助读者更好地了解和应用这一重要设备。
一、锻造起重机的分类根据使用场合和形式,锻造起重机可以分为以下几类。
1. 液压锻造起重机:液压锻造起重机以液压为动力,采用液压传动和控制技术,具有操作灵活、响应迅速、起重能力大的特点。
它广泛应用于轻小型锻压、塑性加工和成型等领域,特别适合对材料进行钳装、翻转、堆垛等操作。
2. 机械锻造起重机:机械锻造起重机以机械传动为动力,通过齿轮、链条、蜗轮等机械装置实现起重、运输和操控功能。
机械锻造起重机结构简单、易于维修,适用于中小型锻压设备,例如冲压机、热压机等。
3. 水压锻造起重机:水压锻造起重机采用水压传动系统,具有起重力大、控制精度高的特点。
它主要用于重型锻压设备,能够承担高强度的工作负荷,用于生产大型船舶、压力容器等工件。
4. 电动锻造起重机:电动锻造起重机以电力为动力来源,通过电机带动机械装置实现起重和操控功能。
它具有结构紧凑、运行平稳、动作灵活等特点,特别适合作为中小型锻压设备和装卸货物的起重机种。
二、锻造起重机的特点1. 高起重能力:锻造起重机通常需要举升和搬运重量大、体积庞大的工件,因此具有较高的起重能力。
它的设计和制造需要充分考虑到重物的稳定性和安全性。
2. 精确的控制系统:对于锻造起重机来说,精确的动作控制是至关重要的。
它需要能够精确控制工件的举升、放下、运动速度等参数,以保证锻造工艺的质量和效率。
3. 快速的反应速度:锻造起重机在操作过程中对于动作的迅速响应有很高的要求。
它需要能够快速而准确地响应操纵者的指令,以适应锻造过程中快速变化的工况需求。
4. 高强度和耐久性:由于锻造起重机常常需要处理重量和体积较大的工件,它需要具备高强度和耐久性,以保证设备的安全和长期使用。
常用锻压设备分类
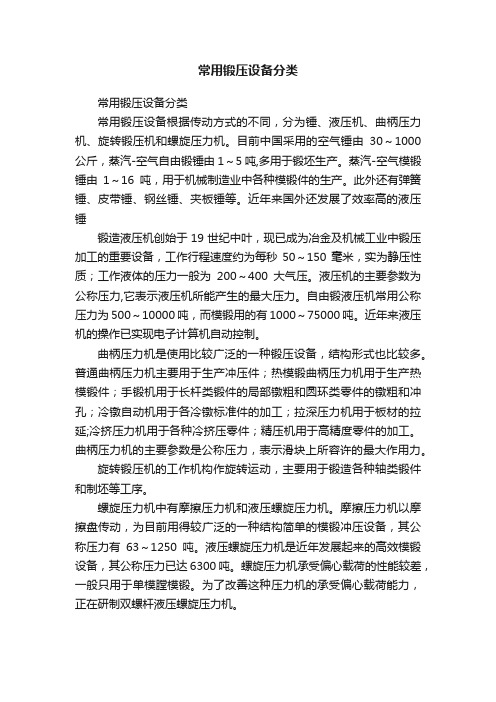
常用锻压设备分类常用锻压设备分类常用锻压设备根据传动方式的不同,分为锤、液压机、曲柄压力机、旋转锻压机和螺旋压力机。
目前中国采用的空气锤由30~1000公斤,蒸汽-空气自由锻锤由1~5吨,多用于锻坯生产。
蒸汽-空气模锻锤由1~16吨,用于机械制造业中各种模锻件的生产。
此外还有弹簧锤、皮带锤、钢丝锤、夹板锤等。
近年来国外还发展了效率高的液压锤锻造液压机创始于19世纪中叶,现已成为冶金及机械工业中锻压加工的重要设备,工作行程速度约为每秒50~150毫米,实为静压性质;工作液体的压力一般为200~400大气压。
液压机的主要参数为公称压力,它表示液压机所能产生的最大压力。
自由锻液压机常用公称压力为500~10000吨,而模锻用的有1000~75000吨。
近年来液压机的操作已实现电子计算机自动控制。
曲柄压力机是使用比较广泛的一种锻压设备,结构形式也比较多。
普通曲柄压力机主要用于生产冲压件;热模锻曲柄压力机用于生产热模锻件;手锻机用于长杆类锻件的局部镦粗和圆环类零件的镦粗和冲孔;冷镦自动机用于各冷镦标准件的加工;拉深压力机用于板材的拉延;冷挤压力机用于各种冷挤压零件;精压机用于高精度零件的加工。
曲柄压力机的主要参数是公称压力,表示滑块上所容许的最大作用力。
旋转锻压机的工作机构作旋转运动,主要用于锻造各种轴类锻件和制坯等工序。
螺旋压力机中有摩擦压力机和液压螺旋压力机。
摩擦压力机以摩擦盘传动,为目前用得较广泛的一种结构简单的模锻冲压设备,其公称压力有63~1250吨。
液压螺旋压力机是近年发展起来的高效模锻设备,其公称压力已达6300吨。
螺旋压力机承受偏心载荷的性能较差,一般只用于单模膛模锻。
为了改善这种压力机的承受偏心载荷能力,正在研制双螺杆液压螺旋压力机。
电液锤、液压机、快锻机和精锻机各自的特点

电液锤、液压机、快锻机和精锻机各自的特点1 电液锤传统蒸汽锤、空气锤能源消耗大,据统计能源利用率不到2%。
为解决蒸汽锤、空气锤存在的问题,国外锻锤设计制造商加快了电液锤的研制步代,取得显著成效。
德国 Lasco公司是世界著名的锻锤制造商。
从电液锤发展历史来看,液压锤经历了从放油打击单动落锤(KH型,称为第1代产品)到放油打击双动落锤(KHK型,称为第2代产品)再到现在的全液压双动落锤(KGH,称为第3代产品)。
全液压双动落锤的打击能量是通过控制油量多少来实现的,打击阀的关闭时间可不受锤头位置的限制,操作十分灵活可靠,彻底根除了放油打击电液锤的许多弊病。
因此,近年来这种电液锤得到较快的发展。
该公司的电液锤已经实现了程序化控制,即打击能量和打击次数都可实现程序控制。
锤的传动效率高达65%,为蒸汽锤和空气锻锤的30倍。
此外,德国Beche公司还研制了全液压锤。
近10年来,我国在电液锤研制方面也取得很大发展,主要表现在传统蒸汽锤、空气锤换头改造上,即采用电液传动装置了代原有锻锤的气缸及动力站,保留原有机架、砧座。
安阳锻压机械公司利用这种技术为数十家企业改造1-3t传统蒸汽锤和空气锤10余台,取得了较好效果,能源利用率由2%提高到20%-60%。
除换头外,电液锤整机的研制仍处于发展阶段,居于德国lasco 公司第2代产品发展水平上,属于液气锤。
全液压锤研究和制造正在起步。
2 液压机液压机的结构特真使其易于获得较大的工作压力、行程和空间;工作压力和工作速度可根据需要进行调整,且平稳,无冲击。
其不足之处是生产效率比较低,活动横梁下死点不易控制准确。
由于液压机具有变形速度低的特点,有利于合金的塑性变形。
因此,比较适用于高合金铸锭锻造。
国外制造液压机技术比较成熟。
俄罗斯重型锻压设备制造公司是生产锻压设备的主导公司,可生产800t,125t,2000t,3150t,6300t液压机,其载重量为5-30t,负载力矩为118-785kN"m,是轨道式锻造操作机。
锻造设备类别和名称
摩擦螺旋压力机
螺
电动螺旋压力机
旋
压
力 液压螺旋压力机
机
双盘摩擦螺旋压力机,模压机
电动程控螺旋压力机、高能螺旋 压力机、电动数控螺旋压力机
两个摩擦盘与中间的飞轮交替接触 而实现提升和打击,公称力 100MN 以下全部可以生产,但在数控和精巧 方面与国外有差距。 电机直接驱动飞轮和螺杆,电机正转 打击,反转回程。国内目前可以生产 公称力 80MN 以下的压力机,但可靠 行不足。 公称力 25MN 以下可以生产,电机直 接驱动下行打击,液压提升回程。
轻合金液压挤压机
速度 10 毫米/秒以上设备可以制造, 卧室主要用于型材生产,少加工功能
零部件。
铜合金挤压机、钛合金挤压机
类似于轻合金液压挤压机,主要用于 原材料坯料制备,也有直接成形功能 部件的。也生产结构件用型材,铜合 金挤压机也用于装饰型材挤压,国内 可以制造各规格。
曲柄压力机、楔式压力机、偏心 压力机、肘杆式压力机
气,锤头抬起,突然释放下腔油压, 上腔压缩氮气膨胀推动活塞下行实 现打击。目前国内可以生产模锻 16T 以下,自由锻 8T 以下的锻锤。国外 自由锻没有,很好生产这类锻锤了。 对于大吨位锻锤,采用对击,其中主 锤头的打击与放油打击一样,目前下 锤头打击是依靠机械联接实现,国内 完全可以制造。 油缸中,上下腔全部充满高压油,由 于上腔面积大而形成推动,推动活塞 下行实现打击。模锻 125KJ 以下,对 击 400KJ 以下可以生产,但可靠性和 可控性与国外有差距。大吨位锻锤, 采用对击,上锤头运行于模锻一致, 下锤头有的是机械联接,有的是液压 驱动,国内目前的结构为机械联接。
国内可以生产。
材料竖向被咬入,完成聚料成形,全
部规格国产。但目前国内还不能生产
锻压设备特点及现状
锻压设备特点及现状1、前言世界锻压工业的柔性自动化发展不断加快。
冲压设备广泛应用于汽车、航空、电子、家电等工业领域,其中,作为衡量一个国家工业水平的标志之一的汽车工业,被当今世界主要工业发达国家和新兴工业国家列为国民经济支柱产业,其发展主导了锻压技术及装备的发展,锻压技术的发展和进步基本围绕汽车工业的发展而进行。
激烈的市场竞争促使汽车更新换代的速度明显加快,产品的市场寿命周期进一步缩短;与此同时,汽车变型品种日益增多,现代汽车工业生产日益呈现生产规模化、车型个性化,车型批量小、车型变化快、多车型共线生产、车身覆盖件大型化一体化的特征。
传统的加工单一品种的刚性生产线显然已不适应这种特征和市场形势发展的要求,其升级换代产品具有高柔性和高效率的自动化锻压设备,成为世界冲压技术及装备发展的主要潮流。
2、工艺锻压是利用锻压机械的锤头、砧块、冲头或通过模具对坯料施加压力,使之产生塑性变形,从而获得所需形状和尺寸的制件的成形加工方法。
按成形方式锻压可分为锻造和冲压两大类;按变形温度锻压可分为热锻压、冷锻压、温锻压和等温锻压等。
锻压的生产过程包括成形前的锻坯下料、锻坯加热和预处理;成形后工件的热处理、清理、校正和检验。
自由锻基本工序分为拔长、镦粗、冲孔、弯曲等。
锻压的分类如图。
自由锻模锻:热模锻(高速锤锻造)、冷模锻锻造镦粗:热镦、冷镦挤压:热挤压、冷挤压锻压拉拔:热拉、冷拉旋转锻造:成形轧制、辊锻、辗扩、径向锻造、摆动辗压高能成形率超塑成型冲裁:剪切冲压成形:弯曲、拉深、胀形、旋压、矫正3、锻造设备锻造装出料机是用于将锻造钢锭或坯料装入加热炉中,并能将加热好的钢锭或坯料从加热炉中取出,送给锻造压机或锻造操作机的设备。
它是锻造过程中一个重要的设备,在我国的发展近二十年的历史了。
轨道式装出料机的典型应用如图所示:若车间工艺布置允许,轨道式装出料机应式锻造厂装出料的首选设备。
但轨道式装出料机也有它的局限性,主要表现在它需要在锻造厂房内铺设轨道,对锻造厂房内的生产布局要求较高。
锻造机的分类及原理
锻造机的分类及原理以下是 7 条关于锻造机分类及原理的内容:1. 锻造机有好多种呢!像模锻机,你看它就如同一个大力士,把金属材料使劲压制成各种形状。
就好比捏橡皮泥,只不过这“橡皮泥”可硬多了!它的原理啊,就是利用强大的力量和模具,让金属乖乖听话,变成我们想要的样子。
哇塞,是不是很厉害?2. 自由锻机也不能小瞧呀!它就像一个灵活的舞者,可以对金属进行各种变幻莫测的锻造操作。
比如要打造一个特别形状的零件,它就能大显身手。
它的原理呢,就是给予金属足够的自由空间来变形,随心所欲地塑造,这不神奇吗?3. 锻锤啊,那可是锻造机里的猛将!每次敲击都像打鼓一样,咚咚咚!你说像不像雷神在锻造他的锤子?它的工作原理就是靠强大的冲击力,一下下把金属锻造成型,厉害得很呢!你能想象那力量吗?4. 液压机呢,这可是个沉稳的家伙!如同一个安静却有力量的巨人。
比如制造一些大型工件,它就能稳稳地发挥作用。
它的原理是通过液压压力来实现锻造,就好像给金属施了魔法一样,让它听话地改变形状,酷吧?5. 旋转锻造机很特别哦!就像个快速旋转的精灵,能让金属材料在旋转中发生奇妙的变化。
你想想看,是不是很像在给金属跳一场华丽的舞蹈?它的原理就是利用旋转和压力来锻造,是不是很新颖?6. 螺旋压力机也有它的独特之处啊!它就如同一头倔强的老牛,有着使不完的力气。
像是要攻克一个坚硬的目标,它就会冲上去。
它的原理是以螺旋的方式施加压力锻造金属,挺有意思吧?7. 机械压力机可是个老大哥呢!它高效又稳定,就跟一个经验丰富的匠人一样。
在大规模锻造生产中那是必不可少的。
它的原理就是通过机械结构产生巨大的压力来工作,简直就是锻造界的明星呀!总之啊,这些锻造机各有各的本事,它们真是工业制造里的大功臣啊!。
锻造压力机的分类及特点分析
锻造压力机的分类及特点分析锻造压力机是一种常见的工业设备,用于将金属材料加工成所需形状的工艺过程。
它通过施加压力和热能将金属材料改变其形状、尺寸和性能。
在金属加工行业中,锻造压力机起着至关重要的作用。
本文将对锻造压力机的分类及特点进行详细分析。
锻造压力机可以根据工作方式、压力种类和结构形式等方面进行分类。
首先,根据工作方式的不同,锻造压力机可以分为液压锻造机、气动锻造机和机械锻造机。
液压锻造机是一种利用液体传动能力的压力机。
它主要由液压系统、传动系统和控制系统组成。
液压锻造机具有工作稳定、压力范围大的特点,可适应不同形状和尺寸的锻件加工。
然而,液压锻造机的成本较高,维护和维修较复杂。
气动锻造机是一种利用气体传动能力的压力机。
它主要由气源系统、传动系统和控制系统组成。
气动锻造机具有结构简单、操作方便的特点,适用于小尺寸和简单形状的锻件加工。
然而,气动锻造机的压力范围有限,无法适应较大的锻件加工需求。
机械锻造机是一种利用机械传动能力的压力机。
它主要由传动系统和控制系统组成。
机械锻造机具有结构稳定、可靠性高的特点,适用于大尺寸和复杂形状的锻件加工。
然而,机械锻造机的工作效率相对较低,需要较大的功率驱动。
其次,根据压力种类的不同,锻造压力机可以分为冷锻机和热锻机。
冷锻机是一种在常温下进行金属锻造的压力机。
冷锻机主要用于加工不锈钢、合金钢等材料,具有加工精度高、强度高的特点。
然而,由于不锈钢等材料的塑性较差,在冷锻过程中需要施加较大的压力,加工难度较大。
热锻机是一种在高温下进行金属锻造的压力机。
热锻机主要用于加工高温合金、钛合金等材料,具有加工效率高、热变形能力强的特点。
然而,热锻机加工过程中需要控制温度和时间,以避免材料烧结或过热。
最后,根据结构形式的不同,锻造压力机可以分为冲击式锻压机、摆辊式锻压机和摆架式锻压机。
冲击式锻压机是一种通过高速下落的压头对工件进行冲击的压力机。
冲击式锻压机主要用于大型锻件的成型,具有冲击力大的特点。
- 1、下载文档前请自行甄别文档内容的完整性,平台不提供额外的编辑、内容补充、找答案等附加服务。
- 2、"仅部分预览"的文档,不可在线预览部分如存在完整性等问题,可反馈申请退款(可完整预览的文档不适用该条件!)。
- 3、如文档侵犯您的权益,请联系客服反馈,我们会尽快为您处理(人工客服工作时间:9:00-18:30)。
电液锤、液压机、快锻机和精锻机各自的特点
1 电液锤
传统蒸汽锤、空气锤能源消耗大,据统计能源利用率不到2%。
为解决蒸汽锤、空气锤存在的问题,国外锻锤设计制造商加快了电液锤的研制步代,取得显著成效。
德国 Lasco公司是世界著名的锻锤制造商。
从电液锤发展历史来看,液压锤经历了从放油打击单动落锤(KH型,称为第1代产品)到放油打击双动落锤(KHK型,称为第2代产品)再到现在的全液压双动落锤(KGH,称为第3代产品)。
全液压双动落锤的打击能量是通过控制油量多少来实现的,打击阀的关闭时间可不受锤头位置的限制,操作十分灵活可靠,彻底根除了放油打击电液锤的许多弊病。
因此,近年来这种电液锤得到较快的发展。
该公司的电液锤已经实现了程序化控制,即打击能量和打击次数都可实现程序控制。
锤的传动效率高达65%,为蒸汽锤和空气锻锤的30倍。
此外,德国Beche公司还研制了全液压锤。
近10年来,我国在电液锤研制方面也取得很大发展,主要表现在传统蒸汽锤、空气锤换头改造上,即采用电液传动装置了代原有锻锤的气缸及动力站,保留原有机架、砧座。
安阳锻压机械公司利用这种技术为数十家企业改造1-3t传统蒸汽锤和空
气锤10余台,取得了较好效果,能源利用率由2%提高到20%-60%。
除换头外,电液锤整机的研制仍处于发展阶段,居于德国lasco 公司第2代产品发展水平上,属于液气锤。
全液压锤研究和制造正在起步。
2 液压机
液压机的结构特真使其易于获得较大的工作压力、行程和空间;工作压力和工作速度可根据需要进行调整,且平稳,无冲击。
其不足之处是生产效率比较低,活动横梁下死点不易控制准确。
由于液压机具有变形速度低的特点,有利于合金的塑性变形。
因此,比较适用于高合金铸锭锻造。
国外制造液压机技术比较成熟。
俄罗斯重型锻压设备制造公司是生产锻压设备的主导公司,可生产800t,125t,2000t,3150t,6300t液压机,其载重量为5-30t,负载力矩为118-785kN"m,是轨道式锻造操作机。
俄罗斯依若尔重机厂能制造12500t的液压机。
俄罗斯上萨尔达冶金生产联合公司是世界上最大的钦生产商,拥有世界上最大的75000t液压机。
2002年,在75000t和30000t液压机上安装了自动控制系统,可生产重达3.2t的锻件。
美国能生产液压机的最大吨位为12000t,日本生产的最大吨位为10000t,我国液压机设计制造技术与国际水平相当,第一重型机械集团、第二重型机械集团公司均可制造12000t液压机。
我国拥有10000t级大型液压机数量己跃居世界第3位。
为了提高液压机的使用效率,国外液压制造商把目光放在锻造液压机的技术改造上,主要对液压系统和控制系统的改造。
在这方面德国sPs公司、德马克公司积累了不少成功经验,液压系统采用现代的先导阀,手工操纵改用计算机控制,改造后液压机具有与快锻机相同的控制精度和性能。
3 快锻液压机
目前,在一些发达国家,尤其是德国,快锻液压机的设计制造技术已经相当成熟。
它们用油作介质,泵直接驱动,大多采用下拉式主机结构,液压泵站一般设置在主机附近的地下室内。
某些公司设计制造的快锻液压机具有一系列先进性,主要表现在:液压系统采用具有快速反应的电磁阀作先导阀,其切换频率高达250次/min,故该阀动态响应快、动作灵敏、启闭迅速,能满足压机快速性要求;主缸和排液设有另外的通道,使充液阀成了只有充液功能的单向阀,减少了液压冲击;快锻液压机采用微机控制,压机与操作机之间联动自如,当锻件的锻造工艺确定后,即可通过计算机控制实现程序化锻造,我国快锻液压机的主要生产厂家有西安重型机械研究所和兰石新技术开发实业公司。
在20世纪80年代中期,由西安重型机械研究所和北京重型机械厂研制成国内第1台800t快锻液压机组,在兰石公司投人运行。
兰石公司对该机组的液压系统、主机、微机控制系统进行全面评估,发现了快速电磁阀电路板设计、高速轻型泵的泵头阀、主机圆形立柱与调整导套间隙不易调均,运动不够平衡等技术问题,在总结经验的基础上,提出了一系列改进措施,取得了成效。
目前,兰石公司已能生产800t和1600t快锻液压机,制造水平有了很大提高,但其液压系统的主要部件如泵、先导阀等还需国外配套。
我国快锻液压机的总体水平与德国制造技术相比还有较大的差距。
随着现代工业的快速发展,人们对自由锻件的尺寸精度和生产效率提出了越来越高的要求,因而对液压机的锻造速
度和压下精度的要求也随之提高,为了适应这种要求,快锻液压机应运而生。
国外生产快锻液压机的厂家主要有德国曼内斯曼一德马克
公司、潘因克(pahnke)公司和日本的三菱长崎机工株式会社。
4 精锻机
精锻机(径向精密锻造机)开发于20世纪40年代,其中卧式精锻机用得较多,分为机械驱动和液压驱动2种形式。
径向锻造具有脉冲锻打和多向锻打的特点,而且脉冲锻打频率高(一般为180-1800Zk/min),速度快,每次变形量很小。
采用多锻模(最多可达8个),沿径向从多个方向锻打,使金属变形处于三向压应力状态,有利于提高金属的塑性。
此外,径向锻造机自动化程度高,生产的锻件精度高,表面粗糙度小。
但也有不足之处,因为锻造时,工件表面变形大于中心部位变形,如果锻比控制不当会出现心部锻不透的现象。
另外,由于打击频率高,产生变形热,使锻件局部温度上升,导致钢的显微组织不均匀,影响性能。
奥地利GFM是世界知名的径向锻机生产公司,可生产3种类型的精锻机:
①机械传动的SX型;
②液压传动的PX型;
③(连续式SD型。
吨位从802500t,最大吨位的SX-85径向锻机,锤头最大锻打力为
29420 kN,打击次数125次/min。
此外,德国Eumuco公司也能生产精锻机,以液压传动为主,如SMX-18型,最大打击力2697kN,打击次数180320Zk/min。
从20世纪80年代中期至今我国已从奥地利引进了SX-25,
SX-32,SX-40,SX-55,SX-65型7台精锻机,吨位分别为400t,
500t,800t,1000t和1400t,主要用于锻制特种钢、工具钢和锻件,使用效果比较理想。
我国精锻机的研制进程十分缓慢,至今为止只仿制了2台中型精锻机。
一台是由大连钢厂牵头制造的一台340t精锻机,另一台是由大连精工锻压高新技术公司提供技术,中国一重制造的400t精锻机,投产后已使用5年,年加工量达2000t。
国外电液锤制造技术发展迅速。
目前,我国仅限于蒸汽锤和空气锤的换头改造技术,整机研制处于发展阶段。
我国液压机设计制造技术比较成熟,制造水平与国外相当。
我国生产的快锻机的最大吨位为1600t,关键部件尚需进口,实现国产化还有一段路要走,要制造3000t以上的快锻机必须使设计和制造水平上一个新台阶。
至于精锻机,设计制造工作进展十分缓慢,仍处于起步阶段,与国外相比有很大差距,应加强投人,迎头赶上。