数学建模零件参数的优化设计
在零件的参数优化设计中的数学建模
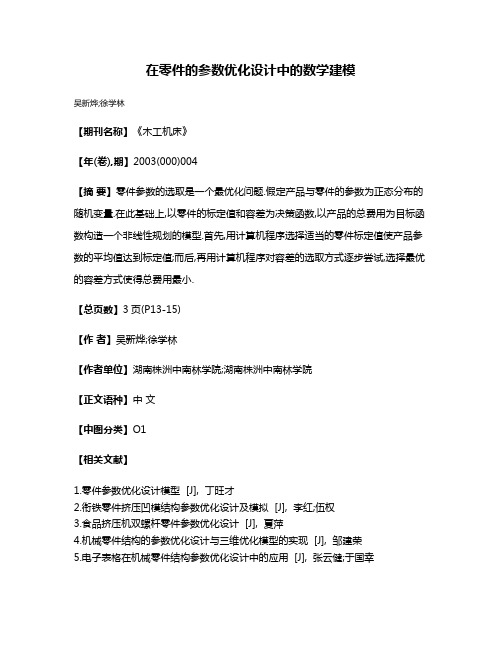
在零件的参数优化设计中的数学建模
吴新烨;徐学林
【期刊名称】《木工机床》
【年(卷),期】2003(000)004
【摘要】零件参数的选取是一个最优化问题.假定产品与零件的参数为正态分布的随机变量.在此基础上,以零件的标定值和容差为决策函数,以产品的总费用为目标函数构造一个非线性规划的模型.首先,用计算机程序选择适当的零件标定值使产品参数的平均值达到标定值;而后,再用计算机程序对容差的选取方式逐步尝试,选择最优的容差方式使得总费用最小.
【总页数】3页(P13-15)
【作者】吴新烨;徐学林
【作者单位】湖南株洲中南林学院;湖南株洲中南林学院
【正文语种】中文
【中图分类】O1
【相关文献】
1.零件参数优化设计模型 [J], 丁旺才
2.衔铁零件挤压凹模结构参数优化设计及模拟 [J], 李红;伍权
3.食品挤压机双螺杆零件参数优化设计 [J], 夏萍
4.机械零件结构的参数优化设计与三维优化模型的实现 [J], 邹建荣
5.电子表格在机械零件结构参数优化设计中的应用 [J], 张云健;于国幸
因版权原因,仅展示原文概要,查看原文内容请购买。
零件参数设计matlab程序(数学建模)
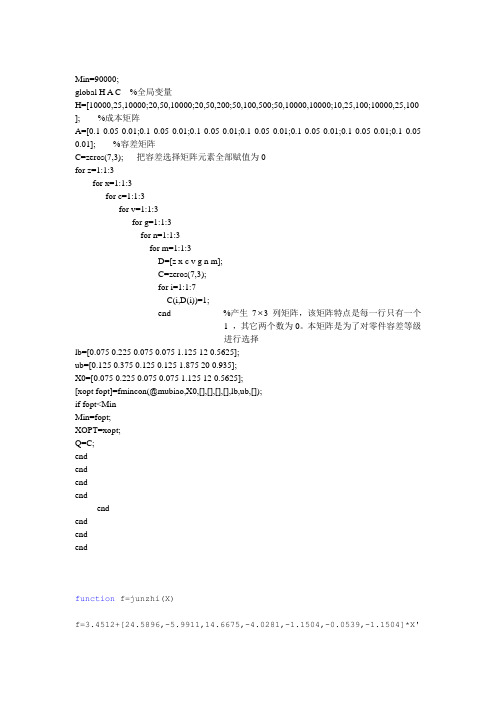
Min=90000;global H A C %全局变量H=[10000,25,10000;20,50,10000;20,50,200;50,100,500;50,10000,10000;10,25,100;10000,25,100 ]; %成本矩阵A=[0.1 0.05 0.01;0.1 0.05 0.01;0.1 0.05 0.01;0.1 0.05 0.01;0.1 0.05 0.01;0.1 0.05 0.01;0.1 0.05 0.01]; %容差矩阵C=zeros(7,3); 把容差选择矩阵元素全部赋值为0for z=1:1:3for x=1:1:3for c=1:1:3for v=1:1:3for g=1:1:3for n=1:1:3for m=1:1:3D=[z x c v g n m];C=zeros(7,3);for i=1:1:7C(i,D(i))=1;end %产生7 3列矩阵,该矩阵特点是每一行只有一个1 ,其它两个数为0。
本矩阵是为了对零件容差等级进行选择lb=[0.075 0.225 0.075 0.075 1.125 12 0.5625];ub=[0.125 0.375 0.125 0.125 1.875 20 0.935];X0=[0.075 0.225 0.075 0.075 1.125 12 0.5625];[xopt fopt]=fmincon(@mubiao,X0,[],[],[],[],lb,ub,[]);if fopt<MinMin=fopt;XOPT=xopt;Q=C;endendendendendendendendfunction f=junzhi(X)f=3.4512+[24.5896,-5.9911,14.6675,-4.0281,-1.1504,-0.0539,-1.1504]*X'; %把一组X取值带入经验公式的简化式,得到期望值μfunction f=junzhi2(X)f=([24.5896,-5.9911,14.6675,-4.0281,-1.1504,-0.0539,-1.1504].*X)/3; %得到一个行向量,为计算均方差σ做准备function f=mubiao(X)global C A H %全局变量B=C.*A;E=(sum(B,2));G= junzhi2(X);F=(G'.*E).^2;b=(sum(F(:)))^0.5; %求解产品参数的均方差,b即是均方差a= junzhi(X); %求解产品参数的期望值p0=normcdf(1.6,a,b)-normcdf(1.4,a,b); %产品为合格品的概率p1=normcdf(1.8,a,b)-normcdf(1.6,a,b)+normcdf(1.4,a,b)-normcdf(1.2,a,b ); %产品为次品的概率p2=1-p0-p1; %产品为废品的概率sunshi=1000*p1+9000*p2; %产品的损失费用I=C.*H; %用容差选择矩阵选择容差等级chengben=sum(I(:)); %零件的总成本f=chengben+sunshi; %目标函数。
数学建模零件参数的优化设计

数学建模零件参数的优化设计Company number【1089WT-1898YT-1W8CB-9UUT-92108】零件参数的优化设计摘要本文建立了一个非线性多变量优化模型。
已知粒子分离器的参数y由零件参数)72,1(=ixi 决定,参数ix的容差等级决定了产品的成本。
总费用就包括y偏离y造成的损失和零件成本。
问题是要寻找零件的标定值和容差等级的最佳搭配,使得批量生产中总费用最小。
我们将问题的解决分成了两个步骤:1.预先给定容差等级组合,在确定容差等级的情况下,寻找最佳标定值。
2.采用穷举法遍历所有容差等级组合,寻找最佳组合,使得在某个标定值下,总费用最小。
在第二步中,由于容差等级组合固定为108种,所以只要在第一步的基础上,遍历所有容差等级组合即可。
但是,这就要求,在第一步的求解中,需要一个最佳的模型使得求解效率尽可能的要高,只有这样才能尽量节省计算时间。
经过对模型以及matlab代码的综合优化,最终程序运行时间仅为秒。
最终计算出的各个零件的标定值为:ix={,,,,,,},等级为:BBCCBBBd,,,,,,=一台粒子分离器的总费用为:元与原结果相比较,总费用由(元/个)降低到(元/个),降幅为%,结果是令人满意的。
为了检验结果的正确性,我们用计算机产生随机数的方式对模型的最优解进行模拟检验,模拟结果与模型求解的结果基本吻合。
最后,我们还对模型进行了误差分析,给出了改进方向,使得模型更容易推广。
关键字:零件参数 非线性规划 期望 方差一、问题重述一件产品由若干零件组装而成,标志产品性能的某个参数取决于这些零件的参数。
零件参数包括标定值和容差两部分。
进行成批生产时,标定值表示一批零件该参数的平均值,容差则给出了参数偏离其标定值的容许范围。
若将零件参数视为随机变量,则标定值代表期望值,在生产部门无特殊要求时,容差通常规定为均方差的3倍。
进行零件参数设计,就是要确定其标定值和容差。
这时要考虑两方面因素:一是当各零件组装成产品时,如果产品参数偏离预先设定的目标值,就会造成质量损失,偏离越大,损失越大;二是零件容差的大小决定了其制造成本,容差设计得越小,成本越高。
数学建模中的参数估计与优化
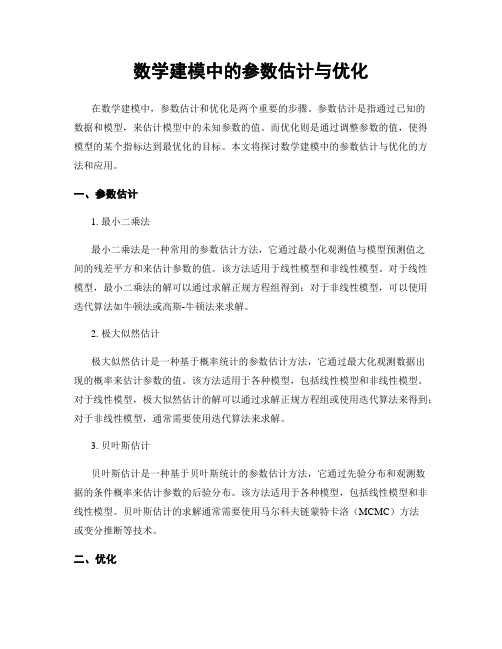
数学建模中的参数估计与优化在数学建模中,参数估计和优化是两个重要的步骤。
参数估计是指通过已知的数据和模型,来估计模型中的未知参数的值。
而优化则是通过调整参数的值,使得模型的某个指标达到最优化的目标。
本文将探讨数学建模中的参数估计与优化的方法和应用。
一、参数估计1. 最小二乘法最小二乘法是一种常用的参数估计方法,它通过最小化观测值与模型预测值之间的残差平方和来估计参数的值。
该方法适用于线性模型和非线性模型。
对于线性模型,最小二乘法的解可以通过求解正规方程组得到;对于非线性模型,可以使用迭代算法如牛顿法或高斯-牛顿法来求解。
2. 极大似然估计极大似然估计是一种基于概率统计的参数估计方法,它通过最大化观测数据出现的概率来估计参数的值。
该方法适用于各种模型,包括线性模型和非线性模型。
对于线性模型,极大似然估计的解可以通过求解正规方程组或使用迭代算法来得到;对于非线性模型,通常需要使用迭代算法来求解。
3. 贝叶斯估计贝叶斯估计是一种基于贝叶斯统计的参数估计方法,它通过先验分布和观测数据的条件概率来估计参数的后验分布。
该方法适用于各种模型,包括线性模型和非线性模型。
贝叶斯估计的求解通常需要使用马尔科夫链蒙特卡洛(MCMC)方法或变分推断等技术。
二、优化1. 单目标优化单目标优化是指通过调整参数的值,使得模型的某个指标达到最优化的目标。
常见的单目标优化方法包括梯度下降法、牛顿法、拟牛顿法等。
这些方法适用于连续可导的优化问题。
对于非连续或不可导的优化问题,可以使用遗传算法、粒子群算法等启发式算法来求解。
2. 多目标优化多目标优化是指通过调整参数的值,使得模型的多个指标达到最优化的目标。
常见的多目标优化方法包括多目标遗传算法、多目标粒子群算法等。
这些方法可以得到模型的一组最优解,形成一个非劣解集合。
三、应用案例1. 线性回归模型线性回归模型是一种常见的参数估计和优化问题。
通过最小二乘法估计线性回归模型的参数,可以得到最优的拟合曲线。
数学建模案例分析--最优化方法建模5产品试验与设计

n
n
n
n
(1)
x
k 1
n
jk
1,
j 1,2,, n
(2)
x
j 1
n
jk
1,
k 1,2,, n
(3)
x jk 0,1 j, k 1,2,, n
由于乘积项 x jk x pq 在(1)式中出现,这是一个二次规划模型。
(4)
k 2k / n, (k 1,2,, n) ,于是当叶片 j
安装在位置 k 上时,产生的离心力(向量)可用复数
f ( j, k ) rj eik , eik cosk i sin k
表示。叶片的安装方案可以看作一个任务分派问题,我们引入0—1变量
1 , 叶片j安装在位置k x jk 0 , 否则
则 n 个叶片的合力(向量)为
F r j e i k x jk
j 1 k 1
n
n
问题的目标函数可取合力F的模的平方
Z
约束条件显然为
r e
j 1 k 1 j
n
n
2 i k
x jk
Hale Waihona Puke r j rp cos( k q ) x jk x pq
j 1 k 1 p 1 q 1
*
(3) (4)
*
x
i 1
n
i
1
(5)
x1 , x2 ,, xn 0
*
(6)
其中 y2 是硬度指标下限, y3 是变形率的上限, (5)是将 x1 , x2 ,, xn 作为配比(%)而引入的。 一般来说,这是一个非线性规划模型。实际上,由(1)式确定 y j f j ( x1 , x2 ,, xn ), j 1,2,3 也可视为非线性规划问题,只不过当它们是线性函数时,问题化为线性规划,很容易求解。 例11 某厂生产 n 种饲料 P 1, P 2 ,, P n ,它们均由 m 种原料 Q1 , Q2 ,, Qm 配合而成, Q j 在 Pi 中 含量(百分比)的上限为 uij ,下限为 l ij 。若 Pi 的售价为 pi (元/千克) , Q j 的成本为 q j (元/千
优化设计数学建模

一、问题重述1、利用优化设计相关理论计算法,对某设计问题做优化设计。
要求如下:①列出优化数学模型;②选择所用优化算法;③画出程序框图;④程序编写;⑤程序调试运算结果。
现根据以上条件,结合生活实际,准备以铁板为材料设计一鱼缸,为了能使鱼儿有更大的生存空间,要求鱼缸容积最大。
现有边长为5米长的方形铁板,预备在四个角减去四个相等的方形面积,用以制成方形鱼缸,如何减能使鱼缸的容积最大。
二、问题分析2.1、对于此问题,我采用的数学模型包括三部分,即设计变量、目标函数和约束条件。
模型如下:其中,设裁去铁块的边长为:x(0<x<2.5)则鱼缸的容积可表示成函数:y=-x*(5-2*x)^2上述问题则可以描述为:求变量:x使函数:min y=-x*(5-2*x)^2(前加有”负”号,,故所求最大容积为最小y值)...........................................................................(1*)约束条件:0<x<2.5(保证能够做成鱼缸)2.2、本模型采用无约束优化数学模型,运用一位搜索中的0.618法进行最优值求解,通过Visio软件制作流程图,结合MATLAB软件进行编程(因C语言编程多次调试没能成功),plot函数进行绘图分析,最终成功的调试得出运算结果。
三、程序框图四、程序编写及函数图像4.1求极值所用程序如下:function q=line_s(a,b)N=10000;r=0.01;a=0;b=1.5;for k=1:N;v=a+0.382*(b-a);u=a+0.618*(b-a);fv=-25*v+20*v^2-4*v^3;fu=-25*u+20*u^2-4*u^3;if fv>fuif b-v<=rufubreak;elsea=v;v=u;u=a+0.618*(b-a);endelseif u-a<=rv-fvbreak;elseb=u;u=v;v=a+0.382*(b-a);endk=k+1endend4.2 函数曲线图程序如下:如下曲线所得y值为负,前面(1*)已作解释。
机械优化设计数学模型
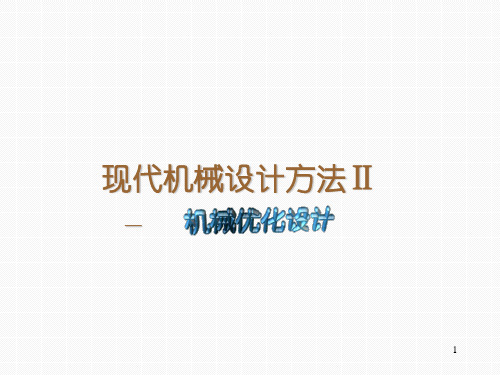
10
1.2优化设计的数学模型
1.2.1机械设计中优知: P=1000 N M=100 N-m [f ]=0.01 cm [ w ] 120 MPa [ ] 80 MPa
E 2 105 MPa
圆形销轴 P
d
M
l
11
7.8 t
m
3
, 轴长不小于 8cm
设计变量可用一个列阵来表示,如:上节中 例1.的设计变量可表示为:
x1 d X [ x1 , x 2 ]T x 2 l ①设计变量的一般表达式
x1 x X 2 [ x1 , x 2 x n ]T xn
设计变量(代表某一设计方案)→ “ 设计矢量”
22
“设计方案→设计矢量→设计点”一一对应的
④设计空间
— 设计点的集合(由各设计变量的坐标轴 所描述的空间)
工程中的设计空间属于 实欧氏空间
R n — n维实欧氏空间
23
当矢量X中的各个分量 xi (i 1,2n)都是实数 决定了 n X R 中的一个点 变量时, 用集合概 念可写成:
H 2 [ H 2 ]
1 40796 2 2 620 m Z1 b
㈢ 不根切条件:
Z1 17
b 1.2 ㈣ 齿宽系数的要求: d m Z1
综上,这是一个在满足㈠、㈡、㈢、㈣式的 条件下,合理选择Z1和m、b,使直齿圆柱齿轮副
体积最小的问题
18
总 结:
一个机械优化问题包含的内容: ①追求的设计目标 → “目标函数” ②需求解的一组独立参数 →“设计变量” ③设计变量必须满足若干限制条件 →“设计约束”
绪 论
数学建模_零件参数的优化设计说明

零件参数的优化设计摘要本文建立了一个非线性多变量优化模型。
已知粒子分离器的参数y由零件参数兀(, = 1,2…7)决定,参数儿的容差等级决定了产品的成本。
总费用就包括y偏离y。
造成的损失和零件成本。
问题是要寻找零件的标定值和容差等级的最佳搭配,使得批量生产中总费用最小。
我们将问题的解决分成了两个步骤:1.预先给定容差等级组合,在确定容差等级的情况下,寻找最佳标定值。
2.采用穷举法遍历所有容差等级组合,寻找最佳组合,使得在某个标定值下,总费用最小。
在第二步中,由于容差等级组合固定为108种,所以只要在第一步的基础上,遍历所有容差等级组合即可。
但是,这就要求,在第一步的求解中,需要一个最佳的模型使得求解效率尽可能的要高,只有这样才能尽量节省计算时间。
经过对模型以及mat lab代码的综合优化»最终程序运行时间仅为3. 995秒。
最终计算出的各个零件的标定值为:^=(0. 0750, 0. 3750, 0.1250, 0.1200,1. 2919,15. 9904, 0. 5625},等级为:d = B,B,B,C,C,B,B一台粒子分离器的总费用为:421.7878元与原结果相比鮫,总费用由3074. 8 (元/个)降低到421.7878 (元/个),降幅为86.28%,结果是令人满意的。
为了检验结果的正确性,我们用计算机产生随机数的方式对模型的最优解进行模拟检验,模拟结果与模型求解的结果基本吻合。
最后,我们还对模型进行了误差分析,给出了改进方向,使得模型更容易推广。
关键字:零件参数 非线性规划 期望 方差一、问题重述一件产品由若干零件组装而成,标志产品性能的某个参数取决于这些零件的 参数。
零件参数包括标定值和容差两部分。
进行成批生产时,标定值表示一批零 件该参数的平均值,容差则给出了参数偏离其标定值的容许围。
若将零件参数视 为随机变量,则标定值代表期望值,在生产部门无特殊要求时,容差通常规定为 均方差的3倍。
- 1、下载文档前请自行甄别文档内容的完整性,平台不提供额外的编辑、内容补充、找答案等附加服务。
- 2、"仅部分预览"的文档,不可在线预览部分如存在完整性等问题,可反馈申请退款(可完整预览的文档不适用该条件!)。
- 3、如文档侵犯您的权益,请联系客服反馈,我们会尽快为您处理(人工客服工作时间:9:00-18:30)。
数学建模零件参数的优化设计IMB standardization office【IMB 5AB- IMBK 08- IMB 2C】零件参数的优化设计摘要本文建立了一个非线性多变量优化模型。
已知粒子分离器的参数y由零件参数)72,1 (=ixi 决定,参数ix的容差等级决定了产品的成本。
总费用就包括y偏离y0造成的损失和零件成本。
问题是要寻找零件的标定值和容差等级的最佳搭配,使得批量生产中总费用最小。
我们将问题的解决分成了两个步骤:1.预先给定容差等级组合,在确定容差等级的情况下,寻找最佳标定值。
2.采用穷举法遍历所有容差等级组合,寻找最佳组合,使得在某个标定值下,总费用最小。
在第二步中,由于容差等级组合固定为108种,所以只要在第一步的基础上,遍历所有容差等级组合即可。
但是,这就要求,在第一步的求解中,需要一个最佳的模型使得求解效率尽可能的要高,只有这样才能尽量节省计算时间。
经过对模型以及matlab代码的综合优化,最终程序运行时间仅为秒。
最终计算出的各个零件的标定值为:ix={,,,,,,},等级为:BBCCBBBd,,,,,,=一台粒子分离器的总费用为:元与原结果相比较,总费用由(元/个)降低到(元/个),降幅为%,结果是令人满意的。
为了检验结果的正确性,我们用计算机产生随机数的方式对模型的最优解进行模拟检验,模拟结果与模型求解的结果基本吻合。
最后,我们还对模型进行了误差分析,给出了改进方向,使得模型更容易推广。
关键字:零件参数非线性规划期望方差一、问题重述一件产品由若干零件组装而成,标志产品性能的某个参数取决于这些零件的参数。
零件参数包括标定值和容差两部分。
进行成批生产时,标定值表示一批零件该参数的平均值,容差则给出了参数偏离其标定值的容许范围。
若将零件参数视为随机变量,则标定值代表期望值,在生产部门无特殊要求时,容差通常规定为均方差的3倍。
进行零件参数设计,就是要确定其标定值和容差。
这时要考虑两方面因素:一是当各零件组装成产品时,如果产品参数偏离预先设定的目标值,就会造成质量损失,偏离越大,损失越大;二是零件容差的大小决定了其制造成本,容差设计得越小,成本越高。
试通过如下的具体问题给出一般的零件参数设计方法。
粒子分离器某参数(记作y )由7个零件的参数(记作x 1,x 2,...,x 7)决定,经验公式为:y 的目标值(记作y 0)为。
当y 偏离y 0+时,产品为次品,质量损失为1,000元;当y 偏离y 0+时,产品为废品,损失为9,000元。
零件参数的标定值有一定的容许范围;容差分为A、B、C三个等级,用与标定值的相对值表示,A等为+1%,B等为+5%,C等为+10%。
7个零件参数标定值的容许范围,及不同容差等级零件的成本(元)如下表(符号/表示无此等级零件):现进行成批生产,每批产量1,000个。
在原设计中,7个零件参数的标定值为:x 1=,x 2=,x 3=,x 4=,x 5=,x 6=16,x 7=;容差均取最便宜的等级。
请你综合考虑y 偏离y 0造成的损失和零件成本,重新设计零件参数(包括标定值和容差),并与原设计比较,总费用降低了多少?二、模型假设1、将各零件参数视为随机变量,且各自服从正态分布;2、假设组成离子分离器的各零件互不影响,即各零件参数互相独立;3、假设小概率事件不可能发生,即认为各零件参数只可能出现在容许范围内;4、在大批量生产过程中,整批零件都处于同一等级,。
本题可认为1000各零件都为A 等、B 等或C 等;5、生产过程中出质量损失外无其他形式的损失;6、在质量损失计算过程中,认为所有函数都是连续可导的。
三、符号说明i x :第i 类零件参数的标定值(i=1,2……7);i x ∆:第i 类零件参数的实际值相对目标值的偏差(i=1,2……7);i r :第i 类零件参数的容差(i=1,2,……7);i σ:第i 类零件参数的方差(i=1,2,……7);i i b a ,:标定值i x 的上、下限;y :离子分离器某参数的实际值;y:离子分离器该参数的目标值;y:离子分离器某参数的均值;y∆:离子分离器某参数的实际值y相对平均值y的偏差;σ:离子分离器某参数的方差;yP:一批产品中正品的概率;1P:一批产品中次品的概率;2P:一批产品中废品的概率;3W:一批产品的总费用(包括损失和成本费);C:第i类零件对应容差等级为j的成本(j=A,B,C)单位:元/个。
ij四、问题分析布,联想正态分布的性质——当各变量均服从正态分布时,其线性组合也服从正态分布。
题中所给经验公式为一复杂的非线性的公式,无法直接对其分析处理,所以需借助泰勒公式将其展开并作相应处理使其线性化。
而对于零件成本,需先确定容差等级才能求得成本费。
由容差等级和各类零件的标定值i x 便可知道给类零件的容差i r 。
最后,便将问题转化为i x 、i r 关于总目标函数的最优解的问题上。
在进行零件参数设计时,如果零件设计不妥,造成产品参数偏离预先设定值,就会造成质量损失,且偏差越大,损失也越大;零件容差的大小决定了其制造成本,容差设计得越小(即精度越高)零件成本越高。
合理的设计方案应既省费用又能满足产品的预先设定值,设计方向应该如下:(1)设计的零件参数,要保证由零件组装成的产品参数符合该产品的预先设定值,即使有偏离也应是在满足设计最优下的容许范围。
(2)零件参数(包括标定值和容差等级)的设计应使总费用最小为优。
此外分析零件的成本及产品的质量损失不难发现,质量损失对费用的影响远大于零件成本对费用的影响,因而设计零件参数时,主要考虑提高产品质量来达到减少费用的目的。
五、模型建立为了确定原设计中标定值(x i i (,,,)=127 的期望值)及已给的容差对产品性能参数影响而导致的总损失W ,即确定y 偏离目标值y 0所造成的损失和零件成本,先列出总损失的数学模型表达如下:当然,为了确定总损失W ,必须知道1P 、2P 、3P (即正品、次品及废品的概率)。
为此,将经验公式用泰勒公式在)72,1( ==i x X i 处展开并略去二次以上高次项后来研究y 的概率分布,设y x f =)(,则将标定值)72,1( =i x i 带入经验公式即得 所以 i i ix x fy y y ∆∂∂=-=∆∑=71 由于在加工零件时,在标定值知道的情况下,加工误差服从正态分布,即 且i x ∆相互独立,由正态分布性质可知 由误差传递公式得 22712712)()()(i i i i ii i i yx x x f x f σσσ∑∑==∂∂=∂∂= (1)由于容差为均方差的3倍,容差与标定值的比值为容差等级,则 y 的分布密度函数为y 偏离1.00±y 的概率,即次品的概率为⎰⎰+=8.16.14.12.12)()()()(y d y y d y P ϕϕ (2)y 偏离3.00±y 的概率,即废品的概率为⎰⎰+∞∞-+=8.12.13)()()()(y d y y d y P ϕϕ (3)由于y 偏离0y 越远,损失越大,所以在y σ固定时,调整y 使之等于目标值0y 可降低损失。
取0y y y -=∆即0y y =,则)(t φ为标准正态分布函数。
综合考虑y 偏离y 0造成的损失和零件成本,设计最优零件参数的模型建立如下: 目标函数min )90001000(10003271P P C W i ij ++⨯=∑=. )72,1( =≤≤i a x b ii i六、模型求解初略分析对于原给定的设计方案,利用matlab编程计算(见附录),计算结果如下:由于按原设计方案设计的产品正品率过低,损失费过高,显然设计不够合理。
进y=太远,致使损失过大。
尽管原设计方案保一步分析发现,参数均值y=偏离目标值证了正本最低,但由于零件参数的精度过低,导致正品率也过低。
所以我们应综合考虑成本费和损失费。
模型的实现过程:本模型通过matlab进行求解,我们通过理论模型求解和随机模拟的求解过程如下:在给定容差等级的情况下,利用matlab中求解非线性规划的函数fmincon,通过多次迭代求解,最终求得一组最优解。
最初,我们设定的fmincon函数的目标函数就是总费用,约束条件为各个标定值的容许范围,以及各零件标定值带入产品参数表达y,即。
然而,在迭代过程中我们发现,求解过程十分慢,在给定容差等级的式应为确定的情况下,计算最优标定值需要将近400秒,如果在此基础上对108种容错等级进行穷举查找最优组合,将需要大概12小时。
显然这是不合理的。
因此,我们在仔细对matlab实现代码研究发现,求解过程之所以慢,是因为代码中存在多次调用求偏导和积分的函数,在fmincon的多次迭代中,耗费大量时间。
所以,为了提高求解速度,我们首先利用matlab中diff函数对产品参数中的各个表达式进行求偏导,然后得到多个带参表达式,利用int函数对y的概率密度函数进行积分,分别得到出现次品和废品概率的表达式,然后将这些表达式写进程序里,这样在求解过程中就不需要在每一次迭代中都要求偏导和积分了,修改后的程序运行时间大大减少。
程序流程图模型检验对设计方案进行动态模拟,由于每种零件参数均服从正态分布,用正态分布随机数发生器在每种零件参数允许范围内产生1000个随机数参与真实值i x 的计算随机模拟N 次后结果如下:根据最优解的y =,y σ=画出y 的概率分布图,再对x 随机取样画出y 的概率分布图(见图),由图可知:两组数据所画概率分布图的拟合度相当高,进一步确保了模型的正确性。
图概率分布图对比图通过以上数据,与原设计方案所得结果相比较,总费用由(元/个)降低到(元/个),降幅为%,结果是令人满意的。
七、误差分析1、在建模过程中,通过泰勒公式将)(X f y =展开并略去二次及以上项使线性化,不可避免地产生了截断误差,所以展开后的式子只是原经验公式的近似关系式。
但在一般情况下,线性化和求总和在实用上具有足够的精度,所以由于函数线性化而略去的高次项可以忽略不计。
在函数关系式较复杂的情况下,将其线性化更具有明显的优势。
2、本模型忽略了小概率事件发生的可能,认为零件的参数只可能出现在允 范围内,即[]i i i i x x σσ3,3+-。
现实中,小概率事件仍有发生的可能性,但在大批量生产中,小概率事件的发生对最终结果没有影响,所以可以忽略。
3、该模型对于质量损失的计算,将所有函数都看作连续函数,而这对于每 个零件参数而言是不可能的,所以其中也会产生误差。
八、模型的评价及推广1.优点(1)建模过程中,采用泰勒公式将经验公式简化,并假设各零件参数都服从满足大量数据的正态分布,使得整个模型的建立及求解得到大大简化。