设备管理--设备管理的发展过程与趋势
设备管理设备管理的发展过程与趋势
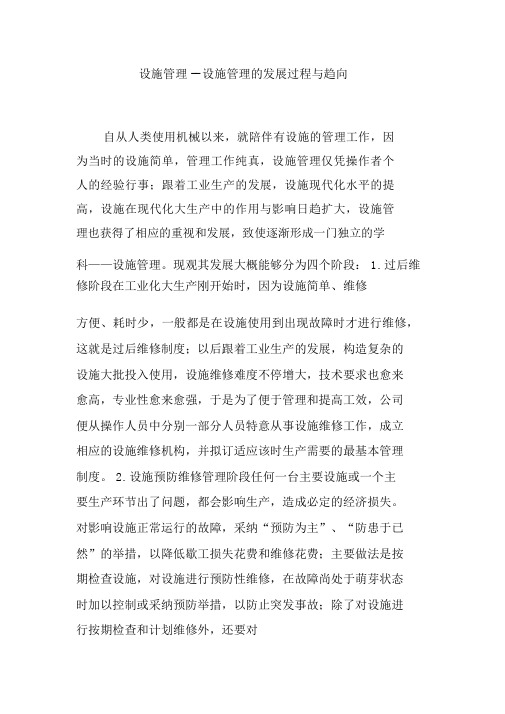
设施管理 -- 设施管理的发展过程与趋向自从人类使用机械以来,就陪伴有设施的管理工作,因为当时的设施简单,管理工作纯真,设施管理仅凭操作者个人的经验行事;跟着工业生产的发展,设施现代化水平的提高,设施在现代化大生产中的作用与影响日趋扩大,设施管理也获得了相应的重视和发展,致使逐渐形成一门独立的学科——设施管理。
现观其发展大概能够分为四个阶段: 1. 过后维修阶段在工业化大生产刚开始时,因为设施简单、维修方便、耗时少,一般都是在设施使用到出现故障时才进行维修,这就是过后维修制度;以后跟着工业生产的发展,构造复杂的设施大批投入使用,设施维修难度不停增大,技术要求也愈来愈高,专业性愈来愈强,于是为了便于管理和提高工效,公司便从操作人员中分别一部分人员特意从事设施维修工作,成立相应的设施维修机构,并拟订适应该时生产需要的最基本管理制度。
2. 设施预防维修管理阶段任何一台主要设施或一个主要生产环节出了问题,都会影响生产,造成必定的经济损失。
对影响设施正常运行的故障,采纳“预防为主”、“防患于已然”的举措,以降低歇工损失花费和维修花费;主要做法是按期检查设施,对设施进行预防性维修,在故障尚处于萌芽状态时加以控制或采纳预防举措,以防止突发事故;除了对设施进行按期检查和计划维修外,还要对设施进行平时的维修;预防维修比过后维修有显然的优胜性;早先拟订设施的检修计划,采纳预防为主的维修举措,可减少设施恶性事故的发生和歇工损失,延伸设施的使用寿命,提高设施的完满率,有益于保证产品的产量和质量。
经过多年实践,在“以我为主,博采众长”精神的指导下,对引进设施的计划预修制度进行了研究和改良,探索出拥有我国特点的计划预修制度,其主要特点是:采纳项目维修往常设施有养护、小修、中修和大修几个环节,但我国许多公司采纳项目维修取代设施中修,或许采纳几次项目维修取代设计备大修,使维修作业量更平衡,节俭了维修工时。
划预修与过后维修相联合对生产中所处地位比较重要的设备推行计划预修,而对一般设施推行过后维修或按设施使用状况进行维修,使计划预修与过后维修相联合。
设备管理的发展阶段及趋势

设备管理的发展阶段及趋势1.设备管理的发展阶段在工业革命之前,人们借助简单的工具进行生产,生产规模小,技术水平低,操作工兼做修理工,谈不上设备的维修与管理。
随着工业生产的发展和现代设备的出现,设备管理才逐步形成了比较系统、完备的管理理论和管理模式。
设备管理的发展大体经历了以下4个不同的阶段。
1)事后维修阶段事后维修又称“坏了再修”,是指机器设备在生产过程中发生故障或损坏之后才进行维修。
事后维修能够最大限度地利用设备的零部件,提高了零部件使用的经济性,常用于修理结构简单、易于修复、利用率很低以及发生故障停机后对生产无影响或影响很小的设备。
2)预防维修阶段事后维修使故障停机时间过长而无法保证设备的正常使用。
尤其是社会化大生产和流水线的出现使设备故障对生产的影响越来越大,任何一台主要设备或主要生产环节出现故障都会造成巨大的损失,特别是在流程式生产的企业中,突发性故障造成的直接及间接损失更是难以估量。
在这种条件下,出现了为防止突发故障而对设备进行预先修理的“预防性”修理模式,即预防维修模式。
预防维修制有两大体系,分别是苏联的“计划预修制”及美国的“预防维修制”。
(1)计划预修制为了防止生产设备的意外故障,应按照预定的计划进行一系列预防性修理。
其目的是保障设备正常运行和保持良好的生产能力,减少和避免设备因不正常的磨损、老化和腐蚀而造成的损坏,延长设备使用寿命,充分发挥其潜力。
计划预修制规定:设备在经过规定的运行时间以后,要进行预防性的定期检查、调整和各类计划修理。
计划预修制中,各类不同设备的保养、修理周期、周期结构和间隔是确定的。
在这个规定的基础上,组织实施预防性的定期检查、保养和修理。
计划预修制是以设备的磨损规律为基础制订的。
按照计划预修制的理论,影响设备修理工作量的主要因素是设备的开动台时,合理的开动台时是预防性维修的依据。
(2)预防维修制预防维修制以设备的日常检查和定期检查为基础并据此确定修理内容、方式和时间,由于没有严格规定的修理周期,因而有较大的灵活性。
设备管理状况及发展趋势

设备管理状况及发展趋势一、设备管理已形成新格局“企业自主管理,社会中介服务,政府依法监督”是我国市场经济国家经贸委设备管理的职能、机构和人员。
政府将依法对国有资产流失、设备的安全、节能、环保等方面进行监督。
对违法者要追究行政、经济责任和刑事责任。
通过近10年的过渡,企业对设备工作已主动管理起来,管、用、养、修全面负责。
天津大沽化工厂生产副厂长汤吉彦在中国机械工程学会设备与维修工程分会组织的设备管理调研会上说:“我主管生产,先抓设备。
设备维护良好,生产的产品数量、质量就有保证,产值、成本、利润就能完成。
不抓设备、不保养、不维修、不改造,设备陈旧落后,经常停机影响生产,安全也没保证。
因此,要积极努力地抓设备基础管理、现场管理、维修保养、定期检修、技术改造,使设备确保生产。
”近年来,该厂产品质量和产量逐年提高,总资产上升到几十个亿,负责率大幅下降,企业蒸蒸日上。
最近又获11亿元技改国贷资金,有望5年产值再翻一翻,达到百亿。
这是企业自主管理设备取得的成果。
社会中介服务不断发展,各行业、各地方的设备管理经验交流、学术交流、资产评估、设备监理、工程技术人员的在岗培训和再教育、工程技术人员的技术职称评定、闲置设备和备件的调剂、维修服务、维修市场建立与发展、技术咨询和服务工作等,尽管还不能完全满足市场需要,但学会、协会和其他社会中介机构都积极做这些工作。
社会中介服务好的地区,很多企业已不在内部配备维修管理人员和维修队伍,依靠社会力量维修。
二、企业领导重视设备管理、改造和更新工作企业自主管理后,凡是生产好、效益好的企业都十分重视设备管理。
相反,生产不饱满,产品没市场或占市场份额小或近乎破产的企业一般设备管理也差。
首钢副总工程师和机动部长在设备与维修工程分会调研会上说:“首钢生产依靠炼焦设备、炼铁设备、炼钢设备和轧钢设备,生产要上去,设备必须完好。
累些,首钢设备系统组织健全、岗位责任明确,并不断引进高新技术。
过去炼铁高炉大功率风机常有突发故障,首钢领导和机动部常常现场指挥抢修,缩短停机时间,减少生产损失。
设备管理的现状与发展趋势

设备管理的现状与发展趋势引言在现代社会中,设备管理是各行各业中不可或缺的一项工作。
它包括对物理设备(如计算机、服务器、网络设备等)进行管理、监控和维护,以确保设备的正常运行和高效性能。
随着技术的不断发展和企业规模的扩大,设备管理也面临着新的挑战和发展趋势。
本文将探讨设备管理在现状和未来的发展趋势。
现状目前,许多企业都采用专门的设备管理系统来管理自己的设备,以提高设备的利用率和降低运营成本。
这些系统通常包括以下功能:1.资产管理:跟踪和记录企业拥有的设备,包括型号、序列号、购买日期等信息,以便更好地管理设备的生命周期和维护计划。
2.配置管理:记录设备的配置信息,包括操作系统、软件版本、网络设置等,以便进行快速修复和升级。
3.监控与警报:实时监控设备的状态和性能指标,如CPU使用率、内存利用率等,并通过警报通知管理员进行及时处理。
4.维修和保养:记录设备的维修记录和保养计划,以确保设备的正常运行和延长使用寿命。
然而,当前的设备管理仍存在一些挑战。
首先,设备数量庞大,难以手动管理和监控每一台设备。
其次,设备种类繁多,不同设备的配置和管理方法各异,需要专业知识和经验。
此外,大规模的设备管理还需要强大的计算和存储能力,对网络和服务器的要求较高。
发展趋势随着技术的不断进步,设备管理也在不断发展和改进。
以下是设备管理未来的发展趋势:1.自动化和智能化:通过引入自动化和智能化技术,设备管理可以更高效、准确地实现。
例如,基于人工智能和机器学习的设备管理系统可以自动分析设备数据,提供预测性维护和故障预警,优化设备配置和网络优化等。
2.云端管理:将设备管理系统部署在云端,可以实现设备管理的远程访问和集中管理。
管理员可以通过网络随时随地监控和管理设备,极大地提高了管理的灵活性和便捷性。
3.虚拟化和容器化:利用虚拟化和容器化技术,可以将物理设备抽象成为虚拟设备或容器,统一管理和分配资源。
这样可以更好地利用设备的计算和存储能力,减少资源浪费和管理复杂度。
设备管理的发展史

Break down 事后维修
1950年 1960年
1970年 1980年 1990年
为什么要强调全员?
拆掉这堵 隔离墙!
操作人员天天接 触设备,了解设 备一举一动,但 不对设备负责;
出 现
了 信
息
隔
绝
维修人员不 在设 备旁边,但需要设 备细微信息;
突出变化:把“全员参与设备管理”的理念落地
第一讲 设备管理的发展历程
2
1.1 生产管理和质量管理模式的发展背景 生产管理的发展历史
精益生产 (Lean Production)
80年代后--
丰田的生产方式 (TPS-Toyota Production System)
70年代--
通用的生产管理方式 (多品种-规模)
福特的大量生产方式 3S-标准化/简单化/专门化
CBM:Condition Based Maintenance PdM:Predictive Maintenance
基于状态的预防维修 (预知维修,状态维修)
6
生产维修阶段(PM,第三代)
事后维修
(BM,breakdown maintenance)
生 产
一为是 种生以 维产生
维
修服产
修
体务为 制的中
全员参与的生产维护体系
现场自主管理
生产维修(专业PM)
清洁
点检 保养 自主维修
润滑
预防 维修 (PvM)
事后 维修
纠正性 维
(PvM,preventive maintenance)
纠正维修 (CM,corrective maintenance)
维修预防
设备管理的技术趋势和发展方向
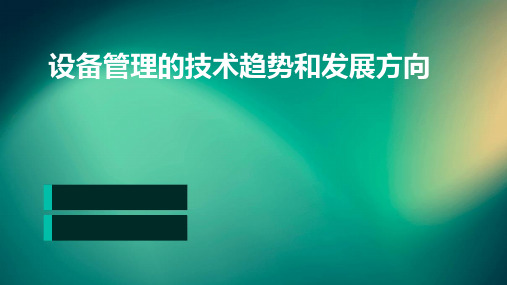
高可用性和可恢复性
03
云计算技术可以提供高可用性和可恢复性的设备管理服务,保
证设备管理的稳定性和可靠性。
大数据分析在设备管理中的应用
数据挖掘和分析
通过大数据技术,对设备运行数据进行分析和挖掘,发现设备的 运行规律和潜在问题。
优化决策
基于大数据分析结果,优化设备管理决策,提高设备管理效率。
预测性维护
03 设备管理发展方向
智能化设备管理
智能化设备管理是指利用先进的信息技术和人工智能技术,实现设备的自动化、 智能化管理。通过实时监测设备的运行状态、预测设备故障、优化设备运行效率 等功能,提高设备的管理效率和可靠性,降低设备的维护成本和故障率。
智能化设备管理的发展方向包括:利用物联网技术实现设备的远程监控和数据采 集、利用大数据和云计算技术对设备运行数据进行处理和分析、利用机器学习和 人工智能技术实现设备的故障预测和智能维护等。
设备管理的技术趋势和发展方向
目 录
• 设备管理概述 • 设备管理技术趋势 • 设备管理发展方向 • 设备管理面临的挑战和解决方案 • 设备管理未来展望
01 设备管理概述
设备管理的定义和重要性
设备管理定义
设备管理是对企业生产经营所需的各 类设备进行科学管理,确保设备高效 、安全、经济地运行。
设备管理的重要性
05 设备管理未来展望
5G技术在设备管理中的应用前景
5G技术将为设备管理提供更高 效、更实时的数据传输和处理 能力,支持远程监控和控制。
5G技术将促进设备之间的互联 互通,实现更智能化的协同工 作。
5G技术将提升设备故障预警和 诊断的准确性和及时性,降低 维护成本。
区块链技术在设备管理中的应用前景
预测性维护
设备管理--设备管理的发展过程与趋势

设备管理--设备管理的发展过程与趋势自从人类使用机械以来,就伴随有设备的管理工作,由于当时的设备简单,管理工作单纯,设备管理仅凭操作者个人的经验行事;随着工业生产的发展,设备现代化水平的提高,设备在现代化大生产中的作用与影响日益扩大,设备管理也得到了相应的重视和发展,以致逐步形成一门独立的学科——设备管理。
现观其发展大致可以分为四个阶段:1.事后维修阶段在工业化大生产刚开始时,由于设备简单、修理方便、耗时少,一般都是在设备使用到出现故障时才进行修理,这就是事后维修制度;后来随着工业生产的发展,结构复杂的设备大量投入使用,设备修理难度不断增大,技术要求也越来越高,专业性越来越强,于是为了便于管理和提高工效,企业便从操作人员中分离一部分人员专门从事设备修理工作,建立相应的设备维修机构,并制定适应当时生产需要的最基本管理制度。
2.设备预防维修管理阶段任何一台主要设备或一个主要生产环节出了问题,都会影响生产,造成一定的经济损失。
对影响设备正常运行的故障,采取“预防为主”、“防患于未然”的措施,以降低停工损失费用和维修费用;主要做法是定期检查设备,对设备进行预防性维修,在故障尚处于萌芽状态时加以控制或采取预防措施,以避免突发事故;除了对设备进行定期检查和计划修理外,还要对设备进行日常的维修;预防维修比事后修理有明显的优越性;预先制定设备的检修计划,采取预防为主的维修措施,可减少设备恶性事故的发生和停工损失,延长设备的使用寿命,提高设备的完好率,有利于保证产品的产量和质量。
经过多年实践,在“以我为主,博采众长”精神的指导下,对引进设备的计划预修制度进行了研究和改进,摸索出具有我国特色的计划预修制度,其主要特点是:2.1采用项目修理通常设备有保养、小修、中修和大修几个环节,但我国不少企业采用项目修理代替设备中修,或者采用几次项目修理代替设备大修,使修理作业量更均衡,节省了修理工时。
2.2计划预修与事后修理相结合对生产中所处地位比较重要的设备实行计划预修,而对一般设备实行事后修理或按设备使用状况进行修理,使计划预修与事后修理相结合。
设备运行管理现状分析与发展趋势

日期
电机 总台数
100KW及以上电机
计划 预知 事后 检修 检修 检修
一般低压电机
计划 预知 事后 检修 检修 检修
检修 总台数
电机 维修率
2012年 995 10 4 3 27 44 13 101 10.15%
2013年 1000 3
2
2
7 43 12
69
6.90%
4、设备检修费用管理
费用支出:检修费用主要由维护费和修理费构成,修理费按月检修计划、大检 修计划及临时计划项目的执行来控制。 费用指标:根据吨油加工成本,根据上一年生产情况及下一年检修计划安排, 向总部申请检修费用,总部平衡后,下达检修费用指标,分解到各单位。
专项工作 检查数量 查出问题 已整改 整改率
细小部位
18885 1339 1317 98%
不锈钢螺栓 151824 2836 2836 100%
电动机接线盒 6972 108 105 97.20%
仪表电磁阀
5406 158 158 100%
•机组状态检测技术的运用
2、设备维护管理
2013年控制检费用的举措.doc
二、当前设备管理中的一些变化
4、装置运行周期越来越长 随着技术进去, 炼油装置2年一大修,3年一大
修,4年一大修的越来越多,装置的长周期运行要求 对设备的可靠性要求越来越高。 5、环保要求越来越高,检修要求零排放零污染。
二、当前设备管理中的一些变化
6、低成本战略加工高硫原油,带来的设备腐蚀的问 题越来越严重
2、设备维护管理:
设备维保专业化外包情况
开展DCS(PLC)厂家系统集中运保, 运保范围涵盖HONEYWELL、 FOXBORO 、 YOKGAWA 、 YAMATAKE 、 西 门 子 5 家 产 品 , 约 185 套 DCS(PLC)系统,全年累计开展巡检860余套/次,完成系统点检64 套,更换卡板等各类备件约157件,故障维护211次,协助各单位完成 组态修改等工作160余次,完成系统培训68人/次。目前集中运保数量 占全厂系统总数约57.27%。
- 1、下载文档前请自行甄别文档内容的完整性,平台不提供额外的编辑、内容补充、找答案等附加服务。
- 2、"仅部分预览"的文档,不可在线预览部分如存在完整性等问题,可反馈申请退款(可完整预览的文档不适用该条件!)。
- 3、如文档侵犯您的权益,请联系客服反馈,我们会尽快为您处理(人工客服工作时间:9:00-18:30)。
设备管理--设备管理的发展过程与趋势自从人类使用机械以来,就伴随有设备的管理工作,由于当时的设备简单,管理工作单纯,设备管理仅凭操作者个人的经验行事;随着工业生产的发展,设备现代化水平的提高,设备在现代化大生产中的作用与影响日益扩大,设备管理也得到了相应的重视和发展,以致逐步形成一门独立的学科——设备管理。
现观其发展大致可以分为四个阶段:1.事后维修阶段在工业化大生产刚开始时,由于设备简单、修理方便、耗时少,一般都是在设备使用到出现故障时才进行修理,这就是事后维修制度;后来随着工业生产的发展,结构复杂的设备大量投入使用,设备修理难度不断增大,技术要求也越来越高,专业性越来越强,于是为了便于管理和提高工效,企业便从操作人员中分离一部分人员专门从事设备修理工作,建立相应的设备维修机构,并制定适应当时生产需要的最基本管理制度。
2.设备预防维修管理阶段任何一台主要设备或一个主要生产环节出了问题,都会影响生产,造成一定的经济损失。
对影响设备正常运行的故障,采取“预防为主”、“防患于未然”的措施,以降低停工损失费用和维修费用;主要做法是定期检查设备,对设备进行预防性维修,在故障尚处于萌芽状态时加以控制或采取预防措施,以避免突发事故;除了对设备进行定期检查和计划修理外,还要对设备进行日常的维修;预防维修比事后修理有明显的优越性;预先制定设备的检修计划,采取预防为主的维修措施,可减少设备恶性事故的发生和停工损失,延长设备的使用寿命,提高设备的完好率,有利于保证产品的产量和质量。
经过多年实践,在“以我为主,博采众长”精神的指导下,对引进设备的计划预修制度进行了研究和改进,摸索出具有我国特色的计划预修制度,其主要特点是:2.1采用项目修理通常设备有保养、小修、中修和大修几个环节,但我国不少企业采用项目修理代替设备中修,或者采用几次项目修理代替设备大修,使修理作业量更均衡,节省了修理工时。
2.2计划预修与事后修理相结合对生产中所处地位比较重要的设备实行计划预修,而对一般设备实行事后修理或按设备使用状况进行修理,使计划预修与事后修理相结合。
2.3合理确定修理周期设备的检修周期不是根据磨损情况,而是根据主要设备的具体情况来定。
如按设备的设计水平、制造和安装质量、役龄和使用条件、使用强度等情况确定其修理周期,使修理周期和结构更符合实际情况及更加合理。
2.4修理与改造相结合我国多数企业往往结合设备修理对原设备进行局部改进或改装,使大修与设备改造结合起来延长设备的使用寿命。
2.5设备保养维护与检修结合企业在计划预修的基础上吸收三级保养,创立了一种新的设备维修管理制度——计划保修制。
其根据设备的结构特点和使用情况的不同,定时或定运行里程对设备施行规格不同的保养,并以此为基础制定设备的维修周期,这种制度突出了维护保养在设备管理与维修工作中的地位,充分调动操作人员管好设备的积极性,使设备管理工作建立在广泛的基础之上。
3.设备系统管理阶段随着科学技术的发展及系统理论的普遍应用,对关键设备采取重点维护政策,以提高企业的综合经济效益,主要内容有:3.1修理费用高的偶发性故障且零部件更换困难的,运用状态监测方法,根据实际需要随时维修。
3.2修理费用低的寿命型故障,且零部件易于更换的,采用定期更换策略。
3.3修理费用十分昂贵的零部件,应考虑无维修设计,消除故障根源,避免发生故障。
4.设备综合管理阶段设备综合管理思想的两个典型代表是“设备综合工程学”和“全员生产维修制”。
“设备综合工程学”是以设备寿命周期费用最经济为管理目标,对设备进行综合管理围绕四方面展开: 4.1企业管好、用好、修好、经营好机器设备对同等技术的设备进行价格、运转、维修费用、折旧、经济寿命等方面的计算和比较,把好经济效益关,建立和健全合理的管理体制。
4.2设备的可靠性与维修性无论是新设备还是老设备,都必须重视设备的可靠性和维修性问题,提高可靠性和维修性,减少故障和维修作业时间,达到提高设备有效利用率。
4.3设备的一生为研究和管理对象及运用系统工程观点,把设备的规划、设计制造、安装调试、使用维修、改造、折旧报废的全过程作为设备一生的研究和管理对象。
4.4设备工作循环过程的信息反馈设备使用部门要把有关设备的运行记录和长期经验积累所发现的缺陷提供给维修部门和设备制造厂家,以便他们综合掌握设备的技术状况,进行必要的改造或在新设备设计时进行改进。
“全系统”是指对设备寿命周期实行全过程管理,从设计阶段起就要对设备的维修方法和手段予以认真考虑,既抓设备前期阶段的先天不足又抓使用维修和改造阶段的故障分析,达到排除故障的目的。
“全员参加”,是指上至企业最高领导下到每位操作人员都参加生产维修活动。
在设备综合管理阶段,设备维修的方针是:建立以操作工点检为基础的设备维修制;实行重点设备专门管理,避免过剩维修;定期检测设备的精度指标;注意维修记录和资料的统计及分析。
综合管理是设备管理现代化的重要标志。
实行设备目标管理,重视设备可靠性、维修性研究,加强设备投产前的前期管理和使用中的信息反馈,提高设备管理的综合经济效益。
5.企业设备管理方案探讨随着经济全球化以及工业化和信息化的发展,机械制造、自动控制、可靠性工程及管理科学出现了新的突破,现代设备的科学管理呈现了新的趋势,不再是狭义上的设备技术的管理,而是更广义的生产力的管理,把握这一新趋势,对于促进企业设备管理的现代化和科学化具有重要的现实意义。
5.1设备管理已形成新格局企业设备管理已形成新格局,企业自主管理和政府依法监督是我国市场经济新形势下设备管理新格局。
企业对设备工作已主动管理起来,管、用、养、修全面负责。
对于设备管理强调:“主管生产,先抓设备。
设备维护良好,生产的产品数量、质量就有保证,产值、成本、利润就能完成。
不抓设备,不保养、不维修,不改造,设备陈旧落后,经常停机影响生产,安全也没保证。
因此,要积极努力地抓设备基础管理、现场管理、维修保养、定期检修、技术改造,使设备确保生产。
5.2企业领导重视设备管理、改造和更新工作企业自主管理后,凡是生产和效益好的企业都十分重视设备管理。
但很多企业已不在内部配备维修管理人员和维修队伍,依靠社会力量来维修设备。
凡是生产好、效益好的企业都十分重视设备管理;相反生产不饱满,产品没市场或占市场份额小或近乎破产的企业一般设备管理也差;生产要上去,设备必须完好,因此不断进引高新技术,缩短停机时间,减少生产损失,对关键设备实行监控;很多企业领导已认识到企业资本的50%以上是设备资产,设备不能发挥应有效能,等于资本积压,同时认识到设备在某种程度上决定着现代生产,关系到产品品种、产量、质量、安全、消耗、成本等,关系到企业效益和职工切身利益。
企业重视设备管理,对设备管理和技术人员实行岗位责任制,并经常进行岗位培训,提倡综合管理和主动维护,使设备管理不断创新,这是企业自主管理设备取得的成果。
设备管理的经验可以归纳为:设备管理和维修工作目标明确,为企业经济效益服务,实行优胜劣汰,提高全员素质,充分发挥设备效益,利用率追求100%,故障率要求零。
推行点检制度,推广全员维修和预防维修,利用诊断技术预防停机故障。
企业自修、检修与社会化修理相结合,采用最经济的维修体制和方法。
进行设备现代化管理,数据采集要正确,存档要及时并利用管理软件定期分析预报。
备件维修资金严格考核,不准浪费,经常开展岗位培训和继续教育,考核制度化,提倡设备综合管理,坚持依靠技术进步,促进生产发展和预防为主的方针,在设备全管理过程中坚持设计、制造与使用相结合,维护与计划检修相结合;技术管理与经济管理相结合的原则,不断改善和提高企业技术装备素质,充分发挥设备效能,以达到良好投资效益,为提高企业经济效益和社会效益服务。
5.3造就高素质的设备管理与维修人才随着装备水平和管理水平的提高,企业设备管理与维修工作要涉及许多新技术,例如:计算机和软件技术、数控数显技术、电液自动化技术、监测和诊断技术、润滑和液压新技术;应用粘接、喷涂、冷焊等表面工程技术和复合表面工程技术;应用信息和网络、遥控和互联网技术;应用虚拟技术和纳米技术等。
所以对管、用、养、修设备的人才必须加紧培养。
很多企业引进高新技术设备时,重视培养维修技术人员,派人出国进修、监造、学习。
目前我国已涌现出一批既有实践经验和能力,又有一定理论水平的高素质的设备管理、使用、维修人才,代表着现代设备管理工作的希望和未来。
很多现代企业,已认识到并开始实践“培训教育先行”,重视职工培训投人,使设备工程技术人员除勤奋工作外,还要勤奋学习,不断提高业务水平。
6.设备管理的发展趋势设备管理模式国际化、经济全球化,使大量先进设备和管理方法不断引进,我国设备管理模式和方法将逐步与国际接轨,设备管理的科技化逐步向自动化、高效率、低耗能、少污染和高可靠性运行方面发展。
所以设备管理和维修工作也将高科技化,管用养修设备人员要掌握高新技术,才能使用好,维修好,管理好现代化设备。
设备管理的市场经济化:设备管理的模式和方法,将根据市场经济、企业产品结构调整而变化。
设备管理的目标将根据市场经济要求,不仅为生产服务,更主要的是为提高企业效益服务。
设备管理与维修,要为提高产品质量、降低能耗、控制污染、减少成本和占领市场服务。
设备管理的维修专业化、社会化:国有企业中将改变“大而全”、“小而全”,维修部门逐步走向社会,在市场经济中求生存和发展。
为了社会整体效益,维修专业化和社会化将是发展趋势。
设备管理与维修人才高素质化适应高科技设备管理要求必须提高设备管理和维修工程技术人员素质。
现代企业也要培养高素质人才,通过进修、培训深造、企业内部实践和学习进行继续教育,不断学习高新技术,从而实现设备管理人才现代化。
设备管理的新趋势是和当前社会生产的技术经济点相适应,这些新趋势带来了设备管理综合水平的提升,只有好好把握这些趋势,才能真正适应社会化大生产的要求,切实为生产保驾护航,为企业运营提供有力的保障,促进企业整体水平的不断提升。