结晶器振动技术
结晶器振动技术的发展
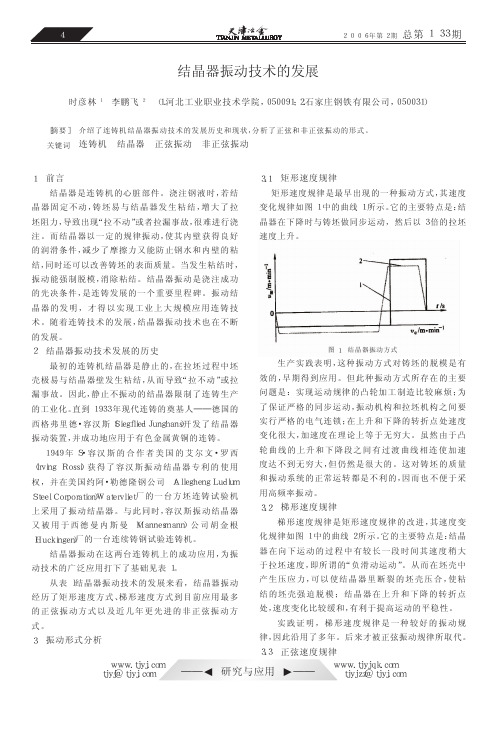
TIANJIN METALLURGY
2 0 0 6 年第 2 期 总第 1 33 期
结晶器振动技术的发展
时彦林 1 李鹏飞 2 ( 1.河北工业职业技术学院, 050091; 2.石家庄钢铁有限公司, 050031)
[ 摘要] 介绍了连铸机结晶器振动技术的发展历史和现状, 分析了正弦和非正弦振动的形式。
Key wor ds: solvent method; hot galvanizing; hot- rolled sheet; base; state; coating quality
Development of Oscillation Technique of Mould Shi Yanlin Li Pengfei
Application and Design of the Welded Steel Str uctur e Fr ame of a Bending Machine
Yang Peihao Wang Ying- Chun Abstr act: A fully- welded steel structure frame was success- fully developed and applied to a bending machine to replace conventional iron casting structure. The plate- shell computa- tional program of finite element method was used to seek the stress and deformation under service condition of the numerical simulation results indicated that the supporting frame met the production requirement.This bending machine was applied suc- cessfully in engineering practice . Key wor ds: frame; casting structure; fully- welded steel struc- ture; finite element method
连铸结晶器振动工艺参数
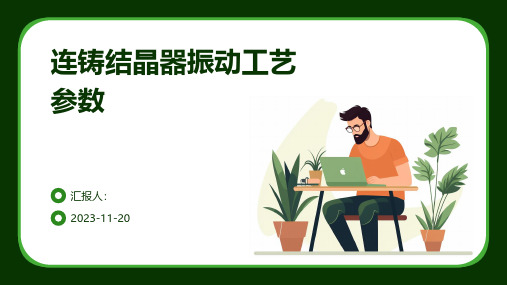
连铸结晶器振动工艺参数2023-11-20汇报人:CATALOGUE目录•结晶器振动工艺参数概述•振动频率•振幅•振动波形•结晶器与铸坯间的摩擦系数•实际生产中的结晶器振动工艺参数调整与优化01结晶器振动工艺参数概述CHAPTER减少摩擦和磨损改善润滑效果促进坯壳均匀生长030201结晶器振动的作用工艺参数对连铸坯质量的影响振动频率01振幅02振动波形03结晶器振动工艺参数的设定与调整CHAPTER振动频率02定义单位振动频率的定义与单位结晶组织裂纹和缺陷润滑和传热振动频率对铸坯表面质量的影响合适振动频率的选择与调整铸坯材质和规格实时监测和调整CHAPTER振幅03定义单位振幅的定义与单位结晶组织振幅过大可能导致铸坯内部气孔和夹杂物的形成,影响铸坯的质量。
气孔和夹杂裂纹振幅对铸坯内部组织的影响铸坯材质铸坯断面尺寸设备性能操作经验01020304合适振幅的选择与调整CHAPTER振动波形04正弦波、方波、三角波等常见波形介绍正弦波方波三角波表面质量不同的波形会对铸坯表面质量产生显著影响。
例如,正弦波能够显著减少铸坯表面裂纹的产生,而方波由于其强烈的振动冲击,可能会导致铸坯表面质量的下降。
内部结构波形也会影响铸坯的内部结构。
例如,三角波由于其稳定性和均匀性,能够促进铸坯形成均匀且稳定的组织结构。
不同波形对铸坯质量的影响选择原则调整策略合适波形的选择与调整05结晶器与铸坯间的摩擦系数CHAPTER通常采用试验测定法,通过模拟结晶器与铸坯的实际接触情况,测量出摩擦力与压力,并计算得到摩擦系数。
摩擦系数的定义与测量方法测量方法定义振动频率摩擦系数的大小直接影响到结晶器与铸坯之间的摩擦力,进而影响到振动频率的选择。
过高的摩擦系数要求更高的振动频率以克服摩擦力,确保铸坯的顺利下滑。
摩擦系数的变化会对振幅产生一定影响。
当摩擦系数增大时,为了保持铸坯在结晶器内的稳定性,可能需要适当增大振幅,以提供足够的振动力。
摩擦系数的不同可能导致振动波形的变化。
《伺服电机驱动的连铸结晶器振动位移系统模糊控制研究》

《伺服电机驱动的连铸结晶器振动位移系统模糊控制研究》篇一一、引言随着现代工业技术的飞速发展,伺服电机驱动技术及其在连铸过程中的应用逐渐受到广泛关注。
连铸结晶器振动位移系统作为连铸工艺的核心部分,其控制精度和稳定性对产品质量具有至关重要的影响。
传统的控制方法往往难以满足复杂多变的工艺要求,因此,本研究致力于探讨伺服电机驱动的连铸结晶器振动位移系统的模糊控制方法。
二、连铸结晶器振动位移系统概述连铸结晶器振动位移系统是连铸工艺中用于控制结晶器振动的重要设备。
其工作原理是通过伺服电机驱动,实现结晶器的精确振动和位移。
该系统的性能直接影响到连铸产品的质量和生产效率。
传统的控制方法多采用PID控制或传统模糊控制,但面对复杂多变的工艺环境,这些方法往往难以达到理想的控制效果。
三、模糊控制原理及其在连铸结晶器振动位移系统中的应用模糊控制是一种基于模糊集合理论的控制方法,能够处理复杂非线性系统中的不确定性和未知性。
在连铸结晶器振动位移系统中,模糊控制通过建立模糊规则库和模糊推理机制,实现对系统输入和输出的精确控制。
与传统的控制方法相比,模糊控制具有更好的适应性和鲁棒性,能够更好地应对复杂多变的工艺环境。
四、伺服电机驱动的连铸结晶器振动位移系统模糊控制研究本研究采用伺服电机驱动的连铸结晶器振动位移系统作为研究对象,通过建立模糊控制系统,实现对系统输入和输出的精确控制。
具体研究内容包括:1. 建立模糊控制系统框架:包括模糊规则库的建立、模糊推理机制的构建以及系统软硬件设计等。
2. 确定系统输入和输出变量:根据实际工艺需求,确定系统输入和输出变量,如振动速度、振动加速度、位移等。
3. 设计模糊控制器:根据输入和输出变量的特点,设计适合的模糊控制器,包括模糊化、推理和解模糊等环节。
4. 实验验证:通过实验验证所设计模糊控制器的有效性,分析其控制精度和稳定性等性能指标。
五、实验结果与分析通过实验验证,所设计的伺服电机驱动的连铸结晶器振动位移系统模糊控制器具有较高的控制精度和稳定性。
连铸结晶器振动工艺参数研究与快捷模型开发

《连铸结晶器振动工艺参数研究与快捷模型开发》xx年xx月xx日CATALOGUE 目录•引言•连铸结晶器振动工艺基础理论•连铸结晶器振动工艺参数研究•基于神经网络的连铸结晶器振动模型开发•基于遗传算法的连铸结晶器振动工艺参数优化•结论与展望01引言连铸结晶器振动在提高铸坯质量和产量方面具有重要作用,但缺乏系统研究和模型支持。
本研究旨在解决现有振动工艺参数优化和模型开发的问题,为提高连铸结晶器振动效果提供理论支撑和实践指导。
研究背景与意义1研究内容与方法23研究连铸结晶器振动的基本原理和影响因素。
研究连铸结晶器振动工艺参数优化方法,包括振动频率、振幅、波形等参数的优化。
研究基于数据挖掘和机器学习的连铸结晶器振动模型构建方法,并开发相应的快捷模型。
研究创新点与特色01本研究将振动原理与工艺参数优化相结合,为连铸结晶器振动工艺参数优化提供了新的思路和方法。
02引入数据挖掘和机器学习技术,构建连铸结晶器振动模型并开发快捷模型,为提高模型预测精度和计算速度提供了新的途径。
03本研究将理论与实践相结合,为提高连铸结晶器振动效果提供了具有可操作性的方案和建议。
02连铸结晶器振动工艺基础理论连铸结晶器振动工艺原理是利用振动机构周期性地对连铸结晶器进行振动,以破坏连铸结晶器内钢水的液面,减少钢水在结晶器内的流动,达到减少连铸坯振痕深度的目的。
连铸结晶器振动工艺的原理基于流体力学和机械振动学的基本理论,通过分析结晶器内钢水的流动状态,确定合适的振动频率和振幅,使结晶器振动对钢水液面的破坏达到最佳效果。
连铸结晶器振动工艺原理连铸结晶器振动工艺的数学模型是描述结晶器振动过程中各种物理量之间相互关系的数学表达式,它可以指导工艺参数的优化和预测振痕深度。
目前,常用的数学模型有经验公式、有限元法、数值模拟等。
这些模型各有优缺点,需要根据实际生产情况选择合适的模型。
同时,数学模型的建立需要大量的实验数据和计算资源。
连铸结晶器振动工艺的数学模型连铸结晶器振动工艺参数包括振动频率、振幅、波形、振动时机等。
结晶器振动

第1章绪论第1章绪论1.1连续铸钢技术的发展钢水凝固成型有两种方法:传统的模铸法和连续铸钢法。
连续铸钢是把液态钢用连铸机浇注、冷凝、切割而直接得到铸坯的工艺。
是连接炼钢和轧钢的中间环节,是炼钢厂的重要组成部分[1]。
连铸的出现从根本上改变了一个世纪以来占统治地位的钢锭——初轧工艺,为炼钢生产向连续化、自动化方向的发展开辟了新的途径[2]。
1.1.1 连续铸钢技术的发展历程早在十九世纪中期美国人塞勒斯(1840年)、赖尼(1843年)和英国人贝塞麦(1846年)就曾提出过连续浇注液体金属的初步设想,并用于低熔点有色金属的浇铸;但类似现代连铸设备的建议是由美国人亚瑟(1886年)和德国人戴伦(1887年)提出来的。
他们的建议中包括有水冷的上下敞口的结晶器、二次冷却段、引锭杆、夹辊和铸坯切割装置等设备,当时用于铜和铝等有色金属的浇铸。
1933年德国人容汉斯建成第一台结晶器可以振动的连铸机,并用其浇铸黄铜获得成功,后又用于铝合金的工业生产。
结晶器振动的采用,不仅可以提高浇注速度,而且使钢液的连铸生产成为可能,容汉斯因此成为现代连铸技术的奠基人。
但连续铸钢步入工业生产阶段,应当归功于英国人哈里德提出的“负滑脱(Negative Strip)”概念。
在哈里德的负滑脱振动方式中,结晶器下振速度比拉坯速度快,铸坯与结晶器壁间产生了相对运动,真正有效的防止了铸坯与结晶器壁的粘结,使钢连续浇铸的关键性技术得以突破[3]。
1.1.2 连续铸钢的优越性连续铸钢与模铸的根本差别在于模铸是在间断的情况下,把一炉钢水浇注成多根钢锭,脱模之后经初轧机开坯得到钢坯;而连铸是把一炉钢水燕山大学工学硕士学位论文连续地注入结晶器,得到无限长的铸坯,经切割后直接生产铸坯。
基于这一根本差别,连铸和模铸比较,就具有许多明显的优越性[4-9]:(1)简化了钢坯生产的工艺流程,节省大量投资,省去了模铸工艺中脱模整模均热及初轧等工序,缩短了钢水到钢坯的周期时间。
结晶器振动全解
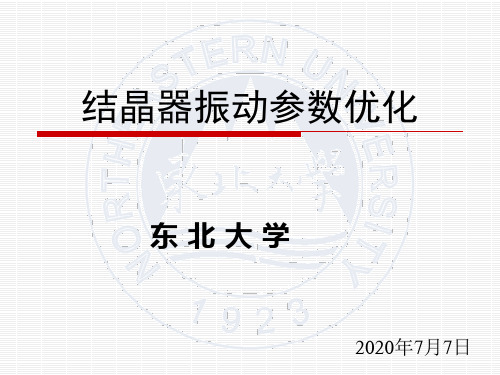
连铸技术
负滑动振动 负滑动振动是指当结晶器往下振动时,其速度大于拉坯速度,形成
负滑动。即: V2=V(1-NS)
而往上振动时,取 V1=2.8 ~ 3.2V2
式中NS为负滑动率,说明结晶器平均下降速度大于拉速,产生负滑 动。负滑动振动的特点是:结晶器先以比拉速稍高的速度下降 一段时间出现负滑动或负滑脱。此时坯壳处于受压状态,既有 利于强制脱模又有利于断裂坯壳的压合。然后再以较高的速度 上升,克服了同步振动时产生较大加速度的缺点。结晶器在下 降或上升过程中都有一段稳定运动时间,有利于坯壳的生成和 裂纹的愈合。
6
连铸技术
③正弦振动 结晶器振动时的运动速度随时间的变化呈一条正
弦曲线。其特点是:结晶器在整个振动过程中 速度一直是变化的,即铸坯与结晶器时刻都存 在相对运动。在结晶器下降过程中有一段负滑 动,能防止和消除粘结,具有脱模作用;另外, 由于结晶器的运动速度是按正弦规律变化的, 加速度必然按余弦规律变化,所以过度比较平 稳,冲击力也较小。
20
连铸技术
负滑脱时间与振痕深度之间的关系
21
连铸技术
结晶器振动参数对连铸粘结性漏钢的影响
结晶器振动的最大特点就是结晶器与坯壳的相对 运动过程中有一段负滑脱时间,这期间坯壳受 压应力作用有利于坯壳的愈合,以防止坯壳断 裂造成漏钢。但是,负滑脱时间不能过长,因 为负滑脱时间越长,则振痕越深,振痕处坯壳 夹渣就越严重,坯壳强度降低,坯壳越容易断 裂而不利于脱模,进而增加了漏钢的可能性。 所以,提高振动频率、缩短负滑脱时间的目的 仍然是为了脱模,以利于防止粘结性漏钢,同 时也可改善铸坯质量。
目前国外有关文献报道,大多数的负滑脱时间取值范围 在 0.1s ~ 0.25s,认为对于不同的钢种最佳负滑动 时间为 0.1s 左右。至于负滑动率 NS,国内外有关 文献报道在 NS值为-20%~240%范围内变化进行 浇铸,结果对铸坯脱模及表面质量没有任何不利影响。 可见,对于负滑动率 NS 的取值范围是很宽的,工艺 参数的确定主要是确定负滑动时间。
DYNAFLEX结晶器液压振动技术的研究与应用
第2 卷 2 1 年第 5 总第 19 ) 8 00 期( 4期
D AF E YN L X结 晶 器液 压 振 动 技 术 的 研 究 与应 用
孟 雷
( 济钢 第三炼 钢厂 济 南
摘 要
200 ) 5 11
介 绍 了 V ( 钢 联 ) 进 的 国 际 先进 的 DY F E 结 晶 器 液 压 振 动 技 术 的 原 理 和 结 构 特 点 , AI奥 引 NA L X
22 液 压 系统 .
D N FE Y A L X液 压振 动装 置 的 液压 系统 主要 由 液压 站及 带 伺服 阀的液 压缸 组 成 ( 图 1 , 见 ) 液压 振
动 的 动 力装 置 为液 压 站 , 作 为 动力 源 向振 动 液 它 压缸 提 供稳 定 压力 和 流量 的油液 。 由于振 动 液压 缸 处 在 高温 、 尘 、 多 潮湿 恶 劣 的环 境 中 , 因此 还 设 计 了一条 压 缩 空气 通 道 , 液 压缸 进 行 冷 却 和 吹 对 扫 。液压 振 动 的核 心 控 制 装 置 为 振 动伺 服 阀 , 它 带 有 位 置反 馈 , 以准 确 地 调 节 其 阀位 。伺 服 控 可 制 阀块 直接 安 装 在 振 动 液 压 缸 缸 体 上 , 利 于 提 有 高 系 统 的 动态 响应 性 。它 灵 敏 度 极 高 , 压 动 力 液 站 提供 动力 如 有 波动 , 服 阀 的动作 就 会失 真 , 伺 造 成 振 动 时运 动 不 平 稳 和 振 动 波 形 失 真 。 为此 , 要 在 系 统 中设 置 蓄能 器 以吸 收 各 类 波 动 和 冲击 , 保
D N FE Y A L X液压 振 动装 置振 动 曲线 为正 弦 或非 正弦 , 主要 技 术参 数 : 幅 0~1 (±6 rm; 动频 振 2 ) a 振 率4 0~20 mi; 正 弦 因数 05~ .; 率变 化 7 次/ n 非 . 07 频 05 z 振 幅变 化 1 m s非 正弦 变化 01 /。 .H ; m /; . mm s
结晶器
液压伺服与比例控制系统三级项目250KN结晶器液压振动系统特性仿真分析学院(系):机械工程学院年级专业: 10级机电控制工程1班小组成员:张迪嘉张天宇王平阳王利双王浩冉指导教师:张伟目录一、结晶器及其振动技术概述 (4)1.2结晶器的振动 (5)二、结晶器振动技术国内外研究现状及发展趋势 (5)2.1国内研究及应用 (5)2.2国外的研究与应用 (6)三、结晶器液压振动结构原理和特点 (7)3.1液压振动装置的构成 (7)3.2液压振动装置原理 (7)3.3液压振动的特点 (8)四、结晶器液压系统工作原理 (9)4.1系统工作原理 (9)4.2液压系统参数及主要元件的选择 (10)4.3结晶器液压振动控制系统 (12)五、结晶器液压伺服系统建模 (13)5.1确定各组成原件的传递函数 (14)5.2系统方框图 (15)六、matlab系统仿真分析 (16)6.1时间响应曲线 (16)6.2频率响应曲线 (17)6.3 PID 控制原理 (19)6.4PID参数对系统特性影响 (20)七、总结与感想 (21)7.1影响阀控缸系统频率特性的参数 (21)7.2心得与感想 (22)参考文献 (22)一、结晶器及其振动技术概述1.1结晶器近年来,传统连铸的高效化生产在工业发达国家取得了长足的进步,特别是高拉速技术引起人们的重视。
通过采用新型保护渣、液面高精度检测和控制等一系列技术措施,使连铸机的生产能力大幅度提高,生产成本降低,给企业带来了极大的经济效益。
而结晶器作为连铸生产的重要设备之一,如图1,它的性能对连铸机的生产能力和铸坯质量都起着十分重要的作用。
图1 连铸设备的组成结晶器是连铸最重要的组成部分,它是一种特殊的无底水冷铸模。
在它的内部有冷却装置,其中有的是管式结晶器隔离水缝冷却,有的是喷淋水喷水冷却,目的是对铸坯进行冷却降温。
并且结晶器由振动装置带动发生振动。
1.2结晶器的振动结晶器振动技术是连铸技术的重要特征。
CVD200手持无线结晶器振动检测仪技术方案
数据分析终端
采集卡 积分模块
加速度信 号
速度信号
数据 分析 平台
位移信号
CVD
200 分析 软件
加速度波形
速度波形
显
位移波形
示
振幅
构
振频 偏斜率
件
同步性
X-Y位移轨迹图
频谱图
图 2工作原理图
4. 技术参数及软件功能:
1. 技术参数
系统参数 偏振检测精度 主振检测精度 振频范围 振频检测精度 振动最大可测幅值
0.02mm 0.02mm 小于 600cpm(10Hz) 1cpm(0.02Hz) 10mm
同步性检测精
±1ms
度
传感器通道数 最多支持传感 器个数 检测参数
软件功能
三通道(主振加两方向偏振)
4个 加速度、速度、位移步性分析、文件打印、数据回放
¾ 图形显示振动加速度、速度与位移波形
¾ 图形显示振动频谱,可观察结晶器振动中其他干扰源频率
¾ 图形显示 X-Y 位移轨迹图,可直观分析结晶器偏振及同步性
¾ 三维图形方式显示结晶器的振动形态
¾ 图形支持多点触控功能,可通过手指进行图形的拉伸和缩放
¾ 可保存检测数据并回放历史数据
¾ 支持图形打印功能
5
国内外已有多家企业研制了采用位移传感器方式的结晶器振动检测仪,主要 用于结晶器的在线测量。
3. 系统组成及工作原理
1. 系统组成: CVD200 手持无线结晶器振动检测仪由数据分析终端和无线传感器两部分组 成。其实物如图 1所示。具体结构及说明如下:
图 1 左为无线传感器,右为数据分析终端
数据分析终端采用主流的 windows 操作系统和多核工业级平板电脑,平台移 植性更好,运行速度更快。该终端采用 9.7 寸液晶电容屏,支持多点触摸操作, 操作简便。无线传感器采用了 12 位精度的 AD 采样芯片进行数据采集,保证系 统具有足够的精度和测量准确性。数据分析终端与无线传感器之间采用无线通讯 方式进行数据传输,数据分析终端能够主动发现和连接无线传感器,免去了传统 检测设备需要拖线的烦恼。无线传感器定制的铝合金外壳经特殊的表面处理,使 系统具有良好的抗干扰能力和防腐蚀能力,适应现场恶劣的工作环境。
结晶器非正弦振动波形构造方法
2023-11-07
目 录
• 引言 • 结晶器振动的基本原理 • 非正弦振动波形的特点 • 非正弦振动波形的设计 • 非正弦振动波形的实验验证 • 结论与展望
01
引言
研究背景和意义
结晶器是工业生产中重要的设备之一,主要用于分离和提纯物质。非正弦振动波 形能够提高结晶器的分离效率,降低能耗,具有重要的实际应用价值。
题提供了新的思路和解决方案。
研究不足与展望
• 研究不足:尽管本文已经对结晶器非正弦振动波形构造方 法进行了较为深入的研究,但在实际应用方面仍存在一些 不足之处。例如,实验中使用的结晶器模型仅为简化版, 可能无法完全模拟实际生产过程中的复杂情况。此外,对 于不同类型和规模的结晶器,该方法的效果和适用性仍需 进一步验证。
其他因素
除上述因素外,还有设备结构、物 料性质、操作条件等也会影响结晶 器的振动。
03
非正弦振动波形的特点
非正弦振动波形的基本概念
• 非正弦振动波形是指一类不是由正弦函数生成的振动波形, 这类波形具有一些独特的性质,如具有更高的频率内容,更 复杂的相位结构等。
非正弦振动波形的优点
• 非正弦振动波形具有许多优点,例如它可以有效地防止信号的谐波失真,提高信号的清晰度和纯净度。此外,非正弦振 动波形能够提供更大的动态范围,从而增加了信号的对比度。
研究不足与展望
展望:未来研究可以针对以下 几个方面进行深入探讨
1. 进一步完善结晶器非正弦振 动波形构造方法,提高波形的
多样性和适用性;
2. 将该方法应用于不同类型和 规模的结晶器中,验证其普适
性和效果;
研究不足与展望
3. 结合工业生产实际需求,将该方法与现有工艺相结 合,提高结晶器的生产效率和产品质量;
- 1、下载文档前请自行甄别文档内容的完整性,平台不提供额外的编辑、内容补充、找答案等附加服务。
- 2、"仅部分预览"的文档,不可在线预览部分如存在完整性等问题,可反馈申请退款(可完整预览的文档不适用该条件!)。
- 3、如文档侵犯您的权益,请联系客服反馈,我们会尽快为您处理(人工客服工作时间:9:00-18:30)。
内蒙古科技大学实习论文题目:结晶器振动技术姓名学号:班级日期:目录内蒙古科技大学煤炭学院 (1)目录 (2)一、摘要 (3)二、前言 (3)三、结晶器振动技术 (5)3.1正弦振动 (5)3.2非正弦振动 (6)3.4结晶器振动参数设置 (9)3.5振动伺服阀 (10)3.6结论 (10)一、摘要连铸连轧结晶器振动技术的发展历史和现状,简单分析了结晶器正弦振动和非正弦振动形式,并讨论了结晶器振动和润滑的关系。
关键词:结晶器;振动;润滑;振动参数;振动伺服阀;二、前言结晶器振动是连铸技术的一个基本特征。
连铸过程中,结晶器和坯壳间的相互作用影响着坯壳的生长和脱膜,其控制因素是结晶器的振动和润滑。
连铸在采用固定结晶器浇注时,连铸直接从结晶器向下拉出,由于缺乏润滑,易与结晶器发生粘结,从而导致出现拉不动或者拉漏事故,很难进行浇注。
结晶器振动对于改善铸坯和结晶器界面间的润滑是非常有效的,振动结晶器的发明引进,工业上大规模应用连铸技术才得以实现。
可以说,结晶器振动是浇注成功的先决条件,十年来发展的重要里程碑。
近年来,冶金工业的迅速发展,要求连铸提高拉速和增加连铸机的生产能力,人们对结晶器振动的认识也在不断深入和发展。
连铸机结晶器振动的目的是防止拉坯时坯壳与结晶器黏结,同时获得良好的铸坯表面。
结晶器向上运动时,减少新生坯壳与铜壁产生黏着,以防止坯壳受到较大的应力,使铸坯表面出现裂纹;而当结晶器向下运动时,借助摩擦,在坯壳上施加一定的压力,愈合结晶器上升时拉出的裂痕,要求向下运动的速度大于拉坯速度,形成负滑脱。
结晶器壁与运动坯壳之间存在摩擦力,此摩擦力被认为是撕裂坯壳进而限制浇注速度的基本因素。
在初生坯壳与结晶器壁之间存在液体渣膜,此处的摩擦为黏滞摩擦,即摩擦力大小正比于相对运动速度,渣膜黏度,反比于渣膜厚度。
在结晶器振动正滑脱期间摩擦力及其引起的对坯壳的拉应力就较大,可能将初生坯壳拉裂,为此开发了采用负滑脱的非正弦振动技术来减小这一摩擦力。
理论研究及模拟实验表明,适当选择非正弦振动参数(偏斜率)可减小摩擦力50% ~60%。
在结晶器液压伺服非正弦振动出现之前都是采用机械式振动装置的,机械式的振动装置由直流电动机驱动,通过万向联轴器,分两端传动两个涡轮减速机,其中一端装有可调节轴套,涡轮减速机后面再通过万向联轴器,连接两个滚动轴承支持的偏心轴,在每个偏心轮处装有带滚动轴承的曲柄,并通过带橡胶轴承的振动连杆支撑振动台,产生振动。
机械振动一般采用正弦曲线振动,振动波形、振幅固定不变。
与机械振动相比,板坯连铸机的液压振动装置具有一系列优点: 振动力由两点传入结晶器,传力均匀;在高频振动时运动平稳,高频和低频振动时不失真,振动导向准确度高;结构紧凑、简单,传递环节少,与结晶器对中调整方便,维护也方便;采用高可靠性和高抗干扰能力的PLC控制,可长期保证稳定的振动波形;可改变振动曲线,并可在线设定振动波形等,增加了连铸机可浇钢种;改善铸坯表面与结晶器铜壁的接触状态,提高铸坯表面质量并减少黏结漏钢。
三、结晶器振动技术在结晶器振动技术发展过程中,在振动形式及振动装置的结构上出现了多种多样的形式。
目前,在工业生产中应用量多的是正弦波模式。
近年来,非正弦波模式又被人们接受,并随着先进的液压振动装置的出现,采用了各种各样的振动曲线。
3.1正弦振动正弦振动就是结晶器的运动速度和时间成正弦曲线关系,如图1曲线2 所示。
这种振动规律的最大优点就是只要用一简单的偏心机构即可实现,易于维护,速度变化平稳无冲击。
由于正弦振动的速度始终处于变化中,在振动机构和拉坯机构之间没有严格的速度关系。
因此,也不必建立严格的连锁。
同时,在运动中仍有一小段负滑脱阶段,具有脱膜作用。
由于加速度较小,这种振动还能实现高频振动,减少负滑动时间以得到较浅的振痕,有利于改善铸坯表面质量,为了使这两个参数最佳化,曾经历了不同方向的发展1。
从大量实践经验可以得出结论,高频率小振幅对改善铸坯表面质量有明显的效果2。
从图2可以看出拉坯速度相同时,小振幅高频率壳减少振痕深度,负滑脱时间tN =60/πfcos-1(1000W拉/2πSf),当振幅S减小,振动频率f增大时,其结果可使负滑脱时间tN缩短,因此也可以说缩短负滑脱时间有利于提高铸坯表面质量,图3也说明了这一点。
目前,有关文献报道大多数负滑脱时间取值范围在0·1~0·25s,对于不同钢种最佳负滑脱时间为0·1s。
但是,正弦振动的特性完全决定于其振幅和频率的数值,即正弦振动只有两个相互独立的振动参数。
变量少,其波形的调节能力就小,难以完全满足高速连铸的工艺要求,特别是对于那些易于粘结的钢种,在高速浇注条件下采用具有较长的正滑动时间的非正弦式结晶器振动是更有利的,而且采用带可调程序控制装置的液压机构很容易实现这种非正弦振动方式。
3.2非正弦振动结晶器振动结构原理如图3所示。
由图3可以看出结晶器振动系统的构成包括两大部分:电气控制部分与液压驱动部分;液压部分主要包括2个振动液压缸和1个蓄能器,其动力源为主液压站,主液压站向2个振动液压缸提供稳定压力和流量的油液。
液压站的运行由远程PLC站来控制。
电气控制元器件:在振动台下面的控制箱内有1个伺服阀、1个位置传感器、1个温度传感器、2个压力传感器(进油压力检测与出油压力检测),另外还有1个箱体冷却电磁阀和1个油路急停电磁阀。
结晶器振动的核心控制装置为伺服阀,它带位置反馈,可以准确的调节其阀位, PLC输出0~±10V的控制信号,反馈回4~20mA的信号,根据反馈信号的大小来调节阀位,因而它的控制精度高于比例阀,比例阀是不带位置反馈的。
伺服阀的灵敏度极高,但液压站提供的压力有波动,伺服阀的动作就会失真,造成振动时运动不平稳和振动波形失真。
因此,要在系统中设置蓄能器以吸收各类波动和冲击,保证整个系统的压力稳定。
控制箱内的温度传感器用来检测缸体温度,以便于观察各元器件的工作环境,它的温度数值可以从HMI上或C7-634上看到,如果由于冷却不良导致环境温度过高时,位置传感器会失控并产生紊乱信号,同时执行保护性停机。
它的一般允许温度最高为80℃,保持良好的冷却,有助于系统的稳定与正弦和非正弦曲线振动靠伺服阀控制,而伺服过PLC控制曲线生成器设定振动曲线(同时也设定振幅和频率)。
曲线生成器通过液压缸传来的压力信号和位置反馈信号来修正振幅和频率。
经过修正的振动曲线信号转换成电信号来控制伺服阀。
只要改变曲线生成器即可改变振动波形、振幅和频率。
曲线生成器输入信号的波形、振幅和频率可在线任意设定,设定好的振动曲线信号传给伺服阀,伺服阀即可控制振动液压缸按设定参数振动。
在软件编程中,同时还设置多种报警和保护措施以避免重大事故的发生。
这种在线任意调整振动波形、振幅和频率是机械振动实现不了的。
图3 液压伺服振动结构组成及控制原理图近年来,现代连铸发展的一个特点是拉坯速度日益提高,同时,连铸坯热送直接轧制技术的发展也对连铸坯的表面质量提出了更高的要求。
实践表明,高频振动和高速铸造均会造成结晶器保护渣消耗量的下降,使坯壳与结晶器壁间的润滑性能变坏,摩擦力增加,容易发生粘结漏钢。
为解决高拉坯速度、高频振动这一新情况下的漏钢问题,将弯月面下初凝的薄弱坯壳顺利拉出,人们一方面采用含有Li2O的低粘度、低熔点、铺展性好的保护渣,以改善铸坯与结晶器间的润滑条件,保持一个合适的保护渣消耗量;另一方面在结晶器的振动方式上采用这样的振动波形:在正滑动区间V振-V拉较小以尽可能降低作用在坯壳上的拉伸应力,而在负滑动区间V振-V拉较大以对坯壳施加足够大的压缩力,并降低负滑动时间率NSR或增大正滑脱时间tP。
在正弦振动中, tN、tP互为增函数关系,不能同时满足上述几个方面的要求。
因此,人们开发了结晶器上升时间比下降时间长的非正弦振动波形,引入了波形偏斜率α这一自由参数。
当然,目前开发的各种波形不同的非正弦振动模式,均是通过液压伺服系统控制的液压振动装置来实现非正弦振动的,除了可以改变振幅和振频外,还可以根据工况的变化自由地调节波形偏余率α,改变振动波形。
图1示出了非正弦振动的位移曲线和速度曲线。
其特点是结晶器的上升时间长且速度平稳,可显著地减小对坯壳的拉伸应力;下降时间短且保持了较大的负滑动量,可对坯壳施加较大的压缩应力。
负滑脱时间tN明显减少,这符合前面提到的缩短tN,有利于改善铸坯表面质量的论述,同时,在非正弦振动中, tN, tP互为减函数关系, tN减少相应增大了正滑脱时间tP,可以保证保护渣的有效供给。
工业实验已经证明,采用合适的非正弦振动波形,至少可使振痕深度减少30%,坯壳与结晶器壁间的摩擦阻力减少40%。
此外,据称非正弦振动方式对于铸坯皮下的纯净度、结晶器的传热以及初生钩形凝固壳的形成都有积极影响。
继国外将液压伺服振动结晶器应用于连铸后,中国的李宪奎教授等提出了用连杆式机械传动实现结晶器的非正弦振动,通过改变连杆机构的杆长比和初相角来得到不同的非正弦振动波形。
与液压驱动的非正弦振动装置相比,连杆式机械传动的非正弦振动装置具有结构简单,便于加工、制造和维修成本低等优点,特别适用于原有连铸机的改造。
这对于振动模型的研究又提供了一种思路。
目前,首钢已在小方坯连铸机上率先采用这种振动装置。
3.3结晶器的振动与润滑的关系结晶器振动的重要影响主要是对润滑和振动痕迹形成的作用。
振动的同时要求提供结晶器润滑,两者的共同作用是减小坯壳和结晶器壁间的摩擦力,以得到最好的表面质量和防止粘结漏钢的最佳安全性。
如前所述,结晶器振动对于改善结晶器壁间的润滑是非常有效的,但对于结晶器振动如何影响结晶器保护渣的消耗和保护渣的润滑作用,其机理并不十分清楚。
早期的研究曾提出一个负滑脱期间保护渣流入量的模型,但是随后的试验结果表明,保护渣消耗量是正滑脱时间的增函数,图4示出了保护渣消耗量与正滑脱时间的关系。
可见,对于振动结晶器,正滑脱时间越长,保护渣消耗量越大,由此也引起了大量的争论。
笔者认为,对于增加保护渣消耗而言,正滑脱期间和负滑脱期间是振动周期内的两个必不可少的过程:正滑脱期间,结晶器相对坯壳向上运动,保护渣在结晶器钢水弯月面处形成的渣圈上移,液渣由钢液面向弯月面流动的通道被“打开”,促进了液渣弯月面附近流动和聚集,由于摩擦力作用液态渣的一部分被“拔出”;负滑脱期间,结晶器相对坯壳向下运动,渣圈随结晶器下移,液渣受到压力而向结晶器和坯壳间填充,同时,由于压缩的作用,液渣流动的通道被“关闭”,也部分阻碍了钢液面上的液渣向弯月面附近流动。
结晶器周期性振动的结果,导致液渣在弯月面处的流动、聚集以及向结晶器和坯壳间填充的重复进行,从而改善了结晶器的润滑状况。