连铸结晶器振动参数取值限度问题
连铸结晶器振动工艺参数
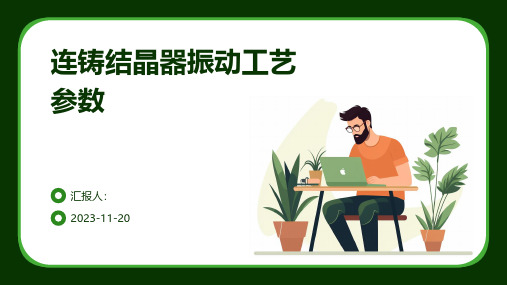
连铸结晶器振动工艺参数2023-11-20汇报人:CATALOGUE目录•结晶器振动工艺参数概述•振动频率•振幅•振动波形•结晶器与铸坯间的摩擦系数•实际生产中的结晶器振动工艺参数调整与优化01结晶器振动工艺参数概述CHAPTER减少摩擦和磨损改善润滑效果促进坯壳均匀生长030201结晶器振动的作用工艺参数对连铸坯质量的影响振动频率01振幅02振动波形03结晶器振动工艺参数的设定与调整CHAPTER振动频率02定义单位振动频率的定义与单位结晶组织裂纹和缺陷润滑和传热振动频率对铸坯表面质量的影响合适振动频率的选择与调整铸坯材质和规格实时监测和调整CHAPTER振幅03定义单位振幅的定义与单位结晶组织振幅过大可能导致铸坯内部气孔和夹杂物的形成,影响铸坯的质量。
气孔和夹杂裂纹振幅对铸坯内部组织的影响铸坯材质铸坯断面尺寸设备性能操作经验01020304合适振幅的选择与调整CHAPTER振动波形04正弦波、方波、三角波等常见波形介绍正弦波方波三角波表面质量不同的波形会对铸坯表面质量产生显著影响。
例如,正弦波能够显著减少铸坯表面裂纹的产生,而方波由于其强烈的振动冲击,可能会导致铸坯表面质量的下降。
内部结构波形也会影响铸坯的内部结构。
例如,三角波由于其稳定性和均匀性,能够促进铸坯形成均匀且稳定的组织结构。
不同波形对铸坯质量的影响选择原则调整策略合适波形的选择与调整05结晶器与铸坯间的摩擦系数CHAPTER通常采用试验测定法,通过模拟结晶器与铸坯的实际接触情况,测量出摩擦力与压力,并计算得到摩擦系数。
摩擦系数的定义与测量方法测量方法定义振动频率摩擦系数的大小直接影响到结晶器与铸坯之间的摩擦力,进而影响到振动频率的选择。
过高的摩擦系数要求更高的振动频率以克服摩擦力,确保铸坯的顺利下滑。
摩擦系数的变化会对振幅产生一定影响。
当摩擦系数增大时,为了保持铸坯在结晶器内的稳定性,可能需要适当增大振幅,以提供足够的振动力。
摩擦系数的不同可能导致振动波形的变化。
板坯连铸机结晶器振动系统故障分析与治理
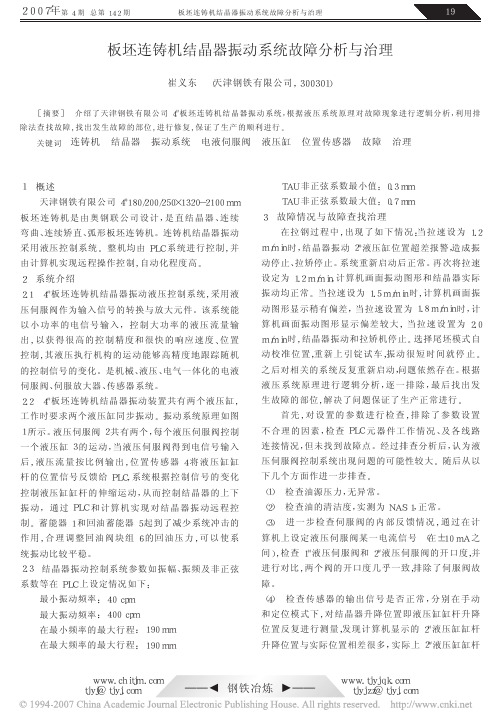
TAU 非正弦系数最小值: 0.3 mm TAU 非正弦系数最大值: 0.7 mm 3 故障情况与故障查找治理 在拉钢过程中, 出现了 如 下 情 况:当 拉 速 设 为 1.2 m/min 时, 结晶器振动 2# 液压缸位置超差报警,造成振 动停止、拉矫停止。系统重新启动后正常。再次将拉速 设定为 1.2 m/min, 计算机画面振动图形和结晶器实际 振动均正常。当拉速设为 1.5 m/min 时, 计算机画面振 动图形显示稍有偏差, 当拉速设置为 1.8 m/min 时, 计 算机画面振动图形显示偏差较 大, 当 拉 速 设 置 为 2.0 m/min 时, 结晶器振动和拉矫机停止。选择尾坯模式自 动校准位置,重新上引锭试车,振动很短时间就停止。 之后对相关的系统反复重新启动,问题依然存在。根据 液压系统原理进行逻辑分析, 逐一排除, 最后找出发 生故障的部位, 解决了问题保证了生产正常进行。 首先, 对设置的参数进行检查, 排除了参数设置 不合理的因素, 检查 PLC 元 器 件 工 作 情 况 、及 各 线 路 连接情况, 但未找到故障点。经过排查分析后, 认为液 压伺服阀控制系统出现问题的可能性较大。随后从以 下几个方面作进一步排查。 ( 1) 检查油源压力, 无异常。 ( 2) 检查油的清洁度, 实测为 NAS 1, 正常。 ( 3) 进一步检查伺服阀的内部反馈情况, 通过在计 算机上设定液压伺服阀某一电流信号 ( 在±10 mA 之 间) , 检查 1# 液压伺服阀和 2# 液压伺服阀的开口度,并 进行对比, 两个阀的开口度几乎一致,排除了伺服阀故 障。 ( 4) 检查传感器的输出信号是否正常, 分别在手动 和定位模式下, 对结晶器升降位置即液压缸缸杆升降 位置反复进行测量,发现计算机显示的 2# 液压缸缸杆 升降位置与实际位置相差很多, 实际上 2# 液压缸缸杆
连铸结晶器振动参数取值限度问题
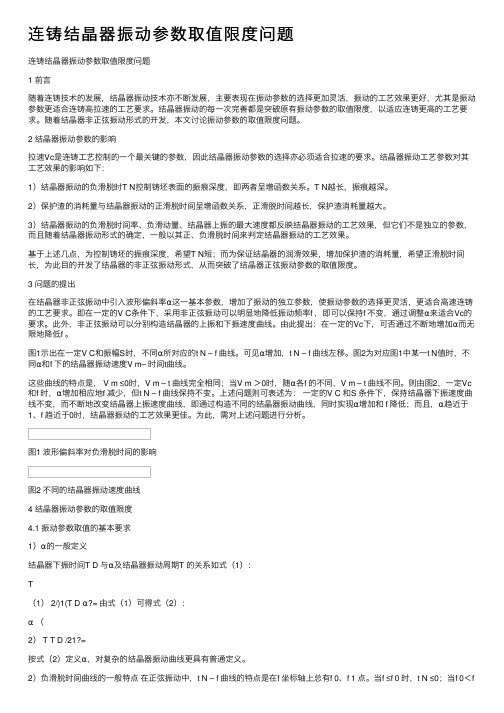
连铸结晶器振动参数取值限度问题连铸结晶器振动参数取值限度问题1 前⾔随着连铸技术的发展,结晶器振动技术亦不断发展,主要表现在振动参数的选择更加灵活,振动的⼯艺效果更好,尤其是振动参数更适合连铸⾼拉速的⼯艺要求。
结晶器振动的每⼀次完善都是突破原有振动参数的取值限度,以适应连铸更⾼的⼯艺要求。
随着结晶器⾮正弦振动形式的开发,本⽂讨论振动参数的取值限度问题。
2 结晶器振动参数的影响拉速Vc是连铸⼯艺控制的⼀个最关键的参数,因此结晶器振动参数的选择亦必须适合拉速的要求。
结晶器振动⼯艺参数对其⼯艺效果的影响如下:1)结晶器振动的负滑脱时T N控制铸坯表⾯的振痕深度,即两者呈增函数关系。
T N越长,振痕越深。
2)保护渣的消耗量与结晶器振动的正滑脱时间呈增函数关系,正滑脱时间越长,保护渣消耗量越⼤。
3)结晶器振动的负滑脱时间率、负滑动量、结晶器上振的最⼤速度都反映结晶器振动的⼯艺效果,但它们不是独⽴的参数,⽽且随着结晶器振动形式的确定,⼀般以其正、负滑脱时间来判定结晶器振动的⼯艺效果。
基于上述⼏点,为控制铸坯的振痕深度,希望T N短;⽽为保证结晶器的润滑效果,增加保护渣的消耗量,希望正滑脱时间长,为此⽬的开发了结晶器的⾮正弦振动形式,从⽽突破了结晶器正弦振动参数的取值限度。
3 问题的提出在结晶器⾮正弦振动中引⼊波形偏斜率α这⼀基本参数,增加了振动的独⽴参数,使振动参数的选择更灵活,更适合⾼速连铸的⼯艺要求。
即在⼀定的V C条件下,采⽤⾮正弦振动可以明显地降低振动频率f ,即可以保持f 不变,通过调整α来适合Vc的要求。
此外,⾮正弦振动可以分别构造结晶器的上振和下振速度曲线。
由此提出:在⼀定的Vc下,可否通过不断地增加α⽽⽆限地降低f 。
图1⽰出在⼀定V C和振幅S时,不同α所对应的t N – f 曲线。
可见α增加,t N – f 曲线左移。
图2为对应图1中某⼀t N值时,不同α和f 下的结晶器振动速度V m– 时间t曲线。
结晶器振动参数对连铸坯表面质量的影响

参数
优 化 前
优 化 后
断面
150 @ 210 150 @ 150 130 @ 130 150 @ 210 150 @ 150 130 @ 130
拉速P m#min- 1
1. 0~ 1. 7 2. 0~ 2. 8 2. 8~ 3. 2
1. 0~ 1. 8 1. 8~ 2. 8 2. 8~ 3. 2
负滑脱率P %
目前铸机条件下结晶器振动参数特点如表根据拉速范围铸坯断面要求选定负滑脱率或负滑脱时间前提下再根据正弦振动形式间的数学关系式确定其它振动参数振动频率负滑脱时间结晶器导前振痕间距振动参数优化由于振程是不容易改变的而且其它振动参数都是通过负滑脱率来调整根据式优化前后结晶器振动参数振程10mmtablemouldoscillationparametersbeforeafteroptimizationoscillationextent10mm参数断面振动频率p次min结晶器导前pmm振痕间距pmm150210131311951015015011154193141613013010174192151615021037381812015515015033341315617515161301303133111751811617
( 4) 在铸坯与结晶器之间润滑不良严重时, 铸坯与结晶器铜板发生粘结, 粘结使该处传热增 加, 弯月面凝固加剧, 弯月面坯壳厚度增加, 强度 增加, 造成钢水溢流并在器壁上凝固, 形成铸坯表 面上的搭结现象, 即带根的疤。
由此, 目前南钢铸坯表面缺陷产生主要原因
为: 润滑不良, 铸坯与结晶器间的机械作用力大, 导致拉坯阻力大所致。
及拉坯力等作用下, 这些裂纹将进一步扩展, 由此 导致振沟下谷部裂纹。该裂纹在高温下产生, 导 致裂纹内被氧化, 形成氧化铁, 这带来轧制过程中 裂纹不能焊合, 轧材上出现结疤及掉块现象。
连铸机结晶器振动装置动态性能分析
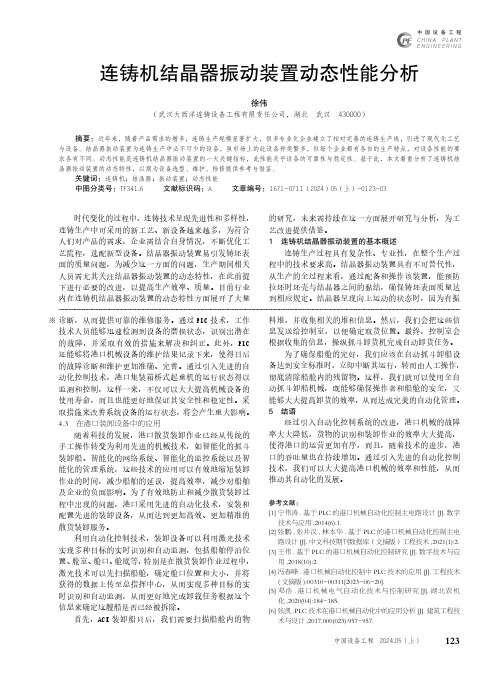
连铸机结晶器振动装置动态性能分析124研究与探索Research and Exploration ·工艺流程与应用中国设备工程 2024.05 (上)动装置,新生坯壳与铜板黏结问题得以缓解,也能避免坯壳上应力过度集中或者过大,对预防铸坯表面的裂纹相对有效。
如结晶器呈向下运动状态,由于存在摩擦作用力,能同步给坯壳施加压力,自动修复结晶器向上时拉出的裂痕。
但需尤其注意,向下运动的速度必须超过拉坯速度,构成负滑脱。
结晶器铜板与运动坯壳之间有摩擦力,在此摩擦作用下可能导致坯壳上的裂纹,在后续浇注作业中,也需考虑摩擦力大小来调整浇注速率。
初生坯壳与结晶器铜板之间有液体渣膜,该部位虽同样存在一定的摩擦力,但依据其作用情况,属于黏滞摩擦,也就是说,摩擦力与相对运动速度之间为正向变化关系,而渣膜黏度与渣膜厚度之间为反比。
综合上述分析,如结晶器振动装置处于正滑脱条件,摩擦力会对坯壳产生较大的拉应力,如此应力超出了坯壳自身的可承受极限,在表面将出现或大或小的裂纹。
因此,实际的工作中相关人员需分析连铸机结晶器振动装置的动态特性,在此基础上减小上述摩擦力作用,保障铸坯表面质量。
结晶器非正弦振动尚未出现之前,大部分连铸机结晶器振动装置均为机械式结构,这类型装置在运行过程中由直流电动机驱动,使装置进入运行状态,借助万向联轴器,在两端转动2个涡轮减速机,但两端构成不同,一端配备有可调节轴套,涡轮减速机后可由万向联轴器辅助,与两个滚动轴承的偏心轴可靠连接,每个偏心轮部位配备有曲柄,该曲柄有滚动轴承,此轴承的振动连杆能起到支撑作用,增强振动台结构的整体稳定性,并同步引发或大或小的振动现象。
机械振动属于正弦曲线振动,振动期间的波形、振幅在任何情况下都无波动。
以某企业为例,其结晶器振动系统为机械驱动,具有一系列不足:振动力从两点逐步传给结晶器,整个传力更为复杂,不能遵循均匀性规定;在高频振动条件下,无法维持相对平稳的运行状态,无论处于高频还是低频状态,振动导向与实际的偏差都相对较大;结构复杂,传力流程多,后续的对中调整、维护工作量大且操作不易;控制效率低且可靠性不足,受外部因素干扰大,无法长时间保持稳定的振动波形条件;不能根据需求调整振动曲线,不具备在线设置振动波形功能。
连铸结晶器振动工艺参数研究与快捷模型开发

《连铸结晶器振动工艺参数研究与快捷模型开发》xx年xx月xx日CATALOGUE 目录•引言•连铸结晶器振动工艺基础理论•连铸结晶器振动工艺参数研究•基于神经网络的连铸结晶器振动模型开发•基于遗传算法的连铸结晶器振动工艺参数优化•结论与展望01引言连铸结晶器振动在提高铸坯质量和产量方面具有重要作用,但缺乏系统研究和模型支持。
本研究旨在解决现有振动工艺参数优化和模型开发的问题,为提高连铸结晶器振动效果提供理论支撑和实践指导。
研究背景与意义1研究内容与方法23研究连铸结晶器振动的基本原理和影响因素。
研究连铸结晶器振动工艺参数优化方法,包括振动频率、振幅、波形等参数的优化。
研究基于数据挖掘和机器学习的连铸结晶器振动模型构建方法,并开发相应的快捷模型。
研究创新点与特色01本研究将振动原理与工艺参数优化相结合,为连铸结晶器振动工艺参数优化提供了新的思路和方法。
02引入数据挖掘和机器学习技术,构建连铸结晶器振动模型并开发快捷模型,为提高模型预测精度和计算速度提供了新的途径。
03本研究将理论与实践相结合,为提高连铸结晶器振动效果提供了具有可操作性的方案和建议。
02连铸结晶器振动工艺基础理论连铸结晶器振动工艺原理是利用振动机构周期性地对连铸结晶器进行振动,以破坏连铸结晶器内钢水的液面,减少钢水在结晶器内的流动,达到减少连铸坯振痕深度的目的。
连铸结晶器振动工艺的原理基于流体力学和机械振动学的基本理论,通过分析结晶器内钢水的流动状态,确定合适的振动频率和振幅,使结晶器振动对钢水液面的破坏达到最佳效果。
连铸结晶器振动工艺原理连铸结晶器振动工艺的数学模型是描述结晶器振动过程中各种物理量之间相互关系的数学表达式,它可以指导工艺参数的优化和预测振痕深度。
目前,常用的数学模型有经验公式、有限元法、数值模拟等。
这些模型各有优缺点,需要根据实际生产情况选择合适的模型。
同时,数学模型的建立需要大量的实验数据和计算资源。
连铸结晶器振动工艺的数学模型连铸结晶器振动工艺参数包括振动频率、振幅、波形、振动时机等。
小方坯连铸机结晶器振动偏摆标准量化分析
小方坯连铸机结晶器振动偏摆标准量化分析摘要:本文采取两种方法,一是按仿弧振动,二是根据结构角度,来对固有偏摆值进行计算,且结合以往经验以及数据积累,获取相应的振动偏摆标准,在此基础上,针对结晶器振动偏摆,就能够判断其有没有合格,总之通过文章的探究,以期能为相关人员提供借鉴。
关键词:结晶器;偏摆标准;结构角度;仿弧振动引言:对于结晶器振动装置来讲,常常被用来支撑结晶器,同时让其根据振动规律,进一步来上下振动。
针对振动偏摆数据,如果其超过标准,将对产品质量造成影响,有的时候,还会造成一系列事故,例如漏钢。
现如今在国内大部分钢厂中,都开展产品质量升级,人们更加注重振动偏摆。
理想情况下,对于结晶器振动来讲,是做仿弧振动的。
不过因为一系列因素,比如设置结构以及安装方法等,难以彻底做仿弧振动,发生偏摆的现象。
在这样的情况下,会对产品质量造成影响,如果情况严重的话,会引起漏钢。
如今大多数企业选择了振动偏摆测试仪,可以对偏摆数据进行测量。
该测试仪有着较多的构成成分,比如振动传感器,数量为2,信息采集系统等。
通常情况下,将传感器置于法兰,由此开展测量。
能够同时测量多个方向的测量信号,也就是X方向、Y方向以及Z方向(即垂直方向)。
不过现如今国内不存在统一的振动偏摆标准,判定数据有没有超过标准。
文章将某小方坯连铸机当作例子,对偏摆标准进行计算。
1.X方向振动偏摆标准理想情况下,该方向偏摆数据应是零,存在较多的因素,可能对偏摆值造成影响,一般体现于以下几点。
第一,测量误差,当放置传感器时,不可以和中心线彻底平行,不然的话,会致使测量误差。
第二,铰接点间隙,游隙形成的偏摆误差。
第三个常见因素是:振动台结构刚度[1]。
结合以往经验与数据积累,用X 来表示这一方向的偏摆标准,数值不超过200微米。
2.Y方向振动偏摆标准由于传感器置于法兰,来开展测量,会让该方向形成固有偏摆值。
也就是理想状况下,该方向偏摆数据,存在固有偏摆值。
不锈钢板坯连铸结晶器振动系统的故障分析及对策
不锈钢板坯连铸结晶器振动系统的故障分析及对策庞伟林①(柳钢中金不锈钢有限公司设备工程部 广西玉林537624)摘 要 柳钢中金不锈钢板坯连铸机结晶器振动系统是连铸机的主要设备之一,结晶器振动系统如果发生故障,板坯连铸机将面临停产,处理结晶器振动系统的故障的时间直接影响到整个生产的正常运行。
通过对结晶器振动系统的故障分类统计,针对故障的原因进行分析,可以有效的降低系统故障率,避免重复性故障发生概率,对于提高连铸板坯生产产量和质量具有非常重要的意义。
关键词 不锈钢板坯连铸 结晶器振动系统 故障 控制措施中图法分类号 TG155.4 文献标识码 BDoi:10 3969/j issn 1001-1269 2022 Z2 0151 前言广西柳钢中金不锈钢有限公司炼钢厂(一下简称中金炼钢厂)板坯连铸机于2015年7月试投产,主要生产200系不锈钢,铸坯规格160×(600-750)×(8500-10000),1机2流。
洁净振动系统主要是为了防止板坯在冷凝的过程中与铜板粘结一起,出现拉裂或者拉漏[1,2],结晶器上下振动能周期性改变钢液面和结晶器壁的相对位置,有利改善结晶器内壁的润滑状况,减少粘结阻力和摩擦力,从而改善板坯表面质量[3,4,],结晶器振动系统的可以保证板坯生产正常进行,因此振动系统的正常与否直接影响到整个连铸生产的正常运行。
结晶振动系统结构较为复杂,主要是由结晶器振动装置及底座、结晶器(框架结构、结晶器本体),其中通过振动装置和底座控制,使结晶器产出弧形振动。
2 结晶器振动系统发生故障的原因结晶器振动系统是连铸机的主要设备之一,其振动的稳定性直接影响到连铸机的正常运行。
由于投产早期设备状况较好,产量较低,基本能满足生产需求,但随着品种的不断增加,生产负荷加大,该连铸机的振动系统的问题逐渐暴露,板坯连铸机结晶器振动系统在生产中经常出现的故障导致振动故障率高、设备使用率低,生产维修成本高,通过对结晶器振动系统故障的研究分析,发现产生这些问题的原因主要有以下几点:2.1 液压故障原因导致维修成本居高不下,由于液压系统是整个振动系统的关键,液压油站是一个独立的油站,伺服液压系统对油的要求很高(清洁度NAS6级及以上、粘度、水分、机械杂质),而且设备所处的运行环境是高温高湿、粉尘超高,环境也是极易引发故障。
连铸结晶器振动工艺参数
异常情况的预警与处理
预警标准
设定异常参数的阈值,当实时监测数据超过阈值时, 发出预警信号。
预警方式
通过声、光、短信等方式提醒操作人员关注异常情况 。
处理措施
根据异常类型,采取相应的处理措施,如调整振动参 数、清洗结晶器等。
工艺参数的调整与优化建议
调整原则
根据实时监测数据和异常情况,及时调整结晶器的振动参数,确 保连铸过程的稳定性和产品质量。
初始阶段
早期的连铸机采用人工敲击的方式使结晶器振动,这种方 式效率低下且不稳定。
机械式振动阶段
随着机械技术的发展,人们开始采用机械传动装置来实现 结晶器的振动,出现了多种形式的机械式振动装置。
液压式振动阶段
液压技术的引入使得结晶器的振动更加平稳可控,液压式 振动装置逐渐成为主流。
智能化振动阶段
随着计算机技术和传感器技术的发展,结晶器的振动控制 逐渐实现智能化,能够根据实际生产情况自动调整振动参 数,提高铸坯质量和产量。
04
连铸结晶器振动工艺参数的优 化
基于实验的参数优化
实验设计
通过实验方法,对连铸结晶器振 动工艺参数进行优化,需要设计 合理的实验方案,包括选择合适 的实验参数、确定实验范围和实
验步骤等。
数据采集与分析
在实验过程中,需要采集各种数 据,如振动频率、振幅、波形等 ,并对数据进行处理和分析,以 确定各参数对结晶器振动效果的
总结词
随着连铸技术的不断发展,新型振动装置的开发与应 用成为研究重点。新型振动装置应具备更高的稳定性 和可靠性,能够实现更加灵活的振动模式和精确的工 艺参数控制。
详细描述
目前,新型振动装置的开发主要集中在智能化、模块 化和集成化等方面。例如,采用智能传感器和控制系 统,实现对结晶器振动状态的实时监测和自动调整; 采用模块化设计,方便对结晶器进行快速更换和维修 ;采用紧凑型设计,减小设备体积和重量,提高设备 的可靠性和稳定性。这些新型振动装置的开发将为连 铸结晶器振动工艺参数的研究提供更加先进和可靠的 实验平台。
连铸机振动参数的优化
- 63 -工 业 技 术操作。
当再次按下开机按钮POWER 键时,I/O 芯片接收到脉冲信号,触发南桥的触发电路模块,南桥会输出持续的SLP-S3低电平信号到I/O 芯片,I/O 芯片会产生高电位通过72脚将ATX 电源的16脚(绿线)恢复为高电位,使PS-ON 信号为高电平,此时ATX 电源停止工作,完成关机操作。
2 台式机开机电路常见故障与检修方法根据台式机开机电路的工作原理,开机电路最常见的故障包括无法开关机、开机过几秒自动关机、通电后自动开机、主板无法加电等。
产生这些台式机开关故障的原因有很多,在实际维修过程中,需要按照一定的检测步骤来对台式机开机故障进行分析,精准地找到台式机开机电路故障点,否则可能会错过真正的故障点,让检测维修陷入困境。
台式机开机电路故障的检测步骤分为六步,具体检测步骤如下:1)首先检查ATX 电源是否故障。
在ATX 电源接上220V 电压后,使用万用表笔检测16脚(绿线)是否为5V 高电压,9脚(紫线)是否为5V 高电平,短接15脚和16脚或16脚和17脚查看ATX 电源风扇是否强转,如果检测脚无高电平,短接后风扇没有转动则判断ATX 电源故障。
2)检测主板开机插针或开机按钮是否有5V 或3.3V 的高电平。
如果没有则说明ATX 电源到开机插针之间的电路存在故障,检测电路上的稳压芯片和电容电阻是否损坏。
3)检测32.768kHz 的晶体振荡器是否起振。
如果晶振无法工作,南桥芯片也同时瘫痪,检测晶振两端的电压是否在0.5V~1.6V,检测晶体振荡器旁边参与谐振电容电阻是否短路。
4)检测电源开关到南桥或I/O 芯片是否有脉冲信号产生。
按下开机键后,I/O 芯片的67脚68脚是否产生脉冲信号,如果没有,就说明电路故障。
5)检测ATX 电源到南桥或I/O 芯片的PS-ON 信号是否正常输入输出。
如果没有,则说明电路故障。
6)部分主板可能存在CMOS 电池亏电等情况,也有可能导致无法开机。
- 1、下载文档前请自行甄别文档内容的完整性,平台不提供额外的编辑、内容补充、找答案等附加服务。
- 2、"仅部分预览"的文档,不可在线预览部分如存在完整性等问题,可反馈申请退款(可完整预览的文档不适用该条件!)。
- 3、如文档侵犯您的权益,请联系客服反馈,我们会尽快为您处理(人工客服工作时间:9:00-18:30)。
连铸结晶器振动参数取值限度问题
1 前言
随着连铸技术的发展,结晶器振动技术亦不断发展,主要表现在振动参数的选择更加灵
活,振动的工艺效果更好,尤其是振动参数更适合连铸高拉速的工艺要求。
结晶器振动的每一次完善都是突破原有振动参数的取值限度,以适应连铸更高的工艺要求。
随着结晶器非正弦振动形式的开发,本文讨论振动参数的取值限度问题。
2 结晶器振动参数的影响
拉速Vc是连铸工艺控制的一个最关键的参数,因此结晶器振动参数的选择亦必须适合
拉速的要求。
结晶器振动工艺参数对其工艺效果的影响如下:
1)结晶器振动的负滑脱时TN控制铸坯表面的振痕深度,即两者呈增函数关系。
TN越
长,振痕越深。
2)保护渣的消耗量与结晶器振动的正滑脱时间呈增函数关系,正滑脱时间越长,保护
渣消耗量越大。
3)结晶器振动的负滑脱时间率、负滑动量、结晶器上振的最大速度都反映结晶器振动
的工艺效果,但它们不是独立的参数,而且随着结晶器振动形式的确定,一般以其正、负滑脱时间来判定结晶器振动的工艺效果。
基于上述几点,为控制铸坯的振痕深度,希望TN短;而为保证结晶器的润滑效果,增
加保护渣的消耗量,希望正滑脱时间长,为此目的开发了结晶器的非正弦振动形式,从而突破了结晶器正弦振动参数的取值限度。
3 问题的提出
在结晶器非正弦振动中引入波形偏斜率α这一基本参数,增加了振动的独立参数,使振
动参数的选择更灵活,更适合高速连铸的工艺要求。
即在一定的VC条件下,采用非正弦振
动可以明显地降低振动频率f ,即可以保持f 不变,通过调整α来适合Vc的要求。
此外,
非正弦振动可以分别构造结晶器的上振和下振速度曲线。
由此提出:在一定的Vc下,可否
通过不断地增加α而无限地降低f 。
图1示出在一定VC和振幅S时,不同α所对应的tN–f 曲线。
可见α增加,tN–f 曲线
左移。
图2为对应图1中某一tN值时,不同α和f 下的结晶器振动速度Vm–时间t曲线。
这些曲线的特点是,Vm≤0时,Vm–t曲线完全相同;当Vm>0时,随α各f 的不同,Vm–
t曲线不同。
则由图2,一定Vc和f 时,α增加相应地f 减少,但tN–f 曲线保持不变。
上
述问题则可表述为:一定的VC和S条件下,保持结晶器下振速度曲线不变,而不断地改变结晶器上振速度曲线,即通过构造不同的结晶器振动曲线,同时实现α增加和f 降低;而且,α趋近于1、f 趋近于0时,结晶器振动的工艺效果更佳。
为此,需对上述问题进行分析。
QuickTime?and a
TIFF (U ncompressed) decom pressor
are needed to see this picture.
图1 波形偏斜率对负滑脱时间的影响
QuickTime?and a
TIFF (U ncompressed) decom pressor
are needed to see this picture.
图2 不同的结晶器振动速度曲线
4 结晶器振动参数的取值限度
4.1振动参数取值的基本要求
1)α的一般定义
结晶器下振时间TD与α及结晶器振动周期T的关系如式(1):
T(1) 2/)1(TDα−=
由式(1)可得式(2):
α(2)TTD/21−=
按式(2)定义α,对复杂的结晶器振动曲线更具有普通定义。
2)负滑脱时间曲线的一般特点
在正弦振动中,tN–f 曲线的特点是在f 坐标轴上总有f 0、f 1 点。
当f ≤f 0 时,tN≤
0;当f 0<f ≤f 1 时,f 增加,tN增加,而且变化很大;当f >f 1 时,f 增加,tN缓慢减少,
并无限趋近于0。
任何振动形式均为周期性运动,所以结晶器振动的速度总是与其f 成正比。
而出现负
滑脱的必要条件是下振的最大速度要>Vc。
因此,在一定的Vc及一定的振动参数条件下, 其tN–f 曲线总有f 0、f 1点,仅在特殊情况下f 0、f 1点,仅在特殊情况下f 0、f 1点重合,
这个特点是振动结晶器的必然特性。
3)振痕深度及振痕间距
振痕深度的主要影响因素是结晶器振动的负滑脱时间,而振痕间距Pm与振痕深度同样
对铸坯表面质量有极大的影响,增加Pm可以改善铸坯表面质量。
Pm可由式(3)表示。
fVcPm/= (3)
4)振动参数取值的基本要求
连铸振动结晶器的一个基本要求是必须出现负滑脱振动,即tN>0。
因此,下振的最大
速度必须>Vc,即负滑动量必须>0。
结晶器振动的负滑动量NSA定义为:负滑脱期间结晶器相对于铸坯下移的距离。
(4)∫−=
2
1 )(
t
t cm dtVVNSA
式中Vm—结晶器下振的速度;
t1—负滑脱开始时间;
t2—负滑脱结束时间。
负滑脱振动必须满足;
NSA> 0 (5)
4.2 振动参数的取值限度
1)正弦振动参数的取值限度
在正弦振动中,TN可表示为:
t(6) )2/(cos/60 1SfVcfNππ−×=
为使tN >0,应有:
2>Vc(7)Sfπ
式(7)为结晶器正弦振动参数的取值限度,即在一定的Vc和S的条件下,f 总有一个
最小的取值要求。
由式(7)可得
fVcPm/= <(8)Sπ2
可见,采用正弦振动,Pm总有一个取值上限2πS。
为增加Pm而增加S,势必会使tN
增加而增加振痕深度,即控制振痕深度与控制Pm是矛盾的。
一般认为Pm ≥12.7mm时,振
痕过深,坯壳厚度的均匀性明显变差。
所以正弦振动中,不可能同时优化每个方面的工艺效果。
2)非正弦振动参数的取值限度
对于非正弦振动波形的负滑脱时间可表示为:
t(9)[SfVf CNπαπα2/)1(cos/)1(60 1−×−= − ]
为使tN>0,应有:
2>Vc(10) )1/(απ−Sf
式(10)即是对非正弦振动参数取值的一个基本要求。
由于振痕深度取决于TN ,两者
呈增函数关系;高频振动时,保护渣消耗量取决于正滑脱时间;低频振动时,保护渣消耗量取决于NSA。
因此Vc、S、f 一定时,增加α,可使TN减小、NSA和正滑脱时间增加,结
晶器振动的综合工艺效果最好。
如果Vc、S一定,增加α同时降低f 的结果如下。
假设在结晶器一个振动周期内,保护渣的填充量Qm为:
NSALKQm1= (11)
式中 K1—比例常数;
L—铸坯的边长。
而其所要润滑的铸坯表面积Sm为:
S(12)fVcLPL mm/==
单位面积的保护渣消耗量Q则为:
(13)VcNSAfKSQQ mm// 1==
为防止坯壳粘结,要求Q>一定的数值Q0,即Q≥Q0,则有
≥Q(14)fNSA VcKKVc010 / =
式中K0 —仅与钢种、保护渣性能有关的常数。
NSA的最大值为2S,则有:
S f ≥(15) 2/0VcK
Pm的上限为:
≤(16)fVcPm/= 0/2KS
式(15)给出了一般振动参数取值的限度,表明在一定的Vc和S条件下,f 总有一个
与α无关的取值下限,即α趋近于1时,f 不能无限趋近于0。
5 讨论
1)式(15)是关于所有结晶器振动形式的振动参数取值限度的一般要求。
2)由于式(16)的要求,铸坯表面的振痕间距不可能控制得无限大。
3)正弦振动可以用S f >Vc/2π作为一般要求,是因为K0 >1/π。
4)振幅对保护渣消耗量的影响是:高频振动时,降低振幅可增加正滑脱时间,有利于
增加保护渣的消耗量;低频振动时,增加振幅可增加负滑动量,有利于增加保护渣消耗量。
5)开浇初期低拉速、低频率时,振幅应大些;高拉速、高频率时,振幅应小些。
这样
有利于改善结晶器的润滑状况。
6)只有振动参数满足式(15)时,波形偏斜率取值才越大越好;而且,频率越高时,
调整波形偏斜率的工艺效果越好。
7)K0的数值需经过试验确定,取值范围应为0~1/π。
6 结语
频率作为结晶器振动的一个基本参数,任何振动形式,总有一个仅与拉速和振幅有关的
最小取值。
通过波形的调整和改变,无法使频率取无限小的数值。
因此,铸坯表面的振痕间距亦不能取无限大的数值,对其控制亦有一定的限度。
同时对于结晶器振动的波形及波形偏
斜率亦应在一定限度内取值,其值未必越大越好。
了解结晶器振动参数取值的限度,从而可以在此限度内合理地选择振动参数,以取得最好的振动工艺效果。