结晶器振动参数计算
《2024年伺服电机驱动结晶器非正弦振动装置的参数计算与模型仿真》范文
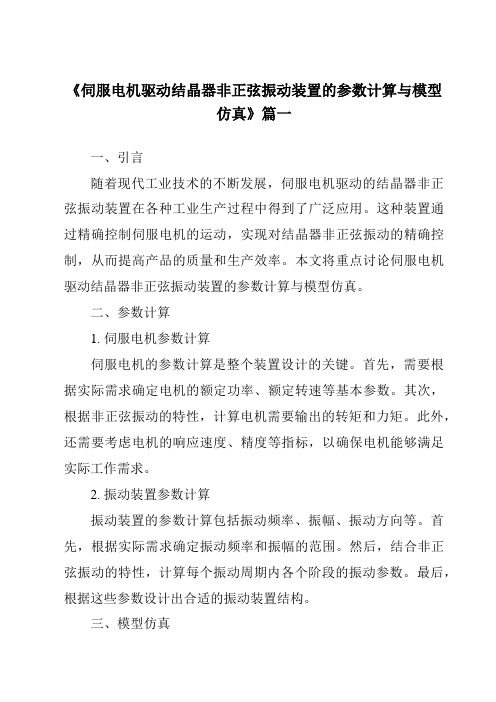
《伺服电机驱动结晶器非正弦振动装置的参数计算与模型仿真》篇一一、引言随着现代工业技术的不断发展,伺服电机驱动的结晶器非正弦振动装置在各种工业生产过程中得到了广泛应用。
这种装置通过精确控制伺服电机的运动,实现对结晶器非正弦振动的精确控制,从而提高产品的质量和生产效率。
本文将重点讨论伺服电机驱动结晶器非正弦振动装置的参数计算与模型仿真。
二、参数计算1. 伺服电机参数计算伺服电机的参数计算是整个装置设计的关键。
首先,需要根据实际需求确定电机的额定功率、额定转速等基本参数。
其次,根据非正弦振动的特性,计算电机需要输出的转矩和力矩。
此外,还需要考虑电机的响应速度、精度等指标,以确保电机能够满足实际工作需求。
2. 振动装置参数计算振动装置的参数计算包括振动频率、振幅、振动方向等。
首先,根据实际需求确定振动频率和振幅的范围。
然后,结合非正弦振动的特性,计算每个振动周期内各个阶段的振动参数。
最后,根据这些参数设计出合适的振动装置结构。
三、模型仿真模型仿真是验证参数计算结果的重要手段。
通过建立仿真模型,可以模拟实际工作过程中伺服电机驱动的结晶器非正弦振动装置的运动状态,从而验证参数计算的正确性。
1. 建立仿真模型建立仿真模型需要选择合适的仿真软件和仿真方法。
首先,根据实际装置的结构和运动特性,建立相应的仿真模型。
然后,设定仿真参数,如伺服电机的转速、转矩等,以及振动装置的振动频率、振幅等。
最后,进行仿真实验。
2. 仿真实验与分析通过仿真实验,可以观察到伺服电机驱动的结晶器非正弦振动装置的运动状态。
通过对仿真结果的分析,可以验证参数计算的正确性。
同时,还可以通过调整仿真参数,优化装置的性能。
例如,可以通过调整电机的转速和转矩,优化振动的稳定性和精度;通过调整振动装置的振动频率和振幅,优化产品的结晶质量和生产效率。
四、结论本文对伺服电机驱动结晶器非正弦振动装置的参数计算与模型仿真进行了研究。
通过合理的参数计算和模型仿真,可以确保装置的准确性和可靠性。
连铸结晶器振动工艺参数
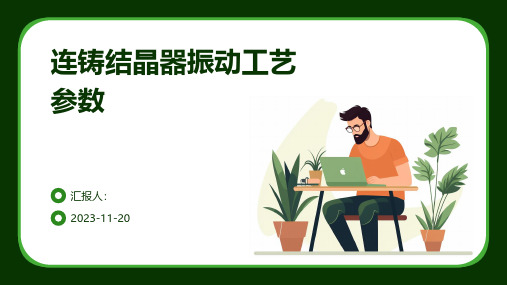
连铸结晶器振动工艺参数2023-11-20汇报人:CATALOGUE目录•结晶器振动工艺参数概述•振动频率•振幅•振动波形•结晶器与铸坯间的摩擦系数•实际生产中的结晶器振动工艺参数调整与优化01结晶器振动工艺参数概述CHAPTER减少摩擦和磨损改善润滑效果促进坯壳均匀生长030201结晶器振动的作用工艺参数对连铸坯质量的影响振动频率01振幅02振动波形03结晶器振动工艺参数的设定与调整CHAPTER振动频率02定义单位振动频率的定义与单位结晶组织裂纹和缺陷润滑和传热振动频率对铸坯表面质量的影响合适振动频率的选择与调整铸坯材质和规格实时监测和调整CHAPTER振幅03定义单位振幅的定义与单位结晶组织振幅过大可能导致铸坯内部气孔和夹杂物的形成,影响铸坯的质量。
气孔和夹杂裂纹振幅对铸坯内部组织的影响铸坯材质铸坯断面尺寸设备性能操作经验01020304合适振幅的选择与调整CHAPTER振动波形04正弦波、方波、三角波等常见波形介绍正弦波方波三角波表面质量不同的波形会对铸坯表面质量产生显著影响。
例如,正弦波能够显著减少铸坯表面裂纹的产生,而方波由于其强烈的振动冲击,可能会导致铸坯表面质量的下降。
内部结构波形也会影响铸坯的内部结构。
例如,三角波由于其稳定性和均匀性,能够促进铸坯形成均匀且稳定的组织结构。
不同波形对铸坯质量的影响选择原则调整策略合适波形的选择与调整05结晶器与铸坯间的摩擦系数CHAPTER通常采用试验测定法,通过模拟结晶器与铸坯的实际接触情况,测量出摩擦力与压力,并计算得到摩擦系数。
摩擦系数的定义与测量方法测量方法定义振动频率摩擦系数的大小直接影响到结晶器与铸坯之间的摩擦力,进而影响到振动频率的选择。
过高的摩擦系数要求更高的振动频率以克服摩擦力,确保铸坯的顺利下滑。
摩擦系数的变化会对振幅产生一定影响。
当摩擦系数增大时,为了保持铸坯在结晶器内的稳定性,可能需要适当增大振幅,以提供足够的振动力。
摩擦系数的不同可能导致振动波形的变化。
结晶器设计计算

结晶器设计计算----2a54667e-6eba-11ec-8c1c-7cb59b590d7d 通过结晶器的热流量通过结晶器释放的热流可计算如下q=levp{c1(te-tl)+lf+cs(ts-to)}(3.1)式中:q:结晶器钢水放出的热量,kj/min;l:结晶器横截面周长,4.012m;e:出结晶器坯壳厚度,0.012m;v:拉速,2.2m/min;p:钢水密度,7.4×10⒊kj/kg℃由此可得:q=levp{c1(te-tl)+lf+cs(ts-to)}=62218kj/min结晶器水缝面积计算结晶器的水隙面积与单位水流量(冷却强度)、钢坯尺寸和冷却水流量有关。
模具的水隙面积可通过以下公式计算:f=qks×106/(3600v)(mm2)(3.2)式中:qk:单位水流量m3/nm,经验值取100-500m3/nm;取100m3/nm。
s:结晶器周边长度,4×120×103m;v:冷却水流速,取6-10m/s,实际取8m/s;即结晶器水缝面积为:f+q ks×106/(3600v)=1.67×103mm33.5结晶器的冷却系统为了使模具壁具有高导热性,铜壁和冷却水之间不会产生水垢和沉积物。
由于模具的高热负荷,接触模具壁的冷却水有时达到汽化温度。
为了防止结垢,水必须软化或脱盐[9]。
结晶器内冷却水的流量,一般按断面周长长度每毫米2-2.5每毫米计算。
经过净化及软处理的水一般都是循环使用。
采用封闭式供水系统。
充分利用回水系压有利于节能。
3.5.1结晶器倒锥钢水在结晶器内凝固是因坯壳收缩形成气隙,通常是将结晶器作成倒锥度,后者定义为:△ = (s向上-s向下)/s向上×L(3.3),其中:△: 结晶器反向锥度%/M;s上,s下:结晶器的上边口,下边口长;l:结晶器长度。
倒锥度值不应太小或太大。
如果它太小,它几乎没有影响,如果它太大,它增加了毛坯拉拔阻力,甚至阻止钢,不能生产[ 9 ]。
结晶器振动

第1章绪论第1章绪论1.1连续铸钢技术的发展钢水凝固成型有两种方法:传统的模铸法和连续铸钢法。
连续铸钢是把液态钢用连铸机浇注、冷凝、切割而直接得到铸坯的工艺。
是连接炼钢和轧钢的中间环节,是炼钢厂的重要组成部分[1]。
连铸的出现从根本上改变了一个世纪以来占统治地位的钢锭——初轧工艺,为炼钢生产向连续化、自动化方向的发展开辟了新的途径[2]。
1.1.1 连续铸钢技术的发展历程早在十九世纪中期美国人塞勒斯(1840年)、赖尼(1843年)和英国人贝塞麦(1846年)就曾提出过连续浇注液体金属的初步设想,并用于低熔点有色金属的浇铸;但类似现代连铸设备的建议是由美国人亚瑟(1886年)和德国人戴伦(1887年)提出来的。
他们的建议中包括有水冷的上下敞口的结晶器、二次冷却段、引锭杆、夹辊和铸坯切割装置等设备,当时用于铜和铝等有色金属的浇铸。
1933年德国人容汉斯建成第一台结晶器可以振动的连铸机,并用其浇铸黄铜获得成功,后又用于铝合金的工业生产。
结晶器振动的采用,不仅可以提高浇注速度,而且使钢液的连铸生产成为可能,容汉斯因此成为现代连铸技术的奠基人。
但连续铸钢步入工业生产阶段,应当归功于英国人哈里德提出的“负滑脱(Negative Strip)”概念。
在哈里德的负滑脱振动方式中,结晶器下振速度比拉坯速度快,铸坯与结晶器壁间产生了相对运动,真正有效的防止了铸坯与结晶器壁的粘结,使钢连续浇铸的关键性技术得以突破[3]。
1.1.2 连续铸钢的优越性连续铸钢与模铸的根本差别在于模铸是在间断的情况下,把一炉钢水浇注成多根钢锭,脱模之后经初轧机开坯得到钢坯;而连铸是把一炉钢水燕山大学工学硕士学位论文连续地注入结晶器,得到无限长的铸坯,经切割后直接生产铸坯。
基于这一根本差别,连铸和模铸比较,就具有许多明显的优越性[4-9]:(1)简化了钢坯生产的工艺流程,节省大量投资,省去了模铸工艺中脱模整模均热及初轧等工序,缩短了钢水到钢坯的周期时间。
结晶器振动全解
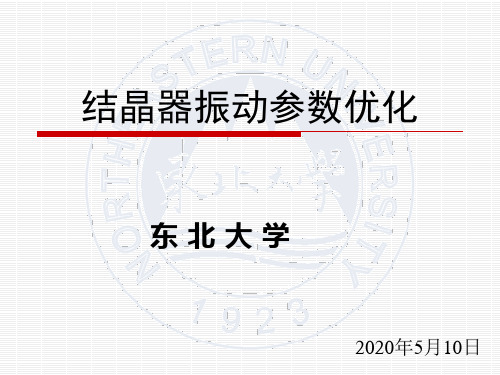
连铸技术
结晶器振动参数对拉速的影响
研究表明,采用高频振动有利于提高拉坯速度, 而且提高拉速还有利于减少振痕。但在一定的 工艺条件下,拉坯速度受到冷却速度及设备精 度的限制,提高拉速将会导致拉漏率的上升。
23
连铸技术
2.2. 结晶器正弦振动的特性分析
目前描述负滑脱的参数较多,对于同一振幅、频率和拉 速的情况下,这些参数给出了不同的数值。但它们当 中独立的参数只有两个:负滑动率 NS 和负滑脱时间 tN。因为负滑脱参数直接关系到铸坯的脱模和铸坯的 质量,所以参数 NS和tN被称为工艺参数。 目前国外有关文献报道,大多数的负滑脱时间取值范围 在 0.1s ~ 0.25s,认为对于不同的钢种最佳负滑动 时间为 0.1s 左右。至于负滑动率 NS,国内外有关 文献报道在 NS值为-20%~240%范围内变化进行 浇铸,结果对铸坯脱模及表面质量没有任何不利影响。 可见,对于负滑动率 NS 的取值范围是很宽的,工艺 参数的确定主要是确定负滑动时间。
27
连铸技术
28
连铸技术
① 全部 tN 曲线与 Ns=-0.024 的射线交于顶点,在一 定的拉速范围内,对于任何一拉速和 tN 曲线都有两 个交点,它们分别对应一个高频率和一个低频率。这 两个频率对应相同的负滑动时间。 ② 全部 tN、Ns 曲线相交于坐标系原点 0 点,曲线的 下部相互靠近,并重合于 Ns=-0.3634(负滑动率极 限值)曲线。s 值越大它们越靠近,tN值越小它们重 合的线段越长,tN=0 时与 Ns=-0.3634 曲线全部 重合。 ③ 增大 s 值,可增大 tN 曲线在拉速 Vc轴上的投影, 因此可根据不同的工作拉速选择相应的 s 值。
4
连铸技术
1—同步式振动 2—负滑脱振动 3—正弦振动 图 1 结晶器振动方式
板坯连铸机结晶器振动液压装置的设计及计算

科 技 创 新
板坯连铸机结晶器振动液压装置的设计及计算
蒋 昊宜 赵 东
( 中 国第 一 重 型机 械 集 团 大连 设 计研 究 院 , 辽 宁 大连 l 1 6 6 0 0 ) 摘 要: 文 章介 绍 了某型 不锈 钢 板坯 连 铸机 组 结 晶 器振 动液 压 装 置的 设计 计 算过 程 计 算 系统 所 需流 量 , 配 置核 心 液压 元件 型 号 规格 , 对循 环 冷却 系统进 行 了精 确 计算 。 关键词: 连铸结晶器; 振动 ; 液压
单 个液压缸输 出功率为
一
,
工作则需要 1 0 2 U m i n , 取效率系数 n 8 , 得1 2 7 U mi n 。 ( 2 ) x t , gt ̄  ̄ 运 动( c = £ L 5 ) 时, 振动所需 的最大供 油流量
同理在 1 y 2 — 3 r T , I 4 周期 计算得 出单个 液压缸输 出功 率为 6 . 1 k w , 取 平 均值 5 . 5 k w 。 因此生 成热量为 H = k ( P p - 2 P j = 2 9 . 5 K w 。 此热功率 占输入功 率 正 弦振动 的速 度为 5 5 k W 的5 3 %。 结 晶器振 动液压装 置的冷却装 置要 比普 通液压站 大 。 这 V= uc o s  ̄ t =A ・ 2 7 r f・ c o s ( 2 7 r f t ) 是 因 为在 选择 系 统压 力和 流 量 的时候 是按 照 两 者 同时 达到 极值 考 虑 最大速度 V 一为 A 2 , r r f , 此 速度 下单缸 最大供 油流 量 8 0 . 1 9 U mi n , 的, 而实际上两 者极值并不 同时出现 。 两个 液压缸 同时工作则需要 1 6 0 . 3 Um i n 。 5结束 语 ( 3 ) 非对称 系数 C = 0 . 7时 , 振动 所需 的最 大供 油流量 对结 晶器振 动装置在 正弦运动 工况 和非正 弦运动 工况下 的负 载和 随着非对称系数 c的不断变大, 下降速度提高。认为 C = 0 . 7 是最大 流量进行 了分析对 比和计 算 , 并在此 基础上配置 核心液压 元件规格 。为 非对 称系数 , 此时 最大速度 出现 在下降段 。 令对 称正弦周 期为 T , 频率 为 后续 的板坯 连铸机组结 晶器振动 液压装置 的设 计提 供 指导 。 参 考 文 献 f , 角 速度 为 ∞ , 非对 称正 弦下 降周期 , 频 率为 f _ , 最大速 度为 A l 【 f 2 竹 。 此 速度下 单缸最 大供油流 量 6 4 . 4 U m i n ; 乘 以塞腔 面积 , 得 到单缸 最大 的 【 1 J 解 通护 . 结晶 器液 压振 动 缸 负载 力的计 算l J 1 . 液 压 气 动 与 密封 , 2 0 1 0 回油流量 1 3 3 . 6 U m i n 。 双缸 同时 工作则需要供 油 1 2 8 . 8 l J mi n , 回油 2 6 7 L / ( 2) : 3 O 一 3 2 . m l n0 【 2 ] 张 梁敬. 结 晶器液压 振动 装置 的设计及 计 算【 J J . 重 工与起 重技 术 , 2 0 l I 综 合( 1 ) — ( 3 ) , 据此 , 选 择泵 的最 大流 量为 1 3 0 U mi n , 只满足 液压 缸运 动的 ( 1 ) : 1 6 - 1 8 . 平 均流量 即可 。出现最大尖 峰流量 时刻 , 由蓄能器提供 油液 。 [ 3 1 z春行. 液压控 制 系统[ M J . 北京 : 机械 工业 出版社 , 1 9 9 9 , 5 : 1 4 8 . 3负载计算和伺 服阀选择
方坯结晶器液压振动功能说明书
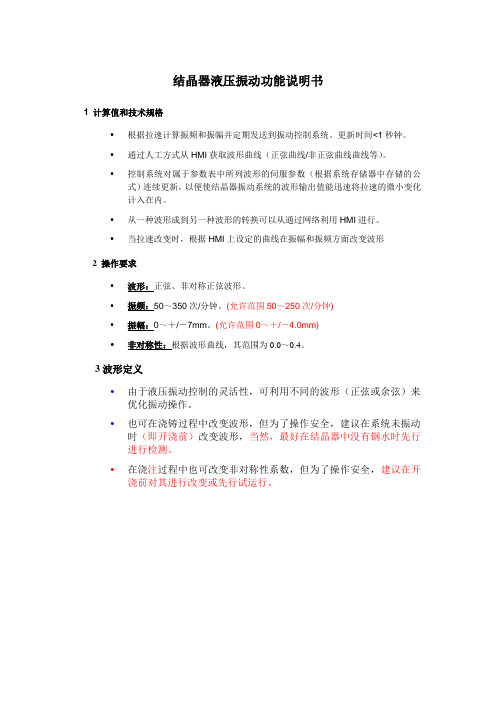
结晶器液压振动功能说明书1 计算值和技术规格•根据拉速计算振频和振幅并定期发送到振动控制系统。
更新时间<1秒钟。
•通过人工方式从HMI获取波形曲线(正弦曲线/非正弦曲线曲线等)。
•控制系统对属于参数表中所列波形的伺服参数(根据系统存储器中存储的公式)连续更新,以便使结晶器振动系统的波形输出值能迅速将拉速的微小变化计入在内。
•从一种波形成到另一种波形的转换可以从通过网络利用HMI进行。
•当拉速改变时,根据HMI上设定的曲线在振幅和振频方面改变波形2 操作要求•波形:正弦、非对称正弦波形。
•振频:50~350次/分钟。
(允许范围50~250次/分钟)•振幅:0~+/-7mm。
(允许范围0~+/-4.0mm)•非对称性:根据波形曲线,其范围为0.0~0.4。
3波形定义•由于液压振动控制的灵活性,可利用不同的波形(正弦或余弦)来优化振动操作。
•也可在浇铸过程中改变波形,但为了操作安全,建议在系统未振动时(即开浇前)改变波形,当然,最好在结晶器中没有钢水时先行进行检测。
•在浇注过程中也可改变非对称性系数,但为了操作安全,建议在开浇前对其进行改变或先行试运行。
1. 操作员站-+C1LC801~+C1LC808“1~8流结晶器操作箱”-L1-HMI “主操作室”2. 操作方式-从+C1LC801~+C1LC808手动开始/停机-从L1-HMI 手动开始/停机-从L1-HMI手动设定调节设定值-从L1-HMI 手动开始校准-自动开始/停机-选择一级参数表-从L1-HMI 上进行一级参数调整3.操作3.1 手动开始/停机前提:-选择“关断”方式、“准备好”、“浇铸”方式或“拉尾坯”方式-液压缸校准完毕-振动液压系统就绪-振动系统状态良好-阀门通电-位置传感器无故障功能:通过按+C1LC801~+C1LC808上的灯光按钮“结晶器振动:开始”启动结晶器。
通过按+C1LC801~+C1LC808上的灯光按钮“结晶器振动:停止”停止结晶器。
《伺服电机驱动结晶器非正弦振动装置的参数计算与模型仿真》范文
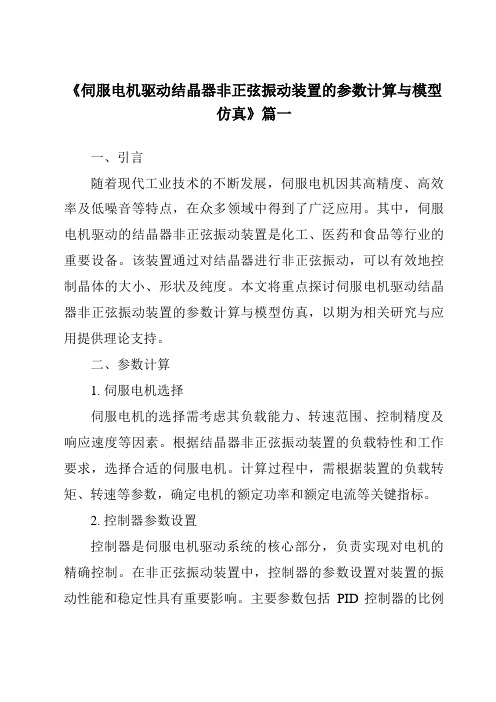
《伺服电机驱动结晶器非正弦振动装置的参数计算与模型仿真》篇一一、引言随着现代工业技术的不断发展,伺服电机因其高精度、高效率及低噪音等特点,在众多领域中得到了广泛应用。
其中,伺服电机驱动的结晶器非正弦振动装置是化工、医药和食品等行业的重要设备。
该装置通过对结晶器进行非正弦振动,可以有效地控制晶体的大小、形状及纯度。
本文将重点探讨伺服电机驱动结晶器非正弦振动装置的参数计算与模型仿真,以期为相关研究与应用提供理论支持。
二、参数计算1. 伺服电机选择伺服电机的选择需考虑其负载能力、转速范围、控制精度及响应速度等因素。
根据结晶器非正弦振动装置的负载特性和工作要求,选择合适的伺服电机。
计算过程中,需根据装置的负载转矩、转速等参数,确定电机的额定功率和额定电流等关键指标。
2. 控制器参数设置控制器是伺服电机驱动系统的核心部分,负责实现对电机的精确控制。
在非正弦振动装置中,控制器的参数设置对装置的振动性能和稳定性具有重要影响。
主要参数包括PID控制器的比例系数、积分系数和微分系数等。
这些参数的设定需要根据装置的实际情况,通过试验和仿真进行优化。
3. 振动装置参数计算非正弦振动装置的参数包括振动频率、振幅、相位等。
这些参数的计算需根据结晶器的特性、生产需求及设备安装空间等因素进行综合考量。
通过理论分析和仿真试验,确定合适的振动参数,以满足生产要求。
三、模型仿真为了验证参数计算的正确性和装置的性能,本文采用仿真软件对伺服电机驱动的结晶器非正弦振动装置进行建模和仿真。
具体步骤如下:1. 建立装置的数学模型根据装置的工作原理和特性,建立数学模型。
该模型应包括伺服电机的运动方程、控制器的控制策略以及非正弦振动的数学描述等。
通过数学模型,可以描述装置的动态特性和静态特性。
2. 仿真分析利用仿真软件对数学模型进行仿真分析。
通过改变控制器的参数、振动参数等,观察装置的振动性能、稳定性及响应速度等指标的变化。
通过仿真分析,可以优化装置的参数设置,提高装置的性能。
- 1、下载文档前请自行甄别文档内容的完整性,平台不提供额外的编辑、内容补充、找答案等附加服务。
- 2、"仅部分预览"的文档,不可在线预览部分如存在完整性等问题,可反馈申请退款(可完整预览的文档不适用该条件!)。
- 3、如文档侵犯您的权益,请联系客服反馈,我们会尽快为您处理(人工客服工作时间:9:00-18:30)。
1)结晶器振动的正弦速度曲线的数学表达式为:V=(πfS/1000)sim((2πf/60)t);式中V( m/min)为结晶器运动速度、S=2A( mm)为振程即2倍于振幅A、f( 1/min)为振动频率。
2)当V=Vc时:负滑动(脱)时间=下降的速度大于拉速的下降时间tn=60/(πfd)arccos(1000Vc/s/π/fd)。
3)设:Z=S/Vc( mm*min/m);则tn=60/(πfd)arccos(1000/s/π/fd/Z)。
A为振幅,单位mm,Vc为拉速,单位m/min,f为频率,单位1/min。
取不同的Z值可画出负滑动时间随振动频率变化的曲线,称为负滑动曲线( tn——f)。
4)据有关资料和厂家的数据,负滑动时间取值范围在0.1~0.25s,认为对于不同的钢种最佳负滑动时间为0.1s左右。
且一般对于底碳钢负滑动时间不小于0.1s,而中碳钢负滑动时间应不小于0.07~0.1s。
1)负滑动率NS=(Vc-Vm)/Vc×100%,式中:Vc为拉坯速度( m/min),Vm为结晶器振动平均速度(Vm=2Vmax/π=2fS/1000;m/min),Vmax为结晶器振动最大速度(Vmax=πfS/1000; m/min)。
正弦NS:20~-240%;非正弦NS:-53.4~-108.8%(有关文献报道的日本钢管公司福山厂5号连铸机)。
2)NS=1-(2Vmax/πVc);当Vc=Vmax时,结晶器中的坯壳处于受拉和受压的临界状态。
此时NS=36.34%为负滑动率的极限值,当Vc>Vmax时,即NS>36.34%时,结晶器对坯壳不产生负滑动;NS<36.34%时产生负滑动。
通过采用数值法上计算机可求得:当NS=2.4%时负滑动时间取得最大值。
3)tn=60/(πfd)arccos(2/π(1-NS));在NS值给定的情况下,tn与f成反比双曲线关系;该曲线称为负滑动率等值曲线。
负滑动时间比率NSR=tn/tc×100%,式中:tn为负滑脱时间(s),tc=60/f为结晶器振动周期(s)。
有些文献中定义:负滑动时间比率
NSR=tn/0.5T×100%,T=60/f;二者相差一倍。
控制模型:频率f=C3 +C4 *Vc(次/分);振程S=C1+C2*Vc
负滑动超前量(负滑动时间里结晶器相对铸坯的位移量;mm)NSA=Ssim(πf/60tn)-1000Vc/60tn,式中:V为结晶器振动下降速度( m/min),Vc为拉坯速度( m/min),S=2A( mm)为振程即2倍于振幅A。
正弦NSA=3~5,非正弦NSA=3.8~5.11,
P为波形偏斜率,P=(tu-td)/tc,上升频率fu=f/(1+P),下降频率fd=f/(1-P) P=0~0.4
振痕间距=拉速Vc*1000/频率f
负滑脱量为下降速度大于拉速时行走的距离,单位mm
正滑动时间tp=tc-tn:正弦tp: 0.24~0.47。