挖掘机动臂强度分析
70吨大型液压挖掘机动臂有限元分析
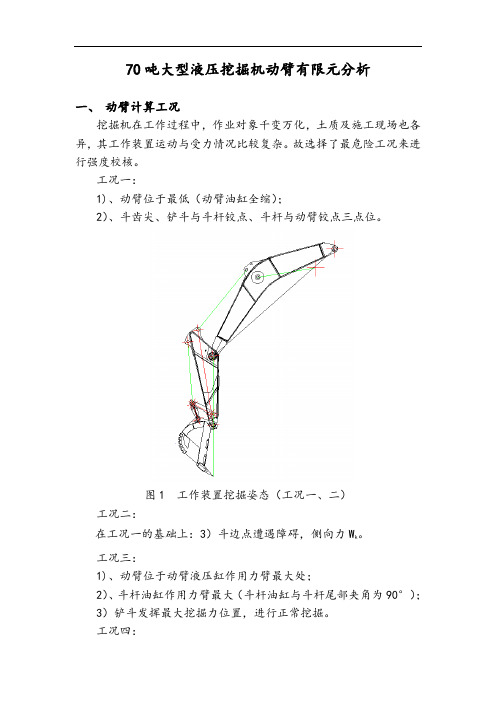
70吨大型液压挖掘机动臂有限元分析一、动臂计算工况挖掘机在工作过程中,作业对象千变万化,土质及施工现场也各异,其工作装置运动与受力情况比较复杂。
故选择了最危险工况来进行强度校核。
工况一:1)、动臂位于最低(动臂油缸全缩);2)、斗齿尖、铲斗与斗杆铰点、斗杆与动臂铰点三点位。
图1 工作装置挖掘姿态(工况一、二)工况二:在工况一的基础上:3)斗边点遭遇障碍,侧向力W k。
工况三:1)、动臂位于动臂液压缸作用力臂最大处;2)、斗杆油缸作用力臂最大(斗杆油缸与斗杆尾部夹角为90°);3)铲斗发挥最大挖掘力位置,进行正常挖掘。
工况四:在工况三的基础上:3)斗边点遭遇障碍,侧向力W k。
图2 工作装置挖掘姿态(工况三)三、斗杆受力分析1)、斗杆铰点载荷的确定①计算工况一:θ1=-41.68°,θ2=131.684°,θ3=180°。
从重庆大学反铲分析软件中提取进行有限元分析所需要的数据:动臂缸作用力为:-927.87kN;斗杆缸作用力为:423.386KN;铲斗缸作用力为:318.225kN;动臂油缸铰点:Rx=915.301 kN;Ry=150.391 kN;斗杆油缸铰点:Rx=264.623 kN;Ry=330.5 kN;斗杆动臂铰点:Rx=-370.888 kN;Ry=-376.969 kN;图3挖掘工况一、二示意图②计算工况二:在工况一的基础上,加上侧齿障碍产生的弯矩和扭矩,及侧向力W k=23.638 KN。
③计算工况三:θ1=4.504°,θ2=111.993°,θ3=151.371°。
图4 挖掘工况三示意图从重庆大学反铲分析软件中提取进行有限元分析所需要的数据:动臂缸作用力为:-927.87 kN;斗杆缸作用力为:834.065 KN;铲斗缸作用力为:584.42kN;动臂油缸铰点:Rx=656.101 kN;Ry=656.106 kN;斗杆油缸铰点:Rx=832.213 kN;Ry=55.55 kN;动臂斗杆铰点:Rx=-1046.18 kN;Ry=20.38 kN;④计算工况四:在工况三的基础上,加上侧齿障碍产生的弯矩和扭矩,及侧向力W k=15.165 KN。
挖掘机动臂有限元模态分析
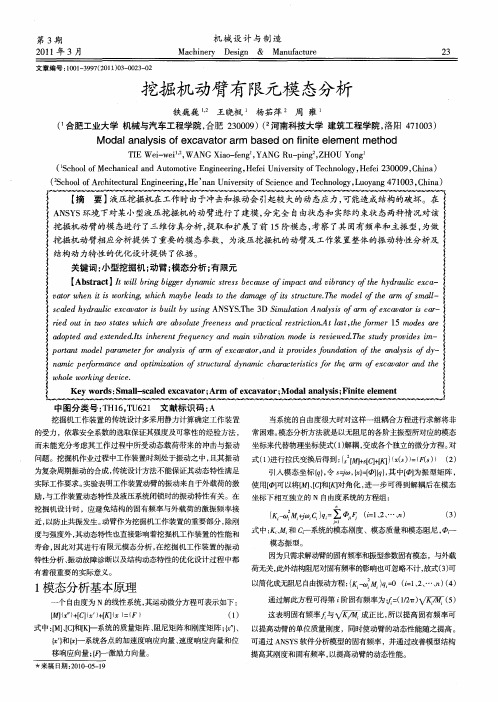
中 图分 类 号 :H1 ,U 2 文 献标 识码 : T 6T 6 1 A
挖掘机工作装置的传统设计多采用静力计算确定工作装置
当系统的 自由度很大时对这样一组耦合方程进行求解将非 模态分析方法就是以无阻尼的各阶主振型所对应的模态 的受力 ,依靠 安全系数的选取保证其强度及 可靠性的经验方法 , 常困难 。 1解耦 , 变成各个独立的微分方程 。 对 而未能充分考虑其工作 过程 中所受动态载荷带来 的冲击与振动 坐标来 代替物理坐标使式( ) 问题 。挖掘机作业过程中工作装置时刻处于振动之 中, 且其振动 式() 1 进行拉氏变换后得到: 怕【] ) ()_ ) () s c+ { s }( } 2 陶 x 5
r dotntos e w i r asltfens adpat a rs i i .tatte o e 5moe r i u i w t s hc ae boue rees n r i etco A s. r1 dsae e t a h c c l rtn l h f aotdadetn e.sihrn eunyadm i ir i oeirve e.h td rvdsi— dpe n xeddI n eetrqec n anv a o m d s eiw dTes y poie m— t f b tn u p r t oe p a eefr ayio m cv o, dipoiefu dt no eaa s — ot dl a m tro l sf a o e aa ra t rvds on ai t l i o d n a m r n a s r f x t n o f h n y sf y n ip r r neadot i i rcua ya i caat ii frt m o cv o dte m f a c e omac i z o o s utr dn c hr esc o ea e aa ra n p m a nf t t l m c r ts h r f x t n h
浅谈挖掘机的动臂有限元及改进设计
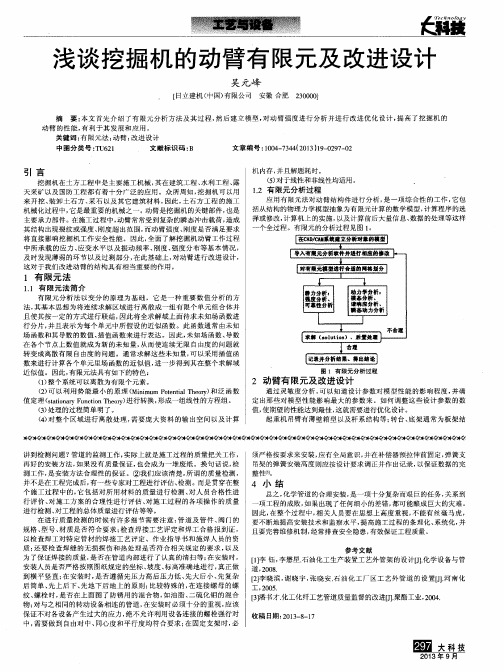
吴 元 峰
【 日立建机 ( 中国) 有 限公司 安徽 合肥 2 3 0 0 0 0 ]
摘 要: 本文 首先介 绍 了有 限元分析 方法及其 过程 , 然后建 立模型 , 对 动臂强度 进行分析 并进行 改进优 化设计 , 提高 了挖掘机 的 动臂 的性能 , 有 利于其发 展和应用 。 关键词 : 有 限元 法 ; 动 臂; 改进设计
ቤተ መጻሕፍቲ ባይዱ
讲到检测 问题 ?管道的监测工作, 实际上就是施工过程的质量把关工作, 再好的安装方法 , 如 果没有质量保证 , 也会 成为一堆废纸 。换句 话说, 检 测工作, 是安装方法合理 性的保证 。⑦我们应 该清楚 , 所谓 的质 量检测, 并不是在工程完成后 , 有一些专家对工程进行评估 、 检 测 。而 是 贯 穿 在 整 个施工过 程中 的, 它包括对所 用材料 的质 量进行检 测、 对人 员合格 性进 行评价 、 对施工方 案的合理性 进行评估 、 对施工过程 的各项 操作 的质量 进行检测 、 对工程 的总体质量进行评估等等 。 在进行质 量检测 的时候有许 多细节需要注 意 : 管道及管件 、 阀门的 规 格、 型号 、 材质是 否符合要 求: 检查焊接 工艺评定 和焊工合格 报到证 , 以检查焊 工对 特定管 材的焊接工 艺评定 、作 业指导 书和施焊人 员 的资 质; 还要检 查焊缝 的无 损探伤和 热处理是 杏符合相关规 定的要 求, 以及 为了保 证焊接 的质量 , 是否在 管道 内部进行 了认真 的清扫等 ; 在安装 时, 安装人 员是否严格按照 图纸规 定的坐标、 坡度 、 标 高准 确地进行 , 真 正做 到横平竖 直; 在安装 时, 是否遵循 先压力 高后压力低 、 先大后小 、 先复杂 后 简单 、 先 上后下 、 先 地下后地上 的原则 ; 比较特殊 的, 在连接螺 母 的螺 纹、 螺栓 时, 是否在上 面图 了防锈 用的混合物 , 如油脂 、 二硫化钼 的混合 物: 对 与之 相同的转动设备相连 的管道 , 在安装 时必须 十分的重视 , 应该 保 证不对 各设备产生过大 的应 力, 绝不允许利用设 备连接的螺栓强行对 中, 需要做 到 自由对 中、 同心度和 平行度均符 合要求 : 在 固定支架 时 , 必
基于ANSYS的挖掘机动臂吊具的有限元分析
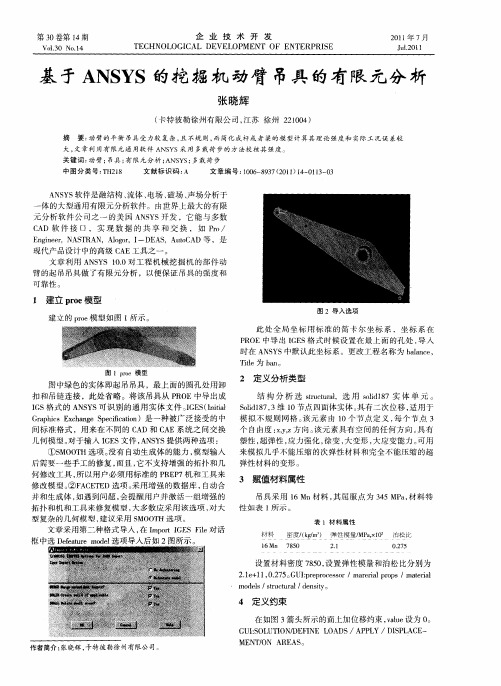
( 卡特彼勒徐州有 限公 司, 江苏 徐州 2 10 ) 20 4
摘 要 : 臂 的 平 衡 吊具 受 力较 复杂 , 不 规 则 , 简化 成杆 或 者 粱的 模 型 计 算其 理 论 强度 和 实际 工 况 误 差 较 动 且 而
大, 文章 利 用有 限 元 通 用软 件 A YS 用 多栽 荷 步 的 方 法 校核 其 强度 。 NS 采
1 建立 po 模型 re
图 2 导 入 选 项
建立的 po 模 型如 图 1 r e 所示 。
此 处全 局坐标 用标 准 的笛 卡尔 坐标 系 .坐标 系在 PO R E中导 出 1 E G S格式时候设置在最上面的孑 处 , L 导入
时在 A S S中默认此坐标系。更改工程名称为 bl c , NY a ne a Tt 为 bn ie l a。
4 定义约束
在如图 3 头所示 的面上加位移约束 ,al设为 0 箭 vhe 。
G I O U I N D F N OA S/A P Y /DI P AC — U : L TO /E I E L D S P L SL E
MENT/ 0N A REAS
作者简介: 张晓辉 , 卡特彼勒徐 州有限公司。
第 3 卷第 1 期 O 4
V0 |O l3 No 1 .4
企 业 技 术 开 发
TECHNOLOGI CAL DEVELOPM ENT OF ENTERPRI SE
21 年 7 01 月
J 1 0 u. l 2 l
基于A Y NS S的挖 掘机 动臂 吊具 的 有限 元 分 析
堪 M l ¨ / x0 白 5 比
02 5 .7
设置材料 密度 7 5 , 80 设置弹性模量和泊松 比分别为
液压挖掘机动臂有限元分析方法研究
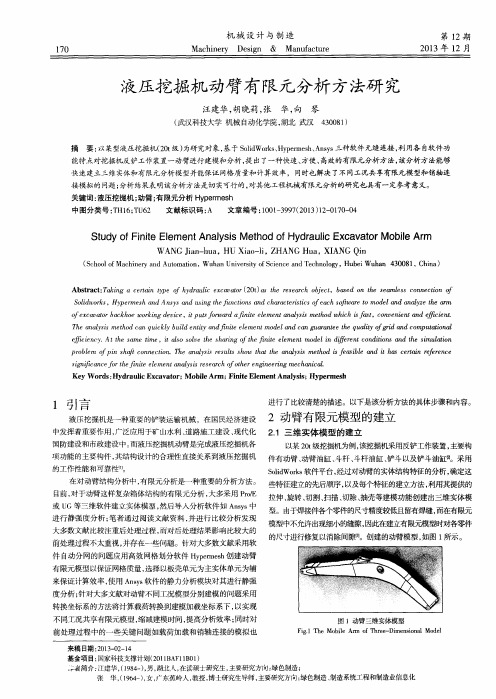
A b s t r a c t : T  ̄i n g a c e r t a i n t y p e o f h y d r a u l i c e x c a v a t o r ( 2 0 t ) t h e r e s e a r c h o b j e c t 。b a s e d o n t h e s e a ml e s s c o n n e c t i o n f o
T h e na a l y s i s me t h o d c a d q u i c k l y b u i l d e n t i t y a n d in f i t e e l e m e n t mo d e l a n d c a r t g u ra a n t e e t h e q u li a t y fg o r i d a n d c o m p u t ti a o n l a e f i f c i e n c y . A t t h e 3 O ; l  ̄ e t i m e , i t a l s o s o l v e t h e s h ri a n g o f t h e i f n i t e e l e m e n t m o d e l i n d f i f e r e n t c o n d i t i o n s nd a t h e s i m u l a t i o n
摘
要: 以某型液压挖掘机 ( 2 0 t 级) 为研 究对 象, 基于 S o l i d Wo r k s 、 H y p e r m e s h 、 A n s y s 三种软件无缝连接 , 利 用各 自软件功
能特点对挖掘机反铲工作装置一动臂进行建模和分析 , 提 出了一种快速 、 方便 、 高效的有 限元分析 方法, 该分析方法能够 快速建立三维 实体和有限元分析模 型并能保证 网格质量和计算效率,同时也解决了不 同工况共享有限元模型和销 轴连 接模拟的问题 ; 分析结果表明该分析方法是切实可行的, 对其他工程机械有限元分析的研究也具有一定参考意义。
某吊运机起重臂的强度分析

某吊运机起重臂的强度分析背景吊运机是工业生产中常用的设备之一,而其重要构件之一就是起重臂。
在正常使用过程中,起重臂需要承受大量的重量和扭矩,因此其强度及合理设计显得至关重要。
本文将分析某吊运机起重臂的强度情况并提出相应建议。
问题某吊运机起重臂存在以下几个问题:1.起重臂承载能力不明确2.起重臂材料种类不确定3.可使用的起重臂附加重量未知这些问题的存在直接影响了起重臂的使用效率和安全性。
数据收集为了解决上述问题,我们进行了数据收集和分析,具体如下:1.通过对该吊运机的使用说明书进行分析,确定了其最大起重和最大半径,在此基础上进行理论计算得出最大承载能力2.对该吊运机进行了现场考察,确定了其起重臂采用热轧钢管加工而成,材料为Q345B钢3.利用同类吊运机的数据对比,推算出该吊运机可承受的附加重量强度分析理论计算根据上述数据收集的结果,我们进行了理论计算,得出了该吊运机起重臂的强度数据,具体如下:1.最大承载能力为5000kg2.起重臂的弯曲极限为24MPa3.起重臂的剪切极限为28MPa4.起重臂的压缩极限为45MPa实际测试为了验证理论计算的结果,我们进行了实际测试,具体如下:1.在最大承载能力下,起重臂没有出现形变或者断裂2.在达到弯曲、剪切和压缩极限时,起重臂均未出现破坏综合理论计算和实际测试结果,我们得出结论:该吊运机起重臂设计强度得到保障,符合安全要求。
建议虽然该吊运机起重臂的设计强度得到了保障,但我们还是提出了一些建议,希望各位用户在使用时能够遵守:1.严格遵守设备规定的最大起重和最大半径限制2.避免超载操作,以免引发任何危险事故3.定期进行起重臂的维护检测,及时发现并处理问题4.在使用过程中,严禁对起重臂进行以外的改动或拆卸结论通过分析该吊运机起重臂的强度情况,我们得出了有关强度的数据,验证了其设计强度得到保障,同时我们提出了一些使用建议,希望各位用户能够认真遵守,确保起重操作的安全性。
挖掘机机械臂测试标准
挖掘机机械臂测试标准挖掘机机械臂是挖掘机的重要部件之一,其性能直接影响到挖掘机的工作效率和质量。
为了保证挖掘机机械臂的优良性能,需要进行相应的测试和评估。
下面是关于挖掘机机械臂测试标准的一些相关参考内容。
1. 功能性测试:1.1 机械臂伸缩功能测试:测试机械臂的伸缩性能,包括伸缩距离、伸缩速度、加载能力等指标。
1.2 机械臂旋转功能测试:测试机械臂的旋转性能,包括旋转角度、旋转速度、旋转平顺性等指标。
1.3 倾斜功能测试:测试机械臂的倾斜功能,包括倾斜角度、倾斜速度、倾斜精度等指标。
1.4 夹持功能测试:测试机械臂的夹持功能,包括夹持力度、夹持精度、夹持稳定性等指标。
2. 动力性能测试:2.1 机械臂动力参数测试:测试机械臂的动力参数,包括最大工作力矩、最大动力输出、动力效率等指标。
2.2 机械臂运动速度测试:测试机械臂的运动速度,包括伸缩速度、旋转速度、倾斜速度等指标。
2.3 机械臂负载能力测试:测试机械臂在不同工况下的负载能力,包括最大负载能力、最大负载距离等指标。
3. 结构稳定性测试:3.1 机械臂结构强度测试:测试机械臂的结构强度,包括升降臂、伸缩臂、铲斗臂的强度等指标。
3.2 机械臂工作平稳性测试:测试机械臂在工作过程中的平稳性,包括工作平衡度、工作过程中的振动情况等指标。
4. 控制精度测试:4.1 机械臂位置控制精度测试:测试机械臂在不同位置的控制精度,包括位置偏差、位置稳定性等指标。
4.2 机械臂力矩控制精度测试:测试机械臂在不同工况下的力矩控制精度,包括力矩偏差、力矩稳定性等指标。
5. 耐久性测试:5.1 机械臂寿命测试:测试机械臂的使用寿命,包括工作时长、工作循环次数、零部件寿命等指标。
5.2 机械臂耐久性测试:测试机械臂在不同工况下的耐久性,包括反复伸缩和旋转测试等指标。
以上是关于挖掘机机械臂测试的一些参考内容,根据实际情况可以进行相应的调整和补充。
通过对机械臂的各项性能指标的测试和评估,可以确保挖掘机机械臂的质量和可靠性,提高挖掘机的工作效率和安全性。
挖掘机动臂的有限元分析
5 . 2工 况 二
挖掘机处 于停 机面最大挖掘半径处 , 铲 斗挖掘 , 铲斗在发挥 最 挖 掘机处于铲斗挖掘 , 铲斗在发挥最大挖掘力位置进行挖掘 。 大挖掘力位置进行挖掘。 经计算 ,工况二 中动臂 最大 变形量 为 2 . 3 1 3厘 米 ,最 大应 力 该位置 出现在斗杆油缸全缩 , 铲斗齿尖 、 斗 杆与铲斗铰 接点及 2 6 7 . 7 M P a , 与许用应力 3 4 5 MP a 相 比, 该工况位置的受力是安全 的。 斗杆与斗杆油缸铰接点这三点处 于同一直线上 , 且大臂油缸缩进使 5 - 3工 况 三 铲斗齿尖处于地面上。 工况三 中动臂最 大变形 量为 2 . 1 4 4厘米 ,最大应力 2 9 0 . 3 MP a , 1 . 2 工 况 二 与材料许用应力 3 4 5 M P a 相比, 该 工况位置 的受力安全 。 挖掘机处 于最深挖掘位置处 , 铲斗挖掘 , 铲 斗在发挥最 大挖掘 6 结 论 力位置进行挖掘。 根据 P r 0 , I Ⅵ E c H A N I A c A计算 可知 , 在三种 工况下 , 挖掘 机在工 此位置 出现在动臂油缸全缩 , 即动臂位 置最低处 , 此 时斗杆与 况三状态时, 即挖掘机处于动臂 、 斗杆最大受力位 置 , 挖掘机 动臂 的 斗杆油缸铰接点 、 斗杆与铲斗铰接点及铲斗齿尖在 同一直线上且垂 受力最大 , 这也和工程实 际相 符 , 工况 三位置挖掘机 动臂 的受 力依 直于挖掘面 。 然安全 , 由此可以得出 , 本挖掘机动臂结构完全符合结构强度要求 。 1 . 3 工 况 三 , 参考文献 大臂 、 斗杆处 于最 大受力位置处 , 铲斗在发 挥最大挖掘 力位置 【 1 1 康 海 洋. 液 压 挖 掘 机 动臂 结 构动 态分 析 [ D 1 . 进行挖掘 。 [ 2 】 杨彩红, 马永杰 . 基 于有 限元的挖掘机 动臂性 能优 化分 析[ J ] . 机械
基于ANSYS的挖掘机动臂吊具的有限元分析
基于ANSYS的挖掘机动臂吊具的有限元分析摘要:动臂的平衡吊具受力较复杂,且不规则,而简化成杆或者梁的模型计算其理论强度和实际工况误差较大,文章利用有限元通用软件ANSYS采用多载荷步的方法校核其强度。
关键词:动臂;吊具;有限元分析;ANSYS;多载荷步ANSYS软件是融结构、流体、电场、磁场、声场分析于一体的大型通用有限元分析软件。
由世界上最大的有限元分析软件公司之一的美国ANSYS开发,它能与多数CAD软件接口,实现数据的共享和交换,如Pro/Engineer, NASTRAN, Alogor, I-DEAS, AutoCAD等,是现代产品设计中的高级CAE工具之一。
文章利用ANSYS 10.0对工程机械挖掘机的部件动臂的起吊吊具做了有限元分析,以便保证吊具的强度和可靠性。
1建立proe模型建立的proe模型如图1所示。
图中绿色的实体即起吊吊具,最上面的圆孔处用卸扣和吊链连接,此处省略。
将该吊具从PROE中导出成IGS格式的ANSYS可识别的通用实体文件。
IGES (Initial Graphics Exchange Specification)是一种被广泛接受的中间标准格式,用来在不同的CAD和CAE系统之间交换几何模型。
对于输入IGES文件,ANSYS 提供两种选项:①SMOOTH选项。
没有自动生成体的能力,模型输入后需要一些手工的修复,而且,它不支持增强的拓扑和几何修改工具,所以用户必须用标准的PREP7机和工具来修改模型。
②FACETED选项。
采用增强的数据库,自动合并和生成体,如遇到问题,会提醒用户并激活一组增强的拓扑和机和工具来修复模型,大多数应采用该选项,对大型复杂的几何模型,建议采用SMOOTH选项。
文章采用第二种格式导入,在Import IGES File对话框中选Defeature model 选项导入后如2图所示。
此处全局坐标用标准的笛卡尔坐标系,坐标系在PROE中导出IGES格式时候设置在最上面的孔处,导入时在ANSYS中默认此坐标系。
正铲液压挖掘机动臂机构的参数对生产效率的影响研究
2019年6月下正铲液压挖掘机动臂机构的参数对生产效率的影响研究戴维师(太原重工股份有限公司,山西 太原 030024)摘 要:正铲液压挖掘机是常见的施工机械,广泛应用于建筑行业,逐渐成为工程中的主力军。
在实际工作中,由于其具有机械种类多、功能齐全以及效率高等优势,因此备受消费者的青睐。
作为正铲液压挖掘机最重要的组成部分,动臂机构动臂的长度、形状、结构以及连杆等参数对生产效率的影响较大,文章对此展开了研究。
关键词:正铲;液压挖掘机;动臂机构;生产效率中图分类号:TU621 文献标志码:A 文章编号:1672-3872(2019)12-0122-01——————————————作者简介: 戴维师(1984—),男,甘肃白银人,本科,助理工程师,研究方向:液压。
1 正铲液压挖掘机的工作原理铲斗主要是由动臂、铲斗、液压缸以及连杆机构等工作装置所组成。
动臂是由强度比较大的钢板焊接而成,在铸造的过程中通常采用是混合结构;与反铲相比,正铲的工作结构是比较特殊,其动臂比较短且是单节的。
动臂油缸布置在下铰接点臂缸上方这样的设置可以确保吊杆具有一定的倾斜角度和动臂力矩,在最大程度上满足挖掘和生产的要求[1]。
2 正铲液压挖掘机的分类及参数现阶段,挖掘机正铲铲斗依据其结构能分为不同的两类,即前卸和底卸式。
当用正铲前卸式铲斗卸土时,铲斗由铲斗液压缸直接翻转,以及土壤会被从铲斗的前面卸载。
该结构显而易见的优点如下:铲斗是一个完整的整体,具有很强的刚度和强度,在实际的工作过程中,为了将土全倒出来,需要满足的条件是前臂与水平方向的夹角在45°以上,铲斗角度的增加,会使旋转铲斗挖掘力减小或倾倒时所需的铲斗缸功率明显增大。
除此之外,前卸式铲斗也会影响卸料的高度[2-3]。
底卸式铲斗在工作时需先打开斗底卸斗,依赖于特殊的油缸结构。
当挖斗底全部关闭时,卸土底会随之打开,将土全部倾倒出去。
这种倾卸斗结构性能较好,但是不足之处是必须加卸土油缸。
- 1、下载文档前请自行甄别文档内容的完整性,平台不提供额外的编辑、内容补充、找答案等附加服务。
- 2、"仅部分预览"的文档,不可在线预览部分如存在完整性等问题,可反馈申请退款(可完整预览的文档不适用该条件!)。
- 3、如文档侵犯您的权益,请联系客服反馈,我们会尽快为您处理(人工客服工作时间:9:00-18:30)。
WY10B挖掘机动臂强度分析
(一拖(洛阳)工程机械有限公司洛阳 471003)
摘要:以WY10B液压挖掘机为研究对象,对反铲挖掘机工作装置——动臂建立Pro/E实体模型,并用Pro/MECHANICA模块对挖掘机动臂的设计模型在受最大应力的危险工况下进行有限元强度分析。
对实体动臂在危险工况下进行实际应力测试,与有限元分析结果进行对比,分析差异,为挖掘机动臂改进提供理论和实际依据。
关键字:液压挖掘机动臂有限元应力
中图分离号:**** 文献标示码:A
1.概述
液压挖掘机是工程机械的主要产品之一,具有较高的技术含量和工作效率,它被广泛应用于建筑、筑路、水利、电力、采矿、石油、天然气管道铺设和军事工程等基本建设之中。
动臂是挖掘机工作装置(铲斗、斗杆、动臂) 3 大部件之一[1],是主要承载件。
在挖掘过程中,动臂直接或间接承受很大外力。
作业环境的状况也对动臂的强度和变形在一定程度上造成很大影响。
目前,在国内液压挖掘机设计中,对动臂的应力进行分析的较多,而对理论与实际结合分析较少。
本文结合WY10B挖掘机的实际作业工况,对挖掘机动臂在受力最大的典型工况下挖掘时进行强度分析和实际应力测试,为挖掘机动臂设计提供理论和实际依据。
2.计算工况选择
对挖掘机动臂进行强度分析时,分析采用的工况必须是有限元模型受力最大的危险工况[2]。
根据挖掘机的连接情况, 使用Pro/ MECHANICAMOTION 模块对其进行动力学分析,利用Pro/MECHANICA MO TION 模块的运动仿真功能,模拟工作装置的运动情况,求出了动臂受力最大的工况。
分析发现,危险断面最大应力发生在采用铲斗挖掘的工况下,因此计算位置可按以下条件确定:
1)、动臂位于动臂油缸作用力臂最大处;
2)、斗杆位于斗杆油缸作用力臂最大处;
3)、铲斗位于发挥最大挖掘力位置。
3载荷计算
工作装置各构件通过销连接,在计算工况中不考虑偏载的影响,可以认为其只承受X、Y向的力,整个结构为静定结构,在计算工况中,铲斗缸产生主动力,大腔半径为27.5mm,压力为28MPa,则最大推力为:F G =R G=πr2P=π×0.02752×28×106=66489.5 N
分别求得动臂各铰点的反力如下:动臂各铰点支反力:
以上求出的力都是合力,在实际结构中,铰点处的受力并非集中力,而其附近的应力分布又是我们所关心的,为模拟实际情况,作如下假定:
1)、载荷在X-Y面内在180°范围内按余弦分布;
2)、分布力的方向为沿销孔表面的法向;
3)、载荷在Z向均布;
由假定构造载荷分布函数为: 式中:
F (θ ) = A cos (θ-α) (1) A 为待定常系数,
合力R 已知,分布力F 在P 向的合力应等于R ,即
式中:l 为销孔长度,r 为销孔半径。
由上式可求得待定系数
由(3)式计算得到各铰点在计算位置的参数如下:
4 确定约束条件
对于静力分析,必须限制模型的刚体位移[3],选择动臂与平台的销孔(C 点)进行全约束,由于动臂的外力对C 点的力矩之和为零,限制C 点的Z 向旋转自由度对计算无影响,但实际约束是产生在销孔面上的,而且六面体单元的节点没有旋转刚度,因此施加在销孔面上的约束实际是限制了销孔面上节点在三个方向的自由度。
这样会在约束的销孔处产生一附加扭矩,使局部应力增大,但对远端的应力计算没有很大影响。
为考察其影响,约束不同的销孔分别进行计算,得到的结果表明除约束点附近的应力值不同外,其余部位的应力大小和分布完全一致,说明这种约束方式是可行的。
5 网格划分
动臂主要结构由厚钢板焊接而成,考虑到板厚较大,而且多处结构需使用体单元,因此决定全部使用三维单元划分,为达到较高的精度,主要使用八节点六面体单元,过渡部位使用五面体单元。
为简便起见,划分时把动臂的前端作为整体处理(实际是两层钢板结构,在边缘有焊缝),对于焊缝则不作处理,划分后动臂节点数为41470,单元数为21260;
6 有限元强度分析结果
为了更加直观形象地将动臂的强度分析结果表现出来,通过 Pro/ MECHANICA 分析模块的后处理程序,绘制出动臂强度分析的应力云图如图 5所示。
轴的夹角。
为合力方向与 X
在此计算模型中没有考虑焊缝的影响,在实际情况中,焊缝应能够减小应力集中,即实际结构中的最大应力应低于计算值。
由动臂的应力云图可以看出,动臂大部分部位的应力值较小,而在动臂缸和斗杆缸铰点处有较大的应力集中,应考虑在这些铰点周围采取加强措施。
7 实际应力测试结果
了解知名品牌挖机结构件结构的特点,并对WY10B动臂进行实际工况下的应力测试,确定了动臂主要部位静态强度和动态强度应力值(应力测试仪)。
测试结果:最大应力点为:动态工况,最大应力为:241.6Mpa,结构件材料为:16Mn,其屈服极限为:345 Mpa,该点安全系数为:1.4
8 结果分析
(1)根据有限元分析和实际应力测量,动臂油缸座前端不仅应力集中,而且受力最大,是动臂受力的关键部位。
加长此处油缸座耳板前端长度,增加耳板、下封板厚度,不仅可以降低此处应力,而且可以化解应力集中。
(2)动臂油缸座后端虽然应力集中,但是所受应力较小,不足以对动臂造成危险。
(3)动臂上斗杆油缸座耳板后应力集中,同样可以通过加长此处油缸座耳板后端长度,增加耳板厚度来解决,以降低此处应力,化解应力集中。
(4)动臂前叉有限元分析未反应应力集中,但是实际测量数值较大。
因为有限元分析忽略了此处焊缝影响,在侧板上有条焊缝,受焊缝影响,此处应力实际值较大。
建议前叉板加长,以改善上下封板前焊缝受力状况,提高疲劳强度。
通过使用Pro/ E 对WY10B 挖掘机动臂进行有限元分析,可以看出,有限元分析的主要工作是数据准备和分析运算结果,建立正确的有限元分析模型才能运算出正确的结果。
根据对运算结果的分析,不断发现产品设计中存在的问题, 但是为了方便有限元分析,往往忽略了一些因素的影响(如:焊缝),这就造成有些问题在分析时没有被及时发现,如果再能结合实际测量,得到的结果就会更加准确。
以上分析结果已在WY10B挖掘机上实施,并取得良好效果,为挖掘机的设计和改进提供了准确的理论和实际依据。
参考文献
1黄东胜,邱斌.现代挖掘机械[M] .北京:人民交通出版社,2003 :6
2于硕 ,张建宗 ,孔喆.液压挖掘机动臂的有限元分析[J ] .工程机械 ,2002 (11) :8 -
10.
3MSC公司. John M. Lee. Linear Static Analysis User's Guide, 1997
邮箱:keke8882006@。