双辊薄带振动铸轧机理及其仿真实验
《2024年双辊薄带振动铸轧振动工艺对凝固组织影响机理实验研究》范文

《双辊薄带振动铸轧振动工艺对凝固组织影响机理实验研究》篇一一、引言随着现代工业的快速发展,金属材料的制备工艺不断更新换代,其中双辊薄带铸轧技术以其高效率、低成本和优异的性能吸引了广泛关注。
为了进一步提高产品质量,优化生产工艺,本研究将针对双辊薄带振动铸轧工艺展开,尤其是对振动工艺对凝固组织影响机理进行实验研究。
通过本文的实验设计和分析,为该领域的技术改进提供理论基础和实验依据。
二、实验材料与方法1. 实验材料本实验采用纯铝作为研究对象,其化学成分和物理性能符合实验要求。
2. 实验方法(1)设备准备:搭建双辊薄带振动铸轧设备,确保设备运行稳定。
(2)实验设计:设计不同振动参数(如振动频率、振幅等)下的铸轧过程。
(3)样品制备:在每种振动参数下,制备一定数量的薄带样品。
(4)组织观察:利用金相显微镜、扫描电镜等设备观察样品的凝固组织。
(5)数据记录与分析:记录实验数据,分析振动工艺对凝固组织的影响。
三、实验结果与分析1. 振动频率对凝固组织的影响实验发现,在一定的振幅下,随着振动频率的增加,凝固组织的晶粒尺寸逐渐减小。
这是因为振动能够有效地打破晶粒生长的连续性,使晶粒细化。
同时,高频率的振动还能使熔体在凝固过程中更好地排除杂质,从而提高铸轧材料的纯度。
2. 振幅对凝固组织的影响振幅也是影响凝固组织的重要因素。
当振幅增大时,振动对熔体的扰动作用增强,有利于晶粒的进一步细化。
但过大的振幅可能导致熔体表面波动加剧,从而影响铸轧过程的稳定性。
因此,存在一个最佳的振幅范围,使得凝固组织的晶粒尺寸达到最优状态。
3. 凝固组织的微观结构分析通过金相显微镜和扫描电镜观察发现,双辊薄带振动铸轧过程中,凝固组织的晶界清晰、组织致密。
在适当的振动参数下,晶粒呈等轴状,且分布均匀。
这表明振动工艺能够有效地改善铸轧材料的微观结构,提高其力学性能。
四、影响机理探讨双辊薄带振动铸轧过程中,振动工艺通过以下途径影响凝固组织:1. 振动能够打破晶粒生长的连续性,使晶粒细化;2. 振动有助于熔体在凝固过程中更好地排除杂质,提高铸轧材料的纯度;3. 适当的振动参数能使熔体在双辊间更好地流动和填充,从而获得致密的微观结构;4. 振动还能降低铸轧过程中的热应力,减少裂纹等缺陷的产生。
《2024年双辊薄带振动铸轧振动工艺对凝固组织影响机理实验研究》范文

《双辊薄带振动铸轧振动工艺对凝固组织影响机理实验研究》篇一一、引言在金属材料加工领域,双辊薄带振动铸轧技术已成为一种高效、低成本的连续铸造工艺。
其独特之处在于,通过引入振动工艺,可以在铸轧过程中显著改善金属的凝固组织,提高材料的综合性能。
本文将重点探讨双辊薄带振动铸轧中振动工艺对凝固组织的影响机理,通过实验研究为优化工艺参数和提升产品质量提供理论支持。
二、实验材料与方法1. 实验材料实验选用的金属材料为铝合金,具有较好的可铸性和加工性能。
在实验前,对原材料进行严格的质量控制和化学成分分析。
2. 实验方法采用双辊薄带振动铸轧机进行实验,通过调整振动参数(如振动频率、振幅等),观察凝固组织的形态变化。
采用金相显微镜、扫描电镜等设备对凝固组织进行观察和分析。
三、振动工艺对凝固组织的影响机理1. 振动对流场的影响在双辊薄带振动铸轧过程中,振动作用可以改变金属液的流场分布。
适当的振动频率和振幅可以促使金属液在凝固过程中形成更为均匀的流线,有利于排除气泡和夹杂物,从而改善组织的致密度。
2. 振动对晶粒形核与长大的影响振动能量可以作用于晶粒形核和长大的过程。
在适当的振动参数下,晶粒的形核率增加,晶粒尺寸减小,从而获得更为细小的组织结构。
此外,振动还可以改变晶粒的生长方向,使其更加趋于随机分布,减少组织的各向异性。
3. 振动对固态相变的影响在凝固过程中,金属可能发生固态相变。
适当的振动参数可以影响固态相变的进程和程度,从而改善组织的均匀性和稳定性。
通过调整振动参数,可以在一定程度上控制固态相变的类型和程度,进而优化材料的性能。
四、实验结果与分析1. 实验结果通过调整双辊薄带振动铸轧机的振动参数,观察并记录了不同参数下凝固组织的形态变化。
实验结果表明,适当的振动参数可以显著改善组织的致密度和均匀性。
2. 分析讨论结合实验结果和理论分析,可以得出以下结论:双辊薄带振动铸轧中的振动工艺对凝固组织具有显著影响。
适当的振动参数可以改变流场分布,促进晶粒的形核和长大,以及影响固态相变的进程和程度。
《双辊薄带振动铸轧振动工艺对凝固组织影响机理实验研究》
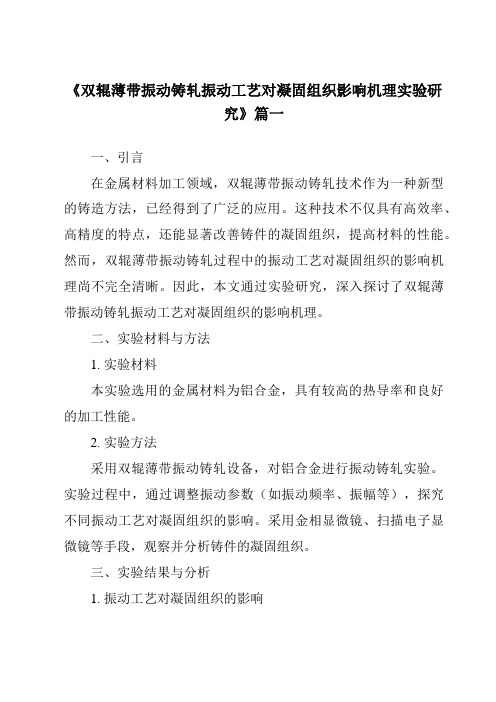
《双辊薄带振动铸轧振动工艺对凝固组织影响机理实验研究》篇一一、引言在金属材料加工领域,双辊薄带振动铸轧技术作为一种新型的铸造方法,已经得到了广泛的应用。
这种技术不仅具有高效率、高精度的特点,还能显著改善铸件的凝固组织,提高材料的性能。
然而,双辊薄带振动铸轧过程中的振动工艺对凝固组织的影响机理尚不完全清晰。
因此,本文通过实验研究,深入探讨了双辊薄带振动铸轧振动工艺对凝固组织的影响机理。
二、实验材料与方法1. 实验材料本实验选用的金属材料为铝合金,具有较高的热导率和良好的加工性能。
2. 实验方法采用双辊薄带振动铸轧设备,对铝合金进行振动铸轧实验。
实验过程中,通过调整振动参数(如振动频率、振幅等),探究不同振动工艺对凝固组织的影响。
采用金相显微镜、扫描电子显微镜等手段,观察并分析铸件的凝固组织。
三、实验结果与分析1. 振动工艺对凝固组织的影响实验结果表明,双辊薄带振动铸轧过程中,适当的振动工艺能显著改善铸件的凝固组织。
在振动作用下,金属液滴在凝固过程中受到周期性的外力作用,有助于破碎枝晶组织,减少晶间缺陷。
同时,振动还能促进溶质的均匀分布,提高铸件的致密度和力学性能。
2. 不同振动参数对凝固组织的影响随着振动频率和振幅的增加,铸件的凝固组织得到进一步优化。
高频率的振动能使金属液滴在较短的时间内完成凝固过程,细化晶粒,提高铸件的性能。
然而,过大的振幅可能导致金属液滴的溅射和飞散,反而对凝固组织产生不利影响。
因此,在双辊薄带振动铸轧过程中,需要选择合适的振动参数,以达到最佳的凝固组织效果。
四、影响机理探讨双辊薄带振动铸轧过程中,振动工艺对凝固组织的影响机理主要包括以下几个方面:1. 破碎枝晶组织:在振动作用下,金属液滴的表面张力发生变化,枝晶组织受到周期性的外力作用而破碎,有利于消除晶间缺陷。
2. 促进溶质均匀分布:振动能促进金属液滴内部的流动和混合,使溶质元素在铸件中更加均匀地分布。
3. 提高致密度:适当的振动能减少铸件中的气孔和夹杂物等缺陷,提高铸件的致密度和力学性能。
《双辊薄带鋳轧熔池流场数值模拟与实验研究》
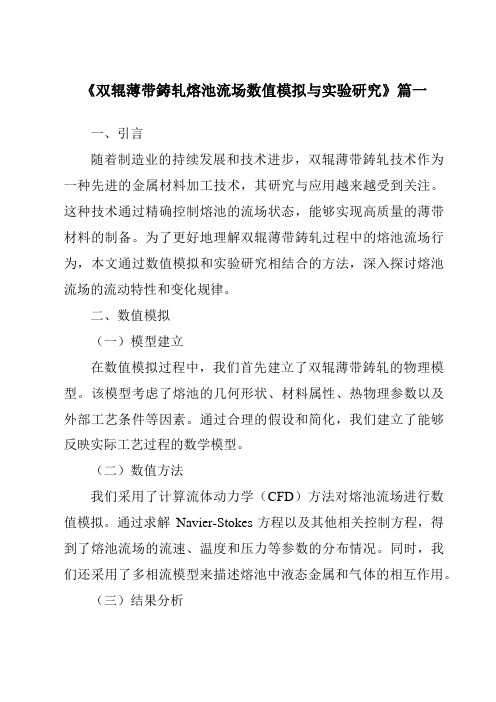
《双辊薄带鋳轧熔池流场数值模拟与实验研究》篇一一、引言随着制造业的持续发展和技术进步,双辊薄带鋳轧技术作为一种先进的金属材料加工技术,其研究与应用越来越受到关注。
这种技术通过精确控制熔池的流场状态,能够实现高质量的薄带材料的制备。
为了更好地理解双辊薄带鋳轧过程中的熔池流场行为,本文通过数值模拟和实验研究相结合的方法,深入探讨熔池流场的流动特性和变化规律。
二、数值模拟(一)模型建立在数值模拟过程中,我们首先建立了双辊薄带鋳轧的物理模型。
该模型考虑了熔池的几何形状、材料属性、热物理参数以及外部工艺条件等因素。
通过合理的假设和简化,我们建立了能够反映实际工艺过程的数学模型。
(二)数值方法我们采用了计算流体动力学(CFD)方法对熔池流场进行数值模拟。
通过求解Navier-Stokes方程以及其他相关控制方程,得到了熔池流场的流速、温度和压力等参数的分布情况。
同时,我们还采用了多相流模型来描述熔池中液态金属和气体的相互作用。
(三)结果分析通过数值模拟,我们得到了熔池流场的流动特性及变化规律。
结果表明,熔池流场的流动状态受到多种因素的影响,包括轧制速度、熔池温度、材料属性等。
在一定的工艺条件下,熔池流场呈现出稳定的流动状态,有利于薄带材料的制备。
三、实验研究(一)实验设计为了验证数值模拟结果的准确性,我们设计了一系列实验。
实验中,我们采用了不同的工艺参数,如轧制速度、熔池温度等,以观察熔池流场的变化规律。
同时,我们还采用了高速摄像机等设备对熔池流场进行实时观测。
(二)实验过程与结果在实验过程中,我们记录了不同工艺参数下熔池流场的变化情况。
通过对比实验结果和数值模拟结果,我们发现两者在流动特性和变化规律上具有较好的一致性。
这表明我们的数值模拟方法是有效的,能够较好地反映双辊薄带鋳轧过程中熔池流场的实际情况。
四、讨论与结论通过数值模拟和实验研究,我们深入探讨了双辊薄带鋳轧过程中熔池流场的流动特性和变化规律。
我们发现,熔池流场的流动状态受到多种因素的影响,包括轧制速度、熔池温度、材料属性等。
双辊薄带铸轧中心线偏析机理与实验研究

双辊薄带铸轧中心线偏析机理与实验研究杜凤山;吕征;黄华贵;许志强;安仲健【摘要】以薄带铸轧中心线偏析问题为研究对象,从宏观和微观角度分析铸轧薄带芯部偏析的成因与机理,建立完全耦合溶质场、流场、温度场的数学模型。
通过数学模型对铸轧铝合金熔池中的Fe、Mn元素分布进行研究。
结果表明:理论研究与实验结果基本吻合。
熔池区凝固组织以柱状晶形式沿〈001〉方向迅速生长,同时溶质成分逐渐偏聚于熔池芯部区域,并在Kiss点区域达到最大值。
其中Fe元素在Kiss点区域的含量明显高于其他区域的,完全凝固后易产生中心线偏析。
随着铸轧速度的提高,辊缝宽度增大,中心线偏析趋势增强。
%The problem of casting Al-alloy strip was studied, the mechanism of as-cast strip centerline segregation was analyzed from the perspective of macro and micro, and a mathematical method was developed which completely couples solute field, flow field and temperature distribution. The distributions of Fe and Mn in the Al alloy molten pool were figured out by the mathematical method. The results show that the theoretical calculation agrees well with the experimental results. The solidification structure grows along 〈001〉direction rapidly by the form of columnar crystal. Meanwhile, the solute elements are focused gradually in the kern zone, and the maximum value is gotten at the Kiss point zone. In particular, Fe content of the Kiss point zone is much higher than the average value, and centerline segregation appears after solidification. The centerline segregation tends to increase with the increase of casting speed and roll gap.【期刊名称】《中国有色金属学报》【年(卷),期】2015(000)010【总页数】7页(P2738-2744)【关键词】双辊薄带铸轧;溶质场;流场;中心线偏析;Kiss点【作者】杜凤山;吕征;黄华贵;许志强;安仲健【作者单位】燕山大学国家冷轧板带装备及工艺工程技术研究中心,秦皇岛066004;燕山大学国家冷轧板带装备及工艺工程技术研究中心,秦皇岛 066004;燕山大学国家冷轧板带装备及工艺工程技术研究中心,秦皇岛 066004;燕山大学国家冷轧板带装备及工艺工程技术研究中心,秦皇岛 066004;燕山大学国家冷轧板带装备及工艺工程技术研究中心,秦皇岛 066004【正文语种】中文【中图分类】TG111.4双辊薄带铸轧技术被认为是21世纪冶金行业最有发展潜力的技术之一,该工艺是将高温金属液浇入一对相对转动结晶辊间形成熔池,金属经过结晶辊冷却和轧制作用,直接加工为成品薄带。
《双辊薄带振动铸轧振动工艺对凝固组织影响机理实验研究》范文

《双辊薄带振动铸轧振动工艺对凝固组织影响机理实验研究》篇一一、引言在金属材料加工领域,双辊薄带振动铸轧技术已成为一种新型、高效的金属凝固成形方法。
通过振动工艺的应用,能够有效控制凝固过程中的温度场和应力场,进而影响金属凝固组织,从而提升材料的性能。
本文以双辊薄带振动铸轧振动工艺为研究对象,探讨其对凝固组织的影响机理,旨在为金属材料加工技术的进一步发展提供理论依据和实验支持。
二、实验材料与方法1. 实验材料本实验采用某合金作为研究对象,该合金具有良好的可铸性和可塑性,适合于双辊薄带振动铸轧技术。
2. 实验方法本实验采用双辊薄带振动铸轧技术,通过调整振动参数(如振幅、频率等),研究其对凝固组织的影响。
同时,采用金相显微镜、扫描电镜等手段,观察和分析金属凝固组织的形貌、成分和结构。
三、双辊薄带振动铸轧振动工艺的介绍双辊薄带振动铸轧技术通过在传统铸轧过程中引入振动工艺,使金属在凝固过程中受到周期性的外力作用,从而改变其凝固行为。
这种技术具有以下优点:一是能够细化晶粒,提高材料的力学性能;二是能够减少热裂、缩孔等缺陷的产生;三是能够提高生产效率,降低能耗。
四、振动工艺对凝固组织的影响机理1. 振动对温度场的影响振动能够使金属在凝固过程中产生周期性的热扰动,从而改变温度场的分布。
这种改变有利于减小温度梯度,使晶粒在凝固过程中能够更加均匀地生长。
2. 振动对应力场的影响振动能够有效地降低金属在凝固过程中的残余应力。
这是由于振动能够使金属在凝固过程中产生周期性的形变,从而松弛内部的应力。
这种松弛作用有助于减少热裂等缺陷的产生。
3. 振动对晶粒细化的作用晶粒细化是双辊薄带振动铸轧技术的重要特点之一。
振动能够使金属在凝固过程中产生更多的形核点,从而增加晶粒的数量。
同时,振动还能够抑制晶粒的异常长大,使晶粒尺寸更加均匀。
五、实验结果与分析1. 实验结果通过调整振动参数,我们观察到金属凝固组织的形貌、成分和结构发生了明显的变化。
《2024年双辊薄带鋳轧熔池流场数值模拟与实验研究》范文

《双辊薄带鋳轧熔池流场数值模拟与实验研究》篇一一、引言双辊薄带鋳轧技术作为一种新型的金属材料加工技术,在工业生产中得到了广泛的应用。
该技术通过两个高速旋转的辊子将熔融金属轧制成薄带材料,具有生产效率高、材料利用率高、产品性能优异等优点。
然而,在双辊薄带鋳轧过程中,熔池流场的稳定性对产品的质量和生产效率有着重要的影响。
因此,对双辊薄带鋳轧熔池流场进行数值模拟与实验研究具有重要的理论意义和实际应用价值。
二、双辊薄带鋳轧熔池流场数值模拟1. 模型建立为了研究双辊薄带鋳轧熔池流场的特性,我们建立了相应的数学模型。
该模型考虑了熔融金属的物理性质、辊子转速、轧制压力等因素对熔池流场的影响。
通过引入适当的边界条件和初始条件,建立了描述熔池流场的三维流动模型。
2. 数值方法采用计算流体动力学(CFD)方法对熔池流场进行数值模拟。
通过离散化处理,将连续的流动问题转化为离散的代数问题,并采用适当的数值算法进行求解。
在模拟过程中,我们采用了高精度的离散格式和算法,以保证结果的准确性。
3. 结果分析通过对模拟结果的分析,我们可以得到熔池流场的流动特性、速度分布、压力分布等信息。
这些信息对于优化双辊薄带鋳轧工艺、提高产品质量和生产效率具有重要意义。
三、实验研究为了验证数值模拟结果的准确性,我们进行了实验研究。
通过在实验室条件下模拟双辊薄带鋳轧过程,观察熔池流场的实际流动情况,并与数值模拟结果进行比较。
1. 实验装置实验装置主要包括两个高速旋转的辊子、加热装置、熔融金属供应系统等。
通过调整辊子转速、加热温度等参数,模拟不同的双辊薄带鋳轧工艺条件。
2. 实验方法在实验过程中,我们采用了高速摄像机等设备记录熔池流场的实际流动情况。
通过分析实验数据,我们可以得到熔池流场的实际流动特性、速度分布、压力分布等信息。
3. 结果分析将实验结果与数值模拟结果进行比较,我们可以评估数值模拟的准确性。
通过分析差异原因,我们可以进一步优化数学模型和数值方法,提高模拟结果的精度。
《双辊薄带鋳轧熔池流场数值模拟与实验研究》范文

《双辊薄带鋳轧熔池流场数值模拟与实验研究》篇一一、引言随着现代工业技术的飞速发展,双辊薄带鋳轧技术作为一种重要的金属材料加工技术,已经得到了广泛的应用。
其工艺特点在于利用高速旋转的双辊将熔融金属材料进行轧制,以实现高效、高精度的材料加工。
在双辊薄带鋳轧过程中,熔池流场的分布和演变对于轧制过程的质量和效率具有重要影响。
因此,对双辊薄带鋳轧熔池流场进行数值模拟与实验研究,对于优化工艺参数、提高产品质量具有重要意义。
二、双辊薄带鋳轧熔池流场数值模拟1. 数学模型建立双辊薄带鋳轧熔池流场的数值模拟主要基于流体动力学理论,通过建立数学模型来描述熔融金属在双辊间的流动过程。
该模型应考虑金属的物理性质、流场动力学特性以及轧制过程中的热力耦合效应等因素。
2. 数值模拟方法采用计算流体动力学(CFD)方法对双辊薄带鋳轧熔池流场进行数值模拟。
通过求解流体动力学方程,可以得到熔融金属在双辊间的流动速度、压力分布以及温度场等关键参数。
3. 模拟结果分析通过对模拟结果的分析,可以得出熔池流场的分布规律和演变过程。
同时,还可以分析不同工艺参数对熔池流场的影响,为优化工艺参数提供依据。
三、实验研究1. 实验装置与材料实验装置主要包括双辊薄带鋳轧机、高温炉、数据采集系统等。
实验材料为金属合金,通过高温炉进行熔化。
2. 实验方法与步骤(1)制备金属合金,并将其放入高温炉中进行熔化;(2)启动双辊薄带鋳轧机,调整轧制速度、辊间距等工艺参数;(3)观察熔融金属在双辊间的流动过程,并使用数据采集系统记录关键参数;(4)分析实验数据,验证数值模拟结果的准确性。
3. 实验结果与讨论通过实验研究,可以观察到双辊薄带鋳轧过程中熔池流场的实际分布和演变过程。
将实验结果与数值模拟结果进行对比,可以验证数值模拟方法的准确性。
同时,还可以分析不同工艺参数对实际轧制过程的影响,为优化工艺参数提供实验依据。
四、结论与展望通过对双辊薄带鋳轧熔池流场进行数值模拟与实验研究,可以得出以下结论:1. 数值模拟方法可以有效地描述双辊薄带鋳轧过程中熔池流场的分布和演变过程;2. 不同工艺参数对熔池流场具有显著影响,通过优化工艺参数可以提高产品质量和效率;3. 实验研究验证了数值模拟方法的准确性,为实际生产提供了有力支持。
- 1、下载文档前请自行甄别文档内容的完整性,平台不提供额外的编辑、内容补充、找答案等附加服务。
- 2、"仅部分预览"的文档,不可在线预览部分如存在完整性等问题,可反馈申请退款(可完整预览的文档不适用该条件!)。
- 3、如文档侵犯您的权益,请联系客服反馈,我们会尽快为您处理(人工客服工作时间:9:00-18:30)。
双辊薄带振动铸轧机理及其仿真实验杜凤山;孙明翰;黄士广;魏洁平;黄华贵;许志强【摘要】A set of?160 mm×150 mm vibration casting machines were designed and manufac-tured in order to carry out the research on the product quality of twin roll strip casting processes.The effects of vibrations on the crystal nucleation and cast microstructure were studied.The distributions and growth rules of the cast microstructures in the solidification zones under the conditions of vibra-tion and non-vibration were compared and analyzed.It is pointed out that improving the vibration fre-quencies may effectively promote the grain refinement.At the same time,according to the require-ments of industrial experiments,a three-dimensional flow field-temperature field coupling finite ele-ment simulation model of molten pools was established by using CFD software.The results show that increasing the vibration frequencies and amplitudes may enhance the"mixing"effects of the cast roll-ing molten pools,which may promote the grain refinements and restrain the segregations.It is found that the solidification point positions(i.e.Kiss point height)are not distributed along the width direc-tion of the plates in the castrolling processes.As a result,the longitudinal inhomogeneous extensions are the direct factors to induce the cast rolling oblique cracks.And the Kiss point position will be moved up with the increase of the amplitudes and the frequencies.%针对双辊薄带铸轧过程存在的产品质量问题进行研究,设计制造了一套?160 mm×150 mm振动式铸轧机.研究了振动对结晶形核及其铸态组织的影响,对比分析了振动与非振动条件下凝固区铸态组织分布及其生长规律.指出提高振动频率能够有效促进晶粒细化.同时,按工业化实验要求,利用CFD软件建立了熔池的三维流场温度场耦合有限元仿真模型,仿真结果表明,增大振频和振幅均能强化铸轧熔池场的"搅拌"效果,进而促进晶粒细化、抑制偏析.通过仿真还发现,铸轧过程中,凝固点位置(即Kiss点高度)沿板宽方向分布不均所导致的纵向不均匀延伸,是诱发铸轧斜向裂纹的直接因素,并且Kiss点位置会随振频和振幅的增大而上移.【期刊名称】《中国机械工程》【年(卷),期】2018(029)004【总页数】8页(P477-484)【关键词】振动;双辊铸轧;铸态组织;晶粒细化;Kiss点【作者】杜凤山;孙明翰;黄士广;魏洁平;黄华贵;许志强【作者单位】燕山大学国家冷轧板带装备及工艺工程技术研究中心,秦皇岛,066004;燕山大学机械工程学院,秦皇岛,066004;燕山大学国家冷轧板带装备及工艺工程技术研究中心,秦皇岛,066004;燕山大学机械工程学院,秦皇岛,066004;燕山大学国家冷轧板带装备及工艺工程技术研究中心,秦皇岛,066004;燕山大学机械工程学院,秦皇岛,066004;燕山大学国家冷轧板带装备及工艺工程技术研究中心,秦皇岛,066004;燕山大学机械工程学院,秦皇岛,066004;燕山大学国家冷轧板带装备及工艺工程技术研究中心,秦皇岛,066004;燕山大学机械工程学院,秦皇岛,066004;燕山大学国家冷轧板带装备及工艺工程技术研究中心,秦皇岛,066004;燕山大学机械工程学院,秦皇岛,066004【正文语种】中文【中图分类】TG30 引言双辊薄带铸轧技术被认为是21世纪冶金工业最具发展潜力的高新技术,具有短流程、低能耗、投资少等特点,其工业化应用研究一直受到国内外科技界的高度关注,一旦形成稳定生产能力,必将对全球的冶金行业产生重要影响。
该技术是以两个逆向旋转的轧辊作为结晶器,将熔融状态下的金属通过中间包注入铸轧辊熔池,通过铸造-轧制直接生产薄带的新工艺。
由于双辊薄带铸轧是在高温快速凝固条件下发生的,因此极易出现裂纹、偏析、夹层和组织性能难以控制等一系列板坯质量问题[1]。
为此,本课题组首次提出了双辊薄带振动铸轧新技术,研究在铸轧过程中引入振动源以控制晶核形成和晶粒细化,提高产品组织性能。
振动已经在铸造方面获得了广泛的应用,早在1868年俄国人Chernov就通过在铸造过程中施加机械摇动振型的方式获得了细小晶粒的铸件[2-3]。
WANG等[4]研究了振动频率对铸造铝合金的影响,认为铸造过程中施加振动和冲击能击碎枝晶。
MIZULANI等[5]通过电磁的方式施加振动,发现镁合金和铝合金凝固过程中施加振动都能够显著地细化晶粒。
张德恩等[6]研究了机械对铝合金铸造凝固过程中组织性能的影响,得到了相对于非振动更为细小的晶粒组织。
目前,振动已经在塑形成形、复合材料制备以及焊接等多个领域得到了广泛的应用。
考虑双辊薄带铸轧是在高速冷凝条件下进行的,通过振动不仅能促进枝晶形核,还能促进形变诱导晶粒细化。
本课题组设计制造了一台φ160 mm×150 mm双辊薄带振动铸轧机,并进行了铝合金振动铸轧物理模拟实验。
1 实验1.1 双辊薄带振动铸轧机及其原理为研究振动对薄带铸轧组织性能的影响,课题组自主设计研发了φ160 mm×150 mm双辊薄带振动铸轧机(图1),图1a给出了铸轧机振动铸轧原理,左侧结晶辊固定转动,右侧结晶辊振动加转动,形成振动铸轧。
1.2 实验结果分析经铸锭振动凝固实验验证振动在凝固过程中的影响后,在铸轧实验机上进行振动铸轧实验,以研究振动对铸轧过程的影响。
实验材料为AlSi9Cu3铸造铝合金,其化学成分见表1,开浇温度为605 ℃,出口侧薄带厚度为4 mm,轧辊线速度为50 mm/s。
如图2所示,铸轧板坯存在明显的振痕,说明在铸轧过程中由于轧辊振动产生了反复搓轧的作用效果,通过双向反复搓轧增大了凝固区剪切变形量,易于促进铸轧过程动态再结晶的形成和晶粒细化。
其中,板坯表面振痕可在后继精轧区消除。
由图2b和图2c可知,随着振动频率的增大,带坯表面振痕变密,单位长度内振痕数增加,说明提高振动频率可增加板坯单位长度内的搓轧次数,增强剪切效果。
为进一步研究振动频率特性对晶粒细化效果的影响,在该铸机振动实验平台上进行了铸锭振动凝固实验。
实验过程如下:将铸轧机的振动侧辊系拆下,将通有循环冷却水的20 mm×30 mm金属模具放置在振动平台上,在振动条件下向模具中注入熔融铝合金,静待其冷却凝固,之后水平切开凝固方坯,腐蚀后观察其凝固组织。
实验以AlSi9Cu3铸造铝合金为研究对象,开浇温度为605 ℃,振动参数如下:振频f为0、10 Hz、20 Hz、30 Hz,振幅A为0.2 mm。
所得振动凝固组织如图3所示。
图3a给出了无振动条件下的粗大枝晶的形貌,图3b~图3d给出了振幅为0.2 mm时振频对晶粒度的影响。
1.左侧固定结晶辊2.浸入式水口3.右侧振动结晶辊(a)单侧辊振动铸轧原理(b)振动铸轧机图1 φ160 mm×150 mm振动式薄带铸轧机Fig.1 φ160mm×150 mm vibrationroll-casting machine表1 AlSi9Cu3铝合金质量分数Tab.1 Mass fraction of AlSi9Cu3 %SiMgMnZnCuNiTi9.00.30.61.23.00.50.2(a)非振动铸轧带坯表面 (b)振动铸轧带坯表面(f=10 Hz)(c)振动铸轧带坯表面(f=20 Hz)图2 不同振动条件下的铸轧带坯表面Fig.2 Surface of cast rolling strip under different vibration conditions(a)f=0(b)f=10 Hz(c)f=20 Hz(d)f=30 Hz图3 不同振动工艺下的铸锭凝固实验结果Fig.3 Experimental results of ingot solidification under different vibration conditions如图3a所示,柱状晶致使铸件产生各向异性、偏析加重、变形性能变差,且由于模具急冷造成铸锭温度场突变过快,因而出现了明显的热裂纹,热裂纹沿着柱状晶晶界开裂且不易消除,严重影响铸锭的二次加工。
当引入振动源后(图3b),铸锭内部的柱状晶区域明显缩小,且边界层柱状晶组织得到明显细化,除此以外,铸锭芯部出现了部分等轴晶区,等轴晶组织第二相分布均匀,缺陷少,具有较好的力学性能。
然而低频激振下,凝固组织中形核率较低,因而等轴晶区晶粒较为粗大,且在边部区域依然有裂纹的存在。
由图3c和图3d可明显看出,随着振动频率的增大,形核率也显著增大,芯部等轴晶区面积增大,且晶粒数增多,晶粒也更加细小。
这主要是由于振动作用,枝晶臂的生长受到抑制,枝晶臂无法向〈0 0 1〉方向延伸,因而形成等轴晶组织,且随着晶核数量的增加,芯部等轴晶得到了明显细化。