铸轧机相关技术资料
连续铸轧技术
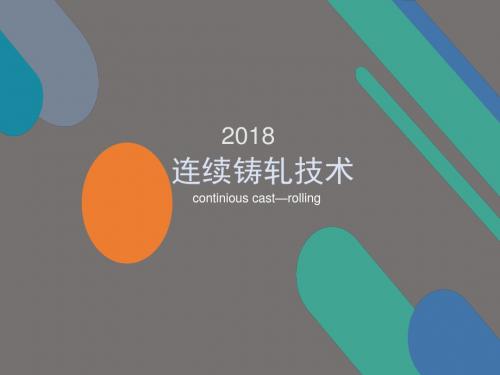
水冷速度 铸轧速度 辊套厚度
辊套材料
例
(3) 连续铸轧的设计参数
① 铸轧角
两辊铸轧中心连线和供料嘴顶 端到铸轧辊中心连线所形成的角 度,即为铸轧角,如右图所示, α一般在 5º~ 10º之间。h为铸轧 区的高度。
O h
R
铸轧角示意图
② 辊径的选择
铸轧辊径一般采取大些尺寸 为好,这样铸轧冷却得好,辊 径越大,在铸轧角一定的情况 下,铸轧区加长,有利于热交 换,辊径一般在 400~550mm 之 间
① 铸轧温度
一般比所铸轧的金属熔点高60~80℃。如果铸轧温度过低,金 属溶液冷凝在浇注系统中,如果过高,则不易成形,或板坯质 量变差。
② 铸轧速度
铸轧速度必须是无级调速。铸轧过程中冷却速度的调整主要是 靠铸轧速度,同时,水冷强度也起着配合作用。
③ 冷却强度
在铸轧过程中,单位时间,单位面积 影响冷却 速度的因 上导出热量的大小即为冷却强度。 素 液体金属 铸轧 向外导热 冷却强度 在铸轧时 速度慢 时间充分 增加 停留时间长
2018
连续铸轧技术
continious cast—rolling
连续铸轧:金属熔体在连续铸造凝固的同时进行轧 制变形的过程。 工艺特点:结晶器为两个带水冷系统的旋转铸轧辊 ,熔体在其辊缝间完成凝固和热轧两个过程,而且 是在很短时间内(2~3s)完成的。 与连铸连轧的区别:连铸连轧实质上是将薄锭坯铸 造与热轧连续进行,即金属熔体在连铸机结晶器中 凝固成厚度约 50~90mm 的坯后,再在后续的连轧 机上连续轧成板材,其铸造和轧制是两道独立的工 序。
③ 铸轧辊套的选择
a) 有足够的导热性能; b) 有较高的力学性能; c) 耐高温; d) 耐热交变应力的疲劳作用
浅谈铝业公司铸轧工作的流程和技术
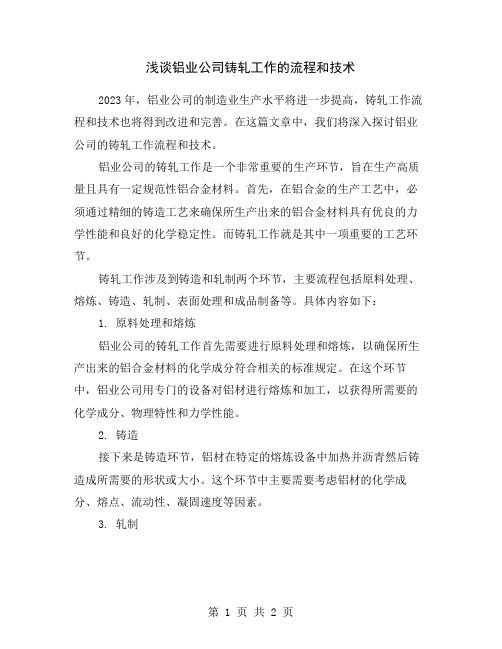
浅谈铝业公司铸轧工作的流程和技术2023年,铝业公司的制造业生产水平将进一步提高,铸轧工作流程和技术也将得到改进和完善。
在这篇文章中,我们将深入探讨铝业公司的铸轧工作流程和技术。
铝业公司的铸轧工作是一个非常重要的生产环节,旨在生产高质量且具有一定规范性铝合金材料。
首先,在铝合金的生产工艺中,必须通过精细的铸造工艺来确保所生产出来的铝合金材料具有优良的力学性能和良好的化学稳定性。
而铸轧工作就是其中一项重要的工艺环节。
铸轧工作涉及到铸造和轧制两个环节,主要流程包括原料处理、熔炼、铸造、轧制、表面处理和成品制备等。
具体内容如下:1. 原料处理和熔炼铝业公司的铸轧工作首先需要进行原料处理和熔炼,以确保所生产出来的铝合金材料的化学成分符合相关的标准规定。
在这个环节中,铝业公司用专门的设备对铝材进行熔炼和加工,以获得所需要的化学成分、物理特性和力学性能。
2. 铸造接下来是铸造环节,铝材在特定的熔炼设备中加热并沥青然后铸造成所需要的形状或大小。
这个环节中主要需要考虑铝材的化学成分、熔点、流动性、凝固速度等因素。
3. 轧制然后是轧制环节。
顾名思义,铝材需要通过轧辊等设备进行轧制,以获得所需要的产品规格和外观要求。
轧制环节中较为关键的是轧制温度和轧制速度,这两个因素将影响铝材的外观和性能特点。
4. 表面处理在铝材被轧制成所需的形状和尺寸之后,需要进行表面处理,主要包括酸洗、氧化、喷雾油、切割等。
这个环节中的表面处理措施的主要目的是增加铝材的抗腐蚀性和美观度,以提高铝材的整体质量。
5. 成品制备最后是成品制备环节,也是铸轧工作的最后一个环节。
在这个环节中,铝材被切割成所需的大小和尺寸。
这个过程不仅需要考虑产品规格和外观,还要考虑整体质量和成本。
综上所述,铝业公司的铸轧工作流程和技术相当复杂和精细,需要用先进设备和管理方法来保证产品质量。
未来,铝业公司的铸轧工作将继续发展和完善,将会更加多样化,并将继续保持其技术和管理领先地位,为行业市场的需求提供优质的铝合金材料。
铸轧机相关技术资料

设备工艺描述及装机水平生产工艺描述铸轧机是把在经过静置炉精炼后的铝液,经静置炉口⇒液面自动控制装置⇒除气箱内进一步精炼⇒过滤⇒前箱嘴子⇒相向转动且内部通有循环冷却水的铸轧辊,使铝液结晶并产生一定的变形率,从而实现铝及铝合金由熔融的液态金属铸轧成6~10 mm铸轧板材,在经过切头⇒卷取后,形成铸卷带材的工艺过程。
本铸轧机架的轴线与地面垂直线成15°倾斜配置(垂直中心线与轧机中心线间),使得在轧制过程中对克服金属偏析和减少金属氧化膜处的表面张力方面具有独到之处。
熔炉和铸轧机之间稳定的液面对轧制的顺利运行至关重要。
液面由一流口流量控制装置,通过调节出口流量来保持恒定。
铸轧的铝合金熔体必须连续供给,并必须清洁,且具有一致的化学成份,经除气装置进一步精炼,接着流入过滤装置,经过过滤后的铝液流入铸轧机前箱。
在熔炉和铸轧机之间,由钛丝送给器把最多两根铝钛硼丝按预先设定的恒定速度送入流槽系统,从而达到细化晶粒的目的。
该铸轧机特有的15︒倾角和前箱内精确的液位控制装置结合,保证前箱能在极其精确的压力下为铸嘴供给铝液。
通过铸嘴的注口,将铝液注入经冷却水冷却的轧辊上,铝液沿轧辊表面宽向分布。
这时,金属处于稍前于轧辊中心线的辊缝处,使液态金属在很短的时间内冷却、凝固,完成整个铸造结晶过程,接着受热轧制成形,形成铸轧板带。
在该过程中熔溶状态铝液的大量热能被轧辊迅速带走。
由于热量是通过铸轧辊传递的,这就要求辊套导热性能必须好。
在轧制过程中,轧辊辊套除了承受轧制机械载荷作用外,还承受着高温←→低温周期性的热载荷的冲击,轧辊外表面每一瞬时都有局部承受着高温金属加热,而内表面则承受着低温强力冷却作用。
因此辊套的结构、材质,冷却水水温的控制都是铸轧成败的主要因素。
铸轧机每侧铸嘴可水平和垂直进行单独精确调整,确保轧出合格的铸轧板材。
铸轧机的每个轧辊都单独由直流电机和行星齿轮减速箱驱动,同步控制由全数字式控制系统实现。
通过火焰喷涂系统在铸轧辊表面不断形成具有分离和润滑作用的集碳,防止铝液粘辊。
连续铸轧技术综述
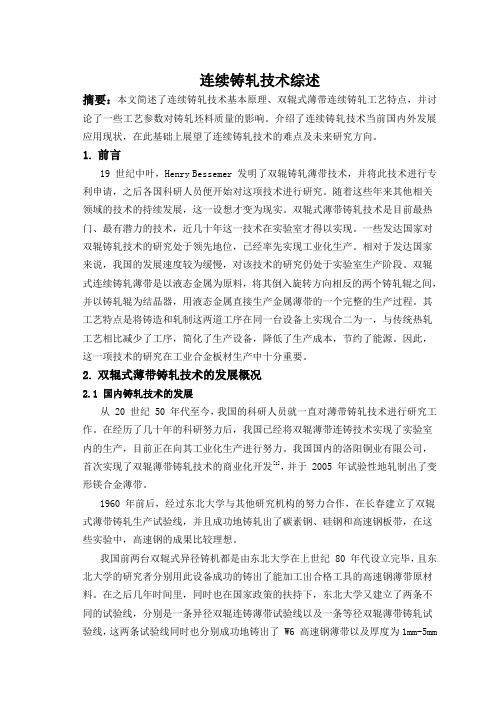
连续铸轧技术综述摘要:本文简述了连续铸轧技术基本原理、双辊式薄带连续铸轧工艺特点,并讨论了一些工艺参数对铸轧坯料质量的影响。
介绍了连续铸轧技术当前国内外发展应用现状,在此基础上展望了连续铸轧技术的难点及未来研究方向。
1.前言19 世纪中叶,Henry Bessemer 发明了双辊铸轧薄带技术,并将此技术进行专利申请,之后各国科研人员便开始对这项技术进行研究。
随着这些年来其他相关领域的技术的持续发展,这一设想才变为现实。
双辊式薄带铸轧技术是目前最热门、最有潜力的技术,近几十年这一技术在实验室才得以实现。
一些发达国家对双辊铸轧技术的研究处于领先地位,已经率先实现工业化生产。
相对于发达国家来说,我国的发展速度较为缓慢,对该技术的研究仍处于实验室生产阶段。
双辊式连续铸轧薄带是以液态金属为原料,将其倒入旋转方向相反的两个铸轧辊之间,并以铸轧辊为结晶器,用液态金属直接生产金属薄带的一个完整的生产过程。
其工艺特点是将铸造和轧制这两道工序在同一台设备上实现合二为一,与传统热轧工艺相比减少了工序,简化了生产设备,降低了生产成本,节约了能源。
因此,这一项技术的研究在工业合金板材生产中十分重要。
2.双辊式薄带铸轧技术的发展概况2.1 国内铸轧技术的发展从 20 世纪 50 年代至今,我国的科研人员就一直对薄带铸轧技术进行研究工作。
在经历了几十年的科研努力后,我国已经将双辊薄带连铸技术实现了实验室内的生产,目前正在向其工业化生产进行努力。
我国国内的洛阳铜业有限公司,首次实现了双辊薄带铸轧技术的商业化开发[1],并于 2005 年试验性地轧制出了变形镁合金薄带。
1960 年前后,经过东北大学与其他研究机构的努力合作,在长春建立了双辊式薄带铸轧生产试验线,并且成功地铸轧出了碳素钢、硅钢和高速钢板带,在这些实验中,高速钢的成果比较理想。
我国前两台双辊式异径铸机都是由东北大学在上世纪 80 年代设立完毕,且东北大学的研究者分别用此设备成功的铸出了能加工出合格工具的高速钢薄带原材料。
铝合金连续铸轧和连铸连轧技术

铝合金连续铸轧和连铸连轧技术近几年,铝合金连续铸轧和连铸连轧技术得到了广泛的关注和应用,在航空、交通、电子和生产等领域发挥着重要作用,并取得了可喜的成就。
本文介绍了铝合金连续铸轧和连铸连轧技术,总结其优点和应用领域,并展望未来发展。
首先,让我们先来介绍连续铸轧技术。
连续铸轧是把铸态的毛坯在双辊铸轧机上连续铸轧的一种特殊的铸轧技术。
它不仅可以在一条生产线上完成整体模块的加工,还可以连续涂层、连续切削、连续横切,从而实现大批量生产,提高生产效率。
此外,它还可以提高材料的性能,降低成本,但是操作起来比较复杂,容易出错。
连铸连轧技术,也称为热轧技术,是将铁水经连续送料炉溅射、蒸发冷凝池或冷却池自动加工成一定规范形状的毛坯精加工成所需规格和性能的钢材的一种特殊的技术。
它有很多优点:操作简单,精度高,材料质量好,成品率高,生产效率高,投资少,特别适用于量大、精度高的产品的生产,有较好的经济效益。
铝合金连续铸轧和连铸连轧技术可用于制造高性能的铝空心结构件、铝芯轴以及汽车零部件等铝合金结构件。
它具有节能、环保、能耗低、操作方便等优势,应用于航空航天、汽车、电子电器、医疗器械等领域可以节约资源,提高工作效率。
未来,随着技术的发展,铝合金连续铸轧和连铸连轧技术将更加成熟,获得更多的关注和应用。
同时,随着用户消费趋向的变化,针对不同类型的产品,研究者也会发展出更多新型的生产工艺,以期在节能、环保、成本等方面取得更好的效果。
综上所述,铝合金连续铸轧和连铸连轧技术是近几年中取得可喜成绩的一种先进技术,它具有节能、环保、成本低等优势,将带给我们更多的经济和社会效益。
未来,铝合金连续铸轧和连铸连轧技术将朝更高层次发展,为人类社会做出更多的贡献。
铸轧操作规程

铸轧车间¢1000×1850 ㎜双驱动铸轧机工艺操作规程(一)、设备主要技术参数一、设备主要技术参数表 1二、¢1000×1850 ㎜双驱动铸轧机主要参数 表 2序号 项目单位 数值1 适应材料1 系、 8 系、 3 系2 铸轧板厚 ㎜ ~103 铸轧板宽 ㎜ 900~17004 卷材外径 ㎜ ¢800~17005 最大卷重 ㎏100006 最大轧制力 MN7 最大卷取力 KN 50 8铸轧速度㎜/min800~11009工作辊直径㎜¢950~1000数值13000-15000850360Cz500 硅碳棒6×3项目炉膛尺寸炉子容量炉膛温度功率加热元件热区数序号123456单位㎜ ㎏℃KW(二)、大清炉3.静置炉每一个月进行一次大清炉。
正常情形下,静置炉炉料铸干或者改换合金时进行大清炉。
特殊情形下,由于持续生产相同合金,静置炉长时刻不能铸干或者改换合金时,由生产计划员安排在每一个月 25-31 日之间将静置炉铸干,进行大清炉。
4、大清炉时,先将炉内残留金属全数放干,把炉渣彻底清除,然后撒入20±2 ㎏粉状溶剂,并将炉温升至800℃以上,用三角铲把炉墙、炉角、炉底的渣子彻底铲净、扒出。
(三)、导炉及精炼5.导炉及精炼导炉:5.1.1导炉前静置炉炉膛温度不得低于740℃,熔体导入前,先将炉墙及炉底熔渣松动待精炼后一路扒出。
5.1.2 当熔炼炉内熔体成份合格,温度适合(720-745℃),后即可导炉,若是在熔炼炉内没有精炼,则导炉进程应进行过流精炼。
为保证产品质量熔体在熔炼炉内的保温时刻,(精炼完毕到导炉开始)不得超过一小时,最长不得超过 4 小时不然应在熔体表面撒上覆盖剂,导炉前从头搅拌、扒渣。
并适当降低熔体温度。
5.1.4 正常铸轧进程,导炉前静置炉熔体深度不该低于200mm。
静置炉内精炼:5.2.1 精炼时熔体温度:740~760℃5.2.2 精炼方式:5.2.2.1 每熔次在导炉前(本公司) 采用四氯化碳进行精炼。
铸轧技术概况

第一章铸轧技术概况双辊铸轧是一种用双辊的表面来冷却液态钢水并使之凝固以生产薄带钢的方法,其工艺特点是液体金属在结晶凝固的同时承受压力加工和塑性变形,在很短的时间内完成从液体金属到固态薄带的全过程]1[。
双辊铸轧的平均冷却速度接近100℃/s,因此,其凝固速度要比常规工艺大约快1000倍左右,并能够铸轧出厚度约为常规铸坯1/100的薄带,取消了热轧过程,由于双辊式铸轧冷却速度快,因此,用这种方法有可能生产具有特殊性能的产品。
1.1我国铝连铸连轧机列开发和发展动向铝连铸连轧是把铝的熔炼至热轧六道完全不同的工艺合并为两道的新的铝加工工艺技术,使铝液结晶并产生一定的变形率,从而实现铝及铝合金熔融液态的金属铸轧成6mm~10mm铸轧板材,形成铸轧卷带材的工艺过程。
20世纪60年代,随着这种新的铝加工工艺技术在美国、前苏联等国家先后研制成功,与之匹配的生产设备 --铝连铸连轧机列开始在世界上许多国家进行装备,用这种机列生产铝卷带材,为冷轧薄板和铝箔提供坯料。
由于这种加工工艺的简化,带来了生产设备的大大简化。
用连铸连轧机列生产铝卷带材,具有投资少、见效快、操作简便等一系列优点。
对中小企业,特别是对轻工、民用材极为适用。
正是由于铝连铸连轧工艺及其设备具有上述突出的特点和优势,在今天蓬勃发展的铝加工技术中,特别是在“ 1+3”、“1+4”铝热连轧技术不断应用于工业生产的情况下,连铸连轧工艺依然具有旺盛的生命力,其工艺革新和设备优化具有广阔的空间。
涿神公司作为中国铝加工专用设备的开发研制基地,在20世纪80年代通过与日本株式会社神户制钢所、神钢商事株式会社的合资,积极引进日本神户制钢的先进技术和先进管理经验,成功研制的从Φ650mm到Φ1023m m、辊身长度从1350mm到1900mm的系列连续铸轧机,基本上涵盖了国内铝加工行业所有的规格类型。
公司在1 995年开发研制成功的Φ960 ×1550mm超型连续铸轧机的性能、技术指标都达到甚至超过国际同类设备的水平。
铸轧机的结构设计

铸轧机的结构设计一台机械能否正常运转不仅与其传动系统有着密切的关系, 而且还与结构设计的合理性有着更紧密的关系, 所以本章内容的设计及说明成为本次设计关键部分.铸轧机的主要结构部分包括:轧辊装置,上机架,下机架,侧封装置,和清辊装置. 由于双辊铸轧技术是一种用双辊的表面来冷却液态钢水并使之凝固以生产薄带钢的方法,其工艺特点是液体金属在结晶凝固的同时承受压力加工和塑性变形,在很短的时间内完成从液体金属到固态薄带的全过程. 所以铸轧辊的设计是轧机能够生产高质量棒线材的核心技术. 下面我将从辊芯, 辊套及其冷却方面开始设计。
2.1 铸轧辊套材料的选择及结构设计铸轧辊主要是由一个中心部位钻有进,出水孔,表面带有沟槽的辊芯和一个辊套组成的。
它是铸轧机中最关键的部件,直接响影着产品的质量。
所以辊芯,辊套从材料的选择,结构的设计,加工的顺序,装配的方法到使用过程每一步都显得十分重要。
2.1.1 铸轧辊辊套材料的选择2.1.1.1 铸轧辊辊套的工作负荷在铸轧过程中,熔铝进入连铸机轧制区并直接同辊套外表面接触,而这个辊套的内侧则受到冷却,就是为了吸收液铝中过多的热量,把它转变成固态铝。
因此,这种铸轧辊的工作能力直接取决于辊套材料的热导性,而辊套被装到辊芯上,为了保障这种辊套在高温下都能牢固的固定在辊芯上,这种辊套材料应该有很低的热膨胀率,即必须在温度为600℃时显现出足够的强度和良好的塑性。
由于在运行时受到复杂载荷的作用,在辊套的表面上会产生不同程度的网状热裂纹,裂纹的扩展速率主要是由力学性能和工艺特点决定的,特别是强度和可塑性的比率。
2.1.1.2 铸轧辊材料的选择辊套材料应具备下述特性:导热性好,耐热变负载,有相当高的强度与刚度,不与铝熔体反应,所以确定辊套时要做综合考虑,根据多方面资料搜索,铸轧机辊套通常采用如下两种材料(见表一)这两种材料能使上述所要求的性能之间达到适当的匹配!保证铸轧机具有最好的工作特性。
- 1、下载文档前请自行甄别文档内容的完整性,平台不提供额外的编辑、内容补充、找答案等附加服务。
- 2、"仅部分预览"的文档,不可在线预览部分如存在完整性等问题,可反馈申请退款(可完整预览的文档不适用该条件!)。
- 3、如文档侵犯您的权益,请联系客服反馈,我们会尽快为您处理(人工客服工作时间:9:00-18:30)。
5.卷取:恒张力或梯度张力控制方式,钳口自动准确停位。
6.预应力控制:压力闭环控制。
7.夹送辊:下辊线速度准确控制,保证与机组速度同步。
8.液压剪:与机组速度同步。
9.电控系统具有过载、超速、堵转等检测功能。
10.液压部分:液压泵配置采用一工一备,工作泵故障停运后,备用泵能立即自动启动,不会因此造成断板事故。
驱动电机:2-DC33Kw,900/2000rpm
底座移动油缸:125×450mm
万向联轴器型号:SWC440
轧制状态下,换辊油缸将主传动机构推至工作位置,万向联轴器与轧辊驱动端接触良好,工作位检测开关发出信号至操作台。
换辊时,手动调节涡轮丝杠升降机支撑住上下辊万向联轴器,底座移动油缸将主传动机构拉回,万向联轴器与轧辊脱开。
轧辊轴承型式:四列圆锥滚子轴承
轴承外形尺寸:400/600X 356(d/D X B XT)
轴承座材质:ZG270-500
2-4-3、旋转接头
通径:DN125mm
进回水形式:一进三出
水压:Max0.8Mpa
水温:Max80℃
流量:180T/h
2-5、铸轧辊传动系统
铸轧辊传动系统包括驱动电机2件、双行星减速箱1件、万向联轴器2件、万向联轴器支座1件。
侧弯度
整卷塔型
整卷错层mm
mm
mm
kg
mm
KN
mm
KN.m
mm/min
KN
KW
KW
mm
mm
KN
次/分钟
单位技术参数AA1000-全部
AA3000-3003、3004、3005、3105AA8000-8011、8079
850
1500
6~10
1ቤተ መጻሕፍቲ ባይዱ000
560
15000
300×450
320
2000
160
2-DC33KW,900/2000rpm
热电偶测温范围:0~1000℃
1-5、前箱、前箱框架
前箱由上下两个小箱体组成,并选用强度高、耐热稳定性好的陶瓷纤维材料制成。前箱是熔铝的输送和供给系统的最后一个箱体,前箱内铝液通过一段中间导管与料嘴连接起来,铝液连续稳定地输送到辊缝处,经轧辊的冷却、轧制作用形成板带。
前箱框架放置在前箱外围,用于保护前箱,前箱框架上装有前箱液面自动控制装置。
附件二主要技术参数技术参数名称单位技术参数铝合金aa1000全部aa30003003300430053105aa8000801180798501500610110005601500030045032020001602dc33kw9002000rpmdc135kw9451600rpm2000最大6103006边边差05板厚一周纵向厚差10板厚2mmm60mm头尾3圈除外50mm轧辊直径最大带宽带材厚度范围最大卷材重量压上油缸直径最大预载力牌坊立柱尺寸单辊最大扭矩轧辊最大线速度最大卷取张力主机传动电机卷取机传动电机卷材外径卷材内径液压缸剪切力剪切频率横向同板差纵向厚差侧弯度整卷塔型整卷错层mmmmmmkgmmknmmknmmmminknkwkwmmmmkn次分钟机列方向从右向左从左向右各一台机组设备组成及详细说明1熔铝的输送和供给系统熔铝的输送和供给系统是铸轧机稳定运行保证带材质量的关键环节
1-1、流槽液面控制装置
流口位置有一个垂直导向的浮标,采用手动调至精确位置,浮标的高度位置以脉冲形式检测,检测结果送到流口液位控制系统,使电动执行器动作,控制流口的塞杆运动,达到控制流口液位的目的,液面控制精度达3mm;同时该控制系统也可手动进行人工控制。
液面控制装置对流口液面的高位和低位设定一个基准值,当接近开关检测液面波动超过高位或低于低位时,提示操作手进行人工干预,避免事故发生。
包括:随机的2根铸轧辊、4个轴承座、4个轧辊轴承、2个轧辊冷却水旋转接头;
2-4-1、铸轧辊
轧辊型式:辊芯辊套热装式
轧辊辊面尺寸:850×1700mm
铸轧辊由辊芯辊套热装配而成,两端由O形密封圈密封。热装配后进行精磨至目标尺寸。冷却水系统通过安装在铸轧辊操作侧的轧辊冷却水旋转接头和铸轧辊内部的冷却水循环通道连通,由冷却水带走轧制热。
通过火焰喷涂系统在铸轧辊表面不断形成具有分离和润滑作用的集碳,防止铝液粘辊。
铸轧带材离开辊缝后,通过导出辊、夹送辊、液压剪、偏导辊,由直流电机驱动的下卷式卷取机进行卷取。卷取机可提供铸轧板带的张力。当带材尺寸符合要求时,需在不停止铸轧生产过程的情况下剪切带材。为了完成这一操作过程,系统配有一套液压驱动的夹送辊,以保持铸轧机出口处的张力。该夹送辊在同步剪切机剪切前夹紧,在换卷后立即打开。
铸轧辊传动系统由两台直流电机各驱动一台双行星减速箱,通过两根万向联轴器驱动铸轧辊同步转动。通过上/下辊直流电机控制器来保证上/下辊线速度一致。接轴支架是为了换辊时支撑住万向联轴器而设置的。主传动机构和万向联轴器支座安装在由油缸驱动的滑座上,滑座在换辊油缸驱动下,可在底座上滑动。
单辊最大传动扭矩:320KN.m
2、主机机组
主机机组是铸轧机的主体部分,主要包含以下项目:
2-1、铸嘴调整装置
铸嘴平台在液压缸推动下在滑座上滑动,把铸嘴及其辅助件推至距铸轧机辊缝一定安全距离的位置,然后由铸嘴水平调节装置把铸嘴调节到目标位置,铸嘴的水平和垂直调整由手动进行调节。铸嘴平台为耐热铸铁结构,安装在一经机加工的钢板架上。铸嘴平台设有一快速夹紧装置,用于把铸嘴组件固定在铸嘴平台上。
本铸轧机架的轴线与地面垂直线成15°倾斜配置(垂直中心线与轧机中心线间),使得在轧制过程中对克服金属偏析和减少金属氧化膜处的表面张力方面具有独到之处。
熔炉和铸轧机之间稳定的液面对轧制的顺利运行至关重要。液面由一流口流量控制装置,通过调节出口流量来保持恒定。铸轧的铝合金熔体必须连续供给,并必须清洁,且具有一致的化学成份,经除气装置进一步精炼,接着流入过滤装置,经过过滤后的铝液流入铸轧机前箱。在熔炉和铸轧机之间,由钛丝送给器把最多两根铝钛硼丝按预先设定的恒定速度送入流槽系统,从而达到细化晶粒的目的。
1-2、双通道钛丝进给装置
包括钛丝送进器和放丝架两部分,钛丝送进器用交流变频电机驱动,钛丝送给速度可调,操作者可以调整钛丝杆的速度和铸轧机速度匹配。
钛丝驱动电机:
功率:0.75KW
速度:1500rpm
钛丝送进速度:150~500mm/min
钛丝直径:8~12mm
钛丝卷内径:≥280mm
钛丝卷重:≤200Kg
11.铸嘴平台:与铝液高温接触的部位采用耐热铸铁。微调采用手动,设计、制造、安装时要充分考虑安全性、可靠性,不能因前箱和铸嘴漏、跑铝而造成传动、信号、电缆等部件或机构损坏。12.流口箱液位高度由接近开关检测并自动控制,前箱液位自动控制。控制精度为±1mm。
13.触摸式显示屏设置在主操作台,用于参数设定、显示和机列状态监控。
为方便立板前清洁轧辊辊面、对料嘴,立板时跑渣等操作,导出辊操作侧可以打开,并沿驱动侧销轴转至驱动侧;立板完成,较完整带坯从轧辊轧出,立即将导出辊合上,并把操作侧锁紧销轴锁定。铸轧板通过导出辊,立即开启导出辊冷却水。
导出辊尺寸:210×1700mm
冷却水旋转接头型号:HS-G25-10
2-4、铸轧辊部件
0.15ml/100g以下,合金的化学成分应该在国家标准中规定的含量范围内,不产生巨大的内部金属颗粒的杂质;保证前箱内铝液温度和液面高度恒定,根据铸轧工艺不同,应控制熔炼炉、静置炉、除气过滤装置中铝液的温度,使经过熔铝的输送和供给系统进入到前箱中的铝液温度控制在685-705℃,且温度波动不超过±2℃。保温炉流口至铸轧机之间熔铝的输送系统包括以下设备:
卷材通过卸卷小车和液压推卷装置从卷取机上卸下卷材,完成整个铸轧生产过程。
装机水平
1.该轧机为倾斜式轧机,机架可摆动直立,采用换辊小车换辊。
2.传动方式:采用直流电机,上下辊单独传动,具有速度补偿功能。
3.辊缝预调整方式:粗调为调整垫块厚度和手动棘轮扳手通过丝杠双斜楔来预置辊缝,微调采用调节压上缸压力调节。
设备工艺描述及装机水平
生产工艺描述
铸轧机是把在经过静置炉精炼后的铝液,经静置炉口液面自动控制装置除气箱内进一步精炼过滤前箱嘴子相向转动且内部通有循环冷却水的铸轧辊,使铝液结晶并产生一定的变形率,从而实现铝及铝合金由熔融的液态金属铸轧成6~10 mm铸轧板材,在经过切头卷取后,形成铸卷带材的工艺过程。
DC13.5KW,945/1600rpm
2000(最大)
610
300
6
边—边差≤0.5%板厚
一周纵向厚差≤1.0%板厚
≤2mm/m
≤±6.0mm (头尾3圈除外)
≤±5.0mm
机列方向:从右向左、从左向右各一台机组设备组成及详细说明
1、熔铝的输送和供给系统
熔铝的输送和供给系统是铸轧机稳定运行、保证带材质量的关键环节。熔铝的输送和供给系统的最终目的是连续提供给前箱合格的铝液,含氢量控制在
铸轧机的每个轧辊都由直流电机和行星齿轮减速箱驱动,同步控制由数字式直流控制系统进行。
牌坊立柱断面:300450mm2
牌坊材质:ZG270-500
牌坊刚度:2000T/mm
机架倾翻油缸:200×450mm2件
机架锁紧油缸:80×150mm2件
2-3、导出辊装置
导出辊装置设置在铸轧机本体的出口,导向辊表面镀硬铬且内部通有循环冷却水,用于带材的导向和确定带材运行的标高,因此又称标高辊。
2-4-1-1、辊套
材质:32Cr
3Mo1V
表面热处理硬度:HB390~430
其中硬度不均匀性不超过±5HB
表面光洁度:Ra0.6-0.7
新辊套标称壁厚:60mm
最小壁厚:25~30mm
2-4-1-2、辊芯
材质:42CrMo
辊芯硬度:HB280-320