汽车主减速器传动比优化
整车动力经济性速比匹配优化策略

3.2经济性验算分析
经济性的计算及验算过程主要是根据已经确定的发动机万有特性及各传动系的参数值依据不同运行工况对车辆燃油消耗量的计算及验算。经济性测量的内容较简单,只需要测量汽车不同运行工况状态的耗油量即可。但是计算、验算等过程也比较复杂,因为需要多次进行测试,确定车辆的空气阻力、滚动阻力等阻力功率的大小,以及变换汽车的行驶状态,按空载、满载、爬坡等多种不同的运行工况来测量。且在不同的路况或者行驶状态下,油耗量也会有一定的差异性。因此,需要进行多次的测量、计算以及验算才能够保证其结果的准确性。
4.3变速箱+后桥速比匹配
变速箱以及后桥速比的匹配情况是在发动机功率恒定的情况下进行的,变速箱的匹配情况主要需要根据汽车在坡路上行驶的状况进行调整、匹配,变速箱配比需要根据整车最大爬坡度和最大起步坡度要求,计算传动系总速比I0×I1的范围,来确定合适的速比匹配。同时,变速箱以及后桥速比的匹配对汽车燃油经济性的好坏也有着重要影响。总之,需同时考虑动力性及经济性的要求来合理匹配变速箱与后桥的速比。除此之外,汽车需求的常用车速区间不同会对变速箱以及后桥速比匹配情况产生一定的影响,需要对汽车行驶速度进行参考。
4.4整车动力性经济性匹配优化
整车动力性经济性匹配优化设计在推广应用过程中存在整车的动力系统出现受热面磨损的问题,整车炉膛的布风板风出现磨损、漏渣严重等问题。整车动力性经济性匹配优化设计的漏渣和磨损问题不仅与不合理的整车动力设计结构有关,还与整车动力的整体设计有关,因而整车动力性经济性匹配优化设计人员应仔细审阅整车动力设计方案,做好反复的整车动力检查工作。为了防止整车动力性经济性匹配优化设计结构的磨损范围在不断扩大,在采用整车动力性经济性匹配优化设计时应对动力材料进行合理选择,减少整车动力系统的脱落、磨损概率。
4806电动汽车传动系统速比的优化计算

率也基本上能满 足电动汽车的动力性要 求。根据设计 要求 ,
本 文 设 计 的 电动 轿 车 整 车 动 力 性 能 及 相 关 参 数 见 表 1 列 。 所 表 1 整 车 动 力 性 等 参 数 要 求
参数名称
参 数 值
1 0 o 0
1 动 力 系 统 结 构 及 动 力性 要 求
第3 2卷
第 2期
四 川 兵 工 学 报
2 1 年 2月 01
【 制造 技术 】
40 8 6电 动 汽 车 传 动 系 统 速 比 的 优 化 计 算
王德 伦 叶 成 涛 罗劲松 徐 才 贵 , , ,
( . 庆理 工 大 学 重 庆 汽 车 学 院 , 庆 1重 重 4 0 5 ; . 北 御 捷 车业 有 限公 司 , 北 清河 000 2河 河 0 40 ) 5 8 2
摘 要 : 保 证 动 力 性 的 同时 , 了提 高 整 车 经 济 性 , 须 对 传 动 系 统 速 比进 行 合 理 选 取 。 以某 纯 电 动 汽 车 为 例 , 据 在 为 必 根 动 力 性 没计 要 求 , 择 了合 适 的 电机 , 选 同时 对 电 机 和 传 动 系 统 速 比 进 行 合 理 的 匹 配 和 优 化 计 算 , 将 其 进 行 实 车 试 并 验 。结 果 表 明 , 任保 证 最 高 车 速 的前 提 下 , 化 后 的速 比降 低 了 电池 放 电 电 流 , 长 电 池 的放 电 时 间 , 而 提 高 了 优 延 从 整车的续驶里程 。 关 键 词 : 动 汽 车 ; 车试 验 ; 比 ; 化 计 算 电 实 速 优
自动变速器效率及主减速比优化对整车性能影响研究

自动变速器效率及主减速比优化对整车性能影响研究代立宏; 胡昌才; 胡鹏【期刊名称】《《汽车实用技术》》【年(卷),期】2019(000)015【总页数】3页(P35-37)【关键词】8档自动变速箱; 变速箱效率; 精细化标定; 整车性能【作者】代立宏; 胡昌才; 胡鹏【作者单位】奇瑞商用车有限公司安徽芜湖 241009【正文语种】中文【中图分类】U469.11概述在日益火爆的汽车市场,由于自动变速器具有消除驾驶技术差异,操作方便的特点,所以搭载自动变速器的车辆在激烈的市场竞争中占有很大市场份额[1]。
自动变速箱技术有电控机械式自动变速箱(AMT)、液力自动变速箱(AT)、无级自动变速箱(CVT)、双离合自动变速箱(DCT)等自动变速箱。
由于AT 技术相对成熟,改善AT 的燃油经济性成为变速箱制造厂家提高竞争力的关键。
增加AT 的档位是燃油经济性的途径之一,因此,自动变速箱从最开始的4AT逐渐发展到6AT、7AT,直到最新推出的8AT。
由于8AT 挡位多、提速快且省油的特点,因此有更为乐观的市场前景。
文献[2~4]对优化变速箱内部结构改善效率进行详细研究;文献[1,5~7]对变速箱效率改善及对整车影响做了较多研究,对整车厂具有理论指导。
本文基于某款乘用车8AT 变速箱,针对实际开发中动力性和经济性满足不了设定目标,进行变速箱硬件效率提升、精细化标定及主减速比优化三个维度开展工作,最终动力性经济性指标均完成并优于设定目标,具有指导意义。
1 实验部分1.1 整车关键参数以8 档自动变速箱为主要研究对象,如表所示,通过优化效率,精细化标定及主减速比优化,测试上述优化方案在一款SUV 乘用车上动力学、经济性的效果。
该整车关键参数见表1 所示。
表1 整车关键参数?1.2 变速箱硬件效率提升方案方案1 是采用低排量油泵,措施有降低电磁阀泄漏和优化系统润滑。
原油泵17cc,降低至14cc 和12cc 两种方案进行验证,排量降低可降低泵的拖拽扭矩,从而提高变速器整机效率。
汽车动力传动系传动比的优化设计

3.2 经济性目标
先用曲面拟合的方法拟合出发动机油耗的
万有特性曲面, 可以得出以发动机功率和转速为
自变量的油耗率多项式 ge=ge( ne, Pe) 在 第 i 挡( 传 动 比 为 xi) 和 车 速 va 下 发 动 机
的转速和功率为
ne=
va·i0·xi 0.377r
(
r/min)
$ % Pe=
6 结束语
( fgoalattain) 、求 解 边 界 约 束 条 件 下 的 非 线 性 最 小化 ( fminbnd) 、求解有约束的非线性最小 化
本文建立了汽车传动系统优化数学模型, 并 利用 Matlab 的优化模块实现汽车传动系传动 比
( fmincon) 、求 解 最 小 最 大 化( fminimax) 、求 解
式中[ D0max] — ——汽车最高动力因数的下限
值。
2
( D0max=
Pemax·x4·x5·ηt / r) -( G
CD·A·va /21.15)
va — ——当 汽 车 处 于 最 高 挡 时( 传 动 比 x4) 对
应于 nM 时的车速。
( 4) 为了满足汽车最高车速的要求, 则有:
g11( X) =( 0.377nN·r/x4·x5) -vamax≤0
标函数的数学模型可以通过 Matlab 编制程序 建
立。
3.3 约束条件
( 1) 保证变速器传动比设计要求: 汽车的变
速器传动比要求大致按等比级数排列, 这样使发
动机的最高和最低转速固定,
即公比
T=
&X n-1 1
,
n
为挡位数, 根据这个要求可以得到约束条件
g1( X) =0.9T-x1 / x2≤0 g2( X) =x1 / x2-1.15T≤0 g3( X) =0.85T-x2 / x3≤0 g4( X) =x2 / x3-1.10T≤0 g5( X) =0.80T-x3≤0 g6( X) =x3-1.05T≤0 g7( X) =0.72-x4≤0 g8( X) =x4-0.82≤0 ( 2) 为了满足汽车最大爬坡度的要求, 则应
轿车变速器主减速从动齿轮制造工艺优化

轿车变速器主减速从动齿轮制造工艺优化主减速齿轮是轿车变速器一对重要的齿轮,在总成工作过程中长期啮合,通常精度要求较高;其中的从动齿轮由于结构原因,热处理变形比较大,同时其工作精度又受到与差速器壳体之间装配精度的影响。
本文针对主减从动齿轮原有制造工艺存在的问题,提出了工艺优化方案,通过热变形控制、装配铆接以及磨齿的试验验证,确定了该工艺方案的可行性,实现了工作精度的大幅度提升,并减少加工工序,降低生产成本;其工艺控制指标可以直接应用于生产控制。
一款自主开发变速器采用横置式结构,差速器壳体总成部件集成于变速器之中。
差速器壳体总成由差速器壳体和主减速从动齿轮两个零件铆接而成,两者之间的配合关系为过盈配合。
总成部件的实际工作精度为铆接之后的齿轮精度,且各项精度指标按6级(GB 10095)统一要求,精度要求较为严格。
一方面,从动齿轮零件本身由于结构原因容易产生较大的热处理变形;另一方面,从动齿轮在与差速器壳体铆接时齿轮精度会有一定损失,故依原有的将两个零件均加工至成品状态最后铆接的工艺难以保证齿轮的工作精度。
本文通过一系列的精度分析及热变形和铆接磨齿试验对主减速从动齿轮的制造工艺进行了优化,达到了保证精度的同时降低成本的效果。
意大利瑟肯PAC渗碳防渗涂料(涂远:************、153****0013)01从动齿轮制造工艺分析主减速从动齿轮的原制造工艺为先将齿轮加工至成品状态,再与差速器壳体零件进行装配铆接,经过对各项齿轮精度的检测,发现即使铆接前齿轮精度可以达到图纸要求,但由于铆接造成的齿轮精度损失,仍会导致总成部件齿轮工作精度超差,如图1所示。
图1 原有工艺铆接精度损失这种磨齿之后铆接的工艺不仅铆接过程中的精度损失难以控制,而且由于磨齿的定位装夹需求,从动齿轮的内孔和端面必须进行热后硬加工,这也造成了制造成本的增加。
针对这两个问题,本文提岀从动齿轮热后不机加,直接与差速器壳体铆接,再进行磨齿加工的工艺。
汽车传动系统技术的性能调优

汽车传动系统技术的性能调优汽车传动系统是汽车的重要组成部分,对于汽车性能的提升和驾驶体验的改善起着至关重要的作用。
在现代汽车工业中,为了追求更高的性能和更好的燃油经济性,对汽车传动系统进行性能调优已经成为一项不可或缺的工作。
性能调优旨在优化汽车传动系统的各个方面,包括提高动力输出、提升燃油经济性、改善换挡平顺性等。
下面将从三个方面介绍汽车传动系统技术的性能调优。
提高动力输出是汽车传动系统性能调优的一个重要目标。
为了实现更高的动力输出,可以通过多种方式进行调整。
首先是优化发动机和变速器之间的匹配程度,确保发动机能够在最佳转速范围内工作,从而提供最大的动力输出。
还可以通过改变齿轮比来调整动力输出的特性,例如增大低速齿轮比,以提供更强的起步动力。
采用先进的涡轮增压技术、进口增压器及增压比的改变等方式,可以显著提高发动机的动力输出。
提升燃油经济性也是汽车传动系统性能调优的重点。
在现代社会,环保和能源效率已经成为汽车发展的重要方向。
汽车厂商和工程师们致力于不断研发新的技术,以减少燃油消耗并降低尾气排放。
为了实现更好的燃油经济性,可以采用多种技术手段。
例如,通过优化换挡逻辑和控制策略,使得变速器能够更加智能地选择适合当前驾驶状态的挡位,以最小化燃油消耗。
还可以使用轻量化材料来减少汽车整体重量,减少发动机的负荷,从而提高燃油经济性。
优化空气动力学设计和减少滚动阻力,也可以降低汽车的空气阻力,进而提升燃油经济性。
改善换挡平顺性也是汽车传动系统性能调优的一个重要方面。
汽车的换挡平顺性对于驾驶者的体验和操控感觉至关重要。
一个平顺的换挡过程可以提升驾驶者的舒适感,并减少传动部件的磨损。
为了达到更好的换挡平顺性,可以通过优化变速器的结构和控制系统来实现。
例如,使用更高品质的离合器和变速器组件,可以减少部件之间的摩擦和冲击,进而提升换挡平顺性。
采用先进的电子控制系统,可以更精准地控制变速器的换挡时机和速度,以实现更加平滑的换档过程。
汽车动力传动系统参数优化匹配方法

1机械传动汽车动力传动系统参数的优化通常包括发动机性能指标的优选,机械变速器传动比的优化和驱动桥速比的优化,以下分别阐述。
7.1汽车发动机性能指标的优选方法 在汽车设计中,发动机的初选通常有两种方法:一种是从保持预期的最高车速初步选择发动机应有功率来选择的,发动机功率应大体上等于且不小于以最高车速行驶时行驶阻力功率之和;一种是根据现有的汽车统计数据初步估计汽车比功率来确定发动机应有的功率。
在初步选定发动机功率之后,还需要进一步分析计算汽车动力性和燃料经济性,最终确定发动机性能指标(如发动机最大转矩,最大转矩点转速等)。
通常在给定汽车底盘参数、整车性能要求(如最大爬坡度max i ,最高车速m ax V ,正常行驶车速下百公里油耗Q ,原地起步加速时间t 等),以及车辆经常运行工况条件下,就可以选择发动机的最大转矩T emax ,及其转矩n M ,最大功率max e P 及其转速P n ,发动机最低油耗率min e g 和发动机排量h V 。
在优选发动机时常常遇到两种情况:一种情况是有几个类型的发动机可供选择,在整车底盘参数和车辆经常行驶工况条件确定时,这属于车辆动力传动系合理匹配问题,可用汽车动力传动系统最优匹配评价指标来处理。
第二种情况是根据整车性能要求和汽车经常行驶工况条件来对发动机性能提出要求,作为发动机选型或设计的依据,而这时发动机性能是未知的。
对于计划研制或未知性能特性指标的发动机性能可看作为发动机设计参数和运行参数的函数,此时,外特性和单位小时燃油消耗率可利用表示发动机的简化模型。
优选汽车发动机参数的方法: (1) 目标函数F (x )目标函数为汽车行驶的能量效率最高。
(2) 设计变量X],,,,[max h M p e em V n n P T X(3) 约束条件1) 发动机性能指标的要求 发动机转矩适应性要求:3.1/1.1≤≤P em T T转矩适应性系数也可参考同级发动机试验值选取。
15-汽车主减速器的优化设计
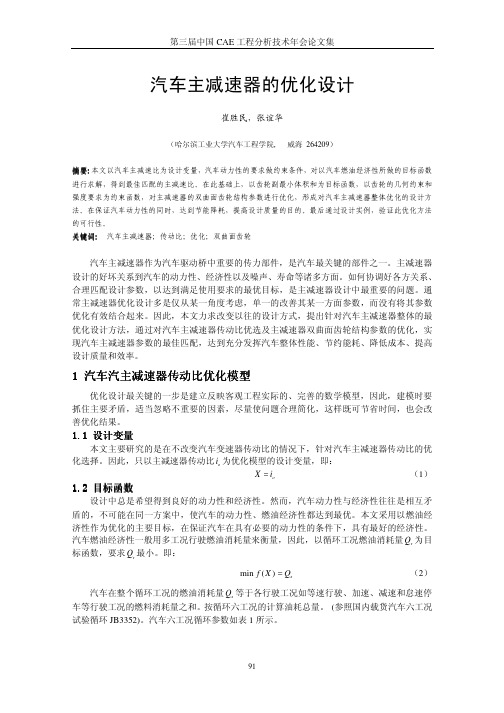
σ w1 ≤ [σ w ] σ w 2 ≤ [σ w ]
齿轮的接触强度约束为:
σj ≤ σ j
式中 σ w1 为主动齿轮弯曲应力; σ w 2 为从动齿轮弯曲应力; σ j 为主动齿轮接触应力; [σ w ] 为 齿轮材料的许用弯曲应力; σ j 为齿轮材料的许用接触应力。 综合上述约束条件,按优化设计方法可得出 9 个约束函数表达式,即: s.t
3 优化设计实例及结果分析
本文设计选特拉卡汽车,总重为 2580kg,轮胎半径 0.376m,主减速器传动比 4.743,发 动机最大功率 90 kw,最大扭矩 200N·m。主减速器为双曲面齿轮传动,齿轮材料为 20Cr。 根据前面建立的汽车主减速器传动比的优选模型,应用黄金分割法,编制计算程序,求 出最佳汽车主减速器传动比为 4.463。从结构上考虑小齿轮齿数为 9,大齿轮齿数为 41,则优 选后的主减速器传动比应调整为 4.56。主减速器传动比优选前、后的汽车整车性能对比如表 2 所示。
பைடு நூலகம்
1 汽车汽 汽车汽主减速器传动比优化模型 主减速器传动比优化模型
优化设计最关键的一步是建立反映客观工程实际的、完善的数学模型,因此,建模时要 抓住主要矛盾,适当忽略不重要的因素,尽量使问题合理简化,这样既可节省时间,也会改 善优化结果。
1.1 设计变量
本文主要研究的是在不改变汽车变速器传动比的情况下,针对汽车主减速器传动比的优 化选择。因此,只以主减速器传动比 io 为优化模型的设计变量,即: X = io (1)
1.3 约束条件
既然选择了经济性作为目标函数,那么为了满足汽车的动力性能的要求,就应以动力性 要求作为约束条件。以原地起步连续换档加速时间 t 代表汽车的动力性,使时间 t 不得大于设 计要求值 t0 ,即约束条件为: g ( X ) = t − t0 ≤ 0 ( 3) 式中 t0 按汽车定型试验标准对汽车动力性要求:原地起步连续换档加速通过400m所需时 间不大于37秒。 汽车原地起步连续换档加速时间 t 为:
- 1、下载文档前请自行甄别文档内容的完整性,平台不提供额外的编辑、内容补充、找答案等附加服务。
- 2、"仅部分预览"的文档,不可在线预览部分如存在完整性等问题,可反馈申请退款(可完整预览的文档不适用该条件!)。
- 3、如文档侵犯您的权益,请联系客服反馈,我们会尽快为您处理(人工客服工作时间:9:00-18:30)。
汽车主减速器传动比的优化专业班级:车辆11级2班姓名:韦永亮学号:2011 1097某轻型货车,发动机型号为492QC-2,车有关数据如下。
发动机的最低转速nmin=600r/min,最高转速nmax=4000r/min。
整车质量2000kg;整车装备质量1800kg总质量3880kg;车轮半径0.367m;传动系机械效率nT=0.85;滚动阻力系数f=0.013;空气阻力系数*迎风面积CDA=2.77m2;主减速器传动比i0=5.83;飞轮转动惯量If=0.218kg.m2;二前轮转动惯量Iw1=1.798kg.m2;后四轮转动惯量Iw2=3.598kg.m2;1档2档3档4档5档变速器传动比 5.56 2.769 1.644 1.00 0.793汽油发动机使用外特性的Tq-n曲线的拟合公式为:Tq=-19.313+295.27*(n/1000)-165.44*(n/1000)^2+40.874*(n/1000)^3-3.8445*(n/1000)^4.负荷特性曲线拟合公式为:b=B0+B1*Pe+B2*Pe.^2+B3*Pe.^3+B4*Pe.^4.拟合公式中的系数为:N/(r/min) B0 B1 B2 B3 B4815 1326.8 -416.46 72.379 -5.8629 0.17768 1207 1354.7 -303.98 36.657 -2.0553 0.043072 1614 1284.4 -189.75 1452.4 -0.51184 0.0068164 2012 1122.9 -121.59 7.0035 -0.18517 0.0018555 2603 1141.0 -98.893 4.4763 -0.091077 0.00068906 3006 1051.2 -73.714 2.8593 -0.05138 0.00035032 3403 1233.9 -84.478 2.9788 -0.047449 0.000282303804 1129.7 -45.291 0.71113 -0.00075215 -0.0000385 68怠速油耗Qid=0.299mL/s(怠速转速400r/min)。
一.建模1.优化变量我们主要考虑,在汽车变速器传动比不变的情况下,汽车主减速器传动比对经济性和动力性的影响。
所以以主减速器传动比i0作为优化变量。
X=i02.目标函数针对该货车,主要考虑优化经济性,这样的话要求在必要的动力性条件下,要求最小的燃油消耗,即要求百公里油耗尽可能少。
q=minf(X)3.约束条件(1)最高车速要求maxUa(X)>=100km/h(2)动力性要求t(x)<=26.4s(3) 最大爬坡度约束imax(x)>=32.5%(4)最高档动力因数校核D0>=[D0]=0.03二.计算求解1.计算加速时间nT=0.85; r=0.367; f=0.013; CDA=2.77; If=0.218;Iw1=1.798; Iw2=3.598; L=3.2; a=1.947; hg=0.9; m=3880;g=9.8; G=m*g; ig=[5.56,2.769,1.644,1.00,0.793];nmin=600; nmax=4000; i0=5.43;u=0.377*r*nmax./ig/i0;for i=1:5deta(i)=1+(Iw1+Iw2)/(m*r^2)+(If*(ig(i))^2*i0^2*nT)/(m*r^2);%旋转质量换算系数endua=[6:0.01:100]; %最低稳定车速6公里每小时N=length(ua);n=0;Tq=0;Ft=0;inv_a=0;delta=0*ua; %数据初始化Ff=G*f;Fw=CDA*ua.^2/21.15;for i=1:Nk=i;if ua(i)<=u(2) %以二档起步计算n=ua(i)*(ig(2)*i0/r)/0.377;Tq=-19.313+295.27*(n/1000)-165.44*(n/1000)^2+40.874*(n/1000)^3-3. 8445*(n/1000)^4;Ft=Tq*ig(2)*i0*nT/r;inv_a(i)=(deta(2)*m)/(Ft-Ff-Fw(i)); %加速度倒数delta(i)=0.01*inv_a(i)/3.6; %加速时间elseif ua(i)<=u(3)n=ua(i)*(ig(3)*i0/r)/0.377;Tq=-19.313+295.27*(n/1000)-165.44*(n/1000)^2+40.874*(n/1000)^3-3. 8445*(n/1000)^4;Ft=Tq*ig(3)*i0*nT/r;inv_a(i)=(deta(3)*m)/(Ft-Ff-Fw(i));delta(i)=0.01*inv_a(i)/3.6;elseif ua(i)<=u(4)n=ua(i)*(ig(4)*i0/r)/0.377;Tq=-19.313+295.27*(n/1000)-165.44*(n/1000)^2+40.874*(n/1000)^3-3. 8445*(n/1000)^4;Ft=Tq*ig(4)*i0*nT/r;inv_a(i)=(deta(4)*m)/(Ft-Ff-Fw(i));delta(i)=0.01*inv_a(i)/3.6;elsen=ua(i)*(ig(5)*i0/r)/0.377;Tq=-19.313+295.27*(n/1000)-165.44*(n/1000)^2+40.874*(n/1000)^3-3. 8445*(n/1000)^4;Ft=Tq*ig(5)*i0*nT/r;inv_a(i)=(deta(5)*m)/(Ft-Ff-Fw(i));delta(i)=0.01*inv_a(i)/3.6;enda=delta(1:k); %定义矩阵t(i)=sum(a); %求和endplot(t,ua);axis([0 80 0 100]);title('汽车二档原地起步换挡加速时间曲线');xlabel('时间t(s)');ylabel('速度ua(km/h)');[x,y]=ginput(1);disp(x);考虑到该货车的最高车速很难达到100km/h(i0为5.83时不到100km/h)以加速到70公里的时间作为加速时间。
改变i0的值得到不同的加速时间如下表。
i0 5.17 5.43 5.83 6.01 6.17 6.33t(s) 26.2673 26.4516 25.8986 25.5300 25.1613 24.79262.计算六工况百公里油耗。
n=600:1:4000;m=3880;g=9.8;G=m*g; i0=6.01;ig=[5.56 2.769 1.644 1.00 0.793];nT=0.85;r=0.367;f=0.013;CDA=2.77;L=3.2;a=1.947;hg=0.9;If=0.218;Iw1=1.798;Iw2=3.598;n0=[815 1207 1614 2012 2603 3006 3403 3804];B00=[1326.8 1354.7 1284.4 1122.9 1141.0 1051.2 1233.9 1129.7];B10=[-416.46 -303.98 -189.75 -121.59 -98.893 -73.714 -84.478 -45.291];B20=[72.379 36.657 14.524 7.0035 4.4763 2.8593 2.9788 0.71113];B30=[-5.8629 -2.0553 -0.51184 -0.18517 -0.091077 -0.05138 -0.047449 -0.00075215];B40=[0.17768 0.043072 0.0068164 0.0018555 0.00068906 0.00035032 0.00028230 -0.000038568];B0=spline(n0,B00,n); B1=spline(n0,B10,n);B2=spline(n0,B20,n); B3=spline(n0,B30,n);B4=spline(n0,B40,n);Ff=G*f;ua5=0.377*r*n/ig(5)/i0;Fz5=Ff+CDA*(ua5.^2)/21.15;Pe5=Fz5.*ua5./(nT*3.6*1000);for i=1:1:3401b5(i)=B0(i)+B1(i)*Pe5(i)+B2(i)*Pe5(i).^2+B3(i)*Pe5(i).^3+B4(i)*Pe 5(i).^4;endpg=6.86;Qt5=Pe5.*b5/(367*pg);plot(ua5,Qt5);hold on;axis([0 100 0 15]);title('油耗曲线'); xlabel('ua(km/h)');ylabel('单位时间油耗ml/s');for i=20:1:50y(i)= interp1(ua5,Qt5,i,'cubic') %插值(立方)不同速度下单位时间油耗enddt1=16.7/15; %每加速一公里时间dt2=14/10;y1=[ y(26) y(27) y(28) y(29) y(30) y(31) y(32) y(33) y(34) y(35) y(36) y(37) y(38) y(39)]y2=[y(41) y(42) y(43) y(44) y(45) y(46) y(47) y(48) y(49)]qd=19.3*0.299; %怠速油耗qj1=0.5*(y(25)+y(40))*dt1+sum(y1,2)*dt1;qj2=0.5*(y(40)+y(50))*dt2+sum(y2,2)*dt2; %加速段油耗qy=y(25)*7.2+y(40)*22.5+y(50)*18; %匀速段油耗qz1=(qd+qj1+qj2+qy)*100/1.075 %总油耗,1.075为六工况下的行驶距离.改变i0的值(取六个不同的值)分别求得各自百公里油耗如下表。
i0 5.17 5.43 5.83 6.01 6.17 6.33Q(L)10.439L 10.615L 10.89L 11.013L 11.122L 11.232L3.绘制燃油经济性-加速时间曲线。
q=[10.439 10.615 10.753 10.89 11.013 11.122 11.232];t=[ 25.8986 25.8986 26.0829 25.8986 25.5300 25.3456 24.7926];plot(q,t,'+r');hold onq1=linspace(q(1),q(6),100);t1=spline(q,t,q1); %三次样条插值plot(q1,t1); %绘制燃油经济性-加速时间曲线title('燃油经济性—加速时间曲线');xlabel('百公里油耗(L/100km)');ylabel('加速时间s');gtext('i0=5.17'),gtext('i0=5.43'),gtext('i0=5.83'),gtext('i0=6.01'),gtext('i0=6.17'),gtext('i0=6.33');4.计算最高车速n=[600:10:4000];Tq=-19.313+295.27*(n/1000)-165.44*(n/1000).^2+40.874*(n/1000).^3-3.8445*(n/1000).^4;%拟合公式m=3880;g=9.8;nmin=600;nmax=4000;G=m*g;ig=[5.56,2.769,1.644,1.00,0.793];nT=0.85;r=0.367;f=0.013;CDA=2.77; i0=5.83;L=3.2;a=1.947;hg=0.9;If=0.218;Iw1=1.798;Iw2=3.598;Ft1=Tq*ig(1)*i0*nT/r;Ft2=Tq*ig(2)*i0*nT/r;Ft3=Tq*ig(3)*i0*nT/r;Ft4=Tq*ig(4)*i0*nT/r;Ft5=Tq*ig(5)*i0*nT/r;ua1=0.377*r*n/ig(1)/i0;ua2=0.377*r*n/ig(2)/i0;ua3=0.377*r*n/ig(3)/i0;ua4=0.377*r*n/ig(4)/i0;ua5=0.377*r*n/ig(5)/i0;ua=[0:5:120];Ff=G*f;Fw=CDA*ua.^2/21.15;Fz=Ff+Fw;plot(ua1,Ft1,ua2,Ft2,ua3,Ft3,ua4,Ft4,ua5,Ft5,ua,Fz);title('驱动力-行驶阻力平衡图');xlabel('ua(km/s)');ylabel('Ft(N)');gtext('Ft1'),gtext('Ft2'),gtext('Ft3'),gtext('Ft4'),gtext('Ft5'),gtext('Ff+Fw');zoom on;[x,y]=ginput(1);zoom off;disp('汽车最高车速=');disp(x);disp('km/h');改变i0的值,求得相应i0下的最高车速(i0为5.17,5.43时最高车速出现在第四档)如下. i0 5.17 5.43 5.83 6.01 6.17 6.33 umax 102.354 101.692 99.074 100.208 101.115 102.0235.绘制i0-umax曲线(求最高车速约束条件下临界i0值)i0=[5.17 5.43 5.83 6.01 6.17 6.33];umax=[102.3535 101.6919 99.0737 100.2079 101.1153 102.0227];plot(i0,umax,'+r');hold oni01=linspace(i0(1),i0(6),100);umax1=spline(i0,umax,i01); %三次样条插值plot(i01,umax1); %axis=[5 6.5 95 105]title('i0-umax曲线');xlabel('i0');ylabel('最高车速km/h');zoom on;[x,y]=ginput(2);zoom off;disp('临界i0=');disp(x);%根据最高车速约束条件,求临界i0值gtext('i0=5.17'),gtext('i0=5.43'),gtext('i0=5.83'),gtext('i0=6.01'),gtext('i0=6.17'),gtext('i0=6.33');临界i0=5.6135 5.9833若以5.17为下限,6.33为上限,则i0的范围为5.17<=i0<=5.6135或5.9833<=i0<=6.33。