烧结机自动称重配料控制方案(优.选)
烧结自动化系统设计 —烧结配料自动控制系统设计 开题报告

河北联合大学轻工学院本科生毕业设计开题报告题目:烧结自动化系统设计——烧结配料自动控制系统设计学部:信息科学与技术部专业:自动化班级:09自动化(3)班姓名:学号:指导教师:2013年 3 月15 日一、选题背景烧结是把粉状物料转变为致密体,是一个传统的工艺过程。
人们很早就利用这个工艺来生产陶瓷、粉末冶金、耐火材料、超高温材料等。
一般来说,粉体经过成型后,通过烧结得到的致密体是一种多晶材料,其显微结构由晶体、玻璃体和气孔组成。
烧结过程直接影响显微结构中的晶粒尺寸、气孔尺寸及晶界形状和分布。
无机材料的性能不仅与材料组成(化学组成与矿物组成)有关,还与材料的显微结构有密切的关系。
众所周知,烧结厂配料系统是整个烧结生产的源头,它担负着所有烧结机的混合料供应任务,如果配料系统遇到问题,那么整个烧结生产都要被迫停止,而且配料系统的计算也要准确无误,以为烧结原料的种类多,配料成分随其供货渠道的变化而变化,各单配料的配合比例也会根据生产的要求随时变化,而且在生产过程中,物料的黏度、比重、粒度及环境的温度、湿度的变化,也会严重影响下斜的精度,因此,配料系统对于提高烧结矿的质量至关重要。
烧结配料自动控制系统在现在应用十分广泛,是在自动控制仪表方面尤其突出。
在此方面根据烧结工艺需求能将各种矿按照所需量自动投入,由皮带运到混合机中进行下一步工艺的生产。
而近年来,我国的钢铁冶炼行业发展十分迅速,烧结矿是炼铁的主原料,而配料这一工艺是影响烧结质量的重要环节,各称量设备只有达到一定精度才能保证矿的质量。
因此烧结配料自动控制系统是各大型钢铁厂必不可少的,也可大大提高生产效率。
据相关统计,目前我国有烧结机近500台,其中在建和投产的180~660 m2的大中型烧结机有125台,烧结机面积已达近40000平方米。
未来,我国的烧结机将继续推进全流程工艺技术装备的升级换代,西门子提供的全集成过程控制系统SIMATICPCS7,可以帮助钢铁企业在提升产品质量的同时也将进一步降低能源消耗、减少污染物排放。
烧结机自动化控制系统设计

烧结机自动化控制系统设计一、引言烧结机是冶金工业中常用的设备,用于将粉状或颗粒状原料通过加热和冷却过程,使其形成坚固的块状产品。
为了提高烧结机的生产效率和产品质量,设计一个完善的自动化控制系统是非常重要的。
本文将详细介绍烧结机自动化控制系统的设计方案。
二、系统架构烧结机自动化控制系统的架构包括硬件和软件两个部分。
硬件部分主要包括传感器、执行器和控制器等组件,用于感知和控制烧结过程中的各项参数。
软件部分则负责数据处理、控制算法和人机界面等功能。
1. 传感器烧结机自动化控制系统需要使用多种传感器来感知烧结过程中的各项参数,如温度、压力、流量、振动等。
这些传感器应具备高精度、高可靠性和耐高温的特点,以确保测量数据的准确性和稳定性。
2. 执行器执行器用于根据控制系统的指令,控制烧结机各个部件的运行状态。
常见的执行器包括电动阀门、电机、气动装置等。
执行器应具备快速响应、精确控制和可靠性高的特点,以确保烧结过程的稳定性和可控性。
3. 控制器控制器是烧结机自动化控制系统的核心部件,负责对传感器采集到的数据进行处理,并根据预设的控制算法生成控制指令。
常见的控制器包括PLC(可编程逻辑控制器)、DCS(分布式控制系统)等。
控制器应具备高性能、可靠性强和扩展性好的特点,以满足烧结机控制系统的需求。
4. 人机界面人机界面用于实现人机交互,方便操作人员对烧结机自动化控制系统进行监控和控制。
常见的人机界面设备包括触摸屏、计算机等。
人机界面应具备友好的操作界面、实时显示和报警功能,以提高操作人员的工作效率和系统的可靠性。
三、控制策略烧结机自动化控制系统的设计需要制定合理的控制策略,以实现对烧结过程的精确控制和优化调节。
以下是常用的控制策略:1. 温度控制烧结过程中的温度是一个重要的参数,直接影响产品的质量和生产效率。
控制系统应根据预设的温度曲线,通过调节加热和冷却设备的工作状态,实现对烧结过程中温度的精确控制。
2. 压力控制烧结过程中的压力也是一个重要的参数,影响烧结过程的稳定性和产品的物理性质。
烧结配料控制系统及优化

自动控制烧结配料控制系统及优化杨俊生(河钢宣钢检修公司,河北张家口075100)摘要:本文介绍了宣钢360m z烧结机配料控制系统的组成和特B,以及为提高系统稳定性所采取的优化措施。
关键词:配料;PLC;速度;通信Sintering Batching Control System and Its OptimizationYANG Junsheng(Maintenance Company of Hebei Iron Steel Group Xuansteel,Zhangjiakou075100,China)Abstract:The composition and characteristics of the batching control system of360m%Sintering Machine in Xuanhua Iron and Steel Co.,Ltd.and the optimization measures taken to improve the stability of the system were introduced.Key words:batching&PLC;speed;communicationo引言宣钢360m z烧结机控制系统选用法国施耐德Quantum PLC,编程软件和上位机监控软件为Unity pro和IF-IX。
配料控制系统由西门子S7-200PLC和K-TP178micro 触摸屏组成。
投产后,配料系统出现一些问题,影响配料的精度和稳定性,如:通过电位器调节,控制皮带速度转速,造成在校零或标定过程中出现累计偏差,影响称量的精度;采用在秤体尾轮安装编码器的方式采集皮带秤速度,一旦编码器与尾轮的连接器断开或编码器损坏,:接料下料量出现严重偏差;配料系统与主控系统采用硬接线方式连接,量信号容易受到干扰,或断线后该种物料将出现失控现象%1配料控制系统的组成和特点配料皮带秤一料连料计量和量定量控制的设备,由皮带秤体、料斗、称器、微机称组成。
浅议烧结配料自动化控制系统

浅议烧结配料自动化控制系统摘要:本文在对炼铁烧结配料自动化控制系统进行简要阐述基础上,对烧结配料自动化控制系统功能、软硬件配置等进行研究,希望可以为炼铁生产的高效、顺利开展提供帮助。
关键词:烧结机;配料;自动化;控制系统在现代生产生活中,铁制品广泛分布于各个领域,炼铁生产效率是人们普遍关注的问题,烧结作为炼铁中的一个关键环节,烧结配料的效率会对炼铁效率、质量产生极大的影响。
在现代信息技术的迅猛发展下,自动化控制技术变得越来成熟,应用于许多工业生产中,起到了良好的效果,所以,加强对烧结配料自动化控制系统的研究,是有着重要现实意义的。
1.烧结配料自动化控制系统概述在黑色冶金烧结过程中,必须借助烧结机这一设备,完成不同粒度、不同成分的富矿粉、精矿粉烧结,并有效剔除矿石中含有的各种杂志,得到金属含量较高的烧结块。
在常用的烧结机中,规格主要是根据长度、宽度不同来划分的,烧结产量与烧结面积之间成正比关系。
从相关生产实践中可知,在烧结机的生产过程中,人工配料的方式会导致配料精度达不到设计要求烧结的质量、产量以及效率等都会受到一定影响,降低了冶炼工作的水平,也减少了冶炼厂的经济效益[1]。
图1:烧结配料自动化控制系统闭环管理示意图对此,在烧结配料中,采取自动化控制系统,将配料操作、配料量等都由计算机、相应软件系统来进行自动化、智能化控制,可以有效减少人为操作的失误,根据对烧结机运行情况的监测以及相关运行经验指标,完成烧结运行数据的采集与分析工作,来自动对下料、频率进行调节,达到提升烧结配料精度的效果,促进烧结效率的大幅度提升。
烧结配料自动化控制系统是一个闭关环管理的过程,烧结生产会产生各种生产数据,同时,配料的控制、生产产品的化验分析都会产生相应的配料数据、分析结果,将这些数据汇总,通过对数据的对比分析,根据一定原则来建立起配料模型,通过计算机运算来确定最佳的配料方案,作用于烧结生产,具体如图1所示。
此外,在烧结配料自动化控制系统中,画面共享也是其具备的基本功能之一,通过各种通讯设备的应用,可以实现烧结主控室、配料生产车间等的相关画面的实时共享,为工作人监督配料过程提供极大帮助,对确保烧结配料的安全、科学,是有极大帮助的。
烧结自动配料控制系统的原理与应用

烧结自动配料控制系统的原理与应用2009-8-17 14:55:00济南钢铁总公司自动化部刘辉刘青凤供稿摘要:本文介绍了烧结配料系统的结构和原理,以及应用中出现的问题和解决方法。
关键词:自动配料、自动控制Abstract: This paper introduces working principle,and configuration of system,and how t o solve the problems in applications.Key words: Automatic proportioning、Automatic control前言众所周知,烧结厂配料系统是整个烧结生产的源头,它担负着所有烧结机的混合料供应任务,如果配料系统遇到问题,那么整个烧结生产都要被迫停止,而且配料系统的计算也要准确无误,因为烧结原料的种类多,配料成分随供货渠道的变化而变化,各单配料的配合比例也会根据生产的要求随时变化,而且在生产过程中,物料的黏度、比重、粒度及环境的温度、湿度的变化,也会严重影响下料的精度,因此,配料系统对于提高烧结矿的质量至关重要。
一、配料系统的工作原理1、配料原理在冶金行业中,烧结矿成分稳定在炼铁工艺中起着非常重要的作用。
其配比的准确性直接关系到烧结矿和炼铁的质量。
在传统的烧结配料生产线上,主要依靠工人的“跑盘”抽样检查原料的配比,再进行控制,这样不仅速度慢、调节不及时, 而且准确性差。
引入计算机控制以后,提高了控制速度和配比的准确性,减轻了工人劳动强度,稳定了烧结矿的化学成分。
在烧结配料生产线上,变频器控制圆盘的转速,从而调节下料速度,原料经阀门落到称重皮带上,再落到总皮带上,各料仓的原料按比例在总皮带上混合后,送混料系统。
圆盘下料量由称重传感器测量,信号为4~20mA,直接送Quantum的模拟量输入模块上,经控制器运算得到瞬时下料量和累计下料量,下料量给定与实际料流量经过PLC的PID控制器运算后,通过PLC输出4~20 mA的信号给变频器上,形成闭环控制,从而使下料量精确。
烧结机配料自动控制系统
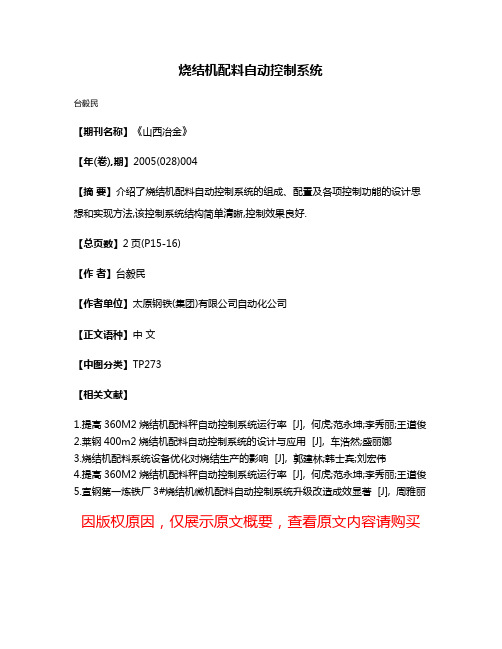
烧结机配料自动控制系统
台毅民
【期刊名称】《山西冶金》
【年(卷),期】2005(028)004
【摘要】介绍了烧结机配料自动控制系统的组成、配置及各项控制功能的设计思想和实现方法,该控制系统结构简单清晰,控制效果良好.
【总页数】2页(P15-16)
【作者】台毅民
【作者单位】太原钢铁(集团)有限公司自动化公司
【正文语种】中文
【中图分类】TP273
【相关文献】
1.提高360M2烧结机配料秤自动控制系统运行率 [J], 何虎;范永坤;李秀丽;王道俊
2.莱钢400m2烧结机配料自动控制系统的设计与应用 [J], 车浩然;盛丽娜
3.烧结机配料系统设备优化对烧结生产的影响 [J], 郭建林;韩士宾;刘宏伟
4.提高360M2烧结机配料秤自动控制系统运行率 [J], 何虎;范永坤;李秀丽;王道俊
5.宣钢第一炼铁厂3#烧结机微机配料自动控制系统升级改造成效显著 [J], 周雅丽因版权原因,仅展示原文概要,查看原文内容请购买。
烧结机配料秤改造

烧结机配料秤改造郑丹君① 王宏 张军(宁波钢铁有限公司炼铁厂 浙江宁波315807)摘 要 为了维持烧结作业区烧结机配料秤配料精度。
逐一排查了配料秤如皮带跑偏、托辊积料、皮带积料等故障,并对皮带称进行一系列改良改造。
结果表明,改造后,秤的精度误差达到了允许范围之内,降低了故障率,满足了生产工艺的需求,保证了烧结矿的质量。
关键词 烧结 配料秤 误差 精度中图法分类号 TG8 TF325.1 文献标识码 BDoi:10 3969/j issn 1001-1269 2023 06 024ImprovingofthePrecisionofBatchingScaleofSinteringMachineZhengDanjun WangHong ZhangJun(NingboIron&SteelCo.,Ltd.,Ningbo315807)ABSTRACT Inordertomaintainthebatchingaccuracyofthesinteringmachinebatchingscaleinthesinteringoperationarea.Thefaultsofthebatchingscalessuchasbeltmistracking,idleraccumulation,beltaccumulation,etc.werecheckedonebyone,andaseriesofimprovementsandtransformationswerecarriedoutonthebeltscale.Theresultsshowthatafterthetransformation,theaccuracyerrorofthescalereachestheallowablerange,whichreducesthefailurerate,meetstheneedsoftheproductionprocess,andensuresthequalityofthesinter.KEYWORDS Sintering Batchingscale Error Precision1 前言宁波钢铁有限公司1#烧结机设计430m2,年产烧结矿443万t/a,于2006年6月投产。
智能烧结配料控制系统使用说明

智能烧结配料控制系统使用说明
一、安全操作规则
1、操作前,应查看安全情况,确保设备正常运行;
2、熔炼过程中,严禁将非工作人员接近熔炼器,以免发生意外;
3、严禁进行自行调整,如有特殊情况,应提前请示技术人员;
4、系统使用时应提前检查电源、控制系统等,以确保安全运行;
5、遇出现异常情况,应处理后才可继续操作;
6、在使用前,应查看操作说明书等,确保操作人员了解性器的正确使用方法;
7、熔炼时,应确保室内空气清洁,以免影响配料质量;
8、应定期清理熔炼现场,保持设备内部洁净整洁;
9、应清除现场的易燃物,以免发生火灾事故;
10、操作结束后,应关闭电源,以保护设备不受损失;
二、操作指南
1、检查熔炼器的运行情况,确保其正常运行;
2、温度控制:根据不同物料,控制熔炼器的温度,以保证物料的质量;
3、配料控制:调节配料机构,将原料按照一定比例投料;
4、配料时间:根据熔炼物料的熔炼温度,控制投料结束的时间;
5、烧结工艺控制:控制熔炼过程的时间和温度,完成烧结工艺;
6、水控制:检测水的质量,确保水的净化;
7、熔炼氧气控制:依据不同物料。
- 1、下载文档前请自行甄别文档内容的完整性,平台不提供额外的编辑、内容补充、找答案等附加服务。
- 2、"仅部分预览"的文档,不可在线预览部分如存在完整性等问题,可反馈申请退款(可完整预览的文档不适用该条件!)。
- 3、如文档侵犯您的权益,请联系客服反馈,我们会尽快为您处理(人工客服工作时间:9:00-18:30)。
烧结机自动称重配料控制方案一)控制方案及系统组成近年来,国内新建烧结机的配料方法均采用重量配料法,重量配料就是按原料的重量来配料,采用电子皮带秤对物料进行连续计量,通过调节圆盘给料机或皮带的速度来实现定量给料,重量配料易实现自动配料,配料精度较高。
烧结机的配料采用13个定量圆盘给料机和电子皮带秤定量给料,为提高皮带配料秤的计量精度和配料系统给料精度,所有给料机的皮带配料秤均采用变频调速的方式进行控制。
该自动称重配料控制由下列五大部分:电子皮带称、称重控制仪表、变频控制柜、监控计算机及现场操作箱部分。
配料自动控制实现烧结用的原料如混匀矿、燃料、熔剂白云石、生石灰、冷返矿按照工艺要求的配比进行自动给料,能够判断下料堵料和失控故障、变频器故障,并报警。
二)系统的工作方式系统检修和工作方式有二种:手动检修方式:即通过现场操作箱选择开关及按钮控制变频器以点动频率驱动电动机正反向运行速度;工作方式有二种第一种是仪表自动给料;即通过称重控制仪表键盘,任意给定所需给料量,并通过给料量大小变化自动调整变频器频率(电动机的运行速度);第二种是上位机自动给料,给料设定就可由上位机画面来完成。
正常工作在上位机自动给料,受计算机控制。
检修或调试时在“检修”状态,可以单机运行。
三)系统各部分功能3.1. 称重皮带秤及控制仪表功能流量恒定的控制原理要确保烧结配料成分的稳定,圆盘给料机和螺旋的流量控制是关键。
通过圆盘给料机和料仓给料器与集料皮带机之间安装调试好的电子配料皮带秤称量检测,以及配料皮带测速编码器(传感器)测量皮带运输原料速度的检测,称重仪表采集测量皮带秤上每单位长度的载荷值q(kg/m)以及皮带在同一时刻的运行速度v(m/s),且两者相乘得到物料的瞬时流量q·v(kg/s)。
只要保证q(t)·V(t)的乘积不变,就可以保证物料流量的恒定。
即随皮带上物料重量的变化控制皮带运行速度做出相应的调整,就可以保证物料流量的恒定。
在本系统中圆盘给料机的速度是恒定不可调的,所以控制流量的恒定只能调节皮带上物料重量,而重量的改变又只能通过改变变频器的频率,以改变皮带秤的速度。
流量恒定控制原理图2所示,每一个称重控制都是一个“小闭环”控制系统。
称重仪表检测并运算q(t)·V(t)的乘积与流量设定值(上位机给定或仪表键盘给定)进行比较,然后进行PID运算,,得出相应的输出频率信号到变频器,实现自动控制流量大小的要求。
1.实现流量恒定的控制仪表控制部分采用模块控制方式,电子秤与仪表控制模块之间的信号传输采用差分频率信号传输技术,具有极强的抗干扰能力和远传能力,从而保证了系统信道的可靠性和准确性,在反馈控制上采用新型的人工智能PID调节算法,无振荡,无超调。
2.仪表控制部分与监控计算机采用CAN总线通信方式,信号传输的快速实时性更高、抗干扰更强、可靠性更高,保证配料精度和稳定性。
3.配料秤有补偿功能,即皮带本身影响自动补偿功能。
能在配料秤正常生产运行过程中,连续不断地测量皮带本身实际重量的变化(如物料局部粘结等造成的皮带皮重的变化,天长日久磨损程度不同导致的皮带薄厚不均,以及张力不匀等所产生的对称重传感器的外部影响),并随时进行精确补偿,因而其动态测量精度要比一般设备厂家的配料秤动态测量精度高。
3.2计算机监控部分该计算机采用品牌机作为控制计算机, 系统软件是在Win2000操作平台下,用组态王(或VB6·0)开发研制的通用应用程序,整个程序兼顾鼠标和键盘操作。
各种操作界面、数据显示及打印管理,用户可方便进行各种数据的修改操作,运行数据的图形显示及打印各种报表。
工艺流程动画显示美观大方,友好的操作界面,简单易学,其功能如下:1.显示功能1)该系统能显示整个配料工艺及流程画面;2)显示各设备瞬时运行情况;3) 显示各台秤的给定流量、实际流量、下料累计量,显示各种原料的瞬间下料量、总流量及总累计量。
4)具有系统报警功能。
2操作及控制功能该系统利用操作提示菜单方便、简单,快速引导进行系统操作。
其功能如下:1)能实现变频器的远程操作(启停、手自动转换、单动);2)能快速修改各台电子秤的计量参数及换仓后各物料吸收系数的变更设置;3)修改配料系统的控制参数;4)根据工艺要求,可随时、方便的选定、修改、更换配比和配料总流量;5)当物料水分含量发生变化时,可方便的变更水分组和手动输入各物料的水分变化量。
6)根据现场实际需要,可对打印时间间隔、报警时间进行设置;3报表及打印功能1)按设置的打印参数方便的打印出各种原料累计消耗量的班报、日报、月报表并能进行相应的查询;2)具有当前趋势和历史趋势的查询功能;3)具有各料仓手动配料时间和配料量的统计功能。
4报警功能1)当系统各测量单元出现故障时,工艺流程主画面将以警示色提醒用户,按下相关键后,可由CRT显示故障代码;2)当系统出现空仓或园盘给料机堵料而无法下料时,工艺流程画面报警提醒用户及时处理。
3. 3变频控制部分皮带电机采用流量闭环变频调速方式,保证配料精度和稳定性,节电效果显著。
将每台变频器集中在变频电控制柜中。
正常工作时,称重仪表PID的输出控制变频器的输出频率,检修调试时,按钮点动控制变频器的输出频率。
3.4 现场操作箱调试或现场检修时,通过现场操作箱实现单机的正反运行。
四)配料设定值调整方案1、总流量调整、各配比不变:修改各料仓设定流量(采用双缓冲,保证前次设定流量不变),在顺起顺停模式下,延时投入(保证新流量在料头的比例);在同起同停模式下,同步投入。
2、总流量不变、各配比调整:1)停料重新启动:延时停料,修正皮重(保证本次配料全部到大批带),得到新配比后重新启动。
2)在线修改配比:得到新配比后送双缓冲区,启动同步计时,到启动时刻按新配比控制。
五)更换料仓及报警处理1、停料更换:延时停料,修正皮重。
按新料仓启动。
2、在线更换:通知其他料仓,减小流量,等待新料仓启动。
按新料仓启动。
3、故障报警:堵料(失控、皮带打滑)、卡料,通知其他料仓,减小流量,等待故障解除,若超时,则延时停料,修正皮重。
如果故障料仓有同种料仓同时下料,当超时可使另一料仓加倍下料。
六)启停模式1、同启同停:以皮带秤上料的比例为准。
2、顺启顺停:以大皮带上料头的比例为准。
七)控制功能和算法设计配料自动控制实现的功能是将烧结用的原料如混匀矿、燃料、熔剂(白云石、生石灰)、冷返矿按照一定配比进行自动给料。
具体功能有配比合理性检查、湿配比的计算和调整、排料量设定值的计算处理、配料秤的工作状态选择处理、控制方式的选择(计算机自动控制和远程手动)、自动换仓的处理等。
1、配料矿槽料位管理l)根据料位计掌握配料槽的料位根据称重式料位计的料重信号(单位;t),对1#~6#混匀矿槽、7#一8#燃料槽、9#~11#熔剂槽、12热14#冷返矿槽、15价16#生石灰槽的料位进行监视。
各贮矿槽的料位(料位%或重量值)可在操作站上进行显示。
(l)上述的重量值都是含有水份的值;(2)料位(%)为料位重量值百分比;(3)槽变更、空槽判断处理、料位报警判断处理及水分率变更等均在操作站上进行相应处理。
2)配料槽料位报警处理在操作站上显示配料槽库存量(原料重量,单位:t),以及配料槽的料位(单位:%),并进行配料槽料位越限报警。
各个矿槽的料位上上限(90%)、上限(80%)、下限(30%)、下下限(20%)报警信号在操作站上以颜色区分显示,其中上上限、下下限报警信号还需送电控联锁。
3)配料槽空槽判断对配料槽作空槽判断,当料位值达到下下限(LL)时将其作为空槽信号送至电气,作为槽变更判断条件之一。
2、配料系统的自动控制烧结用的新原料有混匀矿、熔剂、生石灰等,将这些新原料和冷返矿、燃料按照所要求的配比进行自动给料的过程称为配料系统的自动控制。
操作人员在画面上输入“设定干配比”,设定干配比使用前必须进行人工确认,再通过合理性检查得到“采用干配比”后才能进行湿配比的计算。
根据采用干配比和采用水分率经计算求出各种原料的湿配比,再根据混合料槽料位之需要,确定总的配料量,求出每台配料秤排料量的设定值。
由于贮矿槽空间位置的不同,则设定值必须经过延时处理,使各种原料的实际干配比在总配料量发生变化或槽变更时保持一致。
配料系统的各种计算、延迟设定及跟踪等功能由PLC完成;配料秤二次仪表对排料量设定值和测量值进行PI运算,并将控制输出信号通过通讯方式送给变频器完成闭环控制。
其控制算法15“,]设计如图4一2所示,其中m,c,;为原料干配比,h为原料水分率,砰乍忿为综合输送量,t为延迟时间,Di为配料设备运行状态。
图7一2配料控制算法设计图l)干配比合理性检查所谓干配比,就是按照烧结矿的化学成份以及高炉对烧结矿的要求,经计算求出的各种原料之间的配合比例(干量)。
在干配比设定后要进行如下干配比合理性检查:(l)新原料千配比之和要为100%;(2)单种物料干配比大于等于零;(3)读入配料槽选槽状态。
对槽选择状态信号进行判断,有配比设定的槽必须在选择中;无配比设定的槽应不被选择。
不符合上述条件时,作出报警提示;干配比分配时,根据有配比设定的槽数,其干配比分配为按类均分,无配比设定的槽作备用矿槽。
2)配合比计算总配合比包括新原料配合比,燃料配合比,返矿配合比,总配合比共计100%。
新原料包括混匀矿、熔剂(石灰石、白云石)、生石灰,新原料各成分比例合计100%。
燃料和返矿采用外配方式进行计算。
式中:mi一新原料的配合比(干量);ci一一燃料的配合比(干量);ri一返矿的配合比(干量);Mi—新原料的排料量(湿量);Ci--一一燃料的排料量(湿量);Ri一返矿的排料量(湿量);hi一原料的水分率;i一配料矿槽编号(其中i=1~6时,j=1,k= 6;i=9~11时,j=9,k=11;I=15~16时,j=l5,k=16),编号对应的矿槽如下:1~6:混匀矿槽;7~8:燃料矿槽;9~11:熔剂矿槽;12~14:返矿槽;15~16:生石灰槽.所谓湿配比,即各种原料(湿量)的给料量对于总给料量(湿量)之间的比例系数,称之为湿配比。
湿配比计算的条件:(l)干配比变更时计算:由于原料成份等各种原因引起人为变更干配比,要重新计算湿配比;(2)水分率变更时计算:根据实际生产情况人工变更水分率时,则湿料排料量有变化,需重新计算湿配比。
3)排料量设定值计算处理根据前面己求出的湿配比,可计算出每个矿槽排料量的设定值:Wsi=Wts xHki式中:Wsi:i贮矿槽排料量设定值Wts:综合输送量Hki:i贮矿槽湿配比,其中i为贮矿槽编号1一16其中综合输送量(升介‘)是根据混合料槽料位控制功能计算得到或由操作工根据实际生产情况人工设定的。