烧结机自动称重配料控制方案
配料称重自动控制系统怎样操作

配料称重自动控制系统操作指南1. 系统概述配料称重自动控制系统是一种用于自动化控制配料称重的设备,主要应用于生产线上的配料工序。
该系统能够精确称量不同重量的配料,提高生产效率和质量控制,并减少人力成本和配料误差。
2. 系统组成配料称重自动控制系统由以下几个主要组成部分构成:2.1 称重传感器称重传感器是系统中起主要作用的部分。
它通过测量物料重量并输出电信号来实现准确的配料称重。
在安装和使用称重传感器时,需要遵循以下步骤:•确保称重传感器固定在平稳、牢固的支撑结构上,以避免重量分布不均导致测量错误。
•检查传感器的电源连接和信号连接是否正常,确保传感器能够正常工作。
•对于不同类型的传感器,需要按照相应的规范进行校准和调试,以确保称重准确度。
2.2 控制器控制器是系统的核心部分,用于接收传感器的信号并进行相应的控制操作。
控制器通常由一个微处理器和一些逻辑电路组成。
在操作控制器时,需要按照以下步骤进行操作:•打开控制器电源,确保电源供应正常。
•连接称重传感器和控制器,确保信号传输无误。
•设置控制器的工作参数,如配料重量范围、传感器灵敏度等。
•按下启动按钮,控制器将开始接收传感器信号并进行相应的控制操作。
2.3 操作界面操作界面是用户与系统进行交互的通道,通常由触摸屏或键盘等设备组成。
在操作界面上,用户可以进行以下操作:•输入配料的目标重量,控制器将根据用户的输入进行相应的控制操作。
•监控系统的工作状态,包括当前称重重量、运行时间等。
•进行系统的设置和参数调整,如称重单位、显示方式等。
3. 操作步骤下面是配料称重自动控制系统的一般操作步骤:3.1 系统启动•打开控制器电源,并确保称重传感器和操作界面正常连接。
•检查控制器和传感器的工作状态,确保系统准备就绪。
•启动系统,进入操作界面。
3.2 配料准备•根据生产需要,准备需要配料的容器和物料。
•将容器放置在配料区域,确保容器固定不动。
•打开配料区域的门,准备进行配料操作。
烧结机自动化控制系统设计

1 概述烧结生产过程是把粉矿加入一定比例的熔剂,燃料经过混合后,在一定温度下烧结成高炉需要的原料。
主要生产工艺包括燃料破碎系统、配料室供料系统、混料系统、烧结冷却系统、成品整粒系统、成品矿仓储等。
烧结工艺是一个连续性的生产过程,环节多,控制对象复杂、滞后时间长且受干扰影响大,为了保证烧结矿品质稳定,提高产量和降低燃料消耗,必须对生产过程进行自动化控制。
2 系统设计2.1 PLC控制系统设计根据烧结工艺过程对自动控制系统的要求设计的自动化系统为基础自动化,按“三电一体化”的原则考虑。
上位监控系统由六台工控机组成,现场控制站由四套QUANTUM PLC组成,分别完成对燃料破碎系统、配料系统、烧结冷却系统、成品系统的监视和控制。
图1 系统网络配置图烧结机网络化控制系统采用与QUANTUM PLC相配套的Concept 2.6编程软件实现硬件组态配置与程序编制;采用Montor PRO 7.2监控软件完成数据库与监控画面的开发。
通讯网络采用工业以太网,通讯协议为TCP/IP。
系统网络配置图1所示。
2.2 系统功能(1)设备的联锁控制根据烧结工艺要求,烧结燃料破碎系统、配料系统、烧结冷却系统、成品系统等整条生产料线的控制方式分为:自动控制、集中手动控制、机旁手动控制。
控制方式的选择设在集中操作室内的主操作台上或通过机旁箱选择。
(2)重点参数调节?按配比关系自动配料,保证碱度需求配料的目的是将烧结矿的品位、含碳量和碱度控制在指定的范围内。
本工程配料系统由宽带给料机、配料秤;螺旋给料机、螺旋给料秤组成。
PLC对参与烧结的各种含铁原料、溶剂和燃料根据高炉冶炼的要求进行精确的配料计算,对下料量和配比系数进行设定,通过给料机变频实时调节各配料下料量,以保证烧结矿的含铁量、CaO含量、碱度、MgO、Al2O3及含硫量等主要成分控制在规定范围内。
配料量由上位机统一设定,可进行采集和处理各配料控制回路来的称量信号与开关量状态,实现整个系统的给料、称量检测、料量调节,选择和切换料仓等配料过程的自动控制。
烧结机自动化控制系统设计

烧结机自动化控制系统设计引言概述烧结机是冶金行业中常用的设备,用于将粉状原料烧结成块状物料。
为了提高生产效率和质量,烧结机需要配备自动化控制系统。
本文将探讨烧结机自动化控制系统的设计原则和关键技术。
一、系统架构设计1.1 控制层烧结机自动化控制系统的控制层应包括PLC(可编程逻辑控制器)、DCS(分散控制系统)等控制设备。
PLC负责实时控制烧结机的运行状态,而DCS则用于监控和管理整个生产过程。
1.2 通信网络为了实现设备之间的信息交换和数据传输,烧结机自动化控制系统需要建立可靠的通信网络。
常见的通信网络包括以太网、Modbus、Profibus等。
1.3 数据采集为了实时监测烧结机的运行状态和生产数据,控制系统需要配置数据采集设备,如传感器、仪表等。
这些设备可以将数据传输到控制层,供系统进行分析和决策。
二、控制策略设计2.1 自动调节烧结机自动化控制系统应具备自动调节功能,能够根据生产需求和设备状态自动调整工艺参数,实现最佳生产效率和质量。
2.2 报警系统为了确保生产安全和设备正常运行,控制系统应配置完善的报警系统,能够及时发现并处理异常情况,避免事故发生。
2.3 联锁保护为了防止设备运行时出现不安全状态,控制系统应设计合理的联锁保护策略,确保设备在安全范围内运行。
三、人机界面设计3.1 触摸屏界面为了方便操作人员对烧结机进行监控和控制,控制系统应配置直观友好的触摸屏界面,显示设备运行状态、参数设置等信息。
3.2 远程监控为了方便管理人员对生产过程进行监控,控制系统应支持远程监控功能,可以通过互联网实现对烧结机的远程监控和控制。
3.3 报表分析为了方便管理人员对生产数据进行分析和统计,控制系统应支持报表生成功能,能够输出各种生产数据报表,帮助管理人员做出决策。
四、故障诊断与维护4.1 自诊断功能为了提高设备的可靠性和稳定性,控制系统应具备自诊断功能,能够自动检测设备故障并给出修复建议。
4.2 远程维护为了提高设备的维护效率,控制系统应支持远程维护功能,可以通过互联网实现对设备的远程诊断和维护。
配料称重自动控制系统流程
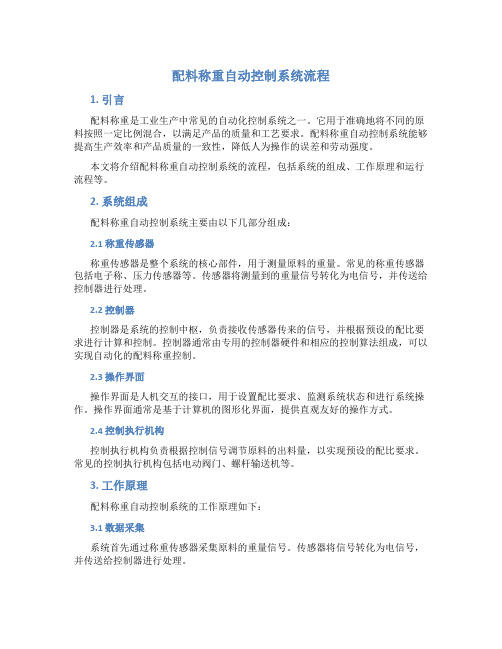
配料称重自动控制系统流程1. 引言配料称重是工业生产中常见的自动化控制系统之一。
它用于准确地将不同的原料按照一定比例混合,以满足产品的质量和工艺要求。
配料称重自动控制系统能够提高生产效率和产品质量的一致性,降低人为操作的误差和劳动强度。
本文将介绍配料称重自动控制系统的流程,包括系统的组成、工作原理和运行流程等。
2. 系统组成配料称重自动控制系统主要由以下几部分组成:2.1 称重传感器称重传感器是整个系统的核心部件,用于测量原料的重量。
常见的称重传感器包括电子称、压力传感器等。
传感器将测量到的重量信号转化为电信号,并传送给控制器进行处理。
2.2 控制器控制器是系统的控制中枢,负责接收传感器传来的信号,并根据预设的配比要求进行计算和控制。
控制器通常由专用的控制器硬件和相应的控制算法组成,可以实现自动化的配料称重控制。
2.3 操作界面操作界面是人机交互的接口,用于设置配比要求、监测系统状态和进行系统操作。
操作界面通常是基于计算机的图形化界面,提供直观友好的操作方式。
2.4 控制执行机构控制执行机构负责根据控制信号调节原料的出料量,以实现预设的配比要求。
常见的控制执行机构包括电动阀门、螺杆输送机等。
3. 工作原理配料称重自动控制系统的工作原理如下:3.1 数据采集系统首先通过称重传感器采集原料的重量信号。
传感器将信号转化为电信号,并传送给控制器进行处理。
3.2 配比计算控制器根据预设的配比要求,对不同原料的重量信号进行计算和比较。
根据计算结果,控制器生成相应的控制信号。
3.3 控制执行控制信号被传送到控制执行机构,控制执行机构根据信号的大小调节原料的出料量。
控制执行机构可以调节电动阀门的开关状态或螺杆输送机的转速等。
3.4 过程监控与反馈在控制执行的过程中,系统会不断地采集和监测原料的重量变化。
控制器通过与预设的控制策略进行比较和分析,判断系统的工作状态是否正常。
如果系统发生异常,控制器会及时发出报警信号,提醒操作员进行处理。
烧结机自动化控制系统设计

烧结机自动化控制系统设计一、引言烧结机是冶金行业中常用的设备之一,用于将粉状的矿石或粉末材料高温烧结成块状物。
传统的烧结机操作需要大量的人工干预,效率低下且存在安全隐患。
为了提高生产效率、降低人工成本并确保操作安全,烧结机自动化控制系统应运而生。
二、系统概述烧结机自动化控制系统是基于现代控制理论和技术,利用计算机、传感器、执行机构等设备构建的一套自动化控制系统。
通过对烧结机的各个参数进行实时监测和控制,实现烧结过程的自动化和智能化。
三、系统功能1. 参数监测与数据采集:通过传感器对烧结机的温度、压力、流量等参数进行实时监测,并将数据采集到控制系统中,用于后续的控制和分析。
2. 过程控制与调节:根据设定的烧结工艺要求,控制系统能够自动调节燃料供给、风量、进料速度等参数,以实现烧结过程的稳定和优化。
3. 报警与故障诊断:控制系统能够根据设定的阈值,及时发出报警信号并采取相应的措施,以避免因异常情况导致的事故发生。
同时,系统还能对故障进行自动诊断和定位,提供相应的故障处理建议。
4. 数据分析与报表生成:控制系统能够对烧结过程中采集到的数据进行分析和统计,并生成相应的报表,为生产管理和决策提供参考依据。
四、系统组成1. 传感器:用于对烧结机各个参数进行实时监测,常见的传感器包括温度传感器、压力传感器、流量传感器等。
2. 执行机构:用于实现对烧结机各个操作参数的自动调节,如燃料供给系统、风量调节系统等。
3. 控制器:负责控制系统的运行和参数调节,常见的控制器有PLC(可编程逻辑控制器)和DCS(分布式控制系统)。
4. 人机界面:提供给操作人员与控制系统进行交互的界面,常见的人机界面有触摸屏、监控软件等。
5. 数据存储与处理系统:用于存储和处理烧结过程中采集到的数据,常见的系统有数据库、数据分析软件等。
五、系统设计1. 硬件设计:根据烧结机的实际情况和工艺要求,选择合适的传感器、执行机构和控制器,并进行布置和连接。
称重仪表在烧结配料系统中的应用与调试

称重仪表在烧结配料系统中的应用与调试中国一冶机电公司自动化部张志高[内容摘要]配料系统中各种原料的配比与混合是影响烧结矿质量的重要环节,而称量仪表的合理使用及精度调校对烧结矿质量起着至关重要的作用.本文以天津钢管公司还原铁厂105m2烧结机配料系统为例对称量仪表控制原理与调试作一分析和总结。
[关键词]标定系数标定P ID设置流量设定频率设定流量反馈1、概述在烧结工程中,上料、破碎、配料、混合、烧结、筛选构成了整个烧结系统的工艺流程,其中配料系统中各种原料的配比与混合是影响烧结矿质量的重要环节,而称量仪表的合理使用及精度调校对烧结矿质量又起着至关重要的作用.本文以天津钢管公司还原铁厂105m2烧结机配料系统为例对称量仪表控制原理与调试作一分析和总结。
2、称量系统控制原理2.1过程控制原理在天津钢管公司还原铁厂105m2烧结机配料系统中,称量装置采用皮带秤,共14个料仓,各仓所储存物料并不完全相同。
在每一个料仓下有一套变频控制的宽带给料机,物料经过宽带流向皮带秤,再由混合皮带传送至混合机(如图2所示)。
每台秤有两个并接于接线盒的称重传感器和一个速度传感器,各信号经过接线盒传输到称重积算仪,再由积算仪将模拟信号和脉冲信号传送给P LC,P LC经过模数转换后将信号传送至工控机,通过工控机监控画面对其进行监控操作,P LC将工控机下达的指令传给积算仪进行处理。
控制操作是P LC通过对变频器的给定来控制宽带给料机的速度,从而控制通过皮带秤的料流量,其过程控制原理如图1所示:图12.2称重仪表的工作原理及调校该皮带秤下面有三个支撑点(如图2中A、B、C),其中A、B为两个称重传感器,两个传感器电源和信号线并联于接线盒中,采用两个并联可起到信号补偿作用。
秤体共有三个支撑点承载皮带上物料重量。
①工作原理的数学模型及分析:皮带运输机输送料是一连续动态的过程,在某段时间(t 0~t 1)内,其输送的物料量就是瞬时重量对速度的积分,可以用下式表示:dt t v t p Q tt )()(10*⎰=式中:Q —t 0~t 1时间内的物料通过量P(t)—称重段上物料重量随时间变化的函数V(T)—皮带运行速度随时间变化的函数T 0—开始称量时刻T 1 —终止称量时刻由于速度函数V(t)等于距离对时间的微分,即:dt ds t V /)(=或ds dt t V =*)( 所以Q 的表达式又可写成:ds s p Q s s )(10⎰=式中:P(s )—称量段上物料重量随皮带运行距离变化的函数S 0—开始称量时皮带的位置S1—终止称量时皮带的位置d s —皮带运动的距离微变量当d s 取得足够小时,Q 值就能精确反映出S 0~ S 1这段皮带上物料的重量,由于采用高精度电阻应变片式荷重传感器来检测P (s),用光电式速度传感器来检测ds 。
智能称量系统与死区PID控制在烧结配料中的应用

刘 娜 ( 东工业职 业 学 院电 气工程 系, 东 淄博 2 6 1 ) 山 山 5 4 4
崔 志 武 ( 山东工业职业学院实训处, 山东 淄博 2 6 1 ) 5 4 4
摘 要
烧 结 生 产 实践 证 明 , 结 配 料 发 生 偏 差 是 影 响 烧 结 过 程 正 常 进 行 和 烧 结 矿 产 质 量 的 重要 因素 。 因此 , 确 配 料 是 十 分 烧 精 重 要 的 。 针 对 实际 需要 , 智 能 称 量 系统 与 带 死 区 PD控 制 算 法 应 用 于 对 烧 结 配料 系统 的控 制 中 , 详 细介 绍 烧 结 配 料 系 将 I 并 统 运 用 智 能 称 量 系统 与 带 死 区 PD控 制 算 法来 实现 精 确 配 料 的 控 制 过 程 。 实践 证 明 ,该技 术 的 应 用取 得 了很 好 的控 制 效 I
动 02 , 使 烧 结 矿 的 强 度 和 还 原 性 受 到 影 响 , 结 矿 的 含 铁 .% 会 烧 量 和 碱 度 波 动就 会 影 响高 炉 炉 温 和 造 渣 制 度 , 重 时 , 引 发 高 严 会
炉 悬 料 、 料 现 象 。 文 着 重介 绍烧 结 配料 系统 运 用 智 能称 量 系 崩 本 统 与带 死 区 PD 控 制 算 法 来 实 现 精 确 配 料 的 控制 过程 。 I 1 系统 控 制 概 述 烧 结 配 料 控 制 以 智 能 称 量 系 统 的物 料 流 量 检 测 为 基 础 。 将
《 业 控 制计 算机 》0 0年 第 2 工 21 3卷 第 8期
7 7
智能称量系统与死区 PD控制在烧结配料中的应用 I
n e l e tW eghn y t m n PI t lg n i i ig S se a d D Co t lW i a — o e n Sit r g Bu d n nr t De d— n i o h z ne i r e n
烧结自动配料控制系统的原理与应用

烧结自动配料控制系统的原理与应用2009-8-17 14:55:00济南钢铁总公司自动化部刘辉刘青凤供稿摘要:本文介绍了烧结配料系统的结构和原理,以及应用中出现的问题和解决方法。
关键词:自动配料、自动控制Abstract: This paper introduces working principle,and configuration of system,and how t o solve the problems in applications.Key words: Automatic proportioning、Automatic control前言众所周知,烧结厂配料系统是整个烧结生产的源头,它担负着所有烧结机的混合料供应任务,如果配料系统遇到问题,那么整个烧结生产都要被迫停止,而且配料系统的计算也要准确无误,因为烧结原料的种类多,配料成分随供货渠道的变化而变化,各单配料的配合比例也会根据生产的要求随时变化,而且在生产过程中,物料的黏度、比重、粒度及环境的温度、湿度的变化,也会严重影响下料的精度,因此,配料系统对于提高烧结矿的质量至关重要。
一、配料系统的工作原理1、配料原理在冶金行业中,烧结矿成分稳定在炼铁工艺中起着非常重要的作用。
其配比的准确性直接关系到烧结矿和炼铁的质量。
在传统的烧结配料生产线上,主要依靠工人的“跑盘”抽样检查原料的配比,再进行控制,这样不仅速度慢、调节不及时, 而且准确性差。
引入计算机控制以后,提高了控制速度和配比的准确性,减轻了工人劳动强度,稳定了烧结矿的化学成分。
在烧结配料生产线上,变频器控制圆盘的转速,从而调节下料速度,原料经阀门落到称重皮带上,再落到总皮带上,各料仓的原料按比例在总皮带上混合后,送混料系统。
圆盘下料量由称重传感器测量,信号为4~20mA,直接送Quantum的模拟量输入模块上,经控制器运算得到瞬时下料量和累计下料量,下料量给定与实际料流量经过PLC的PID控制器运算后,通过PLC输出4~20 mA的信号给变频器上,形成闭环控制,从而使下料量精确。
- 1、下载文档前请自行甄别文档内容的完整性,平台不提供额外的编辑、内容补充、找答案等附加服务。
- 2、"仅部分预览"的文档,不可在线预览部分如存在完整性等问题,可反馈申请退款(可完整预览的文档不适用该条件!)。
- 3、如文档侵犯您的权益,请联系客服反馈,我们会尽快为您处理(人工客服工作时间:9:00-18:30)。
烧结机自动称重配料控制方案一)控制方案及系统组成近年来,国内新建烧结机的配料方法均采用重量配料法,重量配料就是按原料的重量来配料,采用电子皮带秤对物料进行连续计量,通过调节圆盘给料机或皮带的速度来实现定量给料,重量配料易实现自动配料,配料精度较高。
烧结机的配料系统采用13个定量圆盘给料机和电子皮带秤定量给料以及主控皮带控制器组成,为提高皮带配料秤的计量精度和配料系统给料精度,所有给料机的皮带配料秤均采用变频调速的方式进行控制。
该自动称重配料控制由下列五大部分:电子皮带称、称重控制仪表、变频控制柜、监控计算机及现场操作箱部分。
配料自动控制实现烧结用的原料如混匀矿、燃料、熔剂白云石、生石灰、冷返矿按照工艺要求的配比进行自动给料,能够判断下料堵料和失控故障、变频器故障,并报警。
各类控制器任务:1.主控器:全局协调控制、皮带控制、故障处理、人机交互等。
2.配料器:信号采集处理、PID 调节、变频器控制、人机交互等。
… …大皮带大皮带控制器N#控制器2#控制器N-1#控制器1#监控机二)系统的工作方式系统检修和工作方式有二种:手动检修方式:即通过现场操作箱选择开关及按钮控制变频器以点动频率驱动电动机正反向运行速度;工作方式有二种第一种是仪表自动给料;即通过称重控制仪表键盘,任意给定所需给料量,并通过给料量大小变化自动调整变频器频率(电动机的运行速度);第二种是上位机自动给料,给料设定就可由上位机画面来完成。
正常工作在上位机自动给料,受计算机控制。
检修或调试时在“检修”状态,可以单机运行。
三)系统各部分功能3.1. 称重皮带秤及控制仪表功能流量恒定的控制原理要确保烧结配料成分的稳定,圆盘给料机和螺旋的流量控制是关键。
通过圆盘给料机和料仓给料器与集料皮带机之间安装调试好的电子配料皮带秤称量检测,以及配料皮带测速编码器(传感器)测量皮带运输原料速度的检测,称重仪表采集测量皮带秤上每单位长度的载荷值q(kg/m)以及皮带在同一时刻的运行速度v(m/s),且两者相乘得到物料的瞬时流量q·v(kg/s)。
只要保证q(t)·V(t)的乘积不变,就可以保证物料流量的恒定。
即随皮带上物料重量的变化控制皮带运行速度做出相应的调整,就可以保证物料流量的恒定。
在本系统中圆盘给料机的速度是恒定不可调的,所以控制流量的恒定只能调节皮带上物料重量,而重量的改变又只能通过改变变频器的频率,以改变皮带秤的速度。
流量恒定控制原理图2所示,每一个称重控制都是一个“小闭环”控制系统。
称重仪表检测并运算q(t)·V(t)的乘积与流量设定值(上位机给定或仪表键盘给定)进行比较,然后进行PID运算,,得出相应的输出频率信号到变频器,实现自动控制流量大小的要求。
1.实现流量恒定的控制仪表控制部分采用模块控制方式,电子秤与仪表控制模块之间的信号传输采用差分频率信号传输技术,具有极强的抗干扰能力和远传能力,从而保证了系统信道的可靠性和准确性,在反馈控制上采用新型的人工智能PID调节算法,无振荡,无超调。
2.仪表控制部分与监控计算机采用CAN总线通信方式,信号传输的快速实时性更高、抗干扰更强、可靠性更高,保证配料精度和稳定性。
3.配料秤有补偿功能,即皮带本身影响自动补偿功能。
能在配料秤正常生产运行过程中,连续不断地测量皮带本身实际重量的变化(如物料局部粘结等造成的皮带皮重的变化,天长日久磨损程度不同导致的皮带薄厚不均,以及张力不匀等所产生的对称重传感器的外部影响),并随时进行精确补偿,因而其动态测量精度要比一般设备厂家的配料秤动态测量精度高。
3.2计算机监控部分该计算机采用品牌机作为控制计算机, 系统软件是在Win2000操作平台下,用组态王(或VB6·0)开发研制的通用应用程序,整个程序兼顾鼠标和键盘操作。
各种操作界面、数据显示及打印管理,用户可方便进行各种数据的修改操作,运行数据的图形显示及打印各种报表。
工艺流程动画显示美观大方,友好的操作界面,简单易学,其功能如下:1.显示功能1)该系统能显示整个配料工艺及流程画面;2)显示各设备瞬时运行情况;3) 显示各台秤的给定流量、实际流量、下料累计量,显示各种原料的瞬间下料量、总流量及总累计量。
4)具有系统报警功能。
2操作及控制功能该系统利用操作提示菜单方便、简单,快速引导进行系统操作。
其功能如下:1)能实现变频器的远程操作(启停、手自动转换、单动);2)能快速修改各台电子秤的计量参数及换仓后各物料吸收系数的变更设置;3)修改配料系统的控制参数;4)根据工艺要求,可随时、方便的选定、修改、更换配比和配料总流量;5)当物料水分含量发生变化时,可方便的变更水分组和手动输入各物料的水分变化量。
6)根据现场实际需要,可对打印时间间隔、报警时间进行设置;3报表及打印功能1)按设置的打印参数方便的打印出各种原料累计消耗量的班报、日报、月报表并能进行相应的查询;2)具有当前趋势和历史趋势的查询功能;3)具有各料仓手动配料时间和配料量的统计功能。
4报警功能1)当系统各测量单元出现故障时,工艺流程主画面将以警示色提醒用户,按下相关键后,可由CRT显示故障代码;2)当系统出现空仓或园盘给料机堵料而无法下料时,工艺流程画面报警提醒用户及时处理。
3. 3变频控制部分皮带电机采用流量闭环变频调速方式,保证配料精度和稳定性,节电效果显著。
将每台变频器集中在变频电控制柜中。
正常工作时,称重仪表PID的输出控制变频器的输出频率,检修调试时,按钮点动控制变频器的输出频率。
3.4 现场操作箱调试或现场检修时,通过现场操作箱实现单机的正反运行。
四)配料设定值调整方案1、总流量调整、各配比不变:修改各料仓设定流量(采用双缓冲,保证前次设定流量不变),在顺起顺停模式下,延时投入(保证新流量在料头的比例);在同起同停模式下,同步投入。
2、总流量不变、各配比调整:1)停料重新启动:延时停料,修正皮重(保证本次配料全部到大批带),得到新配比后重新启动。
2)在线修改配比:得到新配比后送双缓冲区,启动同步计时,到启动时刻按新配比控制。
五)更换料仓及报警处理1、停料更换:延时停料,修正皮重。
按新料仓启动。
2、在线更换:通知其他料仓,减小流量,等待新料仓启动。
按新料仓启动。
3、故障报警:堵料(失控、皮带打滑)、卡料,通知其他料仓,减小流量,等待故障解除,若超时,则延时停料,修正皮重。
如果故障料仓有同种料仓同时下料,当超时可使另一料仓加倍下料。
六)启停模式1、同启同停:以皮带秤上料的比例为准。
2、顺启顺停:以大皮带上料头的比例为准。
七)控制功能和算法设计配料自动控制实现的功能是将烧结用的原料如混匀矿、燃料、熔剂(白云石、生石灰)、冷返矿按照一定配比进行自动给料。
具体功能有配比合理性检查、湿配比的计算和调整、排料量设定值的计算处理、配料秤的工作状态选择处理、控制方式的选择(计算机自动控制和远程手动)、自动换仓的处理等。
1、配料矿槽料位管理l)根据料位计掌握配料槽的料位根据称重式料位计的料重信号(单位;t),对1#~6#混匀矿槽、7#~8#燃料槽、9#~11#熔剂槽、12~14#冷返矿槽、15~16#生石灰槽的料位进行监视。
各贮矿槽的料位(料位%或重量值)可在操作站上进行显示。
(l)上述的重量值都是含有水份的值;(2)料位(%)为料位重量值百分比;(3)槽变更、空槽判断处理、料位报警判断处理及水分率变更等均在操作站上进行相应处理。
2)配料槽料位报警处理在操作站上显示配料槽库存量(原料重量,单位:t),以及配料槽的料位(单位:%),并进行配料槽料位越限报警。
各个矿槽的料位上上限(90%)、上限(80%)、下限(30%)、下下限(20%)报警信号在操作站上以颜色区分显示,其中上上限、下下限报警信号还需送电控联锁。
3)配料槽空槽判断对配料槽作空槽判断,当料位值达到下下限(LL)时将其作为空槽信号送至电气,作为槽变更判断条件之一。
2、配料系统的自动控制烧结用的新原料有混匀矿、熔剂、生石灰等,将这些新原料和冷返矿、燃料按照所要求的配比进行自动给料的过程称为配料系统的自动控制。
操作人员在画面上输入“设定干配比”,设定干配比使用前必须进行人工确认,再通过合理性检查得到“采用干配比”后才能进行湿配比的计算。
根据采用干配比和采用水分率经计算求出各种原料的湿配比,再根据混合料槽料位之需要,确定总的配料量,求出每台配料秤排料量的设定值。
由于贮矿槽空间位置的不同,则设定值必须经过延时处理,使各种原料的实际干配比在总配料量发生变化或槽变更时保持一致。
配料系统的各种计算、延迟设定及跟踪等功能由PLC完成;配料秤二次仪表对排料量设定值和测量值进行PI运算,并将控制输出信号通过通讯方式送给变频器完成闭环控制。
其控制算法设计如图4一2所示,其中m,c,r;为原料干配比,h为原料水分率,Wts为综合输送量,t为延迟时间,Di为配料设备运行状态。
图7一2配料控制算法设计图l)干配比合理性检查所谓干配比,就是按照烧结矿的化学成份以及高炉对烧结矿的要求,经计算求出的各种原料之间的配合比例(干量)。
在干配比设定后要进行如下干配比合理性检查:(l)新原料干配比之和要为100%;(2)单种物料干配比大于等于零;(3)读入配料槽选槽状态。
对槽选择状态信号进行判断,有配比设定的槽必须在选择中;无配比设定的槽应不被选择。
不符合上述条件时,作出报警提示;干配比分配时,根据有配比设定的槽数,其干配比分配为按类均分,无配比设定的槽作备用矿槽。
2)配合比计算总配合比包括新原料配合比,燃料配合比,返矿配合比,总配合比共计100%。
新原料包括混匀矿、熔剂(石灰石、白云石)、生石灰,新原料各成分比例合计100%。
燃料和返矿采用外配方式进行计算。
式中:mi一新原料的配合比(干量);ci一一燃料的配合比(干量);ri一返矿的配合比(干量);Mi—新原料的排料量(湿量);Ci--一一燃料的排料量(湿量);Ri一返矿的排料量(湿量);hi一原料的水分率;i一配料矿槽编号(其中i=1~6时,j=1,k= 6;i=9~11时,j=9,k=11;I=15~16时,j=l5,k=16),编号对应的矿槽如下:1~6:混匀矿槽;7~8:燃料矿槽;9~11:熔剂矿槽;12~14:返矿槽;15~16:生石灰槽.所谓湿配比,即各种原料(湿量)的给料量对于总给料量(湿量)之间的比例系数,称之为湿配比。
湿配比计算的条件:(l)干配比变更时计算:由于原料成份等各种原因引起人为变更干配比,要重新计算湿配比;(2)水分率变更时计算:根据实际生产情况人工变更水分率时,则湿料排料量有变化,需重新计算湿配比。
3)排料量设定值计算处理根据前面己求出的湿配比,可计算出每个矿槽排料量的设定值:Wsi=Wts xHki式中:Wsi:i贮矿槽排料量设定值Wts:综合输送量Hki:i贮矿槽湿配比,其中i为贮矿槽编号1一16其中综合输送量(升介‘)是根据混合料槽料位控制功能计算得到或由操作工根据实际生产情况人工设定的。