锦纶染色常见疵病及其预防、补救方法
酸性染料在锦纶染色上常见病疵分析

酸性染料在锦纶染色上的常见病疵分析1、横挡、横条1.1原因分析:织物上的锦纶纤维在化学或物理特征上存在差异。
1.1.1、纱线的物理差异,包括纱线支数、纱线中纤维的根数或纤维的纤度不同,纱线中单根纤维的末端卷曲或多根纤维末端卷曲之间的差异;1.1.2、化学差异来源于纤维氨基含量的不同,这种差异可能是在喷丝过程、热牵伸过程,或者并丝过程中产生的。
如锦纶纤维在处理过程中产生的超分子结构的不均一性,如纤维中的结晶度、取向度的差异或皮芯结构的不均一等。
1.2、解决办法:1.2.1、加强坯布检测,有差异的选择作浅色、本白或增白色。
1.2.2、挑选覆盖性、匀染性好的染料。
分散染料的覆盖性、匀染性优于酸性染料,可选择加入部分分散染料。
2、竞染造成的色花2.1、原因分析:锦纶中末端氨基的含量较少,饱和值较低,当两个或两个以上染料拼色染色时,就会发生对染色位置的竞争,即所谓竞染现象,如果选用的染料在上染率和亲和力方面差异较大时,在不同的染色时间内,纤维染得的色泽就会大不相同,造成大小样色差及重演性差。
2.2、解决办法:选择上染曲线及亲和力相似、配伍性好,以及适合生产机台的染化料系列。
掌握各类染料的染色性能,选择染化料时,要综合考虑染料的上染率、上染曲线、匀染性、色牢度性能,以及对温度和匀染剂的敏感性等因素。
2.2.1、充分考虑染料的配伍性使用几种染料拼染时,要选用合适的染料,且控制好染料用量。
一般应尽量选择同一公司的同一系列染料,即使不得不选用不同公司的染料相拼,也应尽量选择上染曲线相似、始染温度近似,以及对温度和匀染剂敏感性相似的染料,尽量避免发生竞染。
2.2.2、注意染料大小样竞染中的差异有些染料在小样染色时竞染并不明显,但在大生产中就完全暴露出来了。
例如,在生产湖绿色和孔雀蓝时,若选用酸性翠蓝和酸性黄相拼,就出现类似的问题。
这是由于酸性翠蓝的分子结构大,与酸性黄上染曲线相差很大,因而引起竞染。
若改用酸性翠篮与带黄光的酸性绿相拼,就基本解决了竞染问题。
定型常见疵病及克服办法
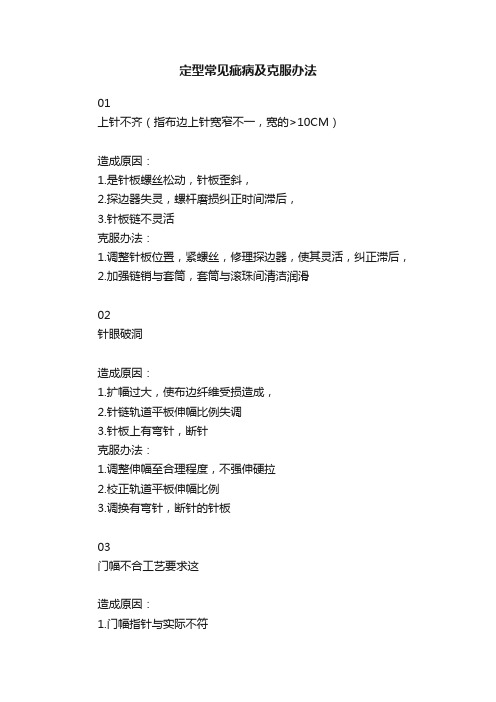
定型常见疵病及克服办法01上针不齐(指布边上针宽窄不一,宽的>10CM)造成原因:1.是针板螺丝松动,针板歪斜,2.探边器失灵,螺杆磨损纠正时间滞后,3.针板链不灵活克服办法:1.调整针板位置,紧螺丝,修理探边器,使其灵活,纠正滞后,2.加强链销与套筒,套筒与滚珠间清洁润滑02针眼破洞造成原因:1.扩幅过大,使布边纤维受损造成,2.针链轨道平板伸幅比例失调3.针板上有弯针,断针克服办法:1.调整伸幅至合理程度,不强伸硬拉2.校正轨道平板伸幅比例3.调换有弯针,断针的针板03门幅不合工艺要求这造成原因:1.门幅指针与实际不符2.调幅螺杆损坏造成指针与实际门幅不符3.前中后位的调幅离合器未吻合紧,造成门幅自动后移,使门幅不准。
克服办法:1.校正门幅指针到标准门幅2.检查修理调幅螺杆3.检查修理调幅离合器04纬斜造成原因:1.运行轨道上两边针铗数量不同,使织物两边纬纱前后不一2.针铗链运行套筒,销子磨损程度不一,使两边实际的运行长度发生差异3.毛刷主动辊超喂时转速有差异4.超喂辊两边压力不均或本事不平,造成织物两边经向张力不匀。
克服办法:1.轨道两边针铗数必须一致2.及时调换有磨损的套筒,销子3.毛刷及超喂辊速度必须控制一致,必要时更换电动机,织物定型前两边干湿度必须一致05针板印(指染色后出现的针板条形)造成原因:1.针板之间高低不平2.针铗链转动不灵活或链条太松3.上针毛刷压布太紧,使织物紧贴针板底部,热风循环不畅,两边有温差克服办法:1.将不平的针板,针铗用云母垫平,使呈水平直线,保持链条滚轴润滑,转动灵活,松紧适宜,使针板汇转成一条直线3.调节毛刷高低位置,使与短针相触4.预热针板链至工艺温度后再上布开车06月亮边或荷叶边造成原因:1.部分针板断针或磨损2.上针毛刷磨损或凹槽3.相邻针板上下高低不平,使针板低的部位布边进针不深,当受伸幅张力滑出针板克服办法:1.调换断针或损坏的针板2.调换磨损的上针毛刷3.校正针板,使上下高低水平定型时卷边怎么办?1.拉幅定形时在定型机的轧槽中,进行软整理可以达到客户对布匹的要求,并使其在导布轮上不易擦伤,拉幅定型使织物布面平整尺寸稳定,可消除染整加工过程中形成的皱纹,折痕,同时在定型时,需严格控制定型工艺条件。
锦纶染色和样不符问题及解决方案

锦纶染色和样不符问题及解决方案编辑:庄杰小张肆零零捌捌捌陆柒柒伍锦纶染色时,造成大小样色差的原因是多方面的,如大小样所用坯布、染化料、大小样工艺条件不同等。
可采取的预防及补救有:减少环境及光源的影响,规范打样和对色操作;分析大小样之间的差异,对小样的数据进行修正放样。
笔者从广州庄杰化工团队了解到,解决锦纶染色和样不符问题可以从以下方面控制。
1、小样对色务必严格、精确(1)化验室对色、配色环境设计,应尽可能采用黑白灰等系列颜色,这样可以预防因环境色彩对眼睛生理所引起的“残像”而影响对色。
对色环境的照明必须充足,以防止对色时因光源而发生的色相变化,应采用“有条件”的固定光源,或配备符合国际标准的灯箱。
如果光源变化的几率比较高,如化验室对色环境为开放式,则窗外光源会因不同时间不同光源的变化(如早上与下午的光源不同,阴天与晴天的光源不同),而影响配色效率。
(2)在打确认样之前应该先弄清楚客户的各种要求,如原样色光偏向,是否有特殊整理,纤维染色用染料是否被指定等。
(3)打小样用水应与大样生产一致,并需每日对水质及其pH值进行测试,并调节至工艺要求,避免产生色光差异。
(4)锦纶纤维的染色性能还随其染色前受热史而变化。
热定形条件不同会造成织物吸色率不同,从而造成织物批与批之间的色差。
锦纶织物前处理的工艺控制也对染色效果影响非常大,所以大小样的组织规格要相同,染前半制品的工艺条件力求一致,最好采用同一批半制品。
(5)小样应采用与大样同一产地、同一工厂、同一品名、同一批号的染化料。
配色时选择的染料配伍值要基本一致,这样才能保证染色过程中各染料在染液中的比例关系,有利于染色色光的稳定性和重现性。
拼色时主色染料宜固定,变动调节色光用染料,以便于大小样色光一致。
对于在染色加工过程中容易引起变色的染料不予采用。
2、规范化验室配色操作(1)一般来说,越接近灰色系列的颜色,其灰彩度越难判断,因为它包含的吸收色相比较复杂,经常需要三种染料拼混,故接近灰色系列的色相,配色时可仅以黄、红、青的感觉做色偏向的选择。
固色、柔软处理后染色疵病机理及回修分析
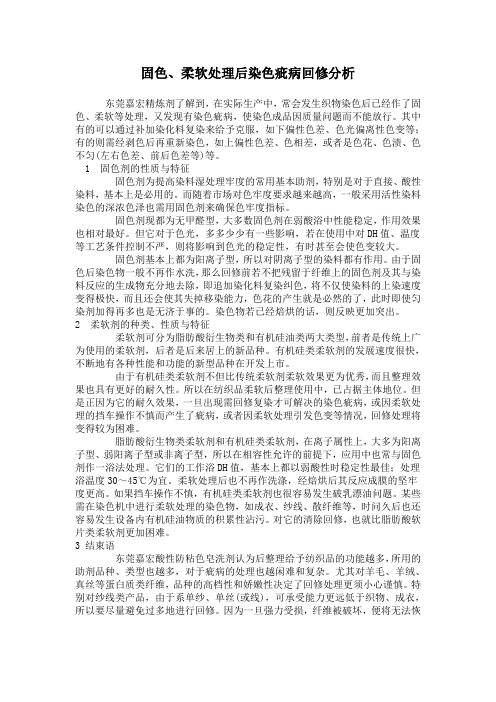
固色、柔软处理后染色疵病回修分析东莞嘉宏精炼剂了解到,在实际生产中,常会发生织物染色后已经作了固色、柔软等处理,又发现有染色疵病,使染色成品因质量问题而不能放行。
其中有的可以通过补加染化料复染来给予克服,如下偏性色差、色光偏离性色变等;有的则需经剥色后再重新染色,如上偏性色差、色相差,或者是色花、色渍、色不匀(左右色差、前后色差等)等。
1 固色剂的性质与特征固色剂为提高染料湿处理牢度的常用基本助剂,特别是对于直接、酸性染料,基本上是必用的。
而随着市场对色牢度要求越来越高,一般采用活性染料染色的深浓色泽也需用固色剂来确保色牢度指标。
固色剂现都为无甲醛型,大多数固色剂在弱酸浴中性能稳定,作用效果也相对最好。
但它对于色光,多多少少有一些影响,若在使用中对DH值、温度等工艺条件控制不严,则将影响到色光的稳定性,有时甚至会使色变较大。
固色剂基本上都为阳离子型,所以对阴离子型的染料都有作用。
由于固色后染色物一般不再作水洗,那么回修前若不把残留于纤维上的固色剂及其与染料反应的生成物充分地去除,即追加染化料复染纠色,将不仅使染料的上染速度变得极快,而且还会使其失掉移染能力,色花的产生就是必然的了,此时即使匀染剂加得再多也是无济于事的。
染色物若已经焙烘的话,则反映更加突出。
2 柔软剂的种类、性质与特征柔软剂可分为脂肪酸衍生物类和有机硅油类两大类型,前者是传统上广为使用的柔软剂,后者是后来居上的新品种。
有机硅类柔软剂的发展速度很快,不断地有各种性能和功能的新型品种在开发上市。
由于有机硅类柔软剂不但比传统柔软剂柔软效果更为优秀,而且整理效果也具有更好的耐久性。
所以在纺织品柔软后整理使用中,已占据主体地位。
但是正因为它的耐久效果,一旦出现需回修复染才可解决的染色疵病,或因柔软处理的挡车操作不慎而产生了疵病,或者因柔软处理引发色变等情况,回修处理将变得较为困难。
脂肪酸衍生物类柔软剂和有机硅类柔软剂,在离子属性上,大多为阳离子型、弱阳离子型或非离子型,所以在相容性允许的前提下,应用中也常与固色剂作一浴法处理。
当染色车间出现这8大染疵时,技术员必须学会的解决方案!【建议收藏】

当染色车间出现这8大染疵时,技术员必须学会的解决方案!【建议收藏】染色产品常见疵病分析建议收藏保存色差染色制品所得色泽深浅不一,色光有差异。
根据色差的不同又分为同批色差和同匹色差。
同批色差是指在同批产品中,一个色号的产品,箱与箱之间、件与件之间、包与包之间、匹与匹之间存在色差。
同匹色差是指同匹产品中的边中色差、前后色差或正反面等位置上的色差。
产生原因1、坯布原因2、染料在织物上先期分布不匀织物因素(布面上浆情况)吸液因素(吸液、渗透不匀)预烘因素(烘干不匀)3、染料在织物上固着程度不同:固着条件控制不当(如焙烘)4、染料选择不当5、染料色光发生变异染前因素(半制品白度、pH值等)染色因素(如温度过高)染后因素(后整理中的工艺和所加助剂)皂洗因素6、操作原因:化料不匀、加料不当;卷染上布不齐克服办法1、加强坯检,保证坯布质量2、选用合适设备、采用均匀轧车或改善轧车的均匀性3、加强练漂管理,提供合格半制品同一批染物采用相同坯布染前布面干燥要均匀一致染前定型效果要均匀丝光后布面pH值控制中性4、合理选择染料(上染曲线相似、加强染料测试等)5、染色时加入匀染性助剂6、染色工艺合理7、重视染后处理,水洗、皂洗要充分8、后整理助剂选择要慎重,工艺条件要一致色不符样染色成品的色泽与指定的样品色泽不符,并超过了允许色差标准。
表现为:不符同类布样(生产实样与原样属相同纤维、相同组织的色样)不符参考样(不同原料不同组织的色泽)不符成交小样(提供给客户并经双方确定的样品)不符数字样(客户提供的电脑测配色系统的数字样)产生原因1、染色工艺制定不当,大小样生产条件不相同2、审核色样光源不统一3、染色计划安排不周4、染料、助剂分批管理不善5、染色工艺条件、操作掌握不好半制品不符要求染色采用硬水染色管理不妥染化料量称错染色中没有严格掌握工艺条件克服方法1、大小样织物的组织规格要相同,半制品工艺相同;2、轧染时轧辊压力要固定,浸染时浴比要保持一致;3、大小样的染色工艺条件一致;(染料、助剂、温度、浴比等)4、染料要进行筛选易变色染料不用5、采用标准光源(或电脑测色仪器)6、合理安排染色生产计划7、加强染料、助剂的管理8、严格工艺纪律抓好三级检查(挡车工自查、班组及车间检查)掌握工艺条件、保证按工艺上车抓好每车或每缸布的对样、贴样制度色花布面颜色不均匀呈块状色深或色浅不规则色斑。
纺织品染整跟单-染色疵病
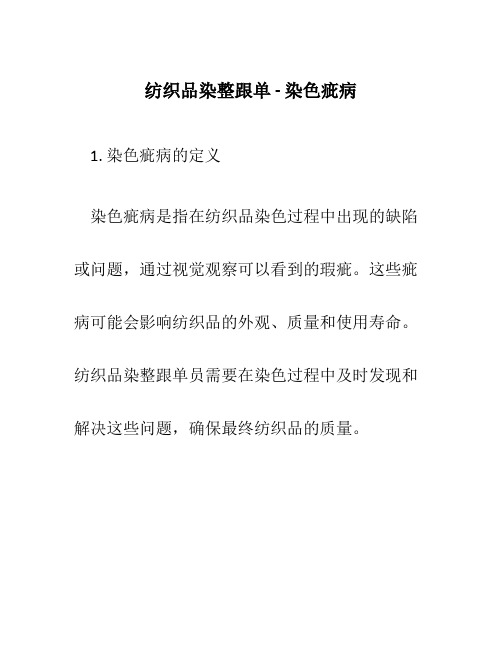
纺织品染整跟单 - 染色疵病1. 染色疵病的定义染色疵病是指在纺织品染色过程中出现的缺陷或问题,通过视觉观察可以看到的瑕疵。
这些疵病可能会影响纺织品的外观、质量和使用寿命。
纺织品染整跟单员需要在染色过程中及时发现和解决这些问题,确保最终纺织品的质量。
2. 常见的染色疵病类型2.1 色斑色斑是指在染色过程中出现的颜色不均匀的区域。
常见的原因包括染料的分散性不佳、浴液的循环不畅、染色温度不合适等。
染色疵病员需要密切关注染色机器的运行情况,调整相关参数以避免色斑的产生。
2.2 斑点斑点是指在纺织品上出现的局部颜色变化,呈圆形或椭圆形。
斑点的产生通常与染料分散性不佳、浴液中杂质或杂纤维的存在、搅拌不均匀等有关。
纺织品染整跟单员需要对染色机器进行充分清洁和维护,并确保染料的质量和稳定性。
2.3 着色不良着色不良是指纺织品整体颜色与所需色差过大。
常见的原因包括染料配方错误、浴比不当、染色机器故障等。
染色疵病员需要确保染色配方的准确性和纺织品的一致性,并及时调整相关参数以获得所需的色差。
2.4 染色剥落染色剥落是指染色后颜色在水洗或摩擦过程中脱落的现象。
常见的原因包括染料的附着力不够、染色温度过高、染浴pH值不合适等。
染色疵病员需要确保染料的附着力,控制染色温度和pH 值,并适当增加水洗或摩擦的时间和力度。
2.5 染缸色差染缸色差是指同一批染缸中染出的纺织品之间的颜色差异。
常见的原因包括浴液的循环不畅、染色机器的温度控制不准确、染料配方不均匀等。
染色疵病员需要确保染色机器的正常运行,控制好温度和浴液循环,并注意调整染料配方以获得一致的染色效果。
3. 染色疵病的预防和处理3.1 预防措施•严格控制染料的质量,选择稳定性好、分散性好的染料。
•保持染色机器的清洁和维护,定期进行检查和清洗。
•控制染色温度、浴液pH值等关键参数,避免过高或过低的条件。
•确保染料配方的准确性和一致性。
3.2 处理方法•将染色疵病标记清楚,并记录下相关信息,以便于后续追溯和处理。
锦纶染色产生疵点的原因及防止措施
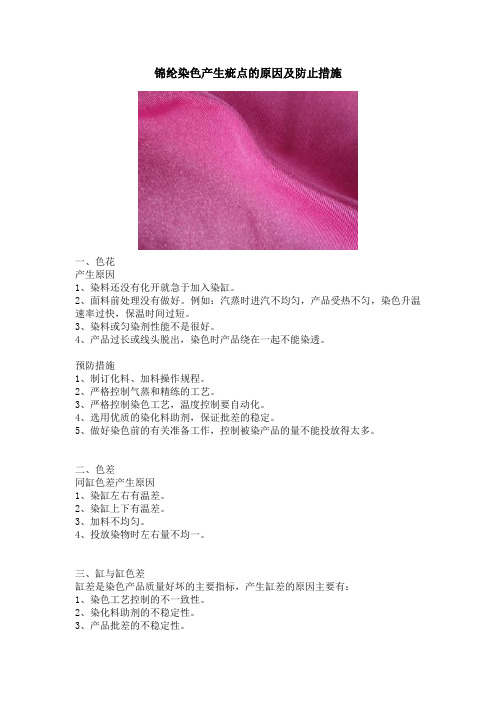
锦纶染色产生疵点的原因及防止措施一、色花产生原因1、染料还没有化开就急于加入染缸。
2、面料前处理没有做好。
例如:汽蒸时进汽不均匀,产品受热不匀,染色升温速率过快,保温时间过短。
3、染料或匀染剂性能不是很好。
4、产品过长或线头脱出,染色时产品绕在一起不能染透。
预防措施1、制订化料、加料操作规程。
2、严格控制气蒸和精练的工艺。
3、严格控制染色工艺,温度控制要自动化。
4、选用优质的染化料助剂,保证批差的稳定。
5、做好染色前的有关准备工作,控制被染产品的量不能投放得太多。
二、色差同缸色差产生原因1、染缸左右有温差。
2、染缸上下有温差。
3、加料不均匀。
4、投放染物时左右量不均一。
三、缸与缸色差缸差是染色产品质量好坏的主要指标,产生缸差的原因主要有:1、染色工艺控制的不一致性。
2、染化料助剂的不稳定性。
3、产品批差的不稳定性。
4、染色技术员和操作工的敬业性和责任性。
预防措施1、改善染色设备。
例如:改用外置加热或底部加循环泵,保证左右升温均匀。
2、加快桨叶的运转速度,使上下传热加快。
3、产品投缸时要保证左右中间量的均匀性。
4、加料能改成自动加料系统。
5、严格控制染色工艺,确保缸次间工艺的一致性。
6、优选染化料助剂,做好染料和助剂换批的检测工作,保证染色处方准确性。
7、加强产品白坯的管理,保证配缸重量的准确性,不混淆产品的批次,不乱混产品货号。
8、加强员工的素质教育,提高员工素养和敬业精神。
四、色点和色斑产生原因1、纱线不纯,有杂质或者色纱混入其中,染色后无法消除。
2、在织造生产过程中混入有颜色飞毛。
3、白坯堆放时间过长产生霉斑和黄斑。
4、染色过程染料飞沾到产品上成色点。
5、产品部分地方在前处理或染色时碰到了某种助剂原液,影响了染料的上染,从而在此产生白点或浅色斑。
6、与某些溶解度特别小的染料拼色时,没有充分化料就加入染缸,没有完全溶解的染料沾到产品上产生色点。
预防措施1、加强进原料时的质量检验和控制,防止不纯纱线的进入。
如何解决锦纶织物染色时产生的横档和经柳问题?
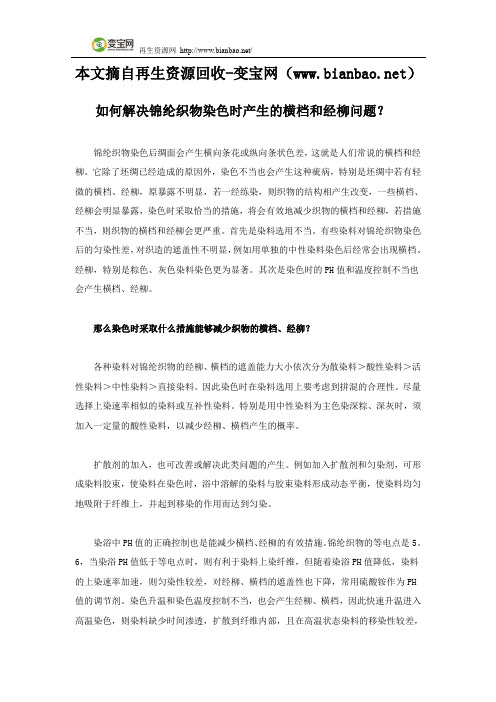
本文摘自再生资源回收-变宝网()如何解决锦纶织物染色时产生的横档和经柳问题?锦纶织物染色后绸面会产生横向条花或纵向条状色差,这就是人们常说的横档和经柳。
它除了坯绸已经造成的原因外,染色不当也会产生这种疵病,特别是坯绸中若有轻微的横档、经柳,原暴露不明显,若一经练染,则织物的结构相产生改变,一些横档、经柳会明显暴露,染色时采取恰当的措施,将会有效地减少织物的横档和经柳,若措施不当,则织物的横档和经柳会更严重。
首先是染料选用不当。
有些染料对锦纶织物染色后的匀染性差,对织造的遮盖性不明显,例如用单独的中性染料染色后经常会出现横档、经柳,特别是粽色、灰色染料染色更为显著。
其次是染色时的PH值和温度控制不当也会产生横档、经柳。
那么染色时采取什么措施能够减少织物的横档、经柳?各种染料对锦纶织物的经柳、横档的遮盖能力大小依次分为散染料>酸性染料>活性染料>中性染料>直接染料。
因此染色时在染料选用上要考虑到拼混的合理性。
尽量选择上染速率相似的染料或互补性染料。
特别是用中性染料为主色染深粽、深灰时,须加入一定量的酸性染料,以减少经柳、横档产生的概率。
扩散剂的加入,也可改善或解决此类问题的产生。
例如加入扩散剂和匀染剂,可形成染料胶束,使染料在染色时,浴中溶解的染料与胶束染料形成动态平衡,使染料均匀地吸附于纤维上,并起到移染的作用而达到匀染。
染浴中PH值的正确控制也是能减少横档、经柳的有效措施。
锦纶织物的等电点是5。
6,当染浴PH值低于等电点时,则有利于染料上染纤维,但随着染浴PH值降低,染料的上染速率加速,则匀染性较差,对经柳、横档的遮盖性也下降,常用硫酸铵作为PH 值的调节剂。
染色升温和染色温度控制不当,也会产生经柳、横档,因此快速升温进入高温染色,则染料缺少时间渗透,扩散到纤维内部,且在高温状态染料的移染性较差,而造成经柳、横档,所以染色时需逐步升温。
在高温时(70℃以上)升温速度要慢,以保证染料有充分的时间吸附、渗透和扩散,达到均匀染色。
- 1、下载文档前请自行甄别文档内容的完整性,平台不提供额外的编辑、内容补充、找答案等附加服务。
- 2、"仅部分预览"的文档,不可在线预览部分如存在完整性等问题,可反馈申请退款(可完整预览的文档不适用该条件!)。
- 3、如文档侵犯您的权益,请联系客服反馈,我们会尽快为您处理(人工客服工作时间:9:00-18:30)。
锦纶染色常见疵病及其预防、补救方法
1 前言
锦纶是一种疏水性纤维,纤维上含有氨基和羧基[1],可以用分散染料、酸性染料,特别是弱酸性染料染色。
其染色具有上染速率快、竭染率高的特点,但由于纺丝工艺规格的不同,造成纤维结构差异很大,引起上染性能差别较大,容易产生色差。
因此,如果制订小样工艺时稍有疏忽,就有可能造成上染不匀,产生色差、色渍、色点、深浅边、条花、色不符样和染色牢度差等疵病。
所以,锦纶染色时,小样人员一定要制订合理的染色工艺,并严格把关全程工艺,以降低次品率,减轻大生产压力。
笔者通过十多年对锦纶染色打样工作的实践,总结锦纶染色常见疵病,以及预防和技术补救的方法。
2 常见疵病及预防和补救措施
2.1 竞染造成色花和色不符样
这是由于染化料选择不当引起的。
锦纶的染色饱和值很低,因此在拼染浓色时,不同染料间的竞染就显得很突出。
如果选用的染料在上染率和亲和力方面差异较大时,在不同的染色时间内,纤维染得的色泽就会大不相同,造成大小样色差及重演性差。
预防及补救措施是选择上染曲线及亲和力相似、配伍性好,以及适合生产机台的染化料系列。
要求打样人员要全面掌握各类染料的染色性能,选择染化料时,要综合考虑染料的上染率、上染曲线、匀染性、色牢度性能,以及对温度和匀染剂的敏感性等因素。
2.1.1 充分考虑染料的配伍性
使用几种染料拼染时,要选用合适的染料,且控制好染料用量。
一般应尽量选择同一公司的同一系列染料,即使不得不选用不同公司的染料相拼,也应尽量选择上染曲线相似、始染温度近似,以及对温度和匀染剂敏感性相似的染料,尽量避免发生竞染。
2.1.2 注意染料大小样竞染中的差异
有些染料在小样染色时竞染并不明显,但在大生产中就完全暴露出来了。
例如,在生产湖绿色和孔雀蓝时,若选用酸性翠蓝和酸性黄相拼,就出现类似的问题。
这是由于酸性翠蓝的分子结构大,与酸性黄上染曲线相差很大,因而引起竞染。
若改用酸性翠篮与带黄光的酸性绿相拼,就基本解决了竞染问题。
2.1.3 注意机台对染料的适应性
染机有喷射、经轴和卷染机等。
喷射染色机中染液与织物接触充分,匀染性好,产品手感丰满,且重现性好,缸差小,但其耐湿处理牢度相对较差。
可选用牢度好,但匀染性略差的弱酸性染料或1∶2金属络合酸性染料进行染色。
经轴染色机的产品门幅控制简便,固色容易,但易出现深浅层和头尾色差等问题。
可选用匀染性好而牢度略差的染料,并略提高匀染剂的用量,染色后再加强固色。
2.2 工艺不合理造成的疵病
锦纶染色对工艺要求极高。
工艺条件是影响染色产品色光和匀染性的重要因素,如温度、浴比、pH值等,都会影响产品的质量。
不合理的工艺容易产生匀染差、色花、色柳、色差、牢度差等病疵。
2.2.1 控制始染温度及升温速率
温度是控制上染的重要因素。
温度的高低,会影响纤维的膨化程度、染料的性能(溶解性、分散性、上染率、色光等)以及助剂性能的发挥。
锦纶是热塑性纤维,温度低时上染速率很慢,温度超过50℃,纤维的溶胀随温度升高而不断增加。
温度对染料上染速率的影响还因染料的不同而有所不同,匀染性染料的上染速率随温度升高而逐渐增加;耐缩绒染料的上染率要在染浴温度高于60℃以后才开始随温度的升高而
迅速增加。
特别在65~85℃的温度范围内,控制升温速率是锦纶染色成败的关键,若控制不当,就会造成上色快、移染性差,易花难回修的问题。
若采用耐缩绒染料染锦纶时,始染温度应为室温,在65~85℃温度段,严格控制升温速率1℃min左右,并加入匀染剂,采取阶梯升温办法;然后升温至95~98℃,保温45~60min。
另外,这种纤维的染色性能还随染色前所受到的热处理条件而变化,经干热定形后的纤维上染速率显著下降。
2.2.2 确定合适的浴比
由于设备的限制,小样浴比会比大生产大,但浴比过大会降低上染率,造成大小样色差。
轻薄型的塔夫绸浴比一般为1∶50,较厚重的织物浴比为1∶20,以织物可完全浸入染液为准。
2.2.3 控制pH值
染浴pH值对染料的上染率影响很大,上染率随pH值的降低会快速增加。
用弱酸性染料染锦纶时,染浅色的pH值一般控制在6~7(常用醋酸铵调节),并提高匀染剂的用量,以加强匀染,避免染花,但pH值也不能过高,否则色光会萎暗;染深色的pH值为4~6(常用醋酸和醋酸铵调节),并在保温的过程中加入适量的醋酸降低pH值,促进染料上染。
2.2.4 注意匀染剂的选用及用量
针对锦纶染色匀染性及覆盖性差的特点,应在染浴中加入少量阴离子或非离子型匀染剂,其中以阴离子型表面活性剂为主。
既可在染色时与染料同浴使用,亦可以用匀染剂对锦纶进行染前处理。
阴离子型匀染剂在染浴中离解成负离子,进入纤维,首先占据锦纶纤维上有限的染座,然后在染色过程中随温度升高逐渐被染料所替代,降低了染料与纤维之间的结合速度,达到匀染的目的;非离子型匀染剂则在染浴中与染料发生氢键结合,然后在染色过程中逐渐分解释放出染料,并被纤维吸附。
通过试验发现,匀染剂的加入可明显改善匀染性及盖染能力,但随助剂浓度的增加,上染速率下降,导致竭染率不同程度下降,因此匀染剂用量不可太多。
因为匀染剂在染色过程中除起匀染效果外,同时还有阻染作用。
匀染剂用量过大,会降低酸性染料上染率,使染色残液浓度升高,造成大小样色差及重演性差。
一般,染浅色时匀染剂用量较大;染深色时,匀染剂用量较少。
长期以来,业界一直认为pH值的控制是锦纶染色成败的关键。
经过多年生产经验的积累,我们发现引入缓冲体系后,匀染剂的选用及用量对控制大小样色差起决定性作用。
匀染剂要与相应的染料类别配套使用,但用量一定要根据实际情况进行调整。
小样生产时,匀染剂的用量控制在0.2~1.5gL,即在达到良好的匀染效果的前提下,若浅色的残液率在2%~3%、中深色在5%~15%,则该匀染剂用量即为所需量。
大生产再根据小样用量进行修正,可达到很好的效果。
2.3 大小样色差
锦纶染色时,造成大小样色差的原因是多方面的,如大小样所用坯布、染化料、大小样工艺条件不同等。
可采取的预防及补救有减少环境及光源的影响,规范打样和对色操作;分析大小样之间的差异,对小样的数据进行修正放样。
2.3.1 小样对色务必严格、精确
(1)化验室对色、配色环境设计,应尽可能采用黑白灰等系列颜色,这样可以预防因环境色彩对眼睛生理所引起的“残像”而影响对色。
对色环境的照明必须充足,以防止对色时因光源而发生的色相变化,应采用“有条件”的固定光源,或配备符合国际标准的灯箱。
如果光源变化的几率比较高,如化验室对色环境为开放式,则窗外光源会因不同时间不同光源的变化(如早上与下午的光源不同,阴天与晴天的光源不同),而影响配色效率。
(2)在打确认样之前应该先弄清楚客户的各种要求,如原样色光偏向,是否有特殊整理,纤维染色用染料是否被指定等。
(3)打小样用水应与大样生产一致,并需每日对水质及其pH值进行测试,并调节至工艺要求,避免产生色光差异。
(4)锦纶纤维的染色性能还随其染色前受热史而变化。
热定形条件不同会造成织物吸色率不同,从而造成织物批与批之间的色差。
锦纶织物前处理的工艺控制也对染色效果影响非常大,所以大小样的组织规格要相同,染前半制品的工艺条件力求一致,最好采用同一批半制品。
(5)小样应采用与大样同一产地、同一工厂、同一品名、同一批号的染化料。
配色时选择的染料配伍值要基本一致,这样才能保证染色过程中各染料在染液中的比例关系,有利于染色色光的稳定性和重现性。
拼色时主色染料宜固定,变动调节色光用染料,以便于大小样色光一致。
对于在染色加工过程中容易引起变色的染料不予采用。
2.3.2 规范化验室配色操作
(1)一般来说,越接近灰色系列的颜色,其灰彩度越难判断,因为它包含的吸收色相比较复杂,经常需要三种染料拼混,故接近灰色系列的色相,配色时可仅以黄、红、青的感觉做色偏向的选择。
越是色彩感觉强的颜色,颜色的鲜与纯对色相的判断越是重要,故配色时要首先作出正确判断,选用正确的染料。
(2)对色时要注意观察样与光线照射角度的变化,以保持一致。
(3)把握样布染色后的烘干程度。
烘干过度,会造成色光不可逆的偏红;烘干不够,则影响色样的色光饱和度。
两种情况都会造成色光偏差。
(4)仿色时应重视分品种、分色系,且留样,积累资料建立色样库(有对应的实际生产样更好)。
2.3.3 严格控制大小样工艺的一致性
(1)打样染浴的pH值及升温工艺应尽量与大生产一致。
大样生产由于水质及直接蒸汽或间接蒸汽的交叉使用,往往锅炉蒸汽带入碱性而使染浴pH值偏高,使用缓冲剂或配备pH值在线监控仪可以解决这个问题。
(2)小样染色的保温时间要与大样保持一致,以免由于染透性差而造成色差。
(3)因固色也会影响色光,所以,小样固色后一定要调节色光,才能进入大生产的工艺制订。
3 结语
影响锦纶染色产品质量的因素很多,主要包括设备、工艺、染化料、大小样色差及操作等几方面。
生产实践证明,抓好了上述几个环节,可以提高锦纶染色的准确性和稳定性,使小样放样的一次成功率达到90%以上。