中文翻译-模具型腔数控加工计算机辅助刀具选择和研究
模具数控加工计算机辅助刀具选择研究外文文献翻译、中英文翻译、外文翻译

外文翻译专业机械设计制造及其自动化学生姓名陈曦班级BD机制031学号0320110129指导教师刘道标.模具数控加工计算机辅助刀具选择研究耿铁段修涛译引言数控加工中包括刀具轨迹的产生和刀具选择两个关键问题。
前一问题在过去的20 年里得到了广泛而深入地研究,发展的许多算法已在商用CAD/ CAM 系统中得到应用。
目前大多数CAM 系统能够在用户输入相关参数后自动产生刀具轨迹。
比较而言,对以质量、效率为优化目标的刀具选择问题的研究还远未成熟,当前还没有商用CAM 系统能够提供刀具优选的决策支持工具,因而难以实现CAD/ CAM 的自动有机集成。
刀具选择通常包括刀具类型和刀具尺寸。
一般来说,适合一个加工对象的刀具通常有多种,一种刀具又可完成不同的加工任务,所以仅考虑满足基本加工要求的刀具选择是较容易的,尤其对孔、槽等典型几何特征。
但实际上,刀具选择通常和一定的优化目标相联系,如最大切削效率、最少加工时间、最低加工成本、最长使用寿命等,因此刀具选择又是一个复杂的优化问题。
比如模具型腔类零件,由于几何形状复杂(通常包含自由曲面及岛) ,影响刀具选择的几何约束在CAD 模型中不能显式表示,需要设计相应的算法进行提取,因而选择合适的刀具规格及其刀具组合,以提高数控加工的效率与质量并非易事。
模具型腔一般用数控铣的加工方法,通常包括粗加工、半精加工、精加工等工序。
粗加工的原则就是尽最大可能高效率地去除多余的金属,因而希望选择大尺寸的刀具,但刀具尺寸过大,可能导致未加工体积的增多;半精加工的任务主要是去除粗加工遗留下来的台阶;精加工则主要保证零件的尺寸及表面质量。
考虑到目前完全由计算机进行自动选刀还存在一定困难,因而在我们开发的计算机辅助刀具选择(Computer Aided Tool Selection ,CATS)系统中,立足于给用户提供一个辅助决策工具,即粗加工、半精加工、精加工等,真正的决策权仍留给用户,以充分发挥计算机和人的优势。
CNC机床加工中的刀具选型与切削参数优化

CNC机床加工中的刀具选型与切削参数优化CNC(Computer Numerical Control)机床是一种能够按照预先输入的程序指令进行自动化加工的机床。
在CNC机床加工中,刀具选型与切削参数的选择对于加工质量和效率起着至关重要的作用。
本文将就CNC机床加工中的刀具选型与切削参数优化进行探讨。
一、刀具选型在CNC机床加工中,刀具的选型要根据加工材料、加工要求以及加工方式来选择,常用的刀具选型有以下几种:1.硬质合金刀具硬质合金刀具具有优异的耐磨性和高硬度,适用于加工硬度较高的材料,如铸铁、合金钢等。
同时,硬质合金刀具还能够提供较好的切削性能和切削稳定性,因此在高速切削中得到广泛应用。
2.高速钢刀具高速钢刀具是热处理过的优质合金钢,具有较高的硬度和耐磨性。
高速钢刀具适用于一般加工材料的加工,价格相对较低,是较为经济实用的刀具选型。
3.立铣刀具立铣刀具适用于铣削工艺,能够完成平面铣削、开槽、镗孔等加工操作。
立铣刀具具有较高的刚性和切削性能,能够提高加工效率和加工精度。
4.钻孔刀具钻孔刀具用于钻孔加工,分为普通钻头和中心钻头两类。
普通钻头适用于常规钻孔操作,而中心钻头则适用于加工前的定位孔。
二、切削参数优化在CNC机床加工中,刀具的切削参数选取直接关系到加工效率和加工质量,合理的切削参数优化能够提高加工效率和延长刀具寿命。
下面分别从切削速度、进给量、切削深度等几个方面进行优化探讨。
1.切削速度切削速度是指刀具在加工过程中的旋转速度,需要根据材料硬度和刀具类型来选择合适的转速。
过高的切削速度会导致切削过程中的高温和过量磨损,而过低的切削速度则会影响加工效率。
因此,在确定切削速度时,需要考虑加工要求和刀具特性,以达到切削效果和刀具寿命的平衡。
2.进给量进给量是指刀具在加工过程中沿工件表面前进的距离,选择合适的进给量可以控制加工负荷,保证加工质量。
过小的进给量会导致切削效率低下,过大的进给量则容易引起振动和过度磨损。
数控加工技术学习中的刀具选择指南

数控加工技术学习中的刀具选择指南随着科技的不断发展,数控加工技术在工业生产中得到了广泛应用。
而在数控加工过程中,刀具的选择是至关重要的一环。
本文将为大家介绍数控加工技术学习中的刀具选择指南,帮助大家更好地理解和掌握这一技术。
一、刀具材料选择刀具材料的选择直接影响着加工效果和刀具寿命。
常见的刀具材料有高速钢、硬质合金和陶瓷等。
在选择刀具材料时,需要考虑加工材料的硬度、韧性和热导率等因素。
1. 高速钢刀具:适用于加工低硬度材料,具有较好的韧性和耐磨性,价格相对较低。
但对于高硬度材料的加工,高速钢刀具的寿命较短。
2. 硬质合金刀具:适用于加工高硬度材料,具有较高的硬度和耐磨性。
但硬质合金刀具的韧性较差,容易断裂,价格也相对较高。
3. 陶瓷刀具:适用于加工高硬度和高温材料,具有优异的耐磨性和高温稳定性。
但陶瓷刀具易碎,加工过程需要注意避免冲击和振动。
二、刀具几何形状选择刀具的几何形状对加工效果和刀具寿命有着重要影响。
常见的刀具几何形状包括平头刀、球头刀和锥度刀等。
1. 平头刀:适用于平面加工和开槽等操作,具有较大的切削面积,能够提高加工效率。
但平头刀容易产生振动和噪音,需要注意加工过程中的稳定性。
2. 球头刀:适用于曲面加工和倒角等操作,能够实现复杂曲线的加工。
球头刀具有较小的切削力和较好的表面质量,但加工效率相对较低。
3. 锥度刀:适用于孔加工和倒角等操作,能够实现不同直径的孔加工。
锥度刀具有较好的切削刚度和切削稳定性,但需要注意加工过程中的刀具中心偏移问题。
三、刀具涂层选择刀具涂层能够有效提高刀具的耐磨性和耐高温性,延长刀具的使用寿命。
常见的刀具涂层包括涂层碳化物、涂层氮化物和涂层氧化物等。
1. 涂层碳化物:具有较高的硬度和耐磨性,能够有效减少切削力和热膨胀。
涂层碳化物适用于加工高硬度材料和高温材料。
2. 涂层氮化物:具有较好的耐磨性和耐高温性,能够提高刀具的切削速度和切削深度。
涂层氮化物适用于高速切削和重切削操作。
数控加工刀具的比较与选择

数控加工刀具的比较与选择摘要:数控加工技术越来越被广泛应用,而刀具作为数控加工过程中不可缺少的一环,对于加工效果和效率具有至关重要的影响。
在刀具选择方面,应考虑到材料、形状、刃口结构、切削力和切削速度等因素。
本文探讨了常见的几种数控加工刀具类型及其特点,分析它们的优缺点,并提出了在不同的加工情况下如何选择适合的刀具。
关键词:数控加工、刀具、选择正文:随着现代制造业的发展,数控加工技术已得到广泛应用。
在数控加工过程中,刀具是实现高效加工和质量保障的关键所在。
因此,在选择数控加工刀具时需要考虑到多个因素。
1. 刀具材料优秀的刀具材料应具有高硬度、高韧性和较高的耐磨性。
目前市面上常见的刀具材料包括高速钢、硬质合金、陶瓷和多晶体立方石。
高速钢刀具是质量较高、价格较低的选项,但其硬度和耐磨性相对较低。
硬质合金刀具具有较高的硬度和耐磨性,但韧性较差。
陶瓷刀具则可以用于高速加工,但其价格较高。
2. 刀具形状刀具形状对其能否在处理中达到良好的效果和性能起着重要作用。
目前市场上较为常见的刀具形状有直刀、球头刀、圆弧刀和T形刀等。
不同的刀具形状适用于不同的加工类型和材料。
3. 刃口结构刃口结构是决定刀具切削效果的关键所在。
常用的刃口结构包括单刃、双刃、三刃和四刃刀等。
三刃刀比单刃刀具有较高的切削效率,但相应地也会产生更大的切削力。
4. 切削力和切削速度刀具的切削力取决于刀具的形状和材料。
对于高硬度的材料,需要选择较为坚硬的刀具来保证其稳定性和耐用性。
切削速度和动力也应根据不同的加工工件进行适当调整以获得最佳的加工效果。
综合上述因素,目前市场上常见的几种数控加工刀具包括高速钢刀具、硬质合金刀具、陶瓷刀具和多晶体立方石刀具。
在实际操作中,应根据具体的加工需求选择最合适的刀具。
例如,在加工新材料时,可以尝试使用陶瓷刀具或多晶体立方石刀具,因其具有更好的切削性能和质量保证。
总之,刀具的选择是数控加工过程中的一项重要决策。
除了上述因素,应还考虑到刀具的生产厂家、质量和价格等方面,以获得最佳的加工效果和经济效益。
数控模具加工中的刀具选型与刀具磨削

数控模具加工中的刀具选型与刀具磨削在数控模具加工中,刀具的选型和磨削是非常重要的环节。
合理的刀具选型和精确的刀具磨削可以提高加工效率和产品质量,降低生产成本。
本文将从数控模具加工的特点、刀具选型和刀具磨削技术等方面进行探讨。
一、数控模具加工的特点数控模具加工是利用计算机控制的数控机床进行的模具加工。
相比传统的手工加工和普通机床加工,数控模具加工具有以下特点:1. 高精度要求:模具加工通常需要达到较高的精度要求,以保证模具的质量和加工件的精度。
2. 复杂形状加工:模具通常具有复杂的形状和结构,需要进行多轴、多面、多角度的加工。
3. 加工难度大:模具材料通常较硬,如钢、合金等,加工难度大,对刀具的性能要求高。
二、刀具选型刀具选型是数控模具加工中的关键环节。
合理的刀具选型可以提高加工效率和产品质量。
1. 刀具材料选择:对于模具加工,通常选择硬质合金刀具。
硬质合金刀具具有高硬度、高耐磨性和高热稳定性等特点,适合加工硬材料。
2. 刀具形状选择:根据加工件的形状和结构,选择合适的刀具形状。
常见的刀具形状有平头刀、球头刀、锥度刀等。
3. 刀具刀尖半径选择:刀尖半径的选择直接影响加工表面的质量。
一般情况下,刀尖半径越小,加工表面的质量越好,但同时也会增加刀具的易损性。
4. 刀具刃数选择:刀具刃数的选择要根据具体的加工要求和加工材料来确定。
刃数越多,加工效率越高,但刀具的稳定性和切削力也会增加。
三、刀具磨削技术刀具磨削是刀具维护和修复的重要环节。
合理的刀具磨削技术可以延长刀具的使用寿命,提高加工质量。
1. 磨削工艺选择:根据刀具的不同形状和材料,选择合适的磨削工艺。
常见的磨削工艺有平面磨削、外圆磨削、内圆磨削等。
2. 磨削参数控制:在磨削过程中,控制好磨削参数对于刀具的磨削质量至关重要。
磨削参数包括磨削速度、进给速度、磨削厚度等。
3. 刀具修复技术:对于损坏的刀具,可以通过修复技术进行修复。
常见的刀具修复技术有热处理修复、电火花修复等。
UG加工部分中英文翻译对照
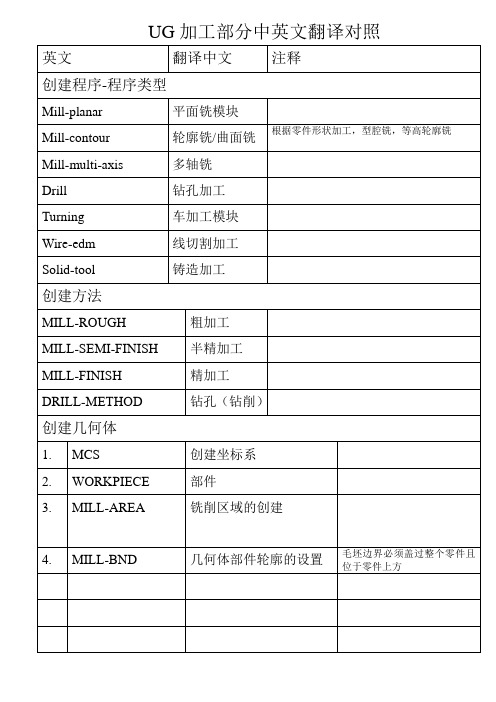
创建刀具时刀号参数:1.“补偿寄存器”为长度补偿。
2.“刀具补偿寄存器”为半径补偿,在G41 G42时用
l-planar类型下:
1.
Mill
端铣刀(平面铣刀)
2.
CHAMFER-MILL
倒角刀
3.
BALL-MILL
球刀
4.
SPHERICAL-MILL
球状铣刀
5.
T-CUTTER
MILL-ROUGH
粗加工
MILL-SEMI-FINISH
半精加工
MILL-FINISH
精加工
DRILL-METHOD
钻孔(钻削)
创建几何体
1.
MCS
创建坐标系
2.
WORKPIECE
部件
3.
MILL-AREA
铣削区域的创建
4.
MILL-BND
几何体部件轮廓的设置
毛坯边界必须盖过整个零件且位于零件上方
T形铣刀(专用刀)
2.drill类型下:
1.
SPOTFACING-TOOL
键槽铣刀
用于斜面或曲面上的孔加工
2.
SPOTDRILLING-TOOL
中心钻
钻中心孔
3.
DRILLING-TOOL
麻花钻
4.
BORING-BAR
镗刀
5.
REAMER
铰刀
6.
COUNTERBORING-TOOL
沉头孔刀
用于加工沉头孔
UG加工部分中英文翻译对照
英文
翻译中文注释创建程序-源自序类型Mill-planar
平面铣模块
Mill-contour
轮廓铣/曲面铣
数控机床技术中的加工刀具的选用与磨削

数控机床技术中的加工刀具的选用与磨削随着科技的进步和工业生产的发展,数控机床在制造业中发挥着越来越重要的作用。
而在数控机床的加工过程中,加工刀具的选用和磨削技术的应用对于加工质量的保证和生产效率的提高起着至关重要的作用。
本文将着重探讨数控机床技术中加工刀具的选用和磨削方面的相关知识。
首先,加工刀具的选用对于数控机床的加工质量和效率具有重要影响。
在选择加工刀具时,需要根据加工材料的特点、加工工艺要求和加工形式来进行评估。
首先,要考虑加工材料的硬度和切削性能。
不同材料的硬度和切削性能不同,因此需要选择适合的刀具材料和结构。
对于硬度较高的材料,如钢铁、合金等,通常选择硬质合金刀具或陶瓷刀具,以保证刀具的耐磨性和切削性能。
而对于切削性能要求较高的材料,如铜、铝等,可以选择高速钢刀具,以提高加工效率。
其次,加工工艺要求也是刀具选用的重要考虑因素。
不同的加工工艺对刀具的要求不同。
例如,对于精密加工工艺,如车削、铣削等,通常需要选择高精度的刀具,以保证加工的精度和表面质量。
而对于粗加工工艺,如钻孔、铣槽等,可以选择经济实用的刀具,以提高生产效率。
最后,加工形式也会影响刀具的选用。
不同的加工形式,如平面加工、轮廓复杂加工等,需要选择不同类型的刀具来满足加工要求。
例如,对于平面加工,可以选择钢质刀具或高硬度刀具来进行加工;而对于轮廓复杂加工,可以选择球头铣刀、T型刀具等来满足不同形状的加工需求。
除了刀具的选用,磨削技术也是数控机床加工中不可忽视的重要环节。
刀具的磨削过程可以帮助恢复刀具的切削性能和延长其使用寿命。
在刀具磨削过程中,首先需要选择合适的磨削工艺和磨削液。
磨削工艺的选择应考虑刀具的材料和几何特征。
对于硬质合金刀具,常用的磨削工艺有平面磨削、外圆磨削等;而对于高速钢刀具,常用的磨削工艺有刃磨、外圆磨削等。
在磨削过程中,应合理选择磨削液,以提高刀具的磨削质量和表面粗糙度。
其次,在刀具的磨削过程中,需要掌握正确的磨削参数。
数控加工工艺及编程 项目8腔槽--刀具选择
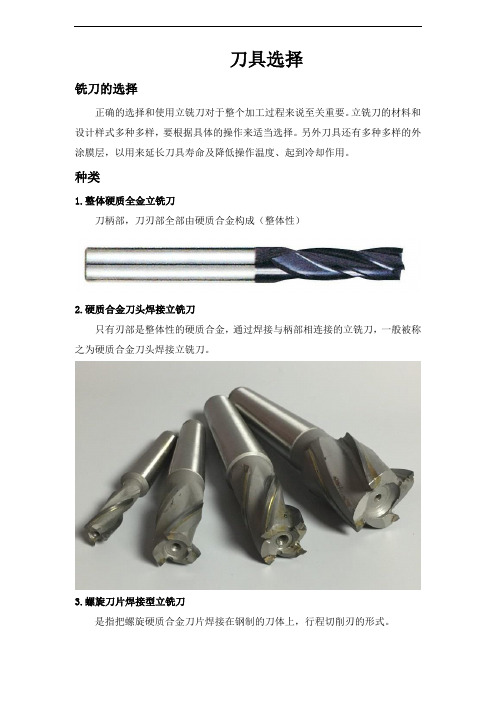
刀具选择铣刀的选择正确的选择和使用立铣刀对于整个加工过程来说至关重要。
立铣刀的材料和设计样式多种多样,要根据具体的操作来适当选择。
另外刀具还有多种多样的外涂膜层,以用来延长刀具寿命及降低操作温度、起到冷却作用。
种类1.整体硬质全金立铣刀刀柄部,刀刃部全部由硬质合金构成(整体性)2.硬质合金刀头焊接立铣刀只有刃部是整体性的硬质合金,通过焊接与柄部相连接的立铣刀,一般被称之为硬质合金刀头焊接立铣刀。
3.螺旋刀片焊接型立铣刀是指把螺旋硬质合金刀片焊接在钢制的刀体上,行程切削刃的形式。
4.可转位型立铣刀通过销子锁紧等方式装夹硬质合金刀片来使用的立铣刀为可转位型立铣刀。
特点等介绍1.螺旋角(1)螺旋方向:从立铣刀的正面看,容屑槽朝刀柄方向伸延时是向左倾的就叫左螺旋,向右倾的就叫右螺旋。
左螺旋右螺旋(2)当螺旋角很大时,刀刃很锋利,刀具的刚性很差,易卷刃、崩刃,从而影响刀具的使用寿命。
为了防止螺旋刃的卷刃和崩刃,通常沿刃口磨出一小平面或小弧面的倒棱。
(3)螺旋角的选取方法:对一般的粗铣、精铣,考虑到刀具的使用寿命,通常选用30左右的螺旋角。
加工切削阻力比较小的轻合金时,通常选用40左右的螺旋角。
2.立铣刀的刃数立铣刀的刚性和容屑槽的大小很重要的,一般刃数少的铣刀容屑槽大,排屑良好。
但另一方面截面积率减小,刚性降低。
因此切削时容易发生弯曲。
单刃刀 2刃 3刃4刃 5刃 6刃对铣侧面来说,因为切屑阻塞现象较小,不大考虑容屑槽的大小,而较重视刀具的刚性。
一般认为采用刃数多的刀具切削阻力变化小,刀具刚度大,不易弯曲变形,被加工面的表面质量刀。
3.楔角(1)圆周刃的前角过大时,虽然切削刃比较锋利,但刃口的强度小,在加工中已出现振动、卷刃和崩刀。
圆周刃的锋利度不好,切削阻力较大,排屑差,前面易磨损。
(2)圆周刃的后角过小时,虽不但会出现背切现象。
而且刀刃磨损快。
刀具寿命短;相反圆周刃后角过大,容易导致振动、卷刃和崩刀。
- 1、下载文档前请自行甄别文档内容的完整性,平台不提供额外的编辑、内容补充、找答案等附加服务。
- 2、"仅部分预览"的文档,不可在线预览部分如存在完整性等问题,可反馈申请退款(可完整预览的文档不适用该条件!)。
- 3、如文档侵犯您的权益,请联系客服反馈,我们会尽快为您处理(人工客服工作时间:9:00-18:30)。
模具型腔数控加工计算机辅助刀具选择和研究
引言
数控加工中包括刀具轨迹的产生和刀具选择两个关键问题。
前一问题在过去的20 年里得到了广泛而深入地研究,发展的许多算法已在商用CAD/ CAM 系统中得到应用。
目前大多数CAM 系统能够在用户输入相关参数后自动产生刀具轨迹。
比较而言,对以质量、效率为优化目标的刀具选择问题的研究还远未成熟,当前还没有商用CAM 系统能够提供刀具优选的决策支持工具,因而难以实现CAD/ CAM 的自动有机集成。
刀具选择通常包括刀具类型和刀具尺寸。
一般来说,适合一个加工对象的刀具通常有多种,一种刀具又可完成不同的加工任务,所以仅考虑满足基本加工要求的刀具选择是较容易的,尤其对孔、槽等典型几何特征。
但实际上,刀具选择通常和一定的优化目标相联系,如最大切削效率、最少加工时间、最低加工成本、最长使用寿命等,因此刀具选择又是一个复杂的优化问题。
比如模具型腔类零件,由于几何形状复杂(通常包含自由曲面及岛) ,影响刀具选择的几何约束在CAD 模型中不能显式表示,需要设计相应的算法进行提取,因而选择合适的刀具规格及其刀具组合,以提高数控加工的效率与质量并非易事。
模具型腔一般用数控铣的加工方法,通常包括粗加工、半精加工、精加工等工序。
粗加工的原则就是尽最大可能高效率地去除多余的金属,因而希望选择大尺寸的刀具,但刀具尺寸过大,可能导致未加工体积的增多;半精加工的任务主要是去除粗加工遗留下来的台阶;精加工则主要保证零件的尺寸及表面质量。
考虑到目前完全由计算机进行自动选刀还存在一定困难,因而在我们开发的计算机辅助刀具选择(Computer Aided Tool Selection ,CATS)系统中,立足于给用户提供一个辅助决策工具,即粗加工、半精加工、精加工等,真正的决策权仍留给用户,以充分发挥计算机和人的优势。
1 系统基本结构
CATS系统的输入为CAD模型,输出为刀具类型、刀具规格、铣削深度、进给量、主轴转速(切削速度) 和加工时间等六个参数(如图1) ,包括刀具类型选择辅助决策工具、粗加工刀具选择辅助决策工具、半精加工刀具选择辅助决策工具及精加工刀具选择辅助决策工具等
鉴于粗加工在型腔加工中的重要地位(通常为精加工时间的5~10 倍) ,粗加工时系统具有刀具自动优化组合的功能,以提高整体加工的效率。
除了上述决策工具外,系统还具有查看刀具详细规范、根据刀具类型和尺寸推荐加工参数及评估加工时间等功能,最后生成总的刀具选择结果报表。
系统所有的刀具数据及知识均由后台数据库做支
持。
2 关键技术及算法
2.1 刀具类型选择
根据模具型腔数控加工实践,型腔铣加工的刀具一般分为平头铣刀、圆角铣刀及球头铣刀三种。
设刀具直径为D,圆角半径为r ,当r=0 时为平头铣刀,0<R 刀具又可分为整体式和镶片式。
对于镶片式,关键是选取刀片的材质,刀片材质的选择取决于三个要素:被加工工件的材料、机床夹具的稳定性以及刀具的悬臂状态。
系统将被加工工件的材料分为钢、不锈钢、铸铁、有色金属、难切削材料和硬材料等六组。
机床夹具的稳定性分为很好、好、不足三个等级。
刀具悬臂分为短悬臂和长悬臂两种,系统根据具体情况自动推理出刀片材质,决策知识来源于
WALTER刀具手册,系统由用户首先交互选择刀具类型。
对镶片式刀具,基于规则自动推理出合适的刀片材质。
例如,如果被加工工件的材料为“钢”,机床夹具的稳定性为很好,刀具悬臂为短悬臂,则刀片材质应为WAP25 。
粗加工刀具组合优化
型腔粗加工的目的就是最大化地去除多余的金属,通常使用平头铣刀,采取层切的方法。
因此,3D模具型腔的粗加工过程,实际上就是对一系列2.5D模具型腔的加工。
刀具优化的目的就是要寻找一组刀具组合,使其能够以最高的效率切除最多的金属。
刀具组合优化的基本方法如下:
A. 以一定的步长做一组垂直于进刀方向的搜索平面与型腔实体相交,形成若干搜索层。
B. 求出截交轮廓。
C. 计算内外环之间或岛与岛之间的关键距离,即影响刀具选择的几何约束.
D. 根据合并原则(相邻关键距离相差小于给定阈值) 对搜索层进行合并,确定加工平面和可行刀具集,形成加工层。
E. 确定每一加工层使用的刀具,即型腔加工的刀具组合。
F. 根据刀具推荐的加工参数(切削速度、铣削深度和进给速度) ,计算材料去除率。
G. 根据加工层实际切除的体积,计算每一加工层的加工时间。
H. 计算型腔总的加工时间和残余体积。
I. 对该组刀具组合的总体加工效率进行评估。
J. 重复a~i,直至求出最优的刀具组合。
如以时间为目标,即要求以整个型腔的加工时间t 最短来优化刀具组合。
2.2半精加工刀具选择
半精加工的主要目的是去除粗加工残留下的台阶状轮廓。
为完全去除台阶,铣削深度必须大于每一台阶到零件表面的距离x。
其算法步骤如下:
步骤1 由零件实体模型获得两个相邻截面的表面积以及相应的轮廓长度;
步骤2 计算平均轮廓长度;
步骤3 计算台阶宽度;
步骤4 计算台阶拐角到零件表面的法向距离x ;
步骤5 重复步骤1~步骤4 ,决定每一台阶的铣削深度;
步骤6 计算刀具直径D,按经验D=x/0.6或根据刀具手册推荐;
步骤7 选择铣削深度大于x 的最小刀具。
2.3 精加工刀具选择
精加工刀具选择的基本原则是:刀具半径尺寸R 小于零件表面最小的曲率半径r,一般取R=(0.8~0.9)r。
其算法步骤如下:
步骤1: 从零件实体模型计算最小曲率半径;
步骤2: 从刀具库中检索出刀具半径小于计算所得的曲率半径的所有刀具;
步骤3: 选出满足上述要求的最大刀具;
步骤4: 如果所有刀具大于最小的曲率半径,选择最小的作为推荐刀具。
4 小结与讨论
模具型腔加工的工艺规划通常需要很高的技术与经验,准备NC 数据的时间几乎和加工时间一样多。
因此,自动产生型腔加工的工艺计划及NC加工指令的需求就显得愈加迫切。
本文系统研究了模具型腔工艺规划中的刀具选择问题,提出了模具型腔粗加工、半精加工、精加工刀具选择的原则和方法,构造了相应的实现算法,并在UG/OPEN API环境下进行了初步编程实现,开发了CATS原型系统。
在刀具类型和规格确定的基础上,系统还可根据刀具手册推荐加工参数(切削速度、铣削深度、进给量等) ,对相应的加工时间进行评估。
其最终目的是真正实现CAD/CAM的集成,继而通过后处理产生数控加工指令。
目前CATS系统的界面还是独立于UG的CAM界面,CATS的决策结果还需要用户重新输入到CAM。
需要指出的是,要提高模具型腔的总体加工效率,需要从粗加工、半精加工、精加工的整体上考虑,进行多目标组合优化,这将是我们下一步要进行的工作。