单管内排屑深孔钻削技术
一种改进的内排屑深孔钻头

(4)除 外 齿 与 外 缘 一 侧 为 尖 角 外 , 其 余 刀
5
中间尖齿
15°
146°
中心齿
减震块
5°
5°
6°
外刀齿
图 3 改进的深孔钻头 凿 岩 机 械 气 动 工 具 ,2009(1)
齿都进行了倒角, 同时带有 6°~12°的侧后角, 消除了尖角,增大了刀齿的散热体积,同时也 增强了刀齿强度,不易崩刃,有利于提高钻头 的耐用度。
21
明,f =140°~146°之间时, 切屑流出方向近似与 钻头轴线平行,有利排屑。
钻头上也有两个硬质合金导向、 支承块。 几何参数是:
2准=145±5°,Kr1≈73°,Kr2=112°,e= 0.1d, α0 =8° ~12° ,λt2 =5° ~8° ,bα1 =1 ~1.5mm,br1 = 1.2 ~2mm,h =0.4 ~0.5mm,R =1 ±0.1mm,τ =2° ~ 6°,外刃中间齿突前量为(1~2)f。
刃上方与之成 90°的位置(见图 3)。在正常切削
时,切削合力指向两导向块之间,使导向块紧
贴己加工孔壁,起导向作用,而减 振块位于后
端, 刃齿有倒锥使与己加工孔壁有一定的间
隙,不起作用;当钻削力失去平衡发生振动,产
生偏离导向块方向的位移时, 减振块才起作
用,可以减振、消振,保护刀刃和提高加工孔的
形状精度。
(2)改中间齿为尖齿。 为了提高钻削稳定
凿 岩 机 械 气 动 工 具 ,2009(1)
性,我们将中间齿设计为尖齿(见图 1)。 切削
时,中间齿在孔底形成环形凸筋,与内折线刃
在孔底形成的反锥(见图 2)同时起到定心、稳
定钻削的作用。
(3)增加减振块。 普通深孔钻大都采用两
深通孔加工方法
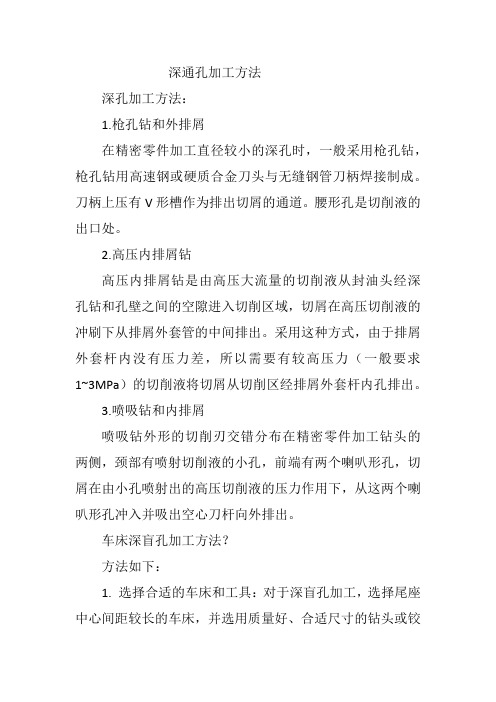
深通孔加工方法深孔加工方法:1.枪孔钻和外排屑在精密零件加工直径较小的深孔时,一般采用枪孔钻,枪孔钻用高速钢或硬质合金刀头与无缝钢管刀柄焊接制成。
刀柄上压有V形槽作为排出切屑的通道。
腰形孔是切削液的出口处。
2.高压内排屑钻高压内排屑钻是由高压大流量的切削液从封油头经深孔钻和孔壁之间的空隙进入切削区域,切屑在高压切削液的冲刷下从排屑外套管的中间排出。
采用这种方式,由于排屑外套杆内没有压力差,所以需要有较高压力(一般要求1~3MPa)的切削液将切屑从切削区经排屑外套杆内孔排出。
3.喷吸钻和内排屑喷吸钻外形的切削刃交错分布在精密零件加工钻头的两侧,颈部有喷射切削液的小孔,前端有两个喇叭形孔,切屑在由小孔喷射出的高压切削液的压力作用下,从这两个喇叭形孔冲入并吸出空心刀杆向外排出。
车床深盲孔加工方法?方法如下:1. 选择合适的车床和工具:对于深盲孔加工,选择尾座中心间距较长的车床,并选用质量好、合适尺寸的钻头或铰2. 制定加工方案:根据工件的形状和尺寸、材料以及待加工孔的位置和深度制定加工方案。
3. 用钻头或铰刀钻孔:在车床上,用钻头或铰刀逐步钻孔,每钻到一定深度,要及时切断切屑,保持孔内干净,避免堵塞。
4. 用扩孔器扩大孔径:钻完深孔后,用扩孔器逐步扩大孔径,使其达到要求。
5. 修整孔面:对于要求较高的工件,需使用磨头修整孔面,使其光洁度和精度达到要求。
6. 清洁孔内:在加工完成后,要用空气枪或其他工具将孔内的切屑、污物彻底清洁干净。
7. 检查孔的质量:最后,检查孔的尺寸、形状、表面质量和内部质量等,确保达到要求。
如盲孔底钻头角度存在可以的话,先用13.8的钻头打孔深50毫米(钻头尖除外),再有Φ14H7铰刀(上偏差为+0.015 下偏差为+0.007 单位均为mm,铰刀前面导向刃磨去)铰孔至尺寸。
如果盲孔是平底的话13.8钻头钻好孔后,再磨平底钻底面到50毫米深,用Φ14H7铰刀铰至尺寸,步骤如下:1.先在车床上将工件夹紧,确定好孔的位置和深度。
单管内排屑深孔钻削技术

STS钻由
φ18.4~65mm为焊接 刀片结构, φ65~180mm的大直 径钻头采取机夹可转 位刀片的组装结构, 分别见图2.4(a)和 (b)。
焊接刀片型BTA钻原来为可重磨式,其切削刀 片和导条较长。但由于断屑台的刃磨涉及工件材质、 进给量等复杂因素,加上刀具为错齿结构,中间齿 的切削刃与其他齿的切削刃不在一个圆锥面上,因 而一般企业用户基本不具备重磨条件,不得不在一 次使用后尚可重磨的情况下将钻头报废。20世纪80 年代后,这种焊片式钻头一律改为短刀齿的一次性 使用(Disposible)产品。 BTA扩钻由BTA实体钻所派生,其排屑方法与 实体钻相同。BTA扩钻的主要用途是对工件已有的 粗孔(如无缝管孔、铸孔等)进行加工,也可对已 钻出的较小孔进行扩大。
但是,这些实验记录与生产实践中的应用效果并不 能相提并论。要求操作人员根据不同的工件材质、 钻头直径、进给量大小相应地控制断屑台尺寸参数 和分屑刃参数,并且在切削刃重磨时,保持断屑台 的参数不变,这在实践中几乎是行不通的。基于上 述原因,当时欧洲的跨国研究机构“钻镗孔与套料 协会”(Boring and Trepanning Association,简 称BTA)对这种内排屑钻头加以总结后,推出了由 双出屑口单管内排屑深孔钻和扩孔钻、套料钻三种 内排屑深孔刀具组成的BTA刀具系列。20世纪60年 代后,BTA刀具基本上由瑞典 SANDVIK/COROMANT公司独家生产,单出屑口 的实体钻结构一律由双出屑口结构取代,又称为 STS(single-tube system,单管钻)钻头。
输油器后端与钻杆的密封也很重要。除了保 证切削液不泄露这一基本功能以外,密封件 实际上还起到钻杆辅助支承的作用。密封件 因磨损而必须及时调节或更换;当更换不同 直径的钻杆时,需相应地换装不同直径的密 封件。因此,换装密封件是否方便快速,将 直接影响机床的工作效率。 装配好的输油器,其钻套中心线应与机床主 轴的回转中心严格保持一致。
深孔钻削应用指南

深孔钻削应用指南深孔钻削可采用多种机床安装方式:工件旋转,刀具做进给运动;工件不动,刀具旋转又做进给运动;工件旋转,刀具做反向旋转又做进给运动。
具体采用何种方式则依据工件特征及所加工孔的情况而定。
目前常用的深孔钻削加工系统有枪钻系统、BTA单管钻系统、喷吸钻系统。
它们代表着先进、高效的孔加工技术,通过一次走刀就可以获得精密的加工效果,加工出来的孔位置准确,尺寸精度好;直线度、同轴度高,并且有很高的表面光洁度和重复性。
能够方便的加工各种形式的深孔,对于特殊形式的深孔,比如交叉孔、斜孔、盲孔及平底盲孔等也能很好的解决。
上述深孔加工系统可达到加工精度孔径尺寸:lT6~lT11表面粗糙度: Ra0.2~ Ra6.3um直线度: <0.3mm/1000mm偏斜度:≤1mm/1000mm下图为最常用的两种深孔钻削加工刀具:枪钻和BTA单管钻深孔钻削的最主要特征1.极高的材料去除率;在正常加工条件下钻削深孔均一次贯穿,无需中途退刀;能获得极佳的孔径尺寸精度、直线度、表面粗糙度,并能加工各种形式的深孔,如交叉孔,盲孔,斜孔等;加工质量的高度一致性。
当钻削深孔时,整个切削过程对刀具、机床及其相关设备有着极高的要求。
2.深孔加工是处于封闭或半封闭的状态下,故不能直接观察到刀具的切削情况。
目前只能凭经验,通过同声音、看切屑、观察机床负荷及压力表、触摸震动等外在现象来判断切削过程是否正常。
3.切削热不易传散。
一半切削过程中有80%的切削热被切屑带走,而深孔钻削只有40%,刀具占切屑热得比例较大,扩散迟、易过热,刀口温度可达600℃,必须采取强制有效地冷却方式。
4.切屑不易排出。
由于孔深,切屑经过的路线长,容易发生堵塞,造成钻头崩刃。
因此,切屑的长短和形状要加以控制,并要进行强制性排屑。
5.工艺系统刚性差。
因受孔径尺寸限制,孔的长径比较大,钻杆细而长,刚性差,易产生震动,钻孔易走偏,因而支撑导向极为重要。
这点在枪钻机床中更为突出。
中大孔径内排屑深孔钻削系统设计
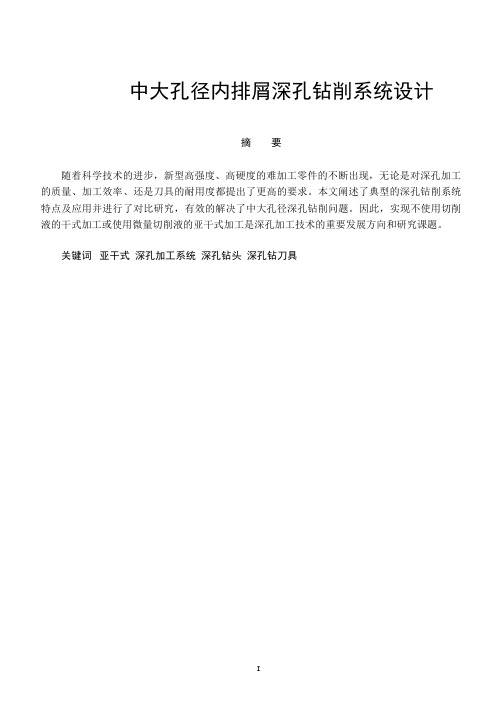
根据深孔钻削加工的特点,采用完全干式切削(即完全不使用切削液)的加工方式在实际生产中一般很难实现。因为深孔钻削加工不同于普通的车削、铣削加工,它是在封闭状况下进行,单位时间所产生的切削热量大,排屑通道长,切屑和切削热不易及时排出;此外,刀具在深孔加工中是依靠导向块完成定心和导向作用,导向块与孔壁之间会因长时间接触挤压而产生较大摩擦,而切削液(切削油)可以在导向块与孔壁之间形成一层油膜,起到润滑和减摩作用,如无油膜,导向块将很快被磨损和撕裂,从而引起切削振动或打刀。因此,选择用少量切削液的亚干式切削方式比较适合深孔加工的实际情况。
由于亚干式深孔加工系统采用雾化切削液润滑、冷却刀具,用压缩空气进行排屑降温,既克服了传统深孔加工中大量循环使用切削液所带来的诸多弊病,大大减少了切削液使用量,又确保了导向块与内孔表面之间、刀具前后刀面与切屑之间的切削液润滑层,同时切削液在雾化状态下吸热充分、润滑均匀,能更好地发挥作用;使用连续的压缩空气排屑既可增大排屑空间(相对于使用高压油),又能迅速将切屑从切削区吹出,缩短了切屑传热时间,并可将部分热量直接带出,降低了切削区温度。
亚干式深孔加工采用压缩空气排屑和雾化切削液冷却,因此切屑形状不能太宽太长。为防止切屑堵塞,最好是形成细小的“C”型切屑;为使切屑更快脱离刀面,刀具与切屑的接触面不宜过大,为此可采用分屑刃或强制断屑措施。
针对以上几点要求,我们对刀具进行了结构分析和优化设计,使其满足系统的加工要求。
3.2.刀具结构的选取及优化设计
中大孔径内排屑深孔钻削系统设计
摘 要
随着科学技术的进步,新型高强度、高硬度的难加工零件的不断出现,无论是对深孔加工的质量、加工效率、还是刀具的耐用度都提出了更高的要求。本文阐述了典型的深孔钻削系统特点及应用并进行了对比研究,有效的解决了中大孔径深孔钻削问题。因此,实现不使用切削液的干式加工或使用微量切削液的亚干式加工是深孔加工技术的重要发展方向和研究课题。
组合机床深孔钻削及工艺参数选择

( 0 05~ 0 12) 0 06
( 50~ 70) 50
( 0 05~ 0 12) 0 07
( 55~ 75) 55
( 0 09~ 0 15) 0 08
( 60~ 80) 60
( 0 05~ 0 17) 01
( 30~ 50) 120
( 0 02~ 0 1) 0 06
( 35~ 55) 130
( 0 02~ 0 1) 0 07
表 6 三菱
! ∀ 推荐的双刃枪钻的切削用量
工件材料
抗拉强度 N/ mm2
6~ 8
v
f
8~ 10
v
f
10~ 12
v
f
12~ 15
v
f
15 以上
v
f
普通铸铁 球墨铸铁
铝合金
350 450 500~ 800 -
70
0 06
75
0 08
80
01
85
0 12
90
0 14
( 60~ 80) 50
( 0 02~ 0 1) 0 06
52
精度制造, 导套则取为 10 003+0 0. 005mm。当导向套 磨损超过 0 02mm 时, 就应更换。导向套一般采用淬 硬工具钢制造, 更好的是用硬质合金导向套。导向套 固定在导向装置支架上, 其后应有足够的空间排除带 有切屑的脏切削液, 导向架后端则有一个防切削液向 后冲的防护套。调整机床时, 主轴与导向套同轴度应 小于 0 02mm。对于特长的钻杆, 还应在主轴与导向 装置之间增设中心支承装置, 以防钻杆弯曲。
0. 8f
( 6~ 8) d ( 0. 6~ 0. 65) v
0. 8f
6种常见的深孔加工技术简介

六种常用的深孔加工系统什么是深孔加工?所谓深孔,就是孔的长度与孔的直径比大于10的孔。
而一般的深孔多数情况下深径比L/d≥100。
如油缸孔、轴的轴向油孔,空心主轴孔和液压阀孔等等。
这些孔中,有的要求加工精度和表面质量较高,而且有的被加工材料的切削加工性较差,经常成为生产中一大困难。
对于深孔加工,你能想到哪些方法呢?1、传统钻削深孔加工起源于美国人发明的麻花钻。
这种钻头的结构相对简单,切削液导入方便,便于制造出不同直径和长度的钻头以适用于加工不同尺寸的孔。
2、枪钻深孔枪管钻最初是应用于枪管(俗称深孔管,枪管并非用无缝精密管制作,精密管制作工艺根本上无法满足精度要求)制造业因此得名枪钻。
随着科技的不断发展和深孔加工系统制造商的不懈努力,深孔加工已经成为一种方便高效的加工方式。
并被广泛应用于如:汽车工业、航天工业、结构建筑工业、医疗器材工业、模具/刀具/治具工业及油压、空压工业等领域。
枪钻是理想的深孔加工解决方案,采用枪钻可以获得精密的加工效果,加工出来的孔位置精确,直线度、同轴度高,并且有很高的表面光洁度和重复性。
能够方便的加工各种形式的深孔,对于特殊深孔,比如交叉孔,盲孔及平底盲孔等也能很好的解决。
↑↑枪钻系统组成↑↑↑↑枪钻钻头↑↑视频资料:3、BTA系统国际孔加工协会发明的一种内排屑深孔钻,BTA 系统中钻头与钻杆为中空圆柱体,提高了刀具刚性和快速拆装问题。
其工作原理如图所示,切削液经加压从入口进入授油器后通过钻杆与孔壁形成的密封环状空间,流向切削部分进行冷却润滑,并将切屑压入钻头上的出屑口,经钻杆内腔从出口排出。
BTA 系统主要适用于直径φ>12mm 的深孔加工。
↑↑BAT系统组成↑↑↑↑BAT钻头↑↑4、喷吸钻系统喷吸钻系统是瑞典Sandvik 公司利用流体力学的喷吸效应原理发明的双管内排屑深孔钻削方法。
其喷吸钻系统采用双层管刀杆,切削液经加压后从入口进入,其中2/3的切削液进入内、外钻杆间的环形空间,流向切削部分进行冷却和润滑,并将切屑推入钻杆内腔;其余1/3 的切削液,从内钻杆上月牙状喷嘴高速喷入内钻杆,在内钻杆内腔形成一个低压区,对携带切屑的切削液产生抽吸作用,在喷、吸双重作用下,促使切屑快速从出口排出。
深孔钻断排屑机理与变切深加工数控宏程序研究
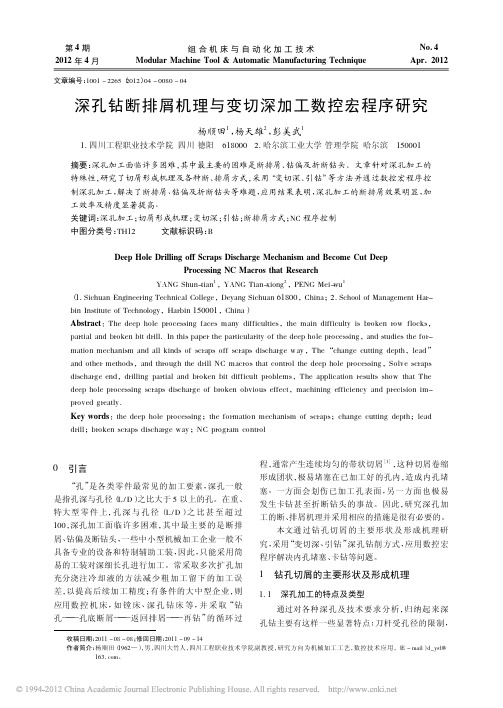
Deep Hole Drilling off Scraps Discharge Mechanism and Become Cut Deep Processing NC Macros that Research YANG Shuntian1 ,YANG Tianxiong2 ,PENG Meiwu1 ( 1. Sichuan Engineering Technical College,Deyang Sichuan 61800 ,China; 2. School of Management Harbin Institute of Technology,Harbin 150001 ,China) Abstract: The deep hole processing faces many difficulties,the main difficulty is broken row flocks, partial and broken bit drill. In this paper the particularity of the deep hole processing , and studies the formation mechanism and all kinds of scraps off scraps discharge w ay ,The “change cutting depth,lead ” and other methods,and through the drill NC macros that control the deep hole processing ,Solve scraps discharge end,drilling partial and broken bit difficult problems,The application results show that The deep hole processing scraps discharge of broken obvious effect,machining efficiency and precision improved greatly. Key words: the deep hole processing ; the formation mechanism of scraps; change cutting depth; lead drill; broken scraps discharge w ay ; NC program control