设计失效模式及后果分析程序
FMEA潜在失效模式及后果分析管理程序
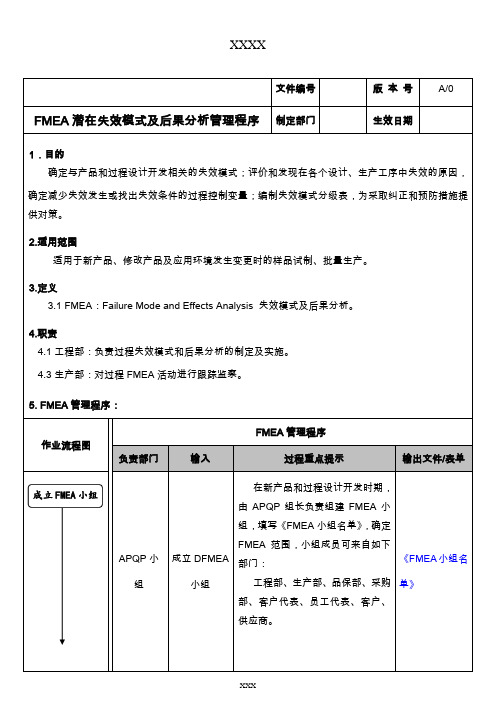
XXX
XXXX
文件编号
版本号
A/0
FMEA 潜在失效模式及后果分析管理程序 制定部门
生效日期
FMEA 分析
FMEA 分析小组应当建立一个 过程流程图,识别每步操作相关的 产品/过程特性,结合 DFMEA,图 样和设计记录,内外部不符合历史, 质量与可靠性历史等信息来源制定 《FMEA》。
PFMEA 分析
评定准则可参考 PFMEA 严重度 评定准则表:
FMEA 严重度评定准则表参照《FMEA 管理手册》
FMEA 分析
14.分类:作为识别与确定特殊 特性的重要工具,小组应在PFMEA 分析中识别并确定过程特殊特性, 并以《APQP管理程序》规定的符号
XXX
XXXX
文件编号
FMEA 潜在失效模式及后果分析管理程序 制定部门
XXX
XXXX
文件编号
版本号
A/0
FMEA 潜在失效模式及后果分析管理程序 制定部门
生效日期
描述失效的影响,尽可能采用表 达顾客关注和感受的词汇。如:操 作者眼睛受伤害,零件破损将机器 损坏,外观不良,无法装配,等等。 对最终顾客的影响应使用与产品或 系统的性能有关的术语来描述,例 如噪声、振动、工作不正常、停止 工作、工作不稳定、操作力过大、 异味、性能衰退、观外不良、褪色, 等等。
式是指:过程不能达到过程功能要 求或过程设计意图的问题的表现形 式。一般情况下,它是指按规定的 操作规范进行操作时的潜在的失效 问题,但由于过程设计中对技术与 能力考虑不足而造成的失效,或容 易产生误操作的问题也是潜在失效 模式考虑的范围。潜在失效模式应 当用专业的技术术语描述,不必描 述成顾客能够注意到的现象。在进 行 FMEA 时应当假定即将接收的零 件/材料是正确的。
失效模式及后果分析程序 - 新版2019(DFMEA)

设计失效模式及后果分析程序页码:第1页,共9页文件修订履历修订修订内容简述编制人生效日期1 推行ISO9001:2008,ISO14001:2004,新制订2014.01.102 组织架构发生变化2014.08.263 按ISO9001:2015、ISO14001:2015、IATF16949:2016升级2017.12.304 按照AIAG&VDA FMEA修改2019.08.31审批栏受控印章栏编制人:审核人:批准人:分派一栏表(用“√”注明分发部门),分发部门在签收栏签收:分发部门代码发放份数分发部门代码发放份数总经理财务部市场部行政部采购部工程部工艺部品质部生产部维修部计划部仓库设计失效模式及后果分析程序页码:第2页,共9页1.0目的在产品设计阶段,预先发现、评价产品可能潜在的失效与后果,及早找出能够避免或减少这些潜在失效发生的措施,并将此过程文件化,为以后的设计提供经验与参考。
2.0范围适用于产品设计中的设计失效模式及后果分析。
3.0职责3.1多方论证小组:负责制订DFMEA的各项内容及相关改进措施,建立纠正措施优先体系;当有新的失效模式出现时及时更改DFMEA。
3.2工艺部:主导多方论证小组分析并制订所有潜在失效模式及后果。
3.3各部门:参与DFMEA的制订和评估,相关纠正和预防措施的执行。
4.0定义4.1DFMEA:(Design Failure Mode& Effects Analysis)设计失效模式及后果分析.4.2顾客:顾客对DFMEA而言通常指“终端顾客”或“使用者”,但顾客也可能是法律法规要求4.3MSA:Measurement System Analysis(测量系统分析)包括准确性、线性、重复性、再现性、稳定性。
5.0流程无6.0内容6.1DFMEA制订说明:6.1.1工程部主导成立多方论证小组(即APQP策划小组);并确定DFMEA的实施项目。
多方论证小组根据客户的要求和生产加工情况,在APQP总进度中明确DFMEA项目的实施进度要求。
失效模式和后果分析

失效模式和后果分析失效模式和后果分析(Failure Mode and Effects Analysis,FMEA)是一种系统性的风险评估工具,用于识别和评估系统、设计、过程或设备中可能发生的失效模式及其潜在后果。
它通过对潜在风险进行评估和控制,帮助组织预防和减少质量问题和事故的发生。
FMEA通常由跨职能团队进行,在项目的早期阶段实施,并随着项目进展进行更新和完善。
它通常包括以下步骤:1.确定风险:确定系统、设计、过程或设备中的所有可能的失效模式,并将其列出。
这些失效模式可以是机械失效、电气故障、材料错误等。
2.评估风险:对每个失效模式进行评估,包括失效发生的可能性、严重性和检测能力。
通常使用1到10的评分系统,其中1表示较低的风险,而10表示较高的风险。
3.优先处理:根据评估的结果,确定需要优先处理的失效模式。
通常优先处理那些评分较高的失效模式,因为它们可能会对安全、质量或生产能力产生较大的影响。
4.实施修复措施:为每个优先处理的失效模式制定修复措施。
修复措施可以包括改进设计、更换零件、增加检测或监控程序等。
5.重新评估风险:在实施修复措施后,重新评估每个失效模式的风险,以确定修复措施的有效性。
FMEA的主要目标是识别和降低风险,提高系统或过程的可靠性和质量。
通过在项目早期识别和处理潜在的风险,可以减少产品或过程失效带来的成本和风险。
FMEA的应用范围广泛,包括汽车、电子、医疗器械、航空航天、制药等行业。
在汽车行业中,FMEA被广泛用于对汽车设计和生产过程进行质量控制,以减少故障和事故的发生。
在制药行业中,FMEA用于识别和处理可能导致产品污染或不合格的因素。
FMEA的优势在于它的系统性和针对性。
它可以帮助组织集中精力和资源处理最重要的风险,并制定相应的修复措施。
此外,FMEA还可以促进跨职能团队的合作和沟通,以共同解决风险和问题。
然而,FMEA也有一些局限性。
首先,FMEA侧重于识别和处理已知的失效模式,而可能会忽视未知的或新的失效模式。
潜在失效模式后果分析FMEA控制程序
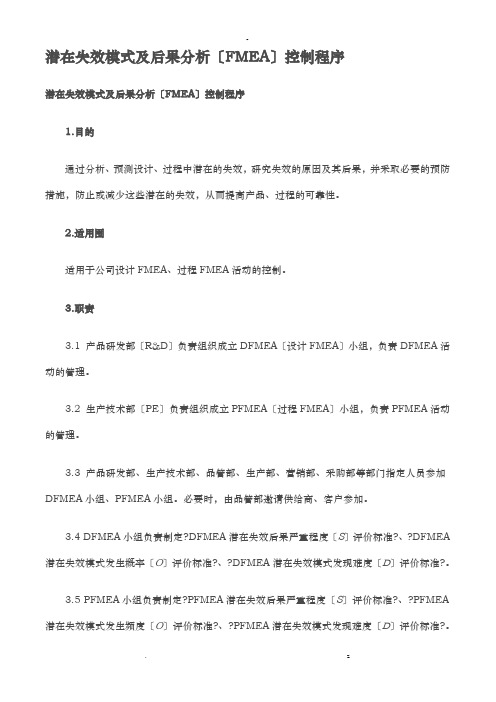
潜在失效模式及后果分析〔FMEA〕控制程序潜在失效模式及后果分析〔FMEA〕控制程序1.目的通过分析、预测设计、过程中潜在的失效,研究失效的原因及其后果,并采取必要的预防措施,防止或减少这些潜在的失效,从而提高产品、过程的可靠性。
2.适用围适用于公司设计FMEA、过程FMEA活动的控制。
3.职责3.1 产品研发部〔R&D〕负责组织成立DFMEA〔设计FMEA〕小组,负责DFMEA活动的管理。
3.2 生产技术部〔PE〕负责组织成立PFMEA〔过程FMEA〕小组,负责PFMEA活动的管理。
3.3 产品研发部、生产技术部、品管部、生产部、营销部、采购部等部门指定人员参加DFMEA小组、PFMEA小组。
必要时,由品管部邀请供给商、客户参加。
3.4 DFMEA小组负责制定?DFMEA潜在失效后果严重程度〔S〕评价标准?、?DFMEA 潜在失效模式发生概率〔O〕评价标准?、?DFMEA潜在失效模式发现难度〔D〕评价标准?。
3.5 PFMEA小组负责制定?PFMEA潜在失效后果严重程度〔S〕评价标准?、?PFMEA 潜在失效模式发生频度〔O〕评价标准?、?PFMEA潜在失效模式发现难度〔D〕评价标准?。
4.工作程序4.1 设计FMEA的开发实施DFMEA实施的时机.1 按APQP的方案进展DFMEA。
.2 在出现以下情况时,DFMEA小组应在产品零件图纸设计之前进展DFMEA活动:① 开发新产品/产品更改;② 产品应用的环境发生变化;③ 材料或零部件发生变化。
DFMEA实施前的准备工作① 产品研发部〔R&D〕牵头成立DFMEA〔设计FMEA〕小组,生产技术部、品管部、生产部、营销部、采购部等部门指定人员参加DFMEA小组,必要时,由品管部邀请供给商、客户参加。
② 在DFMEA活动实施前,DFMEA小组应制定出?DFMEA潜在失效后果严重程度〔S〕评价标准?、?DFMEA潜在失效模式发生概率〔O〕评价标准?、?DFMEA潜在失效模式发现难度〔D〕评价标准?。
失效模式及后果分析程序 - 新版2019(DFMEA)
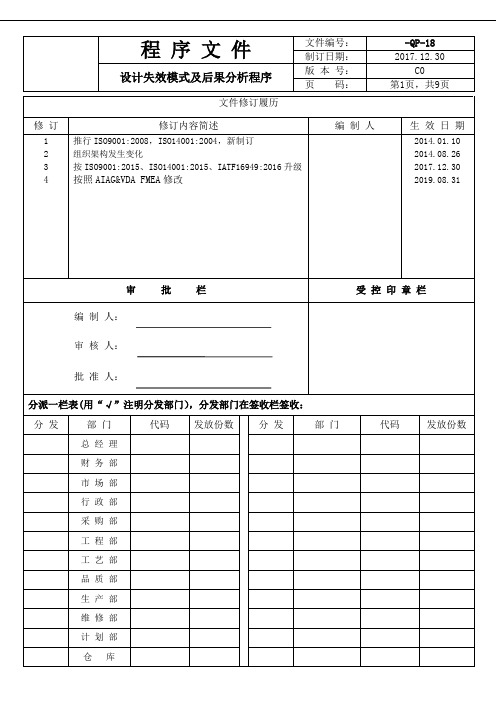
1.0目的在产品设计阶段,预先发现、评价产品可能潜在的失效与后果,及早找出能够避免或减少这些潜在失效发生的措施,并将此过程文件化,为以后的设计提供经验与参考。
2.0范围适用于产品设计中的设计失效模式及后果分析。
3.0职责3.1多方论证小组:负责制订DFMEA的各项内容及相关改进措施,建立纠正措施优先体系;当有新的失效模式出现时及时更改DFMEA。
3.2工艺部:主导多方论证小组分析并制订所有潜在失效模式及后果。
3.3各部门:参与DFMEA的制订和评估,相关纠正和预防措施的执行。
4.0定义4.1DFMEA:(Design Failure Mode& Effects Analysis)设计失效模式及后果分析.4.2顾客:顾客对DFMEA而言通常指“终端顾客”或“使用者”,但顾客也可能是法律法规要求4.3MSA:Measurement System Analysis(测量系统分析)包括准确性、线性、重复性、再现性、稳定性。
5.0流程无6.0内容6.1DFMEA制订说明:6.1.1工程部主导成立多方论证小组(即APQP策划小组);并确定DFMEA的实施项目。
多方论证小组根据客户的要求和生产加工情况,在APQP总进度中明确DFMEA项目的实施进度要求。
6.1.2多方论证小组组织品质部、工程部、生产部等相关部门的人员对整个生产流程进行评定。
6.1.3工程部针对过程失效模式和后果分析,确定相关过程的“严重度(S)”、“频度(O)”、“探测度(D)”,并通过S、O、D值的排列组合“措施优先级(AP)”,进行改进,编制DFMEA。
6.2在针对措施优先级(AP)行动时,需考虑以下因素:6.2.1严重度数高的(≥ 9)必须实施;6.2.2措施优先级(AP)为高(H)的优先实施;6.2.3措施优先级(AP)为中(M),但是易于实施,成本投入少的,优先实施。
6.2.4客户,项目小组,或者公司高层,在文件化的时候,提出采取改进措施的,给予实施;6.3工程部针对新产品、新材料、新技术应提交相关DFMEA资料。
潜在失效模式及后果分析管理程序
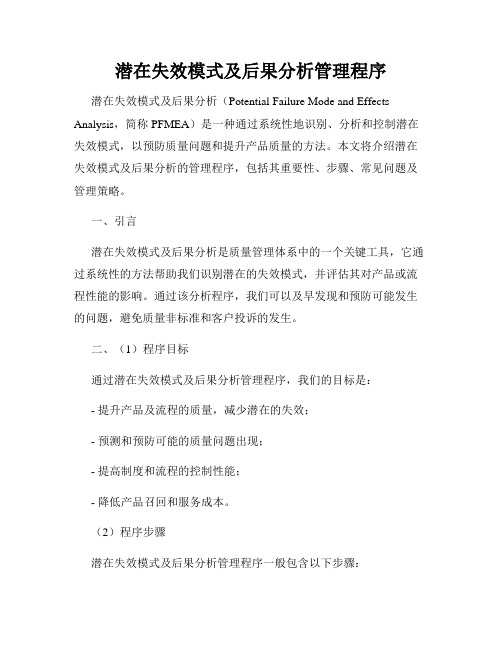
潜在失效模式及后果分析管理程序潜在失效模式及后果分析(Potential Failure Mode and Effects Analysis,简称PFMEA)是一种通过系统性地识别、分析和控制潜在失效模式,以预防质量问题和提升产品质量的方法。
本文将介绍潜在失效模式及后果分析的管理程序,包括其重要性、步骤、常见问题及管理策略。
一、引言潜在失效模式及后果分析是质量管理体系中的一个关键工具,它通过系统性的方法帮助我们识别潜在的失效模式,并评估其对产品或流程性能的影响。
通过该分析程序,我们可以及早发现和预防可能发生的问题,避免质量非标准和客户投诉的发生。
二、(1)程序目标通过潜在失效模式及后果分析管理程序,我们的目标是:- 提升产品及流程的质量,减少潜在的失效;- 预测和预防可能的质量问题出现;- 提高制度和流程的控制性能;- 降低产品召回和服务成本。
(2)程序步骤潜在失效模式及后果分析管理程序一般包含以下步骤:1. 确定分析对象:选择需要进行分析的产品或流程。
2. 制定团队:组建跨职能团队,包括设计师、工程师、生产经理及质量专家等。
3. 制定流程图:绘制分析对象的流程图,详细记录每个操作步骤。
4. 识别潜在失效模式:根据流程图,识别可能存在的失效模式,以及导致其发生的原因。
5. 评估失效后果:评估每种潜在失效模式对产品或流程性能的影响,确定其后果等级。
6. 制定预防控制措施:针对每种潜在失效模式,制定相应的预防控制措施,以降低失效发生的概率。
7. 实施控制措施:在生产或流程中实施预防控制措施。
8. 监控效果:对实施的控制措施进行监控,并评估其效果。
9. 持续改进:根据实施和监控结果,进行持续改进,提升产品或流程的质量和性能。
(3)常见问题及管理策略在潜在失效模式及后果分析管理过程中,常见的问题包括:- 遗漏潜在失效模式:由于团队成员的专业背景和经验不同,可能会遗漏一些潜在失效模式。
解决方案是广泛征求团队成员的意见,并进行多层次的复查。
设计失效模式和后果分析程序文件

Q/6DG13.707-2003
设计失效模式及后果分析程序
2003-04-20发布2003-05-01实施
发 布
设计失效模式及后果分析程序
1 目的:
确定与产品相关的设计潜在失效模式和潜在设计失效的机理/起因,评价设计失效对顾客的潜在影响,找出失效条件的设计控制变量和能够避免或减少这些潜在失效发生的措施;完善设计过程,确保顾客满意。
5职责:
项目小组负责设计失效模式及后果分析(DFMEA)的制定与管理。
6 工作流程和容:
工作流程
工作容说明
使用表单
6.1、项目组依《产品质量先期策划程序》在产品图纸/图样设计工作全部结束和完成之前, 从所要分析的系统、子系统或零部件的框图开始,对所有新产品、产品更改以及应用或环境有变化的沿用零件中的所有产品特性(特别是产品的特殊特性)进行DFMEA框图/环境极限条件、DFMEA流程图/风险评定表和DFMEA分析,并将其填写于“DFMEA框图/环境极限条件表”、“DFMEA流程图/风险评定表”和“潜在的失效模式和后果分析(设计FMEA)”表中,然后经项目组组长审查核准,以防止在产品设计和开发过程中发生缺陷。
6.2 设计失效模式及后果分析(PFMEA)和其流程图/风险评定表中的风险分析和评估应包括从单个零件的所有产品特性(即:产品的外观、尺寸、功能和性能等)到总成的所有产品特性 (即:产品的外观、尺寸、功能和性能等)。
6.3 设计FMEA分析应从所要分析的系统、子系统或零部件的DFMEA环境极限框图开始,DFMEA框图指示了信息、能源、力、流体等的流程。其目的是要明确向方框交付的容(输入),方框中完成的过程(功能)以及由方框所交付的容(输出)。DFMEA框图说明了分析中的各项目之间的主要关系,并建立了分析的逻辑顺序。在FMEA准备工作中所有的框图的复制件应伴随FMEA过程。
DFMEA设计潜在失效模式和后果分析管理程序

版本修改条款1.目的通过分析、预测设计、设计中潜在的失效,研究失效的原因及其后果,并采取必要的预防措施,避免或减少这些潜在的失效,从而提高产品、过程的可靠性。
2.适用范围适用于公司产品设计DFMEA活动的控制。
3.职责3.1研发中心(PD)负责组织成立DFMEA(设计FMEA)小组,负责DFMEA活动的管理。
工程部(PE)负责组织成立PFMEA(过程FMEA)小组,负责PFMEA活动的管理。
3.2研发中心、工艺、品质、生产部、业务部等部门指定人员参加DFMEA小组与PFMEA小组。
必要时,由品质邀请供应商、客户参加。
3.3DFMEA小组负责制定《DFMEA潜在失效后果严重程度(S)评价标准》、《DFMEA潜在失效模式发生频度(O)评价标准》、《DFMEA潜在失效模式发现难度(D)评价标准》。
并负责准备《DFMEA和PFMEA的措施优先级(AP)》。
4.工作程序4.1设计FMEA的开发实施4.1.1DFMEA实施的时机4.1.1.1按APQP的计划进行DFMEA。
4.1.1.2DFMEA在设计之前开始。
DFMEA小组应在提交设计计划批准前就要收集资料,对以往的项目、样品试产时出现的问题、以及客户在检测样品时所反馈的信息进行分析。
4.1.1.3发生设计更改时,应复查DFMEA文件,其应体现最新的设计(或工艺设计水平)及改善,采取最新的相应措施。
4.1.2PFMEA实施前的准备工作4.1.2.1研发中心牵头成立DFMEA(设计FMEA)小组,研发中心(R&D)、品质、生产部、物料部采购等部门指定人员参加DFMEA小组,必要时,由品质邀请供应商、客户参加。
4.1.2.2在DFMEA活动实施前,DFMEA小组应制定出《DFMEA潜在失效后果严重度(S)评价标准》、《DFMEA潜在失效模式频度(O)评价标准》、《DFMEA潜在失效模式探测度(D)评价标准》。
a)DFMEA小组根据FMEA手册参考标准,确定出本公司的实际示例。
- 1、下载文档前请自行甄别文档内容的完整性,平台不提供额外的编辑、内容补充、找答案等附加服务。
- 2、"仅部分预览"的文档,不可在线预览部分如存在完整性等问题,可反馈申请退款(可完整预览的文档不适用该条件!)。
- 3、如文档侵犯您的权益,请联系客服反馈,我们会尽快为您处理(人工客服工作时间:9:00-18:30)。
6.5在设计FMEA分析过程中被评价列为高RPN(RPN≧100)的项目和/或严重度≧8的项目,公司必须将其列为特殊特性;同时对所有被评价为高RPN(RPN≧100)的项目和/或严重度≧8的项目公司必须制定纠正/预防措施,对不可降低的高
DFMEA框图/环境极限条件表
DFMEA流程图/风险评重度≧8的项目必须附有明确的探测方法。
6.6所有的特殊特性均需在设计失效模式与后果分析(DFMEA)中加以说明,并将特殊特性的符号或记号在设计失效模式与后果分析(DFMEA)中进行明确标识;
6.7进行设计失效模式及后果分析(DFMEA)可采用QS-9000质量体系标准之参考手册《潜在的失效模式及后果分析》中规定的格式---“潜在的失效模式及后果分析表(设计FMEA)”进行(如顾客有特殊要求时则依顾客规定的表单进行)。
4术语和定义:
DFMEA:Design Failure Mode and Effects Analysis(设计失效模式及后果分析)英文简称。
失效:在规定条件下(环境、操作、时间),不能完成既定功能或产品参数值和不能维持在规定的上下限之间,以及在工作范围内导致零组件的破裂卡死等损坏现象。
严重度(S):指一给定失效模式最严重的影响后果的级别。严重度是单一的FMEA范围内的相对定级结果。
5职责:
项目小组负责设计失效模式及后果分析(DFMEA)的制定与管理。
6工作流程和内容:
工作流程
工作内容说明
使用表单
6.1、项目组依《产品质量先期策划程序》在产品图纸/图样设计工作全部结束和完成之前,从所要分析的系统、子系统或零部件的框图开始,对所有新产品、产品更改以及应用或环境有变化的沿用零件中的所有产品特性(特别是产品的特殊特性)进行DFMEA框图/环境极限条件、DFMEA流程图/风险评定表和DFMEA分析,并将其填写于“DFMEA框图/环境极限条件表”、“DFMEA流程图/风险评定表”和“潜在的失效模式和后果分析(设计FMEA)”表中,然后经项目组组长审查核准,以防止在产品设计和开发过程中发生缺陷。
2范围:
凡公司所有新产品、产品更改以及应用或环境有变化的沿用零件(包括:产品交付给顾客后其之抱怨(投诉)和/或退货的产品)均适用之。
3引用文件:
Q/6DG13.401-2003《文件和资料控制程序》
Q/6DG13.402-2003《质量记录控制程序》
Q/6DG13.701-2003《产品质量先期策划程序》
频度(O):指某一特定的失效起因/机理在设计寿命内出现的可能性。
探测度(D):指与设计控制中所列的最佳探测控制相关联的定级数。探测度是一个在某一FMEA范围内的相对级别。
风险优先数(RPN):指严重度数(S)和频度数(O)及不易探测度数(D)三项数字之乘积。
顾客:不仅仅是“最终使用者”,并且包括负责整车设计或更高一层总成设计的工程师们/设计组,以及在负责生产、装配和售后服务活动的生产/工艺工程师们。
6.8在正式进行图纸设计之前,如顾客有要求时,设计失效模式及后果分析(DFMEA)必须提交顾客评审和批准。
6.9设计失效模式及后果分析表(DFMEA)的栏目填写说明:
1)、DFMEA编号:
填入DFMEA文件的编号,以便查询。
设计FMEA的编号原则: DFMEA零(组)件图号
例如: DFMEA QKZ7C-010
6.1.3设计FMEA不依靠过程控制来克服中潜在的设计缺陷,但是它的确要考虑制造/装配过程中的技术/体力的限制(例如:必要的拔模—斜度;表面处理的限制;装配空间/工具可接近性;钢材淬硬性的限制;公差/过程能力/性能等)。
6.1.3.1设计FMEA还应考虑产品维护(服务)及回收的技术/体力的限制(如:工具的可接近性;诊断/指南能力;材料分类符号—用于回收等)。
有限公司企业标准
Q/6DG13.707-2003
设计失效模式及后果分析程序
2003-04-20发布2003-05-01实施
有限公司发布
设计失效模式及后果分析程序
1目的:
确定与产品相关的设计潜在失效模式和潜在设计失效的机理/起因,评价设计失效对顾客的潜在影响,找出失效条件的设计控制变量和能够避免或减少这些潜在失效发生的措施;完善设计过程,确保顾客满意。
6.4设计失效模式及后果分析(DFMEA)应从整个产品设计过程中的流程图/风险评定开始,流程图应确定与每个系统、子系统或零部件有关的产品特性参数,并分析产品在设计过程中的每一个步骤评定过程的风险;对评定为高风险的项目和特殊特性应优先采取纠正与预防措施;当顾客有要求或公司认为需要的中等风险,也应对其纠正与预防措施。
6.1.1设计FMEA是一份动态文件,应在一个设计概念最终形成之时或之前开始,而且在产品开
发的各阶段中,当发生更改或获得更多的信息时,应及时、持续、不断地修改和更新,并最终在产品加工图样完成之前全部完成。
6.1.2设计FMEA针对设计意图并且假定该设计将按此意图进行生产/装配。制造或装配过程中可能发生的潜在失效模式或/或其原因/机理不需、但也可能包括在设计FMEA当中。当这些未包含在设计FMEA当中时,它们的识别、影响/后果及控制应包括在过程FMEA当中。
6.2设计失效模式及后果分析(PFMEA)和其流程图/风险评定表中的风险分析和评估应包括从单个零件的所有产品特性(即:产品的外观、尺寸、功能和性能等)到总成的所有产品特性(即:产品的外观、尺寸、功能和性能等)。
6.3设计FMEA分析应从所要分析的系统、子系统或零部件的DFMEA环境极限框图开始,DFMEA框图指示了信息、能源、力、流体等的流程。其目的是要明确向方框交付的内容(输入),方框中完成的过程(功能)以及由方框所交付的内容(输出)。DFMEA框图说明了分析中的各项目之间的主要关系,并建立了分析的逻辑顺序。在FMEA准备工作中所有的框图的复制件应伴随FMEA过程。