高炉上料系统
基于PLC控制的高炉自动化上料系统的应用与分析

基于PLC控制的高炉自动化上料系统的应用与分析随着工业的发展,高炉已经成为钢铁企业不可或缺的设备之一。
钢铁行业是国家经济的重要支柱产业,高炉的运行对于钢铁生产起着至关重要的作用。
传统的高炉上料方式存在一些问题,如运行效率低、操作风险大、能耗较高等。
如何实现高炉自动化上料成为了一个热门话题。
基于PLC控制的高炉自动化上料系统应运而生,它可以提高高炉上料的效率、降低操作风险、减少能源消耗,受到了广泛的关注和应用。
1. 高炉自动化上料系统的应用高炉自动化上料系统是基于PLC控制技术的一种新型自动化系统,它通过精确控制上料过程中的各个参数,实现了自动计量、自动送料、自动维护等功能。
在实际应用中,高炉自动化上料系统可以分为以下几个部分:1.1 PLC控制系统PLC控制系统是整个高炉自动化上料系统的核心部分,它可以通过编程实现对系统的自动控制。
PLC控制系统不仅具有高稳定性和可靠性,而且具有很强的抗干扰能力和自适应能力。
通过对PLC控制系统的良好设计和参数调整,可以使高炉自动化上料系统实现高效稳定的运行。
1.2 送料装置送料装置是高炉自动化上料系统中的一个重要组成部分,它通常由送料机、皮带输送机、料仓等设备组成。
送料机通过PLC控制系统实现对上料速度、连续送料、料流稳定等精确控制,实现对高炉的自动上料。
计量装置是保证高炉上料质量的关键部分,它通过PLC控制系统实现对上料的精确计量。
计量装置可以根据高炉的实际情况进行调整,确保上料量达到要求,并且可以实现对不同原料的准确计量,从而保证了高炉的正常运行。
监测装置是对高炉自动化上料系统进行实时监测和数据采集的装置。
通过PLC控制系统实现对设备的工作状态、上料量、物料变化等参数的实时监测,并将监测数据传输给上位机进行处理和分析,能够对高炉的运行状态进行实时监控,以及进行远程故障诊断和维护,保证了高炉自动化上料系统的安全稳定运行。
相比传统的高炉上料方式,基于PLC控制的高炉自动化上料系统具有以下几个优势: 2.1 提高了高炉的上料效率传统的高炉上料方式通常需要人工操作,操作繁琐、效率低下,而且容易出现误差。
高炉上料系统常见故障处理及其工作原理

高炉上料系统常见故障处理及其工作原理理论部分一、关于强电超极限:1、什么是强电超极限?左右料车炉顶的行程极限停车位置所对应在的强电工作主令控制器上的开关点2、其在料车控制中起什么作用?左右料车在上行至炉顶时的极限停车位置,确保料车运行安全。
3、为什么要设置料车强电超极限保护?料车上行到炉顶时其前轮不能悬空,否则料车将被钢丝绳悬挂起来,当炉顶料车在下行时可能会因前轮下落位置不在料车轨道上导致料车翻车。
为确保料车不翻车,在料车控制电气回路上设置了如料车在到达超极限位置时立即切断料车动力电源(料车跳闸),使料车立即停车。
1#高炉强电超极限采用两点串联以提高可靠性。
4、强电超极限常见故障现象的原因及处理办法:故障现象:料车跳闸,合不上闸。
处理办法:①、此时可判断为料车超极限工作点断开了。
应立即将料车打入手动状态,到炉顶检查料车的实际位置,如未发现异常,立即用试电笔检查相对应在炉顶的料车(左车或右车)强电主令控制器侧的强电超极限点两点均应闭合。
(同时检查弱电主令料车到顶点、强电主令料车工作极限点均应断开,如均未断开,说明本次料车跳闸就是由于强、弱电工作限位未断开造成料车跳闸。
也可能是料车弱电到顶工作极限和强电到顶工作极限均相近但和强电超极限点调试距离过近,造成强电超极限点提前误动作)。
②、快速检查法:发现跳闸,立即将料车打入手动状态,按下(保持)相应料车超极限解除按钮,另一人去进行料车合闸,如能合上,立即按第①条处理。
此时,不允许按下(保持)相应料车超极限解除按钮强制料车上行。
警告:十分钟内料车合闸次数不允许超过三次,否则将造成料车变频器损坏。
③、如经过上述①或②条检查操作还合不上闸,立即电话通知电工。
二、关于强电工作极限:1、什么是强电工作极限?料车在手动状态下在炉顶(倒料或不倒料)的正常停车位置所对应的在强电主令控制器上的开关点。
(此点应在强电超极限点前200~300毫米料车行程距离),2、其在料车控制中起什么作用?此工作极限在弱电工作极限后(150~200毫米料车行程距离),当料车在自动状态下,如果料车弱电工作极限未能断开(将造成PLC无到顶信号,料车不动)PLC未能采集到料车到位信号,强电工作极限点将使料车停止运行,确保料车运行安全。
高炉上料自动控制系统中几个关键环节的设计
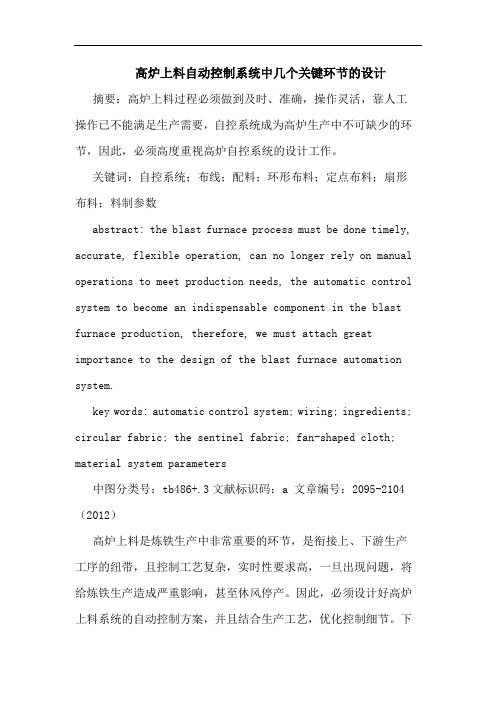
高炉上料自动控制系统中几个关键环节的设计摘要:高炉上料过程必须做到及时、准确,操作灵活,靠人工操作已不能满足生产需要,自控系统成为高炉生产中不可缺少的环节,因此,必须高度重视高炉自控系统的设计工作。
关键词:自控系统;布线;配料;环形布料;定点布料;扇形布料;料制参数abstract: the blast furnace process must be done timely, accurate, flexible operation, can no longer rely on manual operations to meet production needs, the automatic control system to become an indispensable component in the blast furnace production, therefore, we must attach great importance to the design of the blast furnace automation system.key words: automatic control system; wiring; ingredients; circular fabric; the sentinel fabric; fan-shaped cloth; material system parameters中图分类号:tb486+.3文献标识码:a 文章编号:2095-2104(2012)高炉上料是炼铁生产中非常重要的环节,是衔接上、下游生产工序的纽带,且控制工艺复杂,实时性要求高,一旦出现问题,将给炼铁生产造成严重影响,甚至休风停产。
因此,必须设计好高炉上料系统的自动控制方案,并且结合生产工艺,优化控制细节。
下面针对中小型高炉常见的上料控制工艺进行分析,对一些细节问题进行阐述,以供设计人员参考。
高炉上料控制

备用的电机号 4 2 3 1
5、称量误差补正及称量显示
5.1、称量误差补正的控制
5.1.1、简要说明:各种原、燃料均设误差补正。 补正的方式 称量误差补正的原则是本称量漏斗的称量误差由该斗补, 与其它斗无关。设有两种补正方式: ⑴本次的称量误差待下次称量时补正。 ⑵累积误差补正即把每次的称量误差累计到一定量时进 行补正。最大累积误差值(可调)暂定如下: 矿石:200kg, 杂矿:150kg, 焦炭:100kg。
6、X-601及Y-601胶带机废铁检除装置
在X-601矿石胶带机和Y-601焦炭胶带机上各设一套废 铁检除装置。该装置为机电一体化,当废铁经过金属探测 器时,将信号发送给废铁检除装置,则废铁检除装置按预 先设定的程序自动将混入物料中的铁块检除。
7、设备的操作与联锁要求
矿槽系统电控设备约33种,75套设备。除电动葫 芦及传动室吊车不参与联锁外,其余设备在自动运转 时必须保持各设备之间的联锁关系,粉矿仓料位计及 碎焦仓仓下电动闸门参与返矿系统的联锁控制(粉矿 仓料位计及碎焦仓仓下电动闸门属返矿系统,其控制 要求见机械贮运专业提供的相关资料)。为防止误操 作及保护设备,手动操作时应保留必要的安全联锁,
6 炉顶探尺对炉内物料的跟踪、记录与监视 7). 装料系统装料制度、装入待的设定、料线设定、装料 循环周期的处理 8). 空焦装入方式及运转控制 9). 装料操作参数的设定、实际装入操作的数据收集、处 理 10). 装入系统设备的操作与监视 11). 装料系统设备故障处理
2.2、主工艺系统基本控制 2.2.1、炉顶压力选择 设有高压操作和常压操作选择。 2.2.2、控制选择 全自动→1批料(Charge)自动→ 1小批料
2、高炉装料制度
高炉的装料制度为: C↓O↓ C-焦炭 O-矿石(烧结矿、块矿及球团矿)
教学课件:第三章高炉上料设备

在节能减排方面,高炉上料设备的应用有助于企业达到环保标准,提升 企业形象和社会责任感。
高炉上料设备在提高生产效率方面的应用
高炉上料设备通过自动化、智能化的控 制方式,减少了人工干预和操作误差,
提高了生产效率。
该设备能够快速响应高炉生产需求,确 保连续、稳定的生产流程,减少了生产
备也是未来的重要趋势,以适应越来越严格的环保要求。
02
高炉上料设备的组成与工作原理
槽下供料系统
槽下供料系统是高炉上料设备 的起始部分,主要负责将原料 从地面输送到高炉炉顶。
它包括槽下运输设备、称量设 备和放料设备等,能够实现原 料的精确计量和按需放料。
槽下供料系统的运行效率直接 影响高炉的生产效率和原料的 利用率。
生而设置的各类安全设施。
监控系统和安全保护装置的完善 对于保障高炉上料设备的安全、
稳定、高效运行至关重要。
03
高炉上料设备的操作与维护
高炉上料设备的操作规程与注意事项
启动前检查
确保设备周围环境安全,检查设 备各部件是否正常。
启动操作
按照规定的顺序启动设备,确保 设备正常运行。
高炉上料设备的操作规程与注意事项
检查设备各部件的紧固件是否松动,及时紧固。
高炉上料设备的日常维护与保养
保养
根据设备的使用情况,定期对设备进行全面检查和保养。
对设备的润滑系统进行检查和保养,确保设备正常运行。
对设备的电气系统进行检查和保养,确保设备安全运行。
高炉上料设备的常见故障与排除方法
设备运行异常
如振动、异响等。
设备部件损坏
3
PLC_自动上料系统

摘要在高炉冶炼中,各种原料如焦碳、烧结矿、球团矿和石灰石等以一定比例经过准确称量后,经皮带运输到上料小车,再由上料小车送至高炉内。
传统的钢厂配料控制系统设备陈旧、精度低,不仅造成原材料的浪费,更为严重的是导致许多工程质量不合格,因此需要一种高精度动态配料控制系统。
本设计是基于PLC控制、组态软件监控显示、变频器调速的高炉配料自动控制系统,而系统以PLC控制为核心。
本设计为4种原料的配料系统,PLC、变频器分别为西门子公司的S7-300、 M440。
投料系统的交流传动利用西门子公司的6SE70矢量型变频器和PLC结合来实现。
PLC程序的开发以西门子公司的Step7作为软件平台,采用了面向对象的程序设计技术,模块化的设计,从而使系统具有良好的可移植性和可维护性。
在系统中,通过上位机的控制界面设置配料的参数输出到PLC,然后通过PLC自动控制协调各阀门的开关和变频器的输出变化对配料过程进行控制,称量斗上的传感器通过变送器将重量信号送回到PLC,以达到闭环系统对给料的种类和速度的控制,并且对配料过程进行数据记录,使配料过程有数可依,便于管理。
关键词:自动配料,变频调速,自动补偿,可编程控制器S7-300引言研究背景随着课程的进度,我们开始了学业的最后部分——毕业设计。
经过了四年时间的学习,在老师的教导下,我们已经具备了一定基础,为了能够将所学联系起来,较好的应用到生产当中去,我们就需要在毕业设计中好好的锻炼自己。
在毕业设计中,我选择了这样一个题目就是为了能较好的锻炼自己的应用能力以及分析问题、解决问题的能力。
本设计的题目为高炉上料PLC控制系统,为工程类项目,是高炉冶炼中的一部分。
在高炉冶炼中,为了能高质量地进行冶炼,需要将各种原料按照一定的重量和比例准确地添加到高炉中。
传统的钢厂配料控制系统设备陈旧、精度低,不仅造成原材料的浪费,更为严重的是导致许多工程质量不合格,因此需要一种高精度动态配料控制系统。
高炉槽下上料系统操作说明书
槽下配料上料电脑操作系统使用说明书1. 概述本系统实现了槽下14个振动筛、4个给料机、14个称量斗门、6条皮带、14个除尘闸门、1个上料卷扬的画面上的手自动操作。
具有手动时灵活、可靠和自动时运行稳定的特点。
槽下分为两部分进行控制,从给料机到中间斗为备料流程,从中间斗到炉顶为上料流程。
见下图。
2.基本操作2.1. 单台设备的操作2.1.1. 给料机和振动筛的操作▲自动状态时设备被程序所控制,按照连锁条件运行。
当切换到手动时设备由操作窗口内的“启动”,“停止”按钮来控制▲连锁状态选择,设备连锁时会对流程前后的设备的运行状态有影响,如振动筛不运行,给料机不能运行;皮带机不运行,振动筛不能运行;称量斗非空,振动筛不能运行;⏹手动状态下解锁时一定要考虑周全,以应对非正常情况。
⏹自动状态下不允许切换到解锁。
▲起停操作。
左键单击相应按钮,便可以在手动时操作设备。
自动时无效。
▲状态显示。
⏹PC控制方式。
方框显示绿色表示现场操作箱上切换到远程操作,否则为就地。
⏹自动状态。
方框显示绿色表示设备切换到远程且自动状态。
⏹故障状态。
方框显示黄色表示设备的电气回路出现故障且设备停机。
⏹电源状态。
方框显示绿色表示⏹运行状态。
方框显示红色表示设备处于停止状态,方框显示绿色表示设备处于运行状态。
2.1.2.称量斗门的操作▲自动状态选择⏹自动状态选择时设备被程序所控制,按照连锁条件运行。
当切换到手动时设备由操作窗口内的“启动”,“停止”按钮来控制▲连锁状态选择⏹设备连锁时会对流程前后的设备的运行状态有影响,如皮带机不运行,斗门不能关闭,称量斗非满,则斗门不能打开。
⏹手动状态下解锁时一定要考虑周全,以应对非正常情况。
⏹自动状态下不允许切换到解锁。
▲开关操作按钮⏹左键单击相应按钮,便可以在手动时操作设备。
自动时无效。
▲回路状态显示。
⏹PC控制方式。
方框显示绿色表示现场操作箱上切换到远程操作,否则为就地。
⏹自动状态。
方框显示绿色表示设备切换到远程且自动状态。
略钢1#高炉上料系统增容改造实践
略钢1#高炉上料系统增容改造实践通过对略钢炼铁分厂1#高炉上料系统料车卷扬、料车料斗、气动闸门称量斗、自动化控制系统等的改造,上料速度由原来每小时上6.4批料提高到8.3批料,上料速度大大提高,解决了1#高炉上料速度慢的问题,消除了低料线给高炉造成的影响。
标签:高炉;上料速度;料线1 前言略钢炼铁1#高炉容积400m3,于2008年6月12日建成投运,是在原150m3高炉的基础上改扩建而成,上料系统改造也是在原料仓基础上增加了四个东西烧结矿仓,斜桥双料车上料。
根据当时原燃料水平,1#高炉设计利用系数2.80t/m3.d,每天所需烧结矿约2200t,料速按平均6.4批/小时设计,矿批重15t左右,称量斗和料车容积均为2.8m3。
近几年,通过实施精料方针,狠抓原燃料管理,1#高炉得到强化,炉况稳定性得到提高,产量大幅增长,利用系数超过2.90t/m3.d。
高炉强化后常因一些设备小故障或打扫料坑卫生导致慢风操作,上料速度慢的问题成为高炉强化冶炼的瓶颈。
2 1#高炉上料系统存在的问题2.1 称量斗、料车容积小。
1#高炉称量斗和料车容积为2.8m3,每一车只能上矿5.4t,每车料上焦炭1.7t。
每批料为14.2t,每小时上6.4批料,每小时也就35车料,即每小时只能上90.8t,每天最多只能上2181t,这样的运力远远不能满足1#高炉的生产。
2.2 装料速度慢。
从料车到料坑的信号到位后发指令,称量斗的电液动推杆启动,到称量斗全开,这个过程需要6~7秒,放完料延时5秒后到称量斗阀门关上,整个过程约需42秒。
2.3 料车在斜桥上运行速度慢。
料车从装满料后启动,经过一级加速、二级加速和高速运行后,再到二级减速、一级减速运动,再到停车倒料,完成这个过程大约52秒时间。
料车运行时间长,无法做到快速赶料线。
2.4 1#炉槽下由于受地理环境影响,8#皮带中心距19米,而9#中心距45米,上料速度快慢不一样,程序上只能以9#皮带运行时间来设定。
高炉炼铁的上料系统课件
称重系统和配料控制
称重系统
配置精确的称重设备,对原料进行准确计量,确保配料比例 符合工艺要求。
配料控制
采用自动化控制系统,实现对上料、称重、配料等环节的集 中控制,提高生产效率。
03
高炉炼铁上料系统的操作与维护
上料系统的操作流程
料仓的设计与布局
料仓设计
根据原料种类和上料系统规模,设计 合理的料仓结构,满足存储和供料需 求。
料仓布局
合理布置料仓位置,确保原料能够顺 畅流入高炉,同时减少物料损失和环 境污染。
皮带输送机的设计
输送能力
根据上料系统规模和生产需求,选择合适的皮带输送机型号和规格,确保输送 能力满足要求。
输送稳定性
实现自动化控制和监 测,提高生产效率和 产品质量。
对各种原料进行精确 的配料和混合,以满 足高炉炼铁工艺的要 求。
02
高炉炼铁上料系统的设计
原料的选择与准备
原料选择
根据高炉炼铁工艺要求,选择合 适的铁矿石、燃料和熔剂等原料 ,确保满足生产需求。
原料准备
对原料进行破碎、筛分、混合等 预处理,使其达到合适的粒度和 成分,提高上料效率。
修复与更换
对损坏的部件进行修复或更换,恢 复上料系统的正常运行。
03
02
紧急处理
在故障发生时,采取紧急措施,防 止事故扩大。
预防措施
针对常见故障制定预防措施,降低 故障发生的概率。
04
04
高炉炼铁上料系统的优化与改进
自动化控制技术的应用
自动化控制技术在上料系统中的应用,可以大大 提高上料效率,减少人工操作,降低劳动强度。
高炉上料系统施工方案
高炉上料系统施工方案1 引言高炉上料系统是高炉炼铁的关键环节之一,直接影响到生产效率和产品质量。
本文档旨在提供一个高炉上料系统施工方案,包括系统的设计、安装、调试等方面的内容。
2 系统设计2.1 系统功能高炉上料系统的主要功能包括原料的输送与配比、料斗的卸料、输送线的控制和监测等。
具体功能如下: - 原料配比:根据高炉冶炼工艺要求,将不同种类和比例的原料按照要求进行配比。
- 料斗卸料:将配制好的原料从料斗中卸下,并送入相应的输送线。
- 输送线控制:控制输送线的启停、速度调节等,确保原料的顺利输送。
- 监测:对原料的流量、温度、湿度等进行监测,以便及时调整系统参数。
2.2 系统组成高炉上料系统主要由以下几个部分组成: - 天车:用于将原料从存料仓库中取出,运送到指定的料斗。
- 料斗:用于存放原料,并通过卸料口将原料送入输送线。
- 输送线:用于将原料从料斗中输送到高炉的上料口。
- 控制系统:包括PLC控制、传感器监测和人机界面等,用于控制和监测整个系统的运行。
3 施工过程3.1 前期准备在施工之前,需要进行一系列的前期准备工作,包括: - 设计方案:根据高炉的工艺要求和现场情况,制定高炉上料系统的设计方案。
- 采购原材料和设备:根据设计方案,采购所需的原材料和设备。
- 组织人员:安排项目经理、施工人员和监理人员等,确保施工过程的顺利进行。
3.2 安装和调试安装和调试是高炉上料系统施工的关键环节,包括以下步骤: - 天车安装:将天车安装在指定位置,并进行调试,确保其正常运行。
- 料斗安装:将料斗安装在指定位置,并与天车和输送线连接,进行调试。
- 输送线安装:将输送线安装在指定位置,并与料斗和高炉上料口连接,进行调试。
- 控制系统安装:安装PLC控制器、传感器和人机界面,进行调试和联动测试。
3.3 系统验收在施工完成后,进行系统验收是必不可少的步骤。
验收过程中需要完成以下内容: - 系统功能测试:对高炉上料系统的各项功能进行测试,检查其是否满足设计要求。