三维表面形貌仿真模型
基于MATLAB的MEMS表面形貌重构

1 绪论1.1 本课题背景及研究意义随着微细加工技术的不断进步和微电路、微光学组件、微机械等微观结构表面的不断出现,对表面微观三维形貌的测量技术也提出了更高的要求[1]。
表面形貌是由机械加工、化学加工、喷镀涂层等工艺过程形成的,主要体现了表面的外在特征,同时它与表面的内在特性也有密切的关系。
在机械工业中,机械零件加工后形成的表面纹理特征在很大程度上决定了零部件的使用性能,对机械系统的摩擦磨损、接触刚度、疲劳强度、配合性质,以及传动精度等影响很大,而且还与导热、导电及抗腐蚀等物理性能有着密切的关系;在电子工业中,随着集成电路集成度的提高,硅片表面的粗糙度对集成电路中薄膜电阻和薄膜电容的影响越来越大,并直接影响到集成电路器件的性能及成品率;在现代光学领域通过多次套刻与刻蚀方法制作的二元光学组件表面以及通过微机械加工技术制作的微机械结构表面等,都对其使用性能有很大影响[2]。
与机械零件的表面微观三维形貌测量不同的是,微电路、微光学组件、微机械等微观结构表面是由微观结构单元组成的三维复杂结构,其微表面形貌的测量不仅要测量表面的粗糙度或瑕疵,还要测量表面的轮廓、形状偏差和位置偏差,要求有较高的横向分辨率和纵向分辨率,有较大的测量纵深和测量范围,这对我们形貌检测的手段和方法提出了更高的要求;此外,表面微观轮廓测试技术还在机器人视觉、实物仿形、计算机辅助设计等领域有着重要意义和广阔的应用前景[3]。
1.2 表面微观形貌测量技术概述目前,三维微表面形貌测量方法大致可以分为接触式的探针法和非接触式的光学测量法[4]。
接触式的探针法包括古老的机械触针法和20世纪后期出现的扫描探针显微镜等测量方法。
非接触式测量法大都采用光学技术,以各种光学原理、光学现象为基础,配合精密机械、计算机技术、信号处理技术、传感技术,实现高精度、无接触测量。
其测量方法主要有:光学针瞄法、光切法、投影光栅法、干涉显微法等。
(1)机械触针法[5]机械触针法是研究最为充分的一种表面形貌测量方法、它利用机械探针接触并沿被测表面移动,通过位移传感器将表面轮廓的变化转化为电信号,经数据采集和处理后得到表面轮廓参数。
matlab的平磨工件表面三维模型仿真方法

文章标题:深入探讨matlab的平磨工件表面三维模型仿真方法一、引言在制造业中,表面质量对工件的性能和外观至关重要。
平磨是一种常见的表面加工方法,对工件表面质量的影响非常大。
为了更好地理解和控制平磨工件表面的三维模型,使用matlab进行仿真已成为一种有效的方法。
本文将深入探讨matlab的平磨工件表面三维模型仿真方法。
二、matlab在平磨工件表面三维模型仿真中的应用1. 数据采集与处理在进行平磨工件表面三维模型仿真时,首先需要对工件表面进行数据采集。
这涉及到使用各种传感器来获取工件表面的高度数据。
matlab提供了丰富的数据处理工具,可以对采集到的数据进行滤波、插值等预处理,以准备好用于仿真的数据。
2. 三维模型建立基于采集到的工件表面高度数据,利用matlab可以方便地建立工件的三维模型。
通过对数据进行表面重建算法的运用,可以得到工件表面的三维模型,并进行可视化展示。
3. 条件设置与仿真在建立工件的三维模型后,可以在matlab中设定不同的加工条件,如磨削速度、磨削压力等,对工件表面进行仿真。
matlab提供了多种仿真方法,如有限元法、离散元法等,可以有效地模拟平磨过程对工件表面的影响。
4. 结果分析与优化通过matlab进行仿真后,可以对仿真结果进行分析,并根据需要进行优化。
可以通过对仿真结果进行曲面拟合,找出工件表面的几何特征,对表面质量进行评价,并提出相应的优化建议。
三、个人观点和理解matlab作为一款强大的科学计算软件,在平磨工件表面三维模型仿真中具有广泛的应用前景。
通过matlab的仿真方法,不仅可以更好地理解平磨工件表面的变化规律,还能为工程实践提供科学依据。
对我来说,深入学习和掌握matlab在平磨工件表面三维模型仿真中的方法,将有助于我在相关领域的研究和实践中取得更优异的成果。
四、总结与回顾通过本文的讨论,我们对matlab在平磨工件表面三维模型仿真中的方法有了更深入的了解。
磨削加工运动学及有限元建模与仿真

磨削加工运动学及有限元建模与仿真韩振鲁 李长河(青岛理工大学 山东青岛 266033)摘 要 介绍了建立磨削加工运动学模型的基本方法,讨论了对砂轮表面形貌的模拟,多种运动几何模型的比较以及应用运动学经验模型解析公式。
详细介绍了有限元分析的基础,在磨削加工中利用有限元分析的理论,所开发的有限元仿真自主软件,能够自动产生完全的模拟仿真过程。
研究表明,建模仿真对于研究磨削过程是非常适合的方法。
有限元仿真方法可以让使用者对于加工过程有更好的理解,并可以帮助分析复杂的试验结果。
经过计算机程序中的误差处理后,加工工件就能达到较高的精度,同时降低了制造成本。
关键词运动学模型 表面形貌 模拟仿真 有限元分析1 运动学模型自从建立第一个磨削过程的运动模型,迄今已有45年了。
尽管从那时到现在所有的方法都用来开发建模,包含对砂轮、工件和磨削运动学的描述,但是各种模型间仍具有显著的差异。
20世纪60年代和20世纪70年代早期的磨削运动学模型奠定了二维磨削理论的基础,在1980年后,当计算机运算速度大大提高后,人们建立了更加复杂的模型,这些方法中最典型的是对磨削过程采用三维立体的观点,主要是基于工件表面和砂轮表面的在几何学上的互相渗透的经验运动模型。
该模型中,磨削过程的输出参数可以通过解析和经验公式计算出来。
1.1 砂轮表面形貌的模拟在讨论磨削加工的所有模型中,对砂轮表面形貌的模拟是必不可少的一部分。
现在有两种方法来对砂轮表面形貌进行定量描述:一是直接对砂轮表面进行扫描,二是运用统计学的方法对砂轮表面进行分析来合成砂轮表面形貌。
Inasaki在他的磨削过程模拟中,提出了一个直接得到砂轮表面形貌的方法。
他得到了绕砂轮一周的表面形貌数据,并将这些数据储存在微机以供日后模拟使用。
通过已扫描的表面来分析砂轮的特性进而导出砂轮的表面形貌的一般数据信息。
利用这些统计的砂轮表面形貌数据,例如磨粒大小的平均值和分布、磨粒分布的方向以及磨粒突出表面的高度等等,综合这些参数就有可能得到比较合理的砂轮表面形貌数据。
砂轮表面形貌仿真方法研究
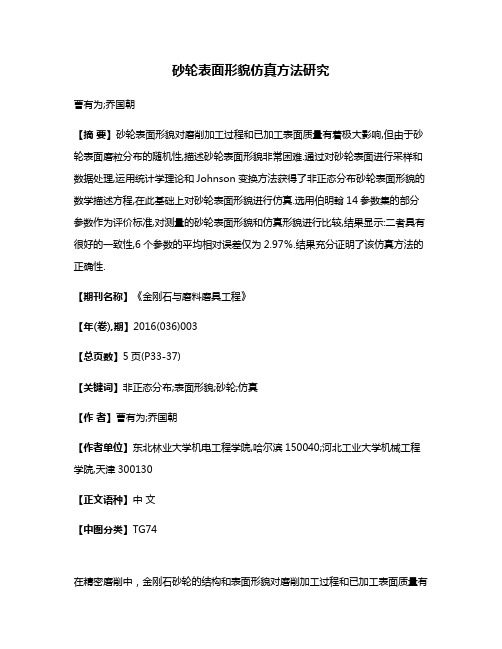
砂轮表面形貌仿真方法研究曹有为;乔国朝【摘要】砂轮表面形貌对磨削加工过程和已加工表面质量有着极大影响,但由于砂轮表面磨粒分布的随机性,描述砂轮表面形貌非常困难.通过对砂轮表面进行采样和数据处理,运用统计学理论和Johnson变换方法获得了非正态分布砂轮表面形貌的数学描述方程,在此基础上对砂轮表面形貌进行仿真.选用伯明翰14参数集的部分参数作为评价标准,对测量的砂轮表面形貌和仿真形貌进行比较,结果显示:二者具有很好的一致性,6个参数的平均相对误差仅为2.97%.结果充分证明了该仿真方法的正确性.【期刊名称】《金刚石与磨料磨具工程》【年(卷),期】2016(036)003【总页数】5页(P33-37)【关键词】非正态分布;表面形貌;砂轮;仿真【作者】曹有为;乔国朝【作者单位】东北林业大学机电工程学院,哈尔滨150040;河北工业大学机械工程学院,天津300130【正文语种】中文【中图分类】TG74在精密磨削中,金刚石砂轮的结构和表面形貌对磨削加工过程和已加工表面质量有着巨大的影响。
但是,由于大量形状和尺寸各异的磨粒随机分布在砂轮表面上,各个磨粒的突出高度和空间间隔各不相同,在加工过程中实际参与磨削的有效磨粒数无从确定,从而影响对磨削过程中磨削力、磨削温度、加工表面质量等方面的研究,严重阻碍磨削加工技术的发展。
为了解决这个问题,许多学者开始研究砂轮表面形貌的建模和仿真方法。
Zhou[1]等认为,砂轮表面磨粒的分布特征符合高斯分布,进而建立了基于高斯分布的砂轮表面形貌仿真模型,并把该模型应用到磨削加工表面粗糙度预测技术当中,取得了一定的效果。
Koshy等[2-4] 把磨粒的形状简化成球形,假设磨粒的直径符合正态分布,磨粒在砂轮表面均匀分布,以此为基础研究了砂轮表面形貌的分布特征。
Xie等[5]建立了砂轮表面磨粒分布的几何模型,尝试定量分析砂轮表面突出磨粒的特征,结果显示:磨粒的突出高度约为0~28 μm,磨粒前角为-45°~-89.1°。
基于电涡流传感器的金属材料表面形貌三维可视化检测

E AC 7 3 ;2 0 0 9 E C:2 0 7 3 R;2 T
d i1 . 9 9 ji I 1 0 - 6 9 2 1 .3 0 8 o :0 3 6 /.S I 0 4 1 9 .0 2 0 . 1 S.
基于电涡流传感器的金属材料表面形貌三维可视化检测 木
吴相楠 , 李陇杰 , 张 冰 , 丁 晖
力 的 电涡流传 感器 。 以下介绍 对该 种传感 器 的仿真
及 实验研 究 。
1 高 空 间分 辨 能 力 电涡 流 位 移 传 感 器 原 理 及 仿 真
1 1 屏 蔽套 对 电涡流 传 感 器 空 间检 测 分 辨 能 力 的 .
改善作 用
件: 另一种 是仿 真 区域 的左 边 界 及 轴 对称 结 构 的 对
( 西安交通大学电气材料表 面形貌检测问题 , 论文没计 制作 了一种高空问分辨力 的电涡流传感器 , 可实现金属 管道内壁复杂 表 面形貌及裂纹的高分辨检测 。论 文采用 A S S有限元分析软件对传感器进行 了仿 真分析 , NY 验证 了传 感器对金属材料表 面形 貌变化的高空间分辨检测 能力。论 文同时对该种传感器性能进行 了实验测试 。实 验结果表 明, 比传统 的 电涡流传 感器 , 相 本 文设计的传感器对裂纹 、 对金属材料表面形貌变化具有 更高 的检 测分辨 力。最 后 . 文采用 三维可 视化技术 . 论 将传 感器对 金 属板表面形貌的扫描检测 数据 转化成j维 图像 , 可直观地 显示 出被测金 属板表面形貌 变化及裂纹位置 。
Absr t: n w i d o d y c re ts n o , ih c u d b s d i e sng s ra e tpo r ph fme a t ras tac A e k n fe d u r n e s r wh c o l e u e n s n i u f c o g a y o tlmae il a e o n zng t e c a k n t e s ra e o tlma ei l t ih s a ilr s l to s d vs d a n r d c d nd r c g ii h r c s o h u fc fme a tras wi h g p ta e ou in i e ie nd i to u e h h r .F nt lme ta ay i sa pl d i n lzn n mo sr t h ih s ailr s lto e snga ii e f e e i i ee n n lssi p i n a ay i ga d de n tai t e h g p ta e ou i n s n i b l i so e e ng t t e p o o e e s r Mo e v r t ha a tr ft e p o o e e s r ae as e n tae y e pe me t . e e — h r p s d s n o . r o e ,he c r ce so h r p s d s n o r lo d mo sr td b x r n s Th x i pei n s d mo sr td t tt e p o o e e s rh shih r s ails n i g r sl t n i e o n zng t u f c o rme t e n ta e ha h r p s d s n o a g e p ta e sn e o ui n r c g ii he s ra e t o p g a y o r c s o he mea t ras b o a i g wih t e ta i o a d y c r n e s r o r ph fc a k ft tl mae l y c mp rn t h r dt n le d ure ts n o .At ls , c n i g i i a t s a n n daa o ti e wh n e s r s a s h o h h d tc e mea p ae r ta sae i t a r p b a p y n t b an d e s n o c n t r ug t e e e td tl lt a e r n ltd n o g a h y p l i g 3D v s aiain t c n lg . n t i y, oh t e c n e o u fc o o r p y a d l c to s o r c n t e s ra e o iu lz to e h o o y I h swa b t h ha g fs ra e tp g a h n o ain fc a kso h u f c f t e mea tras a e d s ly d i t i v l n la l h t lmae il r ip a e n u t ey a d ce ry. i Ke r s: d y c re tpo e; n t lme ta ay i ;D iu lzto e h oo y;u a e tp g a h fmea tras y wo d e d u r n rb f i ee n n lss 3 vs aiain tc n lg s r c o o r p y o tlmaei i e f l
数控铣削加工表面形貌建模及预测技术研究

加工 转变 ,从 基 于加工 理论 向人 工智 能 手段转 变 , 从 只考虑 切 削速度 、进给率 和 切削深 度 基本 影响 因 素 的预测模 型到综 合考 虑 到 了机 床震 动 、刀具 变形 等更 多影 响 因素 的预 测模 型转 变 。 在切 削 过程 中 ,影响表 面 形貌 的 因素有很 多 ,
表 面形貌 和表 面粗糙 度 的预测 。B . H. K i m等_ 4 提 出的
一
种 纹理 叠加 法 ,通过 有效 的残 留面积得 出表 面粗
糙度 ,基 本思 路 是按 照给定 的切 削条 件 和刀具 形状
通 过纹 理叠加 程 序构成 维表 面纹 理 。非 线性 回归
法( R S M: R e s p o n s e S u r f a c e Me t h o d o l o g y ) 是用 于表 面
粗糙 度 预测 的一 种很成 功 的方法 ,它结合 数学 和统 计学 原 理 ,用 于 建模 和分 析多 个独立 变量 影 响一个
独 立响 应一类问题 的方 法 。在应 用 于加 T表 面粗糙 度 预测 的研 究 中 ,多个独 立变 量就 是切 削速 度 、进
给率 和切 削深度 等加 工过 程参 数 ,而相 应形 成 的表
文 章 编 号 :1 6 7 2 — 6 3 3 2( 2 0 1 3) 0 1 — 0 0 4 4 — 0 5
【 信息技术应用研究 】
数 控 铣 削 加 工表 面 形 貌 建模 及预 测 技 术研 究
陈 慧群
( 深圳信息职业技术学院思政部 ,广 东 深圳 5 1 8 1 7 2 )
不同粗糙度下磨削表面形貌特征与仿真研究

( College of Petrochemical Engineeringꎬ Lanzhou University of Technologyꎬ Lanzhou 730050ꎬ China)
Abstract: Based on fractal theoryꎬ the bivariate W - M function is studiedꎬ and the variation range of grinding surface profile height
中图分类号:TG580.6 文献标志码:B 文章编号:1671 ̄5276(2022)05 ̄0110 ̄04
Characteristics and Simulation of Grinding Surface Morphology under Different Roughness
LIANG Ruiꎬ CHENG Dongcaiꎬ JIANG Feng
yD/μm
(a) Ra=0.8
xD/μm
yD/μm
(b) Ra=1.6
xD/μm
(c) Ra=3.2
-
(
cos arctan
( yx ) -πmM ) +ϕ ]}
mꎬn
(4)
为了得到随机相位下不同表面粗糙度的表面轮廓示
意图ꎬ现取样本长度 L = 5 mmꎻ截止长度 L s = 1 nmꎻ随机相
位ϕ mꎬn 不同ꎬ得到的表面轮廓的示意图也略有差别ꎮ ϕ mꎬn
可以用 Matlab 中随机函数 rand( ) 与 2π 的乘积来实现ꎬ于
一种岩石结构面三维表面形貌的测定方法

(2019年第18期〕Research Findings|研究成果|•17*一种岩石结构面三维表面形貌的测定方法蒋庆仁,胡寒露,杨秀涛(中国电建集团贵阳勘察设计研究院有限公司,贵州贵阳550081)摘要:岩石结构面表面形貌与结构面抗剪强度有密切联系。
文章介绍了一种基于激光扫描试验的岩石结构面三维表面形貌数据测定方法。
通过激光位移传感器及电移台组成餉系统对结构面进行精确扫描,获得的大量数据通过C语言编程批量处理。
处理后的数据可利用Surfer软件生成线框图及3D表面图直观展示,也可通过C语言编程计算各类形貌.参数,用于结构面形貌量化描述,为结构面形貌特征与抗剪强度关系的研究奠定基础。
关键词:岩石结构面;表面形貌.;激光扫描;C语言中图分类号:TU452文献标志码:A文章编号:2096-2789(2019)18-0017-03结构面是岩体中没有或具有低抗拉强度的力学不连续面的总称,包括层面、节理、劈理、片理等。
在工程荷载作用下,岩体破坏常以沿软弱结构面的滑动破坏为主,岩体力学重点研究结构面抗剪强度大量研究表明,单组结构面抗剪强度主要决定因素包括岩石抗压强度、法向应力及表面几何形貌等I"、表面几何形貌具有很强的随机性和复杂性,对表面形貌的描述多年来一直是结构面抗剪强度研究的热点问题,目前在经验估值法、统计参数法、分形几何法等方向已经有大量的研究,通过岩石直剪试验、数值仿真试验等方法取得了较多成果”打这类研究均需要对结构面表面几何形貌进行测定,文章提出一种基于激光扫描技术的结构面三维表面形貌测定方法,并对其数据处理方法进行详细介绍。
1结构面激光扫描试验岩石结构面直剪试验釆用的试件可以是天然试件,也可以釆用快劈法获得人工试件。
本试验釆用巴西劈裂法制备的长方形花岗岩试件,结构面尺寸为10cmX20cm。
三维激光扫描试验釆用高精度激光位移传感器,对节理面进行非接触式扫描,获取节理表面形貌的数据。
试件放在电移台上,随着平台在长度和宽度方向上做匀速周期往返运动,能够以0.001mm的精度获取扫描点的高度值。