催化裂化主分馏塔扩能改造
催化裂化装置两器旋风分离器更换技术探讨

梁
卓
彭振亚
周旭东
构 景武
中国石油天然气第一建设公司 河南洛阳
4 7 1 0 1 2
摘
要
随着我 国炼油建设总体技术水平的发展 , 催化裂化装置两器 内旋风分离器 的更换施工技术有了长足发展。如何利 用施工企业现有机械设 备、 根据现场催化装置特点和施工条件 , 经济合理选择施 工方案成 了施工企业 日益关注的 问题。本 文通过对旋风分离器 内部组焊 、 侧壁开孔 、 顶部开 孔、 整体更换施工技术进行 比较分析 , 对 几种施工方法进
头 1 0 沉 降段 1 1提 升 管 l 2 汽提 段 1 3待 生立 管 l 4 二 段 密 相床 1 5再 生立 管 1 6再生塞阀
同样采用临时拉杆 固定后焊接 。焊接后对旋风分离器整体进行
复查。待所有安装料腿 、 拉杆及翼阀安 装完毕 , 检查合格后对所
有加固件进行拆除。
大成 为催 化裂化装置检修的重点 。合理 的选择施工方案是保证 施工企业 目标控 制、 进度控制 、 费 用控 制重要的技术 手段 。
1旋风 分 离器 更换 的原 因
在两器 内长期 高温的作用下 ( 再生器 6 5 0 ~6 8 0  ̄ C,反应器 4 8 0 ~5 0 0  ̄ C) , 会 发生 金属 蠕变、 焊缝 开裂 、 局部变形及 衬里脱 落
图 2同轴式提升管催化裂化
首先对旋 风分离本体安装就位后 ,采用临时拉杆与两器器壁进
行 相 焊 加 固 。焊 接 完 毕 经 复 查 合 格 , 然 后对 灰 斗 部分 进 行 组 对 ,
注: l空气分布管 2待 生塞 阀 3一段密相床 4 5旋风分 离器 6外部烟气集合 管 7旋风分 离系统 8快速分离设 施 9耐磨弯
催化裂化装置的节能改造及运行分析

催化裂化装置的节能改造及运行分析在石油炼化装置中,催化裂化设备对能量的消耗较大,运行的成本高,通过采用先进的节能技术改造,可以有效地降低催化裂化设备的运行成本。
文章分析了催化裂化设备能量消耗大的原因,提出降低设备能耗的技术改造措施,对于提高催化裂化设备的能量利用率、降低设备的运行成本、提升经济效益均具有重要的作用。
标签:催化裂化装置;节能改造;运行近年来,世界经济发展模式发生了深刻的变革,降低能源消耗、实现低投入高产出已经是企业提高市场竞争力的主要手段。
催化裂化过程的能耗除化学反应热产品转移到产品外,其他能量都通过不同途径散失于周围环境之中。
减少这部分热量损失就是节能。
鉴于经济效益的原因,散失和排放热量是不可避免的,笔者从几个方面论述如何减少排放和损失。
1催化裂化装置耗能大的原因催化裂化装置的能源消耗主要由耗电量、循环水、烧焦、蒸馏水、脱盐水、烟气等构成,其中电量、烧焦又是主要的能源消耗者。
1.1电量消耗分析三机组是催化裂化装置的主要耗电设备,烟机的运行效率会对其用电量产生重要影响,比如,当催化裂化装置正在运行的时候,烟机偶尔会因为震动强度过大而被强制退出系统,这就会增大催化裂化装置的耗电量。
除此之外,催化剂细粉的数量也会对三机组的运行效率产生影响,比如,当细粉在烟机转盘上粘黏堆积的时候,有可能会导致三机组轮轴震动。
1.2烧焦消耗分析催化裂化装置的反再系统和分馏、稳定系统需要在一定的生焦率下来维持自身运转对能量的需求,但生焦率需要控制在一定的比例内,一般受原料轻重和反应深度的影响,生焦率在6%~9%左右。
生焦率过高则系统内部热量严重过剩,会造成能耗大幅度增加,液收也会降低。
2催化裂化装置的节能改造及运行2.1原料结构优化,降低原料重金属和钙的含量钙的主要来源在于原料,优化原料品种,对该装置使用的原油构成中,掺炼渣油的先经过渣油加氢装置进行加氢、脱硫和脱重金属处理,从油种优化前后比较,Fe、Ni等金属含量减少了40%~50%。
柴油加氢裂化装置最大量生产重石脑油和喷气燃料改造总结

柴油加氢裂化装置最大量生产重石脑油和喷气燃料改造总结李志敏(中海石油宁波大榭石化有限公司,浙江省宁波市315812)摘要:2.0Mt/a工业加氢裂化装置设计原料为环烷基柴油,主要生产重石脑油和超低硫柴油。
受市场环境变化影响,对产品结构进行了调整,最大量生产重石脑油和喷气燃料。
通过调整产品切割点、增设分馏塔等措施实现了该目的。
工业运转结果表明,以柴油为原料,该装置生产的重石脑油和优质喷气燃料的收率分别为52.98%,29.35%,高价值产品收率超过82.3%,柴油收率仅3.63%。
各馏分产品性质优良,其中喷气燃料烟点30.2mm,硫、氮质量分数均小于0.5μg/g,冰点-53℃。
关键词:柴油加氢裂化装置 重石脑油 喷气燃料 改造方案 标定数据 国内炼油产品逐步走向产能过剩,柴汽比逐步降低[1 3]。
然而为了满足国内外非生产性税费一致性的要求,目前仍然暂缓征收喷气燃料产品消费税,对于有喷气燃料需求的企业,提高喷气燃料/柴油比例成为优化产品结构的重要手段,使柴油加氢装置增产喷气燃料成为现实选择。
通过将直馏柴油精制装置改为生产直馏喷气燃料、调整加氢裂化转化率和切割点等方式可以增产喷气燃料[4 6]。
中海石油宁波大榭石化有限公司2.0Mt/a工业燃料油加氢裂化装置上周期主要以环烷基直馏柴油为原料,生产超低硫柴油和重石脑油等,重石脑油收率达到50%以上。
该装置需要将未转化的柴油最大量地转化为喷气燃料。
GB6537—2018《3号喷气燃料》要求其闪点(闭口)不低于38℃,10%回收温度不高于205℃,50%回收温度不高于232℃。
另外市场上优质喷气燃料大多要求烟点高于25mm,冰点低于-50℃,闪点在40~50℃。
装置前期产品以柴油和石脑油为主,主分馏塔重馏分侧线抽出压力不高,如何在工业装置上满足侧线喷气燃料的产品质量要求也成为现实难题[7 8]。
结合装置实际运行情况,优选了中国石油化工股份有限公司大连石油化工研究院催化剂及工艺,依托中石化洛阳工程有限公司进行设计,在2018年底进行了装置改造建设。
汽油分馏塔改造及运行优化
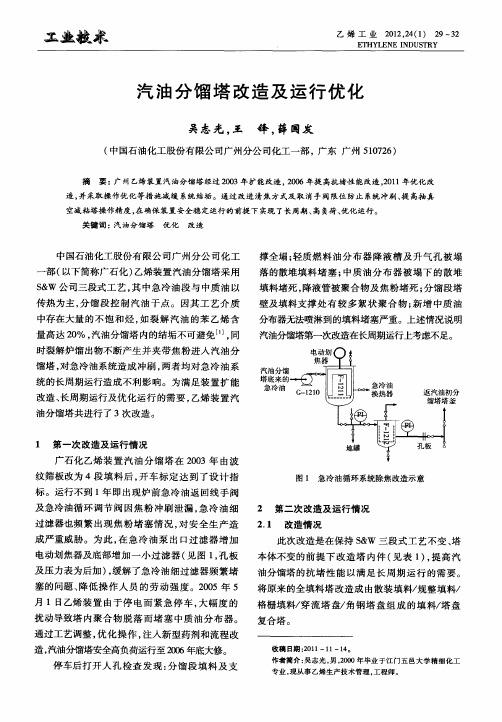
及 急冷 油循 环 调 节 阀 因焦 粉 冲 刷 泄 漏 , 冷 油 细 急
过 滤器 也 频 繁 出 现 焦 粉 堵 塞 情 况 , 安 全 生 产 造 对 成严 重 威 胁 。 为 此 , 急 冷 油 泵 出 口过 滤 器 增 加 在
2 第二次 改 造及 运 行情 况
薹 渡 米
乙 E Y2 IUR ~ 烯 T LE21Y 3 工 E2 ( 2 2 H N, S 业 0N T 9 1 4) D
汽 油 分 馏 塔 改 造 及 运 行 优 化
吴志光 , 王 锋 , 国发 薛
( 中国石 油化 工 股份有 限公 司广 州分 公 司化 工一 部 , 东 广州 5 0 2 ) 广 17 6
作者简介 : 吴志光 , ,0 0年毕业 于江 门五 邑大学 精细化工 男 20 专业 , 现从事 乙烯生 产技术管理 , 工程师。
・
3 ・ 0
乙 烯 工 业
第2 4卷
全塔填料层总高度及总板数
填料 1 0 m+ 36 0m 7层大孔穿流筛板 +3层角钢塔盘
中质油 及急 冷油 回流分 布 器 采用 喷 嘴 式 液体 分 布器 , 消除焦 粉 或 聚合 物 堵塞 的隐 患 , 实现 既 又 了喷雾 传 热 ; 汽油 分 馏 塔 10~10℃ 区间 ( 3 4 即分 馏段 下 部 ) 极 易发生 聚合 反 应 的部 位 , 用 4层 是 采 大孔 穿 流筛 板 提 高 其 抗 堵 性 能 ; 中质 油 段 下 部 采 用 3层 传 热 效 率 较 高 且 流 通 量 大 的 大 孔 穿 流 筛 板, 缓解 该部 位 的通量 与传 热效 率之 间 的矛盾 。
2 1 改造 情 况 . 此 次改 造是 在 保持 S W 三段 式 工 艺 不 变 、 & 塔
设备及公用工程
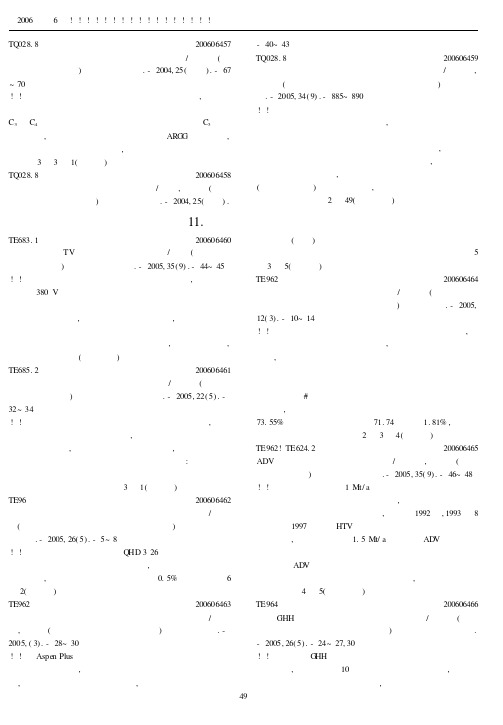
TQ028.8200606457气体膜分离技术在低压瓦斯回收中的应用刊/王良军(大庆炼化公司储运厂)膜科学与技术.-2004,25(增刊).-67 ~70!!阐述了有机蒸气膜分离的原理、性能及其应用,介绍了大庆炼化公司应用有机蒸气膜分离技术回收低压瓦斯中的C3和C4、原料气进行净化后通过膜装置对瓦斯中的C3以上组分富集,然后通过压缩机把渗透气送到ARG G装置回炼,实现了瓦斯气的全程合理回收,投用后取得了较好的经济效益。
图3表3参1(方静摘)TQ028.8200606458有机蒸气膜在石油化工领域的应用刊/吴勇,赵小平(上海东化环境工程有限公司)膜科学与技术.-2004,25(增刊).-40~43TQ028.8200606459苯环己烷分离渗透蒸发膜的研究进展与展望刊/方志平,姜忠义(中国石油化工股份有限公司科技开发部)石油化工.-2005,34(9).-885~890!!综述了渗透蒸发膜分离苯环己烷混合物的研究进展。
介绍了用于渗透蒸发技术的膜材料,展望了渗透蒸发技术分离苯环己烷混合物的前景。
渗透蒸发膜分离技术应用于苯环己烷混合物的分离目前尚处于实验室探索阶段,该技术的关键是高分离性能膜材料的合成。
研究者认为,利用杯芳烃对苯分子的识别作用,充填在高分子膜中或接枝于高分子(如聚酰亚胺等)的主链或侧链,将是分离苯环己烷混合物的一种膜材料。
图2参49(吴小蓓摘)11.设备及公用工程TE683.1200606460石化企业低压TV系统接地故障保护刊/张建(洛阳石油化工工程公司)炼油技术与工程.-2005,35(9).-44~45!!由于石化企业生产装置逐步联合化、大型化,使得石化企业的380V配电系统的供电范围亦越来越大。
石化企业一般采用相间短路保护电器低压断路器或熔断器兼作单相接地故障保护,当线路末端发生故障时,部分线路的保护灵敏性和可靠性难以得到保证。
指出石化企业低压配电系统接地故障保护存在的问题及其危害性,并做实例分析,提出了解决措施。
催化裂化装置的节能改造及运行分析
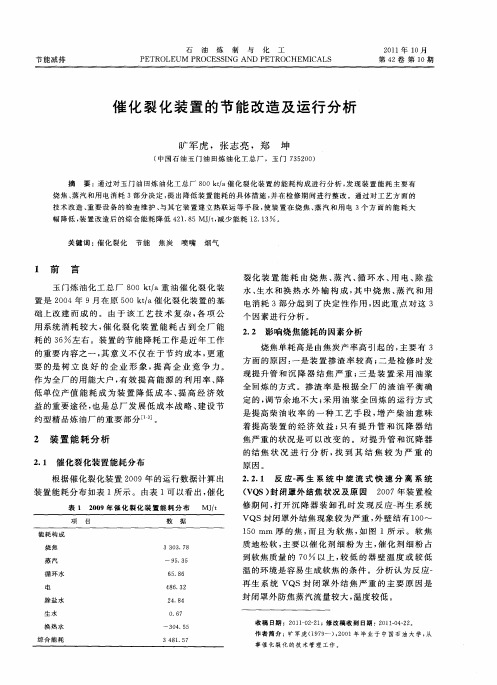
2 3 3 锅 炉 定 排 、 排 热 水 未 得 到 充 分 利 用 锅 .. 连 炉定 排 、 排 ( 称 定 连 排 ) 水 温 度 为 1O ℃左 连 简 热 5
不 足 , 取 了一 系列 措施 。 采
作 者 简 介 :旷 军 虎 ( 99 ) 2 0 1 7 一 ,0 1年 毕 业 于 中 国 石 油 大 学 , 从 事 催 化 裂 化 的技 术 管 理 工 作 。
第 1 期 O
旷 军 虎 等 . 化 裂 化 装 置 的节 能 改 造 及 运 行 分 析 催
8 7
装 置预分 馏 塔 的 进 料 温 度 、 降低 塔 底 重 沸 器 的 中
( 国 石 油 玉 门 油 田炼 油 化 工 总 厂 ,玉 门 7 5 0 ) 中 32 0
摘 要 : 过 对 玉 门 油 田炼 油化 工 总 厂 8 0k / 催 化 裂 化 装 置 的 能 耗 构 成 进 行 分 析 , 现 装 置 能 耗 主 要 有 通 0 t a 发
烧 焦 、 汽 和 用 电消 耗 3部 分 决 定 , 出 降 低 装 置 能 耗 的 具 体 措 施 , 在 检 修 期 间 进 行 整 改 。通 过 对 工 艺 方 面 的 蒸 提 并 技 术改 造 、 要 设 备 的检 查 维 护 、 其 它 装 置 建 立 热 联 运 等 手 段 , 装 置 在 烧 焦 、 汽 和 用 电 3 方 面 的 能 耗 大 重 与 使 蒸 个 幅 降低 , 置 改 造 后 的 综 合 能 耗 降低 4 i8 /, 少 能 耗 1 . 3 。 装 2 . 5MJt减 2 1
低 单位 产 值 能 耗 成 为 装 置 降 低 成 本 、 高 经 济 效 提 益 的重 要 途径 , 也是 总 厂 发 展 低成 本 战略 、 设 节 建
催化裂化(LTAG+MIP)技术工业应用

催化裂化(LTAG+MIP)技术工业应用发布时间:2022-04-28T10:06:01.653Z 来源:《科学与技术》2022年1期作者:郝仁[导读] 某炼化企业新建催化裂化装置郝仁中石化北海炼化有限责任公司,广西壮族自治区北海市 536017摘要:某炼化企业新建催化裂化装置,采用LTAG工艺技术,配置有催化柴油加氢改质装置,双反应器共用再生器,主反应器进料为加氢蜡油与低硫渣油混合进料,副反应器进料为加氢后催化柴油。
主反应器采用MIP技术,提升管分第一、第二反应区。
LTAG+MIP技术的应用,多生产高辛烷值汽油组分及化工原料,提高轻油收率,全厂柴汽比降至1以下。
关键词:催化裂化双器柴汽比轻油收率化工原料目前,汽油需求增长缓慢,柴油需求有下降趋势,航空煤油需求保持相对稳定增长,化工原料需求增长迅速,炼油产能过剩,为可持续发展,提高经济效益,需要炼化企业提高轻油收率,减少柴油生产,多生产化工原料。
向“油产化、油转化、油转特”方向发展。
根据公司自身状况,合理利用原有装置流程,选用(LTAG+MIP)技术催化裂化装置,灵活调整产品结构,以适应市场需求。
1装置概况及技术特点某炼化公司新建120×104t/a催化裂化装置,同时配置65×104t/a催化柴油加氢改质装置。
采用中国石化股份有限公司石油化工科学研究院的MIP技术和LTAG技术,以生产高辛烷值低烯烃的汽油、富含丙烯的液化气为主,催化剂为CGP专用催化剂。
再生部分采用单段逆流高效再生技术。
重油沉降器、柴油沉降器、再生器并列式三器布置。
重油提升管加工加氢蜡油与低硫渣油,加工规模80×104t/a。
柴油提升管加工加氢后催化柴油,加工规模40×104t/a。
主副反应器顶反应油气管线合并后进入分馏塔。
主要产出物料有干气、液化气、稳定汽油、柴油、油浆。
简要流程见图1。
2原料性质装置3股原料,其中柴油及蜡油2股原料经过加氢处理,渣油原料采用低硫渣油,原料性质提高,大幅降低原料硫含量、多环芳烃、残碳、金属含量等指标,在催化剂及高温条件下尽量向预想方向进行反应,既可达到理想收率,又能提高产品性质。
催化裂解(DCC) 新技术的开发与应用

催化裂解(DCC)新技术的开发与应用王巍谢朝钢(中国石化集团石油化工科学研究院,北京,100083)摘要:文章介绍了DCC技术的主要特点、原料油和催化剂、典型工业试验结果,并重点介绍催化裂解技术的最新工业应用情况。
对于石蜡基常压渣油原料,DCC-Ⅰ型技术的丙烯质量收率可以达到24.8%,DCC-Ⅱ型技术的丙烯质量收率可以达到14.6%。
另外对新开发的高丙烯选择性催化裂解催化剂的工业应用情况进行了总结。
关键词:催化裂解丙烯催化剂工业化随着石油化学工业的快速发展,我国丙烯产量大幅增长。
2001年我国丙烯产量为4.75 Mt,2002年达到5.32 Mt,2003年则达到5.93 Mt,年增长率达到12%左右。
预计2005年丙烯产量可以达到6.75 Mt,丙烯表观消费量为7.92 Mt左右,而2010年丙烯表观消费量将达到10.49 Mt,2005-2010年年均增长率为5.8%。
丙烯平衡存在大量缺口,大力发展我国的丙烯生产技术具有很重要的现实意义。
目前丙烯的生产主要依靠蒸汽裂解和催化裂化的副产,全球丙烯产量中70%来源于蒸汽裂解,28%来源于催化裂化和2%来源于丙烷脱氢等技术。
在我国,催化裂化生产的丙烯占总产量的比例为39%左右,而蒸汽裂解生产的丙烯占总产量的比例约为61%。
由于我国原油偏重,轻烃和石脑油资源贫乏,而催化裂化生产丙烯技术具有原料重质化、产品中丙烯/乙烯比值高以及生产成本低的优点,因此发展多产丙烯的催化裂化技术是适合我国国情的一条丙烯生产技术路线。
20世纪80年代末,石油化工科学研究院成功地开发出了以重油为原料、以生产丙烯为主要目的的催化裂解(Deep Catalytic Cracking-DCC)新工艺[1~2]。
该技术在生产丙烯的同时,兼产异丁烯及高辛烷值汽油组分。
DCC技术分别获得中国、美国、欧洲和日本专利,并于1991年获中国专利金奖,1992年获中国石化科技进步特等奖,1995年获国家发明一等奖。
- 1、下载文档前请自行甄别文档内容的完整性,平台不提供额外的编辑、内容补充、找答案等附加服务。
- 2、"仅部分预览"的文档,不可在线预览部分如存在完整性等问题,可反馈申请退款(可完整预览的文档不适用该条件!)。
- 3、如文档侵犯您的权益,请联系客服反馈,我们会尽快为您处理(人工客服工作时间:9:00-18:30)。
催化裂化主分馏塔扩能改造后, 一般随着顶
循、 中段回流取热量的增加, 使得该段液体负荷相 应增加许多, 采用当今常用的一些传质元件很难
分馏塔进行简单改造已无法达到扩能要求。针对 这种状况, 提出在分馏塔塔体直径不变的情况下, 采用新型高效传质设备分离技术一 催化裂化主分 馏塔技术, 对塔内件进行技术改造以达扩能目的。
2 设计简述
21 设计依据 .
中国石化武汉分公司工 套重油催化裂化装置 始建于 1 5 原为加工能力 06 a 9 年, 7 . M/ 的蜡油催 t 化裂化装置, 8 年引进 Sn & bt 公司的 17 9 te W sr o ee 技术, 改造为加工能力 1 a M/ 的高低并列式两段 t 再生重油催化裂化装置。此后, 虽然围绕着装置 扩能、 节能降耗以及产品分布和产品质量的改善
塔底温度/ ℃
8 55 7 3
20 7 2 2 6 6 2 9
30 5
23 改造方案 . 本次改造在不动塔体的情况下将旧的塔内件 全部拆除, 重新设计 , 单溢流改为双溢流; 塔盘更 换为高效导流浮阀塔盘、 D 塔盘、 G塔盘, T J F L V 以
提高处理能力和传质效率。 导流浮阀塔盘, 其优点在于从导流浮阀吹出
部操作困难, 发生液泛, 出现淹塔现象, 同时装置 要进行 M D改造, G 汽油回炼量达 2 t , 2 液化石油 置扩能和产品质量要求。 / h 气收率有较大幅度提高, 分馏塔气、 液相负荷也将 收稿日 20 一 0 2 期: 4 1- 8 0 大幅度增加。此外, 该分馏塔塔顶结盐问题严重, 作者简介: 高有飞, 工程师, 8 年毕业于北京石油化工学 19 9 院 经常堵塞塔盘, 造成塔盘效率降低, 影响产品质
的经济效益。
降器顶至分馏塔顶压力降为02 一 . P, . 02 M a与 2 4
改造前相近。
() 3产品质量控制 良好。在塔顶负荷大幅增 加的情况下, 汽油干点仍能控制在 1 ℃左右。在 8 0 不出重柴油的情况下, 轻柴油与油浆的分离效果
() 3催化裂化主分馏塔分离技术作为一项新 技术, 不仅拓宽了催化裂化装置扩能改造的思路, 也更好地体现了现有装置设备利旧、 节约改造投 资、 缩短施工周期以及节能降耗这一改造设计原
进行了一系列技术改造, 但实际加工能力仍没突
设计依据是 套重油催化裂化装置 20 年 I 01 的全年平均物料平衡数据, 并参考了装置 20 年 01 9 月8日 最大处理量 1 t 和处理量 1 t 时 3 / 2 h 1/ 5 h 的操作数据。
22 工况说明 .
改造分为以下两个工况: 工况 1第一阶段最大产柴油方案, : 装置处理 量 12 a年开工时间 8 h . t , M/ 40 0 o
步提高冷回流温度来减轻结盐程度。
顶 循环油流量/ -- k hI g
一中抽出温度/ ℃ 一中返塔温度/ ℃
10 7
一中 量 k h' 流 /- g-
二中抽出温度/ ℃ 二中返塔温度/ ℃
13 3 2 0 3
30 3 2 印
二中 量/g 一 流 k" ’ h
循环油浆返塔温度/ ℃ 循 浆流量/ - 环油 k h’ g一
炼 油 技 术
20 年 3 05 月
工 与 程
F 'OL tM nNE Y ENGI E N G Ett E J Rh 1 R N ERI
第 3 卷第 3 5 期
催化裂化主分馏塔扩能改造
高有飞, 谢凯云2 刘 兴‘ 张振千, 蔡连波‘ 刘家海2 俞晓梅3
1中国石化集团洛阳石油化工工程公司工程研究院( . 河南省洛阳市41 3 7 0) 0 2中国石化武汉分公司( . 湖北省武汉市(08) 1 2 0 3 浙江工业大学( . 浙江省杭州市 3 0 ) 11 04
降液管 分配比, 液流程数 %
线5 35 4 2一8 5 2 顶循 T D 塔盘 FJ 液化石油气 2 50 1 8
汽油 轻柴油 重柴油 油浆 焦炭 损失
5 00 00 4 05 24 6 85 2 1 65 3 3 91 一0 ( 9 50 7
摘要: 介绍了催化裂化主分馏塔技术, 其特点在于综合了高效导流浮阀塔盘、 D 塔盘、V 塔盘三者的优点, T J F LG 根据催化裂化主分馏塔各段不同的汽液负荷及结盐、 结焦情况, 采用不同的塔盘。采用该技术后结盐、 结焦堵塞塔 盘的状况基本消除, 液化石油气收率提高 了23 个百分点, . 9 在汽油回炼量增加 2 t 的情况下, 0 / h 该装置的处理能力
工况2 第二阶段最大产柴油方案, : 装置处理
量 1 a年开工时间 8 h M/ , t 40 0 o 根据表 1 提供的装置物料平衡数据和表 2 提
破 1 a M/。生产方案以柴油为主, t 出重柴油。 该装置的主分馏塔改造前主要存在的问题是 在较大处理量、 柴油生产方案条件下, 分馏塔中下
项 目
产量 t 一 产率, /" ’ h 鱼
1 6 2
吕. 1 3{
产量/"一 1*, t t I 鱼 h - '
17. 3 5 1 .5 97 17.5 1 7
1 0. 0 0 0
抽出、 返回口 及人孔进行了相应的改造; 对上部板 间距作了适当调整; 对部分热电偶作了相应移位。
原料 焦化蜡油 减压蜡油 减压渣油 产品 干气 酸性气 液化石油气 汽油 轻柴油 重柴油 油浆 焦炭 损失
供的操作条件, 对主分馏塔进行了模拟, 塔按工况 1 设计, 并对工况 2 进行了核算。计算表明, 采用 新开发的催化裂化主分馏塔技术完全可以满足装
量, 甚至被迫停工。还有柴油抽不上量的问题也
果
, 一直从事石油化工传质领域的研究, 并取得多项专利和 成
, 联系电 0 9 4 7 1 一 1g y e @ . 话: 7一8 4 ; 、 ; o i 1 二 3 84 E w u9 6 f 3
1 6 7.3
3 8 9. 1 2 6 4. 8
27 54 32 东 4.
…53 14 89
3 .7 98
2 .8 38 30 .1 35 .6
28 .7 4.5 9 56 .5
0. 4 3
8 7. 1
0. 01
56 .8
0.0 0
第3ห้องสมุดไป่ตู้期
高有飞等. 催化裂化主分馏塔扩能改造
油浆中 30 5℃含量下降。 从表4 可以看出, 本次分馏塔改造效果良 好, 明显改善, 具体表现在以下几个方面: () 1分馏塔处理能力大幅提高。在液化石油 气产 率 由改 造 前 的 1. 提 高 到 目前 的 7 6% 3 2. %, 00 汽油回炼增加 2 t 2 0 / h的情况下, 装置处 理量达到了 1 . t , 11 M/( 3 5 合 . t 按每年 8 0 7 / h 6 a 40 h 计算)分馏塔仍操作正常, , 且不用出重柴油。 20 年 3 9 04 一 月平均处理量为 1 . /, 3 3 t 而期间 3 6 h 加工每吨原料的利润为 36 B 单从增加处 2 R Y, M 理量方面, 每年可净增效益 2 1.x 0R B 055 ' M Y。 1 () 2在处理量增加, 液化石油气收率提高 23 . 9 个百分点, 汽油回炼量增加 2 t 的情况下, 0 / h 从沉
28 7
对于分馏塔结盐问题, 从工艺角度看, 操作应
尽量使原料的盐浓度低于3 L塔顶冷回流温 m/, g
度从4℃提高到 69。本次设计, 5 0 0 塔上段采用的 传质元件为抗堵性能良好的TD 塔盘和 LG FJ V塔 盘, 轻度结盐对其影响不大。本次改造, 顶循段塔 盘的操作上限明显提高, 在适当情况下, 可以进一
原来, 催化裂化主分馏塔存在柴油经常抽出 不上量的问题, 这可能与操作负荷较低, 抽出层塔 盘漏液有关。粗汽油回炼后, 这种情况估计会有 所减轻。某些情况下, 抽出斗设计不合理, 也会发 生这种情况。故本次设计考虑将柴油抽出层塔盘 改为导流浮阀塔盘以改善该层塔盘的操作状态。 对于回炼油段, 本次设计采用抗堵性较好的 LG塔盘, V 以缓解该段的结焦问题。
0 0
66 .5 7 3 4.5 1 .0 90
1 3 4. 6
9 .8 36
2 9 3.4
8 .4 56 00 .0
0的 .
17. 3 5 4.8 7
0. 8 6
10 0 0 .0
36 .2 04 .5
10 0 0 .0
34 .8 05 .0 2 .2 00
2 功 31 3. 6. 7. 仓
:2l 朋 62 24 12 43
3 改造效果
的气体是水平的, 防止了液体的返混, 改善了汽液 接触, 浮阀阀腿前端的导流孔, 使气流的推液作用 加强了, 也使阀间区域液体得到活化, 塔板性能得 到了较大的改善。与普通浮阀相比, 压力降可降 低 1%一 5 汽相负荷下限降低 1 , 5 2%, / 汽相负荷 3 上限提高 1%一 5 塔盘效率提高5 0 2%, %以上。 TD 塔盘具有结构简单、 FJ 液体通量大、 塔板效 率较高以及抗堵性能好等特点。 LG塔盘具有结构简单、 V 液体通量大、 压力降
低以及抗堵性能好等特点。 在改造过程中, 为适应新的塔盘方位, 对塔的
装置改造后, 为了考察效果, 20 年 4 于 04 月 1- 6日 4 1 对该装置进行了 标定。改造前后装置物 料平衡的对比列于表4 0
表4 改造前后装置物料平衡对比 一一一一一一一一一 配 ] 一一 1 U 一一改 后 造
满足该段流体力学的要求。针对这一情况, 采用 高效导流浮阀塔盘、FJ TD 塔盘、 G L 塔盘的成套组 V 合技术, 成功地将视为没有扩能余地的中国石化 武汉分公司 I 套重油催化裂化装置主分馏塔的处 理能力由原来的 1 6 a . t 提高到 11 M/o 0 M/ . t 6 a