催化裂化主分馏塔的模拟策略与用能分析优化
催化裂化装置稳定塔操作优化分析

总第191期2021年第1期山西化工SHANXI CHEMICAL INDUSTRYTotal191No.1,2021奏题讨谑DOI:10.16525/l4-1109/tq.2021.01.38催化裂化装置稳定塔操作优化分析李晓琰(中国石化洛阳分公司,河南洛阳471012)摘要:催化裂化装置液化气C5含量指标$3%,稳定汽油饱和蒸汽压指标随季节变化,两者有着密切的联系。
对催化裂化装置稳定系统进行工艺分析,分析影响稳定塔操作的主要因素,讨论稳定汽油饱和蒸汽压与液化气C5含量之间的关系,总结操作规律,实现操作优化及产品质量控制。
关键词:催化裂化;稳定塔;饱和蒸汽压;液化气C5含量中图分类号:TQ053.5文献标识码:B文章编号:1004-7050(2021)01-0105-03引言汽油和液化气是催化裂化装置主要产品,饱和蒸汽压作为稳定汽油的重要控制指标,与液化气C5含量之间既互相关联又互相影响⑴。
稳定塔是保证汽油性能的关键因素之一,在保证稳定汽油饱和蒸汽压与液化气C5含量符合指标的前提下,尽可能提高高价值产品的产量。
稳定塔为多变量控制,可通过分析该塔各影响因素,优化操作指标,增强产品质量控制,提高装置整体经济效益[沁。
1稳定系统工艺流程某厂2#催化裂化装置稳定塔工艺流程简介:脱乙烷汽油进料自压与稳定汽油换热后进入稳定塔,塔底重沸器由分懈一中系统供热,G以下轻组分从稳定塔顶流出,塔顶油气经换热冷却后进入顶部液化气回流罐,一部分作为冷回流打入稳定塔顶层,另一部分送至液化气脱硫系统。
塔底稳定汽油经换热冷却后分两路,一路打入吸收塔顶作补充吸收剂,另一路送至汽油吸附脱硫装置。
2稳定塔工艺操作对各产品质量的影响稳定塔主要工艺参数有塔顶温度、塔顶压力、塔底温度及回流量等,因两产品质量有十分直接的联系,某一个参数或条件变化,均会影响全塔气液、物 料和热量平衡,进而影响产品质量控制,下面针对这些主要工艺参数及影响因素进行分析。
某石化厂气体分馏装置工艺的模拟优化

《化工过程模拟与优化》设计报告某石化厂气体分馏装置工艺的模拟优化指导老师:钱宇教授学生:吕向红王政2001.12.22某石化厂气体分馏装置工艺的模拟优化摘要针对某石化厂气体分馏装置工艺流程进行了模拟计算,分析并提出了降低各塔热负荷的优化方案,进行了优化计算,并与优化前进行了比较,结果表明,优化方案可行并有效,减少了热负荷,提高了经济效益。
关键词气体分馏丙烯优化方案热负荷提高效益一.前言近20多年来,受两次能源危机的影响和经济全球化的制约,我国炼油企业的节能工作逐渐向广度和深度发展,取得了很大的成绩,主要工艺装置的能耗大大降低,如常减压蒸馏、焦化等,国内先进装置的能耗基本接近世界先进水平,但从炼油厂的整体来看,加工单位原油的能耗还比国外高出不少,具体表现在全厂的蒸汽动力系统、原料和产品储运系统及其它系统(包括厂区采暖、空调等等)能耗高,主要原因是全厂各工艺装置间及装置与这些系统间缺乏热联合,缺乏对大系统能源的总体优化利用的考虑。
丙烯是重要的化工原料,近年来随着聚丙烯工业的发展和车用液化气的不断推广应用,市场对高纯度丙烯、丙烷的需求日趋扩大。
优化操作并合理回收丙烯,得到高纯度丙烯可带来可观的经济效益。
充分利用已有设施,通过方案优化,在不改变主产品丙烯纯度的条件下,减少各塔热负荷用量,从而减少共用工程用量,提高生产过程的经济效益,具有较大的意义。
本模拟优化设计是应用Aspen Plus化工模拟软件针对广州某石化厂实际气体分馏的工艺装置而进行的模拟优化工作。
二.流程描述本流程是某石化厂气体分馏装置工艺流程,1985年设计投入使用,原料是来自催化裂化装置的液化气(气体组成如表2.1所示),液化气由蒸气加热器B1预热到87℃,由泵打入脱丙烷塔B2,操作压力20KG/cm2,温度48℃,塔顶产物为乙烷、丙烷和丙烯的混合物(组成见表2.2),塔底产物碳四、碳五组分,组成见表2.3 。
B2塔顶馏出物进入脱乙烷塔B3,在压力为30Kg/cm2、温度59℃下操作,塔顶主产物为乙烷,组成见表 2.4,塔底产物主要为丙烷和丙烯,组成见表 2.5。
中压加氢裂化装置分馏塔的控制及流程优化方法
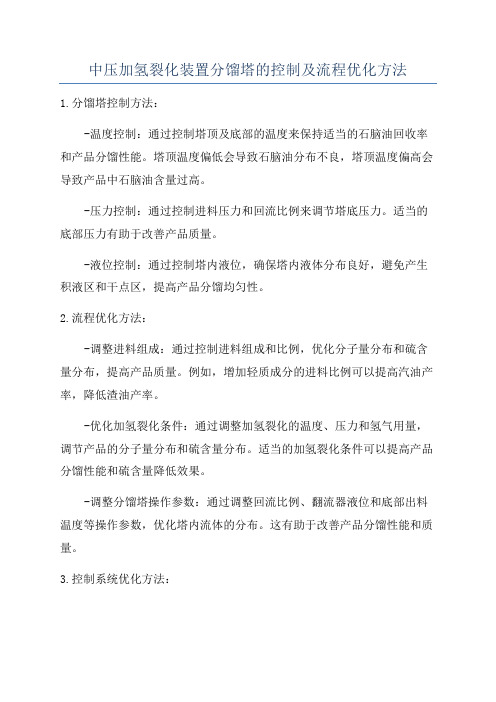
中压加氢裂化装置分馏塔的控制及流程优化方法1.分馏塔控制方法:-温度控制:通过控制塔顶及底部的温度来保持适当的石脑油回收率和产品分馏性能。
塔顶温度偏低会导致石脑油分布不良,塔顶温度偏高会导致产品中石脑油含量过高。
-压力控制:通过控制进料压力和回流比例来调节塔底压力。
适当的底部压力有助于改善产品质量。
-液位控制:通过控制塔内液位,确保塔内液体分布良好,避免产生积液区和干点区,提高产品分馏均匀性。
2.流程优化方法:-调整进料组成:通过控制进料组成和比例,优化分子量分布和硫含量分布,提高产品质量。
例如,增加轻质成分的进料比例可以提高汽油产率,降低渣油产率。
-优化加氢裂化条件:通过调整加氢裂化的温度、压力和氢气用量,调节产品的分子量分布和硫含量分布。
适当的加氢裂化条件可以提高产品分馏性能和硫含量降低效果。
-调整分馏塔操作参数:通过调整回流比例、翻流器液位和底部出料温度等操作参数,优化塔内流体的分布。
这有助于改善产品分馏性能和质量。
3.控制系统优化方法:-采用先进的控制算法:使用先进的控制算法如模型预测控制(MPC)和模糊控制等,对分馏塔进行优化控制。
这些控制算法可以实时监测、预测和调节分馏塔的运行状况,并根据设定的优化目标进行调整。
-数据驱动的优化:利用先进的计算机软件和数据分析技术,对分馏塔的运行数据进行分析和建模,寻找操作参数和产品质量之间的关联规律。
通过对这些关系的深入了解,可以优化分馏塔的控制策略和操作参数。
中压加氢裂化装置分馏塔的控制及流程优化是一个复杂的工作,需要综合考虑许多因素。
上述提到的方法只是其中的一部分,具体的优化方法需要根据实际情况进行深入研究和实践,持续改进,以提高装置的运行效率和产品质量。
优化分馏塔操作,提高催化装置处理量

优化分馏塔操作,提高催化装置处理量【摘要】分馏单元作为催化装置的“中枢”单元,在催化装置生产过程中起到了“承上启下”的作用,分馏单元的平稳操作将对催化整体处理能力及产品质量起着重要的作用。
【关键词】分馏塔;平稳操作;冲塔;柴油抽不出前言催化裂化装置是炼化企业的重要装置之一。
实践证明,在炼油市场经济化的今天,作为原油深加工的龙头装置,催化裂化装置的平稳运行将直接影响企业的经济效益。
一、分馏操作存在的问题催化裂化装置自两段提升管改造以来达到了设计的20万吨/年的处理量。
但分馏岗位一直存在操作不平稳的情况,影响了催化装置安全生产并限制了催化装置的处理能力,对装置的挖潜、增效启到了阻碍作用。
通过对分馏岗位的深入调查分析得出结论认为是中段油与油浆换热流程不太合理导致分馏塔温度梯度分布不合理以致分馏岗位操作经常大幅波动。
因此我们决定把“改造中段油与油浆系统换热流程,提高分馏操作平稳率”作为我们研究的课题二、针对问题的调查分析通过对2012年12月至2013年2月分馏塔的平稳率做了细致的调查,发现影响分馏塔平稳操作主要原因集中在分馏塔冲塔和分馏塔柴油抽不出上。
三、确定主要影响因素通过长时间的深入调查分析得出了影响分馏塔平稳操作的主要问题是分馏塔冲塔和柴油抽不出,而造成这种现象的原因是分馏塔热分配不合理。
根据多年的操作经验和对实际生产的跟踪调查对分馏岗位冲塔和柴油抽不出做了全面的分析,找出主要影响因素:分馏塔塔底负荷大,热量取不出。
我们在生产柴油方案小组成员对分馏塔进行了热平衡计算,分馏塔的取热分配为塔顶:中段:塔底=29:19:52,通过查阅资料在生产柴油方案时分馏塔正常取热分配为塔顶:中段:塔底=19:48:33。
通过比较可以看出分馏塔的取热分配不合理。
我们又对偏差最大中段部位取热进行跟踪和测量。
中段油先到H208与油浆换热温度被升高,然后给稳定系统和蜡油加热最后至H209油浆将温度加热到230℃-240℃后返回到分馏塔。
催化裂化分馏塔动态机理模型与仿真研究

第43卷 第2期厦门大学学报(自然科学版)Vol.43 No.2 2004年3月Journal of Xiamen University(Natural Science)Mar.2004 文章编号:043820479(2004)022*******催化裂化分馏塔动态机理模型与仿真研究收稿日期:2003204230作者简介:周华(1976-),男,硕士.周 华,江青茵,曹志凯(厦门大学化学工程与生物工程系,福建厦门361005)摘要:首先经严格的机理分析给出分馏塔逐板计算的模型,然后采用房室法、虚拟组分法将模型简化.最后对所建立的机理模型进行求解仿真,并给出了仿真结果,通过仿真验证了模型的准确性.关键词:催化裂化;模型;仿真;分馏塔.中图分类号:TQ015.9,TQ202文献标识码:A 复杂化工过程的优化与控制一直是研究热点.采用机理方法建立过程的动态或稳态数学模型并进行仿真模拟,可以了解过程的内在关系和不同因素对过程的影响.由于化工过程大都非常复杂,过程动态机理建模一直是难题[1].催化裂化装置是石油二次加工的重要装置,由反应再生、分馏及稳定装置组成.在催化裂化反应-再生建模与优化控制方面,本实验室已经做了大量的研究工作[2,3],故本文只讨论分馏塔的建模和仿真.催化裂化分馏塔所处理的是包含了无数沸点相近、受反2再工况的反应深度影响的复杂混合物,进入分馏塔的热量也由反2再工况决定.本文在借鉴目前研究较为成熟的精馏塔及各种常减压分馏塔动态模型[4~12]的基础上,结合催化裂化分馏塔的流程特点,运用虚拟组分和房室法[13],对逐板计算模型进行简化处理,全塔分成5个等效的塔段并假设有5个虚拟组分,分别列出每段组分的质量和能量的连续性方程.建立了以液相组分与塔段温度为主要状态变量,塔段的液相滞留量为辅助变量,由若干微分方程和代数方程组成的全塔模型,并对模型进行仿真研究,从而分析验证模型的准确性.1 工艺描述催化裂化装置对一次加工后的重油(腊油、渣油)进行裂化反应,反应油气进入分馏塔,在分馏塔中经过脱过热段和循环回流取热后得到不同的成品油产物.催化裂化分馏塔(见图1)是一个耦合严重、非线性、不确定性强的复杂的工业装置,其控制水平的高低直接影响产品的分布及质量;它具有以下工艺特征[14]:1)分馏塔底设有脱过热段,处理物料为复杂混合物;2)塔顶多采用循环回流,有侧线抽出;3)大量采用中部循环回流来控制各段温度;4)从塔底进料,进料为过热油气. 图1 催化裂化分馏塔12回炼油罐;22泵;32换热器;42分馏塔;52冷却器;62粗汽油罐;72汽提塔 Fig.1 FCCU fractionator2 分馏塔动态机理建模在分离工程和物理化学等学科对分离过程的内在机理、热力学计算、工艺参数计算等研究的基础上,综合全塔的物料平衡、能量平衡、相平衡、组分平衡等方程,可得出分馏塔的逐板计算的全塔动态模型.为简化计算,依据生产工艺的实际情况提出以下几条假设:1)每块塔板上的液相充分混和;2)每层塔板上的汽相滞留量忽略不计;3)同层塔板内温度均匀;4)离开塔板的液相组分与塔板上液相滞留量的组分相同;5)各板的热量损失忽略不计;6)侧线以液相形式抽出;7)忽略汽液相温差引起的传热,只考虑汽液相传质引起的潜热变化;8)进行各种衡算时将物料分为汽相和液相两个对象进行考虑.分馏塔中塔盘的汽液流程图如图2所示,基本上代表了每块塔板的情况,对于图2所示的第j 层塔板的第i 个组分,其逐板计算的动态模型可由以下几组方程描述:液相物料平衡方程: 图2 分馏塔中各塔盘的物料流示图 Fig.2 Diagram of input 2output streams for plate j inFCCU fractionatord M jd t=L j -1+L F -L o -L j +N tj(1)液相组分平衡方程:d (M j x ij )d t=L j -1x ij -1+L F x iF - L o x io -L j x ij +N ij (2)液相能量平衡方程:d (M j H j )d t =L j -1H j -1+L F H F - L o H o -L j H j +E tj(3)气相物料平衡方程(忽略气相动态滞留量):V j -V j -1-N tj +V F =0,N tj =∑ci =1N ij(4)气相组分平衡方程:V j x ij -V j -1x ij -1-N ij +V F x iF =0(5)气相能量平衡方程:V j h j -V j -1h j -1-E tj +V F h F =0(6)组分加和方程:∑ci =1x ij =1(7)∑ci =1y ij =1(8)焓值计算方程[15,16]:H ij =αi +βi T j(9)h ij =γi +δi T j(10)汽液相热量传递方程:E tj =∑ci =1N ij h ij(11)汽液传质速率方程:N ij =K G ij (y ij -K j x ij )(12) 图3 转化率升高对各组分含量以及温度的影响B 2塔底液相汽油含量;C 2塔底液相柴油含量D 2塔度液相油浆含量;E 2塔底液相回炼油含量 Fig.3 Inf luences on dif f erent com ponents and operat 2ing tem peratures af ter a step change (f rom 0.40to 0.45)in conversion rate式中K G ij 为传质系数,其计算参见文献[17],式(12)中相平衡系数K j 的计算参见文献[18].压力衡算方程(由p =RV n T 推导):d p d t =R V (T d n d t +nd Td t)(13)式中d nd t由式(1)和式(13)联立可以求解.塔板水力学计算参照文献[19]所给定的有关公式,有关符号说明参见附录A .式子(1)~(10)为图2所示的有N 层塔板的逐板计算模型,式(9)和(10)表示每层塔板的液相焓和汽相焓,这些焓值都是塔板温度的函数.・812・厦门大学学报(自然科学版) 2004年如果不做任何简化,一个分馏塔有几十层塔板,假设有10个组分(催化裂化分馏塔实际上不只这些组分),采用逐板计算方法将会产生几百个非线性微分方程和几百个代数方程,这给模型的求解和仿真带来很大困难,且很难满足工业实时计算的要求.表1 虚拟组分焓值计算方程参数表Tab.1 Parameters def ined in the enthalpy equation of pseudo com ponentsZX Y A 00A 01A 02×102A 10A 11×102A 12×102 H 3L T 3A PI 3.81920.2483-0.27060.37180.19720.4754 H 33VT 3A PI 78.12120.3917-0.16540.30590.09960.4630 H V 2T K 24.2206-20.517158.570.8627-7.55000.0672 G V 1H V K -1557.44408.443-1906.32-4.66634.8260.1010 G V 2G V 13A PI 512.06-8.6401-3.016-0.24971.8720.5582 H V 1G V 2P24.47-0.33270.0129-0.15780.17620.2387 H L ,HV 2分别为液、汽相焓,千卡/公斤;P 2系统压力,公斤/厘米3;T 2体系温度,℃;K 2特性因数;3A PI 2比重指数.为简化模型,针对催化裂化分馏塔的实际情况,将有32块塔盘的分馏塔分为5个块(j =1,2,3,4,5),即采用房室法处理,突出有物料进入、侧线抽出的塔盘以及3个循环取热回流的塔盘的计算.将分馏塔内的物料按其产品划分为5个虚拟组分(c =5),即汽油、柴油、回炼油、油浆、富气.其中富气在塔内为不凝气,在液相中不予考虑.另外虚拟组分焓值计算方程[20]如下:Z =∑2i =0∑2j =0A ij X i Y j (i +j ≤2)(14)其中Z ,A ij ,X ,Y 的值见表1.虚拟组分分子量的计算采用石油大学提出的经验式,该式不仅适合直馏馏分,也适用二次加工产物.M i =a +b T +c KT +d (KT )2+e ρT (15)其中参数a ,b ,c ,d ,e 的值源于文献[21],式中:T -馏分的中平均沸点,K;K -馏分的特性因数;ρ-馏分油20℃时的密度,g/cm 3;a =184.5,b =2.2945,c =-0.223,d =0.133853×10-4,e =-0.62217.进料汽相或者液相的平均分子量的计算:M L =∑ci =1x i M i(16) M L =∑c i =1y i M i(17)上述5个分段4个虚拟组分(富气当作不凝气处理)的简化模型共包含若干微分方程和代数方程,采用四阶Runge 2Kutta 法求解,求解时设反应转化率的初值均为0.40,考察转化率降低及转化率升高 图4 转化率降低对各组分含量以及温度的影响B 2塔底液相汽油含量;C 2塔底液相柴油含量D 2塔底液相油浆含量;E 2塔底液相回炼油含量F 2进料转化率:G 2塔底段温度 Fig.4 Influences on different components and operatingtemperature after a step change (from 0.40to 0.35)in conversion rate对全塔组分和温度的影响,图3为转化率阶跃减少0.05的仿真结果,图4为转化率阶跃增加0.05的仿真结果.从图3、4中可以看出,当进料转化率升高,轻组分含量增加,重组分含量降低,塔底段温度升高,当转化率降低时,轻组分含量减少,重组分含量增加,塔底段温度降低.提高转化率有利于提高重油加工过程的轻质油收率.上述仿真结果与工业过程实际情况相符,说明本文给出的动态机理模型可以较好的反映实际工业装置的动态特性.3 结 论采用房室法和虚拟组分法建立催化裂化分馏塔动态数学模型,并进行了裂化反应转化率对分离过・912・第2期 周 华等:催化裂化分馏塔动态机理模型与仿真研究程影响的仿真,得到的仿真结果与实际相符.附录A 符号说明:M 2液相物料积累量 L 2液相流量 N 2传质量x 2液相组分摩尔分率 h 2气相焓值H 2液相焓值E 2传热量V 2气相流量y 2气相组分摩尔分率 M 2平均分子量下标:L 2液相 v 2气相 i 2组分 j 2塔段或者塔板参考文献:[1] 王骥程.过程动态模型[M ].杭州:浙江大学出版社,1994.[2] 江青茵,曹志凯,陈紫鸾.催化裂化提升管反应器不可测输入的在线观测[J ].化工学报,2003,54(2),204-208.[3] 江青茵.催化裂化装置优化控制系统[P ].中国专利:Z L 95115925.9,200026224.[4] Drozdowicz B ,Martinez E.Reduced models for separa 2tion processes in real 2time simulations [J ].Comput.Chem.Engng.,1988,12(2):547-560.[5] 杨健,钱积新,周春晖.非理想多元物系精馏塔动态数学模型[J ].化工学报,1990(1):103-110.[6] Revaglio M ,Ranzi E ,Biardi G ,et al.Rigorous dynamicsand control of continuous distillation systems :Simulation and experimental results [J ].Comput.Chem.Engng.,1990,14(8):871-887.[7] G ani R ,Ruiz C A ,Cameron I T.A generalized modelfor distillation columns 2I :Model description and applica 2tions[J ].Comput.Chem.Engng.,1986,10(3):181-198.[8] G ani R ,Ruiz C A ,Cameron I T.A generalized modelfor distillation columns 2II :Model description and applica 2tions[J ].Comput.Chem.Engng.,1986,10(3):199-211.[9] 于静江,高衿畅,周春晖.大型原油蒸馏塔的模型化及控制[J ].工业过程模型化与控制,1991(4):65-171.[10] Lang P ,Szalmas G ,Chinkany G ,et al.Modelling of acrude distillation column[J ].Comput.Chem.Engng.,1991,15(2):133-139.[11] 张亚乐,徐博文,方崇智,等.常压蒸馏塔的严格在线模型与仿真研究[J ].石油炼制与化工,1997,28(6):41-46.[12] 郑远扬,郝富军.催化裂化分馏塔动态仿真数学模型和算法[J ].化工学报,1994,6(45):704-711.[13] Morari M ,Stephanopoulos G.Studies in the synthesisof control structures for chemical processes ,part II :Structural aspects and the synthesis of alternative feasi 2ble control schemes[J ].AIChE J ,1980,26(2):232-260.[14] 林世雄.石油炼制工程(下)[M ].北京:石油工业出版社,1994.326.[15] 王松汉.石油化工设计手册(石油化工基础数据)[M ].北京:化学工业出版社,2001.909-987.[16] 石油大学炼制系.石油炼制及石油化工计算方法图表集[M ].山东东营:石油大学出版社,1997.501-509.[17] Krishnamurthy R ,Taylor R.A nonequilibrium stagemodel of multicomponent separation column process :parison with experiments[J ].AIChE J ,1985,31:449.[18] 郭天民.多元汽-液平衡和精馏[M ].北京:化学工业出版社,1983.[19] 化学工程手册编辑委员会.化学工程手册(第三卷)[M ].北京:化学工业出版社,1989.177-181.[20] 林世雄.石油炼制工程(上)[M ].北京:石油工业出版社,1994.100.[21] 梁文杰.石油化学[M ].山东东营:石油大学出版社,1995.97.Dynamic Mechanics Model &Simulation forCatalytic Cracking FractionatorZHOU Hua ,J IAN G Qing 2yin ,CAO Zhi 2kai(Dept.of Chemical and Biochemical Engineering ,Xiamen University ,Xiamen 361005,China )Abstract :This paper discusses the dynamic modeling for the fractionator of Fluidized Catalytic Cracking Unit(FCCU ).In this modeling ,compartment method is adopted and the products of the catalytic cracking are de 2scribed as five pseudo components.The simulation results show that this dynamic model can predict the dynamic responses of each compartment when the operating conditions of the fractionator are changed.K ey w ords :catalytic cracking ;dynamic model ;simulation ;fractionator・022・厦门大学学报(自然科学版) 2004年。
石油化工催化裂化技术的工艺优化分析

石油化工催化裂化技术的工艺优化分析发布时间:2023-03-03T08:56:47.868Z 来源:《科技新时代》2022年第20期作者:王中亮杨立志[导读] “三油并轨”政策的实施和车用柴油标准的升级将进一步减少污染物的排放王中亮杨立志中国石油哈尔滨石化公司第二联合车间 150056摘要:“三油并轨”政策的实施和车用柴油标准的升级将进一步减少污染物的排放,保护环境,并推动发动机企业技术进步和炼油企业转型升级。
例如,车用柴油国Ⅵ质量标准要求大幅降低柴油的硫含量和多环芳烃含量,这将使催化裂化柴油(LCO)占比较高的炼油企业面临巨大技术经济挑战。
这是因为LCO的总芳烃质量分数为50%~70%,且双环芳烃占比很大,为总芳烃的40%~60%;同时LCO的硫、氮等杂质含量高、十六烷值低,难以直接作为柴油馏分,必须进一步深入加工才能满足国Ⅵ柴油质量标准的要求。
LCO深加工技术主要有加氢精制、加氢改质等技术。
通过加氢,可以脱除LCO中的硫和氮元素,但LCO加氢过程需要高苛刻度的工况条件,氢耗高、操作成本高、经济效益差。
同时,随着消费柴汽比的不断下降,炼油企业间的竞争不断加剧,为LCO加工路线的选择带来巨大挑战。
因此,探寻最优LCO加工路径,实现低成本提升LCO经济价值成为研究热点。
关键词:催化裂化;低辛烷值汽油;辛烷值引言我国FCC汽油为商品汽油的主要组分,其在商品汽油中的比例达70%以上,无论目前还是可预见的未来,FCC汽油在炼油厂中的重要地位不容置疑。
FCC汽油性质明显优于热裂化汽油,而且,稳定性要比热裂化汽油高得多,各种烃类在FCC汽油中大致分为正构烷烃约5%,异构烷烃在25%~33%之间,环烷烃在6%~12%之间,烯烃在33%~46之间,芳烃在16%~22%之间。
高辛烷值汽油能够提高发动机的功率和热效率,提高汽油辛烷值已经成为各汽油生产单位的主要努力方向。
粗汽油作为终止剂在催化裂化装置上进行工业应用已经取得了不错的效果,能够抑制氢转移二次反应和减少热裂化反应,提高重油催化裂化的轻质油和液化气收率,降低干气和焦炭产率。
加氢裂化装置分馏塔的模拟优化_李宗雯

6.6% 0
4.9% 2.2% 5.1% 1.4% 0.9% 3.2% 1.1%
2.2 灵敏度分析 对建立好的模型进行灵敏度分析,得出各产
品干点随着操纵变量的关系,进而得出最优的操 作变量,表2为加热炉温度的变化导致的各产品干 点的变化。
表2 加热炉温度对产品干点的影响
加热炉温度 ℃
LDRY ℃
HDRY ℃
LDRY ℃
HDRY ℃
DDRY ℃
15
75.69428
138.7914
267.1454
16.44444
75.73402
140.3815
274.1683
17.88889
75.77844
148.6977
279.5347
19.33333
75.83418
155.4447
286.8893
20.77778
75.89836
图2 ASPEN PLUS模拟流程图
C-52:主分馏塔 FEED:混合进料 STM1:脱硫化氢汽提塔汽提蒸汽 GAS:干气 SWATER1:脱硫化氢汽提塔蒸馏水 LG:液化气 B1:脱硫化氢塔底出料 STM2:主分馏塔汽提蒸汽 SWATER2:主分馏塔蒸馏水 LIGHT:轻石脑油 HEAVY:重石脑油 DIESEL:柴油 BOTTOM:裂化尾油
190.6263
359.5876
28
76.21742
196.9634
369.784
【8】 第35卷 第5期 2013-05(下)
从表3中可以看出,随着重石脑油抽出量增 大,各产品干点均出现上升趋势,轻石脑油的干 点上升的较小,重石脑油的干点上升较大,柴油 干点上升尤为显著。主要原因是因为随着重石脑 油抽出量的提高,塔内液相负荷减小,气相负荷 增大,各产品抽出温度升高,各产品干点上升。
流程模拟技术优化Ⅱ套催化装置分稳系统操作

流程模拟技术优化Ⅱ套催化装置分稳系统操作朱向阳谢晓东中石化股份有限公司九江分公司催化车间江西九江332004摘要:介绍流程模拟在九江分公司Ⅱ套催化裂化装置应用情况,包括建模、调试和应用情况。
通过离线调优,来指导生产操作,并取得较好经济效益。
关键词催化裂化装置分稳系统流程模拟建模前言中国石化股份有限公司九江分公司Ⅱ套催化装置建模项目于2006年2月份启动,2006年3月份派技术员到燕山石化学习。
为了对模型进行验证和在实际生产中进行应用,九江分公司的工程师于2006年4月17日至2006年4月26日在石化盈科上海分公司进行模型的初步验证和测试工作。
2006年全面核算了Ⅱ催分馏系统及吸收稳定系统各塔的气液相负荷、换热器负荷,整个分馏、稳定系统的物料平衡。
实际操作中调整了Ⅱ催分馏塔顶冷回流和塔底温度及各中段回流热负荷的分配、吸收塔补充吸收油流量、稳定塔顶压力、冷回流和塔底温度,取得了比较满意的效果。
2007年~2008年,继续加强了流程模拟技术在Ⅱ催装置上的应用,主要工作为在2006年应用的基础上,进行更接近生产实际的模拟,以找出装置瓶颈。
1装置概况九江分公司Ⅱ催装置是洛阳院设计、处理能力为1Mt/a的重油催化裂化装置,采用反应-再生高低并列式布置的两器形式,设内提升管反应器,再生器二段再生的结构。
1997年9月投入运行。
1999年装置进行MGD技术改造,新增汽油回炼。
2004年进行MIP-CGP技术改造,改造为外提升管、二段反应。
改造后,液化气产率有较大幅度的增加。
装置主要存在问题有:干气流量超过7000Nm3/h,容易出现带液现象;稳定系统、尤其是稳定塔负荷超过设计能力。
装置设有与催化裂化装置相配套的产品精制系统。
2模拟过程2.1模型条件以标定数据为建模基础,包括诸物流和单元的物料、热量和操作条件等数据。
同时以此数据对所建模型作测试,即初步验证。
2.1.1建模数据(1)干气组成见表1。
表1干气组成组成比例,%甲烷17.67氢气36.24氮气20.77二氧化碳 1.6一氧化碳0.98乙烯10.13乙烷8.55丙烷0.27丙烯0.97正丁烷0.22异丁烷0.67正丁烯0.12反-2-丁烯0.18异丁烯0.12顺-2-丁烯0.06戊烷0.04硫化氢 1.14氧气 1.82合计100流量/(kg·h-1)4570压力/MPa0.21温度/℃490(2)液化气组成见表2。