催化车间-分馏塔
化分馏塔结盐分析及对策

化分馏塔结盐分析及对策【摘要】随着炼油厂原料的日益重质化,原油结构的劣质化,原油中所含为s、n等元素增多,即加大了电脱盐装置的处理难度,又对下游装置平稳长周期运行增添了许多风险,为了获取更高的轻质油收率和经济效益,延迟焦化装置作为炼厂重油加工的主要装置,其地位日趋重要。
如何保证延迟焦化装置的安、稳、长周期运行也成为炼厂的重点技术课题。
本文结合玉门炼化总厂延迟焦化装置生产波动及分馏塔内部结盐的现状,对分馏塔结盐的原因进行了分析,提出了解决分馏塔结盐的适用方法。
【关键词】原油劣质化延迟焦化结盐1 前言严格执行现场巡回检查制度,加强关键、要害部位的运行监控,加大装置对辐射进出口管线、转油线、热油泵房等高温部位的监控检查力度,严格执行冬季安全生产要求和操作规程,防止冻凝管线,及时发现和处置异常情况,认真执行设备运行维护制度,加强设备基础管理,保证设备本质安全。
车间采取有力措施保障了装置安全生产,但是在最近两个月出现了操作平稳率和产品质量波动。
2 塔内部结盐的原理及波动原因受常减压装置电脱盐不彻底或油田在原油开采过程中使用助剂等原因的影响,以及我装置回炼污油代替蜡油做急冷油使用,致使焦化原料中含有较多的氮化合物等成分,由此在延迟焦化装置生产过程中在分馏塔及塔顶冷却器等部位结盐(结垢),导致分馏系统工艺操作困难。
延迟焦化原料携带的氮化合物在焦炭塔反应过程中,会生成n2、nh3、h2s、hcl和o2等产物。
nh3与hcl反应生成nh4cl。
氯化铵极易溶于水,在分馏塔的下部,nh4cl分解为nh3和hcl,遇冷后则重新生成nh4cl颗粒。
细小的nh4cl颗粒在分馏塔的上部,可溶解在局部低温水相中,在随内回流下降的过程中,温度逐步升高,nh4cl逐步失水而浓缩成为一种粘度很大的半流体。
这种半流体与铁锈、焦炭粉末等混合在一起沉积于塔盘、塔顶回流线、降液管、汽油线、受液盘处,积累到一定程度就会阻碍液体的流动,堵塞塔盘上的孔,导致分馏塔压降逐渐增大,破坏了分馏塔的正常操作。
中级催化裂化装置操作工考试题库及答案
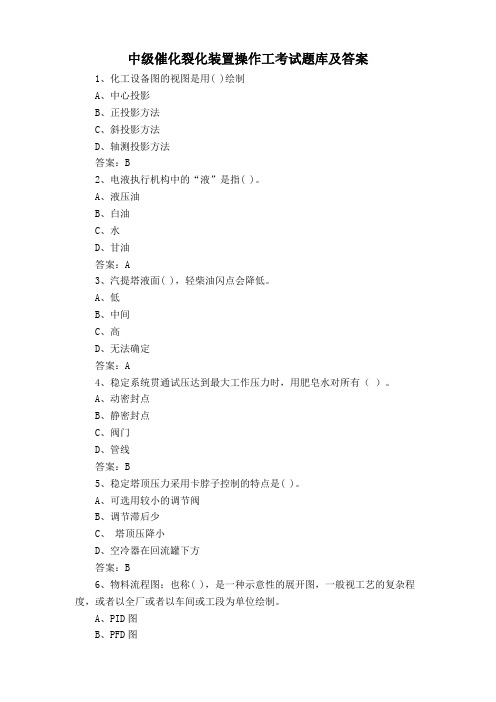
中级催化裂化装置操作工考试题库及答案1、化工设备图的视图是用( )绘制A、中心投影B、正投影方法C、斜投影方法D、轴测投影方法答案:B2、电液执行机构中的“液”是指( )。
A、液压油B、白油C、水D、甘油答案:A3、汽提塔液面( ),轻柴油闪点会降低。
A、低B、中间C、高D、无法确定答案:A4、稳定系统贯通试压达到最大工作压力时,用肥皂水对所有()。
A、动密封点B、静密封点C、阀门D、管线答案:B5、稳定塔顶压力采用卡脖子控制的特点是( )。
A、可选用较小的调节阀B、调节滞后少C、塔顶压降小D、空冷器在回流罐下方答案:B6、物料流程图:也称( ),是一种示意性的展开图,一般视工艺的复杂程度,或者以全厂或者以车间或工段为单位绘制。
A、PID图B、PFD图C、PDF图D、PAD图答案:B7、适当降低解吸塔压力,液态烃中C2组分含量()。
A、上升B、下降C、不变D、无法确定答案:B8、以下选项中,不属于分馏塔冲塔的现象的是()。
A、油品颜色变深B、油品比重增大C、顶温迅速上升D、油品变轻答案:D9、对带有干气预提升的催化裂化装置,干气带凝缩油会影响( )。
A、反应操作B、气压机操作C、稳定操作D、精制操作答案:B10、分馏系统建立三路循环升温过程中,当温度达到( )时,进行恒温。
A、100~110℃B、110~120℃C、120~130℃D、130~140℃答案:A11、辅助燃烧室点火前要调好一、二次风比例,百叶窗开全程的( )。
A、全开B、1/2C、1/3D、全关答案:C12、提升管喷汽油时,要控制分馏塔顶温度比正常时( ),因为此时油气分压变了。
A、高B、低C、不变D、没有要求答案:A13、精馏操作过程必须具备的条件不包括( )。
A、混合液各组分相对挥发度不同B、气液两相接触时必需存在密度差C、塔内有气相回流和液相回流D、具有气液两相充分接触的场所答案:B14、再生器喷燃烧油时,()。
A、床层催化剂必须淹没燃烧油喷嘴B、再生器内必须有催化剂C、床层催化剂接近燃烧油喷嘴就行D、再生器内无须有催化剂答案:A15、增加生成物的浓度或减小反应物的浓度,有利于逆反应的进行平衡( )。
催化裂化装置工艺流程及设备简图
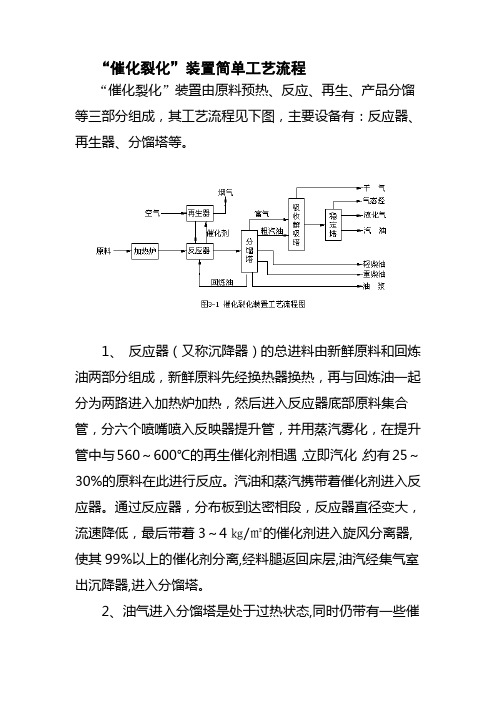
“催化裂化”装置简单工艺流程“催化裂化”装置由原料预热、反应、再生、产品分馏等三部分组成,其工艺流程见下图,主要设备有:反应器、再生器、分馏塔等。
1、反应器(又称沉降器)的总进料由新鲜原料和回炼油两部分组成,新鲜原料先经换热器换热,再与回炼油一起分为两路进入加热炉加热,然后进入反应器底部原料集合管,分六个喷嘴喷入反映器提升管,并用蒸汽雾化,在提升管中与560~600℃的再生催化剂相遇,立即汽化,约有25~30%的原料在此进行反应。
汽油和蒸汽携带着催化剂进入反应器。
通过反应器,分布板到达密相段,反应器直径变大,流速降低,最后带着3~4㎏/㎡的催化剂进入旋风分离器,使其99%以上的催化剂分离,经料腿返回床层,油汽经集气室出沉降器,进入分馏塔。
2、油气进入分馏塔是处于过热状态,同时仍带有一些催化剂粉末,为了回收热量,并洗去油汽中的催化剂,分馏塔入口上部设有挡板,用泵将塔底油浆抽出经换热及冷却到200~3000C,通过三通阀,自上层挡板打回分馏塔。
挡板以上为分馏段,将反应物根据生产要求分出气体、汽油、轻柴油、重柴油及渣油。
气体及汽油再进行稳定吸收,重柴油可作为产品,也可回炼,渣油从分馏塔底直接抽出。
3、反应生焦后的待生催化剂沿密相段四壁向下流入汽提段。
此处用过热蒸汽提出催化剂,颗粒间及表面吸附着的可汽提烃类,沿再生管道通过单动滑阀到再生器提升管,最后随增压风进入再生器。
在再生器下部的辅助燃烧室吹入烧焦用的空气,以保证床层处于流化状态。
再生过程中,生成的烟通过汽密相段进入稀相段。
再生催化剂不断从再生器进入溢流管,沿再生管经另一单动滑阀到沉降器提升管与原料油汽汇合。
4、由分馏塔顶油气分离出来的富气,经气压机增压,冷却后用凝缩油泵打入吸收脱吸塔,用汽油进行吸收,塔顶的贫气进入二级吸收塔用轻柴油再次吸收,二级吸收塔顶干气到管网,塔底吸收油压回分馏塔。
5、吸收脱吸塔底的油用稳定进料泵压入稳定塔,塔顶液态烃一部分作吸收剂,另一部分作稳定汽油产品。
催化裂化装置非计划停工原因分析及
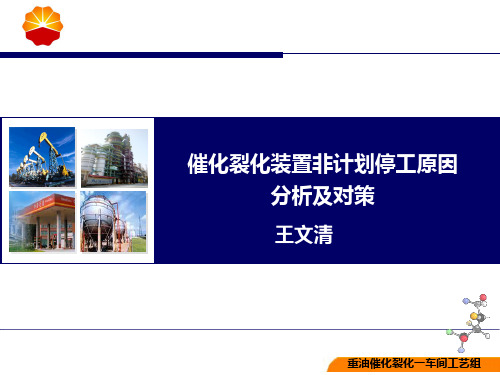
三、催化裂化装置非计划停工原因分析及对策
❖油浆系统结焦 • 油浆系统结焦原因 :
(1)油浆系统性质变差是油浆系统结焦的重要原因; (2)分馏塔温度变化时油浆系统结焦的直接原因。随 着油浆温度的升高,轻馏分逐渐蒸发,油浆浓缩,生焦性 能增加。同时,油浆中的烯烃、多环芳烃产生缩合反应, 当温度升高到一定值时,缩合反应速度会升高得很快。 (3)油浆的停留时间。当油浆在某一高温下停留时间 足够长时,油浆中将有焦炭生成。 (4)油浆流速过低,容易使缩合物沉积在管道表面结焦。
重油催化裂化一车间工艺组
三、催化裂化装置非计划停工原因分析及对策
❖油浆系统结焦 • 防范措施 :
(3)选用气蚀余量较大的机泵,避免油浆泵不上量而 引发大量催化剂沉积在分馏塔底。
(4)选用合适的油浆阻垢剂,从装置投用起连续注入, 防止油浆中不溶物附着在换热器的管壁。
(5)适当的外甩油浆,调节油浆排放物量以降低油浆 相对密度,控制油浆中稠环芳烃浓度。
重油催化裂化一车间工艺组
三、催化裂化装置非计划停工原因分析及对策
❖油浆系统结焦 • 防范措施 :
(6)降低循环油浆返塔温度,加大油浆返塔下 部入口量。用极冷油浆极冷,既可加强对塔底的冲 刷作用,防止催化剂堆积在分馏塔底的缓流区而结 焦,又可使塔底油浆快速降温,防止油浆组分因高 温聚合而结焦。
重油催化裂化一车间工艺组
一般意义的紧急停工是指装置部分设备或工艺生 产在故障状态下紧急切断提升管进料,维持分馏、 稳定部分油品循环,两器进行流化状态。如果设备 或生产故障短时间内解决不了,并有进一步扩大的 趋势,可将装置全面紧急停工。
重油催化裂化一车间工艺组
二、催化裂化装置紧急停工条件及处理原则
催化装置开工方案
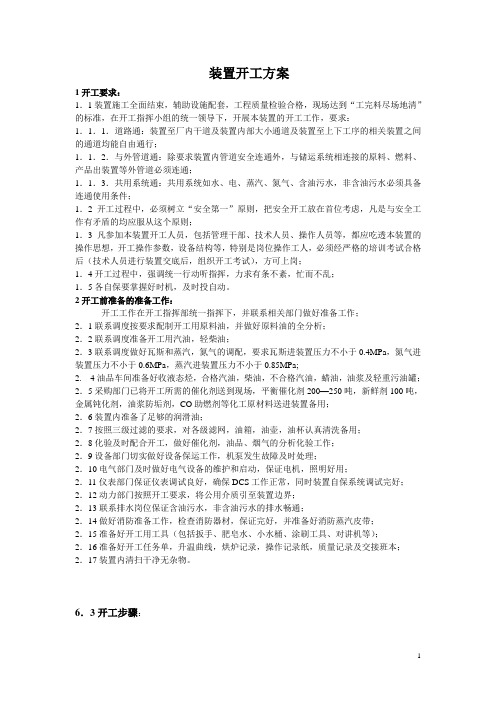
装置开工方案1开工要求:1.1装置施工全面结束,辅助设施配套,工程质量检验合格,现场达到“工完料尽场地清”的标准,在开工指挥小组的统一领导下,开展本装置的开工工作,要求:1.1.1.道路通:装置至厂内干道及装置内部大小通道及装置至上下工序的相关装置之间的通道均能自由通行;1.1.2.与外管道通:除要求装置内管道安全连通外,与储运系统相连接的原料、燃料、产品出装置等外管道必须连通;1.1.3.共用系统通:共用系统如水、电、蒸汽、氮气、含油污水,非含油污水必须具备连通使用条件;1.2开工过程中,必须树立“安全第一”原则,把安全开工放在首位考虑,凡是与安全工作有矛盾的均应服从这个原则;1.3凡参加本装置开工人员,包括管理干部、技术人员、操作人员等,都应吃透本装置的操作思想,开工操作参数,设备结构等,特别是岗位操作工人,必须经严格的培训考试合格后(技术人员进行装置交底后,组织开工考试),方可上岗;1.4开工过程中,强调统一行动听指挥,力求有条不紊,忙而不乱;1.5各自保要掌握好时机,及时投自动。
2开工前准备的准备工作:开工工作在开工指挥部统一指挥下,并联系相关部门做好准备工作;2.1联系调度按要求配制开工用原料油,并做好原料油的全分析;2.2联系调度准备开工用汽油,轻柴油;2.3联系调度做好瓦斯和蒸汽,氮气的调配,要求瓦斯进装置压力不小于0.4MPa,氮气进装置压力不小于0.6MPa,蒸汽进装置压力不小于0.85MPa;2. 4油品车间准备好收液态烃,合格汽油,柴油,不合格汽油,蜡油,油浆及轻重污油罐;2.5采购部门已将开工所需的催化剂送到现场,平衡催化剂200—250吨,新鲜剂100吨,金属钝化剂,油浆防垢剂,CO助燃剂等化工原材料送进装置备用;2.6装置内准备了足够的润滑油;2.7按照三级过滤的要求,对各级滤网,油箱,油壶,油杯认真清洗备用;2.8化验及时配合开工,做好催化剂,油品、烟气的分析化验工作;2.9设备部门切实做好设备保运工作,机泵发生故障及时处理;2.10电气部门及时做好电气设备的维护和启动,保证电机,照明好用;2.11仪表部门保证仪表调试良好,确保DCS工作正常,同时装置自保系统调试完好;2.12动力部门按照开工要求,将公用介质引至装置边界;2.13联系排水岗位保证含油污水,非含油污水的排水畅通;2.14做好消防准备工作,检查消防器材,保证完好,并准备好消防蒸汽皮带;2.15准备好开工用工具(包括扳手、肥皂水、小水桶、涂刷工具、对讲机等);2.16准备好开工任务单,升温曲线,烘炉记录,操作记录纸,质量记录及交接班本;2.17装置内清扫干净无杂物。
炼油厂中使用的主要设备有哪些?
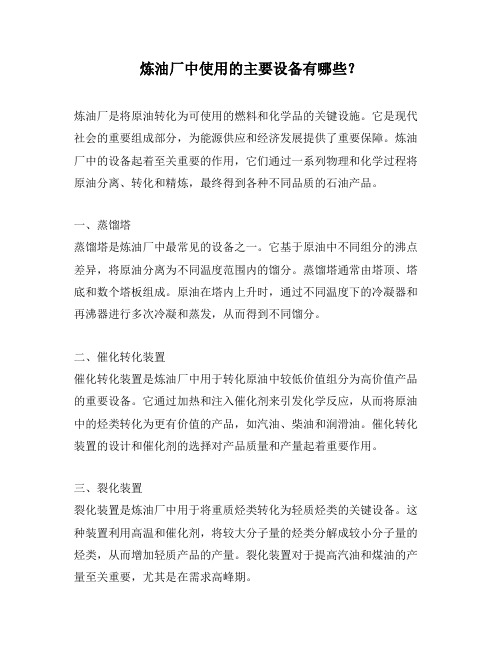
炼油厂中使用的主要设备有哪些?炼油厂是将原油转化为可使用的燃料和化学品的关键设施。
它是现代社会的重要组成部分,为能源供应和经济发展提供了重要保障。
炼油厂中的设备起着至关重要的作用,它们通过一系列物理和化学过程将原油分离、转化和精炼,最终得到各种不同品质的石油产品。
一、蒸馏塔蒸馏塔是炼油厂中最常见的设备之一。
它基于原油中不同组分的沸点差异,将原油分离为不同温度范围内的馏分。
蒸馏塔通常由塔顶、塔底和数个塔板组成。
原油在塔内上升时,通过不同温度下的冷凝器和再沸器进行多次冷凝和蒸发,从而得到不同馏分。
二、催化转化装置催化转化装置是炼油厂中用于转化原油中较低价值组分为高价值产品的重要设备。
它通过加热和注入催化剂来引发化学反应,从而将原油中的烃类转化为更有价值的产品,如汽油、柴油和润滑油。
催化转化装置的设计和催化剂的选择对产品质量和产量起着重要作用。
三、裂化装置裂化装置是炼油厂中用于将重质烃类转化为轻质烃类的关键设备。
这种装置利用高温和催化剂,将较大分子量的烃类分解成较小分子量的烃类,从而增加轻质产品的产量。
裂化装置对于提高汽油和煤油的产量至关重要,尤其是在需求高峰期。
四、加氢装置加氢装置是炼油厂中用于改善燃料品质和减少污染物排放的设备。
通过将氢气注入到原油中,加氢装置可以去除硫、氮等污染物,并减少产生的有害废气和颗粒物。
加氢装置还可以将较重的烃类转化为较轻的产品,如汽油和柴油,提高产品的产量和质量。
五、脱硫装置脱硫装置是炼油厂中用于去除原油中硫化物的设备。
硫化物是一种有害物质,会对环境和人体健康造成污染和危害。
脱硫装置使用不同的方法,如氢气气体吸附、触媒反应等,将中硫化物转化为无害的化合物,保护环境和减少硫化物排放。
综上所述,炼油厂中的设备种类繁多,每个设备都承担着不可或缺的作用。
通过蒸馏塔,原油可以分离为不同温度范围内的馏分;催化转化装置将原油中的低价值组分转化为高价值产品;裂化装置将重质烃类分解为轻质烃类增加产量;加氢装置改善产品质量和减少污染物排放;脱硫装置去除原油中的有害硫化物。
焦化分馏塔顶结盐问题的分析及处理

焦化分馏塔顶结盐问题的分析及处理潘春生;陈金;王良龙;刘远航;刘伟【摘要】分馏塔顶结盐直接造成分馏塔顶部塔盘堵塞,严重时使分馏塔无法正常运行,必须停工处理塔盘堵塞问题,损失较大.因此延迟焦化车间提出在线不停工处理分馏塔顶结盐问题的思路,通过分析分馏塔顶结盐问题的原因,采取分馏塔降顶温脱盐、在线水洗塔盘、柴油洗塔盘、提高分馏塔顶温等处理措施,解决了分馏塔顶部结盐、塔盘堵塞的问题.【期刊名称】《化工科技》【年(卷),期】2016(024)001【总页数】4页(P65-68)【关键词】分馏塔;结盐;水洗;柴油洗;提温【作者】潘春生;陈金;王良龙;刘远航;刘伟【作者单位】中国石油吉林石化公司炼油厂,吉林吉林132022;中国石油吉林石化公司炼油厂,吉林吉林132022;中国石油吉林石化公司炼油厂,吉林吉林132022;中国石油吉林石化公司炼油厂,吉林吉林132022;中国石油吉林石化公司炼油厂,吉林吉林132022【正文语种】中文【中图分类】TE962中国石油吉林石化公司炼油厂延迟焦化装置由中国石化集团公司洛阳石油化工工程公司设计,设计加工能力为100万t/a,装置于2003年5月10日建成,2003年6月1日装置一次开车成功,装置以炼油厂常减压装置生产的减压渣油及催化裂化车间的油浆为原料进行二次加工,生产干气、液化石油气、汽油、柴油、轻蜡油、重蜡油以及焦炭产品。
装置设计循环比为0.6,生焦周期24 h。
工艺上采用一炉二塔、有井架水力除焦、无堵焦阀密闭放空的先进工艺。
装置工艺主体包括焦化、分馏、吸收稳定、气体脱硫4大部分。
在装置运行过程中,曾经出现过分馏塔顶部结盐,堵塞塔盘的问题,针对此情况采取一些临时处理措施缓解了塔顶塔盘结盐问题,最后,通过操作摸索逐渐形成了提高分馏塔顶温、使塔顶结盐部位后移等技术,已基本解决了分馏塔顶结盐问题。
分馏塔自2009年6月检修后一直正常运行。
1 结盐问题的出现分馏塔顶部结盐问题主要出现在2008年和2009年。
催化装置提高柴油收率的措施及对装置的影响

141 装置基本概况玉门炼油厂催化车间原设计生产能力为50wt/年,经技术改在后,装置生产能力提高至80wt/年,采用两段提升管工艺,新鲜原料主要进入第一提升管进行反应,回炼油浆和回炼油进入第二提升管反应,烧焦部分采用前置烧焦罐形式,烧焦罐出口采用稀相管烧焦方式,分馏系统和吸收稳定系统未进行技术改造。
2 柴油收率的影响因素实际生产中,影响柴油收率的因素较复杂,主要包括原料性质、催化剂型号、反应操作参数和分馏塔温度分布情况及提升管生产工艺等,生产工艺和催化剂的选择一般不会有较大调整,本文不再讨论。
2.1 反应操作参数柴油方案适合采用较低的反应温度和催化剂活性,在较低的反应温度下,原料中的长链烃类的裂化性能明显下降,在相同的反应时间内,提升管出口的产品中可以保留较大的柴油组分,所以,适当降低催化的活性和反应温度,这种缓和的反应环境可以大大提高柴油的收率。
2.2 原料性质优化原料性质对柴油收率的影响较大,催化的原料主要包括常压来裂化料、常压渣油和焦化来蜡油组分,常压来裂化料是最好的裂化原料,但因其出色的裂化性能,并不利于提高柴油收率。
为了提高柴油收率,可以适当提高常压渣油的掺炼比例。
2.3 分馏塔温度分布分馏塔作为产品分割的主要设备,其温度分布决定着柴油收率的大小,适当提高回炼油回炼量,可以为分馏系统提供更充足的热源,为操作调整带来很大富裕度,油浆回炼量不宜太高,因油浆回炼过程中大部分进行了结焦反应,会降低装置的整体液体收率。
适当降低分馏塔顶部温度和提高一中的温度,可以使汽油中的较重组分进入柴油产品中,进而提高柴油的收率。
3 提高柴油收率的措施3.1 提高反应温度,采用高回炼比目前反应温度控制在510℃左右,经调整后,反应温度降低至500~505℃之间,降低反应温度后,分馏塔液面和回炼油液面有明显的上升趋势,迫使要提高一中的温度。
降低反应深度,可以提高装置柴油的收率。
3.2 优化原料性质近期装置进料性整体偏轻,密度一般在900~910kg/m 3之间,维持较低的反应温度时,分馏塔低部的液面也难以维持,证明进料组分轻,较易裂化为汽油组分,导致产品中柴油组分收率较低。
- 1、下载文档前请自行甄别文档内容的完整性,平台不提供额外的编辑、内容补充、找答案等附加服务。
- 2、"仅部分预览"的文档,不可在线预览部分如存在完整性等问题,可反馈申请退款(可完整预览的文档不适用该条件!)。
- 3、如文档侵犯您的权益,请联系客服反馈,我们会尽快为您处理(人工客服工作时间:9:00-18:30)。
导向浮阀塔盘
1.塔板上配有导向浮阀,浮阀上有一 个或二个导向孔,导向孔的开口方向 与塔板上的液流方向一致。
2.导向浮阀两端设有阀腿,在操作中 汽体从浮阀的两侧流出,汽体流出的 反向垂直于踏板上的液体流动向。因 此,导向浮阀塔板上的液体返混是很 小的。 3.由于导向浮阀在操作中不转动,浮 阀无磨损,不脱落。 4.目前,I催化装置分馏塔使用的是具 有一个导向孔的导向浮阀塔盘
降液板,受液盘与溢流堰
受液盘上有一个泪孔。 泪孔开孔直径小,正常操 作时由于上升的气相的作 用,不会漏液。 最主要的作用就是系 统停车时,泪孔可以把受 液盘内的积液排掉,使塔 内的物料放净,便于置换 和检修。
溢流堰为塔板上液体溢出的结构,具 有维持板上液层及使液体均匀溢出的作用, 又可分为出口堰及入口堰。
破涡器 如果产生漩涡,液体会带 着气体进入塔釜泵,造成 气缚!一般需要加防涡板。
一.什么是分馏塔?
二.分馏塔流程
三.分馏塔塔盘
四.分馏塔内构造
一、分馏塔
分馏塔就是 对混合挥发液 体(例如石油 )进行分馏的 一种化工设备 。
I催化裂化装置 分馏塔,塔高47 米、直径3.8米 重达180吨(约 为120辆小轿车 的重量)。
二、分馏塔的流程
1. 自沉降器顶部出来的反应油气(约480℃) 进到分馏塔下部,油气向上经过脱过热段8层 人字挡板和30层塔盘(15层单溢流舌形塔盘和 15层双溢流浮阀塔盘);分馏后得到气体、粗 汽油、轻柴油、回炼油、油浆。 2. 8层人字挡板为脱过热段,同时起到洗涤 催化剂的作用
3. 1-2#塔盘为回炼油循环段。 4. 16-18#塔盘为中段循环段。
5. 19-22#塔盘为柴油。
6. 27-30#塔盘为顶回流循环段。 7. 塔顶为油气出口。
三、分馏塔塔盘
固舌型
舌形塔属于喷射形塔。
舌孔有三面切口和拱形切口两 种。常用的三面切口舌片的开
启度一般为20°。
分馏塔1—15层为单溢流 舌形塔盘
分馏塔15—30层为双溢 流浮阀塔盘
四、分馏塔的构造
人字塔板
升气孔与 集液箱
降液板、受 液盘与溢流 堰
分布管与返 塔口
人字塔板
人字挡板共分为8层,高温反应油气和循环油 浆在这里逆向接触,脱除所带来的催化剂颗粒 及反应油气脱过热。 1.将油气脱过热,使反应油气脱过热后呈气液 平衡状态,饱和状态有利于分馏塔的产品分离。 2.洗涤催化剂,防止催化剂堵塞塔盘(降液 管),减少各抽出物携带催化剂带入下游设备, 导致分馏塔压降增大。 3.最上一层人字挡板有锯齿,可以使油浆分布 更加均匀。
分布管与返塔口
在分布管上,会均匀的分 布着这样的小孔,作用是有利 于返塔液体更加均匀的洒在塔 盘上进行气液传质。
这是分馏塔底 的抽出口,在这 个抽出口上,使 用了伞帽与过滤 网。作用是防止 油浆中大块焦块 物体进入抽出管 道,堵塞管道。
由于在分馏塔底部,所以下返塔为环形分布管, 目的是让循环油浆更加均匀的喷洒,与上升气体 均匀传质。
单溢流 、双溢流
单溢流与双溢流在操作上没有任 何区别,它指的是塔内降液槽的个 数,这是根据塔内气液相分布而决 定的。 分馏塔的中段抽出口以上,气、 液相较大,塔盘开孔率高,所以采 用双溢流设计,分馏塔的上部会采采用单溢 流。
由于舌孔方向与液流方向一致 ,故气体从舌孔喷出时,可减 小液面落差,减薄液层,减少 雾沫夹带。 舌形塔盘物料处理流量大,压 降小,结构简单,安装方便。 但操作弹性小,塔板效率低。
汽 体 从 舌 孔 向 上 液 体 流 动 方 向
浮阀塔板
浮阀塔板上开有—定形状 的阀孔(圆形或矩形),孔 中安有可上下浮动的阀片 有圆形、矩形、盘形等, 从而形成不同型式的浮阀 塔板。 浮阀塔板因其具有优异的 综合性能(生产能力大、操 作弹性大、塔板效率高、 制造费用低等)已成为目前 应用最广泛的一种塔板。
升气孔与集液箱
在分馏塔的16层和27 层,分别有集液箱与4个升 气孔。 1.升气孔的作用就是气 体通过的通道,还有一定 的气体分布作用,结构一 般有方形和圆形之分。我 们的分馏塔采用的是圆形。 2.集液箱主要作用是收 集液体,用于液体的再分 布或产品的抽出或中段换 热。 3.升气孔所在的位置就 是集液箱。