浅谈催化裂化装置中分馏塔塔顶压力
催化裂化吸收稳定流程说明
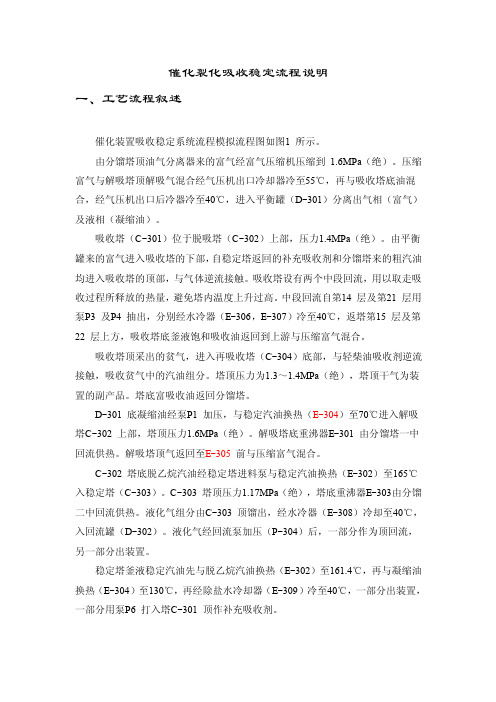
催化裂化吸收稳定流程说明一、工艺流程叙述催化装置吸收稳定系统流程模拟流程图如图1 所示。
由分馏塔顶油气分离器来的富气经富气压缩机压缩到1.6MPa(绝)。
压缩富气与解吸塔顶解吸气混合经气压机出口冷却器冷至55℃,再与吸收塔底油混合,经气压机出口后冷器冷至40℃,进入平衡罐(D-301)分离出气相(富气)及液相(凝缩油)。
吸收塔(C-301)位于脱吸塔(C-302)上部,压力1.4MPa(绝)。
由平衡罐来的富气进入吸收塔的下部,自稳定塔返回的补充吸收剂和分馏塔来的粗汽油均进入吸收塔的顶部,与气体逆流接触。
吸收塔设有两个中段回流,用以取走吸收过程所释放的热量,避免塔内温度上升过高。
中段回流自第14 层及第21 层用泵P3 及P4 抽出,分别经水冷器(E-306,E-307)冷至40℃,返塔第15 层及第22 层上方,吸收塔底釜液饱和吸收油返回到上游与压缩富气混合。
吸收塔顶采出的贫气,进入再吸收塔(C-304)底部,与轻柴油吸收剂逆流接触,吸收贫气中的汽油组分。
塔顶压力为1.3~1.4MPa(绝),塔顶干气为装置的副产品。
塔底富吸收油返回分馏塔。
D-301 底凝缩油经泵P1 加压,与稳定汽油换热(E-304)至70℃进入解吸塔C-302 上部,塔顶压力1.6MPa(绝)。
解吸塔底重沸器E-301 由分馏塔一中回流供热。
解吸塔顶气返回至E-305 前与压缩富气混合。
C-302 塔底脱乙烷汽油经稳定塔进料泵与稳定汽油换热(E-302)至165℃入稳定塔(C-303)。
C-303 塔顶压力1.17MPa(绝),塔底重沸器E-303由分馏二中回流供热。
液化气组分由C-303 顶馏出,经水冷器(E-308)冷却至40℃,入回流罐(D-302)。
液化气经回流泵加压(P-304)后,一部分作为顶回流,另一部分出装置。
稳定塔釜液稳定汽油先与脱乙烷汽油换热(E-302)至161.4℃,再与凝缩油换热(E-304)至130℃,再经除盐水冷却器(E-309)冷至40℃,一部分出装置,一部分用泵P6 打入塔C-301 顶作补充吸收剂。
催化裂化提高汽油收率操作分析

催化裂化提高汽油收率操作分析摘要:通过对催化裂化装置操作调整的分析,改善操作,有效提高汽油收率。
关键词:催化裂化;操作调整;汽油收率催化裂化装置的汽油是原油进提升管经过裂化反应,通过分馏塔组分切割,再经过吸收稳定精馏分离而出来的。
下面通过对装置操作调整分析,确定怎样来提高汽油收率。
本文从反应再生系统,分馏系统,吸收稳定系统三个方面的操作调整,分析对汽油收率的影响。
1.反应再生系统的操作1.1 反应温度催化裂化反应是吸热反应,反应温度升高有利于裂化反应的进行,由于我们反应温度一般投自动控制,提高反应温度的同时再生滑阀开大,增加催化剂循环量,增加催化剂活性中心,增加反应深度。
则提高反应温度,汽油收率增加。
但当反应温度提至很高时,热裂化反应趋于重要,汽油组分开始减少,干气组分明显增多。
表1 反应温度与汽油收率图1 反应温度与汽油收率由表1和图1中可以看出,其他条件不变时,提高反应温度,汽油收率增加.反应温度在504℃时,汽油收率最高。
505℃时,汽油收率开始下降,干气收率增加。
1.2急冷介质在反应温度不变情况下,提高汽油收率另一种手段就是在提升管反应部分喷入急冷介质,提高剂油比和反应深度,减少二次裂化和热裂化,从而提高汽油收率。
急冷介质一般用粗汽油或者水或者两者混合。
但急冷介质的喷入会影响系统的油气分压,分流塔产品质量的控制需相应调整。
1.3 再生温度本装置再生器采用重叠式两段再生型式。
两个再生器重叠布置,一段再生位于二段再生上面。
一再贫氧、CO部分燃烧;二再富氧再生、CO完全燃烧。
催化裂化反应所需热量是通过再生器内完全再生的热催化剂提供的,所以再生温度的高低也直接影响催化剂循环量的大小。
再生温度高则催化剂循环量降低,反应的催化剂活性中心减少,反应深度降低,汽油收率降低。
表2 再生温度与汽油收率图2再生温度与汽油收率由表2与图2可以看出其他条件不变时,汽油收率随再生温度升高而降低,但当再生温度降至670℃以下后,再生器烧焦效果变差,再生器稀相出现尾燃。
炼油催化裂化分馏塔顶腐蚀原因分析及对策
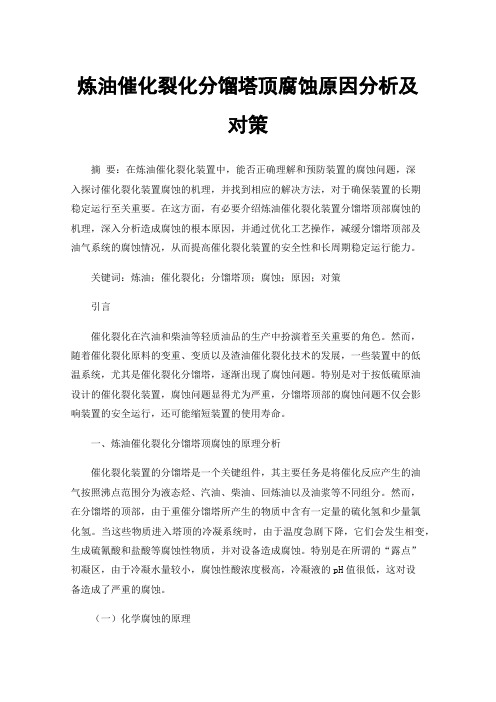
炼油催化裂化分馏塔顶腐蚀原因分析及对策摘要:在炼油催化裂化装置中,能否正确理解和预防装置的腐蚀问题,深入探讨催化裂化装置腐蚀的机理,并找到相应的解决方法,对于确保装置的长期稳定运行至关重要。
在这方面,有必要介绍炼油催化裂化装置分馏塔顶部腐蚀的机理,深入分析造成腐蚀的根本原因,并通过优化工艺操作,减缓分馏塔顶部及油气系统的腐蚀情况,从而提高催化裂化装置的安全性和长周期稳定运行能力。
关键词:炼油;催化裂化;分馏塔顶;腐蚀;原因;对策引言催化裂化在汽油和柴油等轻质油品的生产中扮演着至关重要的角色。
然而,随着催化裂化原料的变重、变质以及渣油催化裂化技术的发展,一些装置中的低温系统,尤其是催化裂化分馏塔,逐渐出现了腐蚀问题。
特别是对于按低硫原油设计的催化裂化装置,腐蚀问题显得尤为严重,分馏塔顶部的腐蚀问题不仅会影响装置的安全运行,还可能缩短装置的使用寿命。
一、炼油催化裂化分馏塔顶腐蚀的原理分析催化裂化装置的分馏塔是一个关键组件,其主要任务是将催化反应产生的油气按照沸点范围分为液态烃、汽油、柴油、回炼油以及油浆等不同组分。
然而,在分馏塔的顶部,由于重催分馏塔所产生的物质中含有一定量的硫化氢和少量氯化氢。
当这些物质进入塔顶的冷凝系统时,由于温度急剧下降,它们会发生相变,生成硫氰酸和盐酸等腐蚀性物质,并对设备造成腐蚀。
特别是在所谓的“露点”初凝区,由于冷凝水量较小,腐蚀性酸浓度极高,冷凝液的pH值很低,这对设备造成了严重的腐蚀。
(一)化学腐蚀的原理将常压渣油加热至200℃后,引入提升管反应器的下部喷嘴,通过蒸汽雾化将其分散成微粒,然后进入提升管内。
在提升管内,与来自再生器的高温催化剂发生接触,随后汽化并进行反应。
有机硫化物在高温下分解成酸性H2S和RSH等化合物,随着反应油气一起进入分馏塔。
电脱盐过程未能完全去除的无机盐类会在高温下熔化、水解,有机氯化物也会在高温下分解生成HCl。
H2S和HCl会在水蒸汽结雾时溶解其中,产生强烈的化学腐蚀。
催化裂化装置工艺条件一览表

一、催化裂化装置主要工艺指标
1、反应再生单元
序号工艺指标名称单位仪表位号控制范围
1
重油提升管出口温度
℃
TRCA22101A
500~530
2
出管芳烃提升口温度烃芳提升管出口温度
℃℃
TRCA22101B TRCA22101B
440~480(低硫)480~530(高硫)
3
反应压力
50±20
10
液位T22201A
%
LC22201
20
±50
11
T22201B液位
%
LC22202
50±20
12
V22203A液位
%
LICA2220
50±20
13
V22203B液位
%
LICA2220
50±20
14
电脱盐罐温度
℃
110~140
15
电脱盐罐压力
Mpa
0.8~1.5
16
电脱盐罐电场强
kv/cm
15
过热蒸气温度
℃
TIC22461
380~410
16
汽外取热包压力
MPa
PRA22421
3.5~4.1
17
省煤器上水温度
℃
TI22468
>122
18
外取热汽包液位
%
LRC22421
50±20
2、分馏单元
序号
工艺指标名称
单位
仪表位号
控制范围
1
重油分馏塔塔顶
℃
TRCA2220
120~150
2
芳烃分馏塔塔顶
90~130
认真分析 开拓思路 催化装置稳定塔顶压力偏低的异常操作得到解决

认真分析开拓思路稳定塔顶压力偏低的异常操作得到解决——王军刘龙脱科峰一、概述催化装置吸收稳定系统自从2008年5月份改造后,稳定塔顶压力一段时间一直处于偏低状态,虽然采取了一系列传统的操作调整手段,但是效果仍然不佳,长时间稳定塔顶压力补压热旁路控制调节阀处于全开,付线阀也处于全开状态,但压力仍然偏离工艺指标控制值,压力很低。
泄压压力控制调节阀不凝气阀一直处于关闭状态,这种操作现象的存在,造成液态烃质量不合格,液态烃中的C5含量超标。
C2含量由于溶解于液相中很难排出而超标,这样一来,液态烃的脱前总硫含量大大上升,使得液态烃的后续脱硫装置符合大大增加,液态烃脱后硫含量超标,碱液单耗猛增,超标那段时间,每天消耗新鲜碱液使正常稳定工况下的5倍,同时也直接影响了聚丙烯装置的平稳生产。
针对这种操作异常现象,我们认真分析,及时采取了行之有效的措施,使得稳定塔顶压力偏低的问题得到解决,平稳了操作,保证了液态烃质量,减低了碱液单耗,有力的保证了装置的安全、平稳、高效、长周期运行。
二、稳定塔顶压力偏低的弊端a)稳定系统操作波动大,对装置的安全生产造成很大威胁。
b)液态烃质量波动不合格,液态烃中的C5、C2含量超标。
c)液态烃脱后硫含量超标,新鲜碱单耗大大超标。
d)液化气质量直接影响聚丙烯装置的平稳生产,不利于聚合反应的进行三、稳定塔顶压力偏低的原因分析1.改造缺陷2008年5月份对原稳定塔顶回流罐(V302)进行了放大,但改造时是利旧了原气压机出口油气分离器(V301)作为改造后的稳定塔顶回流罐(V302),由于原设备接口少的现状,所以在配值工艺管线时将原从稳定塔顶回流罐顶接入的补压线接口并在了液态烃管线一并进入回流罐内的液层,这样一来,在操作中虽有大量的热态液态烃进入回流罐补压但由于是和冷态的液态烃混合并且进入液层,从而造成大量的热态液态烃不能在回流罐及时很好的汽化进入气相达到补压的效果,致使稳定塔顶压力偏低。
C2含量由于溶解于液相中很难排出而超标。
催化裂化的装置简介及工艺流程
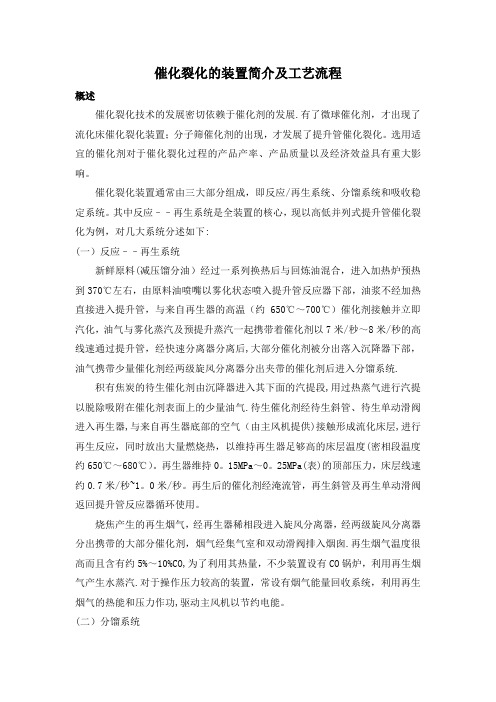
催化裂化的装置简介及工艺流程概述催化裂化技术的发展密切依赖于催化剂的发展.有了微球催化剂,才出现了流化床催化裂化装置;分子筛催化剂的出现,才发展了提升管催化裂化。
选用适宜的催化剂对于催化裂化过程的产品产率、产品质量以及经济效益具有重大影响。
催化裂化装置通常由三大部分组成,即反应/再生系统、分馏系统和吸收稳定系统。
其中反应––再生系统是全装置的核心,现以高低并列式提升管催化裂化为例,对几大系统分述如下:(一)反应––再生系统新鲜原料(减压馏分油)经过一系列换热后与回炼油混合,进入加热炉预热到370℃左右,由原料油喷嘴以雾化状态喷入提升管反应器下部,油浆不经加热直接进入提升管,与来自再生器的高温(约650℃~700℃)催化剂接触并立即汽化,油气与雾化蒸汽及预提升蒸汽一起携带着催化剂以7米/秒~8米/秒的高线速通过提升管,经快速分离器分离后,大部分催化剂被分出落入沉降器下部,油气携带少量催化剂经两级旋风分离器分出夹带的催化剂后进入分馏系统.积有焦炭的待生催化剂由沉降器进入其下面的汽提段,用过热蒸气进行汽提以脱除吸附在催化剂表面上的少量油气.待生催化剂经待生斜管、待生单动滑阀进入再生器,与来自再生器底部的空气(由主风机提供)接触形成流化床层,进行再生反应,同时放出大量燃烧热,以维持再生器足够高的床层温度(密相段温度约650℃~680℃)。
再生器维持0。
15MPa~0。
25MPa(表)的顶部压力,床层线速约0.7米/秒~1。
0米/秒。
再生后的催化剂经淹流管,再生斜管及再生单动滑阀返回提升管反应器循环使用。
烧焦产生的再生烟气,经再生器稀相段进入旋风分离器,经两级旋风分离器分出携带的大部分催化剂,烟气经集气室和双动滑阀排入烟囱.再生烟气温度很高而且含有约5%~10%CO,为了利用其热量,不少装置设有CO锅炉,利用再生烟气产生水蒸汽.对于操作压力较高的装置,常设有烟气能量回收系统,利用再生烟气的热能和压力作功,驱动主风机以节约电能。
催化裂化操作指南(分馏与稳定)解读
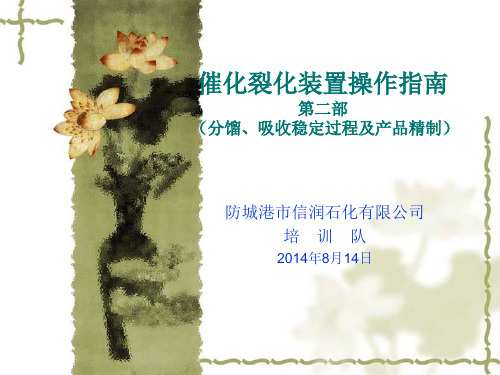
分馏过程
一、设备检查 1、塔器 (1)分馏塔 首次运行的分馏塔,必须逐层检查所有塔盘,确认按图纸正确安装; 如溢流口尺寸、堰高和塔盘水平度等。 对所有浮阀进行检查,确认清洁,活动自如;所有塔盘紧固件安装正 确、紧固;所有分布器安装定位正确,分布孔畅通。 每层塔盘和降液管清洁,顶循、中段、柴油等抽出槽和抽出口清洁无 杂物,集油箱焊缝完好,不泄漏。 底部脱过热段折流板(人字档板)等均坚固,焊缝完好,所有固定螺 栓均已经锤击或被点焊。 塔底搅拌蒸汽分布器、支撑等完好;油浆过滤器及其附件清洁,固定 或焊接牢固。 塔内设备检查完成后,应马上安装人孔,安排专人现场负责该项工作。
分馏过程
档板或园盘型档板,进入油气与260-360℃循环油浆逆流接触、换热、 冼涤,油气被冷却,将油气中夹带的催化剂细枌冼涤下来,防止其污染 上部的测线产品,堵塞上部塔盘。 (2)全塔过剩热量大 分馏塔进料是过热度很高的反应油气(480-510 ℃ ),塔顶是低温 (100-130 ℃ )气体,其他产品均以液态形式离开分馏塔。在整个分 馏过程中有大量的过剩热量需要移出。所以系统有大量的冷换设备和热 水器。 (3)产品分馏要求较容易满足 油品分馏难易程度可用相邻馏分50%馏出温度差值来衡量。差值越大, 馏分间相对挥发度越大,就越容易分离。催化分馏塔除塔顶为粗汽油外 还有轻柴油、重柴油、回炼油三个侧线组分。催化裂化各侧线组分50% 馏出温度值较大,馏分容易分离,所以产品分馏要求容易满足。
分馏过程
(5)轻污油系统 分馏、吸收稳定部分轻油设备(换热器、泵、过滤器、采样器等) 在停工或检修时存有少量的轻油,通过污油系统自流至地下轻污油罐, 用污油泵送出装置。 (6)重污油系统 装置内重油设备在停工或检修时存有少量的重油,通过重污油系统 送出装置。 5、事故处理流程 (1)富气放火炬流程 开工时提升管反应器已经进油,但富气压缩机还没有启动,在此期 间产生的富气从分馏塔顶油气分离器引出经富气放空管道排放至火炬系 统。正常生产中富气压缩机因故障紧急停机,则启用富气放火炬系统。 (2)汽油紧急排放流程 当分馏塔顶油气分离罐粗汽油液位突然升高,用正常方法处理不及 时,有汽油进入富气压缩机的危险时,可启用汽油紧急放空(粗汽油泵 入口管排放到轻污油罐)。
催化裂化装置分馏系统工艺分析
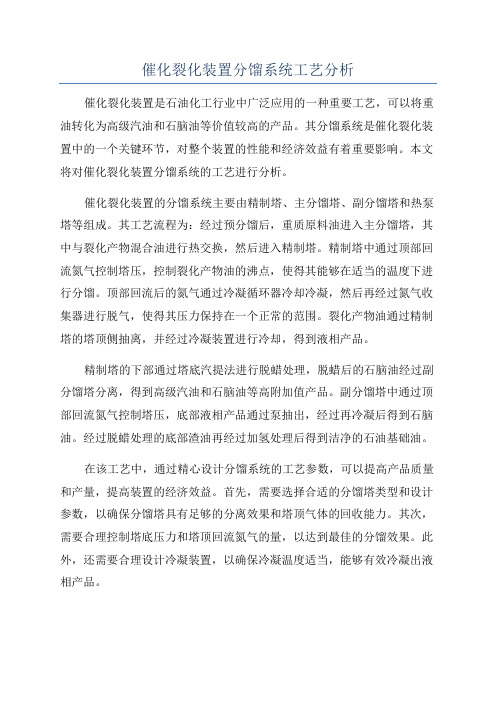
催化裂化装置分馏系统工艺分析催化裂化装置是石油化工行业中广泛应用的一种重要工艺,可以将重油转化为高级汽油和石脑油等价值较高的产品。
其分馏系统是催化裂化装置中的一个关键环节,对整个装置的性能和经济效益有着重要影响。
本文将对催化裂化装置分馏系统的工艺进行分析。
催化裂化装置的分馏系统主要由精制塔、主分馏塔、副分馏塔和热泵塔等组成。
其工艺流程为:经过预分馏后,重质原料油进入主分馏塔,其中与裂化产物混合油进行热交换,然后进入精制塔。
精制塔中通过顶部回流氮气控制塔压,控制裂化产物油的沸点,使得其能够在适当的温度下进行分馏。
顶部回流后的氮气通过冷凝循环器冷却冷凝,然后再经过氮气收集器进行脱气,使得其压力保持在一个正常的范围。
裂化产物油通过精制塔的塔顶侧抽离,并经过冷凝装置进行冷却,得到液相产品。
精制塔的下部通过塔底汽提法进行脱蜡处理,脱蜡后的石脑油经过副分馏塔分离,得到高级汽油和石脑油等高附加值产品。
副分馏塔中通过顶部回流氮气控制塔压,底部液相产品通过泵抽出,经过再冷凝后得到石脑油。
经过脱蜡处理的底部渣油再经过加氢处理后得到洁净的石油基础油。
在该工艺中,通过精心设计分馏系统的工艺参数,可以提高产品质量和产量,提高装置的经济效益。
首先,需要选择合适的分馏塔类型和设计参数,以确保分馏塔具有足够的分离效果和塔顶气体的回收能力。
其次,需要合理控制塔底压力和塔顶回流氮气的量,以达到最佳的分馏效果。
此外,还需要合理设计冷凝装置,以确保冷凝温度适当,能够有效冷凝出液相产品。
此外,还需要注意操作控制的安全性和稳定性。
对于分馏系统来说,要注意控制好分馏温度和压力的变动,以防止分馏塔内发生过热、过压等异常情况。
在日常操作中,要注意监控分馏系统的各个关键参数,及时发现问题并进行调整和处理。
综上所述,催化裂化装置分馏系统是催化裂化装置中一个重要的工艺环节。
通过合理设计和精心操作,可以提高产品的质量和产量,提高装置的经济效益。
但需要注意操作的安全性和稳定性,及时处理和解决问题。
- 1、下载文档前请自行甄别文档内容的完整性,平台不提供额外的编辑、内容补充、找答案等附加服务。
- 2、"仅部分预览"的文档,不可在线预览部分如存在完整性等问题,可反馈申请退款(可完整预览的文档不适用该条件!)。
- 3、如文档侵犯您的权益,请联系客服反馈,我们会尽快为您处理(人工客服工作时间:9:00-18:30)。
浅谈催化裂化装置中分馏塔塔顶压力
的影响因素
炼油一车间
赵强
浅谈催化裂化装置中分馏塔塔顶压力
的影响因素
赵强
(乌石化炼油厂一车间)
前言:催化裂化分馏塔的主要任务是将来自反应系统的高温油气脱过热后,根据各组分沸点的不同切割为富气、汽油、柴油、回炼油和油浆等,通过温度,压力,回流量等工艺因素控制,保证各馏分质量合格。
关键词:催化裂化,分馏塔,压力,汽油,柴油,回炼油,油浆
一 基本情况介绍:
蜡油催化裂化装置近期在生产过程中,分馏塔顶压力一直不好控制,从原来的115kPa 下降到113kPa 在到现在的110kPa ,如图(一),
分馏塔顶压力月平均
111
111.5112112.5113113.5114114.5115115.5
1月份
2月份
3月份
4月份
5月份
6月份
图1 2008年1月份到6月份
在我装置生产过程中,分馏塔顶压力要控制在105kPa 到135kPa 之间,从上述据上看分馏塔的压力都在正常控制压力之内,但是在近期的观察中,发现分馏塔顶压力一直在降低。
在催化裂化装置中分馏塔顶压力是控制
各侧线流出产品质量的重要参数,分流塔顶压力的过高或过低都会使产品的质量受到很大影响,当分馏塔顶压力过低时,粗汽油的干点就会升高,而柴油的终馏点却会降低;当分馏塔塔顶压力过高则反之。
而汽油
的干点说明了汽油在发动机
中蒸发完全的程度,这个温度过高,说明重
质成分过多,其结果是降低发动机的功率和
经济性,因此我们要控制好分馏塔的压力。
二原因分析:
影响分馏塔顶压力的主要原因有以下几点:原料的性质,反应温度,反应压力,催化剂的活性,分馏塔顶的温度,分馏塔的中部温度,塔底的气相温度,分馏塔的顶部及各中部回流量,气压机的转速,塔顶的安全阀,以及Dg400,Dg200阀的开度等因素,下面从原料性质,分馏塔中部温度,分馏塔底汽相温度3个方面来分析分馏塔顶压力。
2.1 在催化裂化装置中,分馏塔顶的压力来源于原料裂解之后经过分馏塔的各中段回流和塔顶回流之后的不凝气体,这些气体是通过高温催化剂和原料的相互接触使原料裂解而生成的,所以分馏塔的压力和原料的性质,催化剂的活性,反应温度都有关系,下面就是6月15日到6月17日之间原料性质和反应温度的变化情况;
原料性质变化情况
罐位初馏点℃5% 10% 50% 90% 终馏点℃残碳密度
5号285 320 340 420 505 555 0.17 881.6
6号277 344 360 435 521 --- 0.21 882.9
7号270 325 345 430 515 570 0.12 881.7
反应温度变化情况
6月15日6月16日6月17日
反应温度塔顶压力反应温度塔顶压力反应温度塔顶压力1点485113485113489111 3点485113485113489110 5点485113484113487110 7点485114484113487109 9点485113484113487110 11点484113483112488111 13点484113483113487108 15点484112487114481109 17点482114488113481109 19点483113489113482111 21点484113489111482110 23点486113489111480110平均值484.3333113.0833485.8333112.6667485109.8333
这个表格中从6月15日的19点钟到6月16日的15点钟是5号罐裂解,6月16日17点到6月17日13点是6号罐裂解,6月17日以后的7号罐裂解
从上边两个表的数据来看,在6月15日到17日之间,近似的把催化剂的活性看成是一定的,分馏塔顶的压力和原料的5%点有着密切的关系,当原料的5%点从5号罐320℃上升到6号罐344℃再到7号罐的325℃,反应温度从485℃改变到489℃然后在回到480℃的情况下分馏塔顶的压力从113kPa 下降到了111kPa再到110kPa,在反应温度的变化是随着原料性质的变化而变化的情况下,反应压力却一直保持在172 kPa,从这些数据来看分馏塔顶的压力和原料的性质有这直接的关系。
2.2 分馏塔顶的压力不仅只和原料性质、反应操作有关系,它还和分馏塔的操作有关系,下边是分馏塔在生产操作中的一些基本数据:
7号罐TR203 (℃) TRC101 (℃) TR211 (℃) PR210 ( kPa) 1点236 485 367 113
3点234 485 364 113
5点236 485 366 113
7点238 485 368 114
9点235 485 367 113
11点230 485 363 112
13点230 485 362 112
6月15日7号罐分馏塔底气相温度和分馏塔顶压力的变化趋势
从上表中看到在反应温度不变的情况下,分馏塔底汽相温度和中部温度在7点中升高时候,分馏塔顶压力也随之升高,在11点和13点下降的时候分馏塔顶的压力也随之降低。
2.3 分馏塔的操作能够直接影响分馏塔顶的压力,但影响分馏塔顶压力的因素还有很多,如气压机的转速忽高忽低使得分馏塔顶压力不稳,分馏塔顶安全阀失灵,在规定的压力下没有能够起跳,在没有达到规定压力下突然起跳,Dg400和Dg 200火炬阀的失灵开启,大油气线上电动阀的自动关闭或开启,冷凝器的泄露,空冷风机的运转情况,D210液面的高低,D501的压油,C302底部压油都会影响分馏塔顶的压力。
三结论:
经过以上分析,原料的性质,反应温度,反应压力,催化剂的活性,分馏塔顶的温度,分馏塔的中部温度,塔底的气相温度,分馏塔的顶部及各中部回流量,气压机的转速,塔顶的安全阀,以及Dg400,Dg200阀的开度等因素都会对分馏塔顶压力造成影响,而在中些因素中原料性质,反应温度,反应压力对分馏塔顶的压力影响最大,还有分馏塔底汽相温度,和分馏塔的中部温度,顶部温度都可以影响分馏塔顶的压力。
参考文献:
炼油厂一车间蜡油催化裂化装置操作规程,中国石油乌鲁木齐石化公司,2007年1月1日
催化裂化装置技术问答,中国石油化工出版社,2007年6月化工原理(第二版)上册,化工工业出版社
流化催化裂化,中国石化出版社,2008年1月。