涤纶短纤维生产前纺常见问题分析
涤纶短纤维纺丝工艺及其影响因素.

10
• 2.纺丝(卷绕)速度:指牵引辊1000m/min • 影响:纺速↑→纺丝线上速度梯度↑、丝束与冷空气的摩擦阻 力↑→ 卷绕丝预取向度↑(双折射↑)、后拉伸倍数↓(初生 纤维内应力增大,沸水收缩率增大) 纺速↓→丝束张力↓→卷绕时发生跳动→纺丝稳定性↓、并丝↑ 喂入轮的速度:约提高1% • 3.喷丝头拉伸比:第一导丝盘速度与熔体喷出速度之比 • 影响:喷丝头拉伸比↑→后拉伸倍数↓→对卷绕丝预取向度影 响小 • 4.卷绕车间温湿度:夏20~27℃,冬20℃ ;相对湿度 60~75%
3
• 2. 纺丝温度Ts(纺丝熔体温度):熔体流出喷丝板孔道
适:285~290℃
前的温度 (1)范围:Tm<纺丝温度< Td;258~265℃<纺丝温度<300℃; 最
;相对分子质量
(2)影响:
Ts高,热降解大,纺丝时易注头,成品纤维的伸长率偏大; Ts低,剪切应力大,形成硬丝,拉伸时易毛丝、断头;波动大,易产生染色 偏差
11
(五)纺丝工艺影响因素
熔体清洁
熔体粘度
原料相对分子质量 熔融温度 纺丝温度 干切片含水率 纺丝压力
机械杂质含量
Hale Waihona Puke 干燥粘度降可纺性孔径 长径比 卷绕速度
吐出量
孔的形状
形变速率
12
冷却均匀性
纺丝温度变动 吹风不匀 风温、风速、风量变动
卷绕丝 均匀性
吐出量波动 卷速波动 组件压力 喷孔排列方式 使用时间
9
• (四)卷绕工艺控制
• 1.上油:卷装、集束等后加工工序顺利进行 • 目的:消除静电,防止绕辊;增加丝束的平滑性,防止丝 束在导丝辊处产生毛丝;增加丝束抱合力,防止丝束松散 • 影响:油剂浓度↑、油轮转速↑、丝束与油盘接触长度 ↑→上 油↑ 上 油 ↑↑→丝条间的集束性↓→卷绕丝桶成型差→丝条后加 工产生粉末 ↑、发烟量↑→ 丝条后加工打滑→成品物理机械 性能↓ 通过调节辊的转速,24对油盘由一台电机传动; 含油水率控制在20~25%。
涤纶短纤维疵点产生的原因及对策
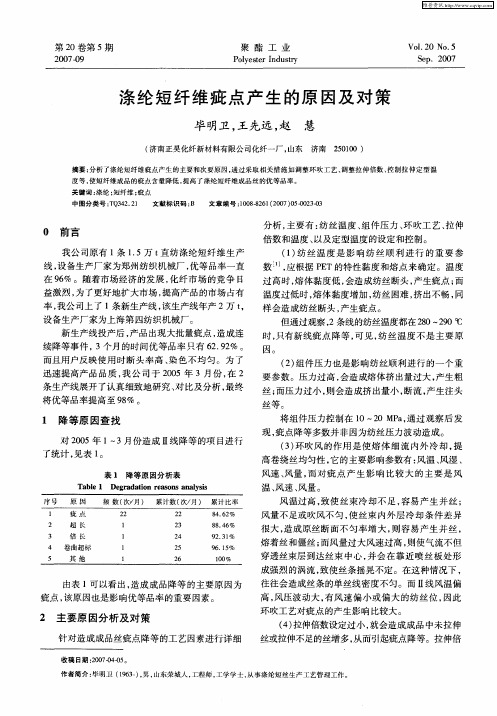
4.1 次要原 因分 析 (1)人 的因素 :使尾 巴丝或 浆块通过 拉 伸工序 进
入切 断机 ,会 造成成 品疵 点多 ;控制 不好 成 品丝 的打 废时 间 ,让综合丝进 入成品 中,也会造成疵点增 多。
(2)环境 的 因素 :设备 清理不 干净 ,一些缠在 辊 子 、导丝 圈上 的 未拉 伸 (或拉 伸 不 足 )毛 丝 、或 浆 块 等 随丝束一 起进 入切断 机 ,也 造成疵点 增 多。
(5)要保 证 成 品 的品 质 ,拉 伸 和 定 型 温 度 都 必 须要选 择 在纤维 的 t (玻 璃 化 温度 )以上 ,t (熔 点 ) 以下 2 J。 Ⅱ线 拉 伸 定 型 温 度 不 稳 定 ,时有 变化 ,过 高 或过低 ,结果造 成疵点 较多 。
调整 ,见 表 3。
表 3 I。H线调整的工艺参数设定值及控制值
Table 3 Process parmneters design value and control value 0f I and H product ion line after treatm ent
3 解 决 方 案
针对 造 成疵 点 降 等 的主要 原 因 ,作 出 了如下 解 决 方案 。 3.1 调整 环吹 工艺
降低 风温 、稳 定风压 、均 匀风速 。 (1)原 纺 丝 风 温 设 定 偏 高 ,将 中 心 值 调 整 至 22 cI=,并 规 定厂 内控 制 范 围 为 ±2 cI=,对 于 风 压 则 规定 厂 内范 围为 ±50 Pa,按 时 巡检 ,一旦 发 现 超 出 此范 围 ,及 时上报 处理 。 (2)每 日测 各 纺 丝 位 的 环 吹情 况 ,发 现 不 合 格 的纺 丝位 ,要及时 调整 ,调整不 好时 ,要及时 更换 。 3.2 调整拉 伸倍数 为 了使后处理拉伸倍数 与前纺纺丝速度 匹配 ,减 少拉伸不足 的现象 ,曾多次调 整纺丝速 度和拉 伸倍 数 见表 2,并采取I、Ⅱ两条生产线互换原丝 进行拉 伸的办 法 ,最后选定最 佳参 数 :纺 丝 速度 为 1 105 m/min;拉 伸倍数为 3.784。
前纺知识——常见纺丝异常现象及修正措施
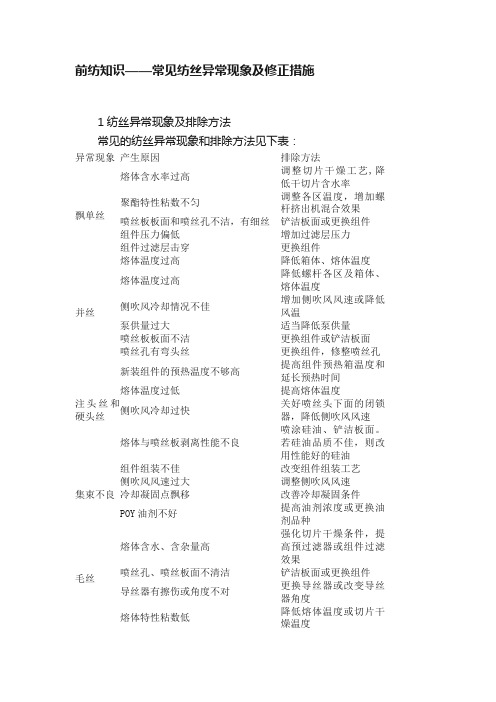
前纺知识——常见纺丝异常现象及修正措施1纺丝异常现象及排除方法常见的纺丝异常现象和排除方法见下表:异常现象 产生原因排除方法飘单丝熔体含水率过高调整切片干燥工艺,降低干切片含水率聚酯特性粘数不匀调整各区温度,增加螺杆挤出机混合效果喷丝板板面和喷丝孔不洁,有细丝 铲洁板面或更换组件 组件压力偏低 增加过滤层压力 组件过滤层击穿 更换组件 熔体温度过高 降低箱体、熔体温度并丝 熔体温度过高降低螺杆各区及箱体、熔体温度侧吹风冷却情况不佳增加侧吹风风速或降低风温泵供量过大 适当降低泵供量 喷丝板板面不洁 更换组件或铲洁板面 喷丝孔有弯头丝 更换组件,修整喷丝孔注头丝和硬头丝 新装组件的预热温度不够高提高组件预热箱温度和延长预热时间熔体温度过低 提高熔体温度侧吹风冷却过快关好喷丝头下面的闭锁器,降低侧吹风风速熔体与喷丝板剥离性能不良 喷涂硅油、铲洁板面。
若硅油品质不佳,则改用性能好的硅油集束不良 组件组装不佳 改变组件组装工艺 侧吹风风速过大 调整侧吹风风速冷却凝固点飘移 改善冷却凝固条件POY 油剂不好提高油剂浓度或更换油剂品种毛丝熔体含水、含杂量高 强化切片干燥条件,提高预过滤器或组件过滤效果喷丝孔、喷丝板面不清洁 铲洁板面或更换组件导丝器有擦伤或角度不对更换导丝器或改变导丝器角度熔体特性粘数低降低熔体温度或切片干燥温度喷丝头拉伸过大降低纺丝速度,增加吐出量丝条晃动过大侧吹风风速过大或过小调整侧吹风风速 卷绕间向纺丝室回风 正确控制纺丝室和卷绕间的风压低分子升华物堵塞侧吹风网清刷侧吹风过滤网2纺丝工艺异常调整表由于聚酯切片、油剂等批号的变更或质量的差异,以及纺丝工艺条件的波动和设备状况的不同,产品和半成品的质量亦会受到影响,为此,必须及时调整工艺参数,确保最佳的生产状况和质量指标。
下表列举主要的工艺调整方法。
调整内容 产生原因调整方法干切片与无油丝间的特性粘数降过大 干切片含水率高改变干燥工艺条件,提高干燥效果螺杆挤出机各区及熔体温度偏高 降低熔体温度,调整螺杆挤出机各区温度 熔体停留时间过长改用浅槽螺杆或提高纺丝吐出量(提高丝条纤度)螺杆转速过快 调整纤维纤度,以适合螺杆挤出机的特性 纤度偏差计量泵吐出量异常 检查讲师泵运转状态,校验计量泵组件漏浆紧固组件、顶紧螺栓或更换组件讲师泵转速过高或过低 调整计量泵转速飘单丝或单丝断裂 按照排队飘单丝的方法处理计量泵之前压力不足 提高计量泵泵前压力 分丝错误认真分丝,集束上油,不分错单丝强度偏差原料切片特性粘数波动加强切片混料和按批号投料干切片含水率波动稳定切片干燥工艺,提高干燥效率 熔体温度过高或过低调整熔体温度 伸度偏差熔体温度过低,引起伸度偏低提高熔体温度 无油丝特性粘数波动改变纺丝、干燥工艺条件,使无油丝特性粘数适中干切片含水率过高,切片干燥温度过高 提高切片干燥效率,降低切片干燥温度 含油不均匀上油嘴部分被阻塞捅通上油嘴孔 上油泵转速不合适调整上油泵转速油剂浓度波动严格分析油剂浓度,调整上油量 油剂浓度过高降低油剂浓度3不良卷绕筒子生产生的原因及排除措施造成卷绕筒子缺陷的原因很多,工艺、设备和操作等因素均会影响卷绕成型,有时,几个因素相互交错,列归纳如表:缺陷名称 产生原因排除措施 凸肩卷绕张力过大增大卷绕角摩擦辊与卷绕筒子接触压力太高降低摩擦辊与卷绕筒子间的接触压力螺旋边卷绕筒管与中间丝层滑动 降低卷绕张力 落丝时,筒管制动速度过快 增大卷绕角筒管夹与摩擦辊未较水平,使卷绕筒子与摩擦辊接触不良 摩擦辊与筒管夹校成平行蛛网丝 横动导丝器每次换向时不在同一位置调整横动导丝器,修正横动凸轮槽换向点 卷绕张力太高降低卷绕张力,增大欠喂率卷绕角太大 减小卷绕角 横动导丝器松动或损坏 调换横动导丝器摩擦辊与筒管夹未较水平校正摩擦辊与筒管夹,增加其转动灵活性 筒管夹转动不灵或筒管有跳动除去筒管夹中可能带入的废丝,更换筒管摩擦辊表面磨损 修理或更换摩擦辊横动导丝器干扰振幅太高减小横动导丝器干扰振幅表面凹凸卷绕张力太高 降低卷绕张力卷绕角过大 减小卷绕角表面丝层脱圈丝不能贴附于筒子两端的表面上减小卷绕角上油量过高增加横动导丝器干扰振幅增加卷绕张力减少上油量叠圈横动导丝器的速度、干扰振幅和周期过小,导丝棒或导丝器与丝接触部分表面损坏增大横动导丝器速度、干扰振幅和周期。
涤纶工业丝断头分析与控制(第三章)
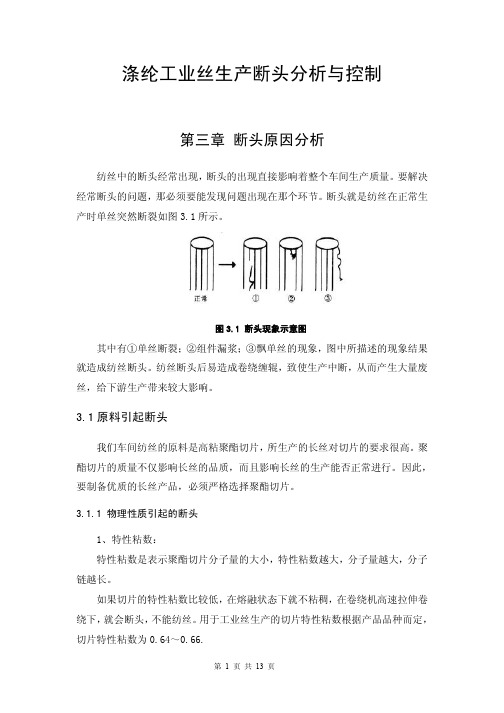
涤纶工业丝装置是把切片熔融纺丝,聚酯切片生产的平稳性就直接影响到纺 丝生产,聚酯车间在做定期作业、失真空、设备日常维护、操作失误时都会造成 粘度波动,使输送给纺丝的熔体品质下降,可纺性变差,引起纺丝工序大量断头 而无法止常生产由于纺丝及后加工工艺是在正常熔体勃度范围内确定的,当熔体
3028 2029 3413
B3-2
454 468 1880 2770 2700 3643
B4-1
598 615 2490 3500 3430 3376
B4-2
531 547 2260 3156 3126 3028
B1-1
88 95 125 226 155
B1-2
88 95 135 232 160
B2-1
或者波动,使纺出的丝条干不匀。 6、组件压力 组件压力用于克服熔体通过过滤层和喷丝板时受得阻力,它与纤维质量的均
匀性密切相关,我们车间是采用高压纺丝,所以组件压力选在 120×105~180× 105。卷绕的质量才比较好。
7、纺丝温度 纺丝温度由螺杆挤出机、纺丝箱体和组件压力决定。熔体的温度控制好,不 仅可纺性好,而且得到的成品丝的物理机械性能也优越。纺丝温度应控制在 285~290℃之间。 8、熔体细流成型区 高聚物在喷丝孔的入口区具有“入口效应”,在孔流区弹性形变的消失需要 一定的时间才能消失,约 0.1~0.3s。由于熔体流经孔道的时间约为 10-4~10-2s, 与松弛时间相差甚远,弹性内应力来不及松弛,故高弹形变的消失非常小。若径 向速度梯度过大,或者说在孔流区的剪切速率过高,亦会继续产生入日效应中的 高弹形变。高弹形变达到极限植,熔体细流发生破裂,无法成纤,引起断头。 9、冷却吹风的温湿度和风速 我们车间采用侧吹风冷却的形式,温度在 25℃左右,纺丝速度增高,侧温 度随之降低,以加快冷却。 冷却风具有一定的湿度,可防止丝条在甬道中与空气摩擦产生静电,湿度控 制在 70%左右。 10、热辊温度 热辊具有牵伸、热定型和改变丝束走向的作用,热辊表面的温度是一个非常 重要的参数。先将我们车间一条线上的卷绕速度及热辊温度罗列如下表:
涤纶短纤维纺丝绕辊因素探讨

Vol. 32 No. 2Mar. 2019第32卷第2期2019-03聚酯工业Polyester Industry doi :10. 3969/j. issn. 1008-8261.2019.02.009涤纶短纤维纺丝绕辘因素探讨张宏伟(中国石油化工股份有限公司天津分公司化工部,天津300270)摘要:对德国NEUMAG 公司引进的短纤维装置近几年的生产情况和控制数据进行了分析,重点探讨了纺丝温度、组件、侧吹 风、上油等关键环节对前纺绕棍的影响,并提出相应对策减少前纺绕規数量.降低熔体单耗。
关键词:涤纶;短纤维;绕棍;纺丝温度;组件;侧吹风;上油中图分类号:TQ323.41 文献标识码:A 文章编号:1008-8261 (2019)02-0031-030前言天津石化化工部短丝前纺装置为直接纺,单线 日产量较高,装置自开车以来由于工艺、设备、操作 等原因出现异常时,绕辐数量相对较多,是影响熔体 单耗的主要因素。
本文结合前纺装置近几年的生产 情况和控制数据,对前纺绕辐产生的原因加以分析 说明,通过优化工艺等措施,明显减少绕银量。
1影响因素1.1聚酯熔体黏度熔体品质好坏对纤维成形和成品品质影响很 大。
特性黏度是聚酯性能最重要的指标,它反映了 高聚物分子质量的大小,是纺丝稳定性的关键。
聚 酯特性黏度和动力黏度的关系是:lg/i = -1.48+330/1+5.02 xlg [q ]⑷。
式中:M 为动力黏度/(Pa • s);t 是熔体温 度/*;["]为特性黏K/(dL-g')特性黏度的波动越小,动力黏度的波动也随之 趋稳,纺丝也就越稳定。
当熔体黏度波动超标时,熔 体支管压力和组件压力会发生较大变化。
低的支管 压力将导致计量泵填充不满,不能均匀地输送熔体, 使原丝线密度不足或不匀;高的支管压力将增大计 量泵的工作负荷,从而使熔体温度升高,冷却成形困 难,原丝取向也会降低。
组件压力的波动不仅使组 件强度受损,使用寿命缩短,而且箱体内熔体温度随 着组件压力降的波动而变化。
涤纶短纤维纺丝工艺及其影响因素

教案首页
教学内容
3. 纺丝工艺控制:
3.1熔融工艺
螺杆各区温度:1个冷却区,5个加热区;
3.1.2 熔体输送
3.1.3纺丝温度(纺丝熔体温度):熔体流出喷丝板孔道前的温度
3.2喷丝条件:
螺杆挤出压力:范围:65*105~75*105Pa
过滤器压力:
3.3泵供量
3.4组件压力(纺丝熔体压力):
3.5丝条冷却固化条件:
(1)风温:范围:20~30℃,±1 ℃,组件调换率、卷绕丝双折射率、卷绕丝条干不匀率最低(2)风湿: 65~85%;风湿对卷绕丝双折射率和纺丝稳定性影响大
(3)风速(风量):0.3~0.7m/s,与熔体吐出量有关
(4)吹出距离(缓冷区):吹风环与板面距离 ,15cm;吹风面距丝束外缘距离1cm;高度20cm (5)纺丝甬道:3.2-7m,圆管Φ280mm
4.卷绕工艺控制:
4.1上油:卷装、集束等后加工工序顺利进行
4.2纺丝(卷绕)速度:牵伸辊1000m/min
4.3喷丝头拉伸比:第一导丝盘速度与熔体喷出速度之比
影响:喷丝头拉伸比↑→后拉伸倍数↓→对卷绕丝预取向度影响小
4.4卷绕车间温湿度:夏20~27℃,冬20℃;相对湿度60~75%
5.工艺影响因素:
卷绕丝均匀性
冷却均匀性 组件结构
可纺性
熔体清洁
熔体粘度
形变速率
孔的形状。
涤纶纤维生产中毛丝原因与措施
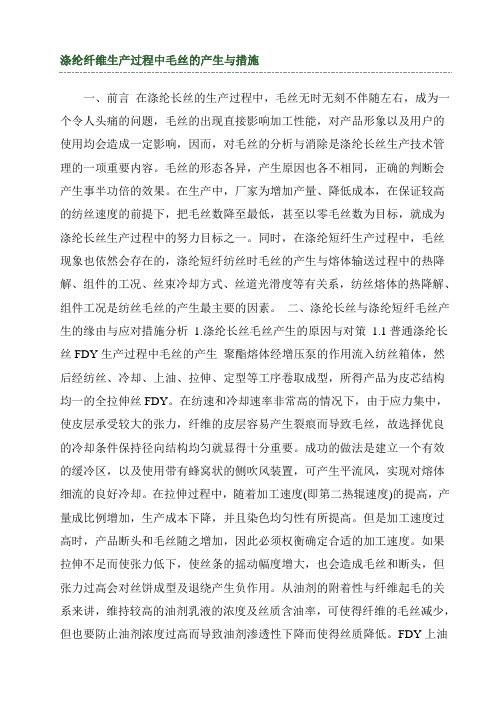
涤纶纤维生产过程中毛丝的产生与措施一、前言在涤纶长丝的生产过程中,毛丝无时无刻不伴随左右,成为一个令人头痛的问题,毛丝的出现直接影响加工性能,对产品形象以及用户的使用均会造成一定影响,因而,对毛丝的分析与消除是涤纶长丝生产技术管理的一项重要内容。
毛丝的形态各异,产生原因也各不相同,正确的判断会产生事半功倍的效果。
在生产中,厂家为增加产量、降低成本,在保证较高的纺丝速度的前提下,把毛丝数降至最低,甚至以零毛丝数为目标,就成为涤纶长丝生产过程中的努力目标之一。
同时,在涤纶短纤生产过程中,毛丝现象也依然会存在的,涤纶短纤纺丝时毛丝的产生与熔体输送过程中的热降解、组件的工况、丝束冷却方式、丝道光滑度等有关系,纺丝熔体的热降解、组件工况是纺丝毛丝的产生最主要的因素。
二、涤纶长丝与涤纶短纤毛丝产生的缘由与应对措施分析1.涤纶长丝毛丝产生的原因与对策 1.1普通涤纶长丝FDY生产过程中毛丝的产生聚酯熔体经增压泵的作用流入纺丝箱体,然后经纺丝、冷却、上油、拉伸、定型等工序卷取成型,所得产品为皮芯结构均一的全拉伸丝FDY。
在纺速和冷却速率非常高的情况下,由于应力集中,使皮层承受较大的张力,纤维的皮层容易产生裂痕而导致毛丝,故选择优良的冷却条件保持径向结构均匀就显得十分重要。
成功的做法是建立一个有效的缓冷区,以及使用带有蜂窝状的侧吹风装置,可产生平流风,实现对熔体细流的良好冷却。
在拉伸过程中,随着加工速度(即第二热辊速度)的提高,产量成比例增加,生产成本下降,并且染色均匀性有所提高。
但是加工速度过高时,产品断头和毛丝随之增加,因此必须权衡确定合适的加工速度。
如果拉伸不足而使张力低下,使丝条的摇动幅度增大,也会造成毛丝和断头,但张力过高会对丝饼成型及退绕产生负作用。
从油剂的附着性与纤维起毛的关系来讲,维持较高的油剂乳液的浓度及丝质含油率,可使得纤维的毛丝减少,但也要防止油剂浓度过高而导致油剂渗透性下降而使得丝质降低。
涤纶短纤维后加工操作要点和故障处理
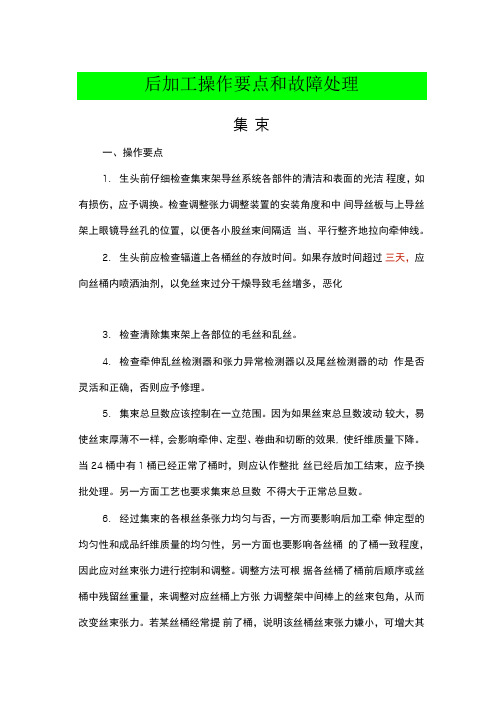
集束一、操作要点1.生头前仔细检查集束架导丝系统各部件的清洁和表面的光洁程度,如有损伤,应予调换。
检查调整张力调整装置的安装角度和中间导丝板与上导丝架上眼镜导丝孔的位置,以便各小股丝束间隔适当、平行整齐地拉向牵伸线。
2.生头前应检查辐道上各桶丝的存放时间。
如果存放时间超过三天,应向丝桶内喷洒油剂,以免丝束过分干燥导致毛丝增多,恶化3.检查清除集束架上各部位的毛丝和乱丝。
4.检查牵伸乱丝检测器和张力异常检测器以及尾丝检测器的动作是否灵活和正确,否则应予修理。
5.集束总旦数应该控制在一立范围。
因为如果丝束总旦数波动较大,易使丝束厚薄不一样,会影响牵伸、定型、卷曲和切断的效果, 使纤维质量下降。
当24桶中有1桶已经正常了桶时,则应认作整批丝已经后加工结束,应予换批处理。
另一方面工艺也要求集束总旦数不得大于正常总旦数。
6.经过集束的各根丝条张力均匀与否,一方而要影响后加工牵伸定型的均匀性和成品纤维质量的均匀性,另一方面也要影响各丝桶的了桶一致程度,因此应对丝束张力进行控制和调整。
调整方法可根据各丝桶了桶前后顺序或丝桶中残留丝重量,来调整对应丝桶上方张力调整架中间棒上的丝束包角,从而改变丝束张力。
若某丝桶经常提前了桶,说明该丝桶丝束张力嫌小,可增大其张力调整架的丝束包角,反之,若某丝桶的桶脚丝一直较多,说明该桶位丝束张力嫌大,这时可减小其张力调整架的丝束包角。
通过调整,可控制各丝束张力均匀一致,从而防止集朿后的大股丝朿中出现“荡丝”、“拖尾丝”等现象。
7.按照操作规程进行集束生头,要求剪去丝端硬头,丝条在导丝架各部件上穿丝位置正确,无扭结、交叉现象。
8.正常生产过程中,应加强巡回检查,发现荡丝、吊丝以及丝条缠结时,可采取停车或不停车处理。
当集束架各导丝罗拉上存有毛丝、乱丝时,应及时清除,以免被丝束带入后加工生产线,形成疵点。
9.集束采用整批换桶,一般中途不补加丝束,但如遇特殊情况处理半桶丝时,可补加丝束,应避免打结,而只需将补加丝头嵌入其它丝束之中即可(待卷曲前将未拉伸部分剪去)。
- 1、下载文档前请自行甄别文档内容的完整性,平台不提供额外的编辑、内容补充、找答案等附加服务。
- 2、"仅部分预览"的文档,不可在线预览部分如存在完整性等问题,可反馈申请退款(可完整预览的文档不适用该条件!)。
- 3、如文档侵犯您的权益,请联系客服反馈,我们会尽快为您处理(人工客服工作时间:9:00-18:30)。
涤纶短纤维生产前纺常见问题分析
摘要:涤纶短纤维实际生产中存在一个问题:断头频发,这使得产品生产成本
大大增加。
要保证生产高效平稳,提高产品质量,需要对纺位的组件、油盘问题进
行处理。
关键字:涤纶短纤维;组件;油盘;断头
1、影响前纺生产平稳的因素
洛阳分公司短纤装置采用聚酯装置生产的聚酯融体为原料,采用熔体纺丝法:纺丝熔体从喷丝板微孔中挤出形成细流,挤出的融体细流拉长、变细、冷却固化,固态丝束给湿上油和卷绕落桶。
前纺的生产流程所关键设备包括:组件、环吹桶、油盘、束丝棒(主要是陶
瓷蝶型辊丝束集束)、疵点检测器、导辊以及七辊牵引机。
在涤纶短纤维的形成中,组件工况不良会出现一些异常如飘单丝以及断头丝,其内部结构分布不均匀,形状不规则,影响纺丝的正常进行;而环吹桶漏风、油盘上油不匀、挂丝等也会
对生产产生不良影响。
对丝束质量产生影响的主要是组件、环吹桶以及油盘。
2、组件工况对生产的影响
2.1 组件的结构
组件的零部件有:上盖、本体、分配板、喷丝板、底座圈等组成。
在组件组
装的过程中过滤材料也需要得到较好的控制,其主要是过滤网和过滤砂。
钢砂更
好的混合和过滤熔体,使融体更加均匀,在分配板、喷丝板均加以过滤网能够有
效过滤杂质,分配板将融体分配不同的喷丝孔,然后在压力的作用下,从喷丝孔
喷出,形成细流。
喷丝板是组件的重要构成部分,其孔径、孔长和导孔底部锥角
都是其关键指标。
2.2 组件组装过程中出现的问题以及影响
组件组装时组装台吹扫不干净,容易造成板面的污染,使喷丝板面光洁度下降,从而影响对融体的剥离性。
喷丝板面的划伤不仅仅影响剥离性,也会损伤喷
丝孔,进而造成出丝不畅而产生毛丝。
组件内部密封性不好,造成融体漏浆。
滤
网不达标会导致融体过滤时阻力不均,出现强丝或弱丝,从而造成纺位浆块、断
头增多影响生产。
2.3 组件使用过程中出现的问题
1、组件升压速度异常
在生产过程中,组件的升压速度,主要受到融体增量和时间的影响。
从一般
角度分析,升压速度会在熔体负荷增加、过滤精度提升的情况下有所加快,升压
会影响组件内部结构。
2、熔体黏板
在板面温度较高时,板面上的杂质会导致剥离性较差,无法均匀喷射硅油,
出现斑点,造成孔口堵塞这种熔体黏板的最终结果,是熔体形成块状,造成纺位
断头
3、喷丝孔出丝异常
如果纺丝过程,喷丝孔内部不光滑或存有杂质,就会形成单丝,而单丝主要
是一节一节的,属于不连续的、间断的丝。
这种单丝会持续较长的时间,有着固
定的位置,是小块聚合体,在涤纶短纤维纺丝中,是一种常见的疵点。
如果板前
网被击穿导致部分出丝孔漏浆,需要组件人员进行堵孔,并做好记录。
4、组件漏浆
主要有两种现象,一是组件内漏,熔体从喷丝板中心或是喷丝板与组件的结
合处,有大部分黑色熔体,黑色融体下落遇冷成为浆块随丝束下行,造成断头,
出现这种情况的原因,是组件的密封性不好,在组件组装过程中各个部件之间受
力不均导致密封圈跑偏或是变形造成的。
第二种现象是组件外漏,主要是组件刚
上机,就在短时间内出现连接处漏浆,这种情况主要是入口垫圈未安装好或紧固
不到位造成的对于中心漏浆,需要对中心螺栓进行热紧,外漏则应该热紧上位螺
栓或更换入口垫圈。
2.4.组件的使用
1 组件组装预热
工作人员需要对纺丝组件进行更换,在使用前需要组装好备用的组件,然后
将其放到预热炉中,在温度达到工艺要求后,进行热紧。
上位前注意组件的降温
时间,防止过热造成粘板。
规范组件的使用的时间,工作人员定期更换组件,能
够更好的控制纺丝的稳定性,提升原丝的质量,降低异常丝的产生。
2 纺丝的修板作业
纺丝的定期修板作业主要在喷丝板表面喷涂硅油,再用修板刀除掉板面的熔
体升华物和硅氧化合物。
通过这种方式增加喷丝板的熔体剥离性,减少粘板情况
和浆块产生,工作人员要较好的控制盛丝桶的最上部或最下部(横动换桶前后),以减少后纺加工时异常丝的产生。
针对纺丝定期作业,要加强标准化操作监督,
保证纺位的作业质量,减少重复断头现象的产生。
3 组件装拆、清洗操作以及喷丝板镜检
工作人员针对到期或异常的下位更换,需要按照标准流程,使用特定的工具
进行组件的装卸。
对于喷丝板等关键部位,工作人员需要认真清洗,然后将其放
入专用的格架,放置板之间的摩擦,由此损坏板面。
工作人员要使用跟踪卡,记
录组装和喷丝板号,以及上机和下机的时间,整体过程需要对喷丝板的使用质量,进行准确的跟踪。
喷丝板的镜验主要是在喷丝板经过超声波清洗后,针对导孔光洁度、有无异
物堵塞、微孔有无异常、板面有无伤痕进行检查,在针对喷丝板的检验中,使用
铅笔、通孔针或是金针等。
如果工作人员在镜验中,发现内部存在堵塞,要使用
金针进行清理,然后使用气枪吹净。
在证镜检合格后可放入干燥、清洁的环境中。
在生产中工作人员要注重纺丝组件的工况检查,聚酯粘度、负荷的波动都会
对组件工况产生影响,尤其在断头大面积更改负荷后组件可能会出现中心螺栓漏
浆现象,需要对组件进行热紧。
3、环吹桶以及油盘工况对生产的影响
在生产过程中到期的环吹桶或者新上位的环吹桶因密封性降低导致漏风会吹
乱新出的丝束,致使出丝孔处丝束粘连形成疵点、浆块从而导致纺位断头;油盘
出油不均,新生丝束无法及时上油从而导致摩丝,造成卷绕缠辊。
在纺丝定修作
业时,首先应对环吹桶进行检查,如果漏风应及时更换,针对出油不匀的油盘应
进行调整,必要时进行更换。
4、结束语
在涤纶短纤维前纺生产中,员工应加强对纺丝设备的关注,对于聚酯粘度、
压力波动要做好恰当的应对措施,对于定修岗位的组件、环吹、油盘工况进行检查,定修作业时要严格按照标准化操作,确保纺位的作业质量,避免重复断头,
保证生产线的平稳运行。
参考文献:
[1]刘力威,尹正路,白万勇. 涤纶短纤维疵点的产生原因及对策[J]. 化工管理,2014,(26):28+30
[2]高仲芳. 涤纶短纤维物理机械特性与混纺纱品质指标的关系[J]. 棉纺织技术,1982,(02):2-5.
[3]王鸣义,林雪梅.民用涤纶短纤维生产技术及产品发展趋势[J].合成纤维,2012(09):6-10。