催化裂化汽油组成及其特点
催化裂化工艺介绍

1。
0催化裂化催化裂化是原料油在酸性催化剂存在下,在500℃左右、1×105~3×105Pa 下发生裂解,生成轻质油、气体和焦炭的过程.催化裂化是现代化炼油厂用来改质重质瓦斯油和渣油的核心技术,是炼厂获取经济效益的重要手段。
催化裂化的石油炼制工艺目的:1)提高原油加工深度,得到更多数量的轻质油产品;2)增加品种,提高产品质量。
催化裂化是炼油工业中最重要的一种二次加工工艺,是重油轻质化和改质的重要手段之一,已成为当今石油炼制的核心工艺之一。
1。
1催化裂化的发展概况催化裂化的发展经历了四个阶段:固定床、移动床、流化床和提升管。
见下图:固定床移动床流化床提升管(并列式)在全世界催化裂化装置的总加工能力中,提升管催化裂化已占绝大多数。
1。
2催化裂化的原料和产品1。
2。
0原料催化裂化的原料范围广泛,可分为馏分油和渣油两大类。
馏分油主要是直馏减压馏分油(VGO),馏程350—500℃,也包括少量的二次加工重馏分油如焦化蜡油等,以此种原料进行催化裂化称为馏分油催化裂化。
渣油主要是减压渣油、脱沥青的减压渣油、加氢处理重油等。
渣油都是以一定的比例掺入到减压馏分油中进行加工,其掺入的比例主要受制于原料的金属含量和残炭值.对于一些金属含量低的石蜡基原有也可以直接用常压重油为原料。
当减压馏分油中掺入渣油使通称为RFCC。
以此种原料进行催化裂化称为重油催化裂化。
1。
2.1产品催化裂化的产品包括气体、液体和焦炭。
1、气体在一般工业条件下,气体产率约为10%-20%,其中含干气和液化气。
2、液体产物1)汽油,汽油产率约为30%-60%;这类汽油安定性较好。
2)柴油,柴油产率约为0—40%;因含较多芳烃,所有十六烷值较低,由重油催化裂化得到的柴油的十六烷值更低,这类柴油需经加氢处理。
3)重柴油(回炼油),可以返回到反应器内,已提高轻质油收率,不回炼时就以重柴油产品出装置,也可作为商品燃料油的调和组分。
4)油浆,油浆产率约为5%—10%,从催化裂化分馏塔底得到的渣油,含少量催化剂细粉,可以送回反应器回炼以回收催化剂。
重油催化裂化

重油催化裂化(residue fluid catalytIC cracking,即RFCC)工艺的产品是市场极需的高辛烷值汽油馏分,轻柴油馏分和石油化学工业需要的气体原料。
由于该工艺采用了分子筛催化剂、提升管反应器和钝化剂等,使产品分布接近一般流化催化裂化工艺。
但是重油原料中一般有30%~50%的廉价减压渣油,因此,重油流化催化裂化工艺的经济性明显优于一般流化催化工艺,是近年来得到迅速发展的重油加工技术。
㈠重油催化裂化的原料所谓重油是指常压渣油、减压渣油的脱沥青油以及减压渣油、加氢脱金属或脱硫渣油所组成的混合油。
典型的重油是馏程大于350℃的常压渣油或加氢脱硫常压渣油。
与减压馏分相比,重油催化裂化原料油存在如下特点:①粘度大,沸点高;②多环芳香性物质含量高;③重金属含量高;④含硫、氮化合物较多。
因此,用重油为原料进行催化裂化时会出现焦炭产率高,催化剂重金属污染严重以及产物硫、氮含量较高等问题。
㈡重油催化裂化的操作条件为了尽量降低焦炭产率,重油催化裂化在操作条件上采取如下措施:1、改善原料油的雾化和汽化由于渣油在催化裂化过程中呈气液相混合状态,当液相渣油与热催化剂接触时,被催化剂吸附并进入颗粒内部的微孔,进而裂化成焦炭,会使生焦量上升,催化活性下降。
因此可见,为了减少催化剂上的生焦量,必须尽可能地减少液相部分的比例,所以要强化催化裂化前期过程中的雾化和蒸发过程,提高气化率,减少液固反应。
2、采用较高的反应温度和较短的反应时间当反应温度提高时,原料的裂化反应加快较多,而生焦反应则加快较少。
与此同时,当温度提高时,会促使热裂化反应的加剧,从而使重油催化裂化气体中C1、C2增加,C3、C4 减少。
所以宜采用较高反应温度和较短的反应时间。
㈢重油催化裂化催化剂重油催化裂化要求其催化剂具有较高的热稳定性和水热稳定性,并且有较强的抗重金属污染的能力。
所以,目前主要采用Y型沸石分子筛和超稳Y型沸石分子筛催化剂。
㈣重油催化裂化工艺1、重油催化裂化工艺与一般催化裂化工艺的异同点两工艺既有相同的部分,亦有不同之处,完全是由于原料不同造成的。
催化裂化
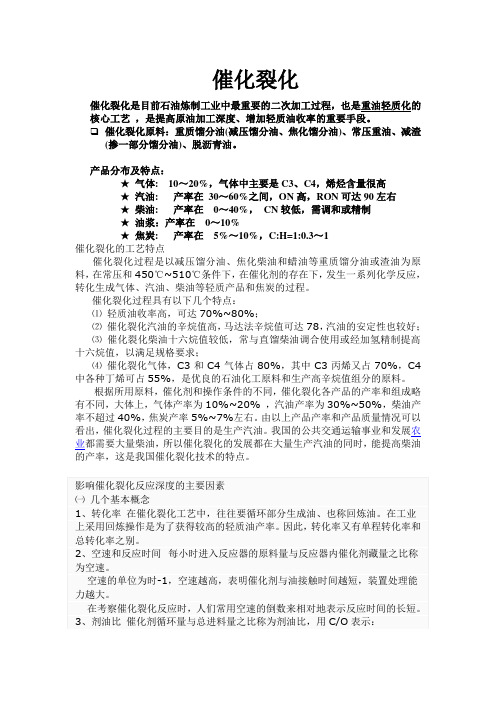
催化裂化催化裂化是目前石油炼制工业中最重要的二次加工过程,也是重油轻质化的核心工艺,是提高原油加工深度、增加轻质油收率的重要手段。
催化裂化原料:重质馏分油(减压馏分油、焦化馏分油)、常压重油、减渣(掺一部分馏分油)、脱沥青油。
产品分布及特点:★气体: 10~20%,气体中主要是C3、C4,烯烃含量很高★汽油: 产率在30~60%之间,ON高,RON可达90左右★柴油: 产率在0~40%,CN较低,需调和或精制★油浆:产率在0~10%★焦炭: 产率在5%~10%,C:H=1:0.3~1催化裂化的工艺特点催化裂化过程是以减压馏分油、焦化柴油和蜡油等重质馏分油或渣油为原料,在常压和450℃~510℃条件下,在催化剂的存在下,发生一系列化学反应,转化生成气体、汽油、柴油等轻质产品和焦炭的过程。
催化裂化过程具有以下几个特点:⑴轻质油收率高,可达70%~80%;⑵催化裂化汽油的辛烷值高,马达法辛烷值可达78,汽油的安定性也较好;⑶催化裂化柴油十六烷值较低,常与直馏柴油调合使用或经加氢精制提高十六烷值,以满足规格要求;⑷催化裂化气体,C3和C4气体占80%,其中C3丙烯又占70%,C4中各种丁烯可占55%,是优良的石油化工原料和生产高辛烷值组分的原料。
根据所用原料,催化剂和操作条件的不同,催化裂化各产品的产率和组成略有不同,大体上,气体产率为10%~20% ,汽油产率为30%~50%,柴油产率不超过40%,焦炭产率5%~7%左右。
由以上产品产率和产品质量情况可以看出,催化裂化过程的主要目的是生产汽油。
我国的公共交通运输事业和发展农业都需要大量柴油,所以催化裂化的发展都在大量生产汽油的同时,能提高柴油的产率,这是我国催化裂化技术的特点。
在同一条件下,剂油比大,表明原料油能与更多的催化剂接触。
㈡影响催化裂化反应深度的主要因素影响催化裂化反应转化率的主要因素有:原料性质、反应温度、反应压力、反应时间。
1、原料油的性质原料油性质主要是其化学组成。
催化裂化汽油辛烷值
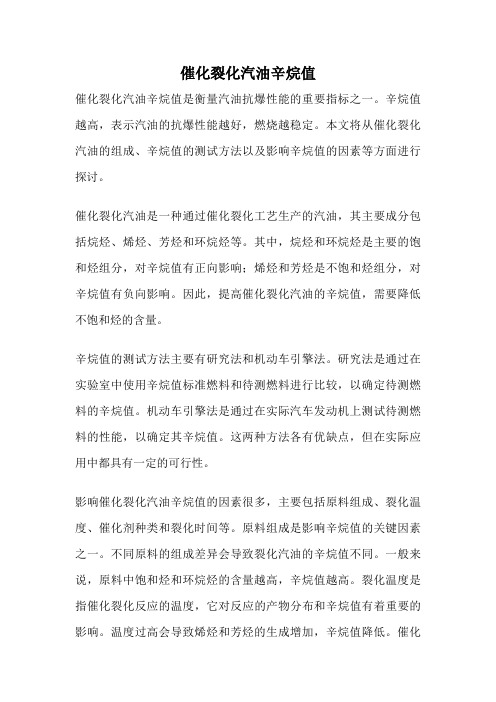
催化裂化汽油辛烷值催化裂化汽油辛烷值是衡量汽油抗爆性能的重要指标之一。
辛烷值越高,表示汽油的抗爆性能越好,燃烧越稳定。
本文将从催化裂化汽油的组成、辛烷值的测试方法以及影响辛烷值的因素等方面进行探讨。
催化裂化汽油是一种通过催化裂化工艺生产的汽油,其主要成分包括烷烃、烯烃、芳烃和环烷烃等。
其中,烷烃和环烷烃是主要的饱和烃组分,对辛烷值有正向影响;烯烃和芳烃是不饱和烃组分,对辛烷值有负向影响。
因此,提高催化裂化汽油的辛烷值,需要降低不饱和烃的含量。
辛烷值的测试方法主要有研究法和机动车引擎法。
研究法是通过在实验室中使用辛烷值标准燃料和待测燃料进行比较,以确定待测燃料的辛烷值。
机动车引擎法是通过在实际汽车发动机上测试待测燃料的性能,以确定其辛烷值。
这两种方法各有优缺点,但在实际应用中都具有一定的可行性。
影响催化裂化汽油辛烷值的因素很多,主要包括原料组成、裂化温度、催化剂种类和裂化时间等。
原料组成是影响辛烷值的关键因素之一。
不同原料的组成差异会导致裂化汽油的辛烷值不同。
一般来说,原料中饱和烃和环烷烃的含量越高,辛烷值越高。
裂化温度是指催化裂化反应的温度,它对反应的产物分布和辛烷值有着重要的影响。
温度过高会导致烯烃和芳烃的生成增加,辛烷值降低。
催化剂种类和裂化时间也会对辛烷值产生影响,不同的催化剂和裂化时间会导致不同的裂化汽油组分分布,从而影响辛烷值的大小。
为了提高催化裂化汽油的辛烷值,可以采取一些措施。
首先,选择适宜的原料。
通过调整原料的配比和来源,可以控制原料中饱和烃和环烷烃的含量,从而影响辛烷值。
其次,优化裂化工艺条件。
通过调整裂化温度、催化剂种类和裂化时间等参数,可以使得裂化汽油的组成更加有利于提高辛烷值。
此外,还可以采用一些辅助措施,如加氢处理和选择合适的催化剂等,来提高裂化汽油的辛烷值。
催化裂化汽油辛烷值是衡量汽油抗爆性能的重要指标之一。
通过调整原料组成、优化裂化工艺条件和采取辅助措施等手段,可以提高催化裂化汽油的辛烷值。
催化裂化机理及特点

催化裂化机理及特点催化裂化是一种通过加热和催化剂的作用将长链烃分子裂解为短链烃分子的重要工艺。
催化裂化机理及特点主要包括以下几个方面:一、催化裂化机理1.构造反应:长链烃分子在裂化过程中首先发生构造反应,通过裂解碳-碳键,形成相对较短的碳链碳烃和烯烃。
2.重排反应:长链烃分子中的骨架碳骨架会经历一系列重排反应,使得产物中更多的是相对稳定的异构体和环状化合物。
3.脱氢反应:重排反应过程中,长链分子中的烃基可能失去氢原子,从而形成烯烃,增加了催化裂化的产物中烯烃的含量。
4.脱氢裂解反应:在高温高压下,部分碳链碳烃可以发生脱氢裂解反应,形成更短的链长烃烃烃烃、烯烃和芳香烃。
二、催化裂化特点1.催化裂化具有高选择性:在催化剂的影响下,催化裂化反应主要发生在长链烃分子中的弱键和缺陷位置,使得产物中的碳链长度相对较短,同时产生更多的异构体和环状化合物。
2.催化裂化反应速度快:催化剂的存在提高了反应活性,使得裂化反应可以在相对低的温度和压力下进行,加快了反应速度。
3.催化裂化可以产生高附加值的产品:催化裂化使得重质燃料油转化为轻质烃类产品,其中包括汽油、炼厂气、润滑油基础油等,这些产品有较高的附加值。
4.催化裂化可以降低能源消耗:通过催化裂化将重质原油转化为较轻质产品,如汽油和炼厂气,不仅提供了更多的高附加值产品,还减少了对原油的需求,降低了能源消耗。
5.催化裂化可以调节产品分布:通过不同的催化剂组合和反应条件,可以调节催化裂化产物的碳链长度分布,以满足市场需求,提高产品经济效益。
总之,催化裂化是一种高效、高选择性的炼油工艺,通过加热和催化剂的作用,将长链烃分子裂解为短链烃分子,产生高附加值产品,并降低能源消耗。
催化裂化机理和特点的深入研究对于提高炼油工艺的效率和降低能源消耗具有重要意义。
催化裂化的工艺特点及基本原理

教案叶蔚君5.1催化裂化的工艺特点及基本原理[引入]:先提问复习,再从我国催化裂化汽油产量所占汽油总量的比例引入本章内容。
[板书]:催化裂化一、概述1、催化裂化的定义、反应原料、反应产物、生产目的[讲述]:1.催化裂化的定义(重质油在酸性催化剂存在下,在470~530O C的温度和0.1~0.3MPa的条件下,发生一系列化学反应,转化成气体、汽油、柴油等轻质产品和焦炭的过程。
)、反应原料:重质油;(轻质油、气体和焦炭)、(轻质油);[板书]2.催化裂化在炼油厂申的地位和作用:[讲述]以汽油为例,据1988年统计,全世界每年汽油总消费量约为6.5亿吨以上,我国汽油总产量为1750万吨,从质量上看,目前各国普通级汽油一般为90-92RON、优质汽油为96-98RON,我国1988年颁布车用汽油指标有两个牌号,其研究法辛烷值分别为不低于90和97。
但是,轻质油品的来源只靠直接从原油中蒸馏取得是远远不够的。
一般原油经常减压蒸馏所提供的汽油、煤油和柴油等轻质油品仅有10-40%,如果要得到更多的轻质产品以解决供需矛盾,就必须对其余的生质馏分以及残渣油进行二次加工。
而且,直馏汽油的辛烷值太低,一般只有40-60MON,必须与二次加工汽油调合使用。
国内外常用的二次加工手段主要有热裂化、焦化、催化裂化和加氢裂化等。
而热裂化由于技术落后很少发展,而且正逐渐被淘汰,焦化只适用于加工减压渣油,加氢裂化虽然技术上先进、产品收率高、质量好、灵活性大,但设备复杂,而且需大量氢气,因此,技术经济上受到一定限制,所以,使得催化裂化在石油的二次加工过程中占居着重要地位(在各个主要二次加工工艺中居于首位)。
特别是在我国,车用汽油的组成最主要的是催化裂化汽油,约占近80%。
因此,要改善汽油质量提高辛烷值,首先需要把催化裂化汽油辛烷值提上去。
目前我国催化裂化汽油辛烷值RON偏低,必须采取措施改进工艺操作,提高催化剂质量,迅速赶上国际先进水平。
催化裂化汽油组成及其特点

5.加氢对催化裂化汽油组成影响
5.1 催化汽油加氢脱硫 5.2 催化汽油加氢脱硫后烯烃变化 5.3 催化汽油加氢脱硫后芳烃变化 5.4 催化汽油加氢脱硫后辛烷值变化
5.1 催化汽油加氢脱硫
—生产S≤50ppm汽油深度脱硫新工艺
5.35 1.38 100.00 68.70 92.65
54.8
29.6
8.4
10.6
82.2
77.3
变化幅度 -18
提升管** 变径提升管
沸石
沸**石
常压渣油
5.5
1.15
变化幅度 -4.35
-0.06 -0.68 +5.43 -4.20
-0.65
+4.20 +0.31
3.79 15.44 44.14 22.57 4.64 8.92 0.50 100.00 72.79 82.15
蒸气压,kPa
从11月1日至4月30日 不大于
从5月1日至10月31日 不大于
硫含量,μg/g
不大于
0.005 /0.01 /0.016 2.7 /0.3
70 120 190 205
2
88 72 150
苯含量,%(v/v) 芳烃含量, %(v/v) 烯烃含量, %(v/v)
不大于
1
不大于
40
不大于
30
汽油收率,% 汽油组成(体积分数),%
饱和烃 烯烃 芳烃 汽油RON 汽油MON
空白 538 0.0 0.0 27.34
10.6 72.8 16.6 95.2 79.8
安庆DCC装置方案 汽油回炼 540 17.5 0.0 23.05
13.3 62.6 24.1 96.3 80.7
催化裂化的工艺特点及基本原理

催化裂化的工艺特点及基本原理催化裂化是一种重要的石油加工工艺,其开发和应用对于提高石油产业发展水平具有重要的意义。
催化裂化工艺的特点和基本原理如下:一、工艺特点:1.高选择性:催化裂化工艺可以将石油馏分中的大分子烃化合物按照其碳数分解为较低碳数的烃化合物,其中可选择的烃化合物主要是汽油和液化气。
因此,催化裂化可以提高汽油和液化气产率,达到更好的操作经济效益。
2.产物分布广:催化裂化反应不仅可以生成汽油和液化气,还可以生成较低碳数的烃化合物,如乙烯、丙烯等。
因此,催化裂化反应可以提供多种不同碳数的烃化合物,满足不同需求。
3.增塔体积积极:催化裂化工艺采用固定床反应器,反应器内填充了催化剂颗粒,因此反应器体积较大。
大体积的反应器可以增加催化裂化反应的容量,提高石油裂解速率,并且还可以增加反应过程的稳定性和可控性。
4.废气利用:催化裂化反应产生的废气中含有非常丰富的烃化合物和能量,可以通过适当的处理和回收利用,从而得到更好的经济效益,并减少对环境的污染。
二、基本原理:催化裂化反应是通过催化剂的作用来进行的,其基本原理如下:1.裂解反应:石油中的长链烃化合物在催化剂的作用下发生热裂解反应,将大分子烷烃分解成较小分子的烃化合物。
这种反应是一个链状反应过程,会生成一系列的短链烃化合物和碳氢烃中间体。
2.重排反应:短链烃化合物和碳氢烃中间体在催化剂的作用下发生重排反应,重新组合成不同碳数的烃化合物。
3.芳构化反应:在催化裂化过程中,由于催化剂特殊的性质,烃化合物还会发生芳构化反应,生成芳烃类化合物,如苯、甲苯等。
4.积碳反应:由于裂化过程产生的碳元素会在催化剂表面析出,形成碳黑,导致催化剂失活。
因此,催化裂化还需要定期对催化剂进行再生,以保持其活性。
综上所述,催化裂化工艺具有高选择性、广泛的产物分布、增塔体积积极和废气利用等特点。
其基本原理包括裂解反应、重排反应、芳构化反应和积碳反应。
催化裂化工艺的开发和应用有助于提高石油产业的经济效益和环境可持续性。
- 1、下载文档前请自行甄别文档内容的完整性,平台不提供额外的编辑、内容补充、找答案等附加服务。
- 2、"仅部分预览"的文档,不可在线预览部分如存在完整性等问题,可反馈申请退款(可完整预览的文档不适用该条件!)。
- 3、如文档侵犯您的权益,请联系客服反馈,我们会尽快为您处理(人工客服工作时间:9:00-18:30)。
美国,φ% 36 35 4 12 5 8
欧洲,φ% 35 38 3 8 7 9
中国,φ% 74.1 14.6 9.8
1.5Leabharlann 我国汽油组成中74%以上来自FCCU
中国化工经济 技术发展中心 2010年报告
1.4 汽油组成特点
项目
硫
苯
芳
烯
辛烷值
直馏汽油
基准
-
-
-
-
催化裂化汽油 高
高
重整汽油
高
高
高
烷基化汽油
蒸气压,kPa
从11月1日至4月30日 不大于
从5月1日至10月31日 不大于
硫含量,μg/g
不大于
0.005 /0.01 /0.016 2.7 /0.3
70 120 190 205
2
88 72 150
苯含量,%(v/v) 芳烃含量, %(v/v) 烯烃含量, %(v/v)
不大于
1
不大于
40
不大于
30
4.不同催化裂化工艺汽油组成特点及其对比
硫、苯、芳、烯
5.加氢对催化裂化汽油组成影响
降硫、苯、芳、烯,辛烷值
6. 结论
1.催化裂化汽油概述
1.1 发动机要求-国标
1.2 理想组成 1.3 汽油池组成 1.4 FCC汽油组成特点
1.1 汽油机要求
汽油作为汽车的点燃式发动机燃料,要求汽油 良好的蒸发性能:馏程&饱和蒸气压 良好的燃烧性能且不爆震:辛烷值、抗爆指数
0.43%,焦炭产率下降0.31%,而液体收率增加1.52%
MIP和FCC处理量对比
图 2 中国石化催化裂化技术统计
图 3 中国石油催化裂化技术统计
图 4 延长集团催化裂化技术统计
图 5 地方炼厂催化裂化技术统计
MIP技术应用情况
MIP技术总液体收率平均增加1.56个百分点, MIP处理 按70Mt/a计算,则可多产出1.092 Mt/a液体产品,仅此 一项年增效益约50亿元以上;
相同液体产量,MIP焦炭产量减少约为0.3548 Mt/a, 相当于减少二氧化碳排放量约为1.30 Mt/a;
汽油质量的改善,从而产生巨大的社会效益;
按镇海炼化考核2005年标定测算,MIP技术每加工吨原 料油效益为210元,则合计经济效益为150亿/年;
MIP装置已运行37套,加工能力为5234万吨/年;15套 装置处于设计和施工中,加工能力约为2700万吨/年, 合计52套,加工能力接近8000万吨/年
3.1 不同工艺所占市场份额 “中石化2010年”
• 常规FCC:中石化23套 • MIP&CGP:中石化32套、中石油9套;延长6套;
中海油2套;蓝星集团:1套 • FDFCC: 中石化4套,洛阳、长岭、济南、荆门 • ARGG: 中石化1套 • DCC: 中石化3套,系统外3套
➢ MIP&CGP加工量占据中石化64%以上,推广迅速 ➢ MIP&CGPvs FCC: 干气产率下降0.78%, 油浆产率下降
异构化汽油
低
低
低
低
高
醚化汽油
FCC汽油特点是硫含量高,烯烃高
我国FCC 汽油特点
➢高烯:40v% ➢高硫:0.02%~0.092% ➢蒸汽压高 ➢氧含量低:<1%
FCC汽油生产:降硫降烯烃、 提高辛烷值
汽油中的烯烃、芳烃和硫含量分布
2. 催化裂化汽油组成影响因素
S,olefine,RON
2.1 原料影响 2.2 催化剂影响 2.3 操作参数影响 2.4 工艺类型影响
剂油比增加,汽油烯烃降低 剂油比增加1 unit,汽油烯烃下降1.5—3.0%
油气分压增加,汽油烯烃&RON降低 油气停留时间增加,汽油烯烃&RON降低 转化率增加,汽油烯烃降低,RON增加 操作参数对汽油硫影响趋势与对烯烃影响相同
2.4 工艺类型影响
项目
硫 苯 芳 烯 辛烷值
常规FCC
基准 - - -
催化裂化汽油组成及其特点
许友好 2013年5月13日燕山石化
石油化工科学研究院
主要内容
1.催化裂化汽油概述
汽油机要求-国标、理想组成、汽油池组成、特点
2. 催化裂化汽油组成影响因素
原料、催化剂、操作参数、工艺
3.不同催化裂化工艺汽油的典型组成
MIP、常规FCC、DCC、FDFCC 市场份额及其汽油典型组成
2.1 原料影响-S
原料S越高,FCC汽油S越多 汽油硫传递系数:常规FCC10%,MIP5%
原料影响-olefin & RON
原料组成影响: 同等转化率下,汽油烯烃: ①石蜡基原料>芳香基原料 ②掺渣原料>不掺渣原料 ③未加氢原料>加氢处理原料
原料碱性氮多,FCC汽油烯烃高 汽油烯烃高,辛烷值高
抗爆性:芳烃>异构烃> 正烯烃&环烷烃> 正烷烃 储存安定性好:碘值、实际胶质、诱导期
产生胶质倾向:链烯烃<环烯烃<二烯烃 无腐蚀作用且污染小
各国均制定严格的排放标准,严格规定汽油的质量、性能
国标GB 17930-1999
项目
抗爆性: 研究法辛烷值(RON) 不小于 抗爆指数(RON+MON)/2 不小于
-
MIP & MIP-CGP
低
较低
DCC & CPP
高 高高 高
FDFCC
低
低
与常规FCC比,MIP&CGP 汽油烯烃含量较低,硫含量低
3.不同催化裂化工艺汽油的典型组成
3.1 不同工艺所占市场份额 3.2 MIP & MIP-CGP汽油 3.3 常规FCC汽油 :ARGG 3.4 DCC&CPP汽油 3.5 FDFCC汽油
严格控制硫苯芳烯,且越严越低
0.005 /0.01 /0.016 2.7 /0.3
70 120 190 205
2
88 65 50
1 35 25
1.2 汽油理想组成
➢低硫低氧少添加 ➢严格控制烯芳苯 ➢多多异构烷烃&环烷烃
清洁燃烧、安全高辛烷值
汽油具体组成与汽油生产工艺有关
1.3 汽油池组成
来源 催化裂化汽油 重整汽油 直馏汽油 烷基化汽油 异构化汽油 醚化汽油
2.2 催化剂影响
催化剂通过氢转移反应降烯烃脱硫 催化剂影响烯烃、硫、RON
稀土高、晶胞大、沸石与基质面积比率大,烯硫低 无稀土CAT:加一定量ZSM-5,可降烯提RON 高稀土CAT:加ZSM-5,烯涨,RON增
2.3 操作参数影响
反应温度升高,汽油烯烃增加&RON升高 温度升高5.6℃,汽油烯烃增1%; 温度升高11.1℃,RON增1 unit
EURO-Ⅲ
90号 93号
97号
90
93
97
85
85
报告
EURO-IV
90号
93号 97号
90
93
97
85
85
报告
铅/ 铁/ 锰含量,g/L
不大于
氧/ 甲醇含量,%(m/m) 不大于
馏程:
10%蒸发温度,℃ 不高于
50%蒸发温度,℃ 不高于
90%蒸发温度,℃ 不高于
终馏点,℃
不高于
残留量,%(v/v) 不大于