_某磁铁矿选矿厂磨选工艺流程考察
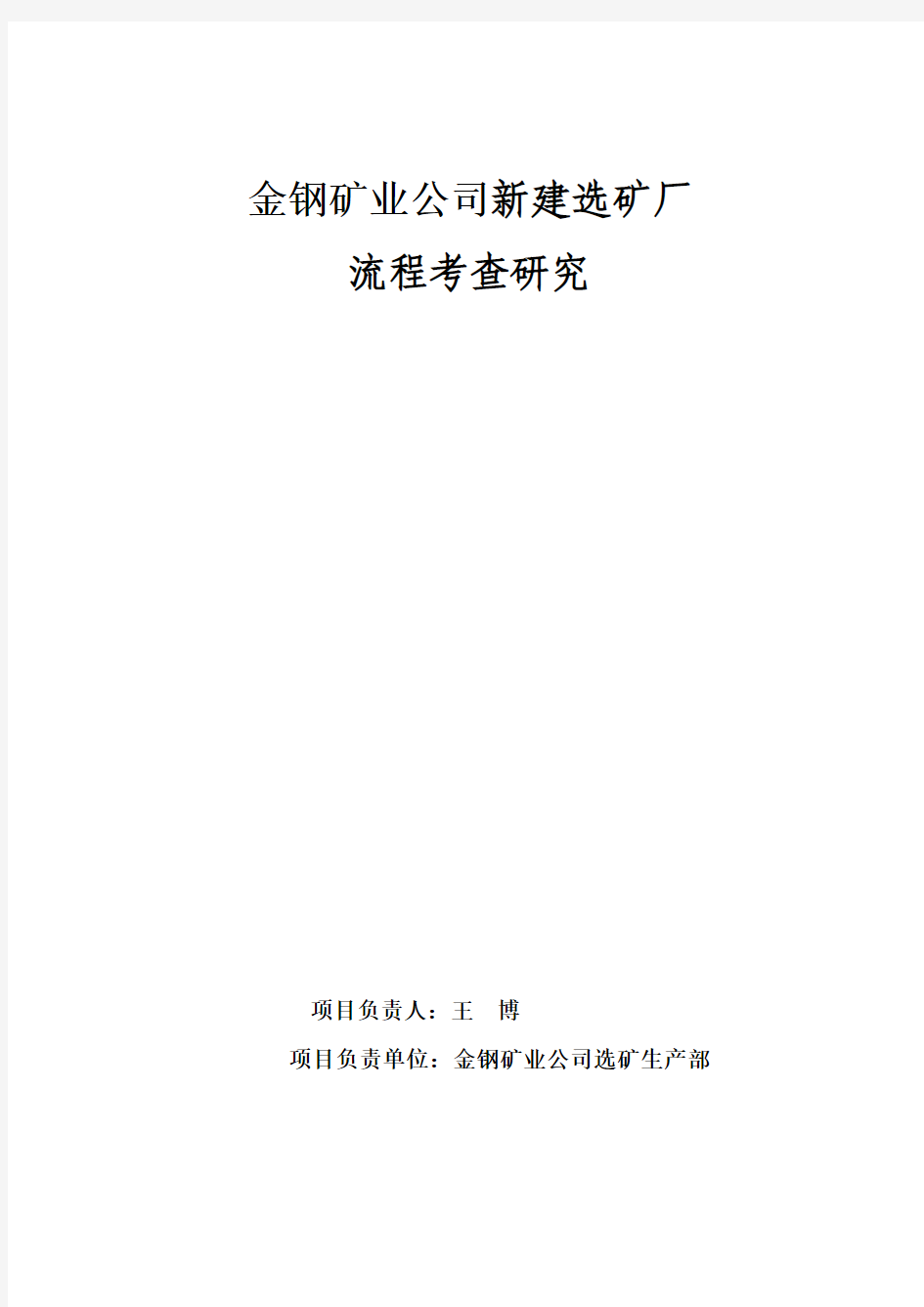

金钢矿业公司新建选矿厂
流程考查研究
项目负责人:王博
项目负责单位:金钢矿业公司选矿生产部
金钢矿业公司选矿厂流程考查研究
为了查明金钢矿业公司选矿厂的现行工艺流程运行情况,为选矿厂的流程改造提供依据,金钢矿业公司选矿厂对现场磨选工艺流程进行考查研究。通过对现行流程的考查及分析,为制定和修改现行流程、技术条件及操作规程提供依据,以便在以后的生产中获得更好的技术经济指标;为总结和修改原设计以及总结生产经验进一步探索新问题提供资料;查明生产中出现异常的原因,寻求平衡生产中不平衡的因素以便改善和提高经济指标。在此基础上采取措施改进生产,从而达到提高选矿厂经济指标的目的。
1样品的采集与制备
1.1样品的采集
本次在选矿厂现场取样包括块矿样和矿浆样两种。取样时间为2013年12月11日,采样周期共计1个白班,每班取样时间为12个小时,自上午11:00—晚上22:00。主厂房磨选作业取样时间间隔为2小时、总共取样5次。
1.1.1磨矿分级磁选系统取样
1.取样点位臵:根据具体情况,可以设臵在管道出口、分级机溢流堰、返砂口、底流口等位臵;个别样品可以在管道垂向开口引出的管道中截取(如旋流器给矿等);
2.为了保证取样样品具有代表性,要求采用化验室专用采样工具(取样勺);
3.采样过程当中,要截取整个矿浆断面,防止矿浆溅漏;
4.每个取样点每次取样的干矿量不少于200g;
5.取样同时,测定每个取样点的矿浆浓度(矿浆浓度由化验室及时测定)。
6.样品编号和收集。按照取样表进行样品的编号和样品名称的标注,同一采样点的不同采样时间的样品首先分别集中,取样完成后混匀作为实验样品。
1.1.2取样点统计
1.一段磨矿分级回路,1系列共4个取样点:入磨粉矿1个、球磨排矿1个、螺旋分级机返砂1个、螺旋分级机溢流1个。
2.Ⅰ段磁选作业,1系列共2个取样点:Ⅰ磁精矿1个、Ⅰ磁尾矿1个。
3.二段磨矿分级回路:1系列共4个取样点:旋流器给矿1个、旋流器溢流1个、旋流器底流(2段球磨给矿)1个、二段球磨排矿1个。
4.Ⅱ、Ⅲ段磁选作业,1系列共4个取样点:Ⅱ段磁选精矿1个、Ⅱ段磁选尾矿1个、Ⅲ段磁选精矿1个、Ⅲ段磁选尾矿1个。
5.精矿过滤1系列2个取样点:过滤铁精粉1个、滤液1个。
6. 综合尾矿1个。
以上一系列磨矿分级磁选系统合计共有17个取样点。
1.2 样品的处理
1.矿浆样品每次取样送至化验室经预先过滤脱水烘干,先做出各样品浓度,然后用带内衬塑料编织袋包装,每个编织袋上注明样品编号及样品名称。
2.入磨粉矿取样每次需标记入磨量。
3.以上所取所有样品交至选矿部化验室。
选矿流程中采样点分布示意图如图1-1所示,采样点说明见表1-1。
Ⅰ系列入磨粉矿
尾矿图1-1金钢矿业公司选矿厂磨选系统采样流程示意图
表1-1金钢矿业公司选矿厂流程考查取样明细表
1.3试验样品的制备
根据项目的研究内容,在对所取的矿浆样进行晾晒、混匀、缩分、筛分及研磨处理,样品的制样流程如图1-2所示:
图1-2 磨矿磁选流程矿浆样品制样流程图
2选矿流程工艺参数的确定
为了查明现行选矿流程的运行状态,对全流程所取试验样品的化学成分、粒度组成、浓度等工艺指标进行了系统的分析检测。
2.1选矿产品的粒度及含铁品位分析
2.1.2 磨矿磁选系统产物的粒度组成及化学成分
磨矿磁选系统各产物的粒度组成及化学成分如表2-1所示。
磨矿分级磁选系统各产物的粒度组成及化学成分特点归纳如下:
1.磨矿分级回路
(1)球磨排矿:1系列球磨排矿中-200目的产率为30%,综合品位为39.91%。从各粒级铁品位变化情况来看,1系列的球磨排矿中,铁在+200目的粒级中明显富集,1系列球磨排矿中该粒级中铁的分布率为72.61%。
(2)螺旋分级机溢流:1系列分级机溢流-200目的含量为68%,-325目的含量为12%,综合品位为31.37%。1系列分级机溢流的品位都远低于分级机返砂的含铁品位,分级机存在明显的反富集现象。从各粒级铁品位变化情况来看,铁在-200目粒级中明显富集,分级机溢流中该粒级的铁分布率为72.61%。
(3)螺旋分级机返砂:分级机返砂中-200目的含量为14%,-325目的含量
为1.44%,综合品位为45.01%。从各粒级铁品位变化情况来看,反映出来的规律一致,铁主要分布在+200目的各粒级中,两个系列分级机返砂中该粒级铁分布率为84.82%。返砂中+100目的粒级中铁品位较低,分级机返砂该粒级的品位为36.59%。而-100目的含铁品位较高,均在50%左右。
2.Ⅰ段磁选作业
(1)Ⅰ磁精矿
1系列Ⅰ磁粗选精矿-200目的含量为70.50%,-325目的含量为13.83%,综合含铁品位为54.33%,较给矿(螺旋分级机溢流)品位提高22.95%。从各粒级铁品位变化情况来看,铁主要分布在-200目以下的各粒级中,其分布率占85.41%,而在+100目粒级中铁的品位较低,仅为17.30%,分布率仅占1.96%。说明粗精矿中的脉石矿物和连生体主要分布在粗粒级中。
(2)Ⅰ磁尾矿
1系列Ⅰ磁粗选尾矿-200目的含量为64.90%,综合含铁品位为9.86%。从各粒级铁品位变化情况来看,随着粒级变细,含铁品位增加,其中-325目的粒级中含铁品位最高,为15.74%,说明Ⅰ磁粗选微细粒级铁流失较严重。
3.旋流器分级作业
(1)旋流器给矿
1系列旋流器给矿:1系列旋流器给矿中-200目的含量为75%,综合品位为60.42%。从各粒级铁品位变化情况来看,在-200目的粒级中含铁品位较高,大于62%,铁主要分布在-200目的细粒级中,该粒级铁分布率为77.97。
(2)旋流器溢流
1系列旋流器溢流:1系列旋流器溢流-200目的含量为78.05%,其中-325目粒级的含量为33.05%,综合品位为54.33%,溢流品位低于旋流器给矿品位(60.42%),更远远低于旋流器底流品位(63.86%)。随着产物的粒级变细,铁品位逐渐升高,溢流中-200目粒级中综合品位达到60.29%,其中-325目粒级铁品位为61.77%。
(3)旋流器底流
1系列旋流器底流:1系列旋流器底流中-200目含量为57.37%,该粒级含量较高,综合品位为63.86%,远远高于旋流器溢流的品位(54.33%)。显然该系
列旋流器底流中细粒级含量高、含铁品位高,说明旋流器的分级效率较低、分级过程中存在明显的反富集现象。从各粒级铁品位变化情况来看,-200目粒级综合含铁品位已达到65.67%,说明在该粒级中的磁铁矿矿物大部分已经发生解离,但合格粒级通过旋流器未能得到有效分离,而是该系列旋流器工况不正常。
4.二段磨矿作业
1系列二段磨矿排矿:1系列二段磨矿产物中-200目的含量为80.04%,粒度相对该系列旋流器底流产物(入磨原料)变细,-200目粒级产率提高约23个百分点,-325目粒级的产率由旋流器底流中的10.70%提高到34.04%。综合含铁品位为63.86%。该系列球磨排矿产物中铁主要分布在-200目以下的粒级中,其铁分布率为81.33%。
5.Ⅱ段磁选作业
(1)Ⅱ磁精矿:Ⅱ磁精矿中-200目的含量为84.57%,综合品位为62.08%;随着各粒级粒度变细,铁品位逐渐升高,-200目以下的粒级综合含铁品位达到65.92%。该产物-325目含量达到41.57%,该粒级铁分布率为44.90%,+200目以上的粒级为16.43%,铁分布率为9.11%。
(2)Ⅱ磁尾矿:Ⅱ磁尾矿-200目的含量为78.07%,综合品位为11.97%。随着尾矿产物粒级变细,铁品位逐渐升高,-325目粒级的含量达到49.59%、含铁品位达到14.86%,说明微细粒级中铁在磁选中流失较多。
6.Ⅲ段磁选作业
(1)Ⅲ磁精矿:Ⅲ磁精矿-200目的含量为84.16%,综合品位为63.63%。精矿中-325目含量为54.16%,该粒级铁品位为68.87%,铁分布率为63.49%,+200目以上的粒级产率为15.84%,铁分布率为8.87%。磁选精矿中,各粒级铁品位随着粒度的变细而增加。
(2)Ⅲ磁尾矿:Ⅲ磁尾矿-200目的含量为78.74%,综合品位为13.08%。尾矿中-325目含量为52.20%,该粒级品位为15.05%,相应铁分布率为59.91%,同样说明Ⅲ段磁选的尾矿中所含的金属铁主要来自一些微细粒的磁铁矿。
7.过滤脱水作业
最终精矿:最终精矿中-200目的含量为83.98%,综合品位为63.94%,品位未能达到合格铁精矿品位要求。最终精矿中-325目粒级的含量为53.98%,该粒
级中的铁品位为68.19%,分布率为57.52%。精矿中各粒级的含铁品位随着粒度的减小而增加。
8.最终尾矿
最终尾矿中-200目的含量为74.00%,铁品位为10.19%。最终尾矿中各粒级的含铁品位随着粒度的变细而增加,其中铁在-325目粒级中的分布率为54.16%。
2.2 磨矿磁选系统样品浓度的测定
1.各取样点测定结果
磨矿磁选系统各取样点不同取样时间矿浆样浓度测定结果如表2-4到2-10所示。
2.磨矿磁选系统各产物浓度测定结果汇总
磨矿磁选系统产物浓度的测定结果如表2-7所示。
从以上各产物(作业)的浓度测定结果来看(表2-7),大部分产物的浓度均存在明显的波动,说明生产过程不够稳定、操作参数的控制不够严格。相对而言,一段磨矿分级系统较为稳定、各段磁选精矿浓度的波动较小,而二段磨矿分级作业的浓度波动较大。问题比较突出的主要是以下几个环节:
(1)一段磨矿分级溢流浓度偏大。一段球磨机排矿和分级机返砂的浓度比较正常,波动却较大,波动范围分别为63~85%、71~80%,而螺旋分级机溢流浓度偏大、波动较小。1系列分级机溢流浓度高为34.83%。说明球磨机给矿和补加水量的控制不够严格,从而导致排矿和返沙分级粒度不稳定,加上球磨机排矿水水量太小,导致分级溢流浓度偏大,分级效果较差。
(2)二段旋流器分级系统浓度波动大。1系列旋流器给矿的浓度为47.14%、波动范围40 ~58%,溢流浓度和底流浓度分别为27.28%和80.06%。给矿浓度波动范围大是造成旋流器工作不稳定的主要原因。
(3)二段三段磁选尾矿浓度普遍偏低。一段磁选尾矿浓度较为合适,而二段磁选尾矿浓度仅为2.51%,三段磁选尾矿浓度仅为1.91%。说明二三段磁选作业中添加水量过大,应注意控制。尾矿浓度过低,必然会对尾矿浓缩脱水造成不利影响,而且大量稀矿浆的泵送能耗也会增加。
3数质量流程和矿浆流程计算
3.1 一段磨选系统
由于1系列的给矿品位和作业指标存在一定差异,根据流程产物的分析结果,进行了计算。1段磨选系列数质量流程和矿浆流程计算结果见图3-1、图3-2。
由图3-1可以看出,1系列给矿品位为31.37%,经过Ⅰ段磨选,Ⅰ段磁选精矿品位为54.33%、回收率为83.77%、尾矿品位为9.86%。总体上取得了良好的分选技术指标。
从一段磨选矿浆流程计算结果(图3-2)来看,1系列球磨排矿加水量偏小,导致分级溢流浓度增高,导致分级效果较差。
另外,从球磨机处理能力来看,球磨新给矿仅为90t/h,与类似矿山相比,处理能力较低,尚有较大潜力。
3.2 再磨磁选系统
再磨磁选系统数质量流程(图3-1)计算结果表明,经过一段磁选精矿经过分级再磨磁选后,最终铁精矿产率为39.37%、品位63.94%、回收率80.25%,铁精矿回收率较好,但精矿品位尚未达到设计要求。存在的主要问题在于:旋流器分级作业溢流产率和品位较低、而旋流器底流产率和品位较高,说明合格粒级未能有效分离,铁矿物存在明显的反富集现象。1系列旋流器溢流平均产率48.38%、平均品位54.33%,而底流平均产率为85.64%、平均品位63.63%。因此,提高旋流器分级作业效率将是流程优化控制的一项重点工作。
从再磨磁选系统矿浆流程计算结果(图3-2)来看,反映出以下几个问题:(1)各段磁选作业加水量偏高,造成一次精矿和各段磁选尾矿浓度偏低,为后续处理造成不利影响。(2)一系列旋流器返回产物较多,造成作业效果不稳定。
铁品位(%);铁回收率(%)
Ⅰ系列入磨粉矿
尾矿
图3-1金钢矿业公司选矿厂磨矿磁选系统数质量流程图
产率(%)
图例:
尾矿图3-2金钢矿业公司选矿厂磨矿磁选系统矿浆流程图
产率(%);浓度(%)
干矿量(t/h);水量(t/h)
4现行流程各作业效率分析
4.1 现行流程分选效果评价
4.1.1 一段磨矿磁选系统
1. 磨矿分级回路的作业效率:根据两个系列的螺旋分级机给矿、螺旋分级机溢流和螺旋分级机返砂的-200目含量,计算1系列螺旋分级机实际的分级效率为67.16%。1系列分级机溢流的品位都远远低于分级机返砂的品位,分级机分级过程中存在磁铁矿的反富集现象。
2.Ⅰ段磁选分选效率:1系列分级机溢流经过Ⅰ段磁选后,磁选精矿的品位由分级机溢流的31.37%提高到54.33%,磁选尾矿品位为9.86%,分选效果良好,1系列1段磁选回收率为8
3.77%。
4.1.2 再磨磁选系统
1. 旋流器分级作业效率:根据旋流器给矿、旋流器底流、旋流器溢流的-200目含量,计算得出1系列旋流器的分级效率为68.10%,旋流器的分级效率较低,导致大量已经单体解离的磁铁矿存在于旋流器底流,旋流器分级过程中存在较严重的磁铁矿反富集现象。旋流器溢流品位为54.33%,而旋流器底流的品位高达63.86%,大部分已解离铁矿物未能进入分级机溢流。因此,旋流器分级作业的优化控制将是流程改造的重要内容。
2. 二段磨矿效率:-200目含量为57.37%的1系列旋流器底流经过二段再磨后,磨矿产物中-200目的含量增加到80.04%,-200目粒级产率提高约23个百分点,磨矿效率较高。从1系列二段磨矿浓度来看,磨矿浓度为80.06%,说明磨矿浓度的提高有利于磨矿效率的提高。因此,应重视二段磨矿浓度(旋流器底流浓度)的控制。
3. Ⅱ段磁选分选效率:1系列旋流器的溢流在矿箱中混合后经过Ⅱ段磁选后,磁选精矿的品位由两系列旋流器溢流的综合品位5
4.33%提高到62.08%,铁回收率为80.92%,尾矿品位11.97%,回收率下降将近3个百分点,说明Ⅱ段磁选有少量的细颗粒磁铁矿流失。
4. Ⅲ段磁选分选效率:经过Ⅲ段磁选,磁选精矿的品位由二段磁选精矿的62.08%提高到63.63%,铁回收率为80.40%,尾矿品位13.08%,Ⅲ段磁选精铁品位提高较少。
5. 精矿脱水:三段磁选精矿经过滤机脱水后,其品位由原来的63.63%变化为63.94%,铁回收率为80.25%,回收率略有降低,说明压滤脱水过程中仍有少量的微细粒磁铁矿流失。矿浆流程计算表明,滤液浓度约为0.97%、滤饼浓度87.15%,应注意提高滤饼浓度,减少滤液中颗粒流失。
总体而言,(1)一段磨矿分级系统的磨矿细度基本满足要求,但磨机处理能力较低、分级机作业参数的控制不够严格。(2)各段磁选作业的分选指标较好,但二三段磁选加水量普遍较大;(3)二段磨矿分级作业效果较差,主要是分级效率低、反富集显著,一段旋流器给矿浓度波动较大。(5)最终精矿品位63.94%、回收率达到80.25%,选矿回收率指标较好,但尚未达到合格铁精矿的品位要求。
4.2流程考查发现的主要问题
1. 二段再磨分级系统
流程考查发现,二段再磨分级系统作业效率低是影响最终分选指标的关键,存在的主要问题包括:(1)二段磨矿浓度波动大;(2)旋流器作业不稳定,给矿压力、给矿量及加水量很不稳定,造成分级效率低、底流浓度不能保证、合格粒级不能有效分离,铁矿物在旋流器底流中的反富集现象严重;(3)旋流器给矿及加水点较多,造成系统波动大。
2. 一段磨矿分级系统
存在的主要问题包括:(1)磨机给矿量较小、给矿量不稳定;(2)分级作业加水量小、分级溢流浓度高,而分级效率较低。
3. 各段磁选作业
各段磁选作业存在的主要问题是二三段磁选加水量偏大,矿浆浓度低。
选矿厂流程考查
选矿厂流程考查 【摘要】:一、流程考查的分类和主要内容;二、流程考查前的准备工作;三、流程考查中原始指标的选定;四、流程考查时常计算的各种指标;五、流程考查;六、流程考查时选别流程的计算;七、流程计算;八、流程考查报告的编写。 选矿厂要定期和不定期的对生产的状况、技术条件、技术指标、设备性能与工作状况、原料的性质、金属流失的去向以及有关的参数做局部及全部的流程调查,该调查称为流程考查。 流程考查的目的是: 1、调查了解全厂各工序、各系统、各循环、各作业、各机组或单机的生产现状和存在的问题,从而对考查的对象进行分析和评价。 2、通过对现行流程的考查及分析、为制定和修改现行流程、技术条件及操作规程提供依据,以便在以后的生产中获得更好的技术经济指标。 3、为总结和修改原设计以及总结生产经验进一步探索新问题提供资料。
4、查明生产中出现异常的原因,寻求平衡生产中不平衡的因素以便改善和提高经济指标。 流程考查是发现问题揭露矛盾的一种手段,在此基础上采取措施改进生产,从而达到提高选矿厂经济指标的目的。 一、流程考查的分类和主要内容 流程考查目的不同,考查的范围和对象也就不同。流程考查一般分为三类: (一)单元流程考查(系统、循环的考查); (二)机组考查(单机、作业的考查); (三)数质量流程(局部、全部)考查。 流程考查的内容大致如下: 1、原矿性质:包括入选原矿的矿物组成、结构、构造、化学组成、粒度组成、含水量、含泥量、矿石中有用矿物和脉石矿物的含量及嵌布特性,矿石的真假比重,摩擦角、安息角、可磨度及硬度等。
2、对生产中各工序、各作业、各机组的技术特性、技术条件、生产中每年产品的数量(矿量、产率、水量、液固比等)和质量(品位、回收率、粒度组成等)作系统的调查。 3、检查某些辅助设备的工作情况,以及对选别过程的影响。 4、计算统计全厂的总回收率,必要的作业回收率,有关产品的粒度组成,金属分布率,嵌布特性,有用矿物和脉石矿物的分布情况,出厂产品的质量情况。 5、检查有用矿物和金属流失的去向,以及某些作业、设备中的富集和积存情况。 6、通过上述考查,对工艺过程和原始数据进行分析、计算、绘制选矿数质量流程图和矿浆流程图,编制三析(筛析、水析、镜析)表、金属平衡表、水量平衡表,绘制有关产品的粒度特性曲线、有关产品的品位-回收率曲线和品位-损失率曲线。 7、按预先要求编写工艺流程考查报告。 二、流程考查前的准备工作
选矿实验流程
选矿试验的要求 选矿试验资料是选矿工艺设计的主要依据。选矿试验成果不仅对选矿设计的工艺流程、设备选型、产品方案、技术经济指标等的合理确定有着直接影响,而且也是选矿厂投产后能否顺利达到设计指标和获得经济效益的基础。因此,为设计提供依据的选矿试验,必须由专门的试验研究单位承担。选矿试验报告应按有关规定审查批准后才能作为设计依据。在选矿试验进行之前,选矿工艺设计者应对矿床资源特征、矿石类型和品级、矿石特征和工艺性质、以及可选性试验等资料充分了解,结合开采方案,向试验单位提出试验要求,在“要求”中,一般不必详述试验单位通常都应做到的内容,而应着重提出需要试验单位解决的特殊内容和主要问题。 一、选矿试验类型的划分 选矿试验按研究的目的可分为可选性试验、工艺流程试验和选矿单项技术试验三种,按试验规模可分为试验室试验、半工业试验和工业试验三种。为便于明确选矿试验要求和叙述的方便,概括上述两种分类,将选矿试验类型划分为可选性试验、试验室小型流程试验、试验室扩大连续试验、半工业试验、工业试验和选矿单项技术试验六种。 (1)可选性试验。一般由地质勘探部门完成。在地质普查、初勘和详勘阶段,应循序渐进地提高和加深可选性试验研究深度。可选性试验着重研究和探索各种类型和品级矿石的性质与可选性差别,基本选矿方法与可能达到的选矿指标,有害杂质剔除的难易,伴生成分综合回收的可能性等。试验研究的内容和深度应能判定被勘探的矿床矿石的利用在技术上是否可行、经济上是否合理,能为制订工业指标和矿床评价提供依据。可选性试验是在试验室装置或小型试验设备上进行的,一般只作矿床评价用。 (2)试验室小型流程试验。试验室小型流程试验是在矿床地质勘探完成之后,可行性研究或初步设计之前进行。它着重对矿石矿物特征和选矿工艺特性、选矿方法、工艺流程结构、选矿指标、工艺条件及产品(包括某些中间产品)等进行试验研究和分析,并应进行两个以上方案的试验对比。试验研究的内容和深度。一般应能满足设计工作中初步制订工艺流程和产品方案、选择主要工艺设备及进行设计方案比较的要求。由于试验室小型流程试验规模小、试料少、灵活性大、入力物力花费较少,因此允许在较大范围内进行广泛的探索,又因它的试料容易混匀,分批操作条件易于控制,因此是各项试验的最基本试验。但是,它是在试验室小型非连续(或局部连续)试验设备上进行的,其模拟程度和试验结果的可靠性虽优于可选性试验,但不及试验室扩大连续试验。 (3)试验室扩大连续试验。试验室扩大连续试验是在小型流程试验完成之后,根据小型流程试验确定的流程,用试验室设备模拟工业生产过程的磨矿、选别乃至脱水作业的连续试验。它着重考察流程动态平衡条件下(包括中矿返回)的选矿指标和工艺条件。各试验研究单位连续试验设备的能力很不一致,一般为 40 一 200kg/h。试验室扩大连续试验比小型流程试验的模拟性较好,可靠性较小型流程试验高些。 (4)半工业试验。半工业试验是在专门建立的半工业试验厂或车间进行的,试验可以是全流程的连续,也可以是局部作业的连续或单机的半工业试验。试验的目的主要是验证试验室试验的工艺流程方案,并取得近似于生产的技术经济指标,为选矿厂设计提供可靠的依据或为进一步做工业试验打下基础。半工业试验所用的设备为小型工业设备,试验厂的规模尚无明确的规定,一般为 1~5t/h。 (5)工业试验。工业试验是在专门建立的工业试验厂或利用生产选矿厂的一个系列甚至全厂进行的局部或全流程的试验,由于其设备、流程、技术条件与生产或今后的设计基本相同,故技术经济指标和技术参数比半工业试验更为可靠。
机械铸造厂废水的处理工艺
2010级毕业生实习报告 学生: 学号: 班级: 学院: 时间:2014年2月24日至3月23日
机械铸造厂废水的处理工艺 一:实习过程简介 市旺源机械铸造厂,于2001年正式成立,公司位于省市解放区瓷路8号,公司资金实力雄厚,生产经营能力强大。加上公司总裁夏胜宝的英明领导,目前已发展成为业一家较具实力的生产型企业。公司主营铸钢件,铸铁件,机加工。我于2014年2月24日至3月23日在该厂进行为期一个月的毕业实习。二:具体实习容 在厂里师傅的带领下了解了铸造厂废水:铸造厂废水是在铸铁融熔时对化铁炉的冷却废水。这种冷却水受污染很小,经对污浊物加以去除并进行冷却处理后,废水即可循环使用。对于铸造车间受灰尘及烧土污染的废水,则常采用凝聚沉淀处理后回用于生产,有时也直接排往堆渣场处置。 1铸造废水回用 铸造水力清砂工艺是利用高压水产生的强烈射流,将铸件表面残存的型砂冲洗干净。其废水中主要含有制造砂型所使用的各种原料,其中SS最高可达几千mg/L,pH值偏高,而COD一般在40—50mg/L之间。 冲洗铸件后所产生的废水先落入地面的砂坑,渗过废砂层后进入地下贮水池中,再用水泵将其抽入废水箱后逐渐排放。 水力清砂工艺对用水水质的要,不损害工艺设备和设施,不影响铸件的质量,对喷枪、高压泵、阀门、管道等设备不造成堵塞。参考国外有关回用水水质的某些规定,并与厂方商定,将清砂回用水水质标准定为,浊度10度,COD20mg/L,其它指标以对生产工艺不产生不良影响为准。 铸造污水处理工艺流程高效污水处理工艺在废水处理污水处理应用效果好稳定,铸造污水处理工艺流程高效污水处理工艺经专家认定是废水处理污水处理领域的高新技术,铸造污水处理工艺流程图高效污水处理净化系统具有污水处理工程投资少、占地面积小、污水处理废水处理反应迅速、运行成本低、广
选矿方法(基本原理、工艺流程)
1、重介质选矿法: (1)方法是基于矿石中不同的矿粒间存在着密度差,(或粒度差),籍助流体动力和各种机械力作用,造成适宜的松散分层和分离条件,使不同物料得到分离。 重介质选矿分选原理 根据阿基米德定理,小于重介质密度的颗粒将在介质中上浮,大于重介质密度的颗粒在介质中下沉。 (2)工艺流程 矿石的重选流程是由一系列连续的作业组成。作业的性质可分成准备作业、选别作业、产品处理作业三个部分。(1) 准备作业,包括a:为使有用矿物单体解离而进行的破碎与磨矿;b:多胶性的或含黏土多的矿石进行洗矿和脱泥;c:采用筛分或水力分级方法对入选矿石按粒度分级。矿石分级后分别入选,有利于选择操作条件,提高分选效率。2) 选别作业,是矿石的分选的主体环节。选别流程有简有繁,简单的由单元作业组成,如重介质分选。(3) 产品处理作业,主要指精矿脱水、尾矿输送和堆存。 2、跳汰选矿法 (1)原理:跳汰选矿是在垂直交变介质流的作用下,使矿粒群松散,然后按密度差分层:轻的矿物在上层,叫轻产物;重的在下层,叫重产物,从而达到分选的目的。介质的密度在一定范围内增大,矿粒间的密度差越大,则分选效率越高。 实现跳汰过程的设备叫跳汰机。被选物料给入跳汰机内落到筛板上,便形成一个密集的物料展,这个物料层,称为床层。在给料的同时,从跳汰机下部周期性的给入上下交变的水流,垂直变速水流透过筛孔进入床层,物料就是在这种水流中经受跳汰的分选过程。 (2)工艺过程 当水流上升时,床层被冲起,呈现松散及悬浮的状态。此时,床层中的矿粒,按其自
身的特性(密度、粒度和形状),彼此作相对运动,开始进行分层。在水流已停止上升,但还没有转为下降水流之前,由于惯性力的作用,矿粒仍在运动,床层继续松散、分层。水流转为下降,床层逐渐紧密,但分层仍在继续。当全部矿粒落回筛面,它们彼此之间已丧失相对运动的可能,则分层作用基本停止。此时,只有那些密度较高、粒度很细的矿粒,穿过床层中大块物料的间隙,仍在向下运动,这种行为可看成是分层现象的继续。下降水流结束,床层完全紧密,分层便暂告终止。水流每完成一次周期性变化所用的时间称为跳汰周期。在一个跳汰周期内,床层经历了从紧密到松散分层再紧密的过程,颗粒受到了分选作用。只有经过多个跳汰周期之后,分层才逐趋完善。最后,高密度矿粒集中在床层下部,低密度矿粒则聚集在上层。然后,从跳汰机分别排放出来,从而获得了两种密度不同,即质量不同的产物。 3、浮选 (1)原理:浮选是根据矿物表面物理化学性质的差异,而分选矿物的一种选矿方法。 (2)浮选流程包括磨矿,分级,调浆及浮选的粗选、精选、扫选作业。有一段磨浮流程;分段磨矿-浮选的阶段磨浮流程;精矿或中矿再磨再选流程。浮选产出粗精矿的作业称粗选;粗精矿再选作业称精选;尾矿再选作业称扫选。回收矿石中多种有用矿物时,不同矿物先后浮选的流程称优先浮选或选择浮选;先将有用矿物全部浮出后再行分离的流程,称混合-分离浮选。工业生产时必须针对矿石的性质和对产品的要求,采用不同的药方和浮选流程。 浮选的原则流程即浮选的骨干流程或流程的主干结构。它一般包括段数、循环和矿物的浮选顺序等内容。 3)浮选机:浮选机类型:机械搅拌式浮选机、充气式浮选机、混合式浮选机或充气搅拌式浮选机、气体析出式浮选机。
选矿工艺流程修订稿
选矿工艺流程 WEIHUA system office room 【WEIHUA 16H-WEIHUA WEIHUA8Q8-
工艺流程试验是为选矿厂设计(或现有选矿厂的技术改造)提供依据,在选矿厂初步设计(或拟定现场技术改造方案)前进行。一般选进行试验室试验,然后在试验室试验的基础上,根据情况决定是否进行半工业或工业试验。 选矿工艺流程试试验内容和必要的资料收集,一般由试验研究单位负责制订,有条件的可由试验、设计和生产部门三结合洽商确定。 一、收集资料的一般内容如下,但具体工程需根据条件的不同,区别对待 (一)了解上级机关下达任务的目地和委托单位提出的要求,例如:选矿厂规模、服务年限;主要有用成分和伴生成综合利用问题;试验阶段的划分;要求试验完成日期;选矿厂处理单一矿床的矿石还是几个矿床、不同类型的矿石;用户对精矿化学成分的特殊要求以及对精矿等级和粒度的要求;建厂地区的水源,选矿药剂,焙烧用燃料等的供应情况和性能分析资料等。 (二)了解有关地质资料,例如:矿床类型;地质储量;矿体产状;矿石类型;品位特征;嵌布特性;围岩脉石等变化情况;远景评价;采样设计等。 (三)了解采矿设计方面的资料,例如:采矿的开拓方案和采矿方法;不同类型矿石的混采、分采;围岩混入率和矿石采出品位;开采设计矿区的矿石类型配比和平均品位;开采设计5-10年内逐年开采的矿石类型配比和平均品位等。 (四)了解选矿方面资料,例如:选矿设计对试验的特殊要求。国内外类似矿石的试验研究和生产实践情况,可能应用的选进技术等。 二、选矿工艺流程试验主要内容有 (一)矿石性质研究 是选择选矿方案和确定选厂设计方案时与类似矿石生产实践作对比分析的依据,其中某些数据是选厂具体设计中必不可少的原始数据。 矿石性质研究包括:光谱定性和半定量,化学全分析,岩矿鉴定,物相分析,粒度分析,磁性分析,重液分析,试金分析,磨矿细度,矿石可磨度,及各种物理性能(比重、比磁化系数、导电率、水分、真比重和假比重、堆积角和摩擦角、硬度、粘度等)。 (二)选矿方法、流程结构,选矿指标和工艺条件 直接关系到选矿厂的设计方案和具体组成,是选厂设计的主要原始资料,必须慎重考虑,要求选矿方法、流程结构合理,选矿指标可靠。
选矿厂全流程考察
选矿厂全流程考察 一、流程考察的分类和主要内容;二、流程考察前的准备工作;三、流程考察中原始指标的选定;四、流程考察市场计算的各种该指标; 五、流程考察;六、流程考察时选别流程的计算;七、流程的计算; 八、流程考察报告的编写。 选矿厂要定期和不定期的对生产的状况、技术条件、技术指标、设备性能与工作状况、原料的性质、金属流失的去向以及有关的参数做局部及全部的流程调查,该调查称为流程考查。 流程考查的目的是: 1、调查了解全厂各工序、各系统、各循环、各作业、各机组或单机的生产现状和存在的问题,从而对考查的对象进行分析和评价。 2、通过对现行流程的考查及分析、为制定和修改现行流程、技术条件及操作规程提供依据,以便在以后的生产中获得更好的技术经济指标。 3、为总结和修改原设计以及总结生产经验进一步探索新问题提供资料。 4、查明生产中出现异常的原因,寻求平衡生产中不平衡的因素以便改善和提高经济指标。 流程考查是发现问题揭露矛盾的一种手段,在此基础上采取措施改进生产,从而达到提高选矿厂经济指标的目的。 一、流程考查的分类和主要内容
流程考查目的不同,考查的范围和对象也就不同。流程考查一般分为三类: (一)单元流程考查(系统、循环的考查); (二)机组考查(单机、作业的考查); (三)数质量流程(局部、全部)考查。 流程考查的内容大致如下: 1、原矿性质:包括入选原矿的矿物组成、结构、构造、化学组成、粒度组成、含水量、含泥量、矿石中有用矿物和脉石矿物的含量及嵌布特性,矿石的真假比重,摩擦角、安息角、可磨度及硬度等。 2、对生产中各工序、各作业、各机组的技术特性、技术条件、生产中每年产品的数量(矿量、产率、水量、液固比等)和质量(品位、回收率、粒度组成等)作系统的调查。 3、检查某些辅助设备的工作情况,以及对选别过程的影响。 4、计算统计全厂的总回收率,必要的作业回收率,有关产品的粒度组成,金属分布率,嵌布特性,有用矿物和脉石矿物的分布情况,出厂产品的质量情况。 5、检查有用矿物和金属流失的去向,以及某些作业、设备中的富集和积存情况。 6、通过上述考查,对工艺过程和原始数据进行分析、计算、绘制选矿数质量流程图和矿浆流程图,编制三析(筛析、水析、镜析)表、金属平衡表、水量平衡表,绘制有关产品的粒度特性曲线、有关产品的品位-回收率曲线和品位-损失率曲线。
进行铸造厂技术改造或设计的基本步骤
进行铸造厂技术改造或设计的基本步骤 清华大学吴浚郊 当前世界上先进国家铸造技术发展的四个目标 ?保护环境,减少以至消除污染 ?提高铸件质量的可靠性,生产优质近终形铸件 ?降低生产成本,增加经济效益 ?缩短交货期 为了使我国的铸造行业在新的世纪能在国际激烈的竞争中立于不败之地,我国的铸造厂必须抓紧技术革新,提高技术水平,积极采用机械化、自动化生产,大力引入计算机等高新技术,千方百计的提高铸件质量及其附加值。 铸造行业的基本任务 ?在符合环保要求的前提下,用尽可能低的成本生产出更多的近终形铸件。 造型及制芯工部的 设计 造型及制芯工艺过程是设计任何一个新铸造厂或对已有铸造厂进行技术改造的核心,其工程设计费用和设备费用通常要占总投资的50~60%,每个铸造厂都必须根据其生产纲领和生产要求来设计。 造型及制芯工部设计的基本步骤 生产工艺过程的选择取决于铸造厂所拟生产的铸件品种。应当弄清楚:浇注何种合金、铸件品种数、其尺寸和质量、预期生产的数量和吨位。 通常铸件产值的75~80%是由模板库中不到25%的模板所生产的,对于这些典型模板,要进行详细的设计计算。 虽然对于所有被预测的要求都必须考虑适宜的设备能力。此时,应对生产纲领中特殊情况进行评估,并考虑作出取消某些模板的关键性决定,这些模板不仅引起生产纲领的不平衡,而且通常也是没有效益的。 为进行造型工部的布置,对于每一典型模板,需要了解以下信息: ?铸件单重
?浇注重量 ?砂箱尺寸及每箱件数 ?砂型光洁程度要求,诸如手工修型,喷涂料、烘干等 ?下芯及下芯撑时间 为进行造型工部的布置,对于每一典型模板,需要了解以下信息(续): ?浇注时间 ?型内最少冷却时间 ?废品率 ?每小时多少箱 ?生产铸件的造型系统 ?每小时或每班换模板数 为进行制芯工部的布置,对于每种砂芯或每个典型芯盒,需要了解以下信息:?芯盒类别(金属的、木制的、射芯用、震实用) ?砂芯单重及每盒芯数 ?芯砂类别(壳芯、冷芯盒、热芯盒、CO2等) ?生产率——每小时几盒 ?砂芯底板或烘芯器 为进行制芯工部的布置,对于每种砂芯或每个典型芯盒,需要了解以下信息(续):?烘干时间及温度(若需烘干的话) ?砂芯修整生产率——每小时多少砂芯 ?上涂料、二次烘干时间及温度 ?废芯率 ?制芯机类型、规格 ?每班更换芯盒数
铸造工艺流程介绍
铸造生产的工艺流程 铸造生产是一个复杂的多工序组合的工艺过程,它包括以下主要工序: 1)生产工艺准备,根据要生产的零件图、生产批量和交货期限,制定生产工艺方案和工艺文件,绘制铸造工艺图; 2)生产准备,包括准备熔化用材料、造型制芯用材料和模样、芯盒、砂箱等工艺装备; 3)造型与制芯; 4)熔化与浇注; 5)落砂清理与铸件检验等主要工序。 成形原理 铸造生产是将金属加热熔化,使其具有流动性,然后浇入到具有一定形状的铸型型腔中,在重力或外力(压力、离心力、电磁力等)的作用下充满型腔,冷却并凝固成铸件(或零件)的一种金属成形方法。 图1 铸造成形过程
铸件一般作为毛坯经切削加工成为零件。但也有许多铸件无需切削加工就能满足零件的设计精度和表面粗糙度要求,直接作为零件使用。 型砂的性能及组成 1、型砂的性能 型砂(含芯砂)的主要性能要求有强度、透气性、耐火度、退让性、流动性、紧实率和溃散性等。2、型砂的组成 型砂由原砂、粘接剂和附加物组成。铸造用原砂要求含泥量少、颗粒均匀、形状为圆形和多角形的海砂、河砂或山砂等。铸造用粘接剂有粘土(普通粘土和膨润土)、水玻璃砂、树脂、合脂油和植物油等,分别称为粘土砂,水玻璃砂、树脂砂、合脂油砂和植物油砂等。为了进一步提高型(芯)砂的某些性能,往往要在型(芯)砂中加入一些附加物,如煤份、锯末、纸浆等。型砂结构,如图2所示。 图2 型砂结构示意图 工艺特点 铸造是生产零件毛坯的主要方法之一,尤其对于有些脆性金属或合金材料(如各种铸铁件、有色合金铸件等)的零件毛坯,铸造几乎是唯一的加工方法。与其它加工方法相比,铸造工艺具有以下特点:1)铸件可以不受金属材料、尺寸大小和重量的限制。铸件材料可以是各种铸铁、铸钢、铝合金、铜合金、镁合金、钛合金、锌合金和各种特殊合金材料;铸件可以小至几克,大到数百吨;铸件壁厚可以从0.5毫米到1米左右;铸件长度可以从几毫米到十几米。 2)铸造可以生产各种形状复杂的毛坯,特别适用于生产具有复杂内腔的零件毛坯,如各种箱体、缸体、叶片、叶轮等。 3)铸件的形状和大小可以与零件很接近,既节约金属材料,又省切削加工工时。 4)铸件一般使用的原材料来源广、铸件成本低。 5)铸造工艺灵活,生产率高,既可以手工生产,也可以机械化生产。 铸件的手工造型 手工造型的主要方法 砂型铸造分为手工造型(制芯)和机器造型(制芯)。手工造型是指造型和制芯的主要工作均由手工完成;机器造型是指主要的造型工作,包括填砂、紧实、起模、合箱等由造型机完成。泊头铸造工量具友介绍手工造型的主要方法: 手工造型因其操作灵活、适应性强,工艺装备简单,无需造型设备等特点,被广泛应用于单件小批量生产。但手工造型生产率低,劳动强度较大。手工造型的方法很多,常用的有以下几种: 1.整模造型 对于形状简单,端部为平面且又是最大截面的铸件应采用整模造型。整模造型操作简便,造型时整个模样全部置于一个砂箱内,不会出现错箱缺陷。整模造型适用于形状简单、最大截面在端部的铸件,如齿轮坯、轴承座、罩、壳等(图2)。
选矿厂流程考查的步骤是什么
选矿厂流程考查的步骤是什么? 流程考查可按如下步骤进行: (1)绘制详细的流程图。到现场了解情况,根据了解的情况绘制出所要考查的详细流程图。 (2)绘制流程考查取样计划图。根据详细流程图、流程考查的要求、流程计算的需要以及结合现场各作业点取样方便、安全可靠等情况绘制流程考查取样计划图。其中各取样点试样的最小质量应按公式Q=kd2确定。 (3)绘制流程考查人员分工表和所需工具计划表。根据取样流程图,结合现场情况和取样的难易情况分工。对人员的分工和所需要的工具要做出周密的计划,应考虑取样人员的活动范围不能太大,作业及矿石性质相似。总之,应该取样方便,使所取的矿样准确。 (4)确定取样时间和取样次数。取样时间一般4~8h,每隔10~20min取一次,如果试样质量要求大,可以每隔5min取样一次,质量分数小的矿浆取样次数也可以适当增加。 (5)确定测定方法和分析方法。例如,质量分数测定采用干法还是湿法,筛析需要分成多少级,哪些级需要进行化学分析,分析哪些元素等。 (6)按流程考查计划进行取样、测定、计算、分析和研究。 1.如何确定选别流程原始指标数目? 在确定取样点时,应按计算流程所必需的充分的原始指标数目而定。必需的原始数据数目可按下式求出: N=(n-a)C 式中N——计算流程所必须的原始指标数目(不包括已知的原矿指标); n——计算流程时所涉及的全部选别产品数目; a——计算流程时所涉及的全部选别作业数目; C——每一作业可列出的平衡方程式数目(单金属C=2,双金属C=3,三金属C=4)。 在确定取样点时,应注意以下几点: (1)选定的取样点应该是生产中最稳定的和影响最大的而且易于测定的产物。例如浮选这种得出两个产物的选别作业,应该选取精矿和尾矿的化验样。对于能够产出三种产物的重选作业,除了取精矿、中矿、尾矿的化验样外,还应该取精矿的质量样。 (2)在某些情况下,还可以多增加几个辅助取样点,以防某一取样点有问题时作为补充取样点。 (3)另外应根据生产特点和可能遇到的技术问题来确定取样点。 2.流程考查中应注意哪些事项? 流程考查中应注意如下事项: (1)注意设备的操作条件是否正常,测定应在设备正常运转时进行,考查过程中应详细记录设备运转及其他条件的变化情况。 (2)取样时注意切勿使矿浆溢出取样盒或取样勺。各样品不能随便倒出澄清的水。取样工具不能混用。所取试样应妥善保管,不得混入杂物。 (3)取样前认真核对取样点号码与标签是否相符。 (4)各项原始记录必须誊写清楚。 (5)筛析和水析样烘到含水5%左右就要缩分,不得过分干燥以免碎裂、改变粒度组成。
选矿工艺流程介绍
选矿工艺流程介绍(附流程图) [导读]:选矿是冶炼前的准备工作,从矿山开采下来矿石以后,首先需要将含铁、铜、铝、锰等金属元素高的矿石甄选出来,为下一步的冶炼活动做准备。选矿一般分为破碎、磨矿、选别三部分。其中,破碎又分为:粗破、中破和细破;选别依方式不同也可分为:磁选、重选、浮选等。本专题将详细向大家讲述选矿的一些具体工艺常识,以及主要选矿设备的大致工作原理,主要控制要点等知识。由于时间的仓促和编辑水平有限,专题中难免出现遗漏或错误的地方,欢迎大家补充指正。 选矿的目的:提高矿石品位。 选矿方法: ◆重力选矿法。根据矿物密度的不同,在选矿介质中具有不同的沉降速度而进行选矿。 ◆磁力选矿法。磁力选矿法是利用矿物的磁性差别,在不均匀的磁场中,磁性矿物被磁选机的磁极吸引,而非磁性矿物则被磁极排斥,从而达到选别的目的。 ◆浮游选矿法。浮游选矿法是利用矿物表面不同的亲水性,选择性地将疏水性强的矿物用泡沫浮到矿浆表面,而亲水性矿物则留在矿浆中,从而实现不同矿物彼此分离。 选矿后的产品:精矿、中矿和尾矿。 ◆精矿是指选矿后得到的含有用矿物含量较高的产品。 ◆中矿为选矿过程中间产品,需进一步选矿处理。 ◆尾矿是经选矿后留下的废弃物。
选矿的流程: (一)矿石破碎 我国选矿厂一般采用粗破、中破和细破三段破碎流程破碎铁矿石。粗破多用1.2m或1.5m旋回式破碎机,中破使用2.1m或2.2m标准型圆锥式破碎机,细破采用2.1m或2.2m短头型圆锥式破碎机。通过粗破的矿石,其块度不大于1m,然后经过中、细破碎,筛分成矿石粒度小于12mm的最终产品送磨矿槽。 (二)磨矿工艺 我国铁矿磨矿工艺,大多数采用两段磨矿流程,中小型选矿厂多采用一段磨矿流程。由于采用细筛再磨新工艺,近年来一些选矿厂已由两段磨矿改为三段磨矿。采用的磨矿设备一般比较小,最大球磨机 3.6m×6m,最大棒磨机 3.2m×4.5m,最大自磨机5.5m×1.8m,砾磨机2.7m×3.6m。 磨矿后的分级基本上使用的是螺旋分级机。为了提高效率,部分选矿厂用水力旋流器取代二次螺旋分级机。 (三)选别技术 1.磁铁矿选矿 主要用来选别低品位的“鞍山式”磁铁矿。由于矿石磁性强、好磨好选,国内磁选厂均采用阶段磨矿和多阶段磨矿流程,对于粗粒嵌布的磁铁矿采用前者(一段磨矿),细粒、微细粒嵌布的磁铁矿采用后者(二段或三段磨矿)。我国自己研制的系列化的永磁化,使磁选机实现了永磁化。70年代以后,由于在全
选矿厂各生产车间考核细则(2021)
When the lives of employees or national property are endangered, production activities are stopped to rectify and eliminate dangerous factors. (安全管理) 单位:___________________ 姓名:___________________ 日期:___________________ 选矿厂各生产车间考核细则 (2021)
选矿厂各生产车间考核细则(2021)导语:生产有了安全保障,才能持续、稳定发展。生产活动中事故层出不穷,生产势必陷于混乱、甚至瘫痪状态。当生产与安全发生矛盾、危及职工生命或国家财产时,生产活动停下来整治、消除危险因素以后,生产形势会变得更好。"安全第一" 的提法,决非把安全摆到生产之上;忽视安全自然是一种错误。 为了细化选矿厂生产管理,进一步提高公司生产效益,按照公司2008年管理计划要求,根据选矿厂各车间实际情况,特制定本考核细则。 各车间考核项目 1、碎矿车间 1.1、生产任务 1.1.1、生产任务以当月公司计划任务为准,完成当月任务时,不奖不罚。 1.1.2、若因人为因素和设备保养不善而造成欠产时,每欠产100吨,扣罚0.1分。 1.2、碎矿粒度标准: 1.2.1、碎矿车间必须按选矿工艺规定,保证矿石粒度Φ13mm占90%,15mm占10%,否则每次扣罚0.1分。 1.2.2、碎矿车间若因料块过粗而影响磨矿时,每次考核扣罚2分。
2、磨浮车间 2.1生产成本可控部分(可控材料总额为元/吨)名称 标准 单位/吨 金额 备注 (1)黄药 400克 - (2)硫酸铜 650克 - (3)硫酸锌 200克 - (4)苯胺 2克
(工艺流程)消失模铸造技术简介及工艺流程
消失模铸造工艺简述 消失模铸造是把涂有耐火材料涂层的泡沫塑料模样放入砂箱,模样四周用干砂充填,采用微震加负压紧实,在没有芯子的情况下浇注液态金属,在浇铸和凝固过程中继续保持一定的负压,使泡沫塑料气化继而被金属取代形成铸件的一种新型铸造工艺方法。 一.消失模铸造的工艺流程如下: 1)预发泡 模型生产是消失模铸造工艺的第一道工序,复杂铸件如汽缸盖,需要数块泡沫模型分别制作,然后再胶合成一个整体模型。每个分块模型都需要一套模具进行生产,另外在胶合操作中还可能需要一套胎具,用于保持各分块的准确定位,模型的成型工艺分为两步,第一步是将聚苯乙烯珠粒(EPS)预发到适当密度,一般通过蒸汽快速加热来进行,此阶段称为预发泡。 2)模型成型 经过预发泡的珠粒要先进行稳定化处理,然后再送到成型机的料斗中,通过加料孔进行加料,模具型腔充满预发的珠粒后,开始通入蒸汽,使珠粒软化、膨胀,挤满所有空隙并且粘合成一体,这样就完成了泡沫模型的制造过程,此阶段称为蒸压成型。 成型后,在模具的水冷腔内通过大流量水流对模型进行冷却,然后打开模具取出模型,此时模型温度较高而强度较低,所以在脱模和储存期间必须谨慎操作,防止变形及损坏。 3)模型簇组合 模型在使用之前,必须存放适当时间使其熟化稳定,典型的模型存放周期多达30天,而对于用设计独特的模具所成型的模型仅需存放2个小时,模型熟化稳定后,可对分块模型进行胶粘结合。大批量生产的铸件其分块模型胶合必须使用热熔胶在自动胶合机上进行,才能保证粘合精度。中小批量生产的铸件可采用冷粘胶手工粘合,胶合面接缝处应密封牢固,以减少产生铸造缺陷的可能性 4)模型簇浸涂、干燥 为了每箱浇注可生产更多的铸件,有时将许多模型胶接成簇,把模型簇浸入耐火涂料中,然后在大约30~60C(86-140F)的空气循环烘炉中干燥2~3个小时,干燥之后,将模型簇放入砂箱,填入干砂振动紧实,必须使所有模型簇内部孔腔和外围的干砂都得到紧实和支撑。 5)浇注 模型簇在砂箱内通过干砂振动充填坚实后,抽真空形成负压加强紧实度,铸型就可浇注,熔融金属浇入铸型后,模型气化被金属所取代形成铸件。在消失模铸造工艺中,浇注速度比传统空型铸造更为关键。如果浇注过程中断,砂型就可能塌陷造成废品。因此为减少每次浇注的差别,最好使用自动浇注机。 6)落砂清理
选矿方法(基本原理、工艺流程)
1、重介质选矿法:(1)方法是基于矿石中不同的矿粒间存在着密度差,(或粒度差),籍助流体动力和各种机械力作用,造成适宜的松散分层和分离条件,使不同物料得到分离。重介质选矿分选原理根据阿基米德定理,小于重介质密度的颗粒将在介质中上浮,大于重介质密度的颗粒在介质中下沉。(2)工艺流程矿石的重选流程是由一系列连续的作业组成。作业的性质可分成准备作业、选别作业、产品处理作业三个部分。 (1) 准备作业,包括a:为使有用矿物单体解离而进行的破碎与磨矿;b:多胶性的或含黏土多的矿石进行洗矿和脱泥;c:采用筛分或水力分级方法对入选矿石按粒度分级。矿石分级后分别入选,有利于选择操作条件,提高分选效率。2) 选别作业,是矿石的分选的主体环节。选别流程有简有繁,简单的由单元作业组成,如重介质分选。 (3) 产品处理作业,主要指精矿脱水、尾矿输送和堆存。 2、跳汰选矿法(1)原理:跳汰选矿是在垂直交变介质流的作用下,使矿粒群松散,然后按密度差分层:轻的矿物在上层,叫轻产物;重的在下层,叫重产物,从而达到分选的目的。介质的密度在一定范围内增大,矿粒间的密度差越大,则分选效率越高。实现跳汰过程的设备叫跳汰机。被选物料给入跳汰机内落到筛板上,便形成一个密集的物料展,这个物料层,称为床层。在给料的同时,从跳汰机下部周期性的给入上下交变的水流,垂直变速水流透过筛孔进入床层,物料就是在这种水流中经受跳汰的分选过程。 (2)工艺过程当水流上升时,床层被冲起,呈现松散及悬浮的状态。此时,床层中的矿粒,按其自身的特性(密度、粒度和形状),彼此作相对运动,开始进行分层。在水流已停止上升,但还没有转为下降水流之前,由于惯性力的作用,矿粒仍在运动,床层继续松散、分层。水流转为下降,床层逐渐紧密,但分层仍在继续。当全部矿粒落回筛面,它们彼此之间已丧失相对运动的可能,则分层作用基本停止。此时,只有那些密度较高、粒度很细的矿粒,穿过床层中大块物料的间隙,仍在向下运动,这种行为可看成是分层现象的继续。下降水流结束,床层完全紧密,分层便暂告终止。水流每完成一次周期性变化所用的时间称为跳汰周期。在一个跳汰周期内,床层经历了从紧密到松散分层再紧密的过程,颗粒受到了分选作用。只有经过多个跳汰周期之后,分层才逐趋完善。最后,高密度矿粒集中在床层下部,低密度矿粒则聚集在上层。然后,从跳汰机分别排放出来,从而获得了两种密度不同,即质量不同的产物。 3、浮选(1)原理:浮选是根据矿物表面物理化学性质的差异,而分选矿物的一种选矿方法。(2)浮选流程包括磨矿,分级,调浆及浮选的粗选、精选、扫选作业。有一段磨浮流程;分段磨矿-浮选的阶段磨浮流程;精矿或中矿再磨再选流程。浮选产出粗精矿的作业称粗选;粗精矿再选作业称精选;尾矿再选作业称扫选。回收矿石中多种有用矿物时,不同矿物先后浮选的流程称优先浮选或选择浮选;先将有用矿物全部浮出后再行分离的流程,称混合-分离浮选。工业生产时必须针对矿石的性质和对产品的要求,采用不同的药方和浮选流程。 浮选的原则流程即浮选的骨干流程或流程的主干结构。它一般包括段数、循环和矿物的浮选顺序等内容。 3)浮选机: 浮选机类型:机械搅拌式浮选机、充气式浮选机、混合式浮选机或充资料试卷电气设备,在安装过程中电气系统接线等情况,然后根据规
锑矿选矿工艺流程分析
锑矿选矿工艺流程分析 流程介绍: 提取方法: 锑矿的提取方法除应根据矿石类型、矿物组成、矿物构造和嵌布特性等物理、化学性质作为基本条件来选择外,还应考虑有价组分含量和适应锑冶金技术的要求以及最终经济效益等因素。锑矿石的选矿方法,有手选、重选、重介质选、浮选等。 手选: 锑矿石手选工艺是利用锑矿石中含锑矿物与脉石在颜色、光泽、形状上的差异进行的。该方法虽然原始,且劳动强度较大,但用于锑矿石选矿仍具有特殊意义:因为锑矿物常呈粗大单体结晶或块状集合体晶体产出,手选常能得到品位较高的块锑精矿,适合于锑冶金厂竖式焙烧炉的技术要求;手选能降低选矿生产成本和能耗,因此它在我国广泛使用。据资料统计:我国现生产的18个主要锑选矿厂中,有手选作业的有15座,占83.3%,其中单一硫化锑矿选厂4座,硫化—氧化混合锑矿选厂4座,含锑复杂多金属矿选厂7座。手选选出的块状锑精矿,只需含锑7%以上就可进入竖式焙烧炉直接挥发焙烧,以制取三氧化二锑。手选出含锑高于45%的块状硫化锑精矿,通过熔析法可制取纯净的三硫化二锑(俗称生锑),用于生产。手选除拣出高品位块状锑精矿外,也可以直接丢弃大量废石,以提高入选原矿品位。适合手选的矿石粒度,大都在28~150毫米间。大多数锑选厂采用宽级别手选,只有个别选厂如锡矿山北选厂采用分级成窄级别手选。由于原矿往往含泥,因此洗矿作业常是手选前不可缺少的预备作业。入选原矿经过洗矿然后手选,比不经洗矿直接手选效果要好。 重选: 锑矿石的重选工艺对于大多数锑矿石选厂均适用,因为锑矿物属于密度大、粒度粗的矿物,易于用重选方法与脉石分离。其中:辉锑矿密度为 4.62克/厘米3,而脉石密度介于2.6~2.65克/厘米3之间,其等沉(降)比为2.19 ~2.26,属易选矿石;黄锑华密度为5.2克/厘米3、红锑矿密度为7.5克/厘米3、锑华为5.57克/厘米3,它们与脉石的等沉(降)比分别为2.55~2.63,3.93~4.06和2.76~2.86,这三种锑矿石属于按密度分选的极易选矿石。只有水锑钙,石密度3.14克/厘米3,与脉石等沉(降)比值仅1.29,属于按密度分选较难选矿石,但它在锑矿石中并不算主要成分,不影响重选的使用。总之,不论单一硫化锑矿石或硫化( 氧化混合锑矿石,均具有较好的重选条件。且重选费用低廉,又能在较粗粒度范围内、分选出大量合格粗粒精矿,并丢弃大量脉石,因此,重选仍是当今锑选矿工作者乐于采用的选矿方法。有时,它即使不能直接选出合格锑精矿,然而作为锑浮选作业的预选作业,也常被人接受,特别是浮选在现阶段处理氧化锑矿石的困难很多的情况下,因而重选成了氧化锑矿石的主要选矿方法。 浮选: 浮选是锑矿物最主要的提取方法。硫化锑矿物属易浮矿物,大多采用浮选方法提高矿石晶位。其中:辉锑矿常先用铅盐作活化剂,也有用铜盐或铅盐铜盐兼用的,然后用捕收剂浮选。常用的捕收剂为丁黄药或页岩油与乙硫氮混合物,起泡剂为松醇油或2号油;氧化锑矿则属难浮矿石。
精密铸造项目计划书
中温蜡精密铸造项目计划书 第一章:项目总论 一、项目概要 1、项目名称:精密铸造项目 2、项目建设性质:新建 3、项目承办单位名称:未定 4、总投资资本:万元 5、隶属国民经济类别:铸造行业 6、项目建设地址: 7、项目用地规模:2000-5000平方米 8、项目投资概算:该项目预计总投资额为500万元,其中固定资产投资200万元,流动资金300万元 9、项目达纲年限:2年(不含项目建设期) 10、项目达纲年预计总产出规模:3000万元(含税) 第二章:项目背景和发展概况 1、精密铸造项目背景 随着时代的发展和进步,铸造业也是发生了翻天覆地的变化。据《中国铸造机械行业市场前瞻与投资规划分析报告》显示,在“十二五”期间中国铸件产量增速趋于稳定,步入稳定发展阶段,这就显示了我国的铸造业在近年来发展较为良好,呈现增长趋势。同时,在我国加快推进“中国制造2025”和“互联网+”的计
划的进程中,我国的铸造业充分借助了互联网的发展优势和大数据时代的信息优势,加快促进铸造业的转型升级,彻底的改造传统行业。 2、精密铸造项目发展展望 我国是铸造大国。据不完全统计,我国有2万多家铸造厂(车间),从业人员达120 万人,年产量达1200万吨。铸造行业是一个劳动力、资源相对密集的产业,我国生产资源丰富,生产能力过剩,劳动力成本具有优势。铸造生产正在从发达国家向发展中国家扩展和转移。我国加入WTO给铸造业带来了前所未有的发展机遇。现代机器的生产,对铸件精度和整体质量提出了越来越严格的要求,这为能实现精密铸造生产的熔模铸造和实型铸造的大力发展提供了契机。目前,我国熔模铸造存在两类工艺水平的企业。一类是采用中、高温模料,硅溶胶或硅酸乙酯型壳工艺,生产航空、燃气轮叶片等和不锈钢商业精铸件的工厂;二类是采用低温模料、水玻璃型壳工艺,主要生产碳钢件的工厂。一类工厂数量少,工艺水平高;二类工厂数量多,生产质量低。现代熔模铸造正朝着“精密、大型、薄壁”方向发展,我国熔模铸造应顺应时代发展潮流。第一类工厂应紧跟国际先进技术,改进管理,与国际标准接轨,积极参与国际竞争,更多地走向国际市场。生产应不再停留于主要生产高尔夫球头、五金件、马具和管阀类精度要求较低的产品上,而应扩大精度要求较高的高附加值的机械零件产品。加大对第二类工厂的改造,采用高质量模料,粘结
各种系列的选矿工艺流程介绍
各种系列的选矿工艺流程介绍 选矿行业分为许多分支,研究各种系列的选矿工艺流程对于区分他们的应用具有现实意义。 磁铁矿选矿工艺流程 磁铁矿是一种氧化铁的矿石,主要成份为Fe3O4,是Fe2O3和 FeO 的复合物,呈黑灰色,比重大约 5.15左右,含Fe72.4%,O 27.6%,具有磁性。 开采的矿石先由颚式破碎机进行初步破碎,在破碎至合理细度后经由提升机、振动给料机均匀送入球磨机,由球磨机对矿石进行粉碎、研磨。经过球磨机研磨的矿石细料进入下一道工序:分级。螺旋分级机借助固体颗粒的比重不同而在液体中沉淀的速度不同的原理,对矿石混合物进行洗净、分级。矿物颗粒在被送入浮选机,根据不同的矿物特性加入不同的药物,使得所要的矿物质与其他物质分离开。 赤铁矿选矿设备工艺流程: 赤铁矿的主要成分为Fe2O3,单晶体常呈菱面体和板状,集合体形态多样。有金属光泽至半金属光泽,硬度为5.5~6.0,密度为5.5~5.3 g·cm-3。呈铁黑色、金属光泽的片状赤铁矿集合体称为镜铁矿;呈灰色、金属光泽的鳞片状赤铁矿集合体称为云母赤铁矿;呈红褐色、光泽暗淡的称为赭石;呈肾状的赤铁矿称为肾状赤铁矿。赤铁矿在自然界中分布极广,是重要的炼铁原料,也可用作红色颜料。我国著名产地有辽宁鞍山、甘肃镜铁山、湖北大冶、湖南宁乡和河北宣化。针对我国赤铁矿的特点,部分可采用洗矿后用重选富集,此方法投资、
用电负荷较小,05年以来新建的中小型选场很多。对难选的矿石,一般先采用磁化焙烧、磁选、浮选。对原有选场品位较低的,我公司可代为配置精矿再磨反浮选脱硅设备,使铁精粉的品位提高达标。可提供用户选场供新用户考察,代为用户设计、配套、调试生产。铁闪锌矿的浮选流程 对于含铁闪锌矿的多金属硫化矿的浮选,一般有3种流程结构可 供选择,即混合浮选、优先浮选和等可浮流程。 混合浮选包括全混合浮选和部分混合浮选。全混合浮选是先全浮选铜、铅、锌、硫,然后再分选为单一的精矿。部分混合浮选是先铜铅锌混合浮选,再选硫;或者优先选铜铅,再锌硫混合浮选,随后再 分离浮选,其选别指标往往取决于锌与硫分选的优劣程度。 优先浮选即首先浮选铜、铅,再选锌,最后选硫的依次浮选流程。从浮选工艺的观点看,优先浮选较混合浮选更为有利。优先浮选时,磨矿后,表面新鲜的黄铁矿可得到有效的抑制。倘若是混合浮选,锌矿物和黄铁矿表面均吸附有捕收剂和活化剂,在锌硫分离浮选时,若要很好地抑制黄铁矿,就必须除去其表面的捕收剂,这比使表面新鲜的黄铁矿受到抑制更加困难。所以,优先浮选比混合浮选更有利于锌和硫化铁矿物的分选。在很多时候,铁闪锌矿浮选的实质,也就是铁 闪锌矿与黄铁矿或者磁黄铁矿的分离问题。 但在实际生产中,须根据具体的矿石性质决定采取哪种流程。分细粒级的锌矿物根本无法回收而损失到尾矿中;加大捕收剂用量强拉,又使得一部分可浮性极强的黄铁矿上浮,在锌回路中造成黄铁矿
选矿实验报告
选矿试验报告的内容 选矿试验报告是选矿试验成果的总结和记录。试验报告应该数据齐全可靠、问题分析周密、结论符合实际、文字和图表清晰明确、内容能满足设计的要求。试验室试验报告的内容 应比较详细。半工业试验及工业试验一般都是在试验室试验或前一种试验的基础上进行的, 其试验报告的内容应结合前面所做的基础试验编写,但着重反映本次试验的情况。 选矿工艺流程试验报告的主要内容通常有: (1)前言。包括试验任务的来源、目的和要求、试验确定的工艺和达到的结果。 (2)矿样的采集制备与代表性的评价。 (3)原矿石的工艺矿物学研究。包括矿石中的主要金属矿物与脉石矿物的成分和百分含量;研究矿石的结构与构造,根据结构、构造确定矿石的自然类型及工艺类型;矿物粒度统 计分析、有用矿物解离度分析;研究各矿物嵌布状态、颗粒形态与其它矿物的嵌连关系等。 (4)选矿试验。包括探索试验、工艺方案的选择对比、药剂种类与用量条件试验、矿浆 调整条件试验、开路与闭路流程试验。 (5)精矿产品(包括某些中间产品)的分析检查结果。 (6)尾矿产品的分析结果。 (7)技术经济分析。 (8)结论:试验结果的评述、推荐意见、存在问题和建议。 (9)有关附件。篇二:选矿试验报告 选矿试验报告 ** 研究院 2 0** 年 *月 一前言 受**公司委托对某铜铅锌硫化矿进行选矿试验研究,以确定处理该矿较合理的选矿工艺 流程和药剂制度,为原有铅锌选矿厂增建回收铜系列提供技改参考依据。 1.1试验内容 要求进行较系统的工艺流程和药剂制度试验,包括药剂种类及药剂用量条件试验。并进 行“优先浮铜”和“铜铅混浮再分离”两大工艺流程的对比试验,确定处理该矿较合理的工 艺流程和选矿指标。 1.2试验研究结果 该矿原矿品位:铜**%,铅**%,锌**%。选矿试验采用优先浮选工艺流程,在磨矿细度 -0.074mm占**%的条件下,使用**捕收剂优先浮铜,低碱(ph=*)以下用**浮铅、**浮锌, 试验获得的指标:铜精矿产率**%、铜品位**%、铜回收率**%;铅精矿产率**%、铅品位**%、铅回收率**%;锌精矿产率**%、锌品位**%、锌回收率**%,试验指标理想。 选矿废水经检测,全面达到国标gb8979—1996二类企业排放标准。该铜铅锌矿的浮选采 用本试验推荐的药剂制度,不会发生废水超标的问题。 二试样的采集和加工 试样由委托方采集并送至我院,试样重约**kg。为制备试验矿 样,对送来的矿样进行了加工。加工流程如图2.1所示。 图2.1 试样加工流程图 三试样性质研究 3.1试样化学分析 试样多元素化学分析结果见表3.1。 表3.1 试样多元素化学分析结果 成分含量(%)