卧式连续退火炉工艺设备与控制问题探讨
浅析连续退火炉的温度控制

三 、结 语
对 于燃 烧控 制 ,实 际应 用 中 ,存在 调节 时问相 对较 长 , 生产 过程 由于 阀 门开度 与流量存 在 非线 性 ,使 常规 燃烧控 制 技术 难 以进行 有效 的控 制 。因此 ,我们 将进一 步研 究高 水平
!
! ! 里
堡 星 堡 : ≥
浅 析 连 续 退 火 炉 的温 度控 制
◆王
摘要 :带钢加热过程是一个具有大惯性滞后、多变量的复杂工况系统,而且连续退火炉处理的带 钢 品种规格 多,带钢速 度 变化频繁 ,采 用常规 的控制 方 法无 法 实现控 制 目标 。本 文就 我厂镀 锌线 退火
炉温度控 制进行 简要说 明。
琦
关键 词 :退 火炉 ;温度控 制 ;调节
一
、
退火炉 工艺技术概况
一
该 回路 控制设 备保持 过程变 量 ( P V ) 严格接 近来 自监视 系
统 的设 定点 ( S P ) 。 回路 的输 出 ( OU T ) 是 调节 阀 的需 要位 置 。 旦S P>P V, 阀打开 ;反之 , 若S P < P V,则 阀关 闭。
无扰 切换 。
性 能 指标 。带 钢连 续 退火 炉 的出 现 , 克 服 了过 去 罩式 退火 炉 生产 效率 偏 低 、热均 匀性 较 差等 不足 , 目前 已被 广 泛地 应用 于带 钢热 处理 工艺 。带钢 连续 退火 炉从炉 型上 主要 分 为卧式
和立 式两 大类 ,而 相对 于两种 不 同的炉 型 ,采 用 的热处 理工
段为例 对其温 度控制 进行说 明 。
出的命令 ( 启动 ,停止 ,复位,等等 ) 。每个烧嘴装有火焰
连续退火炉温度控制系统探析
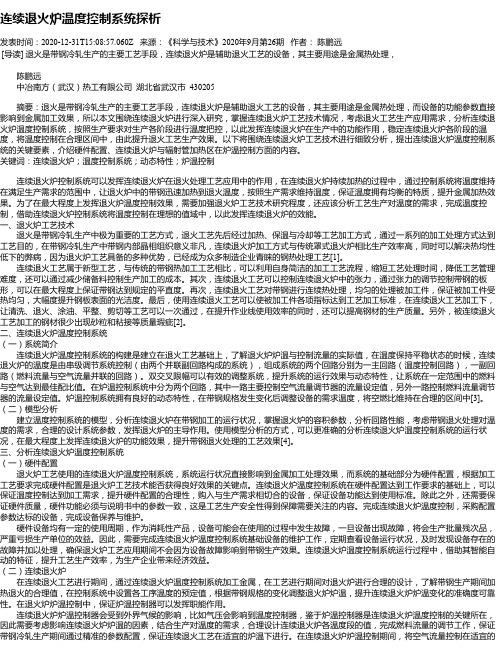
连续退火炉温度控制系统探析发表时间:2020-12-31T15:08:57.060Z 来源:《科学与技术》2020年9月第26期作者:陈鹏远[导读] 退火是带钢冷轧生产的主要工艺手段,连续退火炉是辅助退火工艺的设备,其主要用途是金属热处理,陈鹏远中冶南方(武汉)热工有限公司湖北省武汉市 430205摘要:退火是带钢冷轧生产的主要工艺手段,连续退火炉是辅助退火工艺的设备,其主要用途是金属热处理,而设备的功能参数直接影响到金属加工效果,所以本文围绕连续退火炉进行深入研究,掌握连续退火炉工艺技术情况,考虑退火工艺生产应用需求,分析连续退火炉温度控制系统,按照生产要求对生产各阶段进行温度把控,以此发挥连续退火炉在生产中的功能作用,稳定连续退火炉各阶段的温度,将温度控制在合理区间中,由此提升退火工艺生产效果。
以下将围绕连续退火炉工艺技术进行细致分析,提出连续退火炉温度控制系统的关键要素,介绍硬件配置、连续退火炉与辐射管加热区在炉温控制方面的内容。
关键词:连续退火炉;温度控制系统;动态特性;炉温控制连续退火炉控制系统可以发挥连续退火炉在退火处理工艺应用中的作用,在连续退火炉持续加热的过程中,通过控制系统将温度维持在满足生产需求的范围中,让退火炉中的带钢迅速加热到退火温度,按照生产需求维持温度,保证温度拥有均衡的特质,提升金属加热效果。
为了在最大程度上发挥退火炉温度控制效果,需要加强退火炉工艺技术研究程度,还应该分析工艺生产对温度的需求,完成温度控制,借助连续退火炉控制系统将温度控制在理想的值域中,以此发挥连续退火炉的效能。
一、退火炉工艺技术退火是带钢冷轧生产中极为重要的工艺方式,退火工艺先后经过加热、保温与冷却等工艺加工方式,通过一系列的加工处理方式达到工艺目的,在带钢冷轧生产中带钢内部晶相组织意义非凡,连续退火炉加工方式与传统罩式退火炉相比生产效率高,同时可以解决热均性低下的弊病,因为退火炉工艺具备的多种优势,已经成为众多制造企业青睐的钢热处理工艺[1]。
论连续退火炉节能减排降耗的控制措施
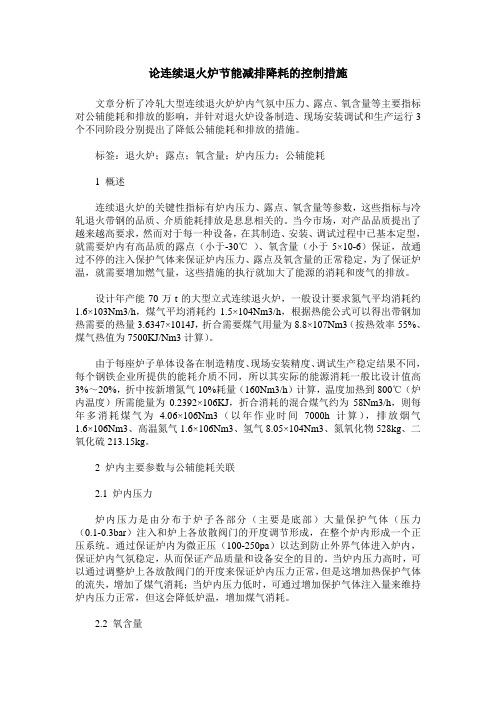
论连续退火炉节能减排降耗的控制措施文章分析了冷轧大型连续退火炉炉内气氛中压力、露点、氧含量等主要指标对公辅能耗和排放的影响,并针对退火炉设备制造、现场安装调试和生产运行3个不同阶段分别提出了降低公辅能耗和排放的措施。
标签:退火炉;露点;氧含量;炉内压力;公辅能耗1 概述连续退火炉的关键性指标有炉内压力、露点、氧含量等参数,这些指标与冷轧退火带钢的品质、介质能耗排放是息息相关的。
当今市场,对产品品质提出了越来越高要求,然而对于每一种设备,在其制造、安装、调试过程中已基本定型,就需要炉内有高品质的露点(小于-30℃)、氧含量(小于5×10-6)保证,故通过不停的注入保护气体来保证炉内压力、露点及氧含量的正常稳定,为了保证炉温,就需要增加燃气量,这些措施的执行就加大了能源的消耗和废气的排放。
设计年产能70万t的大型立式连续退火炉,一般设计要求氮气平均消耗约1.6×103Nm3/h,煤气平均消耗约1.5×104Nm3/h,根据热能公式可以得出带钢加热需要的热量3.6347×1014J,折合需要煤气用量为8.8×107Nm3(按热效率55%、煤气热值为7500KJ/Nm3计算)。
由于每座炉子单体设备在制造精度、现场安装精度、调试生产稳定结果不同,每个钢铁企业所提供的能耗介质不同,所以其实际的能源消耗一般比设计值高3%~20%,折中按新增氮气10%耗量(160Nm3/h)计算,温度加热到800℃(炉内温度)所需能量为0.2392×106KJ,折合消耗的混合煤气约为58Nm3/h,则每年多消耗煤气为 4.06×106Nm3(以年作业时间7000h计算),排放烟气1.6×106Nm3、高温氮气1.6×106Nm3、氢气8.05×104Nm3、氮氧化物528kg、二氧化硫213.15kg。
2 炉内主要参数与公辅能耗关联2.1 炉内压力炉内压力是由分布于炉子各部分(主要是底部)大量保护气体(压力(0.1-0.3bar)注入和炉上各放散阀门的开度调节形成,在整个炉内形成一个正压系统。
连续退火炉温度控制系统的研究
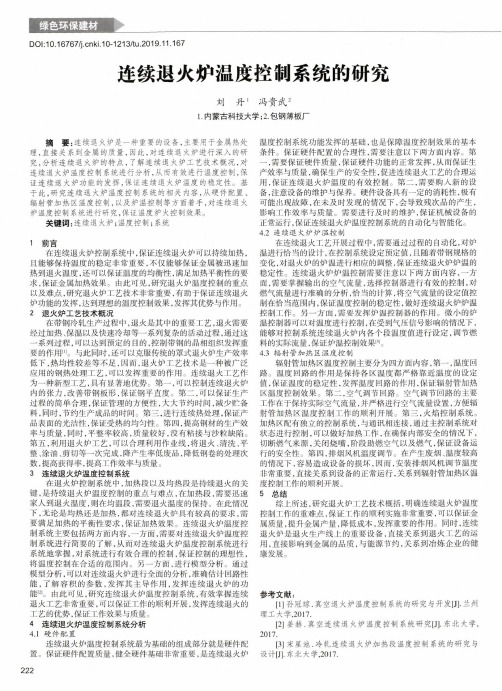
D0l:10.16767/ki.10-1213/tu.2019.11.167连续退火炉温度控制系统的研究刘丹]冯贵武2I.内蒙古科技大学;2.包钢薄板厂摘要:连续退火炉是一种重要的设备,主要用于金属热处理,直接关系到金属的质量,因此,对连续退火炉进行深入的研究,分析连续退火炉的特点,了解连续退火炉工艺技术概况,对连续退火炉温度控制系统进行分析,从而有效进行温度控制,保证连续退火炉功能的发挥,保证连续退火炉温度的稳定性。
基于此,研究连续退火炉温度控制系统的相关内容,从硬件配置、辐射管加热区温度控制,以及炉温控制等方面着手,对连续退火炉温度控制系统进行研究,保证温度炉火控制效果。
关键词:连续退火炉;温度控制;系统1前言在连续退火炉控制系统中,保证连续退火炉可以持续加热,且能够保持温度的稳定非常重要,不仅能够保证金属被迅速加热到退火温度,还可以保证温度的均衡性,满足加热平衡性的要求,保证金属加热效果。
由此可见,研究退火炉温度控制的重点以及难点,研究退火炉工艺技术非常重要,有助于保证连续退火炉功能的发挥,达到理想的温度控制效果,发挥其优势与作用。
2退火炉工艺技术概况在带钢冷轧生产过程中,退火是其中的重要工艺,退火需要经过加热、保温以及快速冷却等一系列复杂的活动过程,通过这一系列过程,可以达到预定的目的,控制带钢的晶相组织发挥重要的作用与此同时,还可以克服传统的罩式退火炉生产效率低下,热均性较差等不足,因而,退火炉工艺技术是一种被广泛应用的钢热处理工艺,可以发挥重要的作用。
连续退火工艺作为一种新型工艺,具有显著地优势。
第一,可以控制连续退火炉内的张力,改善带钢板形,保证钢平直度。
第二,可以保证生产过程的简单合理,保证管理的方便性,大大节约时间,减少贮备料,同时,节约生产成品的时间。
第三,进行连续热处理,保证产品表面的光洁性,保证受热的均匀性。
第四,提高钢材的生产效率与质量,同时,平整率较高,质量较好,没有粘接与沙粒缺陷。
卧式退火炉炉内张力控制研究

卧式退火炉炉内张力控制研究发布时间:2023-02-20T07:27:42.275Z 来源:《新型城镇化》2022年24期作者:武俊[导读] 随着国内冷轧工艺与电气控制技术、信息技术的发展,高效率的卧式退火炉已经被广泛应用到实际生产中,逐渐替代了罩式退火机组。
中铜华中铜业有限公司湖北省黄石市 435005摘要:卧式退火炉炉内张力极易受到温度与炉辊表面摩擦力的影响,针对此问题,本文以某铜加工企业为例,说明卧式退火炉炉内张力控制过程中所存在的问题,并结合实际情况提出针对性优化策略,希望能够为相关技术人员拓展炉内张力控制提供新思路。
关键词:卧式;退火炉;炉内张力;影响因素;优化策略前言随着国内冷轧工艺与电气控制技术、信息技术的发展,高效率的卧式退火炉已经被广泛应用到实际生产中,逐渐替代了罩式退火机组。
而炉内张力便是卧式退火炉稳定通板的关键因素,合适的张力能够保障铜带高速稳定运行,帮助铜带获得良好的成型。
而且炉内张力还能对带铜形成一定纠偏作用,始终将其维持在中心线位置。
因此,加强炉内张力控制是解决炉内异常现象的主要途径,张力越稳定,控制精度越高,生产过程中所产生的波动便越小,通板速度便越快。
1.案例概况该铜加工企业所采取的退火炉机组总长超过200m,高度约为20m。
机组整体可分为三个部分,分别为入口、炉内以及出口段。
入口段相关设备会完成铜卷的焊接与清洗,出口段设备则具有卷曲、平整等功能。
两者之间为炉内段,主要功能为高温退火,此部分也是连续退火机组的核心。
该退火机组的产量为35万吨/年,最大重量在25t以下,带铜厚度为0.5mm,宽度在800-1030mm之间,铜卷内径为508mm,外径为900-1800mm。
入口段的最大速度可达到1000m/min,出口速度可达到100m/min,穿带速度最高为60m/min。
下文便对该机组及炉内张力控制中存在的问题进行说明。
2.卧式退火炉炉内张力控制中存在的问题该退火机组在生产过程中出现了较为严重的带铜跑偏现象,经过初步分析,可将铜带跑偏现象归结为温度与炉辊表面摩擦力异常两方面原因,具体如下。
连续退火炉的施工要点

浅谈连续退火炉的施工要点摘要:冷轧立式连续退火炉的工艺比较复杂,施工过程中需要特别注意的问题较多。
本文从立式连续退火炉施工过程中的工艺钢结构、炉壳、辐射管及炉辊设备安装和炉体气密性试验等四个方面,浅要分析了连续退火炉施工过程中的要点。
关键词:退火炉;炉体;炉壳;施工要点连续退火机组主要用于轧后带钢的再结晶退火,以消除冷加工硬化,产品主要用于建筑、家电、汽车等行业。
我国第一条连续退火机组是宝钢在1989年从新日铁引入的2030mmcapl线。
连续退火机组工艺线上的退火炉分为立式炉和卧式炉两种。
相比于结构简单的卧式炉,立式炉的结构复杂得多,施工难度更大,其施工要点也就更值得研究总结。
连续退火机组立式炉的设备一般由炉体设备、炉内设备、炉外设备三部分组成。
从整体来说,立式连续退火炉设备安装的施工要点主要体现在炉子工艺钢结构、炉壳、辐射管、炉辊和炉子气密性试验上。
笔者就宝钢1750mmcal为例对这几个方面的施工要点进行分析与探讨。
从工艺上来说,退火一般分为9段:分别为喷气预热段、辐射管加热段、均热段、缓冷段、闪冷段、过时效段1、过时效段2、最终冷却段及水淬塔段。
生产时连续退火炉段工艺速度可达420m/min。
一、炉子工艺钢结构的施工要点因连续退火炉的工艺特点,炉子工艺钢结构及其平台的安装与炉壳安装、风机、热交换器、管道施工等必须穿插进行,一层结构一层设备,整个退火炉的安装期间呈现高空立体交叉作业状态。
工艺钢结构的安装要分别从入口和出口向炉中安装,这样可以把安装过程中的误差在炉中消除,能够更好地保证安装精度。
为了减少高空作业和确保施工安全,一般把炉体两侧的工艺钢结构柱子及梁预拼装成“井”字形框架。
再进行整体吊装作业。
吊装作业主要利用厂房内的桥式起重机进行,由于主厂房内桥式起重机数量有限,退火炉施工又为多点作业,行车使用频繁,需另配置数台汽车吊配合钢结构拼装作业。
作为整个退火炉工艺钢结构安装的基础,钢结构下段立柱及横梁的各项安装精度都应严格按设计要求和规范来进行,然后进行地脚螺栓的一次灌浆,待强度达到后进行立柱的精找和下部横梁的连接,使底层结构形成刚性框架,最后再进行柱、梁的找正找平。
连续式燃气退火炉设备改进
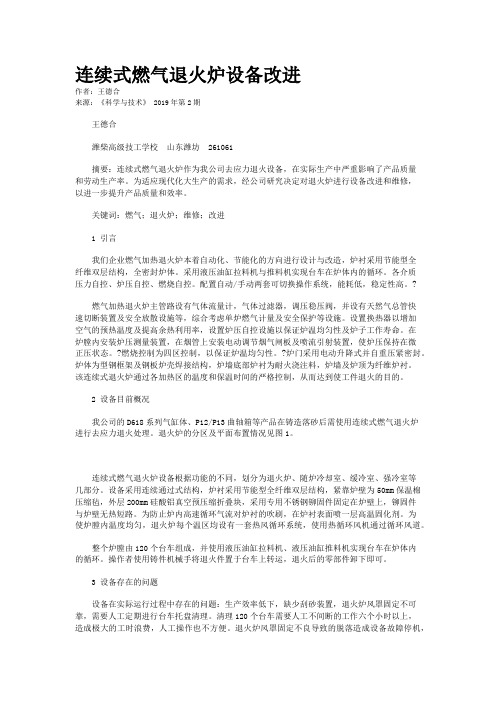
连续式燃气退火炉设备改进作者:王德合来源:《科学与技术》 2019年第2期王德合潍柴高级技工学校山东潍坊 261061摘要:连续式燃气退火炉作为我公司去应力退火设备,在实际生产中严重影响了产品质量和劳动生产率。
为适应现代化大生产的需求,经公司研究决定对退火炉进行设备改进和维修,以进一步提升产品质量和效率。
关键词:燃气;退火炉;维修;改进1 引言我们企业燃气加热退火炉本着自动化、节能化的方向进行设计与改造,炉衬采用节能型全纤维双层结构,全密封炉体。
采用液压油缸拉料机与推料机实现台车在炉体内的循环。
各介质压力自控、炉压自控、燃烧自控。
配置自动/手动两套可切换操作系统,能耗低,稳定性高。
?燃气加热退火炉主管路设有气体流量计,气体过滤器,调压稳压阀,并设有天然气总管快速切断装置及安全放散设施等,综合考虑单炉燃气计量及安全保护等设施。
设置换热器以增加空气的预热温度及提高余热利用率,设置炉压自控设施以保证炉温均匀性及炉子工作寿命。
在炉膛内安装炉压测量装置,在烟管上安装电动调节烟气闸板及喷流引射装置,使炉压保持在微正压状态。
?燃烧控制为四区控制,以保证炉温均匀性。
?炉门采用电动升降式并自重压紧密封。
炉体为型钢框架及钢板炉壳焊接结构,炉墙底部炉衬为耐火浇注料,炉墙及炉顶为纤维炉衬。
该连续式退火炉通过各加热区的温度和保温时间的严格控制,从而达到使工件退火的目的。
2 设备目前概况我公司的D618系列气缸体、P12/P13曲轴箱等产品在铸造落砂后需使用连续式燃气退火炉进行去应力退火处理。
退火炉的分区及平面布置情况见图1。
连续式燃气退火炉设备根据功能的不同,划分为退火炉、随炉冷却室、缓冷室、强冷室等几部分。
设备采用连续通过式结构,炉衬采用节能型全纤维双层结构,紧靠炉壁为50mm保温棉压缩毡,外层200mm硅酸铝真空预压缩折叠块,采用专用不锈钢铆固件固定在炉壁上,铆固件与炉壁无热短路。
为防止炉内高速循环气流对炉衬的吹刷,在炉衬表面喷一层高温固化剂。
连续式退火炉的原理浅析
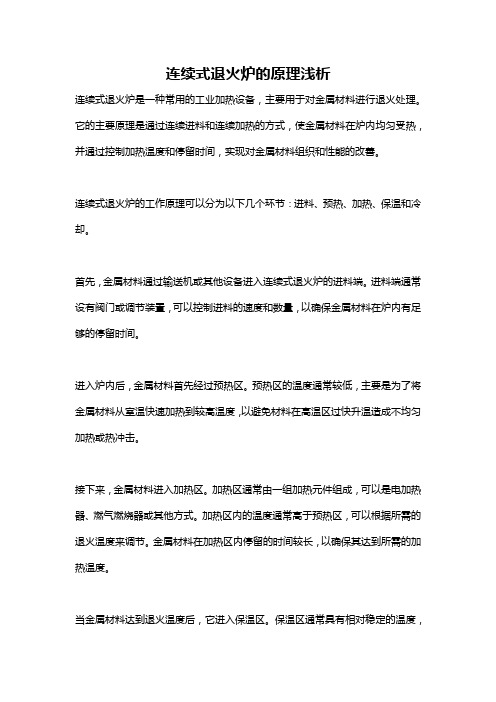
连续式退火炉的原理浅析连续式退火炉是一种常用的工业加热设备,主要用于对金属材料进行退火处理。
它的主要原理是通过连续进料和连续加热的方式,使金属材料在炉内均匀受热,并通过控制加热温度和停留时间,实现对金属材料组织和性能的改善。
连续式退火炉的工作原理可以分为以下几个环节:进料、预热、加热、保温和冷却。
首先,金属材料通过输送机或其他设备进入连续式退火炉的进料端。
进料端通常设有阀门或调节装置,可以控制进料的速度和数量,以确保金属材料在炉内有足够的停留时间。
进入炉内后,金属材料首先经过预热区。
预热区的温度通常较低,主要是为了将金属材料从室温快速加热到较高温度,以避免材料在高温区过快升温造成不均匀加热或热冲击。
接下来,金属材料进入加热区。
加热区通常由一组加热元件组成,可以是电加热器、燃气燃烧器或其他方式。
加热区内的温度通常高于预热区,可以根据所需的退火温度来调节。
金属材料在加热区内停留的时间较长,以确保其达到所需的加热温度。
当金属材料达到退火温度后,它进入保温区。
保温区通常具有相对稳定的温度,以保持金属材料在一定的温度范围内持续保温。
保温的时间和温度取决于具体的材料和要求,以确保材料的组织和性能得到良好的改善。
最后,经过保温后,金属材料进入冷却区。
冷却区可以采用不同的方式进行冷却,如风冷、水冷、盐浴冷却等。
冷却的方式会根据材料的要求进行选择,以控制退火后的材料组织和性能。
连续式退火炉的设计和操作需要考虑以下几个因素:1. 温度控制:退火温度是影响材料组织和性能的重要因素,炉内的温度应能够准确控制,并且温度均匀性也要能够得到保证。
2. 时间控制:炉内停留的时间对于材料的退火效果也有重要影响,炉内的输送速度应能够根据所需的停留时间进行调节。
3. 炉内气氛控制:在一些特殊需求的退火处理中,炉内的气氛会对退火效果产生一定影响,因此需要通过加气、减压等方式来调节炉内的气氛。
4. 炉内结构和材料选择:连续式退火炉的炉膛结构和材料选择也非常重要,要能够耐高温和耐腐蚀,同时还要具备合理的热传导性能,以确保退火过程的顺利进行。
- 1、下载文档前请自行甄别文档内容的完整性,平台不提供额外的编辑、内容补充、找答案等附加服务。
- 2、"仅部分预览"的文档,不可在线预览部分如存在完整性等问题,可反馈申请退款(可完整预览的文档不适用该条件!)。
- 3、如文档侵犯您的权益,请联系客服反馈,我们会尽快为您处理(人工客服工作时间:9:00-18:30)。
卧式连续退火炉工艺设备与控制问题探讨
【摘要】由于立式退火炉主要采用辐射管间接加热,在带钢的表面质量控制上有一定优势,在近十几年得到了飞速的发展。
与此同时,卧式连续退火炉一方面主要用于家电板、建材的生产,另一方面其炉内张力较立式炉要小,非常适合生产硅钢和不锈钢等特殊钢种,目前仍被广泛应用。
本文将就卧式连续退火炉工艺设备以及模型控制的研究进展及其发展趋势进行分析。
【关键词】卧式连续退火炉;工艺设备;加热技术
1.工艺设备概况
带钢经过冷轧变形后,内部发生晶粒的扭曲和破碎,导致加工硬化和残余应力的产生,通常还需要经过退火处理。
退火是将带钢加热到适当的温度,然后经过一段时间的保温,并按规定的速度进行冷却,以此来获得良好的工艺性能及使用性能。
对冷轧卷的退火属于再结晶退火,在这一过程中带钢的内部组织将经过回复、再结晶、晶粒长大等三个主要过程。
为了完成上述工艺过程,通常采用连续退火炉对带钢进行热处理。
卧式连续退火炉一般由预热段、加热段(包括加热段和保温段)、冷却段等构成。
预热段一般为不供热段,主要利用从加热段流过来的高温烟气对带钢进行预热。
根据带钢表面质量和加热速度的要求,加热段可以选用明火焰直接加热和辐射管间接加热两种方式。
整个加热段内划分为数个独立控制区域,每一控制区域的烧嘴或辐射管可以进行单独控制。
冷却段分为缓冷段和快冷段,缓冷段通常采用气体喷射冷却方式,快冷段一般采用水雾冷却和水喷射冷却,使带钢达到工艺要求的冷却速度。
除上述主要工艺段之外,在炉子入口段一般都设有事故冷却段,在断带事故发生时用于冷却从炉子入口端回退的带钢。
在预热段,还设有余热回收装置,用于对烟气余热的多级回收。
高温烟气首先用来预热助燃空气,而后与带钢干燥用空气进行热交换,使最终排烟温度进一步降低。
在最终冷却段后还设有带钢干燥段,利用热空气对带钢进行干燥。
2.工艺设备发展
总体上看,卧式炉内主要热过程可分为加热和冷却。
加热方式主要有直接加热和间接加热两种。
在直接加热过程中,热源与带钢直接接触,尽管这种方式加热效率很高,但对带钢表面质量的影响较大。
而在间接加热方式下,热源与带钢非直接接触,故不会对带钢表面质量造成影响。
目前应用于板带退火过程的其它加热方法有电阻加热、盐浴加热等。
而一些研究结果表明快速加热可以使板带具有超高塑性,为其它一些快速加热方法在板带退火过程中的应用提供了理论依据。
例如:激光照射加热、等离子流加热和电容储能加热等。
退火过程中的另外一个关键点就是冷却方式的选取及控制。
传统用于带钢快速冷却的方式主要有高速气体喷射冷却、辊冷技术、气-水双相冷却技术和水冷技术等。
除了上述冷却方式之外,新发展的一些工艺具有更高的表面质量以及低的能耗。
如全空气悬浮冷却技术,由于带钢在冷却过程中不与炉辊接触,可以大幅提高带钢的表面质量。
比利时冶金研究中心(CRM)开发的强紊流辊冷技术(HTRC),相比传统喷射冷却能耗大幅降低。
今后连续退火设备将朝着机组高速度、带钢高
质量、控制智能化、低能耗和低污染的方向发展。
3.模型研究进展
由于连续退火工艺过程复杂,包括预热、加热、均热、缓冷和快冷等一系列热过程,涉及的传热方式和传热机理差异也很大,同时由于生产过程频繁变化,过于简化模型难以反映系统的动态特性,而复杂模型又难以满足实时性要求。
目前国内外有关带钢连续退火机组热过程数学模型,广泛应用的主要有两类:一类是利用现场数据进行模型关键参数估计的系统辨识模型,另一类是依据经典传热方程建立的传热机理模型。
两种模型各有长处。
带钢退火过程传热模型是依据传热学、流体力学和燃烧学等相关基础理论并经过严密的数学推导而建立起来的。
关于传热机理模型的研究,最具有代表性的是两类模型,即:带温跟踪模型和带温分布模型。
加热段的求解方法有区域法、热流法和蒙特卡洛法等。
区域法的主要思想是将炉膛划分为若干区域,并假定各区域内温度均匀,从而建立各区域间辐射传递方程进行求解。
假想面等效黑度法将辐射管和炉墙对带钢的辐射等效为假想灰平面对带钢的辐射,大大简化了辐射管炉内辐射传热的计算。
蒙特卡洛法利用统计思想,将表面发射的辐射能看成许多能束组成,并对能束进行跟踪统计得到两辐射表面间的传递系数。
求解带钢冷却过程的换热系数,目前主要利用传热反问题的方法解决。
国外有报导的文献对于数学模型的研究较少,在对模型的求解上,采用的方法主要是利用商业软件。
例如利用COMSOL软件建立连续退火炉内三维有限元带温模型,并利用MATLAB软件建立了一维和二维有限差分模型;利用商业软件Ansys计算模拟预热炉中带钢温度和应力分布耦合模型,并在模型中加入炉辊温度平衡方程,经过模拟研究发现锥形炉辊容易导致带钢宽度方向上严重的温度分布不均,从而引起带钢屈曲;这些研究成果也为国内今后的退火炉数学模型的建立及求解提供了新的选择和思路。
4.自动控制系统研究进展
4.1基于带钢数学模型的控制策略
20世纪90年代末,川铁开发出了一套复杂的带钢温度控制模型,通过带速与炉温的匹配来实现优化控制。
国内学者开发了基于带钢全炉温度模型的混合控制仿真模型,开发了连续退火炉炉温优化仿真系统,以连续退火炉数学模型为依据,采用了炉温启发式优化策略,该算法主要由滚动优化和启发式参数调整规则构成。
4.2基于智能优化技术的控制策略
智能优化技术不需要对被控对象建立复杂的物理模型,能够针对不确定的系统特性建立控制模型。
随着智能技术的不断发展,越来越多的智能技术融入到控制理论中,如专家系统控制、模糊控制、神经网络控制、遗传算法、人工免疫等控制算法。
这些控制方法在退火炉等工业炉窑控制中也逐步得到了应用。
5.结论
(1)一些新的高速加热方式,如激光加热、等离子束的加热技术等若用于卧式炉的带钢加热,将会促使卧式炉长度大幅度缩短。
(2)今后卧式炉内的冷却技术发展趋势预计是高效冷却介质的喷射冷却,如液氮、液氨以及甲醇等烃类物。
(3)目前针对卧式炉退火过程数学模型的研究较少,然而卧式退火炉在生产中也存在诸多问题急需解决,对于卧式炉进行相应的建模研究具有重要的理论意义和现实意义。
(4)对于喷流冷却目前还有很多问题没有得到很好的解决,这主要是
喷流过程涉及到湍流问题,而通过仿真模拟的准确度主要取决于湍流模型。
今后对于这一问题的解决方案一是通过对现有湍流模型进行修正,提高仿真精确度;二是在喷流冷却段采用智能控制算法,如利用神经网络技术建立智能模型,并引入自适应方法使模型具有自学习功能。
(5)近年来快速发展的各种智能控制算法,如模糊控制、神经网络和专家系统的引入等将会大大推动卧式退火炉计算机优化控制技术的进步,也会显著提高带钢卧式炉退火过程对带钢热处理质量的预测能力和控制精度及其系统的可靠性。
[科]
【参考文献】
[1]李强,温治,豆瑞锋,程淑明,邹航,董斌.连续热镀锌退火炉内热过程数学模型及其分析[J].工业加热,2007,(03).。