凝固过程温度场共57页文档
第3章 凝固过程的传热[23页]
![第3章 凝固过程的传热[23页]](https://img.taocdn.com/s3/m/0059e3a9294ac850ad02de80d4d8d15abe2300f6.png)
Tw f (t)
第二类边界条件: 给出通过物体表面的比热流随
时间的变化关系
T qx, y, z, t
n
第三类边界条件: 给出物体周围介质温度以及物
体表面与周围介质的换热系数
T = n
Tw
Tf
纯金属在铸型中凝固传热模型
K-导热 C-对流 R-辐射 N-牛顿界面换热
“三传”
所谓“三传”,即金属的凝固过程是一个 同时包含动量传输、质量传输和热量传输 的三传耦合的三维传热物理过程,而在热 量传输过程中同时存在有导热、对流和辐 射传热这三种传热方式。
t x x y y z z
λ --导热系数;
T--热力学温度; q --单位体积物体单位时间内释放的热量; c--比热容;
q L f s
t
ρ--密度;
t--时间。
对具体热场用上述微分方程进行求解时,需要根 据具体问题给出导热体的初始条件与边界条件。
初始条件: 初始条件是指物体开始导热时
第3章 凝固过程的传热
主要内容
3.1 凝固过程的传热 3.2 凝固时间的计算 3.3 液态金属凝固温度场
3.1 凝固过程的传热
3.1.1 凝固过程的传热特点
金属凝固过程中,其传热特点可简要概括为: “一热、二迁、三传”。
“一热”,即在凝固过程中热量的传输是第 一位的,是最重要的,它是凝固过程能否进 行的驱动力。
(即 t = 0 时)的瞬时温度分布。
边界条件:边界条件是指导热体表面与周围
介质间的热交换情况。
“二迁”
所谓“二迁”,是指在金属凝固时存在着 两个界面,即固—液界面和金属—铸型界 面,而这两个界面随着凝固进程而发生动 态迁移,并使得界面上的传热现象变得极 为复杂。
铸件凝固过程温度场分析计算

毕业设计铸件凝固过程温度场分析计算姓名: XX学号: XX班级: 10自动化(数控)2专业:自动化(数控)所在系:自动化工程系指导教师: XXX铸件凝固过程温度场分析计算摘要铸造是国民经济的重要产业部门之一,一个国家制造工业的规模和水平就靠它来反映。
航空、航天、汽车、机械等各行业的迅速发展,对铸件的需求量越来大,对铸造金属的性能及铸件本身的可靠性等要求也越来越高。
先进制造技术的发展要求铸件的生产向轻型化、精确化、强韧化、复合化及无环境污染方向发展。
铸造温度场是铸件在生产、加工及使用过程中产生缩孔缩松的主要原因,缩孔缩松不仅降低铸件的尺寸精度和使用性能,甚至直接导致铸件报废。
对铸造过程温度场进行数值模拟,可以预测铸件的缩孔缩松,为优化铸造工艺、减少应力、应变导致的铸件缺陷,提高铸件尺寸精度和使用寿命提供科学的参考依据[1]。
此毕业设计就是通过计算机模拟铸件的形成过程,并对其进行相应的温度场分析,根据判据找到缺陷发生的位置,旨在为实际生产提供理论基础,为改进工艺设计作贡献。
关键词:ANSYS;有限元分析;温度场;铸件凝固Casting Solidification Temperature Field Analysis andCalculationABSTRACTCasting is one of the important sectors of national economy, manufacturing industrial scale and level of a country depends on it to reflect. Aviation, aerospace, automotive, machinery and other industries, the rapid development of the to the greater demand for the castings, casting the metal on the performance and reliability requirements of the casting itself more and more is also high. The development of advanced manufacturing technology for casting production to light-duty composite, high-precision, strong, and no environmental pollution.Casting temperature field is castings produced in the process of production, processing and use the main cause of porosity shrinkage, porosity shrinkage not only reduce the size of the casting precision and operational performance, even as a direct result of the casting scrap. A numerical simulation of the temperature field of casting process can predict the shrinkage of the shrinkage, in order to optimize the casting process, reduce the stress and strain caused by the casting defects, improve the casting dimension accuracy and provide scientific reference for service life. The formation of this graduation design is through the computer simulation of casting process, and carries on the corresponding temperature field analysis, according to the criterion of finding defects location and aims to provide theoretical basis for actual production, make contributions to improve process design.Key Words:ANSYS;The finite element analysis;Temperature field;Casting solidification目录第一章绪论 (1)1.1本课题的背景和意义 (1)1.1.1铸件凝固过程温度场分析计算的意义 (1)1.1.2国内外发展状况 (1)1.1.3本课题的研究内容 (1)1.2本课题研究的方法和手段 (1)第二章理论及软件 (3)2.1本论文的理论基础 (3)2.1.1热传递的基本方式 (3)2.1.2导热过程的基本概念 (5)2.1.4ANSYS简介 (9)2.1.5软件功能介绍 (9)第三章软件模拟 (11)3.1建模和ANSYS前处理 (11)3.1.1PRO/E建立铸件模型 (11)3.1.2铸件砂型的建立 (12)3.1.3铸件在ANSYS的前处理过程 (15)3.2温度场求解过程 (22)3.2.1定义对流条件 (22)3.2.2求解设置 (25)3.3基于温度场的分析 (26)3.3.1温度场模拟结果 (26)结论 (31)参考文献 (32)致谢 (33)第一章绪论1.1 本课题的背景和意义1.1.1铸件凝固过程温度场分析计算的意义铸造温度场是铸件在生产、加工及使用过程中产生缩孔缩松的主要原因;铸造应力是铸件在生产、加工及使用过程中产生变形和裂纹的主要原因,缩孔缩松和裂纹不仅降低铸件的尺寸精度和使用性能,甚至直接导致铸件报废。
钢锭凝固过程温度场数值模拟
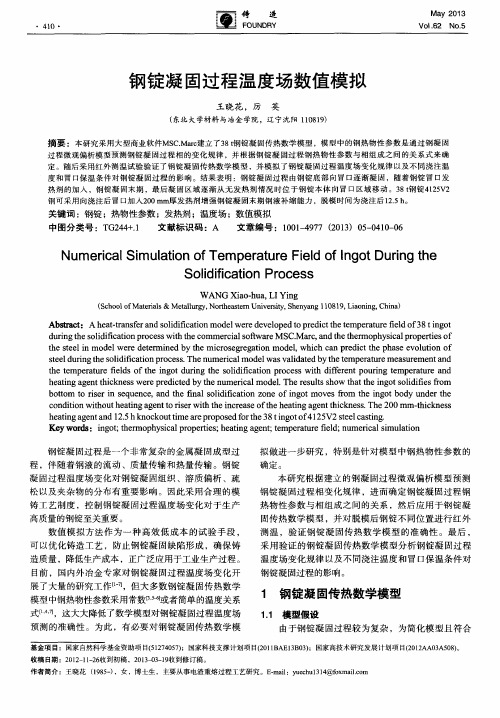
关键 词 :钢锭 ;热物 性参数 ;发热 剂 ;温度场 ;数值模拟 中图分 类号 :T G 2 4 4 + . 1 文献标 识码 :A 文章 编号 :1 0 0 1 — 4 9 7 7( 2 0 1 3 )0 5 — 0 4 1 0 — 0 6
过 程微观偏析模 型预测 钢锭凝 固过 程相 的变化 规律 ,并 根据钢锭凝 固过程钢 热物性参 数与相组成 之间 的关 系式来确 定 。随后采用红外测 温试验验证 了钢锭凝 固传热数 学模 型 ,并模 拟了钢锭凝 固过程温 度场变化 规律 以及不 同浇注温
度和 冒口保 温条件对钢锭 凝 固过程 的影响 。结果 表明 :钢锭凝 固过程 由钢锭底部 向 冒口逐 渐凝 固,随着 钢锭 冒 口发 热剂 的加 入 ,钢锭凝 固末期 ,最后凝 固区域 逐渐从 无发热 剂情况 时位 于钢锭本 体 向冒 口区域 移动 。3 8 t N锭4 1 2 5 V 2
s t e e l d ur i n g t h e s ol i di ic f a t i o n p r o c e s s . The n ume r i c a l mod e l wa s v a l i da t e d b y t he t e mpe r a t u r e me a s u r e me nt a nd
d u r i n g t h e s o l i d i i f c a t i o n p r o c e s s wi t h t h e c o mm e r c i a l s o t f wa r e MS C. Ma r c . a n d t h e t h e r mo p h y s i c a l p r o p e r t i e s o f t h e s t e e l i n mo d e l we r e d e t e r mi n e d b y t h e mi c r o s e g r e g a c a n p r e d i c t t h e p h a s e e v o l u t i o n o f
铸件凝固过程温度场的数值模拟
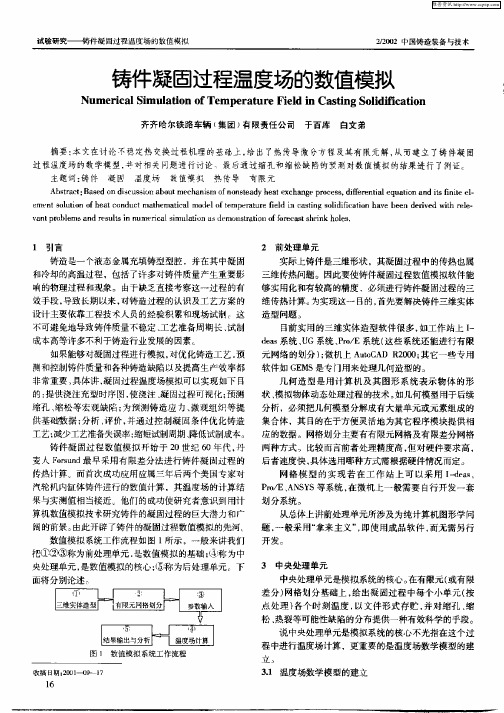
3 中央处 理 单元
从总体上讲前处理单拿来 主义” 即使用成品软件 , , 而无需另行
开 发。
中央处理单元是模拟系统 的核心。 在有限元 ( 或有限 差分) 网格划分基础上 , 给出凝 固过程 中每个小单元 ( 按
点处理 ) 各个时刻温度 , 以文件形式存贮 , 并对缩孔 、 缩
实际上铸件是三维形状 ,其凝固过程中的传热也属
三维传热问题 。因此要使铸件凝固过程数值模拟软件能
够实用化和有较高的精度 ,必须进行铸件凝固过程 的三 维传热计算 。 为实现这一 目的, 首先要解决铸件三维实体
造 型问题 。
目 前实用的三维实体造型软件很多 , 如工作站上 I — da 系统 、G系统、r E系统 ( es U Po / 这些系统还能进行有限
状、 模拟物体动态处理过程 的技术。 如几何模型用于后续
缩孔 、 缩松等宏观缺陷 ; 为预测铸造应力 、 微观组织等提 分析,必须把几何模型分解成有大量单元或元素组成的 供基础数据 ; 分析 、 评价 , 并通过控制凝固条件优化铸造 集合体 ,其 目的在于方便灵活地为其它程序模块提供相 工艺; 减少工艺准备失误率; 缩短试制周期 、 降低试制成本。 应的数据 。网格划分主要有有 限元网格及有限差分网格 铸件凝 固过程数值模拟 开始于 2 0世纪 6 年代 , o 丹 两种方式 比较而言前者处理精度高 , 但对硬件要求高, 麦人 Fr n 最早采用有 限差分法进行铸件凝 固过程 的 os d u 后者速度快 , 具体选用哪种方式需根据硬件情况而定 。 传热计算。而首次成功应用应属 三年后两个美国专家对 网格 模型 的实现 若在 工作 站上可 以采用 Ida 、 - es 汽轮机内缸体铸件进行的数值计算 ,其温度场的计算结 PoE A S S等系统 , r 、N Y / 在微机上一般需要 白行开发一套 果与实测值相当接近。他们 的成功使研究者意识到用计 划 分系统 。 算机数值模拟技术研究铸件的凝固过程的巨大潜力和广 阔的前景。 由此开辟了铸件的凝固过程数值模拟的先河。 数值模拟系统工作流程如图 1 所示 ,一般来讲我们 把①②⑧称为前处理单元 , 是数值模 拟的基础 ; ④称 为中 央处理单元 , 是数值模拟的核心 ; ⑤称为后处理单元 下 面将 分别论 述 ÷
第二章 凝固的温度场
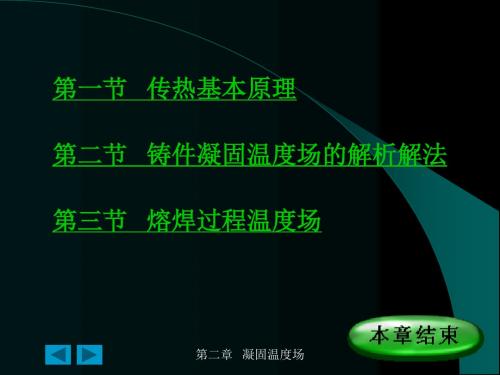
20
三、界面热阻与实际凝固温度场
上述关于铸造过程凝固温度场的分布以及凝固时间的讨 论均将铸件与铸型的接触当作是理想状态下的紧密接触, 实际界面存在热阻。
界面局部接触,有间隙
热阻来源 铸型型腔内表面常存在涂料
实际界面接触状况与涂料状况对界面热阻大小有重要影响。
第二章 凝固温度场
21
第二章 凝固温度场
10
第二节 铸件凝固温度场的解析解法
一、半无限大平板铸件凝固过程的
一维不稳定温度场
二、铸件凝固时间计算 三、界面热阻与实际凝固温度场
四、铸件凝固方式及其影响因素
第二章 凝固温度场
11
一、半无限大平板铸件凝固过程的 一维不稳定温度场
T T10
铸型 λ2 c2 ρ2
x T1 Ti T10 Ti erf 2 a t 1
得:
K
或:
2
K2
18
第二章 凝固温度场
将式(2-24)中的V1与A1推广理解为一般形 状铸件的体积与表面积,并令:
V1 R A1
可得一般铸件凝固时间的近似计算公式:
R K
R为铸件的折算厚度,称为“模数”。“模数法” 也称为“折算厚度法则”。
第二章 凝固温度场
19
从传热学角度来说,模数代表着铸件热容量与散
x erf 2 at 2
x
2 at 0
e
2
d
第二章 凝固温度场
14
代入铸件(型)的边界条件得:
x T1 Ti T10 Ti erf 2 a t 1
T T10
2.凝固温度场的测定
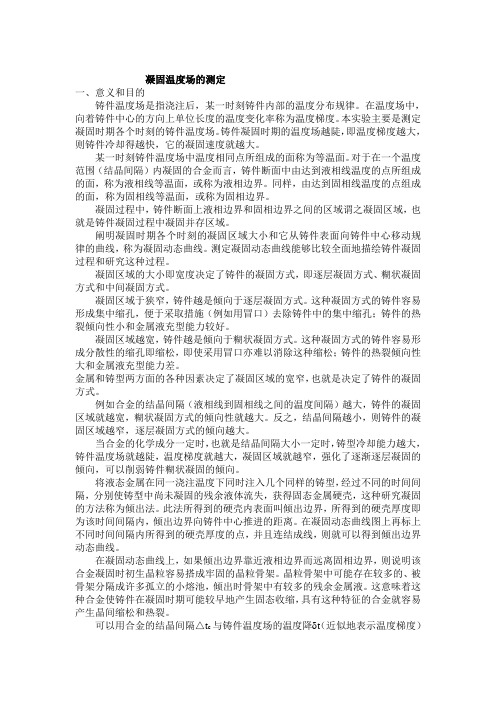
凝固温度场的测定一、意义和目的铸件温度场是指浇注后,某一时刻铸件内部的温度分布规律。
在温度场中,向着铸件中心的方向上单位长度的温度变化率称为温度梯度。
本实验主要是测定凝固时期各个时刻的铸件温度场。
铸件凝固时期的温度场越陡,即温度梯度越大,则铸件冷却得越快,它的凝固速度就越大。
某一时刻铸件温度场中温度相同点所组成的面称为等温面。
对于在一个温度范围(结晶间隔)内凝固的合金而言,铸件断面中由达到液相线温度的点所组成的面,称为液相线等温面,或称为液相边界。
同样,由达到固相线温度的点组成的面,称为固相线等温面,或称为固相边界。
凝固过程中,铸件断面上液相边界和固相边界之间的区域谓之凝固区域,也就是铸件凝固过程中凝固并存区域。
阐明凝固时期各个时刻的凝固区域大小和它从铸件表面向铸件中心移动规律的曲线,称为凝固动态曲线。
测定凝固动态曲线能够比较全面地描绘铸件凝固过程和研究这种过程。
凝固区域的大小即宽度决定了铸件的凝固方式,即逐层凝固方式、糊状凝固方式和中间凝固方式。
凝固区域于狭窄,铸件越是倾向于逐层凝固方式。
这种凝固方式的铸件容易形成集中缩孔,便于采取措施(例如用冒口)去除铸件中的集中缩孔;铸件的热裂倾向性小和金属液充型能力较好。
凝固区域越宽,铸件越是倾向于糊状凝固方式。
这种凝固方式的铸件容易形成分散性的缩孔即缩松,即使采用冒口亦难以消除这种缩松;铸件的热裂倾向性大和金属液充型能力差。
金属和铸型两方面的各种因素决定了凝固区域的宽窄,也就是决定了铸件的凝固方式。
例如合金的结晶间隔(液相线到固相线之间的温度间隔)越大,铸件的凝固区域就越宽,糊状凝固方式的倾向性就越大。
反之,结晶间隔越小,则铸件的凝固区域越窄,逐层凝固方式的倾向越大。
当合金的化学成分一定时,也就是结晶间隔大小一定时,铸型冷却能力越大,铸件温度场就越陡,温度梯度就越大,凝固区域就越窄,强化了逐渐逐层凝固的倾向,可以削弱铸件糊状凝固的倾向。
将液态金属在同一浇注温度下同时注入几个同样的铸型,经过不同的时间间隔,分别使铸型中尚未凝固的残余液体流失,获得固态金属硬壳,这种研究凝固的方法称为倾出法。
第二章凝固温度场
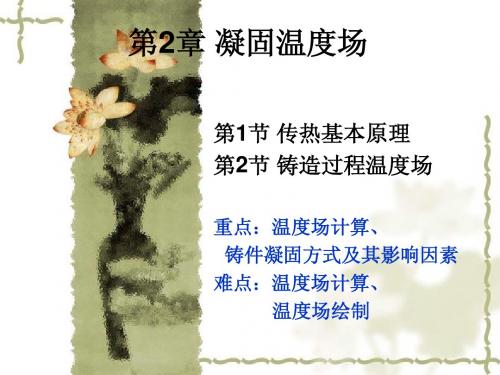
中间凝固方式特点: a、 结晶温度范围较窄 b、铸件断面的温度梯度较大 特点:凝固初期似逐层凝固 ——凝固动态曲 线上的两相边界纵向距较小凝固后期似糊状 凝固
(四)铸件凝固方式的影响因素
1、合金凝固温度区间的影响
2、温度梯度的影响
(五)金属凝固方式与铸件质量的关系 (一)窄结晶温度范围的合金 1、纯金属、共晶成分的合金 凝固前沿平滑
T T T T 2 ( 2 2 2 ) a T t c x y z
2 2 2
三、凝固温度场的求解方法
数学解析法
数值方法
差分法
有限元法
数学解析法
主要目的:利用传热学的理论建立表明铸件凝固过 程传热特征的各物理量之间的方程式、即铸件和温 度场数学模型并加以求解。 优点:物理概念、逻辑推理清楚,解的函数表达式 能够清楚表达温度场的各种影响因素,有利于分析 各参数变化对温度高低的影响。 缺点:只适用于简单热传导问题
(二)凝固区域及其结构
固相区:t<ts,完全凝固的区域; 液相线:t>tL,过热状态的金属液; 凝固区:液固部分:液相占优势----晶体处于悬浮状 态而未连成一片,液相可以自由移动; 固液部分:固相占优势 a、靠近液固部分晶体已连成骨架,液体可移动; b、靠近固相线部分骨架件有相互不沟通的小熔池得 不到补缩; 铸件在凝固过程中凝固区域按动态曲线所示的规律 向铸件中心推进。
he :间隙对流传热的等效换热系数一 可实测。 (3)凝固潜热的处理: 在凝固过程中,使铸件温度下降缓慢,讨论时有以下处理方法。 1)温度回升法 2)等价比热容法 3) 积分法 4)热焓法
凝固过程温度场
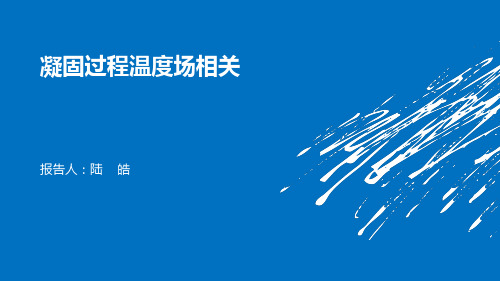
无内热源,且导热系数λ为常数
导热微分方程式:
d 2T dx2
0
温度分布:TC1xC2其中 C1(Tw1Tw2) C2 Tw1
热流通量及热流量: q d d T xT w 1 T w 2
热阻及热阻分析图:R
Tw1Tw2 q
规律:温度分布为直线且斜率大小由导热系数决定;内部各处热流通量 及热流量处处相等;
温度场
2、等温面与等温线 三维物体内同一时刻所有温度相同的点的集合称为等 温面(isothermal surface); 一个平面与三维物体等温面相交所得的的曲线线条即 为平面温度场中的等温线(isotherms)。 3、温度梯度 在具有连续温度场的物体内,过任意一点P温度变化 率最大的方向位于等温线的法线方向上。称过点P的 最大温度变化率为温度梯度(temperature gradient).用grad t表示。
A:垂直于导热方向的截面积[m2] 。 :导热系数(热导率)[W/mK]
一维无内热源单层平壁中
热传导( thermal conduction )
傅立叶定律(Fourier's Law)
傅里叶定律的文字表述:在导热现象中,单位时间内通过给定截面的热量, 正比例于垂直于该截面方向上的温度变化率和截面面积,而热量传递的方 向则与温度升高的方向相反。
温度梯度
温度梯度(temperature gradient)是等温线面法线 方向上的温度变化率。 在温度场中,温度梯度表达了温度在空间上改变的大 小程度,是一个矢量。方向指向温度增大的方向