气体膜分离
常用的处理废气中VOCs的膜分离工艺
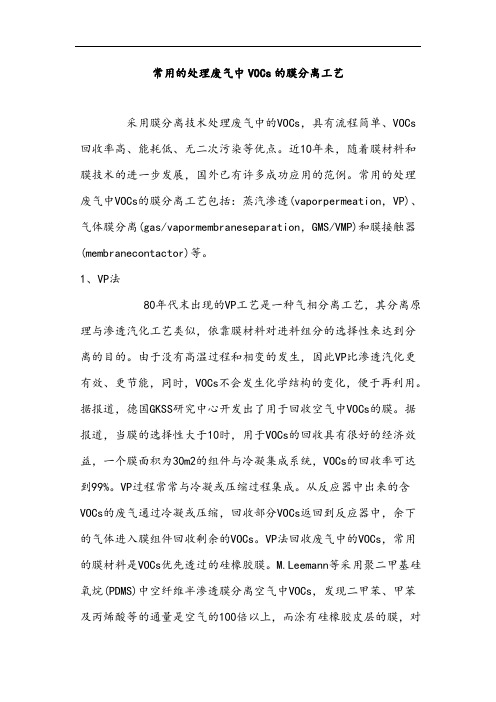
常用的处理废气中VOCs的膜分离工艺采用膜分离技术处理废气中的VOCs,具有流程简单、VOCs 回收率高、能耗低、无二次污染等优点。
近10年来,随着膜材料和膜技术的进一步发展,国外已有许多成功应用的范例。
常用的处理废气中VOCs的膜分离工艺包括:蒸汽渗透(vaporpermeation,VP)、气体膜分离(gas/vapormembraneseparation,GMS/VMP)和膜接触器(membranecontactor)等。
1、VP法80年代末出现的VP工艺是一种气相分离工艺,其分离原理与渗透汽化工艺类似,依靠膜材料对进料组分的选择性来达到分离的目的。
由于没有高温过程和相变的发生,因此VP比渗透汽化更有效、更节能,同时,VOCs不会发生化学结构的变化,便于再利用。
据报道,德国GKSS研究中心开发出了用于回收空气中VOCs的膜。
据报道,当膜的选择性大于10时,用于VOCs的回收具有很好的经济效益,一个膜面积为30m2的组件与冷凝集成系统,VOCs的回收率可达到99%。
VP过程常常与冷凝或压缩过程集成。
从反应器中出来的含VOCs的废气通过冷凝或压缩,回收部分VOCs返回到反应器中,余下的气体进入膜组件回收剩余的VOCs。
VP法回收废气中的VOCs,常用的膜材料是VOCs优先透过的硅橡胶膜。
M.Leemann等采用聚二甲基硅氧烷(PDMS)中空纤维半渗透膜分离空气中VOCs,发现二甲苯、甲苯及丙烯酸等的通量是空气的100倍以上,而涂有硅橡胶皮层的膜,对VOCs的选择性却有所下降。
同时,根据试验结果进行的经济可行性分析,发现在较高VOCs浓度和较低通量下,VP工艺比传统工艺有较大的经济可行性。
2、气体膜分离法膜法气体分离的基本原理是,根据混合气体中各组分在压力推动下透过膜的传质速率不同而达到分离的目的。
目前,气体膜分离技术已经被广泛应用于空气中富氧、浓氮以及天然气的分离等工业中。
近年来,GKSS、日东电工以及MTR公司已经开发出多套用于VOCs回收的气体分离膜。
气体膜分离技术
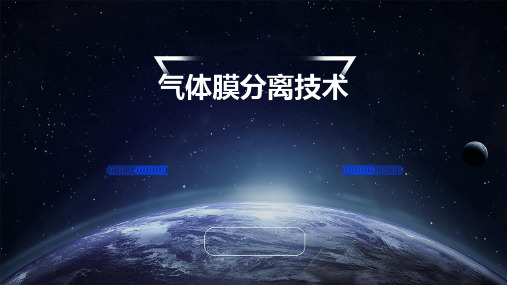
气体膜分离技术面临着来自其他分离技术的竞争压力,如蒸馏、吸附、吸收等。为了在市 场上获得竞争优势,需要不断提高技术的性能和降低成本。
技术创新
通过技术创新不断改进气体膜分离技术的性能和降低成本是市场成功的关键。这包括研发 新型膜材料、优化膜组件的设计和操作参数,以及开发新的应用领域。
未来发展方向与趋势
新型膜材料的研发
随着材料科学的不断发展,未来 将有更多新型的膜材料涌现,为 气体膜分离技术的发展提供新的
可能性。
集成化与智能化
未来气体膜分离技术将朝着集成 化和智能化的方向发展,实现多 级分离、能量回收和自动控制等
功能。
应用领域的拓展
随着气体膜分离技术的不断改进 和成本的降低,其应用领域将进 一步拓展,包括氢气、二氧化碳 等特殊气体的分离,以及生物医
气体膜分离技术
• 气体膜分离技术概述 • 气体膜分离技术的基本原理 • 气体膜分离技术的主要工艺流程
• 气体膜分离技术的实际应用案例 • 气体膜分离技术的挑战与前景
01
气体膜分离技术概述
定义与原理
定义
气体膜分离技术是一种基于气体在压 力驱动下通过高分子膜的选择性渗透 进行混合气体分离的先进技术。
原理
利用不同气体在膜中溶解和扩散速率 的不同实现选择性分离。在压力差的 作用下,渗透速率较快的组分优先透 过膜,从而达到分离目的。
分类与特点
分类
根据膜材料和分离机理,气体膜分离 技术可分为有机膜分离和无机膜分离 两类。
特点
操作简单、能耗低、无相变、无污染、 分离效率高、可实现大规模连续生产 等。
应用领域
工业气体分离
用于从混合气体中分离出氢气 、氮气、氧气等高纯度气体, 广泛应用于石油、化工、冶金
第六章气体膜分离ppt课件

严格执行突发事件上报制度、校外活 动报批 制度等 相关规 章制度 。做到 及时发 现、制 止、汇 报并处 理各类 违纪行 为或突 发事件 。
非多孔均质膜的溶解扩散机理
Knudsen扩散
❖ 气体的渗透速度q:
q43r2RM T1/2pL1R Tp2
气体透过膜孔的速度与其相对分子质量的平方根 成反比。
严格执行突发事件上报制度、校外活 动报批 制度等 相关规 章制度 。做到 及时发 现、制 止、汇 报并处 理各类 违纪行 为或突 发事件 。
分子筛分
❖ 大分子截留、小分子通过孔道,从而实现分 离。
应用阶段 ❖ 1940s:铀235的浓缩(第一个大规模应用) ❖ 1950年:富氧空气浓缩 ❖ 1954年:气体浓缩膜材料的改进
普及阶段 ❖ 1979年:Prism气体分离膜装置的成功
严格执行突发事件上报制度、校外活 动报批 制度等 相关规 章制度 。做到 及时发 现、制 止、汇 报并处 理各类 违纪行 为或突 发事件 。
气体分离膜材料及膜组件
(1)膜材料 有机膜:聚合物膜(便宜,常用) 无机膜:金属膜、陶瓷膜、分子筛膜
严格执行突发事件上报制度、校外活 动报批 制度等 相关规 章制度 。做到 及时发 现、制 止、汇 报并处 理各类 违纪行 为或突 发事件 。
描述气体通过高分子膜的主要参数
① 渗透率:描述膜的气体透过性; ② 渗透系数:单位时间、单位膜面积、单位 推动力作用下所透过气体的量; ③ 分离系数:描述气体分离膜的选择性,一 般将其定义为两种气体i,j渗透系数之比。
严格执行突发事件上报制度、校外活 动报批 制度等 相关规 章制度 。做到 及时发 现、制 止、汇 报并处 理各类 违纪行 为或突 发事件 。
膜分离气体的原理

膜分离气体的原理膜分离是一种常见且有效的气体分离技术,它是利用膜材料对气体分子的选择性渗透性进行分离的过程。
膜分离技术广泛应用于天然气纯化、空气分离、氢气制备、二氧化碳捕集等领域。
膜分离气体的原理基于气体分子在不同材料膜上的渗透速率差异,其分离原理可以归纳为三个基本过程:溶解、扩散和脱附。
首先是溶解过程。
在膜分离过程中,气体分子会溶解进入膜材料内部。
溶解过程的速率取决于气体溶解度和膜材料的亲溶性。
当气体分子的溶解度较高时,溶解过程对分离效果的影响将更加显著。
接着是扩散过程。
溶解在膜材料内部的气体分子会在不同浓度梯度下发生扩散,从而通过膜材料逐渐向另一侧迁移。
扩散过程的速率取决于气体分子在膜材料内部的扩散系数、膜材料的厚度和温度等因素。
通常情况下,较小的气体分子扩散速率更快。
最后是脱附过程。
气体分子在膜材料另一侧的界面上会脱附,重新进入气相。
脱附过程的速率取决于气体分子在膜材料内部的脱附速率和膜材料与气相之间的相互作用力。
当膜材料表面与气体分子之间的亲和力较低时,脱附过程将变得更加容易。
膜分离气体的原理可以通过多种不同类型的膜材料实现,如多孔膜、非多孔膜和复合膜等。
多孔膜是由具有一定孔径和孔隙度的材料制成,通过孔隙内气体分子的溶解、扩散和脱附来实现分离。
非多孔膜则是由透明聚合物制成的非孔隙结构,气体分子通过聚合物链的链隙进行扩散。
而复合膜则是由多层材料组成的,通过不同材料层之间的相互作用来实现分离。
膜分离气体的分离效果受多种因素的影响。
首先是膜材料的选择。
不同膜材料对于不同气体的分离效果有所差异,因此在应用中根据具体需要选择适当的膜材料。
其次是操作条件的控制,如温度、压力和流速等。
适当的操作条件可以提高膜分离的效果。
此外,也可以通过采用多级膜分离和膜组件的组合来提高分离效果。
总的来说,膜分离是一种基于膜材料对气体分子的选择性渗透性进行分离的技术。
它的原理涉及到溶解、扩散和脱附三个过程,通过控制这些过程的速率差异实现对气体分子的分离。
气体膜分离

(1)由于使用TMG膜分离系统,所以没有运动部 件,故障率极低,运行可靠性高,几乎不需维修, 膜组寿命长,使用年限保证在10年以上; (2)完备的控制系统保证氮气的纯度、流量和压 力具有高的稳定性; (3)启动迅速,操作简单,开启3min后即可供氮; (4)系统为模块设计,结构紧凑; (5)气体分离过程无噪音,无污染,并且不产生 任何有害废弃物.经过一级膜分离后,富氮浓度 一般可达99.5%(相对于氧而言,即无氧含量
四、制氮工艺流程
膜分离法制高纯氮的一般工艺流程(以天津 Messer公司产品为例)见图2。 空气经空压机加压后,再经过两级油水分离 器,两级颗粒过滤器以及碳过滤器和加热器, 使得原来含尘、含油、含水分高的空气,变成 含油、含尘、含水低的干净的压缩空气,干净 的压缩空气再在膜组的作用下,实现氧氮分离. 该流程的主要特点为:
2)进一步优化气体膜组件、膜装臵、膜过程 3)气体膜分离装臵向控制自动化程度高的方向发 展.目前已能对气体的浓度、温度、压力、露点 等进行自动控制,甚至可以全面实现与计算机 接口.全部操作可在电脑上进行 4)开发简单方便、普遍适用的制备中空纤维超薄 皮层(<5*10—8m)的方法 5)进一步优化气体膜制备生产工艺,以降低膜的 生产成本
气体膜分离.
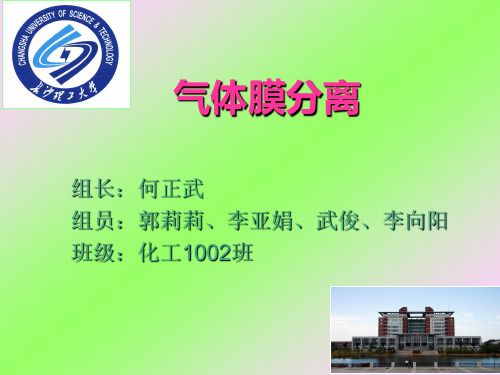
2)完备的控制系统保证氮气的纯度,流量和压力具有 高稳定性。
3)启动迅速,操作简单,开启3分钟后即可供氮。 4)系统为模块设计,结构紧凑。 5)气体分离过程无噪声,无污染,并且不产生任何有害 废弃物。经过一级膜分离后,富氮浓度一般可达99.5%。
膜材料的类型与结构对气体渗透有着显著影响。气体 分离用膜材料的选择需要同时兼顾其渗透性和选择性。
按材料的性质区分,气体分离膜材料主要有高分子材 料、无机材料和高分子-无机复合材料。其中高分子材料 又分橡胶态膜材料和玻璃态膜材料两大类。 高分子材料 和无机材料各有优缺点,采用复合材料可以较好地利用高 分子和无机材料的优点,以实现分离要求。
由上式可知,扩散系数反比于分子大小。从这一点也 可以看出氧的渗透性比氮要高。
此外,气体对给定聚合物的亲合性是有差别的,有时 甚至可以高达6个数量级。聚合物的选择性对气体的渗透 性有非常大的影响。具体到氧、氮来说,取膜质为聚二甲 基硅氧烷,氮气的渗透系数 QN 2 为280Barrer,而氧气的渗透 系数QO2为600Barrer,选择性因子为QO2/QN 2 = 600/280≈ 2.14。由于理想的聚合物膜必须具有高的选择性和通量, 因此,开发具有高的选择性的膜对制氧、制氮也是非常重 要的一个课题。
1). 在膜高压侧,气体混合物中的渗透组分溶解在膜的表 面上;(吸着)
2). 从膜的高压侧通过分子扩散传递到膜低压侧;(扩散) 3). 在低压侧解吸到气相。(解吸)
一般而言,吸附和解吸过程比较快,气体在膜内的扩散较
慢,是气体透过膜的控制步骤。
纯气体在高分子膜中的溶解平衡可以用Henry定律的形
膜分离技术
混合气体通过多孔膜的传递过程应以分子流为主, 其分离过程应尽 可能满足下述条件: 多孔膜的微孔孔径必须小于混合气体中各组分的平均自由程。 由于在大气压力下的λ的值在1000-2000Å,为了使分子流占优势, 取得良好的分离效果, 一般要求多孔膜的孔径在( 50 ~ 300) Å;
混合气体的温度应足够高, 压力尽可能低。
膜改性
(1)表面活性剂改性
表面活性剂是由至少两种以上极性或亲媒性显著不同 的官能团,如亲水基和疏水基所构成,具有不对称结构。 在其与溶液相接的界面上,由于官能团的作用形成选 择性定向吸附,界面的状态和性质即随之发生显著变化。 非离子型表面活性剂会在与它相接的截面上形成致密的亲 水层,改善界面的亲水性。离子型表面活性剂含有电荷可 以通过静电排斥相同电荷的物质在界面上的吸附。
气体从膜的低压侧表面上脱附出去
m= D· · · d A S ΔP/ = ( P / d) · · A ΔP =J · · P A Δ 式中: P -----D· 渗透系数(10-8---10-14) S J------D· 渗透速率 S/d
(2)表征膜性能的基本参数
渗透速率(J) J=D· S/d
膜改性
(5)辐照接枝改性
辐照接枝改性对于聚合物材料的物化特性和制备亲水性的 膜是一种行之有效的方法,是膜表面改性的重要途径之一。 它主要是利用高能Y射线或电子束对聚合物进行高能辐射, 使其产生活性种,然后活性种引发单体进行接枝聚合反应, 把某些性能的基团或聚合物支链接到膜材料的高分子链上, 使膜具有某些需要的性能。 聚合物改性既可改变膜的物理、机械性能,又可改变膜的 化学或物理性能。
膜改性
技术优点
气体膜分离技术及其发展应用
气体膜分离技术及其发展应用气体膜分离技术是一种利用气体分子在多孔膜中传递过程的物理和化学效应进行物质分离的技术。
通过气体在膜材料中的传递过程,不同大小、不同形状、不同性质的气体分子被分离出来,实现了气体纯化、浓缩、脱水和回收等目的。
由于其具有高效、节能、环保等优点,在许多领域的应用中得到了广泛关注。
1.气体分离与纯化:气体膜分离技术可以将混合气体中的组分分离出来,实现气体的纯化。
常见的应用包括空气中的氧气和氮气的分离、天然气中的甲烷和乙烷的分离等。
2.气体浓缩:气体膜分离技术可以将稀薄气体中的目标气体浓缩起来。
例如,将大气中的二氧化碳浓缩并用于工业化学反应、碳酸饮料制造等。
3.气体脱水:气体膜分离技术可以通过控制膜材料的选择和操作条件来去除气体中的水分。
这在天然气处理和乙醇生产等领域中具有重要的应用价值。
4.气体回收:气体膜分离技术可以将废气中的有用气体回收利用。
例如,在石油化工行业中,可以通过膜分离技术将废气中的有机溶剂进行回收利用。
1.早期阶段:20世纪50年代至70年代是气体膜分离技术的早期发展阶段。
在这个阶段,主要关注的是膜材料的选择和制备方法,以及对膜分离过程的理论研究。
2.中期阶段:到了20世纪80年代,气体膜分离技术开始逐渐应用于工业实践。
膜的制备方法和分离设备得到了改进,并且开始有了商业化的应用。
3.现代阶段:进入21世纪以后,气体膜分离技术的研究重点逐渐从传统膜材料向新型材料的研发转变。
例如,有机-无机杂化材料、金属有机框架材料等。
4.未来发展:随着能源和环境问题的日益突出,气体膜分离技术在能源和环保领域中的应用前景广阔。
未来发展的重点将在提高气体分离效率、降低成本、减少能耗等方面进行研究。
总之,气体膜分离技术具有广泛的应用前景。
随着新型材料和技术的不断发展,气体膜分离技术将在能源、化工、环保等领域中发挥更加重要的作用,为人类的可持续发展做出贡献。
气体膜分离技术应用
膜组件设计与制造
中空纤维膜组件
采用中空纤维膜丝束作为 分离元件,具有高装填密 度、低压降等优点。
卷式膜组件
将膜片卷绕在多孔支撑材 料上,形成多层分离结构 ,适用于大规模气体处理 。
板框式膜组件
由平板膜和框架组成,具 有易于清洗、更换方便等 特点。
膜性能评价与优化
渗透性能
评价膜对气体的渗透速率和选 择性,优化膜材料和结构以提
前景
随着环保要求的日益严格和能源结构的转变,气体膜分 离技术将在未来发挥更加重要的作用。例如,利用气体 膜分离技术回收工业废气中的有用组分,减少环境污染 ;在新能源领域,如燃料电池、太阳能等领域,利用气 体膜分离技术提纯氢气等燃料气体,提高能源利用效率 。此外,随着新材料和新技术的不断涌现,气体膜分离 技术的性能和应用范围将进一步拓展,为未来的气体分 离领域带来更多的可能性。
进料系统
将预处理后的原料气按一定压力 、温度和流量要求送入膜分离器 。
膜分离操作过程
膜的选择
渗透气和滞留气的收集
根据原料气的组成和分离要求,选择 合适的膜材料和结构。
渗透气(通过膜的气体)和滞留气( 未通过膜的气体)分别收集,以供后 续处理或应用。
膜分离器操作
在一定的操作条件下,如压力差、温 度等,原料气在膜分离器中实现组分 分离。
后处理及回收系统
渗透气和滞留气的后处理
根据应用需求,对渗透气和滞留气进行进一步的处理,如干燥、 压缩等。
回收系统
对于有价值的组分,可通过回收系统实现资源的有效利用,降低生 产成本。
安全与环保措施
确保整个工艺流程的安全性和环保性,采取必要的措施防止事故和 污染的发生。
04
CATALOGUE
气体分离的工作原理
气体分离的工作原理气体分离是指通过物理或化学方法将混合气体中的不同成分进行分离和提纯的过程。
不同的气体分离方法适用于不同的气体成分和应用场景。
本文将介绍几种常见的气体分离工作原理。
一、膜分离法膜分离法是一种基于气体分子大小差异的分离技术。
通过选择性渗透膜,将混合气体分子按照其大小进行分离。
常见的膜分离方法包括气体渗透膜、纳米孔隙膜和选择性溶剂吸附膜等。
在气体渗透膜中,较小分子将更容易通过膜,从而实现气体的分离。
二、吸附分离法吸附分离法是利用吸附材料对气体成分的选择性吸附特性进行分离。
吸附剂通常是由多孔性材料制成,表面具有高比表面积和可调控的吸附能力。
气体在经过吸附剂时,不同成分的吸附量不同,从而实现气体分离。
吸附分离常用于空气分离、氢气提纯和甲烷脱附等领域。
三、蒸馏分离法蒸馏分离法是一种利用气体成分的沸点差异进行分离的方法。
混合气体通过升温,使不同成分的沸点达到蒸发温度,然后在冷凝器中冷却,分离出不同沸点的气体。
蒸馏分离广泛应用于石油化工和化学工程领域。
四、催化分解法催化分解法利用催化剂对气体分子进行化学反应,将混合气体中的某一成分转化为其他物质,达到分离的目的。
常见的催化分解过程包括氧化、还原和裂解等。
催化分解法在氢气制备、氨合成和一氧化碳转换等反应中得到广泛应用。
五、气体凝聚法气体凝聚法是利用不同气体的凝聚点差异进行分离的方法。
通过调节温度和压力条件,使其中某一成分达到液态或固态状态,然后采取相应的分离操作,如冷凝、冷冻或吸附等。
气体凝聚法常用于甲烷液化、气体提纯和液空分离等过程。
综上所述,气体分离的工作原理包括膜分离法、吸附分离法、蒸馏分离法、催化分解法和气体凝聚法等。
这些方法根据不同气体成分的特性和需求场景的不同而选择。
通过合理应用这些气体分离技术,可以实现高效、经济和环保的气体分离过程。
- 1、下载文档前请自行甄别文档内容的完整性,平台不提供额外的编辑、内容补充、找答案等附加服务。
- 2、"仅部分预览"的文档,不可在线预览部分如存在完整性等问题,可反馈申请退款(可完整预览的文档不适用该条件!)。
- 3、如文档侵犯您的权益,请联系客服反馈,我们会尽快为您处理(人工客服工作时间:9:00-18:30)。
3.膜材料
常用的气体膜分离可分为多孔膜和致密膜两种,他们 可由无机膜材料和高分子膜材料组成。其中,无机材料主 要有多孔玻璃、陶瓷、金属(多孔质)和离子导电型固体、 钯合金等(致密膜);高分子材料主要有聚烯烃类、醋酸 纤维素类(多孔质)和均质醋酸纤维素类、合成高分子 (致密膜) 膜材料的类型与结构对气体渗透有着显著影响。气体 分离用膜材料的选择需要同时兼顾其渗透性和选择性。 按材料的性质区分,气体分离膜材料主要有高分子材 料、无机材料和高分子-无机复合材料。其中高分子材料 又分橡胶态膜材料和玻璃态膜材料两大类。 高分子材料 和无机材料各有优缺点,采用复合材料可以较好地利用高 分子和无机材料的优点,以实现分离要求。
理论分离系数的计算 α =JA/JB 查表得出硅橡胶的氧氮的渗透系数分别为605和 300, α =605/300=2.01 实测的分离系数的计算 α =y A x B/y B x A 当富氧浓度为28%时,α =1.46 当富氧浓度为40%时,α =2.5
(1)膜法富氧的操作方式
(2)医疗用富氧机 治疗慢性支气管炎和肺部疾病的方法之一是 经常呼吸富氧空气,浓度最大不超过40%,否则会 造成氧中毒。正常人的呼吸流量为6~8L/min,浓 度为28%~40%。膜法富氧得到的空气具有一定的 湿度,因为水蒸气可以透过膜,病人可以直接呼 吸无需加湿。考虑成本和噪音的因素,大多富氧 机采用负压操作。目前日本和美国已有富氧及产 品。
(3)富氧助燃 工艺流程
富氧浓度与火焰温度的关系
(4)富氧空调
富氧空调可以通过专用制氧设备产生 氧气以增加空调环境中的氧含量,从而降低 空调的能耗,在国内外许多专利中都提出了 采用膜法制氧的富氧空调"如日本发明专利 JP599457A, 中国发明专利 03126160.4, 97234786.0,98237222.1,03121202等。
气体膜分离
组长:何正武 组员:郭莉莉、李亚娟、武俊、李向阳 班级:化工1002班
目录
1 2 3 4
简介
原理 膜材料
应用
实例
5
1.简介
概 念
主要是根据混合原料 气中各组分在压力的 推动下,通过膜的相 对传递速率不同而实 现分离。
普里森(Prism) 中空纤维膜氮 氢分离器问世。 Heins 发明了 阻力复合膜。
结语
膜技术用于气体混合物的分离,国际公认为有效,且经济 性好。气体膜分离是一项高效节能环保的新兴技术,今后在 开发新的制膜方法、新的制膜材料方面是研究的热点,如开 8 发简单方便且普遍适用的制备无缺陷超薄膜( 5 10 m) 的方法;开发具有高性能同时又易形成无缺陷超薄皮层的 O2/N2分离膜材料;耐高温的有机和无机膜的开发等等。 我国的气体膜分离研究始于20 世纪80 年代初,与国外 差距相对不大,某些方面还具有国际先进水平。但也应看到, 我国气体分离膜产品单一,产业规模小,应用还没有全面展 开。故我国今后要尽快建立无机膜示范工程及技术中心,对 国际上新兴的研究课题,如膜催化、膜反应器等新膜过程, 以及集成过程、杂化膜过程要加大开发力度。争取产生自主 创新技术,跻身国际先进水平。
经济性分析比较 A/GTechnology对同一种浓度的氮气产品(95%),用膜法与PSA 法进行分析比较,比较结果见下表:
从表2可以看出,2种方法制备富氮的费用大致相等,但就基 本投资项而言膜法比PSA法少25%;此外,采用膜法移动部分 较少,预处理部分相对简单,启动快,不需要冷却水,这是PSA 法无法比拟的.
5.2 富氧富氮 5.2.1 膜法富氧 膜法富氧中透过气为富氧空气,尾气为富氮 空气,富氮空气的压力与原料气体的压力相近, 而富氧空气的压力要比原料气的压力低得多。原 料为空气,组成恒定,对膜无污染。典型的富氧 膜材料为硅橡胶,氧氮的分离系数α =2.0。大多 数的富氧材料的α =2~3,其富氧浓度为28%~40%。 主要用于医疗呼吸和助燃。
(5)富氧的经济性分析 A/G Technology公司生产的富氧装置,产品浓 度为:35%,产量为:10吨/d。该公司还采用PSA法 生产富氧空气,二者的经济性比较如下表:
5.2.2 膜法富氮 (1)工艺流程 膜分离法制高纯氮的一般工艺流程(以天津Messer公 司产品为例)见图2. 空气经空压机加压后,再经过两级油水分离器,两级 颗粒过滤器以及碳过滤器和加热器,使得原来含尘、含油、 含水分高的空气,变成含油、含尘、含水低的干净的压缩 空气,干净的压缩空气再在膜组的作用下,实现氧氮分离. 该流程的主要特点为:
2 2
(2)膜分离法制氮的工艺流程 膜分离法制氮的一般工艺流程(以天津Messer公司产品 为例)。见下图:
(3)分析 空气经空压机加压后,再经过两级油水分离器、两级颗 粒过滤器以及炭过滤器和加热器,使得原来含尘、含油、含 水分高的空气,变成含油、含尘、含水低的干净的压缩空气, 干净的压缩空气再在膜组件的作用下,实现氧、氮分离。该 流程的主要特点为: 1)由于使用TMG膜分离系统,没有运动部件,故障率极 低,运行可靠性高,几乎不需维修;膜组件寿命长,性能保证 在10年以上。 2)完备的控制系统保证氮气的纯度,流量和压力具有 高稳定性。 3)启动迅速,操作简单,开启3分钟后即可供氮。 4)系统为模块设计,结构紧凑。 5)气体分离过程无噪声,无污染,并且不产生任何有害 废弃物。经过一级膜分离后,富氮浓度一般可达99.5%。
由上式可知,扩散系数反比于分子大小。从这一点也 可以看出氧的渗透性比氮要高。 此外,气体对给定聚合物的亲合性是有差别的,有时 甚至可以高达6个数量级。聚合物的选择性对气体的渗透 性有非常大的影响。具体到氧、氮来说,取膜质为聚二甲 基硅氧烷,氮气的渗透系数 QN 为280Barrer,而氧气的渗透 系数QO 2 为600Barrer,选择性因子为 QO 2 /QN = 600/280≈ 2.14。由于理想的聚合物膜必须具有高的选择性和通量, 因此,开发具有高的选择性的膜对制氧、制氮也是非常重 要的一个课题。
速率分离
发 展 历 程
成为现代成熟 的化工分离单 元。
20世纪70年代末
80年代
目前
2.原理
根据气体通过膜的分离机理不同其原理主要有以下两种:
溶解扩散机理Biblioteka 吸着扩散解吸机 理
微孔扩散机理
1、分子扩散 2、粘性流动机制
3、(努森)Knudsen 扩散
4、表面扩散机制
2.1.1粘性流机制:
微孔直径
一个分子与其它分 子相继两次碰撞之 间,经过的直线路 程。
当dp >> 时,气体分子与孔壁之间的碰撞几率远远小于分子 之间的碰撞,此时气体通过微孔的传递过程属于粘性流机制,又 称为Poiseuille流。 当 dp ≈ 时,以上两种流动并存,属于平滑流机制。
2.1.2 表面扩散流机制 气体分子与膜表 面发生相互作用,即 吸附于表面并沿表 面运动(扩散),扩方 向为表面浓度递减 的方向。
2.2 溶解-扩散模型 气体通过致密膜(均值膜)的传递过程一般可通过溶解扩 散机理来描述。气体透过膜的过程如下: 1). 在膜高压侧,气体混合物中的渗透组分溶解在膜的表 面上;(吸着) 2). 从膜的高压侧通过分子扩散传递到膜低压侧;(扩散) 3). 在低压侧解吸到气相。(解吸)
一般而言,吸附和解吸过程比较快,气体在膜内的扩散较 慢,是气体透过膜的控制步骤。 纯气体在高分子膜中的溶解平衡可以用Henry定律的形 式表示,即 c=Hp 气体在膜内的扩散可以用Fick定律描述: 如果膜两侧温度相等,则有 J=(p1–p2)·Q /δ 式中: p1 ,p2 —— 分别为膜的高压侧和低压侧气体的压力; J —— 气体的渗透速率 δ —— 为膜的厚度; Q —— 气体组分通过膜的渗透率,它是气体组分 扩散系数与Henry系数的乘积。 当膜低压侧的压力比高压侧小得多是,即p2/p1=0,则 Q1 得 ai , j Q2 即两组分的分离因子等于两组分在膜中的渗透率之比 。
5.实例
5.1 合成氨工业 (1)氧、氮的动力学直径 由于气体分离的基本原理是由渗透系数Q决定的,而 渗透系数Q又是溶解度S和扩散系数D的乘积,而溶解度S与 扩散系数D均与分子的动力学直径有关,因此,氧、氮的动 力学直径影响着氧、氮的分离。 1)溶解度S主要取决于冷凝的难易程度,一般而言,大 分子更容易冷凝。由于氮的动力学直径为0.364nm,氧的 动力学直径为0.346nm,因此,氮分子在聚合物中的溶解度 比氧分子要大。 2)扩散系数D主要取决于两个因素:气体渗透物分子 的大小及聚合物的种类。分子越小,气体扩散系数越高, 尽管氧的分子量比氮大,但氧分子的体积比氮小,从扩散 系数来看,氧的渗透性比氮高。事实上,根据stocks定律, 扩散系数:
(5)小结:
气体膜分离制氮技术是一项高效且非常经 济的技术,是20世纪90年代关键分离技术之一, 深受人们的重视,也得到了一定程度的发展。 但应该指出,空气中氧、氮分离膜的分离性能 远末达到极限,膜过程与其他过程的藕合集成 工艺也未得到充分发展,因此,这就需要我们组 织跨学科、跨行业的科技人员进行合作,使我 国的气体膜分离技术得到更加长远和迅猛的发 展。
(4)膜分离法制氮与PSA法经济性比较 A/GTechnology对制取同一种浓度的氮气产(95%), 用膜法与用PSA法进行了分析比较,比较结果见下表。
从上表可以看出,两种方法制备富氮的费用大致相等, 但基本投资项膜法比PSA法(变压吸附法)少25%。此外, 膜法相对来说移动部分较少,预处理部分相对简单,启动 快,不需要冷却水,这是PSA法所无法比拟的。 此外,气体膜技术还可从合成氨弛放气分离回收 H 2 。 膜分离回收氢气,是当前应用面广,装置销售量最大的一种。 广泛用于合成氨厂、炼油工业和石油化工。用这方法回 收尾气中的氢气,循环于系统中,方法有效又安全,提高系 统的生产能力,最早用于合成氨驰放气中氢气的回收。我 国中型氨厂的合成系统弛放气,长期以来均作为燃料烧掉。 这部份气量相当于合成新鲜气的5一7%,如将其有效成分 回收利用,则对降低合成氨能耗、提高氨产量,增加工厂 的效益具有重要意义。采用膜分离装置回收其中有效成 份后可使氨增产3一5%,每吨氨能耗降低1.8一3%。。