精炼渣成分控制
北京科技大学科技成果——洁净钢生产中精炼渣控制技术

北京科技大学科技成果——洁净钢生产中精炼渣控制技术成果简介在冶金过程中,炉渣的控制对钢质量有着重要的影响。
特别是随着用户对钢质量要求愈来愈高,炉渣的控制技术也显得愈来愈重要。
许多高质量的钢种,对冶金精炼渣提出了极为苛刻的要求。
这就迫切要求炼钢生产厂家对冶炼过程中的各类渣系的冶金精炼性能有清晰的了解,从而达到在冶炼各过程中能做到充分利用和精确控制精炼渣的根本目的,为洁净钢生产服务。
北京科技大学在冶金渣方面的研究已有几十年的历史,无论在理论上还是在工艺上,均已经积累了丰富的经验,形成了自己的特色。
核心技术极低硫钢(≤0.002%)冶炼的精炼渣控制技术。
该技术根据企业实际冶炼或精炼设备提出最佳脱硫工艺以及提供相应的精炼渣控制技术。
低磷钢(≤0.005%)冶炼的精炼渣控制技术。
该技术根据企业实际冶炼或精炼设备提出最佳脱磷工艺以及提供相应的精炼渣控制技术。
低氮钢冶炼过程中脱氮和防治吸氮渣系控制技术。
氮是钢中较难去除的杂质元素,该技术主要是从改进工艺出发,在脱除部分氮的同时,尽可能防止氮从大气中的吸收。
在这方面,造渣技术起着重要的作用。
铝脱氧钢吸收Al2O3夹杂精炼渣控制技术。
铝作为强脱氧剂,在炼钢过程中有着广泛的应用。
但由此形成的Al2O3夹杂对钢非常有害,该技术结合企业铝脱氧工艺,提出最佳的吸收Al2O3夹杂精炼渣系。
无铝脱氧工艺低氧钢精炼渣控制技术。
对于许多质量要求较高的钢种,采用无铝脱氧,这样必然加大了钢液脱氧难度,而合理的精炼渣控制技术会使无铝脱氧钢液氧含量显著降低。
精炼过程中夹杂物的去除和控制技术。
该技术主要是通过合理地控制精炼渣成分来有效地控制钢液中夹杂物形成元素的含量,从而达到控制夹杂物成分和形态的根本目的。
合作方式以上技术可以转让或结合本企业情况共同合作开发,会取得较好经济效益。
控制渣中各种成分的含量精炼过程中泡沫渣的形成

控制渣中各种成分的含量精炼过程中泡沫渣的形成控制渣中各种成分的含量,可以得到发泡性能较好的渣成分,有利于精炼过程中泡沫渣的形成。
(1) Ca0和Si02Ca0是炼钢生产中造渣、脱磷和脱硫等必不可少的成分,其来源广泛,是精炼渣系的主要组元。
Si02主要来源于原料和脱氧产物,从图5-18可以看出,Si02含量在5%-10%茄罱肉时,熔渣发泡指数的上升趋势较为明显d由CaO-Sioz二元系和Al2 03 –CaO-Sioz三元系表面张力图可知,Si02厨质,微信公众号:hcsteel其含量增加有利于熔渣表面张力下降,提高吸附膜的弹性和强度,促进熔渣发泡。
从图5-18 (b)可以看出,渣碱度R(即CaO/Si02)=2时,烙渣发泡指数达到最大。
由Al2 03 –CaO-Si02相图可知,在所确定渣的实验范围,2Ca0,Al2 03。
Sioz组元的熔点较高,它的存在可使熔渣的表观黏度增加,渣膜存在时间延长,从而促进泡沫渣的形,成。
总之,高熔点粒子占渣重量12%时,发泡幅度最大,继续增加其含量,对炉渣发泡的影响不明显,且易使渣子黏度变大,对改善精炼渣流动性不利,所以,白灰的加入量应以10%~12 %、埋弧渣以40%-50%为宜。
(2) Al203Al2 03主要来源于原料和脱氧产物。
对于CaO-Si02-Alz 03-Mg0渣系,为了调节低氟精炼渣的熔化温度,取较高的Al2 03含量(30%左右)。
渣成分在小范围内变化对熔渣的发泡指数影响不大。
这可以由Al2 03 –CaO-Sio即氧化铝含量的变化对熔渣表面张力的影响较小,因而对熔渣发泡指数的影响不明显。
铝矾土改善渣子流动性所能起的作用,对不同的渣系是不同的,况且受成本因素的影响,也不应多加。
(3) CaF2萤石可显著降低精炼渣的黏度,改善炉渣流动性,增加传质。
但其量过大时对炉衬侵蚀严重。
萤石对发泡效果的影响是两方面的:一方面,萤石含量增加使炉渣表面张力降低,有利于熔渣发泡;但另一方面,其量增加又使熔渣黏度降低,这不利于发泡。
精炼渣成分控制

化学成分帘线钢要求控制的化学元素较多,表3列出了国内72, 82帘线钢盘条化学成分要求。
表3只是基本标准,各企业内控各不相同,但实际控制水平均要比表3严格的多。
国内钢厂大多在C,Mn,Si,O等成分的控制上一般没有问题,但在S,P,Al等元素的控制上虽然能达到基本标准,但控制水平大多偏低,同国外相比还有一定差距,这也是制约我国帘线钢水平上一个台阶的重要因素。
夹杂物国际上对帘线钢夹杂物要求常用的是意大利的皮拉利标准,要求夹杂物数量<1000个/cm³,尺寸<15 微米,高强度帘线钢要求夹杂物直径小于钢丝直径的2%;允许有纯Al203夹杂物存在,复合夹杂物中A1203含量≤50%,因铝酸钙类夹杂物无可塑性,也不允许存在。
国内对夹杂物要求一般采用评级的方式,要求塑性夹杂A类、C类≤1级,脆性夹杂B类、D类≤0。
5级。
因此,为了保证钢帘线产品质量,盘条金相组织中索氏体含量≥85%,不得有M、B、网状渗碳体等有害组织,表面脱碳层≤0.08 mm。
力学性能方面,72级帘线钢要求抗拉强度(1050士90) MPa,断面收缩率≥35%,82级要求抗拉强度(1150士90)MPa,断面收缩率≥300%。
非金属夹杂物控制造成帘线钢在拉拔或合股过程中断裂的最重要因素之一就是钢中非金属夹杂物 ,特别是硬质、不变形夹杂物 ,如Al2O3 和(Mg、Mn)O ·Al2 O3 ,对高强度帘线钢的影响更为突出 ,因此在生产高强度帘线钢时,采用洁净钢、超洁净钢冶炼技术就显得十分必要。
帘线钢炉外精炼的目的就是合理控制顶渣成分 ,通过钢渣界面反应来最大限度地减少有害夹杂物的影响 ,并对钢中夹杂物的形态、数量和大小进行有效控制是帘线钢生产的关键性环节。
夹杂物目标化学成分帘线钢中的夹杂物主要有两种类型 ,一种是来自于炉渣的 CaO-SiO2-Al2O3系夹杂物 ,另一种是来自于脱氧产物的 SiO2-MnO2-Al2O3系夹杂物。
金属冶炼中的原料成分控制

03 原料成分的调整与优化
根据产品要求调整
目标产品纯度
根据所需金属产品的纯度要求,对原料中的 杂质含量进行严格控制,确保产品纯度达标 。
金属冶炼中的原料成 分控制
目录
• 原料成分控制的重要性 • 原料成分的检测方法 • 原料成分的调整与优化 • 原料成分控制的实际应用 • 未来展望与挑战
原料成分控制的重要性
01
保证产品质量
01
精确控制原料成分
在金属冶炼过程中,精确控制原料成分是保证产品质量 的关键。通过确保原料中各元素的含量符合标准,可以 生产出具有一致物理和化学性质的金属或合金。
环保法规的影响
1 2
环保标准提高
随着环保法规的日益严格,金属冶炼企业需要不 断改进工艺和设备,降低污染排放,满足更高的 环保标准。
废物处理成本增加
环保法规对废弃物的处理和处置提出了更高要求 ,导致金属冶炼企业需要增加相关成本投入。
3
技术创新推动
环保法规的倒逼效应促使金属冶炼企业加大技术 研发和创新投入,推动行业绿色发展。
提高金属回收率
减少废品和次品
有效的原料成分控制可以减少废品和 次品的产生,提高产品的合格率,进 一步提高了生产效率。
通过精确控制原料成分,可以提高金 属回收率,从而降低生产成本。
降低能耗和排放
减少能源消耗
精确控制原料成分可以降低冶炼 过程中的能源消耗,从而减少对 环境的负担。
降低排放
通过优化原料成分,可以降低有 害物质的排放,减轻对环境的污 染。例如,减少硫、磷等有害元 素的含量可以降低烟尘和废水的 排放。
精炼渣各成分配比及所起作用
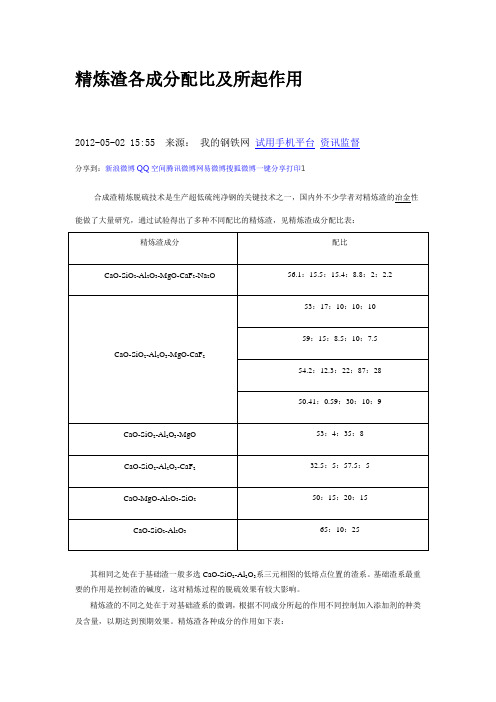
精炼渣各成分配比及所起作用2012-05-02 15:55 来源:我的钢铁网试用手机平台资讯监督分享到:新浪微博QQ空间腾讯微博网易微博搜狐微博一键分享打印1合成渣精炼脱硫技术是生产超低硫纯净钢的关键技术之一,国内外不少学者对精炼渣的冶金性其相同之处在于基础渣一般多选CaO-SiO2-Al2O3系三元相图的低熔点位置的渣系。
基础渣系最重要的作用是控制渣的碱度,这对精炼过程的脱硫效果有较大影响。
精炼渣的不同之处在于对基础渣系的微调,根据不同成分所起的作用不同控制加入添加剂的种类及含量,以期达到预期效果。
精炼渣各种成分的作用如下表:为了提升连铸坯质量,降低降价坯比例,炼钢车间在冶炼过程中成分按中限控制,强调钢包底吹的作用,保证软吹时间,均匀了成分和温度;终点控制上采用高拉碳法,不仅能降低合金、增碳剂、钢铁料等消耗,而且减少了由于增碳剂的加入带来的杂质。
连铸车间开机前对准备工作进行确认,尤其是中间包及水口的烘烤情况,保证中间包、水口的干燥,减少气泡夹杂的产生;对二冷区的喷嘴及水条进行检查清理,减少冷却不均造成的脱方、裂纹等缺陷,及时清理铸坯辊道冷钢、残钢,保证辊道的光滑,减少划痕等缺陷;在浇注过程中,他们稳定控制中间包液面,避免液面波动,减少卷渣造成的连铸坯夹渣缺陷。
同时为改善连铸坯质量,减少温降,该厂改进了原大包包盖,实施浇注全程盖包盖,减少钢水的二次氧化,改善连铸坯质量。
加强了连铸坯在线检查,杜绝不合格连铸坯出厂,9月份连铸坯合格率完成100%,比基本档提高0.15%,比目标档提高0.1%。
电弧炉冶炼终点碳的控制发布时间:2009-11-18 来源:东北特钢浏览人数:1370摘要对电弧炉冶炼过程熔池[C]—[O]反应进行了理论分析,通过现场试验建立了[C]—[O]关系图,试验条件下[O]=0.0032[C]-0.9441,[C]、[Fe]选择氧化的平衡点为[C]=0.035%。
指出在冶炼低碳钢种时,电弧炉终点碳应控制在0.04%以上。
钢铁冶炼中的炼钢渣体系和控制方法
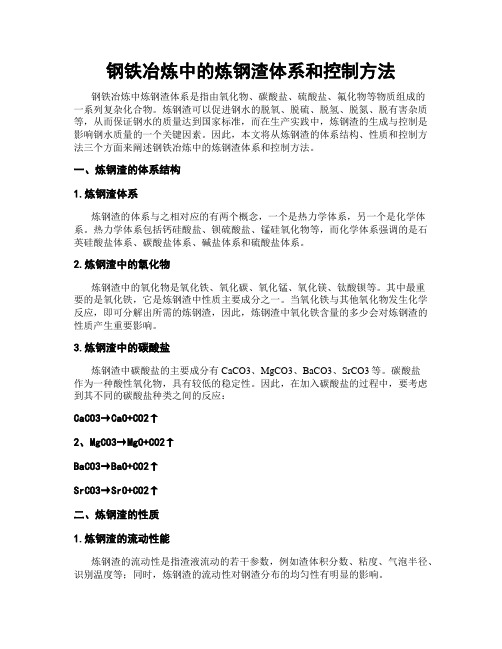
钢铁冶炼中的炼钢渣体系和控制方法钢铁冶炼中炼钢渣体系是指由氧化物、碳酸盐、硫酸盐、氟化物等物质组成的一系列复杂化合物。
炼钢渣可以促进钢水的脱氧、脱硫、脱氢、脱氮、脱有害杂质等,从而保证钢水的质量达到国家标准,而在生产实践中,炼钢渣的生成与控制是影响钢水质量的一个关键因素。
因此,本文将从炼钢渣的体系结构、性质和控制方法三个方面来阐述钢铁冶炼中的炼钢渣体系和控制方法。
一、炼钢渣的体系结构1.炼钢渣体系炼钢渣的体系与之相对应的有两个概念,一个是热力学体系,另一个是化学体系。
热力学体系包括钙硅酸盐、钡硫酸盐、锰硅氧化物等,而化学体系强调的是石英硅酸盐体系、碳酸盐体系、碱盐体系和硫酸盐体系。
2.炼钢渣中的氧化物炼钢渣中的氧化物是氧化铁、氧化碳、氧化锰、氧化镁、钛酸钡等。
其中最重要的是氧化铁,它是炼钢渣中性质主要成分之一。
当氧化铁与其他氧化物发生化学反应,即可分解出所需的炼钢渣,因此,炼钢渣中氧化铁含量的多少会对炼钢渣的性质产生重要影响。
3.炼钢渣中的碳酸盐炼钢渣中碳酸盐的主要成分有CaCO3、MgCO3、BaCO3、SrCO3等。
碳酸盐作为一种酸性氧化物,具有较低的稳定性。
因此,在加入碳酸盐的过程中,要考虑到其不同的碳酸盐种类之间的反应:CaCO3→CaO+CO2↑2、MgCO3→MgO+CO2↑BaCO3→BaO+CO2↑SrCO3→SrO+CO2↑二、炼钢渣的性质1.炼钢渣的流动性能炼钢渣的流动性是指渣液流动的若干参数,例如渣体积分数、粘度、气泡半径、识别温度等;同时,炼钢渣的流动性对钢渣分布的均匀性有明显的影响。
2.炼钢渣的稳定性炼钢渣的稳定性指的是渣液在一定条件下中不被分解、产生新的化学反应,能在限制条件下稳定存在的能力,同时炼钢渣的稳定性还与其流动性和抗渗透性等特点有关。
3.炼钢渣的还原性炼钢渣的还原性体现了其在高温下进行还原反应的倾向。
当加热时,炼钢渣中会产生还原性气体,例如CO和H2等,这些还原性气体在炼钢渣中与氧化铁等发生还原反应,从而影响炼钢渣的稳定性及其对钢水的影响。
钢水精炼处理过程中化学成分的精确控制
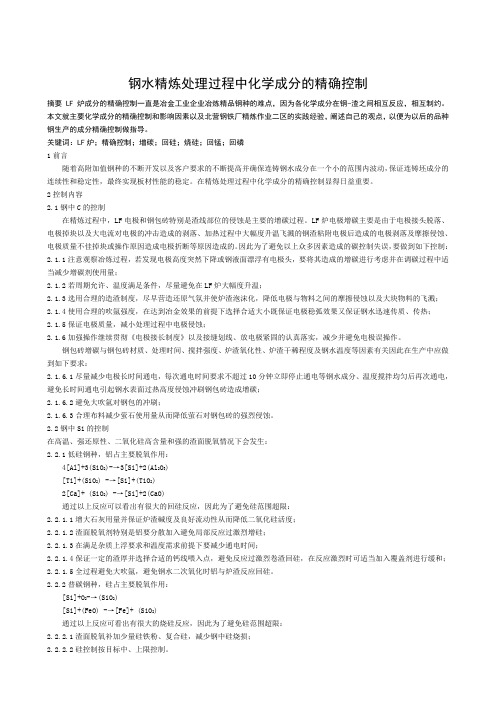
钢水精炼处理过程中化学成分的精确控制摘要 LF炉成分的精确控制一直是冶金工业企业冶炼精品钢种的难点,因为各化学成分在钢-渣之间相互反应,相互制约。
本文就主要化学成分的精确控制和影响因素以及北营钢铁厂精炼作业二区的实践经验,阐述自己的观点,以便为以后的品种钢生产的成分精确控制做指导。
关键词:LF炉;精确控制;增碳;回硅;烧硅;回锰;回磷1前言随着高附加值钢种的不断开发以及客户要求的不断提高并确保连铸钢水成分在一个小的范围内波动,保证连铸坯成分的连续性和稳定性,最终实现板材性能的稳定。
在精炼处理过程中化学成分的精确控制显得日益重要。
2控制内容2.1钢中C的控制在精炼过程中,LF电极和钢包砖特别是渣线部位的侵蚀是主要的增碳过程。
LF炉电极增碳主要是由于电极接头脱落、电极掉块以及大电流对电极的冲击造成的剥落、加热过程中大幅度升温飞溅的钢渣粘附电极后造成的电极剥落及摩擦侵蚀、电极质量不佳掉块或操作原因造成电极折断等原因造成的。
因此为了避免以上众多因素造成的碳控制失误,要做到如下控制:2.1.1注意观察冶炼过程,若发现电极高度突然下降或钢液面漂浮有电极头,要将其造成的增碳进行考虑并在调碳过程中适当减少增碳剂使用量;2.1.2若周期允许、温度满足条件,尽量避免在LF炉大幅度升温;2.1.3选用合理的造渣制度,尽早营造还原气氛并使炉渣泡沫化,降低电极与物料之间的摩擦侵蚀以及大块物料的飞溅;2.1.4使用合理的吹氩强度,在达到冶金效果的前提下选择合适大小既保证电极稳弧效果又保证钢水迅速传质、传热;2.1.5保证电极质量,减小处理过程中电极侵蚀;2.1.6加强操作继续贯彻《电极接长制度》以及接缝划线、放电极紧固的认真落实,减少并避免电极误操作。
钢包砖增碳与钢包砖材质、处理时间、搅拌强度、炉渣氧化性、炉渣干稀程度及钢水温度等因素有关因此在生产中应做到如下要求:2.1.6.1尽量减少电极长时间通电,每次通电时间要求不超过10分钟立即停止通电等钢水成分、温度搅拌均匀后再次通电,避免长时间通电引起钢水表面过热高度侵蚀冲刷钢包砖造成增碳;2.1.6.2避免大吹氩对钢包的冲刷;2.1.6.3合理布料减少萤石使用量从而降低萤石对钢包砖的强烈侵蚀。
金属冶炼中的渣的性质与控制

降低渣的生成量可以提高金属的回收 率,减少资源浪费,同时也可以降低 环境污染。
渣的成分控制
渣的成分直接影响着其物理性质和化 学性质,因此控制渣的成分对于金属 冶炼过程的稳定性和产品质量至关重 要。
REPORT
CATALOG
DATE
ANALYSIS
SUMMARY
金属冶炼中的渣的性 质与控制
目录
CONTENTS
• 金属冶炼渣的基本性质 • 渣的生成与控制 • 渣对冶炼过程的影响 • 渣的处理与利用 • 渣的性质研究进展
REPORT
CATALOG
DATE
ANALYSIS
SUMMAR Y
01
金属冶炼渣的基本性质
SUMMAR Y
05
渣的性质研究进展
高炉渣的基础研究
成分分析
高炉渣主要由硅酸盐矿物和铝酸盐矿物组成,还含有少量的碳化 物和氮化物。
熔化特性
高炉渣的熔化温度和黏度对冶炼过程具有重要影响,熔化温度过 低或黏度过大会影响渣铁分离和金属回收率。
稳定性
高炉渣的稳定性决定了其与金属液滴的相互作用能力,对控制金 属的收得率和质量具有关键作用。
渣的环保处理
Hale Waihona Puke 固化/稳定化处理通过添加固化剂或稳定剂,使渣中的有害物质被固定或稳定,降 低对环境的危害。
土地填埋
经过处理的渣可以在符合规定的场地进行填埋,防止有害物质泄漏 。
烟气和废水处理
冶炼过程中产生的烟气和废水应经过处理,达标排放,以减少对环 境的污染。
REPORT
CATALOG
- 1、下载文档前请自行甄别文档内容的完整性,平台不提供额外的编辑、内容补充、找答案等附加服务。
- 2、"仅部分预览"的文档,不可在线预览部分如存在完整性等问题,可反馈申请退款(可完整预览的文档不适用该条件!)。
- 3、如文档侵犯您的权益,请联系客服反馈,我们会尽快为您处理(人工客服工作时间:9:00-18:30)。
化学成分帘线钢要求控制的化学元素较多,表3列出了国内72, 82帘线钢盘条化学成分要求。
表3只是基本标准,各企业内控各不相同,但实际控制水平均要比表3严格的多。
国内钢厂大多在C,Mn,Si,O等成分的控制上一般没有问题,但在S,P,Al等元素的控制上虽然能达到基本标准,但控制水平大多偏低,同国外相比还有一定差距,这也是制约我国帘线钢水平上一个台阶的重要因素。
夹杂物国际上对帘线钢夹杂物要求常用的是意大利的皮拉利标准,要求夹杂物数量<1000个/cm³,尺寸<15 微米,高强度帘线钢要求夹杂物直径小于钢丝直径的2%;允许有纯Al203夹杂物存在,复合夹杂物中A1203含量≤50%,因铝酸钙类夹杂物无可塑性,也不允许存在。
国内对夹杂物要求一般采用评级的方式,要求塑性夹杂A类、C类≤1级,脆性夹杂B类、D类≤0。
5级。
因此,为了保证钢帘线产品质量,盘条金相组织中索氏体含量≥85%,不得有M、B、网状渗碳体等有害组织,表面脱碳层≤0.08 mm。
力学性能方面,72级帘线钢要求抗拉强度(1050士90) MPa,断面收缩率≥35%,82级要求抗拉强度(1150士90)MPa,断面收缩率≥300%。
非金属夹杂物控制造成帘线钢在拉拔或合股过程中断裂的最重要因素之一就是钢中非金属夹杂物 ,特别是硬质、不变形夹杂物 ,如Al2O3 和(Mg、Mn)O ·Al2 O3 ,对高强度帘线钢的影响更为突出 ,因此在生产高强度帘线钢时,采用洁净钢、超洁净钢冶炼技术就显得十分必要。
帘线钢炉外精炼的目的就是合理控制顶渣成分 ,通过钢渣界面反应来最大限度地减少有害夹杂物的影响 ,并对钢中夹杂物的形态、数量和大小进行有效控制是帘线钢生产的关键性环节。
夹杂物目标化学成分帘线钢中的夹杂物主要有两种类型 ,一种是来自于炉渣的 CaO-SiO2-Al2O3系夹杂物 ,另一种是来自于脱氧产物的 SiO2-MnO2-Al2O3系夹杂物。
其中锰铝榴石(3MnO-Al2O3-SiO2) 和位于钙斜长石(CaO-Al2 O3-SiO2)和假硅灰石(CaO-SiO2)共晶线周边区域的夹杂物属玻璃态塑性夹杂(图 1) ,具有熔点低(1000~1400 ℃) ,变形性好 ,吸附夹杂能力强 ,凝固过程中无外来相析出等特点 ,是帘线钢夹杂物控制的理想区域。
国外学者研究发现 ,在上述两个区域内 ,当 Al2 O3的质量分数为 15 %~25 %时 ,夹杂物的不可变形指数最低(图 2) ,如果 Al2 O3 含量太高 ,凝固过程中 Al2 O3 夹杂易析出 ,如果 Al2 O3 含量太低 ,则凝固过程中 SiO2 夹杂易析出。
因此 ,帘线钢中理想夹杂物成分为: w (CaO) / w (SiO2 ) ≤1. 08 , w (Al2 O3 ) = 15 %~25 %。
轮胎钢帘线作为橡胶轮胎的骨架材料,要求其具有动态弹性率大、强度高、拉伸蠕变小、尺寸稳定性好以及弯曲刚度高等特点。
钢帘线的单丝直径一般为0.15-0. 38mm。
冷拔和捻股过程中发生断丝的主要原因是钢中存在硬而不变形的脆性夹杂物。
在成品钢帘线的动态疲劳性能试验或在轮胎的实际应用中,即便是细小的脆性夹杂物颗粒也能导致早期断裂。
非金属夹杂物除影响帘线钢盘条的强度外,钢丝在拉拔和捻股过程中还容易断丝,给生产带来很大的损失,应用效果也差。
生产高碳钢丝时,线径Φ0.2mm的钢丝中只要存在一个大颗粒夹杂物就会断线,特别是高强度化导致硬度提高,对钢丝影响更大。
帘线钢对钢中的非金属夹杂物有着特别严格的要求。
因此,通常采用炼钢炉外精炼工艺等措施控制非金属夹杂物。
帘线钢中非金属夹杂物的控制夹杂物的控制是帘线钢生产中至关重要的环节。
只有严格控制钢中夹杂物的数量、尺寸及形态,才能减少钢帘线拉拔及合股过程中断丝的几率。
2 1帘线钢中理想的夹杂物形态国外专家对帘线钢中理想的夹杂物形态及成分进行了大量的研究认为,采用Si-Mn脱氧的帘线钢中主要有MnO-A203-SiO2系(来自脱氧产物)和Ca0-Al203-Si2O2系(来自炉渣)两种夹杂物。
MnO-A203-SiO2系理想的夹杂物成分范围应该是锰铝榴石(3Mn0·Al203·3SiO2)及其周围的低熔点区域,见图1所示Ca0-Al203-SiO2系理想的夹杂物成分范围为钙斜长石(Ca0·Al203·2SiO2)与假硅灰石(Ca0·SiO2)相邻的周边低熔点区域,见图2所示。
以上区域的夹杂物熔点较低(≤1500℃),变形性较好,在制作帘线拔丝及合股过程中不会造成断丝。
2 2 LF炉精炼渣设计根据上述分析,配制LF精炼渣的主要成分应为CaO, SiO2和A l2 03。
根据三元系相图(见图3所示)和夹杂物的要求确定精炼渣的成分,利用已知的相平衡状态图和渣结构的基本规律,并结合经验和工艺条件的要求,设计合理的基础渣化学组分。
能最有效控制夹杂物形态的精炼渣成分应该是硅灰石或与其相似成分,硅灰石具有低氧势、低熔点、易吸收脱氧产生的夹杂物等优点,尤其是Al2 03,而且当硅灰石与少量萤石或A l203混合时,熔点将降至1200℃。
3 Al203夹杂物根据S Maeda的研究结果,夹杂物中Al2 03含量与不变形夹杂物指数的关系见图4所示。
由图4可见,夹杂物中Al2 03含量为20%时,不变形夹杂物指数最低,而此时精炼渣中A l203含量约为8%3采用合成渣精炼控制帘线钢中的夹杂物根据相图和上述研究结果,采用硅灰石及其相似成分作为合成精炼渣,能有效地控制钢中夹杂物的数量和类型,主要采取以下工艺措施:(1)铁水预脱硫,入LF炉钢水S含量≤0 010%,为采用低碱度渣创造条件;(2)添加硅灰石及相似成分,造低碱度合成精炼渣,延长渣洗时间,提高去除B类、D类夹杂的能力;(3)采用专用脱氧剂及合金脱氧;(4)在精炼处理过程中不加A}减少渣中Al203含量,精炼结束时炉渣Al203含量控制在8%左右,精炼最终目的是把夹杂物中的Al2O控制在20%左右;(5)保证VD真空处理效果及处理后静吹时间,使夹杂物充分碰撞、聚集并上浮排除。
4结论(1)生产帘线钢时,采取以硅灰石及其相似成分的合成渣精炼工艺能够有效控制帘线钢中非金属夹杂物的形态和数量,得到熔点低、塑性良好的脱氧产物,夹杂物形态以半塑性和塑性为主。
(2)}灯采用合成渣精炼工艺对钢水进行充分的渣洗,使夹杂物有充分的时间碰撞、聚集并上浮,钢中夹杂物的尺寸变小,满足了帘线钢性能的要求。
高质轴承钢要求高的纯净度和组织均匀,即杂质元素和非金属夹杂少,碳化物细小且分布均匀。
精炼渣具有脱氧、脱硫、去夹杂的作用,其性质直接影响LF精炼过程的冶金效果。
当碱性还原渣同钢液密切接触时,钢液中实际的氧、硫的数值大于同渣平衡的氧、硫的数值,使钢液中的氧和硫向渣中打一散川;精炼渣中Ca0 ,A120,等成分能够与Si,A1,Mn等的脱氧产物结合成低熔点的化合物,从而降低脱氧产物的活度,强化脱氧反应;由于精炼渣均由氧化物组成,氧化物之间的界面张力小,易于结合成低熔点化合物,而钢液与脱氧产物间的界面张力大于渣和脱氧产物之间的界面张力,精炼渣可以吸收脱氧产物,使脱氧产物容易从钢液中排除。
此外,精炼渣融化后形成泡沫渣,渣层覆盖钢液,可有效防止气体吸人,且有利于埋弧操作,减轻电弧对钢包内衬和钢包盖的损害,提高热效率,”。
因此,研究精炼渣成分变化及其对钢洁净度的影响,对LF精炼作用的充分发挥具有重要意义。
GCr15轴承钢是重要的机械基础件用钢,在大多数机械产品和工程结构中应用十分广泛,它在很大程度上决定了装备的精度、性能、寿命与可靠性随着科学技术的发展,对轴承的寿命提出了更高更严的要求,而其纯洁度和组织均匀性是影响其使用寿命的重要因素。
要对轴承钢中夹杂物进行控制,首先要对钢中的夹杂物的种类、形态作一下定性分析,弄清楚夹杂物的来源,然后采取针对性的措施,从轴承钢轧材取样,然后通过扫描电镜观察,发现 A 类硫化物夹杂、 B 类氧化铝夹杂、 D 类铝酸钙复合夹杂物以及镁铝尖晶石夹杂和氮化钛夹杂。
其中 A 类硫化物夹杂在轧制过程中可塑性变形,对轴承钢的疲劳寿命危害相对较小,只要把钢中硫含量降低到规格要求以下即可。
B 类氧化铝夹杂是脆性夹杂物,为铝脱氧产物,常聚集为团簇状,轧制过程中沿轧制方向排列为点状或串状。
其对轴承钢疲劳寿命有害,并且钢中高的氧化铝含量会在浇注过程中产生水口结瘤。
D 类铝酸钙复合夹杂物为点状夹杂物,来源为氧化铝与渣中氧化钙生成的复合化合物。
其在轧制过程中不变形,容易造成应力集中形成裂纹源,降低轴承钢疲劳寿命。
镁铝尖晶石是氧化铝与渣中氧化镁和包衬带入的氧化镁复合生成的硬脆性夹杂物,对轴承钢疲劳寿命有害。
氮化钛夹杂是具有棱角的硬而脆的夹杂物,由钢中溶解的氮与合金所带入钢中的钛生成。
其在热加工过程中不变形,并且其棱角容易划伤钢的基体成为疲劳裂纹源。
轴承钢的性能主要取决于钢的化学成分、纯洁度和组织均匀性三个方面,其中尤以化学成分影响最大。
碳在GCr15中保证其具有足够的淬透性、硬度值和耐磨性。
但太高容易产生大块碳化物。
铬是碳化物形成元素,主要作用是提高钢的淬透性和耐腐蚀性能,并可提高强度、硬度、耐磨性、弹性极限和屈服强度。
铬过高会因残余奥氏体量增加而降低硬度,并容易形成大块碳化物,使钢的韧性降低。
锰和铬一样是碳化物形成元素,但这种碳化物易溶于奥氏体,回火时易析出和聚集,所以锰元素主要作为脱氧元素,一般不宜太高。
硅在GCr15中也主要作为脱氧元素,虽可强化铁素体,提高强度,但使钢的过热敏感性、裂纹和脱碳倾向性增加,一般不宜控制太高。
硫、磷在轴承钢中,被视为有害元素。
硫容易形成硫化物夹杂,影响钢的性能磷在钢中严重引起凝固时的偏析,磷溶于铁素体使晶粒扭曲、粗大,且增加冷脆性。
钛溶解钢中的氮有着极强的亲和力,所形成的氮化钛夹杂坚硬、呈棱角状,对轴承钢疲劳寿命影响极大。
其它残余元素:镍由于增加了淬火后残余奥氏体量,降低硬度,故受到限制,铝也作为参与元素存在,其有害作用不明显,铜为低熔点有色金属,它的存在使钢加热时容易形成表面裂纹,同时也会引起钢的时效硬化,影响轴承精度。
轴承钢精炼渣系主要是以Ca0-A1203和Ca0-Si02-A1203的高碱度精炼渣系为主。
由Ca0-A1203二元相图可知:渣中存在低熔点的化合物12Ca0-A1203,可通过调节精炼渣中A1203含量降低熔渣的熔点,改善合成渣精炼的动力学条件。
Si02属于酸性氧化物,不利于精炼渣脱硫,但Si02对熔渣的泡沫化性能有较大的影响。
由Ca0-A120,元系和Ca0-Si02-A1203三元系表面张力图可知,Si02属表面活性物质,其含量增加可降低表面张力,促进发泡,增加渣膜的弹性和强度。