343-paper-B1-精炼渣系对轴承钢D类夹杂物的影响
钢中夹杂物知识.
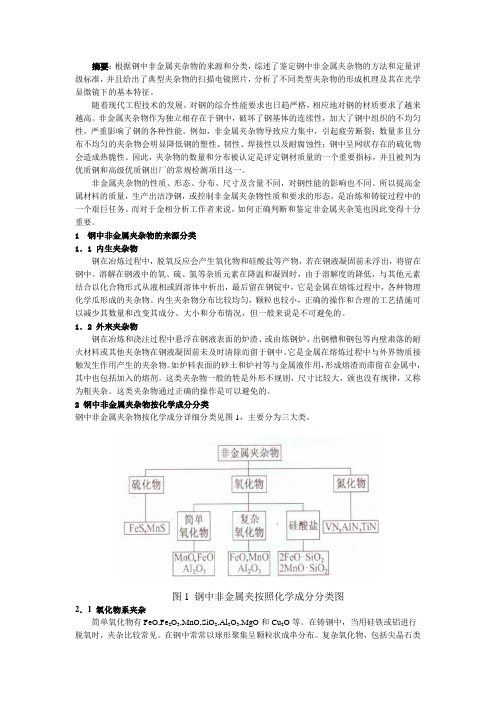
摘要:根据钢中非金属夹杂物的来源和分类,综述了鉴定钢中非金属夹杂物的方法和定量评级标准,并且给出了典型夹杂物的扫描电镜照片,分析了不同类型夹杂物的形成机理及其在光学显微镜下的基本特征。
随着现代工程技术的发展,对钢的综合性能要求也日趋严格,相应地对钢的材质要求了越来越高。
非金属夹杂物作为独立相存在于钢中,破坏了钢基体的连续性,加大了钢中组织的不均匀性,严重影响了钢的各种性能。
例如,非金属夹杂物导致应力集中,引起疲劳断裂;数量多且分布不均匀的夹杂物会明显降低钢的塑性、韧性、焊接性以及耐腐蚀性;钢中呈网状存在的硫化物会造成热脆性。
因此,夹杂物的数量和分布被认定是评定钢材质量的一个重要指标,并且被列为优质钢和高级优质钢出厂的常规检测项目这一。
非金属夹杂物的性质、形态、分布、尺寸及含量不同,对钢性能的影响也不同。
所以提高金属材料的质量,生产出洁净钢,或控制非金属夹杂物性质和要求的形态,是冶炼和铸锭过程中的一个艰巨任务。
而对于金相分析工作者来说,如何正确判断和鉴定非金属夹杂笺也因此变得十分重要。
1 钢中非金属夹杂物的来源分类1.1 内生夹杂物钢在冶炼过程中,脱氧反应会产生氧化物和硅酸盐等产物,若在钢液凝固前未浮出,将留在钢中。
溶解在钢液中的氧、硫、氮等杂质元素在降温和凝固时,由于溶解度的降低,与其他元素结合以化合物形式从液相或固溶体中析出,最后留在钢锭中,它是金属在熔炼过程中,各种物理化学瓜形成的夹杂物。
内生夹杂物分布比较均匀,颗粒也较小,正确的操作和合理的工艺措施可以减少其数量和改变其成分、大小和分布情况,但一般来说是不可避免的。
1.2 外来夹杂物钢在冶炼和浇注过程中悬浮在钢液表面的炉渣、或由炼钢炉、出钢槽和钢包等内壁肃落的耐火材料或其他夹杂物在钢液凝固前未及时清除而留于钢中。
它是金属在熔炼过程中与外界物质接触发生作用产生的夹杂物。
如炉料表面的砂土和炉衬等与金属液作用,形成熔渣而滞留在金属中,其中也包括加入的熔剂。
轴承钢牌号-化学成分及其规范标准对比

调研报告内容:1、概述(研究目的与意义)2、该产品研究国内外研究与发展现状(发展过程、现状及发展前景)3、技术、市场分析(重点介绍)3.1 国内生产现状(包括主要生产厂家、各厂家生产该产品采用的生产工艺流程、生产设备、关键技术、生产规格、执行标准或技术条件、产品产量和质量状况、现有及潜在用户、市场占有情况等)(重点介绍)3.2市场分析(包括现有和潜在市场容量、产品规格、售价、利润情况、主要品种、主要目标用户及加工工艺、技术质量要求等)(重点介绍)4、可行性分析莱钢开发生产该产品的必要性和可行性分析(主要分析莱钢现有装备和工艺条件是否满足、产品利润预测等)5、其它:特殊要求品种需要介绍一下钢种定义、性能特点、主要用途、用户个性化要求等)1、概述(研究目的与意义)作为合金钢的一种,轴承钢包括高碳铬轴承钢、渗碳轴承钢、高温轴承钢、不锈轴承钢及特殊工况条件下应用的特殊轴承钢。
目前,我国轴承钢总产量已达220万t左右,其中高碳铬轴承钢约占轴承钢总产量的90%以上。
轴承钢是所有合金钢中质量要求最严格、检验项目最多、生产难度最大的钢种之一,主要用于制造滚动轴承。
世界公认轴承钢的生产水平是一个国家冶金水平的标志。
对于一个企业来说,轴承钢的生产水平也是一个企业冶金水平的标志,纵观国际及国内的知名特钢生产企业,无一不将轴承钢特别是高标准轴承钢作为其产品调整、发展战略的一个重要目标。
我国的一些知名特钢生产企业如:兴澄特钢、东北特钢、上海宝钢特钢生产的轴承钢具有品质高(通过国际知名轴承公司SKF、FAG、Timken 认证),产量大(年产量基本维持在30-50万吨的水平)等特点。
莱钢特钢作为一个老牌特钢生产企业,目前轴承钢生产只能按国内标准生产,档次低、品种单一、产量低(年产量在1万吨左右),与国际、国内的知名特钢生产企业相比差距明显。
根据现有装备和生产水平,开发高品质轴承钢,并适当扩大产量不仅对于进一步调整、优化企业产品结构,提高莱钢特钢产品的附加值及经济效益,增强市场竞争能力具有重要意义,而且有利于提升企业的知名度。
超低氧特殊钢中非金属夹杂物研究
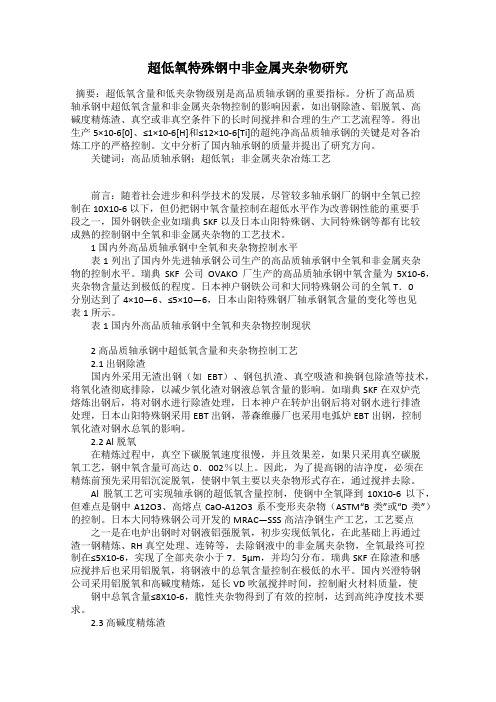
超低氧特殊钢中非金属夹杂物研究摘要:超低氧含量和低夹杂物级别是高品质轴承钢的重要指标。
分析了高品质轴承钢中超低氧含量和非金属夹杂物控制的影响因素,如出钢除渣、铝脱氧、高碱度精炼渣、真空或非真空条件下的长时间搅拌和合理的生产工艺流程等。
得出生产5×10-6[0]、≤1×10-6[H]和≤12×10-6[Ti]的超纯净高品质轴承钢的关键是对各冶炼工序的严格控制。
文中分析了国内轴承钢的质量并提出了研究方向。
关键词:高品质轴承钢;超低氧;非金属夹杂冶炼工艺前言:随着社会进步和科学技术的发展,尽管较多轴承钢厂的钢中全氧已控制在10X10-6以下,但仍把钢中氧含量控制在超低水平作为改善钢性能的重要手段之一,国外钢铁企业如瑞典SKF以及日本山阳特殊钢、大同特殊钢等都有比较成熟的控制钢中全氧和非金属夹杂物的工艺技术。
1 国内外高品质轴承钢中全氧和夹杂物控制水平表1列出了国内外先进轴承钢公司生产的高品质轴承钢中全氧和非金属夹杂物的控制水平。
瑞典SKF公司OVAKO厂生产的高品质轴承钢中氧含量为5X10-6,夹杂物含量达到极低的程度。
日本神户钢铁公司和大同特殊钢公司的全氧T.0分别达到了4×10—6、≤5×10—6,日本山阳特殊钢厂轴承钢氧含量的变化等也见表1所示。
表1国内外高品质轴承钢中全氧和夹杂物控制现状2 高品质轴承钢中超低氧含量和夹杂物控制工艺2.1 出钢除渣国内外采用无渣出钢(如EBT)、钢包扒渣、真空吸渣和换钢包除渣等技术,将氧化渣彻底排除,以减少氧化渣对钢液总氧含量的影响。
如瑞典SKF在双炉壳熔炼出钢后,将对钢水进行除渣处理,日本神户在转炉出钢后将对钢水进行排渣处理,日本山阳特殊钢采用EBT出钢,蒂森维藤厂也采用电弧炉EBT出钢,控制氧化渣对钢水总氧的影响。
2.2 Al脱氧在精炼过程中,真空下碳脱氧速度很慢,并且效果差,如果只采用真空碳脱氧工艺,钢中氧含量可高达0.002%以上。
S34MnV曲轴锻用钢的夹杂物控制

S34MnV曲轴锻用钢的夹杂物控制陈建东【摘要】Refining slag system of CaO-SiO2-Al2 O3-MgO-CaF2 base containing fluorine is used , the content of the CaF2 in the slag is about 20%, this slag system has relatively strong capability in absorbing inclusions .Prior to vacuu-ming, partial MgO-Al2 O3 inclusions has transformed into CaO-MgO-Al2 O3 inclusion with relatively low melting point;vacuumed inclusion is the CaO-MgO-Al2 O3 inclusion of completely changed nature .In the course of prior to vacuuming→aftervacuuming→c asting blank , the amount of inclusions is gradually decreased .The inclusion in the cast blank is the CaO-MgO-Al2 O3 inclusions of completely changed nature , this inclusion does very little harm to the mechanical property of the steel forging for the crankshaft .%采用CaO-SiO2-Al2 O3-MgO-CaF2基含氟精炼渣系,渣中含CaF220%左右,该渣系有较强的吸附夹杂物的能力。
S34MnV曲轴锻用钢的夹杂物控制

S34MnV曲轴锻用钢的夹杂物控制
陈建东
【期刊名称】《大型铸锻件》
【年(卷),期】2014(000)003
【摘要】采用CaO-SiO2-Al2 O3-MgO-CaF2基含氟精炼渣系,渣中含CaF220%左右,该渣系有较强的吸附夹杂物的能力。
真空前钢水中的部分MgO-Al2 O3夹杂物已转变成熔点较低的CaO-MgO-Al2 O3夹杂物,真空后的夹杂物是完全改
性的CaO-MgO-Al2 O3夹杂物。
真空前→真空后→铸坯过程中,夹杂物数量逐
渐减少。
铸坯中的夹杂物是完全改性后的CaO-MgO-Al2 O3夹杂物,该夹杂物
对曲轴锻用钢力学性能的危害很小。
【总页数】4页(P30-33)
【作者】陈建东
【作者单位】上海重型机器厂有限公司大型铸锻件研究所,上海200245
【正文语种】中文
【中图分类】TF111.18
【相关文献】
1.船用曲轴锻件用S34MnV钢过热的原因探讨和细化工艺的研究 [J], 吴佳胤;王
文柏;黄淼;胡亮亮;沈才平
2.C-Mn 系列曲轴锻用钢的夹杂物控制 [J], 陈建东;卢斌;韩国盛;刘立鹤;杨海石;
刘俊;黄飞
3.船用曲轴钢S34MnV液芯锻造研究 [J], 吴永强;付文;王开坤;杨艳
4.夹杂物对易切削钢曲轴耐酸蚀性能的影响 [J], 孔德群;来振华;董晓萌;周建;金晓旭
5.不同金属夹杂物对曲轴钢加工过程中刀具磨损及表面完整性的影响 [J], 秦声;胡蒙;陈小刚;明伟伟;陈明
因版权原因,仅展示原文概要,查看原文内容请购买。
精炼渣组成对31CrMoV9钢夹杂物的影响

Ef fe c t o f Re in f i ng S l a g I n g r e d i e n t o n I n c l u s i o n s i n S t e e l 3 1 Cr Mo V9
X u Z e y u , L i u J i h u i , He Z h i j u n ,C o n g Y u n l i n g , P a n g Q i n g h a i a n d Z h a n We n l o n g
量从 1 0 %增加 到 2 0 %, 每0 。 3 m m 钢中夹杂物的面积 由2 2 . 5 7 增至 2 4 . 2 8 p , m , 增幅为 7 . 5 5 %, 夹杂物的数量
由2 9 2 . 6 7 A ' / 0 . 3 mm 降至 2 7 2 . 0 0+/ o . 3 mm , 降幅为 7 . 0 6 %, 并易形成镁铝尖 晶石类 夹杂 物。综合分析 , 当精炼 渣成分为 1 0 %A 1 2 O , 、 1 0 %M g O、 5 %C a F 2 、 二元 碱度为 3 . 5时精炼效果最 佳。 关键 词 3 1 C r M o V 9钢 C a O — S i O 2 一 A 1 2 O 3 一 M g O — C a F 2系精炼 渣 碱 度 A 1 O 3 夹杂物
杂物数量 、 尺寸 和成分 的影响。结果表明 , 精炼 渣二元碱 度和氧化铝含量对该钢夹杂物 含量 的影 响显 著 ; 当二元 碱 度从 2 . 5增加 到 3 . 5时 , 每0 . 3 m m 钢 中夹 杂物的平 均面积从 2 2 . 0 7 v m 增至 2 5 . 6 7 m , 增幅为 1 6 . 3 1 %; 夹杂物 的数量从 3 1 6 . 6 7+/ o . 3 m l n 2降至 2 5 5 . 0 0个/ 0 . 3 I B m , 降幅为 1 9 . 4 7 %, 且有利于形成复合型夹杂物 。当氧化铝含
炉渣反应平衡对钢中总氧和非金属夹杂物影响的研究

炉渣反应平衡对钢中总氧和非金属夹杂物影响的研究摘要:高强度低合金钢为了控制钢中硫含量,生产过程中采用高碱度、低氧化性精炼渣,致使钢中生成尺寸较大的塑性夹杂物,严重影响钢材质量。
炉渣组成对钢中夹杂物有很大影响,文章介绍了采用钢-渣平衡的方法对五种渣系(不同CaO/SiO2和Al2O3%)钢中总氧和非金属夹杂物影响的研究。
结果表明,钢-渣反应平衡后,顶渣中CaO/SiO2在1.93~4.54,Al2O3%在21%~30%;钢中T.O在7×10-6~19×10-6;钢中夹杂物呈球形,绝大多数尺寸在5μm以下,类型为Al2O3-SiO2-CaO-MgO系,部分夹杂物中含有少量MnO。
当顶渣中Al2O3含量一定时,随着顶渣中(CaO+MgO)/SiO2提高,T.O下降;夹杂物中MnO含量降低,CaO/Al2O3增加。
当顶渣CaO/SiO2一定时,随着渣中Al2O3含量的提高,T.O增加;夹杂物中Al2O3含量增加,CaO含量也相应增加,CaO/Al2O3变化不大,约在1,夹杂物中MgO含量和MgO/Al2O3下降。
随着钢中T.O含量的增加,夹杂物的数量呈上升的趋势;钢中出现大尺寸夹杂物的几率增加。
关键词:高强度低合金钢;顶渣;总氧含量;夹杂物1 前言钢中非金属夹杂物的存在是影响钢制品性能的重要因素,有时甚至是决定性的因素。
夹杂物对钢力学性能和工艺性能的影响,主要是降低材料的塑性、韧性、疲劳性能和耐腐蚀性能,尤其当夹杂物以不利的形状及分布特征存在时,对材料的机械性能影响更为严重。
钢中非金属夹杂物,如氧化物、硫化物等危害性能就在于都呈独立相存在,破坏了钢基体的均匀连续性,造成了应力集中,促进了疲劳裂纹的产生,并在一定条件下加速了裂纹的扩展,从而加速了疲劳破坏的过程,在加工过程中会产生裂纹,使成材率大大降低,产品质量下降[1]。
氧化物和硫化物夹杂对容器壁是最危险的,产生裂纹的临界尺寸是十分之几微米。
浅谈钢中夹杂物的控制对钢质量的影响
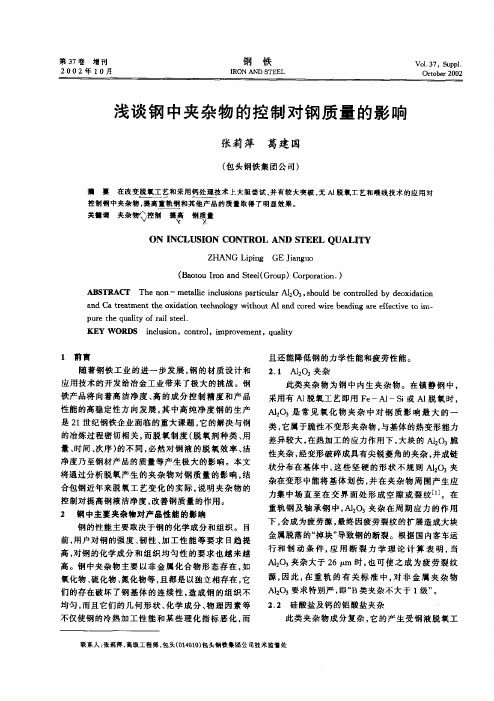
(ao In S eGop Cr ri . Bo u ad l r ) p ao ) t r n t ( u o o tn o e
A SR C T e 一 e l i li s tu r 马, olb c t ld doi tn BT A T h nn m tl n uo prcl A o ai c sn a i a 眨 s u e rl b e d i c h d o o e y x ao n ad t a et oi tn ho g wt u A ad e wr hai a ee i t i n C r t n t x ao t nl y h t n c d e d g fcv o a m e h d i e o i o l o e c r i e n r f t e m- e pr t qat o r l l ue uly a s e h e i f t . i e
金属脱落的“ 掉块” 导致钢的断裂。根据国内客车运 行和制动条件, 应用断裂力学理论计算表明, 当
高。 钢中夹杂物主要以非金属化合物形态存在, 如 氧化物、 硫化物、 氮化物等, 且都是以独立相存在, 它 们的存在破坏了钢基体的连续性, 造成钢的组织不
均匀, 而且它们的几何形状、 化学成分、 物理因素等 不仅使钢的冷热加工性能和某些理化指标恶化, 而
取得了一定的效果。
另外, 在钢液凝固过程中, 低熔点的 FSFO e,e 等由于钢液“ 选分结晶”最后在晶粒边界及树枝晶 ,
间析出i 3 ] 32 外来夹杂 .
这类夹杂主要是由原料带人泥沙、 熔渣及保护 渣等卷人或浇注系统的耐火材料受钢水冲刷、 浸蚀 等进人钢液中并滞留于钢中造成的, 多为大颗粒夹
题。
脱氧工艺二: 包钢引进先进的连铸设备后,98 19 年开始采用 连 铸坯生产重轨, 先进的炉外精炼装备给钢水的净
- 1、下载文档前请自行甄别文档内容的完整性,平台不提供额外的编辑、内容补充、找答案等附加服务。
- 2、"仅部分预览"的文档,不可在线预览部分如存在完整性等问题,可反馈申请退款(可完整预览的文档不适用该条件!)。
- 3、如文档侵犯您的权益,请联系客服反馈,我们会尽快为您处理(人工客服工作时间:9:00-18:30)。
1 编号:B1(中文全文) 精炼渣系对轴承钢D类夹杂物的影响
李 铮1 胡俊辉1 徐明华1 卫建国1 郑少波2 洪 新2 (1.宝钢股份特钢分公司;2.上海大学 上海钢铁冶金重点实验室)
摘 要 研究表明降低精炼顶渣碱度可显著减轻D类氧化物、硫化物和碳氮化钛的尺寸和级别。宝山钢铁股份特殊钢分公司新发明的轴承钢精炼工艺在LF/VD条件下,采用精炼前期高碱度顶渣,精炼后期低碱度顶渣的方法,较好的解决了脱氧、脱硫与降低D类夹杂物级别,缩小D类夹杂物尺寸的矛盾。本文指出随着对轴承钢纯净度要求的提高, LF/VD精炼法的局限性日益暴露出来,新上的轴承钢生产线应考虑配备RH装置。
关键词 轴承钢 精炼工艺 精炼渣系 夹杂物
Influence of Refining Slag Composition on D Type Inclusion in Bearing Steel
Li Zheng1 Hu Junhui1 Xu Minghua1 Wei Jianguo1 Zheng Shaobo2 Hong Xin2
(1. Baoshan Iron & Steel Co., Ltd., Special Steel Branch (2. Shanghai Enhanced Laboratory of Ferrous-Metallurgy,Shanghai University)
Abstract: Key In the paper, it was shown that reducing the basicity of top slag of refining could remarkably reduce the sizes of D type inclusion, sulfide and titanium carbonitride and lower their ratings. A new refining process of bearing steel was invented by Baoshan Iron & Steel Co., Ltd. Special Steel Branch. The process, in which high basicity top slag was applied at earlier stage of refining and low basicity top slag was applied at later stage of refining, would balance deoxidization, desulphurization and lowering the rating of D type inclusion, reducing the size of D type inclusion under LF/VD condition. The author pointed out that it is better to equip RH device in the new bearing steel production line to meet stricter requirements for the cleanliness of bearing steel due to the limitation of LF/VD refining process. Words: bearing steel, refining process, refining slag, inclusion
1 前言 作用于轴承上的是呈周期性变化的压应力,其破坏形式为疲劳剥落。夹杂物特别是在轧制过程中不变形的D类夹杂物在交变应力的作用下会在其周围产生裂纹,成为疲劳剥落的起点。因此,世界各地的轴承钢工作者都将减小D类夹杂物级别、缩小D类夹杂物尺寸作为提高轴承钢纯净度的重点。 上世纪八十年代中期前,我国轴承钢的生产一直采用熔化、氧化、还原的“老三段”的操作法,D类氧化物的级别和尺寸据高不下。为此,冶金部曾组织各特钢企业,开展全国范围内的攻关,但收效甚微。八十年代后期,钢包精炼法开始用于轴承钢生产,D类氧化物显著改善。在相当长的一段时间内,冶金工作者把工作重点转向降低钢中氧含量,以减少氧化物夹杂。近年来,随着国际制造业向中国转移,世界著名的轴承企业纷纷在我国建厂,对轴 2
承钢的质量要求随着不同的国家和不同的用途日益细分并出现了国际化。 以山阳为代表的日本企业,根据用户需要,除对氧含量提出要求外,还对钢中的钛、硫含量提出了越来越高的要求,特殊用途的轴承钢要求氧含量≤7ppm,钛含量≤12ppm,硫含量≤30ppm。超纯轴承钢的氧含量甚至达到3~4ppm,同时钛含量也降低至7~8ppm。以SKF为代表的欧美企业对氧、钛含量的要求没有日本那么苛刻,但他们更重视夹杂物的尺寸、数量和性质,如要求硫含量在0.005~0.015%之间,而不是越低越好。点状定性为长/宽≤5的各类夹杂物,如硫化物、氧化物、氮碳化钛及复合夹杂物。 随着对轴承钢纯净度要求的不断提高,钢包精炼法局限性日益明显的暴露出来,主要表现在:(1)工作真空度最高只能达到66.7Pa,很难进一步提高,而RH很容易就达到13.3Pa。(2)对脱S、脱O有利的高碱度渣,在VD过程中由于渣-钢混冲,很容易造成大颗粒不变形的铝酸钙夹杂物,该夹杂物如果出现在精磨后的轴承套圈辊道上,就会出现“黑斑”缺陷,对轴承的疲劳寿命极为有害。 日本在1964年开始采用钢包精炼法生产轴承钢,但他们很快发现:在高碱度渣的混冲下,钢包精炼法效果不理想,故从1968年开始采用RH脱气法[1]。 2 在VD条件下,夹杂物与顶渣组成的关系 2.1 现阶段精炼顶渣的组成 为满足精炼过程中各种物理化学反应,精炼顶渣应具有合适的粘度,一定的碱度及还原性和稳定性。在偏心底出钢,采用留钢留渣的条件下,为了使脱氧产物有充分的上浮时间,通常在出钢时的高氧位(500~1000ppm)下将2-3Kg/T的铝加入包中,这部分的铝90%以上都会被氧化,生成Al2O3进入渣中,使顶渣稀释。为了完成脱硫和升温的任务,LF炉会加入较多的石灰,形成高铝高碱度的精炼顶渣。其Al2O3和CaO含量分别为25~30%;55~60%,顶渣碱度(CaO/SiO2)为4.0~6.0。该精炼顶渣在不换渣的条件下,很容易将S脱至≤0.008%,与此同时,95%以上的氧含量≤10ppm(上海五钢,2005年,按炉号统计)。因此,在相当大的范围内被推荐使用。 2.2 VD过程中Ca的还原 研究表明[2],在VD过程的真空条件下,轴承钢中1%的C可还原渣中的CaO,即存在如下反应:
(CaO)+[C]=[Ca]+{CO} 1G=600485-177.16T J/mol ……(1) 反应的平衡常数为:
)(][][1lnlnCaOCCOCaaa
pa
k
被还原出来的Ca与钢液中的Al和O结合会生成球状的氧化物(主要为mCaO•n Al2O3)。若Ca与钢液中的S结合,会生成变形能力差的CaS(长/宽≤5)。因此,要解决球状夹杂物的问题,最重要的是减少钢液中的Ca含量,在LF/VD的精炼条件下,在冶炼高碳铬轴承钢时,就是要降低精炼顶渣中的CaO活度。 降低炉渣中CaO活度的最有效的方法是增加炉渣中SiO2含量。顶渣中的SiO2与CaO可结合生成CaO•SiO2、2CaO•SiO2和3CaO•SiO2化合物。因此,当炉渣中CaO/SiO2>3时就会有自由CaO出现,从而大幅度提高了炉渣中CaO的活度。要减少熔渣中CaO活度,就要将熔渣中的CaO和SiO2的比例(碱度)控制在≤2.8(3CaO/ SiO2=3×56/60=2.8),最好控制在≤1.9(2CaO/ SiO2=2×56/60=1.9)的范围内。 当渣中CaO活度比较低时,精炼渣的脱硫能力就比较弱。从CaO脱硫平衡来看,钢中[S]含量很难达到目标值。
=-72226/T+21.31 ……(2) 3
(CaO)+[S]=(CaS)+[O] 91.313748ln][][2TaaaakSCaOOCaS 在采用EBT的电炉冶炼中,钢中硫的去除主要在出钢和精炼过程中完成。因此,解决球状的氧化物夹杂和脱硫就发生了矛盾。 宝钢股份特钢分公司发明了一种新的轴承钢精炼方法,采用前期高碱度后期低碱度的方法,可同时解决脱氧、脱硫和D类夹杂物问题。采用该方法生产的轴承钢氧含量≤10ppm,钛含量≤20ppm,D类夹杂物可满足SKF D33-1 Grade 3S要求。SKF专家评级结果见表1。
表1 试验炉次φ100mm熔检样高倍评级结果 Table 1 Ratings of microstructures of Ф100 mm samples taken from the billet of tested heats 评级标准 炉次 评级结果 SKF D33-1 Grade 3S要求 DIN 50602 A K4=2.18 K4≤7 DIN 50602 B K4=4.3 K4≤7 DIN 50602 C K4=4.7 K4≤7
炉号C轧成φ40mm,洛阳轴承研究所评级结果见表2。 表2 试验炉号φ40材高倍评级结果 Table 2 Ratings of microstructures of Ф40 mm samples taken from the finish product of tested heats A细 A粗 B细 B粗 C细 C粗 D细 D粗 级别 比例 级别 比例 级别 比例 级别 比例 级别 比例 级别 比例 级别 比例 级别 比例 0 3/80 0 78/80 0 77/80 0 80/80 0 80/80 0 80/80 0 44/80 0 80/80 0.5 27/80 0.5 1/80 0.5 3/80 0.5 34/80 1.0 27/80 1.0 1/80 1.0 2/80 1.5 21/80 2.0 2/80
表2说明在受检的80个视场中未出现大于8μm的D类氧化物。 2.3 D类硫化物 如前所述,高碱度顶渣在真空精炼时,渣中的自由氧化钙被钢中的碳还原使钢中的钙含量增加。在凝固过程中,部分钙与钢中的硫化锰结合生成变形能力差(长/宽≤5)的MnS•CaS复合夹杂物。若减少渣中的自由氧化钙,硫在凝固过程中将与锰结合,生成变形能力强(长/宽>5)的MnS。MnS•CaS与MnS的扫描电镜和能谱分析见图1、图2。
探针成分分析 Elem Wt % At % ---------------------------------- MgK 1.93 3.57 S K 29.25 40.24 CaK 4.41 4.85 MnK 41.53 33.34 FeK 22.87 18.06 Total 100.00 100.00