催化裂化油浆系统结焦原因及解决措施
催化裂化油浆系统结焦原因及对策
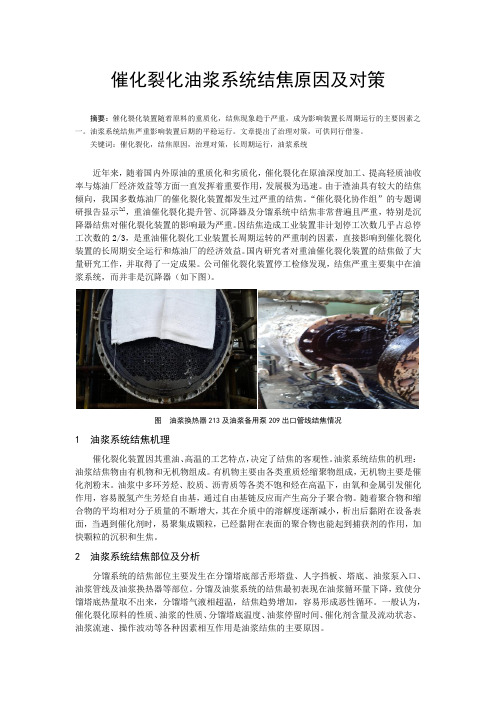
催化裂化油浆系统结焦原因及对策摘要:催化裂化装置随着原料的重质化,结焦现象趋于严重,成为影响装置长周期运行的主要因素之一。
油浆系统结焦严重影响装置后期的平稳运行。
文章提出了治理对策,可供同行借鉴。
关键词:催化裂化,结焦原因,治理对策,长周期运行,油浆系统近年来,随着国内外原油的重质化和劣质化,催化裂化在原油深度加工、提高轻质油收率与炼油厂经济效益等方面一直发挥着重要作用,发展极为迅速。
由于渣油具有较大的结焦倾向,我国多数炼油厂的催化裂化装置都发生过严重的结焦。
“催化裂化协作组”的专题调研报告显示[1],重油催化裂化提升管、沉降器及分馏系统中结焦非常普遍且严重,特别是沉降器结焦对催化裂化装置的影响最为严重。
因结焦造成工业装置非计划停工次数几乎占总停工次数的2/3,是重油催化裂化工业装置长周期运转的严重制约因素,直接影响到催化裂化装置的长周期安全运行和炼油厂的经济效益。
国内研究者对重油催化裂化装置的结焦做了大量研究工作,并取得了一定成果。
公司催化裂化装置停工检修发现,结焦严重主要集中在油浆系统,而并非是沉降器(如下图)。
图油浆换热器213及油浆备用泵209出口管线结焦情况1 油浆系统结焦机理催化裂化装置因其重油、高温的工艺特点,决定了结焦的客观性。
油浆系统结焦的机理:油浆结焦物由有机物和无机物组成。
有机物主要由各类重质烃缩聚物组成,无机物主要是催化剂粉末。
油浆中多环芳烃、胶质、沥青质等各类不饱和烃在高温下,由氧和金属引发催化作用,容易脱氢产生芳烃自由基,通过自由基链反应而产生高分子聚合物。
随着聚合物和缩合物的平均相对分子质量的不断增大,其在介质中的溶解度逐渐减小,析出后黏附在设备表面,当遇到催化剂时,易聚集成颗粒,已经黏附在表面的聚合物也能起到捕获剂的作用,加快颗粒的沉积和生焦。
2 油浆系统结焦部位及分析分馏系统的结焦部位主要发生在分馏塔底部舌形塔盘、人字挡板、塔底、油浆泵入口、油浆管线及油浆换热器等部位。
催化裂化油浆结焦原因及对策

催化裂化油浆结焦原因及对策标签:催化裂化;油浆结焦;解决对策在我国炼油厂的催化裂化过程当中,油浆系统当中产生的结焦结垢问题直接影响到了催化裂化设备的正常工作,主要是因为产生大量的结焦结垢物质,直接降低了热换器的热转化效率,同时提高了管道当中材料输送的阻力,进而造成了蜡油渣油的热转换效率降低。
系统内部产生的蒸汽量减少,同时整个反应设备在工作过程当中的能源消耗量加大,油浆当中多余的热量无法及时被排除,进而造成了整个反应系统内部的热平衡性下降,严重的情况下还直接造成油浆输送系统堵塞,进而影响到了整个生产过程的正常进行。
在最近几年发展过程当中,我国炼油厂的催化裂化原材料质量都不是非常理想,外加上在加油的催化裂化技术方面一直是难以攻克的难题。
因此,催化裂化油浆结焦和结垢的问题受到了各大化工企业的广泛关注,必须要采取相应的解决措施来解决这一问题。
1.催化裂化油浆结焦问题分析1.1温度问题的影响从催化裂化的整个反应过程中可以看出,该反应过程中会受到温度的影响,在相同的催化设备当中分馏塔的底部温度越高,那么出现的结焦现象就越明显。
针对己经产生结焦问题来讲,随着温度不断提高整个反应过程的结焦问题就更加明显,就在模拟FCC油浆的结焦单元当中所得出的结论非常明显。
1.2氧含量的影响通过模拟实验分析了FCC油浆当中产生结焦单元的具体原因,通过向试管当中通入一定量的空气或者是氧气,可以看出在不同量的空气和氧气掺入的情况下,对结焦问题的影响比较明显,其中如果空气或者氧气的参与量较大,那么结焦的问题就越严重。
由此可以看出氧气含量的多少对结焦问题的影响非常明显。
1.3固体和电效应影响通过实际的生产过程可以看出,在催化裂化反应过程当中,如果增加油浆内部的沉降器和过滤器设备之后,在产生结焦和结垢的问题上有着明显的缓解。
因此,这一现象也可以得到充分的证明,从中可以得出催化裂化反应过程中油浆当中,所存在的固体杂质对结焦问题的影响比较明显。
重油催化裂化结焦原因及改进措施

重油催化裂化结焦原因及改进措施重油催化裂化是润滑油加工工艺的一个重要环节,是提高润滑油的质量的关键技术。
在重油催化裂化过程中,结焦是一个常见的问题,会严重降低催化裂化的效率。
重油催化裂化结焦的原因,主要有三个方面:首先,催化剂受污染。
催化剂通常是复合物,容易受到空气、产品成分和其他物质的侵蚀、混入或碳化,受到污染时,催化剂性能会受到严重影响,从而导致结焦。
其次,催化剂不可逆变化。
重油催化裂化温度高,使重油催化剂发生不可逆变化,催化剂的性能也下降,从而导致结焦等问题。
最后,温度控制不当。
重油催化裂化的温度控制是很重要的,太高或太低的温度都会影响催化剂的功能,导致结焦。
为了解决重油催化裂化结焦问题,应采取一些有效的措施。
首先,科学选用催化剂。
重油催化裂化中使用的催化剂一般是催化剂复合物,应根据实际需要科学选择恰当的催化剂,降低催化剂受污染的可能性。
其次,采用稳定性好的催化剂。
重油催化裂化时,要选择温度稳定性较好的催化剂,不变性的催化剂能有效降低结焦的可能性。
再次,做好温度控制。
重油催化裂化时,温度应稳定在一定范围内,太高或太低的温度都会影响催化剂的功能,因此应做好温度控制,以保证重油催化裂化效果。
最后,改善反应条件和催化裂化技术。
采用新型催化剂和剂的组合,改善反应条件,控制反应温度和反应压力,改进催化裂化技术,进一步提高重油催化裂化的效率。
综上所述,重油催化裂化结焦的主要原因是催化剂受污染、催化剂不可逆变化以及温度控制不当。
要改善这种情况,应采取有效的措施,如科学选用催化剂、采用稳定性好的催化剂、做好温度控制、改善反应条件和催化裂化技术等。
只有真正落实这些措施,才能有效防止重油催化裂化结焦,达到质量理想。
催化裂化装置结焦原因分析及对策研究
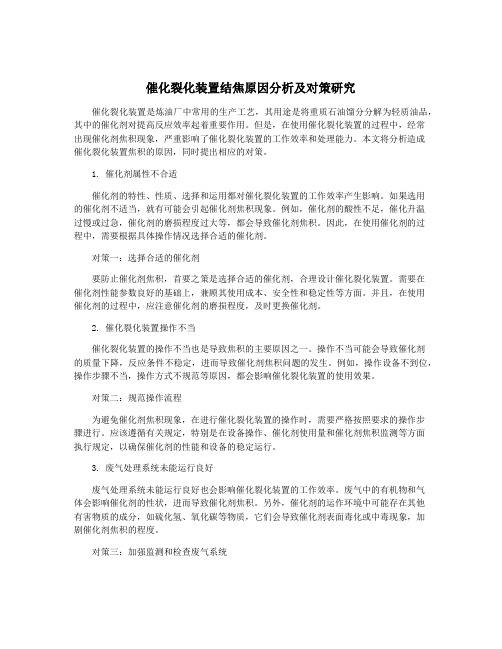
催化裂化装置结焦原因分析及对策研究催化裂化装置是炼油厂中常用的生产工艺,其用途是将重质石油馏分分解为轻质油品,其中的催化剂对提高反应效率起着重要作用。
但是,在使用催化裂化装置的过程中,经常出现催化剂焦积现象,严重影响了催化裂化装置的工作效率和处理能力。
本文将分析造成催化裂化装置焦积的原因,同时提出相应的对策。
1. 催化剂属性不合适催化剂的特性、性质、选择和运用都对催化裂化装置的工作效率产生影响。
如果选用的催化剂不适当,就有可能会引起催化剂焦积现象。
例如,催化剂的酸性不足,催化升温过慢或过急,催化剂的磨损程度过大等,都会导致催化剂焦积。
因此,在使用催化剂的过程中,需要根据具体操作情况选择合适的催化剂。
对策一:选择合适的催化剂要防止催化剂焦积,首要之策是选择合适的催化剂,合理设计催化裂化装置。
需要在催化剂性能参数良好的基础上,兼顾其使用成本、安全性和稳定性等方面。
并且,在使用催化剂的过程中,应注意催化剂的磨损程度,及时更换催化剂。
2. 催化裂化装置操作不当催化裂化装置的操作不当也是导致焦积的主要原因之一。
操作不当可能会导致催化剂的质量下降,反应条件不稳定,进而导致催化剂焦积问题的发生。
例如,操作设备不到位,操作步骤不当,操作方式不规范等原因,都会影响催化裂化装置的使用效果。
对策二:规范操作流程为避免催化剂焦积现象,在进行催化裂化装置的操作时,需要严格按照要求的操作步骤进行。
应该遵循有关规定,特别是在设备操作、催化剂使用量和催化剂焦积监测等方面执行规定,以确保催化剂的性能和设备的稳定运行。
3. 废气处理系统未能运行良好废气处理系统未能运行良好也会影响催化裂化装置的工作效率。
废气中的有机物和气体会影响催化剂的性状,进而导致催化剂焦积。
另外,催化剂的运作环境中可能存在其他有害物质的成分,如硫化氢、氧化碳等物质,它们会导致催化剂表面毒化或中毒现象,加剧催化剂焦积的程度。
对策三:加强监测和检查废气系统为避免催化剂焦积现象的发生,需要严格监测和检查废气系统,确保其正常运行。
催化裂化装置结焦原因分析及对策研究

催化裂化装置结焦原因分析及对策研究催化裂化装置是炼油厂的关键设备之一,其作用是将重质石油馏分分解成轻质产品,包括汽油、柴油和液化石油气等。
由于操作不当或设备故障等原因,催化裂化装置很容易出现结焦现象,严重影响生产效率和产品质量。
对催化裂化装置结焦原因进行分析,并制定相应的对策,对于炼油厂的稳定运行和产品质量具有重要意义。
1. 温度控制不当催化裂化装置工作温度的控制是避免结焦的关键因素之一。
如果温度过高,容易导致催化剂在装置中的积炭过多,从而引发结焦现象。
温度过低也会使催化剂在反应过程中不能充分活化,同样容易导致结焦。
保持合适的工作温度是避免结焦的重要手段。
2. 催化剂质量不良催化裂化装置中使用的催化剂质量的好坏直接影响装置的运行情况。
如果催化剂中存在杂质或者受到空气污染,会导致催化剂的活性降低,从而影响反应的进行,最终导致结焦。
3. 操作人员不当操作催化裂化装置是复杂的设备,需要操作人员具备一定的专业知识和技能。
如果操作人员不当操作,比如在设备运行时不按规定添加催化剂,或者不及时清理催化剂床中的积炭,都会加重结焦的程度。
4. 设备故障设备故障是导致催化裂化装置结焦的另一重要原因。
比如设备堵塞、管道泄漏等故障,都会导致催化剂无法正常流动或者反应不能顺利进行,最终导致结焦。
二、催化裂化装置结焦对策研究为了避免催化裂化装置结焦,首先需要严格控制工作温度。
可以通过安装温度传感器和控制系统,不断监测和调节催化裂化装置的工作温度,保证其在安全范围内稳定运行。
选择高质量的催化剂是避免催化裂化装置结焦的重要措施。
可以通过提高催化剂的制备工艺、严格控制原料质量和加强催化剂检测等手段,提高催化剂的活性和稳定性。
催化裂化装置的操作人员需要接受系统的培训,掌握装置的结构与工作原理,熟悉操作规程,了解可能影响反应的因素,提高操作技能,以减少因操作不当而导致的结焦情况。
4. 定期检查与维护为了预防催化裂化装置结焦,需要定期检查设备的运行情况,发现问题及时处理。
催化裂化油浆结垢原因及解决措施

催化裂化油浆结垢原因及解决措施1前言催化裂化装置的油浆系统设备内的结垢问题是大多数装置存在的问题。
特别是近年来,随着原料的重质化、劣质化以及加工深度的提高, 分馏塔和油浆系统结垢堵塞日益严重,造成能耗增加、装置的处理能力降低、蒸汽发生量减少、油浆多余热量无法取走,系统热平衡遭到破坏,严重影响了装置的正常操作和企业的经济效益。
结垢严重时还会造成油浆输送系统、换热系统堵塞,致使装置停车清垢,这样不仅缩短了装置的运行周期,还可能给装置的安全生产带来隐患。
由此可见,石油加工设备和管线的结垢问题已成为影响装置“安、稳、长、满、优”生产运行的一大障碍,研究能够有效防止或减轻结垢的阻垢剂已是迫在眉睫。
2 垢形成的原因及对策讨论2.1 油浆结垢原因分析2.1.1 原料结构及性质[1]催化裂化原料油日益变重,尤其是大量掺炼减压渣油以后,原料中芳烃、胶质、沥青质含量明显增加。
这就导致油浆中多环芳烃、胶质、沥青质含量增加,这些组分非常容易发生聚合产生结焦。
尤其是外甩油浆少时,加快了油浆浓缩、缩合、生焦。
2.1.2 分馏塔底温度和油浆塔底停留时间[2]分馏塔底温度和油浆在塔底停留时间过长,都会造成油浆系统结焦,使管线和冷换设备堵塞。
催化裂化一般规定塔底温度为360℃以下,但为了达到较高的轻油收率,保证经济效益,分馏塔底需维持较高的操作温度。
当油浆在高温下停留时间过长,或油浆循环量过小时,油浆中有焦生成。
2.2.3 固含量高,油浆系统介质流速低当油浆循环量小,流速低时,造成催化剂颗粒沉积在管壁和设备内部,加速结焦速度。
在低处理量情况下,提升管出口反应油气线速低,导致旋分器效率降低,反应油气携带催化剂粉尘量增加;或者,低处理量时分馏塔底油浆外甩量不足,使油浆中的催化剂颗粒大量沉积在分馏塔底,这些都造成油浆中固含量增高。
另外,由于催化剂机械强度不够,易碎裂,也是油浆中固含量大的一个原因。
2.2 减少结焦的对策2.2.1 使用阻垢剂催化剂粉末沉积问题可以用阻垢剂来控制。
催化裂解装置反应系统结焦原因分析及应对措施
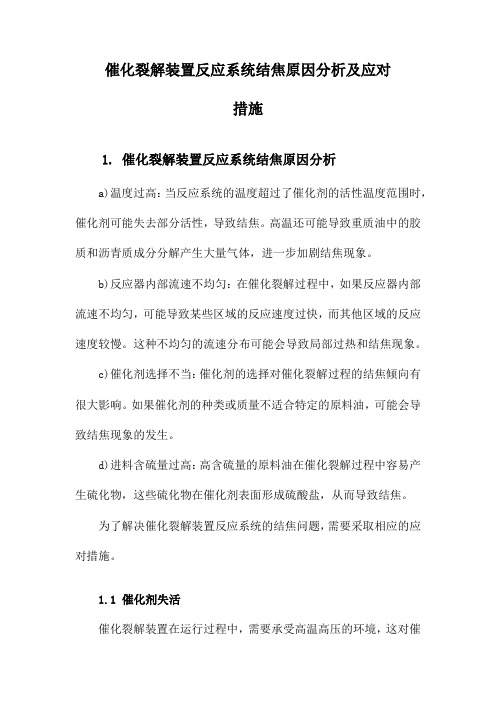
催化裂解装置反应系统结焦原因分析及应对措施1. 催化裂解装置反应系统结焦原因分析a)温度过高:当反应系统的温度超过了催化剂的活性温度范围时,催化剂可能失去部分活性,导致结焦。
高温还可能导致重质油中的胶质和沥青质成分分解产生大量气体,进一步加剧结焦现象。
b)反应器内部流速不均匀:在催化裂解过程中,如果反应器内部流速不均匀,可能导致某些区域的反应速度过快,而其他区域的反应速度较慢。
这种不均匀的流速分布可能会导致局部过热和结焦现象。
c)催化剂选择不当:催化剂的选择对催化裂解过程的结焦倾向有很大影响。
如果催化剂的种类或质量不适合特定的原料油,可能会导致结焦现象的发生。
d)进料含硫量过高:高含硫量的原料油在催化裂解过程中容易产生硫化物,这些硫化物在催化剂表面形成硫酸盐,从而导致结焦。
为了解决催化裂解装置反应系统的结焦问题,需要采取相应的应对措施。
1.1 催化剂失活催化裂解装置在运行过程中,需要承受高温高压的环境,这对催化剂的活性和稳定性提出了很高的要求。
在长时间的高温高压作用下,催化剂会发生热老化、碱腐蚀等现象,导致其活性降低甚至失活。
催化裂解装置的空速是影响催化剂活性的重要参数,如果空速过快,会导致催化剂表面的气体流速过大,从而使催化剂表面积炭速度加快,进而导致结焦现象的发生。
催化裂解装置所处理的原料油品质直接影响催化剂的使用寿命和活性。
如果原料油中杂质含量过高,如硫、磷等元素含量过高,会加速催化剂的失活过程,从而导致结焦现象的发生。
催化裂解装置的操作条件对催化剂的活性有很大影响,如温度、压力、进料量等参数设置不当,都可能导致催化剂失活,进而引发结焦现象。
选择适合催化裂解工艺条件的催化剂,并对其进行优化设计,以提高其抗高温、抗高压、抗污染等性能,从而降低催化剂失活的风险。
通过调整空速参数,使催化剂表面的气体流速保持在合适的范围内,减缓催化剂表面积炭的速度,降低结焦风险。
加强对原料油的质量监控和管理,严格控制原料油中硫、磷等有害元素的含量,降低催化剂失活的可能性。
催化裂化装置结焦原因分析及对策研究

催化裂化装置结焦原因分析及对策研究1. 引言1.1 研究背景催化裂化装置是炼油厂中重要的设备之一,其主要功能是将重质烃分子通过催化剂的作用分解成轻质烃。
在装置长期运行过程中,往往会出现结焦现象,即催化剂表面会沉积焦炭,导致装置效率下降,产品质量下降,甚至影响整个装置的安全稳定运行。
结焦问题一直是炼油行业面临的重要挑战之一,其严重影响了装置的运行效率和经济效益。
目前对于催化裂化装置结焦问题的研究仍存在许多不足之处,需要进一步深入探讨。
本文旨在对催化裂化装置结焦原因进行分析,探讨结焦对装置运行、产品质量和能耗的影响,并提出可行的对策措施,以期提高装置运行效率,保证产品质量,降低能耗,为炼油企业的可持续发展提供有力支撑。
1.2 研究目的研究目的是为了深入分析催化裂化装置结焦的原因,探讨结焦对装置运行、产品质量和能耗的影响,并提出有效的对策研究,以减少结焦现象对装置生产的不利影响,提高装置运行效率和产品质量,降低能耗消耗。
通过研究,我们希望能够为催化裂化装置的优化运行和设备管理提供有益的参考,促进装置的稳定运行和经济效益的提升。
通过对结焦问题的深入探讨和对策研究,我们将为相关行业提供科学合理的解决方案,为我国石油化工行业的发展贡献力量。
【研究目的】是本文研究工作的核心内容,也是我们研究的出发点和目标所在。
2. 正文2.1 裂化装置结焦原因分析裂化装置结焦是由于多种因素共同作用而导致的问题。
主要包括以下几个方面:1. 原料质量不佳:原料中存在硫、氮等杂质或者含硫量、含金属杂质过高,会加剧结焦的风险。
2. 操作条件不当:操作温度、压力、流速等参数控制不严,会导致裂化反应不完全,产生焦碳。
3. 催化剂失活:催化剂在长时间的使用过程中会逐渐失活,失活的催化剂无法有效促进裂化反应,容易引起结焦问题。
4. 设备老化:设备长时间运行会导致管道、换热器等部件堵塞或老化,影响流体正常流动,从而促进结焦现象的发生。
要解决裂化装置结焦问题,需要从原料选取、操作控制、催化剂管理、设备维护等方面进行全面考虑和改进。
- 1、下载文档前请自行甄别文档内容的完整性,平台不提供额外的编辑、内容补充、找答案等附加服务。
- 2、"仅部分预览"的文档,不可在线预览部分如存在完整性等问题,可反馈申请退款(可完整预览的文档不适用该条件!)。
- 3、如文档侵犯您的权益,请联系客服反馈,我们会尽快为您处理(人工客服工作时间:9:00-18:30)。
汽油
( %) 481 66 48122
液化气 总液收率
( %) 191 42 191 88
( %) 851 60 851 88
备注 :反应温度 、处理量等保持不变 ;数据采用平均值 。
由表 1 可以看出 ,塔底温度的不同对产品收率无 明显影响 。
41 3 控制停留时间
蒸汽量 (t/ h)
使用前
275 31 6
使用后 241 10
从表 2 可以看出 ,当油浆注入阻垢剂后 ,换热效 果随之明显好转 ,油浆返塔温度降低 ,蒸汽量增加 。
通过采取以上措施 ,保证了装置的长周期平稳 运行 ,降低了工人的劳动强度 。避免了因油浆系统 堵塞而导致的停工抢修事件的发生 。
催化油浆结焦 、结垢是越来越普遍的现象 ,也是 一个原因较复杂的问题 。各炼厂应根据自己的实际 情况 ,分析原因 ,找出适合自身的工艺操作条件 ,以 取得较好的阻垢效果 。
41 5 添加阻垢剂
选用合适的油浆阻垢剂 ,从装置投用起连续注 入 ,防止油浆中不溶物附着在换热器的管壁 。
我厂使用的阻垢剂型号是 SF22 ,使用的效果可 以从表 2 中看出 ,表中的数据为当催化裂化油浆系 统发生结垢时 ,加入阻垢剂 ,油浆系统部分条件的变 化。
表 2 阻垢剂的使用效果
项目 油浆返塔温度 ( ℃)
多环芳烃 、胶质 、沥青质在高温下容易脱氢产生 芳烃自由基 ,后者相互结合形成分子量更大的缩合
物 ,直至焦炭 。油浆中各类不饱和烃在高温下 ,由氧 和金属引发催化作用 ,通过自由基链反应而产生高 分子聚合物 。随着聚合物和缩合物的分子量不断增 大 ,在介质中的溶解度逐渐减小 ,析出后粘附在设备 表面 ,当遇到有催化剂聚集成的颗粒 ,这些高分子的 聚合物可起到粘合剂的作用 ,使颗粒的聚集大大加 快 ,已经粘附在表面的聚合物也能起到捕获剂的作 用 ,加快颗粒的沉积 。
在分馏塔底保持较短的停留时间 ,尽量将流量 保持在油浆泵的上限 ,维持较低的分馏塔液面 ,以避 免油浆在高温情况下结焦 。分馏塔底停留时间控制 在适宜范围内 (3 —5min) 。
41 4 提高流速
为使油浆循环系统的管道和设备不结焦 ,油浆 在管道中的流速应不低于 11 5 —21 0m/ s ,在换热器 的管程内宜控制在 11 2 —21 0m/ s 。换热器的副线启 用应当慎重 ,确保油浆换热器内流速不低于 11 2 m/ s ,避免油浆在换热过程中 ,由于油温降低 ,粘度增大 而结垢 。
我们对装置采用如下措施以防止系统结焦 : ⑴油浆回炼量维持合适的量 ,不宜太低 ; ⑵油浆连续外甩 ,占日处理量的 2 % ; ⑶每班分析一次固含量 ,当固含量大于 01 6 % 时 ,适当加大外甩量 ; ⑷定 期 测 油 浆 密 度 , 控 制 油 浆 密 度 不 大 于 11 0g/ cm3 。
31 2 分馏塔底温度
分馏塔底温度是导致油浆系统结焦的直接原 因 。随着温度的升高 ,轻馏分逐渐蒸发 ,油浆浓缩 , 生焦性能增强 。同时 ,油浆中的烯烃 、多环芳烃产生 缩合反应 。当温度升高到一定值时 ,缩合反应速度 会变得很快 。
31 3 油浆的停留时间
当油浆在某一高温下停留时间足够长时 ,油浆 中将有焦炭生成 。
46
四川化工 第 8 卷 2005 年第 2 期
31 4 流速过低
当油浆在管道中的流速过低时 ,容易使缩合物 沉积在管道表面而富集 。聚集的缩合物进一步反 应 ,生成“软焦”。
4 防止油浆系统结焦的措施
41 1 降低固含量
油浆中的固体催化剂对油浆系统结焦影响很 大 。催化剂沉积在分馏塔底 ,由于催化剂的吸附作 用而减少了油浆液滴积聚的核心 ,而油浆中催化剂 固体颗粒的碰撞会加快其沉降速度 ,使催化剂颗粒 大量沉积于分馏塔底 ,在合适的条件下形成结焦 。 油浆的相对密度反映油浆的性质 ,相对密度大 ,说明 含有更多的高沸点 、大分子成份 。结焦潜质多 ,容易 造成油浆系统的结焦 ,同时也增加了回炼油浆在提 升管中的结焦 。
第 2 期 催化裂化油浆系统结焦原因及解决措施
45
催化裂化油浆系统结焦原因及解决措施
沙胜利 (河南濮阳县中原油田石油化工总厂 ,濮阳 ,457061)
摘 要 讨论了催化裂化油浆系统的结焦机理及原因 ,结合我厂实际 ,讨论了解决的方法和取得的效 果。
关键词 :催化裂化 油浆 结焦 阻垢剂
41 2 采用较低的塔底温度
降低循环油浆返塔温度 ,加大油浆返塔下部入
口量 。用急冷油浆急冷 ,既可加强对塔底的冲涮作
用 ,防止催化剂堆积在分馏塔底的缓流区而引起结
焦 ,又可使塔底油浆快速降温 ,防止油浆组分因高温
聚合生焦 。我装置是 500kt/ a 催化裂化装置 ( RFC2
CU) ,在实际操作中我装置分馏塔底的温度控制在
1 前言
催化裂化油浆系统结焦问题是普遍存在的问 题 。分馏塔底和油浆系统的结焦 、结垢会造成系统 压力降的增加 、油浆循环量的降低 ,造成能耗增加 、 取热效率低 、装置的处理能力降低 。严重时会造成 油浆系统循环中断 ,迫使装置停工清垢 。我厂油浆 系统就多次发生堵塞造成停工 。1998 年 3 月 ,油浆 系统严重堵塞 ,致使油浆上下返塔堵塞 ,装置被迫停 工抢修 。2000 年 5 月 ,由于沉降器催化剂流损 ,管 线及换热器 ,甚至油浆泵堵死 ,装置停工检修 。2002 年 5 月 ,由于油浆换热器严重堵塞 ,又一次被迫停 工 。由此可见 ,催化裂化装置油浆系统结焦问题已 成为影响装置“安 、稳 、长 、满 、优”生产运行的一大障 碍 。成为催化装置领导 、技术人员关心的问题 。通 过借鉴其他厂的经验和采用一些新技术 、新措施 ,我 厂探索出一套减少油浆系统结焦的系列措施 。这些 应用于生产实践后 ,取的了很好的效果 。
3 油浆结垢原因分析
31 1 油浆性质
油浆性质变差是油浆系统结焦的重要原因之 一 。例如 ,油浆粘度增大将影响其流动性能 。固体 含量增大会使结焦性能增强 。油浆中含有大量的多 环芳烃和一定量的高分子烯烃 ,在高温下极易发生 缩合反应 。随着催化裂化掺炼重油比的增加 ,油浆 中的多环芳烃含量增加 ,相对密度增大 ,油浆因缩合 而生焦的能力增强 。
330 ℃以下 ,效果非常好 。
有资料显示 ,降低塔底温度则可能导致部分轻
组分溶解在塔底油浆里 ,从而影响收率 。为研究塔
底温度与产品收率的关系 ,我们作了对比实验 ,结果
见表 1 。
表 1 塔底温度与产品收率的对比实验结果
时间
塔底温度 ( ℃)
03 年 3 月 10 日 345
03 年 3 月 14 日 318
2 油浆系统结垢的机理
尽管不同油浆的组成差别较大 ,但油浆中胶质 和重质烃含量普遍都高 ,这些成分在高温下都极易 生焦成垢 。
油浆结垢物由有机物和无机物组成 。有机物主 要由各类烃和缩聚物组成 。烃类有链烷烃 、单环芳 烃和多环芳烃 ; 缩聚物主要由沥青质 、高分子聚合 物 、芳烃聚合物和焦炭组成 。结垢物中的无机物主 要是催化剂粉末 。