应用LS_DYNA进行汽车正面碰撞模拟分析
基于LS-dyna的某轻卡驾驶室正面碰撞安全性能研究
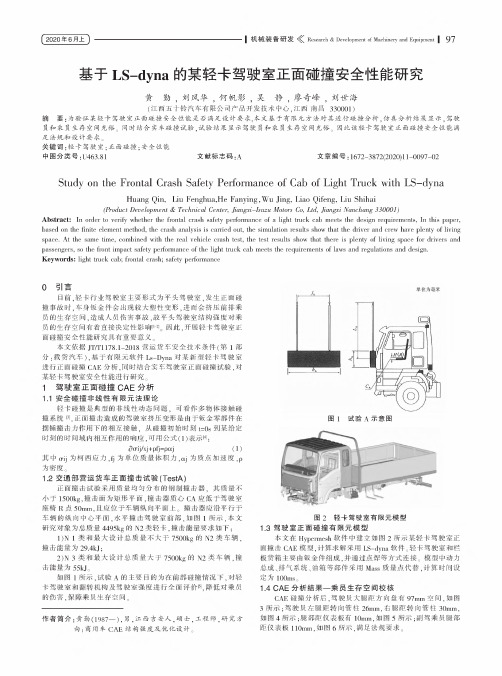
(2020年6月上)机械装备研发《Research&Development of Machinery and Equipment97基于LS-dyna的某轻卡驾驶室正面碰撞安全性能研究黄勤,刘风华,何帆影,吴静,廖奇峰,刘世海(江西五十铃汽车有限公司产品开发技术中心,江西南昌330001)摘要:为验证某轻卡驾驶室正面碰撞安全性能是否满足设计要求,本文基于有限元方法对其进行碰撞分析,仿真分析结果显示,驾驶员和乘员生存空间充裕。
同时结合实车碰撞试验,试验结果显示驾驶员和乘员生存空间充裕。
因此该轻卡驾驶室正面碰撞安全性能满足法规和设计要求。
关键词:轻卡驾驶室;正面碰撞;安全性能中图分类号:U463.81文献标志码:A文章编号:1672-3872(2020)11-0097-02Study on the Frontal Crash Safety Performance of Cab of Light Truck with LS-dyna Huang Qin,Liu Fenghua,He Fanying,Wu Jing,Liao Qifeng,Liu Shihai(Product Development&Technical Center^Jiangxi-Isuzu Motors Co,Lt%,Jiangxi Nanchang330001)Abstract:In order to verify whether the frontal crash safety performance of a light truck cab meets the design requirements,In this paper, based on the finite element method,the crash analysis is carried out,the simulation results show that the driver and crew have plenty of living space.At the same time,combined with the real vehicle crash test,the test results show that there is plenty of living space for drivers and passengers,so the front impact safety performance of the light truck cab meets the requirements of laws and regulations and design. Keywords:light truck cab;frontal crash;safety performance0引言目前,轻卡行业驾驶室主要形式为平头驾驶室,发生正面碰撞事故时,车身飯金件会岀现较大塑性变形,进而会挤压前排乘员的生存空间,造成人员伤害事故,故平头驾驶室结构强度对乘员的生存空间有着直接决定性影响因此,开展轻卡驾驶室正面碰撞安全性能研究具有重要意义。
基于LS-DYNA的汽车正面碰撞仿真分析
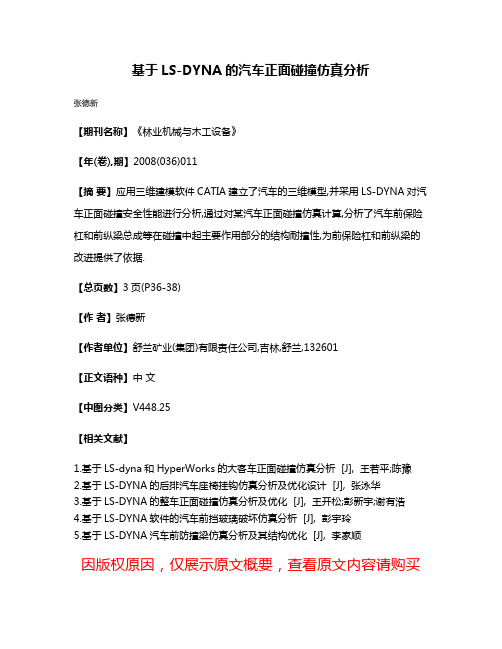
基于LS-DYNA的汽车正面碰撞仿真分析
张德新
【期刊名称】《林业机械与木工设备》
【年(卷),期】2008(036)011
【摘要】应用三维建模软件CATIA建立了汽车的三维模型,并采用LS-DYNA对汽车正面碰撞安全性能进行分析,通过对某汽车正面碰撞仿真计算,分析了汽车前保险杠和前纵梁总成等在碰撞中起主要作用部分的结构耐撞性,为前保险杠和前纵梁的改进提供了依据.
【总页数】3页(P36-38)
【作者】张德新
【作者单位】舒兰矿业(集团)有限责任公司,吉林,舒兰,132601
【正文语种】中文
【中图分类】V448.25
【相关文献】
1.基于LS-dyna和HyperWorks的大客车正面碰撞仿真分析 [J], 王若平;陈豫
2.基于LS-DYNA的后排汽车座椅挂钩仿真分析及优化设计 [J], 张泳华
3.基于LS-DYNA的整车正面碰撞仿真分析及优化 [J], 王开松;彭新宇;谢有浩
4.基于LS-DYNA软件的汽车前挡玻璃破坏仿真分析 [J], 彭宇玲
5.基于LS-DYNA汽车前防撞梁仿真分析及其结构优化 [J], 李家顺
因版权原因,仅展示原文概要,查看原文内容请购买。
纯电动汽车正面碰撞性能仿真分析与优化

Internal Combustion Engine&Parts0引言与传统汽油车相比,纯电动汽车总质量及前后轴荷分配、结构总布置及储能形式方面存在明显差异,碰撞安全性是纯电动汽车设计中关键点,也是整车性能的关键指标[1]。
近年来,为与欧美技术先进汽车接轨和实现汽车电动化战略,国家车辆碰撞安全法规对碰撞性能要求不断提高,纯电动汽车在设计研发过程中汽车被动安全性能被重点关注。
与实车碰撞试验相比,采用计算机仿真技术对整车的碰撞性能进行仿真分析,可在样车试制前完成设计优化,缩短项目开发周期和降低研发费用。
本文采用LS-DYNA和Hyper mesh软件对某纯电动汽车正面碰撞性能进行了仿真分析,从B柱峰值加速度、前门压缩量、方向盘X、Y、Z方向位移量、前围板侵入量和碰撞过程中乘员舱的完整性方面对正面碰撞性能进行评价,并对车辆进行优化分析,为纯电动汽车的车身设计提供一定的依据。
1材料与方法采用Hyper mesh软件对纯电动汽车整车的CATIA模型进行网格划分,整车模型单元数量为1146371个,节点数量为772460个,焊点连接部位采用Rigid单元模拟[2-3],整车重量为1068kg,包含前排主、副驾座椅上各75kg假人。
正面碰撞壁设置完全固定的刚性墙,碰撞速度为50km/h[4-5]。
图1为整车正面碰撞模型,图2为碰撞能量变化曲线。
图1正面碰撞模型图2能量变化曲线车辆在正面碰撞过程中,乘客受到主要伤害为承受的碰撞力过大、乘客留下的生存空间过小、承受的加速度①后处理器的阻尼很小,而且在做模态分析时,对模态频率和振型的贡献很小,所以通常将阻尼忽略,采取无阻尼假设。
不过在计算频率响应函数时,需要考虑阻尼的影响。
②原则上,当外界激振频率与结构频率相差3Hz以上时,才可以达到较好的避频效果。
本文后处理器一阶模态频率为31.4Hz,高于路面频率和点火频率,因此风险较低。
③后处理器的结构优化通常采用改进支架安装位置或者提高支架刚度的方式,增加壳体的厚度或更换材料这种方式较少采用。
汽车保险杠碰撞有限元分析

汽车保险杠碰撞有限元分析摘要:本文基于Hypermesh和LS-DYNA软件对保险杠的正面碰撞进行了仿真模拟分析,分析了保险杠的耐撞性,并以计算结果为依据, 对保险杠的结构进行了改进,优化其吸能能力,对深入研究整车正面碰撞的模拟仿真具有重要的参考价值关键词:保险杠碰撞优化Abstract: this paper, analyzed from the positive impact bumpers on the simulation ofthe Hypermesh and LS-DYNA software , this paper analyzes the bumper crashworthiness, and put the structure of bumper improved, optimize the absorption ability, and further study the collision of the vehicle positive simulation for important reference value.Keywords: bumper; collision; optimization随着轿车的大规模生产和使用, 也由于车速的不断提高, 汽车交通事故的发生率已经大大的增加了。
在汽车交通安全事故中, 出现几率最高的是汽车碰撞, 其中正面碰撞最普遍。
据资料显示,汽车发生正面碰撞的概率在40%左右。
因此, 研究正面碰撞特性, 对降低乘员的伤害非常重要[1]。
而汽车结构中的保险杠是正面碰撞时主要的承载和吸能构件,提高保险杠的吸能能力,可以降低整车碰撞中的加速度,对乘员起保护作用[2]。
因此, 对保险杠吸能特性的研究有着重要的意义。
汽车碰撞是指汽车在极短的时间内发生剧烈碰撞,是一个瞬态的复杂物理过程,它包含结构以大位移、大转动和大应变为特征的几何非线性和各种材料发生大应变时所表现的物理非线性(材料非线性)。
客车正面碰撞仿真分析及性能优化
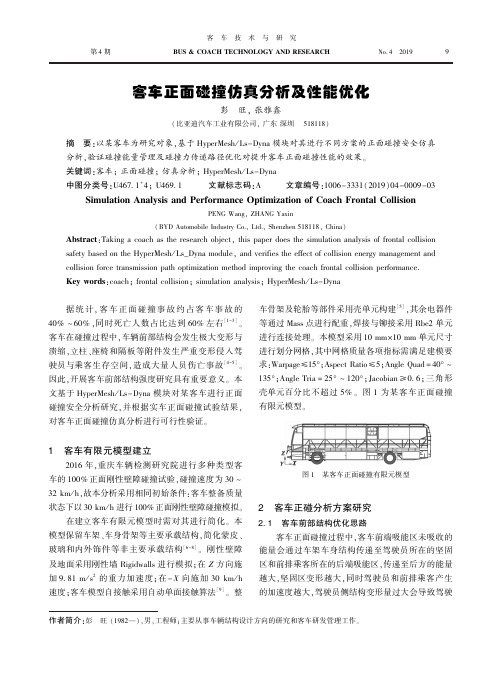
客 车 技 术 与 研 究第4期 BUS &COACH TECHNOLOGY AND RESEARCH No.4 2019作者简介:彭 旺(1982 ),男,工程师;主要从事车辆结构设计方向的研究和客车研发管理工作㊂客车正面碰撞仿真分析及性能优化彭 旺,张雅鑫(比亚迪汽车工业有限公司,广东深圳 518118)摘 要:以某客车为研究对象,基于HyperMesh /Ls-Dyna 模块对其进行不同方案的正面碰撞安全仿真分析,验证碰撞能量管理及碰撞力传递路径优化对提升客车正面碰撞性能的效果㊂关键词:客车;正面碰撞;仿真分析;HyperMesh /Ls-Dyna 中图分类号:U467.1+4;U469.1 文献标志码:A 文章编号:1006-3331(2019)04-0009-03Simulation Analysis and Performance Optimization of Coach Frontal CollisionPENG Wang,ZHANG Yaxin(BYD Automobile Industry Co.,Ltd.,Shenzhen 518118,China)Abstract :Taking a coach as the research object,this paper does the simulation analysis of frontal collision safety based on the HyperMesh /Ls_Dyna module,and verifies the effect of collision energy management and collision force transmission path optimization method improving the coach frontal collision performance.Key words :coach;frontal collision;simulation analysis;HyperMesh /Ls-Dyna 据统计,客车正面碰撞事故约占客车事故的40%~60%,同时死亡人数占比达到60%左右[1-3]㊂客车在碰撞过程中,车辆前部结构会发生极大变形与溃缩,立柱㊁座椅和隔板等附件发生严重变形侵入驾驶员与乘客生存空间,造成大量人员伤亡事故[4-5]㊂因此,开展客车前部结构强度研究具有重要意义㊂本文基于HyperMesh /Ls-Dyna 模块对某客车进行正面碰撞安全分析研究,并根据实车正面碰撞试验结果,对客车正面碰撞仿真分析进行可行性验证㊂1 客车有限元模型建立2016年,重庆车辆检测研究院进行多种类型客车的100%正面刚性壁障碰撞试验,碰撞速度为30~32km /h,故本分析采用相同初始条件:客车整备质量状态下以30km /h 进行100%正面刚性壁障碰撞模拟㊂在建立客车有限元模型时需对其进行简化㊂本模型保留车架㊁车身骨架等主要承载结构,简化蒙皮㊁玻璃和内外饰件等非主要承载结构[6-8]㊂刚性壁障及地面采用刚性墙Rigidwalls 进行模拟;在Z 方向施加9.81m /s 2的重力加速度;在-X 向施加30km /h 速度;客车模型自接触采用自动单面接触算法[9]㊂整车骨架及轮胎等部件采用壳单元构建[5],其余电器件等通过Mass 点进行配重,焊接与铆接采用Rbe2单元进行连接处理㊂本模型采用10mm×10mm 单元尺寸进行划分网格,其中网格质量各项指标需满足建模要求:Warpage≤15°;Aspect Ratio≤5;Angle Quad =40°~135°;Angle Tria =25°~120°;Jacobian ≥0.6;三角形壳单元百分比不超过5%㊂图1为某客车正面碰撞有限元模型㊂图1 某客车正面碰撞有限元模型2 客车正碰分析方案研究2.1 客车前部结构优化思路客车正面碰撞过程中,客车前端吸能区未吸收的能量会通过车架车身结构传递至驾驶员所在的坚固区和前排乘客所在的后端吸能区,传递至后方的能量越大,坚固区变形越大,同时驾驶员和前排乘客产生的加速度越大,驾驶员侧结构变形量过大会导致驾驶9区结构侵入驾驶员生存空间;加速度过大会对人员造成强烈冲击伤害;乘客门侧A 柱位置变形量过大会导致乘客门无法打开影响救援㊂故为了保证驾驶员和乘客的安全,吸能区前部结构需要尽可能多地吸收碰撞能量,所以前部结构设计非常重要[10-13]㊂前部结构分区及碰撞力传递路径如图2所示㊂图2 前部结构分区及碰撞力传递路径2.2 客车正碰分析方案为进一步研究客车前部吸能区结构对提升客车正面碰撞性能的影响,对下列3种方案进行对比分析:1)原方案,未安装吸能防撞装置㊂2)改进方案1,安装吸能防撞装置,如图3所示㊂吸能防撞装置包括防撞梁主梁㊁防撞梁连接件和吸能盒等结构,主要材料为Q345B㊂图3 吸能防撞装置方案13)改进方案2,优化吸能防撞梁结构及吸能盒布置形式㊁数量,如图4所示㊂吸能盒表面变为褶皱结构,溃缩能力增强,单个吸能盒的吸能能力提升;主梁两端变为斜面结构,通过吸能盒满足吸能装置与车架的固定,同时吸能盒数量翻倍,吸能能力也显著增长㊂图4 吸能防撞装置方案23 客车正碰仿真结果分析及验证3.1 客车正碰仿真数据读取碰撞仿真结束后对结果进行分析,读取左右两侧立柱a-c 上5点的X 向相对变形量,位置如图5所示㊂同时读取转向管柱后部位置㊁驾驶员座椅椅脚位置㊁第一排乘客处座椅椅脚位置加速度仿真值,分别定义为ACC1㊁ACC2㊁ACC3,统计X 向加速度大小并进行数据分析[12-13]㊂图5 前部结构变形量测量位置图6为客车正面碰撞仿真结果中立柱a -c 上5点间的X 向相对变形量读取数据,其中Rab_11代表立柱a 和立柱b 上1号点之间的X 向相对变形量,以此类推;表1为各方案ACC1㊁ACC2㊁ACC33点的加速度峰值仿真值读取数据㊂图6 各方案前部结构变形量对比表1 各改进方案加速度峰值与原方案对比g方案序号ACC1ACC2ACC3原方案Max 109.1109.726.8Min-122.8-134.1-16.9改进方案1Max 85.978.518.7Min -71.3-66.4-6.1改进方案2Max 65.859.630.2Min -51.2-46.4-11.93.2 客车正碰仿真数据分析原方案正碰仿真结果中,乘客门侧ab 柱间最大变形量为375mm,可能导致乘客门无法打开㊂驾驶员侧ab 柱间最大变形量为213mm,变形量会侵入驾驶员生存空间㊂驾驶员处-X 向加速度峰值为134.1g ,驾驶员受到的冲击伤害会很大㊂改进方案1正碰仿真结果中,增加吸能防撞装置后,分析结果中乘客门侧ab 柱间最大变形量减小至01客 车 技 术 与 研 究 2019年8月281mm,对比原方案下降25%,乘客门侧ab柱间最大变形量为149mm,下降30%;ACC1㊁ACC2㊁ACC33处X向加速度最大峰值分别下降41.94%㊁50.48%㊁30.22%;变形量及加速度均有改善㊂改进方案2正碰仿真结果中,优化吸能防撞装置后,分析结果中乘客门侧ab柱间最大变形量降为202 mm,对比原方案下降46%,驾驶员侧ab柱间最大变形量降为71mm,下降66%;ACC1㊁ACC2㊁ACC33处X向加速度最大峰值分别下降58.31%㊁65.40%㊁30.22%;变形量及加速度改善程度较改进方案1更加明显㊂从各方案变形量及加速度峰值对比可知,改进方案1相对原方案变形量及加速度均有改善,改进方案2较改进方案1改善量更大,说明整车前部结构的优化可以很大程度地降低驾驶员区和乘客区结构受到的影响,降低乘员伤害,提高客车正面碰撞安全性㊂3.3 仿真可行性验证图7为改进方案1试验车碰撞转向管柱后部位置㊁驾驶员座椅椅脚位置㊁第一排乘客处座椅椅脚位置加速度曲线㊂试验车吸能防撞结构与改进方案1一致㊂试验车3处加速度曲线与改进方案1仿真分析曲线趋势基本一致,试验车3处加速度峰值分别为79g㊁81g㊁16g;改进方案1仿真分析3处加速度峰值分别为85.9g㊁78.5g㊁18.7g㊂通过加速度数据对比可以看出,改进方案1的加速度峰值与试验车偏差分别为13.3%㊁3%㊁16.9%,具有较高一致性;同时分析改进方案1能量曲线可知,滑移能㊁沙漏能均满足标准,初始总能与结束总能能量变化小于2%,故认为该正面碰撞仿真分析方法合理可行㊂图7 试验车各位置加速度曲线4 结 论通过正面碰撞仿真分析对比客车3种前部结构方案,表明优化前部吸能防撞装置能显著提升客车正面碰撞安全性,实车正面碰撞的试验结果对客车正面碰撞仿真分析的方法进行可行性验证㊂参考文献:[1]吴胜国.中日道路交通安全法规的比较研究[D].成都:四川大学,2006.[2]刘晓君.实车正面碰撞法规试验的发展趋势[J].世界汽车,1999(3):3-5.[3]王欣,颜长征.客车正面碰撞标准研究[J].交通标准化, 2011(8):6-10.[4]颜长征,王欣,赵东旭,等.客车正面碰撞乘员保护分析[J].机械研究与应用,2017,30(3):78-80.[5]孙治华.营运客车正面碰撞车身结构安全性仿真和评价[D].西安:长安大学,2011.[6]王钰栋,金磊,洪清泉,等.HyperMesh&HyperView应用技巧与高级实例[M].北京:机械工程出版社,2012:341-375.[7]谭继锦,张代胜.汽车结构有限元分析[M].北京:清华大学出版社,2009:196-200.[8]钟志华.汽车耐撞性分析的有限元法[J].汽车工程,1994 (1):1-6.[9]张胜兰,郑冬黎,郝琪,等.基于HyperWorks的结构优化设计技术[M].北京:机械工业出版社,2007:125-146. [10]胡玉梅.汽车正面碰撞设计分析技术及应用研究[D].重庆:重庆大学,2002.[11]张建,范体强,何汉桥.客车正面碰撞安全性仿真分析[J].客车技术与研究,2009,31(3):7-9. [12]胡远志,曾必强,谢书港.基于LS-DYNA和HyperWorks的汽车安全仿真与分析[M].北京:清华大学出版社, 2011:127-147.[13]王可,尹明德.客车正面碰撞仿真建模与分析[J].机械工程与自动化,2011(2):28-30.收稿日期:2019-01-2411 第4期 彭 旺,张雅鑫:客车正面碰撞仿真分析及性能优化。
汽车碰撞仿真LS-DYNA关键字

控制卡片参数说明
MS1ST:限制第一步的质量缩放,根据时间步确定质量向量一次。默认为0。
DT2MSF:决定最小时间步长的初始时间步长缩减系数,如果使用,DT2MS=-DT2MSF*△t。
DT2MSLC:在显示分析中把DT2MS指定为时间的函数,使用load-curve定义。 *CONTROL_SHELL $ WRPANG ESORT IRNXX ISTUPD THEORY 20 1 -1 0 2 全局控制壳单元参数卡片 WRPANG:最大翘曲角度,默认20度; ESORT:程序自动把退化的四边形单元处理为C0三角形单元公式; IRNXX:单元法向更新开关,该选项只对Hughe_Liu,Belytschko-Wong-Chiang,Belytschko-Tsay等公式起作用 。 (默认为-1,每次循环都重新计算单元方向)。 ISTUPD:单元厚度改变选项。该选项对所有壳单元变形有影响。 BWC MITER 2 1 PROJ
12. DATABASE_BINARY_D3DUMP 设置如下:
13. DATABASE_BINARY_D3PLOT 设置如下:
控制卡片参数设置
14. DATABASE_BINARY_D3THDT 设置如下:
15. DATABASE_BINARY_RUNRSF 设置如下:
16. DATABASE_EXTENT_BINARY 设置如下:
控制卡片参数设置
8. CONTROL_PARALLEL 并行计算控制,最大可以使用4个CPU。
9. CONTROL_SHELL
壳单元控制
10. CONTROL_TERMINATION 计算终止控制卡片,控制计算终止时间,设置如下:
控制卡片参数设置
11. CONTROL_TIMESTEP 计算时间步长相关参数
基于LS-DYNA的汽车前纵梁碰撞性能仿真研究
部 底架结 构 的大变形 来缓 和 冲击 和 吸收 冲击动 能 .
因此端 部底 架 结 构上 的前 纵 梁 的 吸能 特 性 和变 形 模式 , 将决 定着 车体在 撞击 时 的响应 。前纵 梁既 是
吸 收 汽 车 前 部 纵 向碰 撞 能 量 的 主 要 结 构 . 是 控 制 又
在 不改变 汽 车车身 结构 及造 型 的情 况 下 . 通过
di1.9 9 .s. 0 — 4 3 0 0 2 0 o:03 6  ̄i n1 8 5 8 . 1. . 5 s 0 2 00
基于 L — Y A的汽 车前纵梁碰撞 S D N 性 能仿 真 研 究
高 伟 .黎 权 波
( 北汽车工业学院 汽车工程系 , 北 十堰 420 ) 湖 湖 4 0 2
汽 车发 生 正 面碰 撞 时 . 主要 是 由车 身前 部 “ 压 溃 区” 塑性 变形 来 吸收 碰 撞 动能 . 且 主 要是 端 的 并
件…。 以加强 对前纵 梁 的变形 和 吸能特 性 的研 究 所
是 建 立 性模 型 的基础 _ 2 ]
改进 汽 车前纵 梁结 构 .使其 具有 较好 的碰撞 性能 .
是 保 证 汽 车 具 有 良好 正 面 碰 撞 性 能 的 重 要 手 段 和
碰撞 能 量在 汽 车 中 的分布 情 况 的 主要 装 置 据研 究 . 计 良好 的汽车前 纵梁 在正 碰时 吸收 的能量 能 设 达 到总 吸收 能量 的 5 %以上 .是 最 重 要 的吸 能元 0
Ab t a t:Th r n r s f t r n alf r Ch n a nia s smu a e y Hy e Me h a d sr c e fo t c a h o he fo tr i o a g’ n mi c rwa i l td b p r s n LS—DYNA o t r .Th r n a lsr t r s o tmie n h a a ii fa s r i g e e g f sf wa e e fo tr i tucu e wa p i z d a d t e c p b lt o b o b n n r y o y t e r n r i e o e n at r mp o e n wa c mp r d.Th smu a in e ul s o h fo t al f r a d fe i r v me t b s o ae e i l to r s t h w t t h s ha t e c a h rhi e s f t e mp o e fo t r i s n a e .I p o i e c ran ee e c s o f rh r r s wo t n s o h i r v d r n al e h nc d t r v d s e t i r f r n e f r u e i t i r vn h r s wo t i s ft e c r mp o i g t e c a h rh ne s o h a . Ke r s:fo tr i;c a h;smu ai n y wo d r n a l r s i l to
汽车碰撞分析LS_DYNA控制卡片设置
控制卡片参数说明
*CONTROL_TIMESTEP(时间步长控制卡片) $ DTINIT TSSFAC ISDO TSLIMT DT2MS LCTM ERODE MSIST 0.0 0.9 2 0.0 -0.001 0 1 1 $ DT2MSF DT2MSLC 计算所需时间步长时,要检查所有的单元。出于稳定性原因,用0.9(缺省)来 减小时间步:Δt = 0.9 l/c ,特征长度l,和波的传播速度c,都与单元的类型有关。 DTINIT:初始时间步长,如为0.0,由DYNA自行决定初始步长; TSSFAC:时间步长缩放系数,用于确定新的时间步长。默认为0.9,当计算不稳定时,可以减小该值,但同时 增加计算时间; ISDO:计算4节点壳单元时间步长的(不同的值对应特征长度的不同算法,推荐使用2,因为此选项可以获得 最大的时间步长,但有三角形单元存在时会导致计算不稳定); TSLIMT:壳单元最小时间步分配 ,使单元的时间步长控制在最小时间步长之上;只适用于使用 *mat_plastic_kinematic,*mat_power_law_plasticity*mat_strain_rate_dependent_plasticity,*mat_piecewise_linear_pla sticity等材料模型的壳单元,不建议使用该选项,因为使用DT2MS选项更好。 DT2MS:因质量缩放计算得到的时间步长。当设置为一个负值时,初始时间将不会小于TSSFAC*|DT2MS|。质 量只是增加到时间步小于TSSAFC*|DT2MS|的单元上。当质量缩放可接受时,推荐用这种方法。用这种方法时 质量增加是有限的,过多的增加质量会导致计算终止。当设置为正值时,初始时间步长不会小于DT2MS。单 元质量会增件或者减小以保证每一个单元的时间步都一样。这种方法尽管不会因为过多增加质量而导致计算终 止,但更难以作出合理的解释。默认为0.0,不进行质量缩放; LCTM:限制最大时间步长的Load-curve,该曲线定义最大允许时间步长和时间的关系(可选择) ; ERODE:当计算时间步长小于TSMIN(最小时间步长)时体单元和t-shell被自动删除。
基于LSDYNA的汽车正碰分析
中图分类号:U467.1+4
0前言
在汽车被动安全性研究中,汽车碰撞是一个 十分复杂的力学问题,它是一个动态的大位移和 大变形的瞬态接触过程。接触和高速冲击载荷影 响碰撞的全过程,碰撞系统具有大位移、大转动 和大应变的非线性特征,以材料弹塑性变形为典 型特征的材料非线性和以接触摩擦为特征的接 触非线性的多重非线性特点。这些非线性物理陛 能的综合,使得利用传统的手段对汽车碰撞过程 的精确描述和求解变得非常复杂和困难。文中进 行的是汽车100%ODB正面碰撞的仿真分析。采 用动态显式非线性有限元技术,利用NX、ANSA、 LS.DYNA等有限元软件对某汽车进行几何建 模、网格建模和计算求解,依据计算结果分析了 汽车正面主要结构在碰撞中的耐撞性,并将计算 结果与试验结果进行对比,以验证仿真模型的准 确性。
1碰撞模型的建立
1.1汽车几何模型 建立汽车整车几何模型是进行有限元分析
的第一步,模型质量的好环对后续的有限元分析
·34·
文献标识码:A
起着至关重要的作用,直接决定有限元模型网格 的质量和分析时间的长短以及分析进展是否顺 利,尤其在碰撞分析中尤为突出。另外,在保证模 型正确及几何元素相关联的基础上,可以进行简 化,以达到事半功倍的效果。文中利用NX软件建 立某汽车整车的几何模型,该汽车三维几何模型 如图1所示。
[2]陈海树,赖征海,邸建卫.Ls—DYNA在汽车碰撞模拟过程 中的应用[J].沈阳大学学报,2006.
[3]何涛,杨竞.ANSYS/LS—DYNA非线性有限元分析实例指 导教程[M].机械工业出版社.
[4]张金换,杜汇良,马春生.汽车碰撞安全性设计[M].清华 大学出版社.
[5]Oaryl L.Logan.有限元方法基础教程[M].北京电子工业 出版社.
汽车碰撞精确分析LSDYNA控制卡片设置
THKCHG:在单面接触时考虑壳厚度的改变(默认时不考虑)。
ORIEN:在初始化时可选择性的对接触面部分自动再定位。
控制卡片参数说明
ENMASS:接触单元被腐蚀的质量处理。0-节点被移除,1-体单元节点被保留,2-体单元壳单元节点被保留。 USRSTR:每个接触面分配的存储空间,针对用户提供的接触控制子程序。 USRFRC:每个接触面分配的存储空间,针对用户提供的接触摩擦子程序。 NSBCS:接触搜寻的循环数(使用三维Bucket分类搜索),推荐使用默认项。 INTERM:间歇搜寻主面和从面接触次数。 XPENE:接触面穿透检查最大乘数,默认4.0。 SSTHK:在单面接触中是否使用真实壳单元厚度,默认0,不使用真实厚度。 ECDT:时间步长内忽略腐蚀接触。
16. DATABASE_BINARY_RUNRSF 设置如下:
控制卡片参数设置
17. DATABASE_BINARY_RUNRSF 设置如下:
控制卡片参数说明
*CONTROL_TERMINATION
$ ENDTIM ENDCYC DTMIN ENDENG ENDMAS
150
0
0.0
0.0
0.0
SLSFAC:滑动接触惩罚系数 ,默认为0.1。当发现穿透量过大时,可以调整该参数;
RWPNAL: 刚体作用于固定刚性墙时,刚性墙罚函数因子系数,为0.0时,不考虑刚体与刚性墙的作用,>0时, 刚体作用于固定的刚性墙,建议选择1.0;
ISLCHK:接触面初始穿透检查,为0或1(默认)时,不检查。为2时,检查。
后面将逐一介绍碰撞分析中经常用到的控制卡片,并对每个卡片的作 用进行说明。
控制卡片使用规则
卡片相应的使用规则如下:
- 1、下载文档前请自行甄别文档内容的完整性,平台不提供额外的编辑、内容补充、找答案等附加服务。
- 2、"仅部分预览"的文档,不可在线预览部分如存在完整性等问题,可反馈申请退款(可完整预览的文档不适用该条件!)。
- 3、如文档侵犯您的权益,请联系客服反馈,我们会尽快为您处理(人工客服工作时间:9:00-18:30)。
173 科技创新导报 Science and Technology Innovation Herald学 术 论 坛2008 NO.07Science and Technology Innovation Herald应用LS-DYNA进行汽车正面碰撞模拟分析包宇波1 胡斌2(1.同济大学汽车学院 上海 200092; 2.中国矿业大学(北京)机电学院材料系 北京 100083)摘 要:应用LS-DYNA实现不带约束系统的整车的正面碰撞模拟,佐证了计算机模拟技术在现代汽车产品开发中的应用及其发挥的巨大作用。
关键词:LS-DYNA 汽车碰撞 车身耐撞性分析 计算机模拟中图分类号:TP3文献标识码:A文章编号:1674-098X(2008)03(a)-0173-02LS-DYNA 是世界上最著名的通用显式动力分析程序,能够模拟真实世界的各种复杂问题,特别适合求解各种二维、三维非线性结构的高速碰撞、爆炸和金属成型等非线性动力冲击问题,同时可以求解传热、流体及流固耦合问题。
在工程应用领域被广泛认可为最佳的分析软件包。
与实验的无数次对比证实了其计算的可靠性。
由J.O.Hallquist主持开发完成的DYNA程序系列被公认为是显式有限元程序的鼻祖和理论先导,是目前所有显式求解程序(包括显式板成型程序)的基础代码。
1988年 J.O.Hallquist创建LSTC公司,推出LS-DYNA程序系列,并于1997年将LS-DYNA2D、LS-DYNA3D、LS-TOPAZ2D、LS-TOPAZ3D等程序合成一个软件包,称为LS-DYNA。
LS-DYNA的最新版本2004年8月推出的970版。
LS-DYNA的发展与汽车碰撞仿真密不可分,在汽车行业中,CAE仿真分析快速增长的需求和机遇主要是受碰撞法规的驱动,如在1985-2002年之间,法规实验的要求增加了差不多20倍。
其次是从1985年以来计算机硬件、软件的迅速发展和汽车厂商对计算机资源的广泛应用。
还有就是汽车厂商由于市场竞争优势的需要,要求缩短设计周期,而物理样机价格昂贵、试验能力有限以及CPU时间价格的降低,也使得汽车行业CAE仿真分析快速增长。
现在汽车碰撞模型己经发展到上百万个单元规模,三维模型越来越精确。
计算机广泛采用 Cluster并行处理技术,大大的降低了 CPU的运算时间,现在LS-DYNA对一500000单元规模的汽车历时120ms的碰撞过程分析如果采用MPP技术,运算时间可在12h内完成。
在汽车工业中,LS-DYNA被广泛地应用于汽车设计领域。
LS-DYNA能够准确地预测出汽车的碰撞特性,以及汽车碰撞对乘客的影响。
通过使用LS-DYNA,汽车公司和他们的配件公司不需要做模型车就能够检测汽车的设计。
这样能够节省大量的金钱和时间。
1 车身模型的建立采用Altair HyperMesh软件在车身零件的CAD模型上进行有限元划分。
以10mm为网格尺寸的基准,为保证求解速度,最小单元尺寸不能小于3mm,其他如翘曲度、长宽比、梯度、雅可比等参照下表1。
按照以上规则建立的车体有限元模型大约有60万单元。
2 关键字文件LS-DYNA的记录文件为k文件,这一文件被称为关键字文件,它是LS-DYNA计算程序的输入数据文件。
该文件是一个ASCII格式的文本文件,其中包含所要分析问题的全部信息,如节点、单元信息、材料与状态方程信息以及接触、初、边值条件和载荷信息等。
这些信息都是以LS-DYNA的关键字命令(KEYWORD)的格式表达的。
支持LS-DYNA求解程序的前处理软件还有很多,比如ANSYS/LS-DYNA、FEMB、HYPERMESH、PATRAN等。
虽然各种前处理程序的建模操作方法各不相同,但是在建模完成后,都将输出一个格式统一的关键字文件以递交LS-DYNA求解器开始显式动力分析。
也就是说,无论以何种途径建模和分析,最终都是在分析之前形成一个计算程序的输入信息文件,即关键字文件。
本文使用Hypermesh软件对计算模型进行前处理设置,以下各个初值信息都在该软件中进行定义。
3 连接模拟焊点的连接在Hypermesh中1D菜单下完成,可以对具有不同焊点失效特性的焊点采用New Group的方式放在不同的组里,也可以根据不同零件位置把焊点放在不同的组里,便于以后的管理和查错。
焊点的属性在*Section Beam关键字中进行定义。
焊点的属性定义如表2。
其中定义了焊点的失效条件,即当伸张力或扭断力达到这两个数值得时候,焊点就会失效。
在整车碰撞模拟中通常十分重视对焊点的模拟,焊点的处理正确与否,将直接影响到碰撞模拟的精度。
由于在碰撞模拟中,各零部件的变形量和位移量都很大,远远大于焊点自身的变形量,因此碰撞分析与静态分析不同,对分析结果影响更大的是焊点的强度,而不是刚度,所以在碰撞模拟中,通常采用可断裂刚体约束来处理焊点。
4 材料模拟材料参数对于碰撞模拟的精度具有极其重要的意义。
根据材料的拉伸曲线定义各种材料的弹性模量、泊松比、切向模量、破坏极限、应变率参数等,材料厚度按各零件的实际厚度定义,材料密度按各零件实测的重量来调整定义,以保证整车有限元模型的重心与实车重心的一致。
表3中为定义的材料参数:对于各部件的材料定义,遵循与实物尽量一致的原则。
根据要求,钣金件通常使用钢材,车身板厚为0.8~1.2mm,加强件板厚为1.5mm。
框式底架、梁的材料也是用钢材,板厚为2~3mm。
5 碰撞接触的定义在碰撞过程中,车与刚性墙、车身的主要部件之间均会发生接触,有些零件变形后会碰到其它零件,有些零件变形后自身各部表1 网格质量控制标准表2 焊点属性定义表3 材料定义参数174科技创新导报 Science and Technology Innovation Herald2008 NO.07Science and Technology Innovation Herald学 术 论 坛分相互挤压在一块。
这些相互挤压部分之间会有力的作用,在有限元分析中通过接触来模拟它们之间的作用力关系。
尽可能将整车模型定义为AUTOMATIC接触类型,AU-TOMATIC类型的接触是比较新的接触方式,由于在汽车碰撞的过程中,很难人工判断壳单元发生接触的方向,而AUTO-MATIC接触方式主要是针对壳单元的方向问题(体单元以接触面外法线为接触方向,所以总可以产生接触),接触则在壳单元两侧都发生,所以适合各种复杂的接触行为。
对于汽车碰撞分析,一般设置一个总体单面接触(Single Surface),用于所有汽车部件可能发生的接触检测(包括部件自身的接触行为),然而总体接触有时在一些局部区域发生实效,所以需要对一些特殊局部的接触设置局部的接触类型(如安全带与假人的接触等)在Single Surface接触类型中,常用的两种总体接触方式为:*CONTACT_AUTOMATIC_SINGLE_SURFACE*CONTACT_AUTOMATIC_GENERAL其中*CONTACT_AUTOMATIC_SINGLE_SURFACE接触类型通过系列版本的改进,成为一种非常稳定和精确的接触类型,其中一个优点就是对网格划分中的尖角接触处理更好和对三角形及四面体网格的接触更稳定,推荐应用于汽车总体接触定义中。
6 模型求解通过LS-DYNA求解器计算碰撞前100ms的过程,基本上在100ms时碰撞已经结束,碰撞车辆开始回弹。
由于单元数量比较多,使得计算需要比较长的时间。
7 LS-DYNA的输出文件系统LS-DYNA的文件系统可分为输入文件和输出文件。
输入文件包含关键字文件、应力初始化文件、重启动文件、界面段文件、时间历程文件、VDA几何文件和CAL3D输入文件等。
输出文件包括模型信息文件、计算信息文件、ASCII文件、图形输出文件、时间历程文件、接触界面力文件、重启动文件等。
输出文件一般分两类:二进制文件和ASCII文件。
二进制文件由关键字*DATA-BASE BINARY OPTION控制输出,其中使用较多的有D3PLOT和D3DUMP两个二进制文件,D3PLOT文件的关键字名称为*DATABASE_BINARY_D3PLOT,D3PLOT文件主要是用来记录应力、应变、变形的情况,可以输出各种云图和动画。
D3DUMP文件用来进行重启动分析,在每一定义的时间间隔后程序自动生成系列该类型的文件:D3DUMP01,D3DUMP02,D3DUMP03……,用户可以从任何地方进行重启动分析。
ASCII文件由关键字*DATABASEOPTION控制输出,可输出的文件主要包括GLSTAT(总体统计和能量)、MATSUM(材料能量)、RCFORC(接触面反作用力)等。
GLSTAT文件可以查看系统的总体能量及沙漏能的控制问题,MATSUM可以查看每个PART的能量变化和沙漏能控制问题,RCFORC文件中可以查看每个接触界面接触力的大小和方向。
8 结果分析乘员的伤害指标是评价整车碰撞性能的重要因素,但是,它却不是唯一的因素。
研究机构将乘员舱结构的整体性或者说乘员舱的刚性作为汽车整车碰撞性能的另一个重要因素。
对于这一方面的性能,采用了特定的乘员舱的侵入量测量值作为评价指标,即前围板侵入量。
从前围板入侵曲线图(如图1所示)可以看出,在50ms时入侵值达到了最大,达到130mm。
在进行碰撞模拟的认证过程中,从车身的耐撞性来分析乘员的伤害程度,常用的指标是B柱减速度和时间的历程曲线。
原因是由于在碰撞过程中,车身至B柱以后的部分变形量较小,在B柱处获得的减速度曲线较稳定,而减速度曲线能比较综合的反映出车辆在整个碰撞过程中受到的碰撞力的变化过程,便于了解碰撞过程中一些内部的结构因素。
同时在无假人和乘员约束系统的车身耐撞性模拟分析中,也常将这一减速度作为乘员头部所承受图1 前围板入侵曲线的减速度,间接地评价对乘员的伤害程度。
从B柱的减速度曲线可以看出(如图2所示),当t=15-20ms时,汽车保险杠横梁撞上副车架前端,使汽车的减速度迅速增加到第一个高峰值,当t约=35ms时,车辆减速度达到第二个高峰值,当t约=60ms时,车辆减速度达到又一个高峰,此外,值得注意的是,在大约t=85ms时刻,B柱减速度碰撞模拟曲线又出现一个波峰,达到了365.7m/s2。
从汽车安全性设计理念的角度出发,理想的B柱减速度曲线应呈矩形波状,即减速度变化应尽可能平稳。
如果减速度变化非常大,说明车身前部的吸能设计不良,乘员头部所承受的最大减速度很大,并且有可能不仅产生二次碰撞,甚至发生三次碰撞,造成乘员在车内多次剧烈碰撞而伤亡程度加重。
9 结语有限元分析已是汽车产品开发设计链中的常规流程,没有有限元分析的设计不能进入下一个技术流程。