齿轮气体渗碳热处理工艺
渗碳钢的热处理知识点总结

一、渗碳钢的热处理工序用于制造渗碳零件的钢称为渗碳钢。
渗碳钢的主要热处理工序一般是在渗碳之后再进行淬火和低温回火。
处理后零件的心部为具有足够强度和韧性的低碳马氏体组织,表层为硬而耐磨的回火马氏体和一定量的细小碳化物组织。
有些结构零件,是在承受较强烈的冲击作用和受磨损的条件下进行工作的,例如汽车、拖拉机上的变速箱齿轮,内燃机上的凸轮、活塞销等。
根据工作条件,要求这些零件具有高的表面硬度和耐磨性,而心部则要求有较高的强度和适当的韧性,即要求工件“表硬里韧”的性能。
为了兼顾上述双重性能,可以采用低碳钢通过渗碳淬火及低温回火来达到,此时零件心部是低碳钢淬火组织,保证了高韧性和足够的强度,而表层(在一定的深度)则具有高碳量(0.85%~1.05%),经淬火后有很高的硬度(HRC>60),并可获得良好的耐磨性。
二、渗碳钢的成分特点渗碳钢的含碳量一般都很低(在 0.15%~0.25%之间),属于低碳钢,这样的碳含量保证了渗碳零件的心部具有良好的韧性和塑性。
为了提高钢的心部的强度,可在钢中加入一定数量的合金元素,如Cr、Ni、Mn、Mo、W、Ti、B等。
其中 Cr、Mn、Ni 等合金元素所起的主要作用是增加钢的淬透性,使其在淬火和低温回火后表层和心部组织得到强化。
另外,少量的Mo、W、Ti等碳化物形成元素,可形成稳定的合金碳化物,起到细化晶粒、抑制钢件在渗碳时发生过热的作用。
微量的B(0.001%~0.004%)能强烈地增加合金渗碳钢的淬透性。
渗碳钢的分类根据淬透性或强度等级的不同,合金渗碳钢分为三类。
低淬透性合金渗碳钢即低强度渗碳钢(抗拉强度≤800MPa),如15Cr、20Cr、15Mn2、20Mn2等。
这类钢淬透性低,经渗碳、淬火与低温回火后心部强度较低且强度与韧性配合较差。
主要用于制造受力较小,强度要求不高的耐磨零件,如柴油机的凸轮轴、活塞销、滑块、小齿轮等。
这类钢渗碳时心部晶粒易于长大,特别是锰钢。
渗碳工艺的原理过程及应用
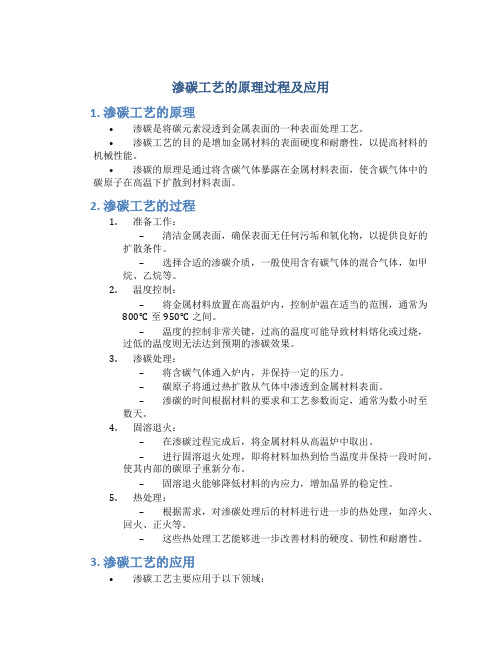
渗碳工艺的原理过程及应用1. 渗碳工艺的原理•渗碳是将碳元素浸透到金属表面的一种表面处理工艺。
•渗碳工艺的目的是增加金属材料的表面硬度和耐磨性,以提高材料的机械性能。
•渗碳的原理是通过将含碳气体暴露在金属材料表面,使含碳气体中的碳原子在高温下扩散到材料表面。
2. 渗碳工艺的过程1.准备工作:–清洁金属表面,确保表面无任何污垢和氧化物,以提供良好的扩散条件。
–选择合适的渗碳介质,一般使用含有碳气体的混合气体,如甲烷、乙烷等。
2.温度控制:–将金属材料放置在高温炉内,控制炉温在适当的范围,通常为800°C至950°C之间。
–温度的控制非常关键,过高的温度可能导致材料熔化或过烧,过低的温度则无法达到预期的渗碳效果。
3.渗碳处理:–将含碳气体通入炉内,并保持一定的压力。
–碳原子将通过热扩散从气体中渗透到金属材料表面。
–渗碳的时间根据材料的要求和工艺参数而定,通常为数小时至数天。
4.固溶退火:–在渗碳过程完成后,将金属材料从高温炉中取出。
–进行固溶退火处理,即将材料加热到恰当温度并保持一段时间,使其内部的碳原子重新分布。
–固溶退火能够降低材料的内应力,增加晶界的稳定性。
5.热处理:–根据需求,对渗碳处理后的材料进行进一步的热处理,如淬火、回火、正火等。
–这些热处理工艺能够进一步改善材料的硬度、韧性和耐磨性。
3. 渗碳工艺的应用•渗碳工艺主要应用于以下领域:1.汽车工业:–渗碳可以提高发动机零部件的硬度和耐磨性,延长零部件的使用寿命。
–例如,曲轴、凸轮轴、齿轮等关键零部件常采用渗碳工艺进行处理。
2.机械制造:–渗碳可以提高机械零部件的表面硬度,减少磨损和疲劳断裂。
–例如,齿轮、轴承、齿条等机械组件可通过渗碳工艺增加其耐磨性和使用寿命。
3.冶金行业:–渗碳可以改善冶金材料的性能,提高其硬度和耐磨性。
–例如,渗碳处理可以将普通碳钢转化为高碳钢,提高钢材的强度和硬度。
4.制造业:–渗碳工艺广泛应用于各种制造业,包括航空航天、船舶、电子、家电等行业。
20CrMnTi热处理工艺
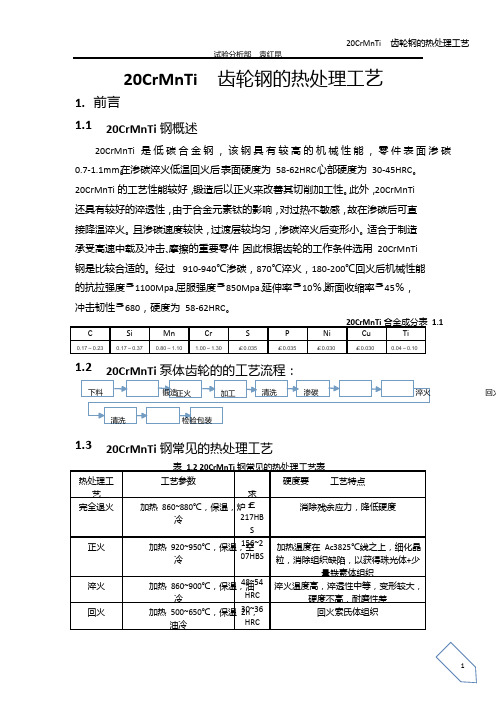
20CrMnTi 齿轮钢的热处理工艺1. 前言1.1 20CrMnTi 钢概述20CrMnTi 是低碳合金钢,该钢具有较高的机械性能,零件表面渗碳 0.7-1.1mm 。
在渗碳淬火低温回火后,表面硬度为58-62HRC ,心部硬度为30-45HRC 。
20CrMnTi 的工艺性能较好,锻造后以正火来改善其切削加工性。
此外,20CrMnTi 还具有较好的淬透性,由于合金元素钛的影响,对过热不敏感,故在渗碳后可直 接降温淬火。
且渗碳速度较快,过渡层较均匀,渗碳淬火后变形小。
适合于制造 承受高速中载及冲击、摩擦的重要零件,因此根据齿轮的工作条件选用20CrMnTi 钢是比较合适的。
经过910-940℃渗碳,870℃淬火,180-200℃回火后机械性能 的抗拉强度³1100Mpa 、屈服强度³850Mpa 、延伸率³10%、断面收缩率³45%, 冲击韧性³680,硬度为58-62HRC 。
20CrMnTi 合金成分表1.1 C Si Mn Cr S P Ni Cu Ti0.17~0.230.17~0.370.80~1.101.00~1.30£0.035£0.035£0.030£0.0300.04~0.101.2 20CrMnTi 泵体齿轮的的工艺流程:1.3 20CrMnTi 钢常见的热处理工艺表1.2 20CrMnTi 钢常见的热处理工艺表热处理工艺 工艺参数硬度要求工艺特点完全退火加热860~880℃,保温,炉 冷£217HB S消除残余应力,降低硬度正火加热920~950℃,保温,空 冷156~2 07HBS 加热温度在Ac3825℃线之上,细化晶 粒,消除组织缺陷,以获得珠光体+少 量铁素体组织淬火 加热860~900℃,保温,油 冷 48~54 HRC 淬火温度高,淬透性中等,变形较大, 硬度不高,耐磨性差回火加热500~650℃,保温2h , 油冷30~36HRC 回火索氏体组织下料 锻造 正火清洗淬火回火加工渗碳包装清洗检验气体渗碳加热900~920℃,以0.15~0.2mm/h计保温时间加热温度不超过920℃,以避免晶粒长大渗碳后淬火与回火淬火:加热820~850℃,保温后油冷60~63HRC心部保持良好韧性的同时,表层获得高的强度、硬度、耐磨性与耐蚀性回火:加热180~200℃,保温2h,空冷表:56~62HRC心:35~40HRC气体碳氮共渗共渗温度840~860℃,出炉油冷60~65HRC心部保持良好韧性的同时,表层获得高的强度、硬度、耐磨性与耐蚀性回火温度160~180℃,出炉空冷表:58~62HRC心:35~40HRC固体渗硼渗硼温度900℃,保温4h,油冷(渗硼剂:85%SiC+10%B4C+5%KBF4) 。
渗碳常用工艺
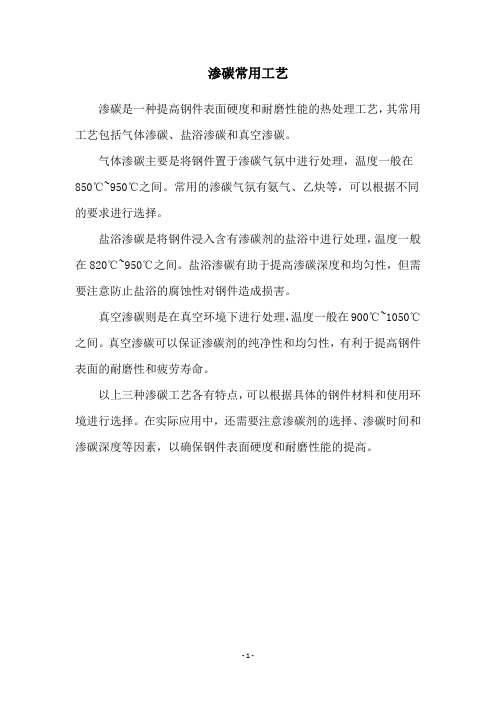
渗碳常用工艺
渗碳是一种提高钢件表面硬度和耐磨性能的热处理工艺,其常用工艺包括气体渗碳、盐浴渗碳和真空渗碳。
气体渗碳主要是将钢件置于渗碳气氛中进行处理,温度一般在850℃~950℃之间。
常用的渗碳气氛有氨气、乙炔等,可以根据不同的要求进行选择。
盐浴渗碳是将钢件浸入含有渗碳剂的盐浴中进行处理,温度一般在820℃~950℃之间。
盐浴渗碳有助于提高渗碳深度和均匀性,但需要注意防止盐浴的腐蚀性对钢件造成损害。
真空渗碳则是在真空环境下进行处理,温度一般在900℃~1050℃之间。
真空渗碳可以保证渗碳剂的纯净性和均匀性,有利于提高钢件表面的耐磨性和疲劳寿命。
以上三种渗碳工艺各有特点,可以根据具体的钢件材料和使用环境进行选择。
在实际应用中,还需要注意渗碳剂的选择、渗碳时间和渗碳深度等因素,以确保钢件表面硬度和耐磨性能的提高。
- 1 -。
渗碳热处理主要材料工艺流程

冷却与清洁
在渗碳结束后,将材料从渗碳介质中取出,进行冷却处理,并清洁表面渗碳残留物。
6
热处理
根据材料和要求,进行淬火、回火等后续热处理工艺,以获得所需的硬度和机械性能。
7
质量检测
对渗碳处理后的材料进行质量检测,包括硬度测试、金相分析等,确保达到预定标准。
8ቤተ መጻሕፍቲ ባይዱ
包装与存储
对合格的渗碳材料进行包装,并存放在干燥、通风的环境中,防止锈蚀和损坏。
渗碳热处理主要材料工艺流程
步骤序号
工艺流程
主要操作与描述
1
材料准备
选择合适的渗碳材料,如钢材、合金等,确保材料质量符合渗碳要求。
2
切割与清洗
将材料切割成所需尺寸,并进行清洗,去除表面氧化物和杂质。
3
预处理
对材料进行预加热处理,去除内部应力和水分,保证渗碳过程的有效性。
4
渗碳处理
将预处理后的材料置于渗碳介质中,控制温度和时间,使碳元素均匀渗透到材料表面层。
齿轮渗碳淬火工艺培训讲义(1)
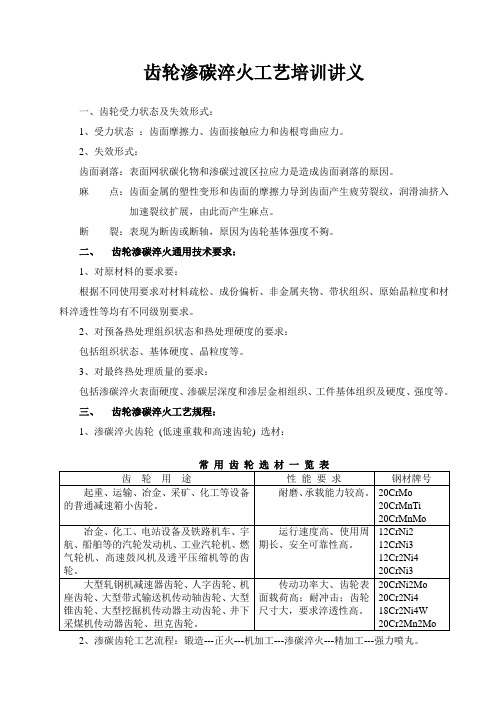
齿轮渗碳淬火工艺培训讲义一、齿轮受力状态及失效形式:1、受力状态:齿面摩擦力、齿面接触应力和齿根弯曲应力。
2、失效形式:齿面剥落:表面网状碳化物和渗碳过渡区拉应力是造成齿面剥落的原因。
麻点:齿面金属的塑性变形和齿面的摩擦力导到齿面产生疲劳裂纹,润滑油挤入加速裂纹扩展,由此而产生麻点。
断裂:表现为断齿或断轴,原因为齿轮基体强度不夠。
二、齿轮渗碳淬火通用技术要求:1、对原材料的要求要:根据不同使用要求对材料疏松、成份偏析、非金属夹物、带状组织、原始晶粒度和材料淬透性等均有不同级别要求。
2、对预备热处理组织状态和热处理硬度的要求:包括组织状态、基体硬度、晶粒度等。
3、对最终热处理质量的要求:包括渗碳淬火表面硬度、渗碳层深度和渗层金相组织、工件基体组织及硬度、强度等。
三、齿轮渗碳淬火工艺规程:1、渗碳淬火齿轮(低速重载和高速齿轮) 选材:2、渗碳齿轮工艺流程:锻造---正火---机加工---渗碳淬火---精加工---强力喷丸。
3、齿轮渗碳淬火技术要求:4、正火热处理:5、齿轮渗碳工艺:渗碳淬火工艺曲线温度时间6、使用设备: 可控气氛多用炉。
7、装炉工装及装料方式:详见附图。
(1)使用工装:工装料架应为抗渗碳、抗热疲劳、高温具有高强度的高Ni-Cr 含量材质的工装。
工装结构视工件大小、结构特征而定。
工装的结构应保证工件加热、冷却均匀,有利于减小工件淬火变形。
(2)、装料方式:一般齿轮类工件垂直挂装,套类齿轮多层碼放。
工件间应留有一定间隙,以保证不同工件和相同工件不同部位加热和冷却均匀。
滚动件均匀、薄层应平摊于料筛底部,采用多层料筛叠放装料的形式较好。
8、淬火介质及淬火冷却方式:(1)、淬火介质采用德润宝或好富顿淬火油较好。
因为这类淬火油蒸气膜持续时间短,蒸气薄且厚度均匀,奥氏体不稳定区冷速较高,有利于避免其产生非马转变;马氏体转变温度下的冷却速度较慢,有利于减小工件淬火应力和淬火变形。
(2)、淬火介质的搅拌强度和循环方向:选择强力向下搅拌为宜,但最终应根据工件淬火效果确定。
渗碳淬火热处理工艺
渗碳淬火工艺1、钢的淬火钢的淬火与回火是热办理工艺中最重要,也是用途最广泛的工为了除去淬火钢的剩余应力,淬火能够明显提升钢的强度和硬度。
序。
获取不一样强度,硬度和韧性配合的性能,需要配以不一样温度的回火。
所以淬火和回火又是不行切割的、密切连接在一同的两种热办理工艺。
淬火、回火作为各样机器部件及工、模具的最后热办理是给予钢件最后性能的重点工序,也是钢件热办理增强的重要手段之一。
淬火的定义和目的而后以大于临界冷却保温一准时间,把钢加热到奥氏体化温度,钢件淬火后获取马氏体或这类热办理操作称为淬火。
速度进行冷却,20CrNiMo 资料淬火、回火工艺。
下贝氏体组织。
图 4 为渗碳齿轮2温830℃度℃油冷200℃8 空冷时间 h资料淬火、回火工艺Mo 渗碳齿轮20CrNi 图 42淬火的目的一般有:提升工具、渗碳工件和其余高强度耐磨机器部件等的强度、硬度和耐磨性。
比如高速工具钢经过淬火回火后,硬度可达63HRC,且拥有优秀的红硬性。
渗碳工件经过淬火回火后,硬度可达58~63HRC。
构造钢经过淬火和高温回火(又称调质)以后获取优秀综协力学性能。
比如汽车半轴经淬火和高温回火(280~320HB)及外圆中频淬火后,不单提升了花键耐磨性,并且使汽车半轴蒙受扭转、曲折和冲击载荷能力(特别是疲惫强度和韧性)大为提升。
淬火时,最常用的冷却介质是水、盐水、碱水和油等。
往常碳素钢用水冷却,水价廉易得,合金钢用油来冷却,但对要求高硬度的轧辊采用盐水或碱水冷却,辊面经淬火后硬度高而均匀,但对操作要求特别严格,不然简单产生开裂。
钢的淬透性2.2.1 淬透性的基本观点所谓钢材的淬透性是指钢在淬火时获取淬硬层深度大小的能力(即钢材淬透能力),其大小用钢在必定条件下(顶端淬火法)淬火获取的有效淬硬层深度来表示,淬透性是每种钢材所固有的属性,淬硬层愈深,就表示钢的淬透性愈好,比如 45、40Cr 、42CrMo 钢三种试样,按同样条件淬火后(油冷却),经检测 45 钢能被淬透的最大直径(称临界直径)φ 10mm;40Cr 钢能被淬透的最大直径φ22mm;142CrMo 钢能被淬透的最大直径φ40mm。
简述气体的渗碳工艺
简述气体的渗碳工艺气体的渗碳工艺是一种将含有碳化物气体(如甲烷、乙烯等)引入金属材料表面,以增加表面碳含量和提高材料硬度的技术。
渗碳工艺广泛应用于机械工程、汽车工业、航空航天等领域,以提高材料的耐磨性、抗蚀性和疲劳寿命。
下面将详细介绍渗碳工艺的原理、过程和应用。
一、渗碳工艺的原理渗碳工艺的原理是通过表面碳渗透到金属材料的过程中,碳原子与材料中的铁原子形成固溶体,从而提高材料的硬度。
碳渗透的主要过程有扩散、吸附、脱碳和析出等。
渗碳过程主要分为四个阶段:表面吸附、离子扩散、脱碳和共稳定固溶体。
1. 表面吸附:气体中的碳化物通过吸附在金属表面,形成碳化膜。
碳化膜的形成是渗碳工艺的第一步,对后续的碳渗透起到了重要的作用。
2. 离子扩散:渗碳过程中,表面的碳化膜中的碳原子开始沿着金属晶界和缺陷扩散,向材料内部渗透。
离子扩散是渗碳过程的关键步骤,它决定了碳原子的扩散速率和扩散深度。
3. 脱碳:脱碳是指在碳渗透过程中,金属材料表面因为碳原子的扩散而变薄。
脱碳会导致表面硬度下降和碳含量变化,因此需要控制脱碳的程度。
4. 共稳定固溶体:当碳原子扩散到一定的深度后,就会与金属原子发生反应形成共稳定的固溶体。
共稳定固溶体的形成,使得材料的硬度得到提高,从而改善了材料的性能。
二、渗碳工艺的过程渗碳工艺的过程主要包括前处理、渗碳和后处理三个步骤。
1. 前处理:前处理主要是为了去除材料表面的氧化层和污染物,并提高材料的渗碳效果。
常见的前处理方法包括酸洗、脱脂和去氧化等。
2. 渗碳:渗碳是将含有碳化物气体的气氛引入渗碳炉中,使其与金属材料表面发生反应。
渗碳炉的温度通常在820~950之间,渗碳时间根据材料和要求而定,一般为几小时至几十小时。
渗碳炉内的气氛主要有氮气、甲烷和一氧化碳等。
3. 后处理:渗碳后,需要对材料进行处理,以去除气氛中的残余碳化物和碳化膜。
常见的后处理方法包括氢气热处理和酸洗等。
三、渗碳工艺的应用渗碳工艺广泛应用于机械工程、汽车工业、航空航天等领域,以提高材料的硬度、耐磨性和抗蚀性。
齿轮的表面热处理工艺流程
齿轮的表面热处理工艺流程下载温馨提示:该文档是我店铺精心编制而成,希望大家下载以后,能够帮助大家解决实际的问题。
文档下载后可定制随意修改,请根据实际需要进行相应的调整和使用,谢谢!并且,本店铺为大家提供各种各样类型的实用资料,如教育随笔、日记赏析、句子摘抄、古诗大全、经典美文、话题作文、工作总结、词语解析、文案摘录、其他资料等等,如想了解不同资料格式和写法,敬请关注!Download tips: This document is carefully compiled by theeditor.I hope that after you download them,they can help yousolve practical problems. The document can be customized andmodified after downloading,please adjust and use it according toactual needs, thank you!In addition, our shop provides you with various types ofpractical materials,such as educational essays, diaryappreciation,sentence excerpts,ancient poems,classic articles,topic composition,work summary,word parsing,copy excerpts,other materials and so on,want to know different data formats andwriting methods,please pay attention!齿轮的表面热处理工艺流程详解齿轮作为机械设备中的重要组成部分,其性能和寿命直接影响到整个设备的运行效率和稳定性。
热处理零件渗碳工艺
热处理零件渗碳工艺
热处理零件渗碳工艺,也称为渗碳热处理,是一种提高金属零件表面硬度和耐磨性的方法。
下面是一般的渗碳工艺流程:1. 准备工件:
- 选择适合的材料,通常为低碳钢或中碳钢。
- 切割、清洗和去除表面氧化物等处理,确保工件表面光洁干净。
2. 预处理:
- 对工件进行预加热处理,以去除内部应力和水分,一般在500~800摄氏度进行均匀加热。
- 对工件进行表面清洁和脱脂,以保证渗碳过程的有效进行。
3. 渗碳处理:
- 将准备好的工件放置在含有渗碳介质的密闭容器中,渗碳介质通常为固体、液体或气体,常用的渗碳介质有气体:一氧化碳(CO)、液体:氰化钠(NaCN)溶液、固体:繁缕石(酸性)等。
- 控制温度和时间,通常温度在800~950摄氏度之间,并保持一定的时间,以使碳元素渗透到工件的表面层中。
- 渗碳时间和温度根据工件材料和要求的硬度深度来确定,通常为几小时至数十小时。
4. 冷却和清洁:
- 在渗碳结束后,将工件从渗碳介质中取出,并进行冷却,可
以采用水冷或者油冷等方式。
- 清洁工件表面的渗碳残留物,以及附着在外表面的污垢。
5. 后处理:
- 经过渗碳处理后的工件,可以进行热处理工艺中的其他步骤,如淬火、回火等,以进一步调整工件的组织结构和性能。
需要注意的是,渗碳工艺中温度、时间和渗碳介质的选择需要根据具体的工件要求和材料特性进行确定。
此外,操作过程中需注意安全,防止渗碳介质产生有害气体对人身和环境造成危害。
因此,渗碳工艺通常在专门的热处理设备或炉中进行,且需严格遵守相关的操作规范和安全标准。
- 1、下载文档前请自行甄别文档内容的完整性,平台不提供额外的编辑、内容补充、找答案等附加服务。
- 2、"仅部分预览"的文档,不可在线预览部分如存在完整性等问题,可反馈申请退款(可完整预览的文档不适用该条件!)。
- 3、如文档侵犯您的权益,请联系客服反馈,我们会尽快为您处理(人工客服工作时间:9:00-18:30)。
我公司齿轮气体渗碳热处理工艺及其质量控制主要内容与使用范围本标准结合中国齿轮标准化技术委员会、机械工业部郑州机械研究所起草的《齿轮气体渗碳热处理工艺及其质量控制》,根据我公司齿轮材料及性能所编写的基本符合产品要求的一般规定。
本标准适用于钢制齿轮的气体渗碳、淬火和回火处理。
一、标准篇1、GB1818金属表面洛氏硬度试验方法2、GB1979结构钢低倍组织缺陷评级图3、GB3077合金结构钢技术条件4、GB5216保证淬透性结构钢技术条件5、GB6394金属平均晶粒度测定方法6、GB8539齿轮材料及热处理质量检验的一般规定7、GB9450钢件渗碳淬火有效硬化层深度的测定与校核8、GB9452热处理炉有效加热区测定方法9、GB10561钢中非金属夹杂物显微组织评定法10、GB/T230金属洛氏硬度试验方法11、GB/T13299钢的显微组织评定法12、GB/T225-88钢的末端淬透性试验方法13、ZB G51 108钢件在吸热式气氛中的热处理14、ZB J36 012 钢件在吸热式气氛中的热处理15、ZB T04 001汽车渗碳齿轮金相检验二、材料篇1、适合我公司齿轮产品的材料(见表一)(遵循我国齿轮行业车辆齿轮钢采购标准CGMA001-2004钢号淬透能力)表一2、齿轮材料的冶金质量1)化学成分合金结构钢化学成分应符合GB/T3077-88《合金结构钢技术条件》中的有关规定,保证淬透性结构钢化学成分应符合GB/5216-85《保证淬透性结构钢条件》中的有关规定。
检验标准执行GB223。
2)纯净度钢材氧含量≤20.0×10-6,含氢量为≤5.0×10-6 ,含硫量<0.015%,当有特殊要求时,按双方协议规定。
3)低倍组织一般疏松≤2级,中心疏松≤2级,偏析≤2.5级。
检验标准执行GBl979-80《结构钢低倍组织缺陷评级图》。
4)非金属夹杂物非金属夹杂物按GB/T10561-89中Ⅸ级标准检验,A≤2,B≤2,C≤1,D≤1。
氧化物<3级,硫化物<3级,氧化物+硫化物<5.5级。
检验标准执行GB/T10561-89《钢中非金属夹杂物显微评定方法》。
5)带状组织钢中带状组织≤3级。
检验标准执行GB/T13299-91《钢的显微组织评定方法》。
6)晶粒度经930℃×3h渗碳后空冷,奥氏体晶粒度≥5级。
检验标准执行GB6394-86《金属平均晶粒度测定法》。
7)末端淬透性根据齿轮具体使用要求,按淬透性带订货,同炉钢中最大离散值为4HRC。
检验标准执行GB /T225-88《钢的末端淬透性试验方法》。
三、锻件质量控制篇1、原材料的控制1)锻件用原材料(含钢锭)应有质量保证书,并符合工艺文件规定的材料牌号、尺寸规格和性能要求。
2)原材料或坯料进厂后需经材料检验部门复检,锻造用的锻材及锻坯,都必须有复检合格单。
复检合格的原材料应有复检印记,不合格料应作出明显的标记。
3)合格料、待检料、不合格料应有明显的标记,且应分区存放,严禁混料。
4)合格料的入库、出库必须有严格的管理制度。
2、锻件的检验1)工序检验①每批锻件必须进行“首检三件”制度,检验合格后方可正式投产。
生产中严格执行自检、互检和专检。
②工序检验员应对生产现场进行巡回检查,对锻件加热炉温度的控制、锻造操作情况进行监控,并定期抽检锻件的外行尺寸和表面质量。
③锻件或坯料经检验合格后,检验员应在工序卡或记录卡上签字后方可转入下道工序。
2)锻件终检①模锻件终检应按锻件图及GB12361、GB12362及合同等有关规定进行。
②自由锻锻件终检应按锻件图及JB4249、JB4385、ZB J32 003.1~003.8、ZB J32 001或合同等有关规定进行。
③在规定的锻件部位上打检验印记(挂标签)或其他标记均可。
④锻造时应使坯料整个截面得到均匀变形,锻造比按GB8539规定。
若采用封闭锻造,其流线应基本呈径向分布。
⑤锻坯不应有裂纹、折叠、过热及其他内部缺陷,也不能有最后加工无法除区的表面缺陷。
3)合格、不合格证①合格证应有检验部门按有关技术标准或合同要求填写和签发锻件合格证。
②不合格品,经检验部门检验,确认为不合格的锻件,应隔离存放,并交质保体系的不合格品处理机构进行处理。
四、热处理设备篇1、渗碳设备1)渗碳可采用连续式气体渗碳、密封箱式炉、井式气体渗碳炉等。
2)连续式气体渗碳炉及密封箱式炉应能有加热、保温、冷却等各个阶段所设定的温度下保持所需时间。
3)连续式气体渗碳炉、密封箱式炉及井式气体渗碳炉的有效加热区内的温度应控制在预定值的±10℃以内,有效加热区按GB9452的规定测试。
4)渗碳加热设备应结构合理,设有使炉内气氛均匀流动的装置,渗碳加热室应具有良好的密封性,渗碳的原料供给系统应安全可靠。
2、淬火冷却设备及冷却介质1)淬火冷却设备应具有可以控制的加热、冷却循环系统及搅拌装置。
2)淬火冷却设备应装有防火排烟装置。
3)淬火冷却介质应具有齿轮淬火所要求的冷却能力,且不易老化,其技术要求应符合有关标准。
在生产现场应有定期分析和调整的管理制度,以确保淬火质量。
3、清洗设备清洗设备应具有浸泡、喷淋、油水分离等功能。
清洗液可用碱水,其温度为60~80℃。
也可用清洗剂。
4、回火设备1)回火可采用连续式或周期式炉,其炉内有效加热区的温度应控制在预定值的±10℃以内。
2)回火设备应配有排油烟装置。
5、温度的测定及控制设备1)渗碳淬火加热炉、回火炉应配有温度测控、自动记录及报警装置,淬火冷却设备应配有温度测控装置。
2)测温仪表及热电偶应定期校检,并应符合GB9452的规定。
6、炉内气氛的测定及控制设备炉内气氛可采用CO2红外仪、氧探头、电阻丝、露点仪、定碳片通讯取气分析等方法进行测定与控制。
相关设备按各自使用说明书操作。
碳势控制精度应在±0.05%范围内。
五、热处理工艺技术篇1、渗碳前的预处理1)等温正火①能有效控制冷却时的相变,使相变在等温温度下进行,能够获得均匀一致、满足要求的显微组织及硬度,其测试部位可参照JB/T6077,硬度应均匀,硬度差值≤25HBS,同一批硬度差≤40HB S。
②粗大的奥氏体晶粒形成的平衡组织(铁素体加珠光体),在后序渗碳加热时可以重新获得细小均匀的奥氏体晶粒。
③预处理采用等温正火处理的零件,能够可靠地获得良好切削加工性能和稳定的淬火变形规律。
2)去应力处理对要求高的齿轮以及模数大于14的齿轮,齿形粗加工后应进行去应力退火处理或在600~68 0℃进行高温回火。
3)渗碳处理前的准备工作①探伤:按GB8539或行业标准,进行超声波或磁粉探伤检验②表面清理:待渗碳的齿轮及料盘均应进行清理或置于450~550℃炉内气化脱脂,除去表面油污、铁屑及其他有害杂物。
③防渗措施:按ZBG51 108规定对齿轮不需渗碳的部位,可以采用防渗涂料涂敷表面。
也可采用镀铜或预留加工余量等防渗措施。
4)随炉试样随炉试样材料应与被处理齿轮材料相同,其形状尺寸应能代表齿轮实际处理情况,根据需要可采用如下任一形式。
①仿形试样或齿形试样,应至少有3个轮齿。
齿根以下截面厚度等于齿根圆齿厚的二分之一,或根据齿轮模数选取,一般大于10mm;齿宽为齿根圆齿厚的2~3倍。
(见附录二)②渗碳层检验试样表表二③心部硬度与心部组织检验试样(见表三)表三5)随炉钢铂定碳①将一定长度30~60mm铂片用细砂把锈渍打磨干净,并用丙酮或酒精清洗干净、晾干,然后用天平测出渗碳前的重量并作记录。
将取样杆抽出,将铂片用镊子置于取样杆端部螺旋丝中,将其插入取样孔球阀外段,拧上后端螺冒,然后打开球阀将杆送入炉内,再将球阀关上少许,在炉内保持20~30分钟,渗碳结束后将取样杆抽出,为避免试样氧化应分两次进行,a、向外抽动300mm,冷却5分钟后打开球阀将端部抽到球阀外段,并关闭球阀。
b、待冷却5分钟后,才打开后端螺冒将铂片取出。
用酒精或丙酮清洗干净后,按JB/T10312-2001规定的方法,依公式计算碳势:(渗后质量-渗前质量)÷渗后质量×%+钢铂原始含碳量=炉内碳势称量一般用电子天平,保留到小数点后5位,并反复称量几次,以保证数据准确。
②随炉试样的数量根据设备类型及装炉情况确定,试样应放置在能代表齿轮热处理质量的部位,周期式渗碳炉的中检试样,可按爱协林公司标准执行。
6)渗碳原料的选用根据热处理设备的类型、渗碳原料的特性及供应状况选择①公司用可控气氛渗碳,吸热气氛原料气为天然气和液化石油气,其成分应符合ZB J36 012规定。
②渗碳原料应成分稳定、有害杂质含量低,含硫量应在0.02%以下,检验符合要求后使用。
③对于新购置的及较长时间未作渗碳使用的设备以及新夹具应进行预渗处理。
2、工艺控制1)渗碳工艺规范应严格按照爱协林公司推杆式双排连续渗碳炉的工艺规范进行生产,现场的工艺制作和控制,由专人负责调试,未经允许不得随意修改任何技术参数。
2)淬火工艺规范我司使用的爱协林设备淬火采用压淬和直淬两种工艺。
压淬保温室和直接淬火分开各走各的道,互不干涉,可实现3~4中不同规格(同一渗碳深度)的盆齿在3~4个压床上进行淬火。
直淬可执行隔盘角齿的直接淬火或其它型号盘齿的直接淬火,方便、更具有灵活性。
3)喷沙或喷丸热处理后齿轮按要求进行喷沙清理或喷丸强化3、质量控制与检验方法1)随炉试样检验①表面硬度:根据有效硬化层深度选用洛式、表面洛式等硬度计,选择方法见表四并按GB/T230或GB1818的规定检测。
表四②当图样要求测表层硬度时,用维氏硬度计在试样截面上距表面0.05~0.10mm处测定,测定方法按GB4340。
对渗碳淬火后需要磨齿的齿轮,表面硬度的测定部位应为从试样表面至轮齿单侧加工余量深度之处。
③表面硬度的均匀性要求见GB8539。
2)心部硬度心部硬度的一般要求30~45HRC,可由设计者根据齿轮使用条件规定。
①齿形试样心部硬度的测定位置参见GB8539。
②当用圆棒试样时,在试棒长度中部截取10mm厚的试样,在试样横截面中心处测定。
试样尺寸与模数关系应符合表3。
3)有效硬化层深度①对于渗碳淬火后需加工的齿轮,渗碳的工艺层深应为图样上标注的渗碳深度加上轮齿单侧的加工余量。
②有效硬化层深度的测定应以硬度法为准,测定部位按GB8539规定,测定方法按GB9450、GB4340,也可按各行业规定或生产厂与用户的协议。
③用金相法、断口法检测渗层深度时,应预先找出与硬度法测定有效硬化层深度的关系,以保证成品齿轮满足图样技术要求。
④渗碳齿轮有效硬化层深度推荐值见附录一⑤当图样要求测定齿根有效硬化层深度时,应在齿形试样的法截面上向内测定,并以其测定结果为准。
4)表层含碳量①表层含碳量为表面至0.10深度范围的平均含碳量。