浅析混凝土搅拌站轴端密封漏浆的原因与维修
混凝土中的渗漏问题与解决方案
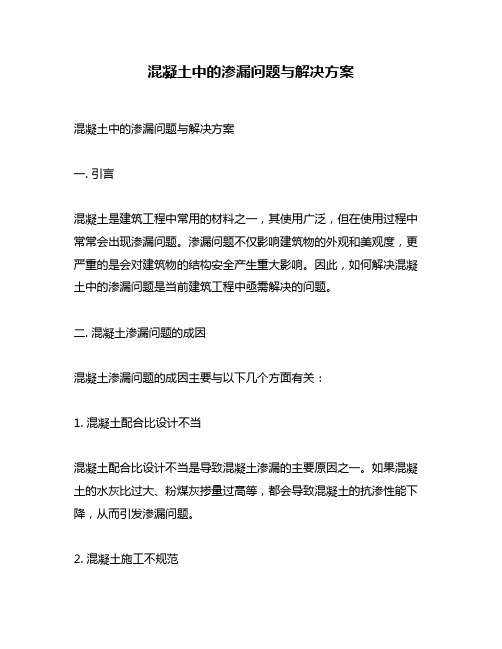
混凝土中的渗漏问题与解决方案混凝土中的渗漏问题与解决方案一. 引言混凝土是建筑工程中常用的材料之一,其使用广泛,但在使用过程中常常会出现渗漏问题。
渗漏问题不仅影响建筑物的外观和美观度,更严重的是会对建筑物的结构安全产生重大影响。
因此,如何解决混凝土中的渗漏问题是当前建筑工程中亟需解决的问题。
二. 混凝土渗漏问题的成因混凝土渗漏问题的成因主要与以下几个方面有关:1. 混凝土配合比设计不当混凝土配合比设计不当是导致混凝土渗漏的主要原因之一。
如果混凝土的水灰比过大、粉煤灰掺量过高等,都会导致混凝土的抗渗性能下降,从而引发渗漏问题。
2. 混凝土施工不规范混凝土施工不规范也是导致混凝土渗漏的原因之一。
如果混凝土施工中的细节处理不当,如混凝土浇筑不均匀、养护不到位等,都会导致混凝土的抗渗性能下降,从而引发渗漏问题。
3. 混凝土老化混凝土老化也是导致混凝土渗漏的原因之一。
混凝土在使用过程中,受到氧化、水分、化学物质等多种因素的影响,会产生龟裂、渗漏等问题。
三. 混凝土渗漏问题的表现形式混凝土渗漏问题的表现形式主要有以下几种:1. 混凝土表面渗漏混凝土表面渗漏是指混凝土外表面出现水迹、水滴等现象。
混凝土表面渗漏会影响建筑物的美观度,同时也会影响建筑物的耐久性和安全性。
2. 混凝土内部渗漏混凝土内部渗漏是指混凝土内部出现水迹、水渍等现象。
混凝土内部渗漏会直接影响建筑物的结构安全,从而对建筑物的正常使用产生重大影响。
四. 解决混凝土渗漏问题的方案针对混凝土渗漏问题,我们可以采取以下几种方案来进行解决:1. 提高混凝土的抗渗性能提高混凝土的抗渗性能是解决混凝土渗漏问题的根本措施。
可以通过调整混凝土配合比,控制水灰比和粉煤灰掺量等,从而提高混凝土的抗渗性能。
2. 加强混凝土的施工质量加强混凝土的施工质量也是解决混凝土渗漏问题的重要措施。
可以通过加强混凝土的浇筑均匀性、养护质量等,从而提高混凝土的抗渗性能。
3. 加强混凝土的维护和修补加强混凝土的维护和修补也是解决混凝土渗漏问题的有效手段。
清水混凝土漏浆处理

清水混凝土漏浆处理清水混凝土是一种常见的建筑材料,用于各种建筑工程中,例如房屋、桥梁、道路等。
然而,在施工过程中,可能会出现漏浆问题,这对于混凝土的质量和结构稳定性都会产生负面影响。
因此,清水混凝土漏浆处理是非常重要的一环。
清水混凝土漏浆是指在浇筑混凝土时,部分混凝土水分从模板或孔洞中流失,导致混凝土表面出现空鼓、裂缝等问题。
漏浆不仅会影响混凝土的强度和耐久性,还会影响建筑物的使用寿命和安全性。
因此,及时有效地处理清水混凝土漏浆问题至关重要。
为了避免清水混凝土漏浆问题的发生,施工人员应该在浇筑混凝土之前做好充分的准备工作。
这包括检查模板和孔洞的密封性,确保没有渗漏的地方。
如果发现问题,应及时修补或更换模板,以确保混凝土浇筑过程中不会出现漏浆现象。
选择合适的混凝土配比也是预防清水混凝土漏浆的重要措施之一。
合理的混凝土配比可以保证混凝土的流动性和可塑性,减少漏浆的可能性。
施工人员应根据具体工程要求和材料特性,选择适当的水灰比和掺合料,以提高混凝土的粘结性和抗渗性。
施工过程中的操作技术也对清水混凝土漏浆有着重要影响。
浇筑混凝土时,应使用适当的浇注方法和工具,确保混凝土能够充分填充模板和孔洞,减少空隙和漏浆的可能性。
同时,施工人员应掌握适当的振捣技术,以提高混凝土的密实性和均质性,避免漏浆问题的发生。
对于已经发生漏浆问题的清水混凝土,及时采取措施进行处理也是至关重要的。
一种常用的方法是使用专门的漏浆修复材料,填补漏浆部位,恢复混凝土的完整性和稳定性。
修复材料应具有良好的粘结性和耐久性,能够与原混凝土良好结合,以确保修复效果的持久性。
为了预防清水混凝土漏浆问题的再次发生,施工人员还应进行相关的质量控制和监测工作。
这包括对混凝土材料进行严格的检验和筛选,确保材料的质量符合要求;对施工过程进行严密的监测和记录,及时发现和解决漏浆问题。
只有通过全面的质量控制和监测,才能有效预防和处理清水混凝土漏浆问题。
清水混凝土漏浆处理是建筑工程中不可忽视的一环。
双端面机械密封泄漏原因及改进措施
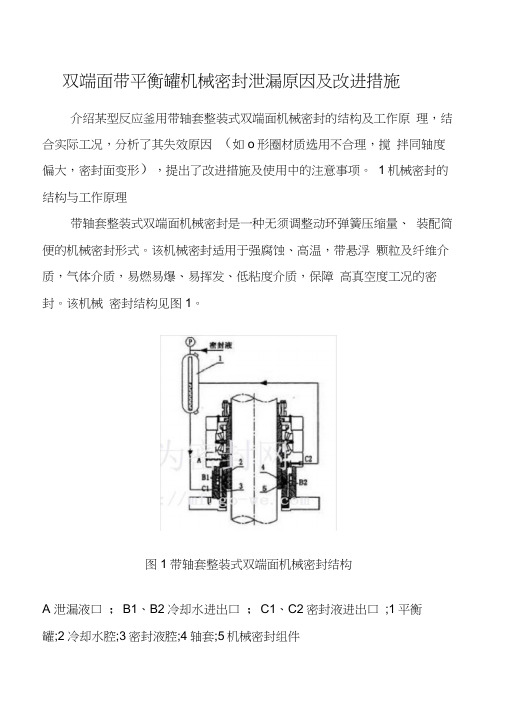
双端面带平衡罐机械密封泄漏原因及改进措施介绍某型反应釜用带轴套整装式双端面机械密封的结构及工作原理,结合实际工况,分析了其失效原因(如o形圈材质选用不合理,搅拌同轴度偏大,密封面变形),提出了改进措施及使用中的注意事项。
1机械密封的结构与工作原理带轴套整装式双端面机械密封是一种无须调整动环弹簧压缩量、装配简便的机械密封形式。
该机械密封适用于强腐蚀、高温,带悬浮颗粒及纤维介质,气体介质,易燃易爆、易挥发、低粘度介质,保障高真空度工况的密封。
该机械密封结构见图1。
图1带轴套整装式双端面机械密封结构A 泄漏液口;B1、B2冷却水进出口;C1、C2密封液进出口;1平衡罐;2冷却水腔;3密封液腔;4轴套;5机械密封组件当搅拌轴运转时,其带动机械密封轴套以及固定在机械密封轴套上的动环组件同步转动,靠动环组件和上、下静环面之间的贴合达到密封效果。
密封面一侧是密封腔室,另一侧是反应釜内环境。
在正常工作状态下,通过外部提供密封液至平衡罐,保持密封液液位在平衡罐液位计的中线,并确保平衡罐内密封液压力(即密封液腔内压力)高于釜内压力0.05〜O.IOMPa。
若密封液压力过高,贝U动、静环摩擦面易加速磨损;若密封液压力过低,则反应釜内物料易泄漏。
2故障分析2.1故障状况某反应釜均采用带轴套整装式双端面机械密封,该机械密封轴径为210mm工作转速为100r/min,工作压力为-0.5〜I.OMPa,工作温度为0〜80C,主要起密封作用的是机械密封组件,见图2。
图2机械密封组件1上静环O形圈;2上静环;3轴套;4上动环;5轴套O形圈;6动环组件;7下动环O形圈;8下动环;9下静环;10下静环O形圈动环密封面材质为SiC,静环密封面材质为井口KC-673石墨,与物料接触的下动环0形圈、上静环0形圈、轴套0形圈材质为聚四氟乙烯报复硅橡胶,其余0形圈材质均为丁腈橡胶。
该机械密圭寸的密圭寸液采用软水,釜内介质主要是聚乙烯等有机物料。
双端面机械密封泄漏原因及改进措施
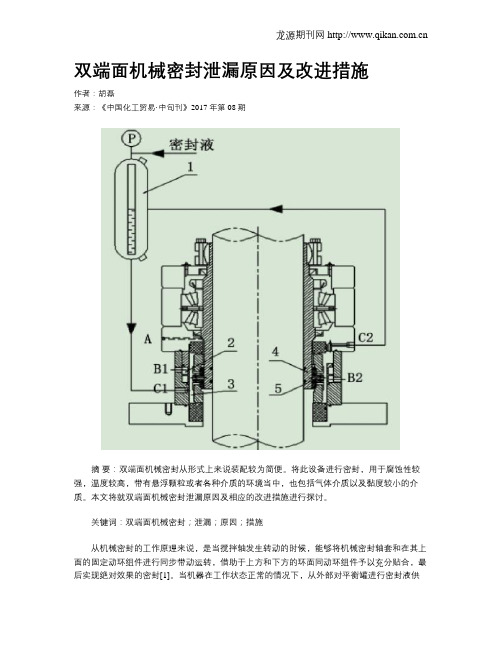
双端面机械密封泄漏原因及改进措施作者:胡磊来源:《中国化工贸易·中旬刊》2017年第08期摘要:双端面机械密封从形式上来说装配较为简便。
将此设备进行密封,用于腐蚀性较强,温度较高,带有悬浮颗粒或者各种介质的环境当中,也包括气体介质以及黏度较小的介质。
本文将就双端面机械密封泄漏原因及相应的改进措施进行探讨。
关键词:双端面机械密封;泄漏;原因;措施从机械密封的工作原理来说,是当搅拌轴发生转动的时候,能够将机械密封轴套和在其上面的固定动环组件进行同步带动运转,借助于上方和下方的环面同动环组件予以充分贴合,最后实现绝对效果的密封[1]。
当机器在工作状态正常的情况下,从外部对平衡罐进行密封液供给,然后始终让平衡罐当中的密封液处在液位的中间位置,同时使平衡罐当中的密封液的压力要比釜内的压力高出0.05到0.1兆帕中间。
因为一旦密封液的压力太大的话,那么动环摩擦面和静环摩擦面就容易发生过快的磨损,而当密封液的压力较小的话,反应釜当中的物料就会出现泄漏。
如图所示,图中1的位置为密封液缓冲罐。
1 双端面机械密封泄漏的故障表现就一台机械密封轴直径为21厘米,转速为100rpm、工作压力为-0.5到1兆帕且工位温度在0-80℃的带轴套整装双面机械密封为例。
静环密封面的材质是KC-673进口石墨,动环密封的材质是SiC,下动的O形圈采用的是聚四氟乙烯包覆硅橡胶材质,且上静环和轴套的O形圈同样采用这一材质。
剩下的O形圈选用的是丁腈橡胶。
同时选用的密封液设定为软水,以及氯乙烯一类的有机物料作为釜内的介质。
当釜内发生反应时,其中的压力会不断的增加,由最初的-0.5兆帕一直上升到1兆帕。
当处在最佳状态之下,平衡罐当中的压力应当是一直比釜内的压力高出0.05兆帕到0.1兆帕之间。
可是就现实的生产情况来说,通过操作人员手动操作调节氮气补压阀,需保证将密封液的压力设定在1.1兆帕,且这一情况始终贯穿于投料直到反应结束的整个过程[2]。
搅拌器机械密封损坏的原因及对策
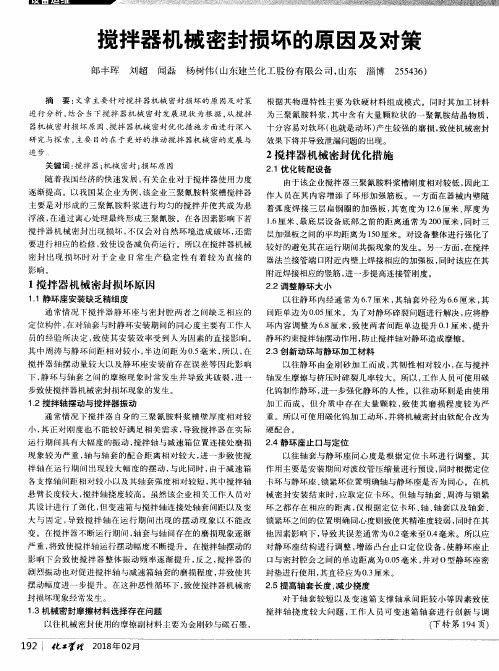
定 位构件 ,在 对轴 套与时 静环安 装期 间的 同心 度主要 有 工作人 环 内容 调整 为 6.8厘 米 ,致 使两 者 问距单 边提 升 0.1厘米 ,提升
员的 经验所 决 定 ,致 使其 安装 效率 受 到人为 因素 的直 接影 响 。 静环约 束搅拌轴摆 动作用 ,防止搅拌 轴对静环造 成摩擦 。
搅拌器机械密封损坏 的原 因及对策
郎丰珲 刘 超 闻磊 杨 树伟 (山东 建 兰化 工股 份有 限公 司 ,山东 淄博 255436)
摘 要 :文章主要针 对搅 拌 器机 械 密封损 坏的原 因及对 策 根 据其 物 理特 性主 要为 软硬 材料 组成 模式 。同时其 加 工材 料 进 行分析 ,结合 当下搅 拌 器机械 密封 发展 现 状为根 据 ,从 搅拌 为三 聚氰胺 料 浆 ,其 中含 有大量 颗粒 状 的一 聚氰 胺结 晶物 质 , 器机械 密封 损坏 原 因、搅拌 器机械 密封优 化措施 方 面进 行深入 十 分容 易对软环 (也就是 动环 )产生较 强的磨 损 ,致使机 械密 封
大 与 固定 ,导 致搅 拌 轴 在运 行 期 间 出现 的摆 动 现 象 以不 能 改 锁紧环 之 间的位置 明确 同心 度则 致使其精 准度较 弱 ,同时在其
变 。在搅拌 器不断 运行 期 间,轴套 与轴 间存在 的磨损现 象逐 渐 他 因素 影响 下 ,导致其 误差通 常为 0.2毫 米至 0.4毫 米 。所 以应
悬 臂长度较 大 ,搅拌 轴挠 度较高 。虽然 该企业 相关 工作人 员对 械 密封安 装结 束时 ,应取 定位 卡环 。但 轴 与轴 套 、周涛 与 锁 紧
其设 计进行 了强化 ,但变速 箱与搅 拌轴连 接处轴 套 间距以及 变 环之 都存 在相 应 的距离 ,仅根 据定 位卡 环 、轴 、轴 套 以及 轴套 、
混凝土离析的原因及补救方法

混凝土离析的原因及补救方法混凝土离析是指混凝土中的骨料和水泥浆体分离,形成骨料堆积和水泥砂浆流失的现象。
这种现象严重影响了混凝土的力学性能和耐久性,给工程质量和使用安全带来了严重隐患。
混凝土离析的原因复杂多样,主要包括材料选用不当、施工工艺不当、养护条件不足等因素。
本文将对混凝土离析的原因及相应的补救方法进行详细介绍。
首先,混凝土离析的原因主要包括以下几个方面:一、骨料选用不当。
混凝土中骨料的粒径、形状、含泥量等参数对混凝土的离析性能有着重要影响。
如果选用的骨料粒径差异过大,或者含泥量过高,都会导致混凝土的离析现象。
二、水灰比过大。
水灰比过大会导致混凝土的流动性增加,容易引起水泥砂浆的分离,从而造成混凝土的离析现象。
三、施工振捣不当。
在混凝土浇筑和振捣过程中,如果振捣不充分或者振捣时间过短,会导致混凝土内部气孔较多,易发生离析现象。
四、养护条件不足。
混凝土在初凝阶段需要进行充分的养护,如果养护条件不足,会导致混凝土内部水分流失过快,从而引起离析现象。
针对混凝土离析的原因,我们可以采取以下补救措施:一、合理选择骨料。
在混凝土配合比设计中,要根据工程要求和骨料的实际情况,合理选择骨料的粒径和形状,并控制其含泥量,以减少混凝土的离析风险。
二、控制水灰比。
在混凝土的配合比设计中,要合理控制水灰比,避免过大的水灰比导致混凝土的流动性增加,从而减少离析的可能性。
三、加强施工振捣。
在混凝土的浇筑和振捣过程中,要加强振捣工作,确保混凝土内部气孔减少,避免离析现象的发生。
四、加强养护管理。
在混凝土浇筑后,要加强对混凝土的养护管理,保持混凝土表面湿润,避免水分流失过快,减少混凝土的离析风险。
综上所述,混凝土离析是混凝土施工中常见的质量问题,其原因复杂多样。
通过合理选择骨料、控制水灰比、加强施工振捣和养护管理等措施,可以有效减少混凝土的离析现象,提高混凝土的力学性能和耐久性,保障工程质量和使用安全。
希望本文对混凝土离析问题的解决有所帮助。
混凝土搅拌站常见设备故障及处理方法

混凝土搅拌站常见设备故障及处理方法摘要:近年来,随着我国经济的发展与进步,建筑工程的规模越来越大,混凝土的应用也越来越普遍。
在混凝土工程施工的过程中,混凝土搅拌站发挥重要作用。
然而因为对混凝土搅拌站的管理存在疏忽,使得其在运行过程中存在较多的不确定因素。
通过在甘白路K79拌合站两年摸索过程中,总结出了混凝土搅拌站常见的设备故障及处理方法,以期确保混凝土搅拌站的长期稳定高效运行。
关键词:混凝土搅拌站;设备故障;处理方法引言在工程施工建设中,随着混凝土搅拌站技术的应用,为优化工程施工、提升工程建设进度创造了有力条件。
在混凝土搅拌站日常生产管理中,随着不同工程建设要求的差异化,对于桥梁、隧道、公路、轨道交通等工程来说,混凝土指标也越来越高。
混凝土搅拌站一旦出现机械等技术故障,将直接影响工程质量和进度。
为此,做好混凝土搅拌站日常技术故障的分析与应对措施就显得尤为重要。
1混凝土搅拌站故障检测与处理的重要性在现代建筑工程施工的过程中,需要使用大量的混凝土,混凝土的使用能够有效地提高建筑强度,延长建筑的使用寿命。
在混凝土施工的过程中,使用混凝土搅拌站来进行混凝土的搅拌能够有效地加快工程的施工进度,优化工程施工过程。
随着建筑行业的不断发展与进步,其对于混凝土的要求也越来越高,需要专业的混凝土搅拌设备进行搅拌,一旦混凝土搅拌站出现设备故障将会导致混凝土的搅拌受到影响,因此做好相应的设备故障检查与处理就显得十分重要。
2混凝土搅拌站设备运行系统(1)搅拌系统主要的组成部分有搅拌主机、润滑机构及支承架。
搅拌主机分为两种形式,主要有自落式和强制式。
在搅拌主机的组成部分中,搅拌罐是通过钢板焊接制成的,并且罐内设有耐磨衬板。
整个搅拌机械是利用电动机驱动搅拌轴的方式开展工作的。
完成混凝土的搅拌工作后,应及时将搅拌好的材料卸下。
(2)骨料供料和贮存系统的主要作用是运输并储存骨料。
骨料运输主要指的是将混凝土原材料送至贮料斗,完成计量工作后便将其放置在主机内搅拌。
混凝土出现蜂窝、麻面、漏筋等问题最全解决方案
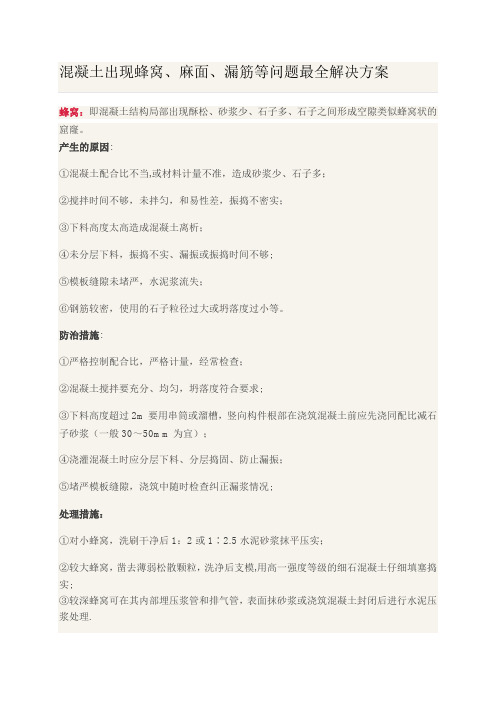
蜂窝:即混凝土结构局部出现酥松、砂浆少、石子多、石子之间形成空隙类似蜂窝状的窟窿。
产生的原因:①混凝土配合比不当,或材料计量不准,造成砂浆少、石子多;②搅拌时间不够,未拌匀,和易性差,振捣不密实;③下料高度太高造成混凝土离析;④未分层下料,振捣不实、漏振或振捣时间不够;⑤模板缝隙未堵严,水泥浆流失;⑥钢筋较密,使用的石子粒径过大或坍落度过小等。
防治措施:①严格控制配合比,严格计量,经常检查;②混凝土搅拌要充分、均匀,坍落度符合要求;③下料高度超过2m要用串筒或溜槽,竖向构件根部在浇筑混凝土前应先浇同配比减石子砂浆(一般30~50mm为宜);④浇灌混凝土时应分层下料、分层捣固、防止漏振;⑤堵严模板缝隙,浇筑中随时检查纠正漏浆情况;处理措施:①对小蜂窝,洗刷干净后1:2或1∶2.5水泥砂浆抹平压实;②较大蜂窝,凿去薄弱松散颗粒,洗净后支模,用高一强度等级的细石混凝土仔细填塞捣实;③较深蜂窝可在其内部埋压浆管和排气管,表面抹砂浆或浇筑混凝土封闭后进行水泥压浆处理.麻面:即混凝土局部表面出现缺浆和许多小凹坑、麻点,形成粗糙面,但无钢筋外露现象。
产生的原因:①模板表面粗糙或杂物未清理干净,钢模板隔离剂未刷或未刷均匀,拆模时粘坏混凝土表面;②木模板未充分湿润,构件表面混凝土的水分被吸去,使混凝土表面水分被模板吸收而失水出现麻面;③模板拼缝不严、缝隙漏浆;④模板隔离剂涂刷不匀,或漏刷或失效,混凝土表面与模板粘结造成麻面;⑤混凝土振捣不实,气泡未排出,停在模板表面,拆模后形成麻点。
防治措施:①模板表面清理干净,不得粘有水泥砂浆等杂物,浇灌混凝土前,模板应浇水充分湿润,模板缝隙,应用双面胶条等堵严;②模板隔离剂应选用长效的,并且涂刷均匀,不得漏刷;③混凝土应分层均匀振捣密实;④若出现麻面缺陷,混凝土表面作粉刷装修时,可不处理,表面无粉刷,应在麻面处浇水充分湿润后,用原混凝土配合比去石子砂浆,将麻面抹平压光.孔洞:即混凝土构件上有较大空隙、局部没有混凝土或蜂窝特别大。
- 1、下载文档前请自行甄别文档内容的完整性,平台不提供额外的编辑、内容补充、找答案等附加服务。
- 2、"仅部分预览"的文档,不可在线预览部分如存在完整性等问题,可反馈申请退款(可完整预览的文档不适用该条件!)。
- 3、如文档侵犯您的权益,请联系客服反馈,我们会尽快为您处理(人工客服工作时间:9:00-18:30)。
浅析混凝土搅拌站轴端密封漏浆的原因与维修
随着国家“十二五”期间一大批大型港口、高速铁路、高级公路、煤矿、油田电站、机场等重点工程的日益增多,同时商品混凝土的强制使用和推广,混凝土搅拌站将发挥着越来越重要的作用。
施工现场的混凝土搅拌站其电控系统中的PLC控制器、称重传感器、中间继电器和机械辅助执行机构均为多发易发故障设备,尤其是主机的轴端密封问题直接影响着混凝土搅拌站的运行性能和整机的使用寿命。
本文针对由混凝土搅拌站主机润滑系统故障造成轴端密封装置漏浆的原因与相关维修进行探讨。
中铁港航局深圳公司2008年11月购置了一台HZS75型混凝土搅拌站,现用于二广高速公路连怀5标项目部。
HZS系列混凝土搅拌站搅拌主机分为FJS和JS两大系列;该搅拌站的搅拌主机为强制式双卧轴JS1500B4型。
JS 系列的搅拌机轴端密封采用的是组合密封型式,混凝土搅拌站轴端保护层为3层,采用集中润滑油路密封,实现对支承座、搅拌轴轴头部位进行润滑、冷却和密封,以确保不侵蚀轴承支承座及搅拌轴部位不受泥浆侵蚀。
轴端密封机械结构如图一所示:
图一:JS1500B4型轴端密封装置
轴端密封的润滑采用的是手动和自动两种润滑方式。
手动润滑方式为手动泵泵入润滑油通过三通注入润滑油分配阀,再由分配阀分配到各轴端密封处。
自动润滑方式为自动泵泵入润滑油,包括机动油泵或集中润滑系统两种方式;自动泵的工作由可编程PLC控制自动工作。
该混凝土搅拌站在项目部经过一年多的使用后,混凝土搅拌站出现异响及主机搅拌轴闷车现象。
经检查发现搅拌主机在减速机一侧的轴端漏浆,衬板装置内搅拌臂的叶片磨损严重。
拆开该主机轴端密封装置发现两处密封圈及油封损坏;浮动环处被混凝土浆堵死,两处轴套也已严重磨损,该处注油的黄油嘴被混凝土浆堵死。
衬板装置内的进给叶片、返回叶片出现破裂、脱落现象,且靠近轴端处的端衬板磨损较严重。
经分析造成轴端密封装置漏浆现象的原因为无润滑油或润滑油量不足,造成油压不够导致混凝土浆渗入,堵塞润滑油道和油嘴。
从而致使搅拌主机轴端轴承运转异常、磨损;轴与轴承间摩擦加剧,使衬板装置内的搅拌臂上的叶片与衬板产生接触摩擦,出现叶片被打断,衬板开裂、磨损现象。
该HZS75型混凝土搅拌站主机采用的是集中润滑系统供油装置,其润滑油路如图二所示。
通过集中润滑系统经递进式油路分配器,或直接经管线实现对搅拌主机四个轴承密封端及支撑底座的润滑、冷却。
图二:轴端润滑系统
搅拌主机发生轴端漏浆及叶片磨损的根本原因在于搅拌站主机集中润滑系统发生故障。
通过对该主机集中润滑系统的检查发现:
1.润滑系统主油泵转动轴出现磨损现象
2.润滑系统主油泵压力表接口的柱塞无法正常工作
3.润滑系统中递进式油路分配器安全阀阀芯堵塞,无法进行油路分配
由于以上原因造成的轴端集中润滑系统故障,需更换润滑系统主油泵,经与厂家联系协商后,决定由原来一压力表接口的泵体更换为四压力表接口泵体(如图二);并取消递进式油路分配器,改为直接由四接口泵体经管线润滑搅拌主机轴端与支撑底座。
这样可以杜绝由于油路分配器阻塞造成的润滑系统油路不通的现象。
混凝土搅拌站主机轴端密封装置漏浆根本原因是浮动密封的损坏。
由于密封圈及油封损坏,润滑系统供油不足致使滑毂、转毂磨损;轴端漏浆造成的轴承磨损,与搅拌主轴的摩擦致使轴端温度过高。
主机轴端是受力集中的部位,零部件在强度较高应力的作用下其使用寿命会大大降低。
因此需及时更换轴端密封装置内的密封圈、油封及滑毂、转毂;以及主机轴端减速机漏浆一侧的轴承。
由于轴端密封装置的使用性能很大程度上取决于其机械零部件的装配质量,因此在维修装配时应注意:
1.维修装配前应先通过图纸或者装配工艺确定各个零部件的装配顺序
2.维修装配前应先检查密封件型号规格、机加零部件的尺寸公差
3.在需密封的零部件之间需按要求加入青稞纸垫或其他密封措施等
4.确保浮动密封环端面无破坏;所有机加零件需清洗干净
5.检查轴、轴套表面,密封腔内壁及密封压盖内表面应无毛刺、沟痕等;否则应修平、搓光,并重新清洗干净
6.应使用干净、柔软的纱布、棉纱或白棉纸等擦洗密封环端面;装配时摩擦接触面上涂一层清洁的机械润滑油脂
混凝土搅拌站出现异响及主机搅拌轴闷车现象是由于搅拌主机轴端轴
承与搅拌主轴的转动异常,使得衬板装置内搅拌臂上的叶片与衬板摩擦,造成搅拌叶片断裂、脱落;衬板变薄、开裂,与罐内壁间隙过大。
经检查发现搅拌装置内的进给叶片与返回叶片均需更换,进给、返回叶片如图三所示;并且应重新紧固所有叶片上的螺栓及固定螺母,调整衬板与罐内壁的间隙。
图三:JS1500B的搅拌装置
混凝土搅拌站的特点是机械化、自动化程度较高,所以生产率也很高。
所以在施工生产中混凝土搅拌站的生产效率也在很大程度上影响着项目的
工程进度。
因此对于混凝土搅拌站应加强保养与维护工作,尽力减少有害因素的影响,保证对搅拌主机轴端密封装置的合理润滑。
保证正常的工作载荷,严格执行设备的日常维护工作,进行定期与不定期的保养。
发现异常应及时处理,对于松动和失调的叶片及其他零部件及时紧固和调整,使混凝土搅拌站处于良好的技术状态。