橡胶燃烧温度
丁苯橡胶分解温度

丁苯橡胶分解温度丁苯橡胶是一种重要的合成橡胶材料,具有优异的耐热性、耐油性和耐溶剂性。
然而,随着时间的推移和外部因素的作用,丁苯橡胶会发生分解现象。
本文将以丁苯橡胶分解温度为标题,探讨丁苯橡胶的分解过程和影响因素。
一、丁苯橡胶的分解过程丁苯橡胶的分解过程主要包括链断裂、氧化反应和热分解等。
链断裂是指丁苯橡胶分子主链中的化学键发生断裂,导致分子结构的改变。
氧化反应是指丁苯橡胶与空气中的氧气发生反应,产生氧化产物,导致橡胶老化。
热分解是指丁苯橡胶在高温下分子结构发生断裂,产生气体和其他化合物。
二、丁苯橡胶分解的影响因素丁苯橡胶的分解温度受到多种因素的影响,主要包括温度、氧气浓度、压力和添加剂等。
1. 温度:温度是影响丁苯橡胶分解的重要因素。
一般情况下,随着温度的升高,丁苯橡胶的分解速度也会增加。
研究表明,丁苯橡胶分解的起始温度约为200℃,但随着温度的升高,分解速度会显著增加。
因此,在使用丁苯橡胶制品时,需要注意避免高温环境,以延缓其分解过程。
2. 氧气浓度:氧气是丁苯橡胶分解的重要催化剂。
氧气浓度的增加会加速丁苯橡胶的氧化反应和分解过程。
因此,在储存和使用丁苯橡胶制品时,需要尽量避免暴露在空气中,以减缓其分解速度。
3. 压力:压力对丁苯橡胶的分解影响较小。
在一定范围内,压力的增加对丁苯橡胶的分解速度没有显著影响。
4. 添加剂:添加剂是影响丁苯橡胶分解的重要因素之一。
适量添加一些抗氧化剂、防老化剂等添加剂,可以延缓丁苯橡胶的分解过程,提高其耐热性和耐老化性能。
三、如何延缓丁苯橡胶的分解过程为了延缓丁苯橡胶的分解过程,可以采取以下措施:1. 控制温度:在使用丁苯橡胶制品时,尽量避免高温环境,以减缓其分解速度。
2. 避免暴露在空气中:尽量在无氧或低氧环境下储存和使用丁苯橡胶制品,避免其与空气中的氧气发生反应。
3. 添加抗氧化剂:在丁苯橡胶的生产和加工过程中,适量添加抗氧化剂等添加剂,可以提高丁苯橡胶的耐热性和耐老化性能,延缓其分解过程。
橡胶、塑料、ABS、尼龙
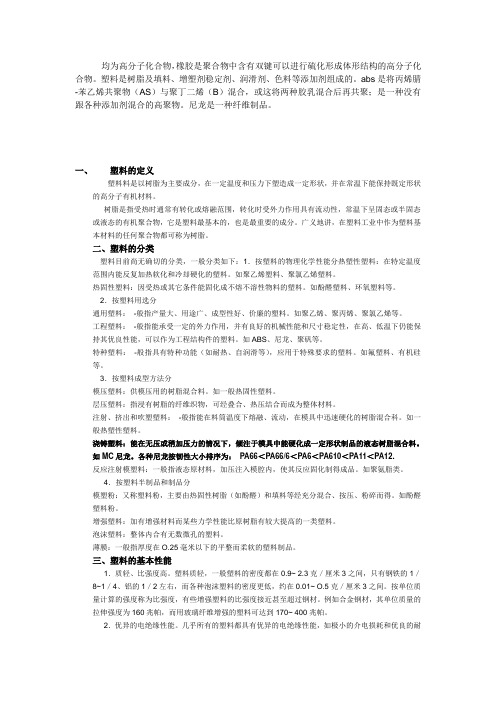
均为高分子化合物,橡胶是聚合物中含有双键可以进行硫化形成体形结构的高分子化合物。
塑料是树脂及填料、增塑剂稳定剂、润滑剂、色料等添加剂组成的。
abs是将丙烯腈-苯乙烯共聚物(AS)与聚丁二烯(B)混合,或这将两种胶乳混合后再共聚;是一种没有跟各种添加剂混合的高聚物。
尼龙是一种纤维制品。
一、塑料的定义塑料料是以树脂为主要成分,在一定温度和压力下塑造成一定形状,并在常温下能保持既定形状的高分子有机材料。
树脂是指受热时通常有转化或熔融范围,转化时受外力作用具有流动性,常温下呈固态或半固态或液态的有机聚合物,它是塑料最基本的,也是最重要的成分。
广义地讲,在塑料工业中作为塑料基本材料的任何聚合物都可称为树脂。
二、塑料的分类塑料目前尚无确切的分类,一般分类如下:1.按塑料的物理化学性能分热塑性塑料:在特定温度范围内能反复加热软化和冷却硬化的塑料。
如聚乙烯塑料、聚氯乙烯塑料。
热固性塑料:因受热或其它条件能固化成不熔不溶性物料的塑料。
如酚醛塑料、环氧塑料等。
2.按塑料用选分通用塑料:-般指产量大、用途广、成型性好、价廉的塑料。
如聚乙烯、聚丙烯、聚氯乙烯等。
工程塑料:-般指能承受一定的外力作用,并有良好的机械性能和尺寸稳定性,在高、低温下仍能保持其优良性能,可以作为工程结构件的塑料。
如ABS、尼龙、聚矾等。
特种塑料:-般指具有特种功能(如耐热、自润滑等),应用于特殊要求的塑料。
如氟塑料、有机硅等。
3.按塑料成型方法分模压塑料:供模压用的树脂混合料。
如一般热固性塑料。
层压塑料:指浸有树脂的纤维织物,可经叠合、热压结合而成为整体材料。
注射、挤出和吹塑塑料:-般指能在料筒温度下熔融、流动,在模具中迅速硬化的树脂混合科。
如一般热塑性塑料。
浇铸塑料:能在无压或稍加压力的情况下,倾注于模具中能硬化成一定形状制品的液态树脂混合料。
如MC尼龙。
各种尼龙按韧性大小排序为:PA66<PA66/6<PA6<PA610<PA11<PA12.反应注射模塑料:一般指液态原材料,加压注入模腔内,使其反应固化制得成品。
橡胶材料使用的下限温度

橡胶材料使用的下限温度
橡胶材料是一种常见的材料,广泛应用于汽车轮胎、密封件、管道和其他工业制品中。
然而,橡胶材料的使用受到温度的限制,特别是在低温环境下。
橡胶材料的下限温度是指在低温条件下,橡胶材料仍能保持其弹性和功能性的温度。
橡胶材料的下限温度取决于其成分和配方。
一般来说,常见的橡胶材料如丁苯橡胶、丁腈橡胶和氯丁橡胶在零下30摄氏度左右开始变得脆硬,失去弹性。
而硅橡胶和氟橡胶等特种橡胶材料则具有更低的下限温度,能在零下60摄氏度甚至更低的温度下保持其弹性和功能性。
在低温环境下,橡胶材料的弹性和柔韧性会受到影响,可能导致密封件失效、轮胎失去抓地力等问题。
因此,在一些特殊的工业领域,如航空航天、极地科考等,需要使用能在极低温环境下保持弹性的特种橡胶材料。
为了确保橡胶制品在低温环境下的可靠性,工程师们需要在设计和选材时考虑到橡胶材料的下限温度,选择合适的材料并进行相应的测试和验证。
同时,在使用过程中,也需要注意避免在低温环
境下对橡胶制品进行过度拉伸和挤压,以免造成材料的损坏。
总之,橡胶材料的下限温度是影响其在低温环境下使用性能的重要因素,了解和掌握橡胶材料的下限温度对于保证其在各种工程应用中的可靠性和安全性具有重要意义。
硅橡胶的耐热温度

硅橡胶的耐热温度硅橡胶是一种特种橡胶,具有优良的耐热性、耐寒性、耐臭氧、耐大气老化等性能。
硅橡胶主链由硅和氧原子交替构成,硅原子上通常连有两个有机基团。
根据硅橡胶种类不同,耐热温度也有所区别,通常范围在200℃到300℃之间。
硅橡胶的种类及应用硅橡胶根据其分子结构和性能可分为甲基硅橡胶、乙烯基硅橡胶、苯基硅橡胶等。
甲基硅橡胶具有良好的耐热性、耐寒性和耐臭氧性能,广泛应用于航空航天、汽车、电子、化工等领域。
乙烯基硅橡胶具有较好的耐磨性和电气性能,主要用于制作电缆、密封件等。
苯基硅橡胶具有较高的耐热性和耐腐蚀性,适用于高温、高压、高腐蚀环境下的密封和防护。
硅橡胶的制备工艺硅橡胶的制备工艺主要包括溶液聚合、悬浮聚合和本体聚合。
溶液聚合制备硅橡胶具有生产效率高、分子量分布窄的特点,但溶剂回收困难。
悬浮聚合制备硅橡胶具有操作简便、成本低廉的优点,但分子量分布较宽。
本体聚合制备硅橡胶具有良好的分子结构和性能,但生产效率较低。
此外,硅橡胶的制备过程中,催化剂的选择和使用条件对橡胶性能也有较大影响。
硅橡胶的改性为了进一步提高硅橡胶的性能,可以通过物理改性或化学改性对其进行改良。
物理改性主要包括填充改性、交联改性和共混改性。
填充改性可以提高硅橡胶的硬度、耐磨性和热稳定性;交联改性可以改变硅橡胶的力学性能和耐热性;共混改性可以通过加入不同性能的硅橡胶或其他材料,实现性能的优化。
化学改性主要包括端基改性和侧基改性,可以改变硅橡胶的化学结构和物理性能。
硅橡胶在我国的发展前景随着我国经济的快速发展,硅橡胶在各领域的应用不断扩大。
航空航天、汽车、电子、化工等行业对硅橡胶的需求不断增长,为硅橡胶产业提供了广阔的市场空间。
同时,我国政府对新材料产业的支持也为硅橡胶的发展提供了有利条件。
在未来,硅橡胶在我国的发展前景十分广阔,有望实现产业规模的持续扩大和产品质量的进一步提升。
总结硅橡胶作为一种高性能的特种橡胶,具有优良的耐热性、耐寒性、耐臭氧和耐大气老化等性能。
胶料焦烧时间t35

胶料焦烧时间t351. 胶料焦烧时间的定义和意义胶料焦烧时间是指胶料在高温下燃烧所需的时间,常用指标之一是t35。
胶料焦烧时间的测定对于评估胶料的阻燃性能具有重要意义。
胶料通常用于制造各种橡胶制品,如轮胎、密封件、橡胶管等。
在使用过程中,这些橡胶制品可能会接触到高温环境或火源,因此其阻燃性能至关重要。
焦烧时间是评估材料阻燃性能的重要参数之一。
2. 胶料焦烧时间测试方法2.1 实验设备和试样准备进行胶料焦烧时间测试需要以下实验设备:•焦炉:用于提供高温环境。
•定时器:用于计时。
•试样:通常为标准尺寸的橡胶样品。
试样准备步骤如下:1.准备标准尺寸的橡胶样品,确保其质量和尺寸一致。
2.清洗试样,并确保其表面干净。
2.2 实验步骤1.将试样放置于焦炉中心位置。
2.打开焦炉,将温度升至设定的测试温度。
3.观察试样燃烧情况,并启动定时器。
4.当试样完全燃烧殆尽时,停止定时器并记录时间。
5.重复以上步骤,进行多次测试,以提高测试结果的准确性。
3. 胶料焦烧时间的影响因素胶料焦烧时间受多种因素的影响,主要包括以下几个方面:3.1 胶料成分胶料的成分对其阻燃性能有重要影响。
一般来说,含有更多阻燃剂的胶料具有更长的焦烧时间。
此外,添加其他助剂(如稳定剂、增塑剂等)也可能对焦烧时间产生影响。
3.2 胶料结构和形态胶料的结构和形态也会对其焦烧时间产生影响。
例如,胶料中存在大量孔隙或表面积较大的颗粒会加速其氧化和燃烧过程,导致焦烧时间缩短。
3.3 测试条件测试条件如温度、氧气浓度等也会对胶料焦烧时间产生影响。
通常情况下,测试温度越高,焦烧时间越短;氧气浓度越高,焦烧时间也会缩短。
3.4 其他因素除了上述因素外,还有其他一些因素可能对胶料焦烧时间产生影响,如湿度、压力等。
这些因素的具体影响需要根据实际情况进行具体分析。
4. 胶料焦烧时间的应用胶料焦烧时间的应用主要体现在以下几个方面:4.1 材料选择和优化通过比较不同胶料的焦烧时间,可以评估其阻燃性能,并选择性能更好的材料。
EPDM

阻燃等级阻燃等级由HB,V-2,V-1向V-0逐级递增:1、HB:UL94标准中最底的阻燃等级。
要求对于3到13 毫米厚的样品,燃烧速度小于40毫米每分钟;小于3毫米厚的样品,燃烧速度小于70毫米每分钟;或者在100毫米的标志前熄灭。
2、V-2:对样品进行两次10秒的燃烧测试后,火焰在60秒内熄灭。
可以有燃烧物掉下。
3、V-1:对样品进行两次10秒的燃烧测试后,火焰在60秒内熄灭。
不能有燃烧物掉下。
4、V-0:对样品进行两次10秒的燃烧测试后,火焰在30秒内熄灭。
不能有燃烧物掉下。
三元乙丙(EPDM)特性及用途三元乙丙橡胶是由乙烯、丙烯经溶液共聚合而成的橡胶,再引入第三单体(ENB)。
三元乙丙橡胶基本上是一种饱和的高聚物,耐老化性能非常好、耐天候性好、电绝缘性能优良、耐化学腐蚀性好、冲击弹性较好。
乙丙橡胶的最主要缺点是硫化速度慢;与其它不饱和橡胶并用难,自粘和互粘性都很差,故加工性能不好。
根据乙丙橡胶的性能特点,主要应用于要求耐老化、耐水、耐腐蚀、电气绝缘几个领域,如用于轮胎的浅色胎侧、耐热运输带、电缆、电线、防腐衬里、密封垫圈、建筑防水片材、门窗密封条、家用电器配件、塑料改性等。
乙丙橡胶的性质与用途。
乙丙橡胶以乙烯和丙烯为主要原材料合成,耐老化、电绝缘性能和耐臭氧发能突出。
乙丙橡胶可大量充油和填充碳黑,制品价格较低,乙丙橡胶化学稳定性好,耐磨性、弹性、耐油性和丁苯橡胶接近。
乙丙橡胶的用途十分广泛,可以作为轮胎侧、胶条和内胎以及汽车的零部件,还可以作电线、电缆包皮及高压、超高压绝缘材料。
还可制造及鞋、卫生用品等浅色制品。
乙丙橡胶的性能与改进:一、1、低密度高填充性乙丙橡胶的密度是较低的一种橡胶,其密度为0.87。
加之可大量充油和加入填充剂,因而可降低橡胶制品的成本,弥补了乙丙橡胶生胶价格高的缺点,并且对高门尼值的乙丙橡胶来说,高填充后物理机械能降低幅度不大。
2、耐老化性乙丙橡胶有优异的耐天候、耐臭氧、耐热、耐酸碱、耐水蒸汽、颜色稳定性、电性能、充油性及常温流动性。
橡胶燃烧产生非甲烷总烃废气原理 -回复

橡胶燃烧产生非甲烷总烃废气原理-回复橡胶燃烧产生非甲烷总烃废气是一个复杂的过程,涉及多种化学反应和气体排放。
在这篇文章中,我将一步一步地解释橡胶燃烧产生非甲烷总烃废气的原理,并探讨其对环境和人类健康的影响。
第一步:橡胶的燃烧过程橡胶燃烧是一个氧化反应,需要氧气作为燃料的氧化剂。
当橡胶被加热到足够高的温度时,其分子内的化学键会断裂,释放出大量能量并产生燃烧反应。
该反应将橡胶分子中的碳、氢、氧等元素与氧气结合形成二氧化碳和水。
橡胶燃烧反应的化学方程式如下:橡胶+ 氧气→二氧化碳+ 水+ 热能第二步:非甲烷总烃的生成然而,除了二氧化碳和水之外,橡胶燃烧还会产生一系列有机化合物,这些化合物被称为非甲烷总烃(Non-Methane Total Hydrocarbons,NMTH)。
NMTH包括各种碳氢化合物,如烷烃、烯烃和芳香烃等。
非甲烷总烃的生成主要是由于橡胶燃烧过程中存在的不完全燃烧和热解反应导致的。
不完全燃烧是指橡胶燃烧过程中,由于氧气供应不足或燃烧温度不够高等原因,无法将所有碳和氢元素完全氧化为二氧化碳和水,从而形成一些未燃烧的碳氢化合物。
与之类似,热解反应是指橡胶燃烧过程中,高温下橡胶分子内部的碳-碳和碳-氢键断裂的过程。
这些断裂的键可能形成新的碳氢化合物,增加了非甲烷总烃的含量。
第三步:非甲烷总烃的环境影响非甲烷总烃的排放对环境和人类健康都有不良的影响。
首先,非甲烷总烃是臭氧(Ozone)和二氧化氮(Nitrogen Dioxide)等酸雨源的重要前体。
当非甲烷总烃与氮氧化物和太阳光等条件结合时,会引发光化学反应,产生臭氧和其他有害气体。
其次,非甲烷总烃还是空气中挥发性有机化合物(Volatile Organic Compounds,VOCs)的主要组成部分之一。
VOCs是空气中污染物的一类,其排放对臭氧层破坏和大气污染都有重要影响。
最后,非甲烷总烃还与气候变化有关。
作为温室气体的一部分,非甲烷总烃的排放直接导致大气中温室效应的增强,加剧了地球变暖的现象。
氟橡胶最高使用温度

氟橡胶最高使用温度氟橡胶是一种具有优异性能的高温材料,其最高使用温度是其突出特点之一。
氟橡胶在高温环境下表现出色,能够保持良好的物理性能,广泛应用于各个领域。
本文将详细介绍氟橡胶的最高使用温度以及其在高温环境下的性能表现。
氟橡胶是一种具有卓越耐高温性能的橡胶材料,其最高使用温度可达到260℃。
与其他常见橡胶材料相比,氟橡胶在高温环境下表现出更好的耐热性和耐候性。
在高温环境下,氟橡胶的物理性能和化学性能几乎不受影响,能够保持其原有的弹性和柔韧性。
氟橡胶的高温使用温度主要是由其独特的分子结构决定的。
氟橡胶分子链中的氟原子取代了一部分氢原子,使其具有更高的热稳定性和耐化学性。
此外,氟橡胶还具有较低的热传导性能,能够有效地隔离热量,保护其它部件不受高温影响。
在高温环境下,氟橡胶能够保持其优异的物理性能。
首先,氟橡胶具有较低的膨胀系数,能够在高温下保持较好的尺寸稳定性。
其次,氟橡胶具有良好的耐磨性和耐疲劳性,能够在高温环境下长时间运行而不出现破裂和损坏。
此外,氟橡胶还具有优异的耐油性和耐溶剂性,能够在高温环境下保持与各种化学物质的良好相容性。
氟橡胶在高温环境下的应用广泛。
它被广泛应用于航空航天、汽车、化工、电子等领域。
在航空航天领域,氟橡胶被用作密封材料,能够在高温和高压环境下保持密封性能。
在汽车领域,氟橡胶被用于制造高温密封件,如发动机密封圈和排气管密封圈。
在化工领域,氟橡胶被用于制造耐酸碱管道和阀门密封件。
在电子领域,氟橡胶被用于制造高温电线和电缆绝缘材料。
尽管氟橡胶具有优异的高温性能,但在实际应用中仍需注意一些问题。
首先,氟橡胶的高温使用温度是指在无氧或低氧环境下的情况,当氧气存在时,其使用温度会有所下降。
其次,氟橡胶在高温下会发生热分解现象,释放出有害气体,因此在高温环境下需注意通风和防护。
此外,氟橡胶的价格相对较高,需要根据具体应用情况进行选择。
氟橡胶是一种具有优异高温性能的橡胶材料,其最高使用温度可达260℃。
- 1、下载文档前请自行甄别文档内容的完整性,平台不提供额外的编辑、内容补充、找答案等附加服务。
- 2、"仅部分预览"的文档,不可在线预览部分如存在完整性等问题,可反馈申请退款(可完整预览的文档不适用该条件!)。
- 3、如文档侵犯您的权益,请联系客服反馈,我们会尽快为您处理(人工客服工作时间:9:00-18:30)。
橡胶燃烧温度
橡胶是一种常见的弹性材料,具有良好的耐磨性和耐腐蚀性。
然而,橡胶也有其燃烧特性,即在一定的条件下可以燃烧。
本文将探讨橡胶的燃烧温度及其相关问题。
一、橡胶的燃烧温度
橡胶的燃烧温度是指橡胶开始自燃并持续燃烧的温度范围。
根据不同类型的橡胶,其燃烧温度会有所不同。
一般来说,常见的天然橡胶和合成橡胶的燃烧温度范围为200℃至400℃。
二、橡胶的燃烧特性
1. 自燃温度:橡胶的自燃温度是指在没有外部热源的情况下,橡胶自身发生自燃的温度。
橡胶的自燃温度一般较高,需要接近或超过其燃烧温度才能发生自燃。
2. 燃烧性能:橡胶的燃烧性能是指橡胶在燃烧过程中的燃烧速率和火焰持续时间。
不同类型的橡胶在燃烧过程中会产生不同的燃烧产物,如煤烟、气体和灰烬等。
3. 燃烧产物:橡胶的燃烧会产生大量的有害气体和烟雾,其中包括一氧化碳、二氧化硫、二氧化氮等。
这些有害物质对环境和人体健康都具有一定的危害性。
三、橡胶燃烧的影响因素
1. 温度:橡胶的燃烧温度受到其周围环境温度的影响。
当环境温度高于橡胶的自燃温度时,橡胶可能会发生自燃。
因此,在储存和使用橡胶时,需要注意避免高温环境。
2. 氧气含量:氧气是燃烧的必要条件之一。
较高的氧气含量会促进橡胶的燃烧过程。
因此,在橡胶储存和使用的场所,要保持良好的通风条件,减少氧气的浓度。
3. 火源:外部火源是引发橡胶燃烧的主要原因之一。
橡胶在接触明火或高温物体时,可能会发生自燃和持续燃烧。
因此,要注意橡胶的存放位置,避免与火源接触。
四、橡胶燃烧的危害
1. 环境污染:橡胶燃烧会产生大量的有害气体和烟雾,对环境造成污染。
这些有害物质会加重大气污染,对空气质量和生态系统产生负面影响。
2. 人体健康影响:燃烧产生的有害气体和烟雾对人体健康具有一定的危害性。
长时间接触橡胶燃烧产生的烟雾可能导致呼吸道疾病和其他健康问题。
3. 火灾风险:橡胶燃烧具有较高的燃烧速度和火焰持续时间,容易
引发火灾。
因此,在橡胶生产和使用过程中,要严格控制火源,加强火灾预防措施。
五、橡胶燃烧的防控措施
1. 储存环境:橡胶应储存在通风良好、温度适宜的场所,避免高温环境和火源。
2. 防火设施:橡胶生产和使用场所应配备消防器材,并建立完善的消防设施和应急预案。
3. 定期检查:定期检查橡胶储存和使用场所,确保消防设备的完好性和可用性。
4. 教育培训:加强橡胶生产和使用人员的消防安全教育培训,提高其防火意识和应急处置能力。
结语
橡胶的燃烧温度对于橡胶的储存和使用具有重要意义。
了解橡胶燃烧特性和相关防控措施,可以有效预防橡胶燃烧引发的火灾和环境污染。
同时,橡胶生产和使用过程中应加强对橡胶燃烧的监测和管理,确保生产安全和环境保护。