某差速器齿轮的动态接触仿真与疲劳分析_端木萍萍
机械齿轮传动系统的动力学分析与优化

机械齿轮传动系统的动力学分析与优化齿轮传动是一种常见的动力传递机构,具有传递力矩大、传动效率高等优点,在工业生产中得到广泛应用。
但是,由于齿轮传动系统存在着一些固有的问题,如齿轮啮合时的振动和噪音、齿面磨损等,因此对其进行动力学分析和优化是非常重要的。
1. 动力学分析1.1 齿轮啮合的动力学模型齿轮啮合过程中,齿轮之间存在着瞬时的压力、速度和加速度变化。
可以通过建立齿轮啮合的动力学模型来分析其动态特性。
常用的方法包括等效单齿转动法和有限元法。
通过分析齿轮齿面接触应力和应力分布,可以预测系统的振动和噪音水平,为后续的优化提供依据。
1.2 动力学参数的测量和计算为了进行动力学分析,需要测量和计算一些关键参数,如齿轮的啮合刚度、传递误差、滚子轴承的刚度等。
其中,传递误差是影响齿轮传动系统性能的重要因素之一,其大小与齿轮加工质量、啮合配合、齿轮轴向和径向跳动等因素有关。
通过合理的测量方法和计算模型,可以准确地获取这些参数,并对系统进行分析。
2. 动力学优化2.1 齿轮传动系统的振动和噪音控制由于齿轮啮合时的动态特性,齿轮传动系统常常会产生振动和噪音。
为了减小振动和噪音的水平,可以从多个方面进行优化,如合理设计齿形、减小啮合间隙、提高齿轮加工精度等。
此外,也可以采用减振装置,如弹性联轴器、减震器等,来降低系统的振动能量传递。
2.2 传动效率的提高传动效率是衡量齿轮传动系统性能的重要指标之一。
为了提高传动效率,可以从减小传动误差、改善齿轮表面质量、减小传动间隙等方面入手。
此外,合理选择润滑方式和润滑油,也可以有效地降低系统的摩擦和磨损,提高传动效率。
2.3 齿轮传动系统的寿命预测齿轮传动系统的寿命是评估其使用寿命和可靠性的重要指标。
通过综合考虑齿轮的强度、疲劳寿命和磨损等影响因素,可以建立寿命预测模型,对系统进行寿命预测和优化设计。
此外,还可以通过监测齿轮的工作状态和健康状况,进行实时的故障诊断和维护。
3. 总结齿轮传动系统的动力学分析和优化是提高其性能和可靠性的重要手段。
基于ANSYS_LS_DYNA的直齿锥齿轮动力学接触仿真分析
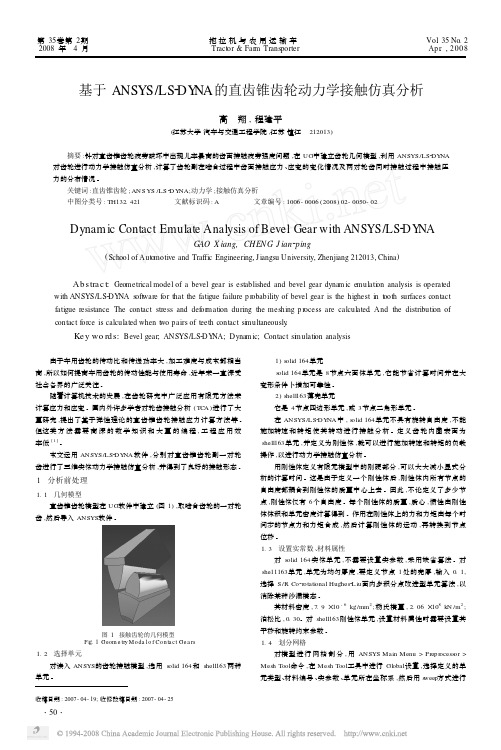
基于ANSYS/LS 2DY NA 的直齿锥齿轮动力学接触仿真分析高 翔,程建平(江苏大学汽车与交通工程学院,江苏镇江 212013)摘要:针对直齿锥齿轮疲劳破坏中出现儿率最高的齿面接触疲劳强度问题,在UG 中建立齿轮几何模型,利用ANSYS/LS 2DY NA 对齿轮进行动力学接触仿真分析,计算了齿轮副在啮合过程中齿面接触应力、应变的变化情况及两对轮齿同时接触过程中接触压力的分布情况。
关键词:直齿锥齿轮;AN S YS /LS 2D Y NA;动力学;接触仿真分析中图分类号:TH132.421 文献标识码:A 文章编号:1006-0006(2008)02-0050-02Dynam ic Contact Emulate Analysis of Bevel Gear with ANSYS/LS 2DY NAGAO X iang,CHEN G J ian 2ping(School of Aut omotive and Traffic Engineering,J iangsu University,Zhenjiang 212013,China )Ab s tra c t:Geometrical model of a bevel gear is established and bevel gear dyna m ic emulati on analysis is operatedwith ANSYS/LS 2DY NA s oft w are f or that the fatigue failure p r obability of bevel gear is the highest in t ooth surfaces contact fatigue resistance .The contact stress and def or mati on during the meshing p r ocess are calculated .And the distributi on of contact f orce is calculated when t w o pairs of teeth contact si m ultaneously .Key wo rd s:Bevel gear;ANSYS/LS 2DY NA;Dyna m ic;Contact si m ulati on analysis 由于车用齿轮的传动比和传递功率大,加工难度与成本都相当高,所以如何提高车用齿轮的传动性能与使用寿命,近年来一直深受社会各界的广泛关注。
Ease-off修形高减速比准双曲面齿轮接触仿真与动态性能试验

2023年第47卷第5期Journal of Mechanical TransmissionEase-off修形高减速比准双曲面齿轮接触仿真与动态性能试验古德万魏冰阳任明辉何宏图(河南科技大学机电工程学院,河南洛阳471000)摘要针对高减速比准双曲面(High Reduction Hypoid,HRH)齿轮大轮齿廓曲率不足、小轮大螺旋角齿面高度扭转的问题,提出了大轮采用刀具修形以实现齿面点接触的方法,小轮采用一般滚切法,简化机床加工参数;建立了大、小轮的三维模型,Ease-off拓扑曲面;解析了接触路径、差曲率、传动误差等齿面接触性能参数;通过三维运动仿真对比修形前后齿面的接触区,修形后避免了边缘接触,接触区位于齿面中部靠近小端,与齿轮实际接触斑点一致。
完成了HRH齿轮减速器动态性能试验,齿轮啮合传动性能优良,啮合质量稳定,验证说明所设计的HRH齿轮修形量控制合理、理论计算与运动仿真正确。
关键词准双曲面齿轮刀具修形差曲面运动仿真振动Contact Simulation and Dynamic Performance Test of Ease-off Modified HighReduction Hypoid GearsGu Dewan Wei Bingyang Ren Minghui He Hongtu(School of Mechanical & Electronic Engineering, Henan University of Science & Technology, Luoyang 471000, China)Abstract Aiming at the problems of insufficient curvature of the tooth profile of the wheel of the high reduction hypoid (HRH) gear, and high twist of the tooth surface of the pinion with a large helix angle, a method of using a tool to modify the wheel to realize the point contact of the tooth surface is proposed; the pinion adopts the general hobbing method, which simplifies the machining parameters of the machine tool. Three-dimensional models of wheels and pinions and Ease-off topological surfaces are established; the contact performance parameters of tooth surfaces, such as the contact path, differential curvatures, transmission error, etc. are analyzed. The contact areas of the tooth surface before and after modification are compared by 3D motion simulation,and the edge contact is avoided after modification, and the contact area is located in the middle of the tooth surface near the small end, which is consistent with the actual contact spot of the gear. The dynamic performance test of HRH gear reducers has been completed, the gear meshing transmission performance is excellent, and the meshing quality is stable, which verifies the reasonable control of the designed HRH gear modification amount, and the correct theoretical calculation and motion simulation.Key words Hypoid gear Modification tool Ease-off surface Motion simulation Vibration0 引言大减速比齿轮传动装置常采用蜗杆或行星传动,其制造难度大、成本高、精度难以保证。
变速器齿轮接触疲劳强度分析

变速器齿轮接触疲劳强度分析刘大龙;李稳迪;张瑞;张凯;施伟辰【摘要】基于ANSYS对变速器各档啮合齿轮进行瞬态动力学分析,再结合齿轮接触理论和疲劳损伤累积理论,求得各档齿轮的接触应力大小和疲劳寿命曲线.从所求结果看出,二档和三挡齿轮啮合时接触应力不大,小于齿轮的许用接触应力,且疲劳寿命较高,满足设计要求;一档和四挡齿轮啮合时的接触应力大于了齿轮的许用接触应力,且疲劳寿命较低,不能满足设计要求.基于以上原因,利用齿向和齿廓相结合的轮齿修形方法,对一档和四挡齿轮进行了轮齿修形,从最终求得结果来看,两组啮合齿轮的接触应力均大幅度降低,同时疲劳寿命得到了提高,轮齿修形达到了很好的效果.【期刊名称】《汽车实用技术》【年(卷),期】2018(000)017【总页数】5页(P33-36,138)【关键词】变速器;齿轮;瞬态动力学;接触应力;疲劳寿命【作者】刘大龙;李稳迪;张瑞;张凯;施伟辰【作者单位】上海海事大学物流工程学院,上海 200120;上海海事大学物流工程学院,上海 200120;上海海事大学物流工程学院,上海 200120;上海海事大学物流工程学院,上海 200120;上海海事大学物流工程学院,上海 200120【正文语种】中文【中图分类】TH123引言在蒸汽机车诞生之时,人类就行通过一种装置能够改变蒸汽机车的输出载荷,以便达到人类想要达到的要求。
在1784年,James Watt申请了常啮合齿轮传动机构的专利,至此出现了变速器的雏形。
1879年,塞尔登成功申请了带有离合器和倒挡中间轴转动装置的变速器专利。
1886年,戈特利布∙戴勒姆创造了世界上第一台真正的汽车0。
发动机的动力经由齿轮和链条传至后轮,从而实现了汽车的行驶。
在接下来的100多年的时间里,变速器呈现出多样性发展,手动变速器、自动变速器、双离合变速器、无级变速器等应运而生。
1 变速器有限元模型创建1.1 三维实体模型创建本文对利用SolidWorks对某乘用车五档汽车变速器进行3D建模,主要包括传动轴、齿轮,其中传动轴包括输入轴、中间轴、输出轴和倒挡轴。
某差速器齿轮的参数化设计及有限元分析_王良模
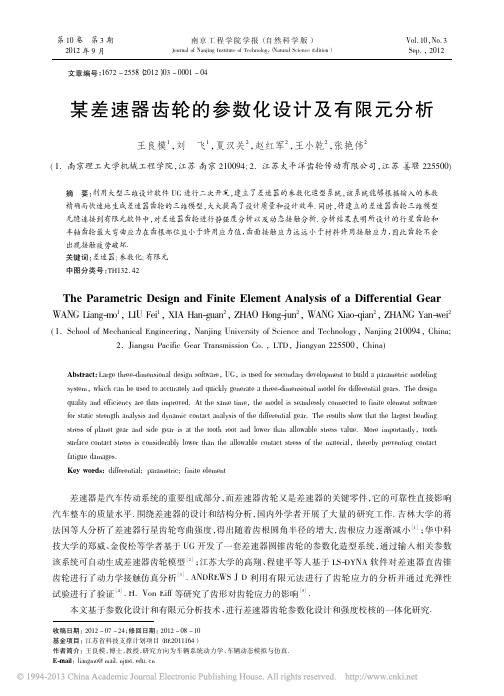
第10卷第3期2012年9月南京工程学院学报(自然科学版)Journal of Nanjing Institute of Technology (Natural Science Edition )Vol.10,No.3Sep.,2012文章编号:1672-2558(2012)03-0001-04某差速器齿轮的参数化设计及有限元分析王良模1,刘飞1,夏汉关2,赵红军2,王小乾2,张艳伟2(1.南京理工大学机械工程学院,江苏南京210094;2.江苏太平洋齿轮传动有限公司,江苏姜堰225500)摘要:利用大型三维设计软件UG 进行二次开发,建立了差速器的参数化造型系统,该系统能够根据输入的参数精确而快速地生成差速器齿轮的三维模型,大大提高了设计质量和设计效率.同时,将建立的差速器齿轮三维模型无缝连接到有限元软件中,对差速器齿轮进行静强度分析以及动态接触分析.分析结果表明所设计的行星齿轮和半轴齿轮最大弯曲应力在齿根部位且小于许用应力值,齿面接触应力远远小于材料许用接触应力,因此齿轮不会出现接触疲劳破坏.关键词:差速器;参数化;有限元中图分类号:TH132.42The Parametric Design and Finite Element Analysis of a Differential Gear WANG Liang-mo 1,LIU Fei 1,XIA Han-guan 2,ZHAO Hong-jun 2,WANG Xiao-qian 2,ZHANG Yan-wei 2(1.School of Mechanical Engineering,Nanjing University of Science and Technology,Nanjing 210094,China;2.Jiangsu Pacific Gear Transmission Co.,LTD,Jiangyan 225500,China)Abstract:Large three-dimensional design software,UG,is used for secondary development to build a parametric modeling system,which can be used to accurately and quickly generate a three-dimensional model for differential gears.The design quality and efficiency are thus improved.At the same time,the model is seamlessly connected to finite element software for static strength analysis and dynamic contact analysis of the differential gear.The results show that the largest bending stress of planet gear and side gear is at the tooth root and lower than allowable stress value.More importantly,tooth surface contact stress is considerably lower than the allowable contact stress of the material,thereby preventing contact fatigue damages.Key words:differential;parametric;finite element收稿日期:2012-07-24;修回日期:2012-08-10基金项目:江苏省科技支撑计划项目(BE2011164)作者简介:王良模,博士,教授,研究方向为车辆系统动力学、车辆动态模拟与仿真.E-mail :liangmo@mail.njust.edu.cn差速器是汽车传动系统的重要组成部分,而差速器齿轮又是差速器的关键零件,它的可靠性直接影响汽车整车的质量水平.围绕差速器的设计和结构分析,国内外学者开展了大量的研究工作.吉林大学的蒋法国等人分析了差速器行星齿轮弯曲强度,得出随着齿根圆角半径的增大,齿根应力逐渐减小[1];华中科技大学的郑威、金俊松等学者基于UG 开发了一套差速器圆锥齿轮的参数化造型系统,通过输入相关参数该系统可自动生成差速器齿轮模型[2];江苏大学的高翔、程建平等人基于LS-DYNA 软件对差速器直齿锥齿轮进行了动力学接触仿真分析[3].ANDREWS J D 利用有限元法进行了齿轮应力的分析并通过光弹性试验进行了验证[4].H.Von Eiff 等研究了齿形对齿轮应力的影响[5].本文基于参数化设计和有限元分析技术,进行差速器齿轮参数化设计和强度校核的一体化研究.南京工程学院学报(自然科学版)2012年9月1差速器齿轮的参数化设计目前常用的齿轮参数化建模方法有两种[5]:一种是利用API 函数直接创建对象,利用这些对象来完成齿轮实体的建模、编辑和修改;另一种是手工创建参数化的齿轮模板,提取其中的关键参数变量,通过修改关键参数变量实现齿轮模型的更新.前一种方法涉及的知识面较宽,对编程人员要求较高;后一种方法比较简单,对于非编程人员应用难度较小.因此本文采用后一种方法,即用手工在UG 中参数化创建齿轮实体模型,并将变量用表达式来表示,得到齿轮模板.然后通过修改齿轮模板中的变量,所得到的齿轮模型实现参数驱动下的自动更新.UG /OPEN 提供的MenuScript 和UIStyler 两个模块用于制作应用程序的用户界面[6].其中MenuScript 图1“行星齿轮参数化设计”对话框用于创建和编辑UG 的下拉菜单和工具栏.使用记事本创建应用程序的菜单文件,该菜单文件包括“行星齿轮”按钮和“半轴齿轮”按钮.按钮用于齿轮的参数化设计.进入UG /OPEN UIStyler 模式,创建如图1所示的“行星齿轮参数化设计”对话框.使用VC ++6.0,创建应用程序的工程,工程名称为planet.利用向导ugopen.awx 创建应用程序,应用程序使用ufsta 函数作为入口函数,当UG 进程结束时,自动卸载.将UG /OPEN UIStyler 模块生成的对话框文件planet_template.c 和plan-et.h 分别重新命名为planet_dialog.c 和planet_dialog.h ,复制到工程文件所在的文件夹,并加入工程中.所有齿轮参数的程序编译完以后,再加上入口函数,检验部件函数,对话框回调函数和取消函数等,就完成了主体函数的编译.在“行星齿轮参数化设计”对话框中更改参数数值,单击“应用”按钮,行星齿轮模型就自动完成更新.利用开发的齿轮参数化造型系统,输入齿轮的模数、齿数、压力角等基本参数,自动生成某轿车差速器行星齿轮模型.2差速器齿轮的有限元分析对于汽车差速器锥齿轮副来说,在大多数情况下,汽车左右轮是等速或接近等速的,锥齿轮的相对转速很小,行星齿轮经常只是起个等臂推力杆的作用,弯曲强度应为主要考虑因素.因此差速器行星齿轮主要进行弯曲强度的计算[7].由于直齿锥齿轮疲劳破坏中出现几率最高的是齿面接触疲劳强度问题,如何提高车用齿轮的传动性能与使用寿命,近年来一直深受社会各界的广泛关注.本文运用ANSYS /LS-DYNA 软件,对差速器的直齿锥齿轮副的三对轮齿进行动力学接触仿真分析,得到了良好的接触形态.2.1差速器齿轮有限元模型的建立基于CAD /CAE 一体化技术,有限元软件选用ANSYS 11.0,该软件和UG 软件可无缝连接,在UG 的主菜单中添加了ANSYS 11.0菜单项[8].在UG 中生成齿轮三维模型后,直接点击ANSYS 11.0菜单项,进入ANSYS 11.0界面,然后选择单元类型、单元尺寸、材料属性等建立差速器行星齿轮、半轴齿轮的有限元模型.2第10卷第3期王良模,等:某差速器齿轮的参数化设计及有限元分析2.2差速器齿轮弯曲强度分析载荷沿齿面接触线的分布是决定齿轮应力的基础,因此精确确定载荷沿齿面接触线的分布状态,对于齿轮强度分析具有十分重要的意义.所分析的齿轮是对称零件,因此建立行星齿轮和半轴齿轮单齿的有限元模型来进行分析.其中行星齿轮单齿有限元模型共有2982个节点,2211个实体单元,行星齿轮单齿有限元模型如图2所示.齿轮加载方法有两种:1)在齿轮轮毂加载等效力矩,此时位移的约束需施加在齿顶部位;2)将齿轮所承受的转矩转化为单齿啮合最高点所承受的线性分布力.本文所研究的差速器行星齿轮的加载方式选择后者.约束行星齿轮内圈的所有自由度,将圆周力F 1=3.52ˑ104N ,径向力F 2=1.36ˑ104N ,轴向力F 3=9.1ˑ103N 近似作线性载荷处理,按照比例施加在单齿啮合的最高点处,通过计算所得有限元结果如图3所示.图2行星齿轮单齿有限元模型图3行星齿轮单齿弯曲应力云图由图3可知,行星齿轮单齿最大弯曲应力为1697MPa ,出现在齿根处.符合行星锥齿轮的破坏多出现在齿根的实际情况.2.3差速器齿轮接触应力的有限元分析图4三对齿啮合的齿轮有限元模型利用8节点solid164实体单元和4节点shell163壳单元建立三对齿啮合的齿轮有限元模型,共有16188个节点、948个壳单元和11610个实体单元.其中齿轮实体采用solid164单元划分网格,齿轮的内圈采用shell163壳单元,并将齿轮内圈定义为刚体.有限元模型如图4所示.在ANSYS /LS-DYNA 模块中,定义4个part ,其中主动齿轮和从动齿轮为弹性体,将它们的内圈定义为刚体,以方便载荷和约束的施加.在主动齿和从动齿之间建立自动面接触,面接触的各定义选项均采用默认设置.通过对模型施加合适的边界条件,可模拟齿轮副的运动和传递的扭矩,分别对齿轮在低速和高速两种情况下进行仿真分析.对主动轮施加转速,所选用的主动齿轮转速分别取1.5rad /s 和9rad /s ,从动齿轮的负载分别为1188N ·m 和199N ·m ,计算时间分别设置为0.04s 和0.08s ,在两种速度工况下进行仿真分析,结果如图5、图6所示.计算结果显示两种转速下瞬时最大接触应力分别为161MPa 和914MPa ,齿轮的材料为20CrMnTi ,其接触疲劳极限应力为2250MPa ,所以此时的接触应力远远小于接触疲劳极限应力.另外通过比较可以得3南京工程学院学报(自然科学版)2012年9月出,主动轮的转速越大,齿轮的接触应力越大.图5齿轮啮合瞬时应力云图(1.5rad /s)图6齿轮啮合瞬时应力云图(9rad /s )3结语本文对UG 软件进行二次开发,创建了差速器齿轮的参数化建模系统,实现了汽车差速器齿轮的快速建模,得到的三维齿轮模型是进行精锻模具设计、动态接触有限元分析、机构仿真和数控编程的必要准备.齿轮参数化造型系统的开发大大缩短了差速器齿轮的设计周期,提高了设计质量和设计效率.另外通过对齿轮的静弯曲强度分析,结果表明所设计的行星齿轮和半轴齿轮所受到的最大弯曲应力都出现在齿根部位,与实际情况相符,并且小于许用值,设计满足要求.对齿轮的动态啮合分析,得到了齿轮副在啮合过程中齿面接触应力、应变的变化情况,结果表明齿面接触应力远远小于材料接触极限应力,因此齿轮不会出现接触疲劳破坏.参考文献:[1]蒋法国.差速器行星齿轮的有限元法强度分析[D ].长春:吉林大学,2006.[2]郑威,金俊松,李大才.基于UG 的汽车差速器圆锥齿轮参数化造型系统的开发[D ].武汉:华中科技大学,2007.[3]高翔,程建平.基于ANSYS /LS-DYNA 的直齿锥齿轮动力学接触仿真分析[D ].镇江:江苏大学,2008.[4]ANDREWS J D.A finite element analysis of bending stresses induced in external and internal involutes spur gears [J ].Journal of Strain Analy-sis ,1991,26(3):153-163.[5]VON EIFF H V.Influence of gear tooth geometry on tooth stress of external and internal gears [J ].Trans ASME ,J of Mech Des ,1990,112:575-583.[6]候永涛,丁向阳.UG /Open 二次开发与实例精解[M ].北京:化学工业出版社,2007.[7]刘惟信.圆锥齿轮与双曲面齿轮传动[M ].北京:人民交通出版社,1980.[8]张朝晖.ANSYS11.0结构分析工程应用实例解析[M ].北京:机械工程出版社,2008.4。
基于solidworks和ls-dyna的斜齿轮动力学接触仿真分析
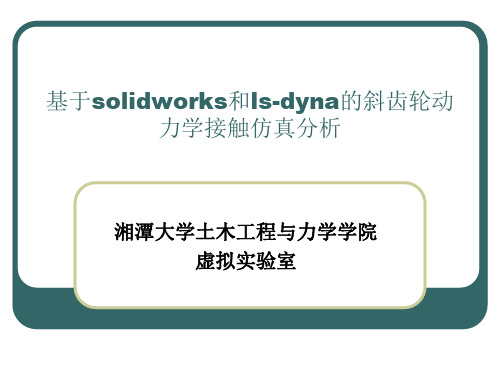
湘潭大学土木工程与力学学院 虚拟实验室
1.建模
齿轮参数: 齿轮参数 。 。 主从齿轮齿数30,模数3,压力角20 ,螺旋角20 , 齿厚18.52mm。 单元选取: 单元选取 solid164和shell163单元。 实常数、材料属性: 实常数、材料属性: 材料属性选线弹性材料,杨氏模量为2.06E8 KPa ,泊 松比为0.3,密度为7.9E-6Kg/mm3。对shell163单元,单元 为均匀厚度,定义节点1处的壳厚为0.1,选择S/R Corotational Hughes-Liu 面内多积分点改进型单元算法,以 消除某种沙漏模态。
5.结果分析
图4.主动轮齿面部位应力图
5.结果分析
图5.从动轮齿面部位应力图
5.结果分析
图6.主动轮齿根部位应力图
5.结果分析
图7.从动轮齿根部位应力图
5.结果分析
图8.齿轮最大Von Mises应力示意图
5.结果分析
图9.斜齿轮传动应力示意图
5.结果分析
图10.斜齿轮传动应力示意图
5.结果分析
图11.斜齿轮传动动画演示
5.结果分析
图12.斜齿轮传动动画演示
1.建模
图1.基于SolidWorks的齿轮模型
1.建模
图2.导入ANSYS后的齿轮模型
பைடு நூலகம்
1.建模
图3.划分网格后的有限元模型
2.定义接触
生成PART之后即可对齿轮的接触方式进行设置, 在LS-DYNA中没有接触单元,只要定义可能接触的接触 表面,它们之间的接触类型,以及与接触有关的一些参 数即可。本文在齿轮的动态模拟中选择面面接触的自动 接触方式(ASTS)来定义接触,同时设置静摩擦因数为 0.3,动摩擦因数为0.25,其他参数采用默认设置,选择 主动齿轮(PART1)为接触面,从动齿轮(PART2)为 目标面。
齿轮系统的接触模态分析

轴向位移,保留圆周方向的自由度;输入轮
是驱动轮,施加绕中心轴线旋转的角速度
-338.98rad/s;太阳轮安装孔的节点上同样约 束径向和轴向位移,同时在节点上施加切线
方向的节点力 Fy:
Fy=-
输入转矩
=
内圈节点数 ×中心孔半径
-531.2N
(5)
Fy 为负值,即太阳轮的负载转矩是顺
时针方向,加载后的效果如图 1 所示
行星齿轮传动被广泛应用于装甲车 先是在考虑接触特性的情况下做静态非线
辆,一般在高速重载、频繁启动工况下工作, 性分析,获得在静态载荷作用下的应力,然
在此工作环境下,有必要分析齿轮系统的固 后把得到的应力以附加刚度的形式叠加到
有振动频率。在设计齿轮系统时不但要考虑 系统的刚度矩阵上,在不考虑接触的条件下
[2] 吴志强,陈予恕.非线性模态的 分类和新的求解方法.力学学 报.1996.28
[3] 陈予恕,吴志强.非线性模态理 论的研究进展.力学进 展.1997.27
[4] 李欣业,陈予恕,吴志强.非线 性模态理论及其研究进展.河北 工业大学学报.2004.33
[5] 白润波,曹平周,曹茂森,陈建锋. 基于优化—反分析法的接触刚 度因子的确定. 建筑科 学.2008.1
discussed. Considering the non-linear contact,the static stress analysis is done the stress above
is imposed on the system rigid matrix as additional stiffness.Finally,the gear system modal
3 行星齿轮系统有限元模型建立
基于Adams的公转二级减速齿轮动力仿真分析

摘要利用SolidWorks建立普通二级圆柱直齿轮减速机构和公转二级圆柱直齿轮减速机构实体模型,把模型导入Adams中建立运动学仿真分析,给出约束、转速、接触力和负载的添加方法,获得齿轮的啮合力和接触频率图像。
与普通状态下的二级齿轮减速机构对比得出两种状态的下的运动规律,仿真结果表明,理论值和仿真值误差较小,对优化设计公转速度和齿轮传动速度及其齿轮和轴的强度校核提供了一定的理论和技术支持。
关键词公转二级减速Adams动力学仿真2.School of Mechanical Engineering,Tianjin University of Technology,Tianjin300384China)Abstract Using SolidWorks to establish the institutions of general level two spur gear and the revolution of two cylindrical gear deceleration entity model,getting the model into Adams to establish the kinematics simulation analysis,given the constraints,speed,contact force and load,get the gear meshing force and frequency of contact pared with the secondary gear reduction mechanism of general condition of two kinds of state of motion,the simulation results show that,the theoretical value and the simulation value has a little error,to provide a certain theoretical and technical support for the revolution speed and speed of gear transmission optimization design and strength checking of gear and shaft.Keywords revolution of two deceleration Adams kinematics simulation0引言二级减速齿轮传动机构是机械传动系统中重要的一部分,圆柱齿轮传动由于具有恒定传动比及传递功率损失很小等传动特点,因此具有其他传动不可替代的优势,因此准确的掌握齿轮传动的力学特性,对整个系统的几何设计和强度设计工作有着重要意义。
- 1、下载文档前请自行甄别文档内容的完整性,平台不提供额外的编辑、内容补充、找答案等附加服务。
- 2、"仅部分预览"的文档,不可在线预览部分如存在完整性等问题,可反馈申请退款(可完整预览的文档不适用该条件!)。
- 3、如文档侵犯您的权益,请联系客服反馈,我们会尽快为您处理(人工客服工作时间:9:00-18:30)。
基金项目:江苏省科技支撑计划(BE2011164) 收稿日期:2013-07-23 修回日期:2014-06-06 第一作者简介:端木萍萍,女,1989年生,南京理工大学,研究生;研究方向——CAE 与疲劳技术。
E-mail :mumudmdp@应 用 力 学 学 报 CHINESE JOURNAL OF APPLIED MECHANICS第31卷 第4期2014年8月V ol.31 No.4Aug. 2014文章编号:1000- 4939(2014) 04-0595-06某差速器齿轮的动态接触仿真与疲劳分析端木萍萍1 王良模1 夏汉关2 赵红军2 董义2(1 南京理工大学机械工程学院 210094 南京;2 江苏太平洋齿轮传动有限公司 225500 姜堰)摘要:为分析差速器齿轮的疲劳寿命,运用动态有限元与试验相结合的方法,研究了锥齿轮在啮合过程中的应力分布以及疲劳强度。
首先基于CATIA 软件对差速器的半轴齿轮、行星齿轮进行了参数化建模,并采用动态有限元法模拟了齿轮副在最大扭矩工况下的动态接触;再根据有限元强度分析结果,将最大接触应力作为静载输入,运用疲劳分析软件对齿轮副的接触疲劳性能进行计算;最后进行了差速器齿轮副的台架试验,并将仿真结果与台架试验进行了对比。
结果表明:齿面最大接触应力产生于节圆附近,齿轮间的最大接触应力为1309MPa ;半轴齿轮在90%存活率下的疲劳寿命为3.394×106;仿真结果与台架试验具有较好的一致性,齿轮满足疲劳寿命要求。
将动态有限元和疲劳寿命分析方法相结合可以有效预测差速器齿轮疲劳寿命。
关键词:齿轮强度;动态接触冲击;疲劳寿命;有限元法中图分类号:U463.21 文献标识码:A DOI :10.11776/cjam.31.04.B0701 引 言锥齿轮作为基础的传动部件,具有重合度大、传动平稳、承载能力强等优点,被应用于机械、水电、冶金等不同行业[1-4]。
锥齿轮的动态性能研究主要涉及齿面分析、加载接触分析、考虑齿面摩擦的热分析、润滑分析等,是一个典型的动态接触问题[5]。
近年来众多学者在齿轮副动态特性方面做了许多工作。
文献[6]从接触冲击的角度分析了不同冲击转速、冲击位置对冲击合力、冲击时间和冲击应力的影响。
文献[7]在ANSYS 中对差速器齿轮的非线性接触进行有限元模拟,研究了行星齿轮和半轴齿轮在啮合周期内最大弯曲应力与对应的啮合位置、齿根应力分布等。
文献[8]基于接触动力学,利用有限元法对螺旋锥齿轮的动态啮合特性进行了研究,考虑了不同惯性载荷、转速、负载、轴变形等因素对动态啮合规律的影响。
在现有研究的基础上,本文利用动态有限元法,对正确啮合、无安装误差的差速器齿轮副间的连续动态啮合过程进行模拟计算,得出一个啮合周期内的啮合规律以及最大接触应力分布。
将最大接触应力作为静载输入对齿轮副的接触疲劳性能进行计算。
为齿轮的设计与强度校验提供一定的参考。
2 差速器齿轮的参数化建模本文利用CATIA 软件分别对差速器的半轴齿轮和行星齿轮进行了参数化建模。
2.1 建模原理在笛卡尔坐标系中,锥齿轮的齿廓表面为球面596 应 用 力 学 学 报 第31卷渐开线(如图1所示),其渐开线方程为=(sin sin cos cos sin )=(cos sin sin cos sin )=cos cos x l y l z l ϕψϕψθϕψϕψθψθ+⎧⎪−+⎨⎪⎩其中:l为基锥的锥长,l =;ψ为O C ′与O N ′之间的夹角;ϕ为OA 与瞬时回转轴ON 之间的夹角;θ为基椎角。
图1 球面渐开线形成过程的几何关系Fig.1 Geometry relationship2.2 参数化建模主要步骤差速器齿轮参数化建模所需要的基本参数如表1所示。
表1 行星齿轮和半轴齿轮的主要参数 Tab.1 Main parameters of gears参数(parameters) 齿数(number of teeth) 模数(module of gear) 压力角(pressureangle)/(°)节圆直径(pitch diameter) /mm 分锥角(angle ofbase cone)/(°) 行星齿轮(pinion) 11 6.5 22.5 71.5 28.82 半轴齿轮 (side gear) 20 6.5 22.5 130 61.189花键 (spline)35 0.75 37.5 --利用CATIA 软件对齿轮进行参数化建模的过程中,需要将表达式的定义、知识工程及创成式自由曲面等功能相结合,具体步骤如下。
1) 根据直齿圆锥齿轮的基本参数和几何尺寸的计算公式,计出建模所需要的几何参数,如齿根高、齿顶高等。
2) 分别画出直齿圆锥齿轮的基圆锥、齿根圆锥面、背锥面、齿顶圆锥面。
3) 根据球面渐开线齿廓面方程,画出齿轮大端的左右齿廓线,并利用Scaling Definition 功能对齿廓线进行仿射,从而得到左右齿廓面。
4) 利用齿根锥面、齿顶锥面、小端面对齿廓面进行修剪,形成单齿。
5) 再利用齿根圆锥面、小端平面、大端球面、背锥面对齿形曲面进行剪切,然后转换到Part Design 模块里生成实体模板,打孔后得到行星锥齿轮;同理,可以得到半轴齿轮。
如图2所示。
(a) 行星齿轮(pinion) (b) 半轴齿轮(side gear)图2 齿轮的几何模型Fig.2 Geometry model of gear3 动态接触的有限元分析锥齿轮的啮合问题包含了正常的接触,也包括了因误差、变形、侧隙、变速等原因引起的瞬态冲击。
其动态啮合过程中的力学性能难以通过实验准确测定,这给理论分析带来了极大困难。
因此,有限元方法成为计算齿轮动态接触问题最普遍、最有效的方法[9]。
基于所建的三维齿轮模型,本文运用动态有限元法,对差速器齿轮副间的动态接触进行模拟计算。
3.1 前处理 3.1.1 模型简化在有限元计算中,为了提高分析精度、节约计算时间,往往对模型进行一些简化。
具体操作为:①忽略行星齿轮、半轴齿轮上的油孔;②忽略行星齿轮、半轴齿轮齿顶部分和轴孔上的倒圆角及倒角;③忽略半轴齿轮上的花键。
3.1.2 网格划分为了保证齿轮的分析精度并避免弯曲载荷作用下的剪切自锁,选择线性减缩积分单元C3D8R 和C3D6R 对齿轮进行网格划分。
行星齿轮模型共有15884个实体单元,19591个节点。
半轴齿轮共有73360个实体单元,83060个节点。
两齿轮一共有89244个实体单元,102651个节点。
行星齿轮和半轴齿轮的有限元模型见图3。
第4期 端木萍萍,等:某差速器齿轮的动态接触仿真与疲劳分析 597图3 行星齿轮和半轴齿轮的有限元模型Fig.3 Assembly of the gears3.1.3 材料属性 差速器行星齿轮和半轴齿轮材料相同,其材料属性见表2。
表2 齿轮的材料属性 Tab.2 Material and Property材料(material)密度(density)/kg·m -3弹性模量(elastic modulus)/MPa泊松比 (Poisson ratio)20CrMnTi 79002060000.2933.1.4 接触、载荷及边界条件在齿轮啮合过程中,行星齿轮以一定的转速转动,驱动半轴齿轮运转,半轴齿轮在阻力矩的作用下达到平衡,对行星齿轮产生反力矩,两齿轮之间通过轮齿接触传递。
根据齿轮模型的接触情况,本文采用surf-to-surf 接触模式,接触主面和从面分别取行星齿轮齿面和半轴齿轮齿面,接触面之间采用有限滑移模式。
接触面间的摩擦系数为0.05。
由于实体没有转动自由度,所以需要建立两个参考点。
将两个齿轮轴孔表面上的节点,分别与各自的参考点耦合,使轴孔面与参考点具有相同的自由度[10]。
在参考点上施加的载荷和边界条件,就等同于施加在轴孔面上。
按照刚体控制的方法,对差速器的工作情况进行加载。
时间步的设置分为接触步和转动步两个部分。
在接触步中,固定行星齿轮,给半轴齿轮施加一个较小的扭矩(50N·m),以确保两只轮在转动中保持接触状态,接触步历时0.01s ,计算步数设为10;在转动步中,给行星齿轮4rad/s 的转速,在半轴齿轮上施加的最大阻力矩为2075N·m ,转动步历时0.4s ,计算步数设为400,平均每0.001s 输出一次结果。
3.2 有限元分析结果因为Abaqus /Explicit 适于求解复杂非线性动力学问题和准静态问题,因此将网格模型导入Abaqus /Explicit 中进行求解。
图4为行星齿轮和半轴齿轮啮入冲击时刻(0.001s)的等效应力云图。
通过等效应力云图可以清楚地看出等效应力在啮合过程中的变化,进而得出连续动态啮合过程中的齿面接触应力及齿根弯曲应力的分布规律,快速地得出模型中最危险的区域。
由图4可知,应力主要集中在接触部位和齿根部位。
半轴齿轮的应力主要体现在接触部分,而行星齿轮的应力主要体现在齿根处。
这与文献[5]中得出的结论一致。
(a) 半轴齿轮(side gear)(b) 行星齿轮(pinion)图4 齿轮的等效应力图Fig.4 Equivalent V on mises stress of gears图5 半轴齿轮接触应力云图Fig.5 Contact stress598 应 用 力 学 学 报 第31卷图5为B 齿在最大接触应力产生时刻的接触应力云图,可见最大接触应力为1309MPa ,而齿轮材料的接触疲劳极限为2250MPa ,计算结果远小于极限值,满足疲劳寿命要求。
最大接触应力产生于节线附近的172320节点处,图6为172320节点在整个啮合过程中的应力曲线。
由图可见:在0.072s 时,B 齿开始啮合,接触应力由0逐渐增大;在0.012时达到最大值;在0.16s 时,B 齿啮出,接触应力逐渐变为0。
整个曲线符合齿轮的啮合规律,曲线走向如同半个正弦曲线。
因此在疲劳分析中,可以将作用在轮齿上的载荷近似地看作为半正弦交变载荷。
图6 节点172320表面法向接触应力图Fig.6Contact stress at node 172320图7 接触区域各节点的表面法向接触应力Fig.7Contact normal stress of nodes in contact region图8 载荷的施加方式 Fig.8 Force on tooth以靠近大端节点为参考点,取接触区域中间的一系列节点,将各节点到大端节点的距离作为x 轴,接触应力作为y 轴,作出它们在某接触冲击瞬间的接触应力图,如图7所示。
齿面的接触线载荷从大端逐渐向小端减小略呈抛物状。