齿轮疲劳试验及装备技术
齿轮弯曲疲劳强度试验方法

齿轮弯曲疲劳强度试验方法全文共四篇示例,供读者参考第一篇示例:齿轮在机械设备中起着至关重要的作用,它们通过齿轮传动来实现机械运动,比如汽车的变速箱、风力发电机和其他机械设备都离不开齿轮。
齿轮在长时间运作中会受到各种力的作用,容易发生疲劳断裂,因此对齿轮的疲劳强度进行测试是非常重要的。
本文将介绍一种关于齿轮弯曲疲劳强度试验方法,以帮助读者了解如何对齿轮进行有效的疲劳强度测试。
一、试验原理齿轮在实际工作中常常处于扭转状态,因此齿轮齿面上会受到交替弯曲负载,导致齿轮的疲劳断裂。
齿轮弯曲疲劳强度试验就是通过加载一定应力的齿轮样品,进行一定次数的循环载荷,观察齿轮在经过一定循环次数后是否发生疲劳断裂,从而得到齿轮的弯曲疲劳强度数据。
二、试验步骤1. 制备齿轮样品:根据要测试的齿轮种类和规格,选择合适的齿轮样品进行测试。
确保齿轮样品的质量和尺寸符合要求。
2. 振动应力加载:将齿轮样品安装在试验设备上,施加振动应力加载进行弯曲疲劳试验。
根据所需的循环次数和载荷大小,设定试验参数。
3. 观察齿轮状态:在试验过程中,定期观察齿轮的状态,包括表面裂纹、变形等情况。
一旦发现齿轮有异常情况,立即停止试验,并对齿轮进行检查和修复。
4. 记录数据:记录齿轮样品在每个循环周期后的疲劳情况,包括疲劳寿命、发生裂纹的次数等数据。
5. 分析结果:根据试验数据分析齿轮的疲劳断裂情况,计算出齿轮的弯曲疲劳强度指标,评估齿轮的使用寿命和安全性。
三、试验注意事项1. 选用合适的试验设备和工具,确保试验过程中的准确性和可靠性。
2. 控制试验参数,包括载荷大小、循环次数等,确保试验结果具有可靠性。
3. 在试验过程中定期检查齿轮的状态,及时发现问题并采取措施修复。
4. 根据试验结果对齿轮进行评估和改进,提高其疲劳强度和使用寿命。
通过以上介绍,相信读者已经对齿轮弯曲疲劳强度试验方法有了一定的了解。
要保证齿轮的安全可靠运行,进行疲劳强度测试是非常关键的。
齿轮疲劳测试实验报告(3篇)

第1篇一、实验目的本次实验旨在研究齿轮在循环载荷作用下的疲劳性能,通过对齿轮进行疲劳测试,获取其疲劳寿命、疲劳极限和疲劳特性曲线,为齿轮的设计和选材提供理论依据。
二、实验原理齿轮疲劳测试是利用实验方法模拟齿轮在实际工作条件下的疲劳失效过程,通过测量齿轮在循环载荷作用下的应力、应变、裂纹扩展等参数,分析齿轮的疲劳性能。
实验通常采用以下原理:1. 应力控制法:通过控制加载装置,使齿轮承受恒定的应力水平,观察齿轮的疲劳寿命。
2. 应变控制法:通过控制应变,使齿轮承受恒定的应变水平,观察齿轮的疲劳寿命。
3. 频谱控制法:通过控制载荷的频率和幅度,模拟齿轮在实际工作条件下的载荷特性,观察齿轮的疲劳性能。
三、实验设备1. 齿轮疲劳试验机:用于施加循环载荷,模拟齿轮在实际工作条件下的载荷特性。
2. 数据采集系统:用于采集齿轮在疲劳测试过程中的应力、应变、裂纹扩展等参数。
3. 光学显微镜:用于观察齿轮表面裂纹的形态和扩展情况。
4. 硬度计:用于测量齿轮表面的硬度。
四、实验材料本次实验选用材料为45号钢,经过调质处理,硬度为HRC35-40。
五、实验步骤1. 实验前准备:将齿轮加工成标准试样,并进行表面处理,如喷丸处理等。
2. 加载:将齿轮试样安装在疲劳试验机上,按照预定程序施加循环载荷。
3. 数据采集:在实验过程中,实时采集齿轮的应力、应变、裂纹扩展等参数。
4. 裂纹观察:在实验结束后,利用光学显微镜观察齿轮表面裂纹的形态和扩展情况。
5. 硬度测试:在实验结束后,利用硬度计测量齿轮表面的硬度。
六、实验结果与分析1. 疲劳寿命:通过实验数据,计算出齿轮的疲劳寿命,即齿轮在循环载荷作用下发生疲劳失效所需的时间。
2. 疲劳极限:通过实验数据,确定齿轮的疲劳极限,即齿轮在循环载荷作用下能够承受的最大应力水平。
3. 疲劳特性曲线:通过实验数据,绘制齿轮的疲劳特性曲线,分析齿轮的疲劳性能。
实验结果表明,齿轮在循环载荷作用下具有良好的疲劳性能。
齿轮接触疲劳强度试验方法

齿轮接触疲劳强度试验方法(GB/T14229-93)1主题内容与适用范围本标准规定了测定渐开线圆柱齿轮接触疲劳强度的试验方法,以确定齿轮接触承载能力所需的基础数据。
本标准适用于钢、铸铁制造的渐开线圆柱齿轮由齿面点蚀损伤而失效的试验。
其它金属齿轮的接触疲劳强度试验可参照使用。
4试验方法确定齿轮接触疲劳强度应在齿轮试验机上进行试验齿轮的负荷运转试验。
当齿面出现接触疲劳失效或齿面应力循环次数达到规定的循环基数N。
而未失效时(以下简称“越出”),试验终止并获得齿面在试验应力下的一个寿命数据。
当试验齿轮及试验过程均无异常时,通常将该数据称为“试验点”。
根据不同的试验目的,选择小列不同的试验点的组合,经试验数据的统计处理,确定试验齿轮的接触疲劳特性曲线及接触疲劳极限应力。
4.1常规成组法常规成组法用于测定试验齿轮的可靠度-应力-寿命曲线(即R-S-N曲线),求出试验齿轮的接触疲劳极限应力。
试验时取4~5个应力级,每个应力级不少于5个试验点(不包括越出点)。
最高应力有中的各试验点的齿面应力循环次数不少于1×106。
最高应力级与次高应力级的应力间隔为总试验应力范围的40%~50%,随着应力的降低,应力间隔逐渐减少。
最低应力级至少有一个试验点越出。
4.2少试验点组合法少试验点组合法通常用于测定S-N曲线或仅测定极限应力。
试验时试验点总数为7~16个。
测定S-N曲线时,应力级为4~10个,每个应力级取1~4个试验点。
测定极限应力时可采用升降法。
采用正交法进行对比试验时,每个对比因素至少有3个试验点。
5试验条件及试验齿轮5.1齿轮接触疲劳强度试验按下述规定的试验条件和试验齿轮进行(对比试验的研究对象除外),上此可确定试验齿轮的接触疲劳极限应力σHlim。
5.1.1试验条件5.1.1.1试验机试验应使用功率流封闭式结构的齿轮试验机,试验机的性能校核见表A(补充件)。
试验机的中心距一般为90~150mm,试验齿轮线速度为8~16m/s。
齿轮弯曲疲劳强度试验方法
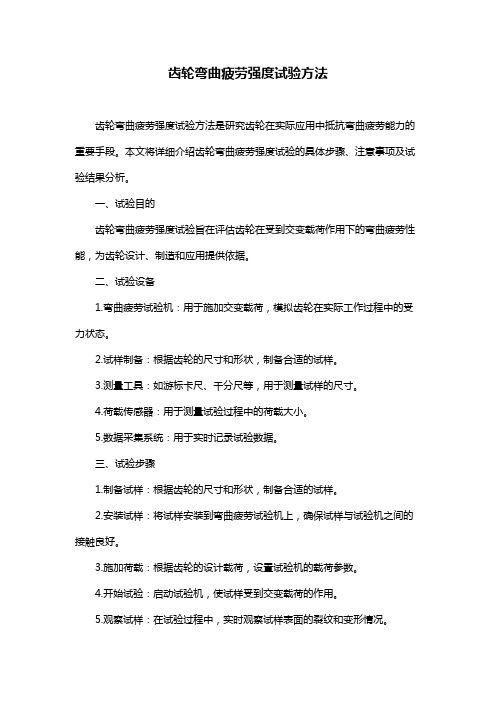
齿轮弯曲疲劳强度试验方法齿轮弯曲疲劳强度试验方法是研究齿轮在实际应用中抵抗弯曲疲劳能力的重要手段。
本文将详细介绍齿轮弯曲疲劳强度试验的具体步骤、注意事项及试验结果分析。
一、试验目的齿轮弯曲疲劳强度试验旨在评估齿轮在受到交变载荷作用下的弯曲疲劳性能,为齿轮设计、制造和应用提供依据。
二、试验设备1.弯曲疲劳试验机:用于施加交变载荷,模拟齿轮在实际工作过程中的受力状态。
2.试样制备:根据齿轮的尺寸和形状,制备合适的试样。
3.测量工具:如游标卡尺、千分尺等,用于测量试样的尺寸。
4.荷载传感器:用于测量试验过程中的荷载大小。
5.数据采集系统:用于实时记录试验数据。
三、试验步骤1.制备试样:根据齿轮的尺寸和形状,制备合适的试样。
2.安装试样:将试样安装到弯曲疲劳试验机上,确保试样与试验机之间的接触良好。
3.施加荷载:根据齿轮的设计载荷,设置试验机的载荷参数。
4.开始试验:启动试验机,使试样受到交变载荷的作用。
5.观察试样:在试验过程中,实时观察试样表面的裂纹和变形情况。
6.记录数据:记录试验过程中的荷载、循环次数等数据。
7.停止试验:当试样出现明显的裂纹或达到预定的循环次数时,停止试验。
四、注意事项1.试样的制备应严格按照齿轮的实际尺寸和形状进行,以保证试验结果的准确性。
2.确保试验机与试样之间的接触良好,避免因接触不良导致的试验误差。
3.在试验过程中,应密切关注试样的裂纹和变形情况,及时记录数据。
4.遵循试验机的操作规程,确保试验安全、顺利进行。
五、试验结果分析1.对比不同齿轮材料的弯曲疲劳强度,为齿轮选材提供依据。
2.分析齿轮设计参数(如模数、齿数等)对弯曲疲劳强度的影响,为优化设计提供参考。
3.研究齿轮制造工艺对弯曲疲劳性能的影响,为改进制造工艺提供指导。
4.通过试验结果,评估齿轮在实际应用中的弯曲疲劳寿命。
总之,齿轮弯曲疲劳强度试验是确保齿轮质量、提高齿轮应用性能的重要手段。
齿轮接触疲劳强度试验
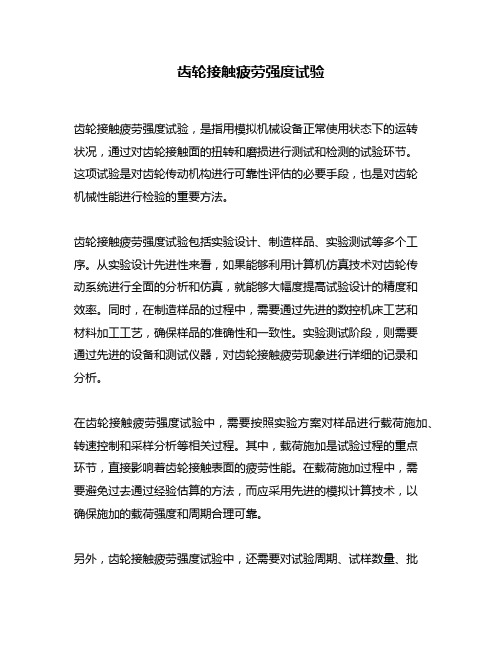
齿轮接触疲劳强度试验
齿轮接触疲劳强度试验,是指用模拟机械设备正常使用状态下的运转
状况,通过对齿轮接触面的扭转和磨损进行测试和检测的试验环节。
这项试验是对齿轮传动机构进行可靠性评估的必要手段,也是对齿轮
机械性能进行检验的重要方法。
齿轮接触疲劳强度试验包括实验设计、制造样品、实验测试等多个工序。
从实验设计先进性来看,如果能够利用计算机仿真技术对齿轮传
动系统进行全面的分析和仿真,就能够大幅度提高试验设计的精度和
效率。
同时,在制造样品的过程中,需要通过先进的数控机床工艺和
材料加工工艺,确保样品的准确性和一致性。
实验测试阶段,则需要
通过先进的设备和测试仪器,对齿轮接触疲劳现象进行详细的记录和
分析。
在齿轮接触疲劳强度试验中,需要按照实验方案对样品进行载荷施加、转速控制和采样分析等相关过程。
其中,载荷施加是试验过程的重点
环节,直接影响着齿轮接触表面的疲劳性能。
在载荷施加过程中,需
要避免过去通过经验估算的方法,而应采用先进的模拟计算技术,以
确保施加的载荷强度和周期合理可靠。
另外,齿轮接触疲劳强度试验中,还需要对试验周期、试样数量、批
次数量等多个因素进行统计分析,以确保得到足够可靠和可行的测试结果。
在试验结果分析过程中,可以通过建立齿轮疲劳数据模型和统计分析模型,对试验结果进行数值化和数学处理,进一步优化试验结果。
总之,齿轮接触疲劳强度试验是对齿轮传动机构进行评估、优化和调整的重要工具,也是检验齿轮机械性能的有效手段。
通过有效的实验设计和多环节的制备、测试与分析过程,可以得到更为准确可信的试验结果,保证齿轮机械产品的质量和性能。
齿轮接触疲劳试验

齿轮接触疲劳试验
齿轮接触疲劳试验是一项重要的试验项目,用于检验齿轮材料的耐用性和寿命,也是评估齿轮性能的一项关键指标。
该试验通过模拟真实的工作环境和工况,对齿轮进行长期的连续载荷试验,观察齿轮的断裂、变形等情况,从而判断齿轮的耐用性和寿命。
齿轮接触疲劳试验一般采用双轮对的测试方式,即将两个齿轮安装在一起,加上适当载荷,通过旋转齿轮来模拟行车工况,重复载荷作用下观察齿轮的变化情况。
此外,还可以加入一些特殊工况,比如不同的温度、湿度等因素,来更真实地模拟真实的工作环境。
齿轮接触疲劳试验的主要步骤包括:选取适当的测试负荷、测试速度和测试时间;制备齿轮样品,并进行表面处理;在测试设备中安装齿轮样品,并进行初始调整;开始测试,观察齿轮的变化情况,并记录数据;分析测试结果,并得出结论。
齿轮接触疲劳试验的结果可用于指导齿轮材料的选择、设计和制造,也可用于评估齿轮的实际工作寿命和可靠性。
通过对多种不同材料、不同设计的齿轮进行接触疲劳测试,可以得出最优的齿轮设计和材料选择方案,从而提高齿轮的性能和寿命,降低故障率和维护成本。
总之,齿轮接触疲劳试验是一项重要的测试项目,可以为齿轮的正确
选择、设计和制造提供指导,也可以为齿轮的实际工作寿命和可靠性
提供保障。
在进行齿轮接触疲劳试验时,需要注意合理选择测试负荷、速度和时间,同时加入适当的特殊工况,以模拟真实的工作环境和工况。
过程中需要对齿轮进行初始调整,并根据测试结果进行分析和评估。
机械设计实验齿轮传动效率及齿轮疲劳实验

机械设计实验—齿轮传动效率及齿轮疲劳实验
二.实验设备及工作原理
2.电动机的输出功率
1) 电动机1为直流调速电机,电动机转子与定轴齿轮箱输 入轴相联,电动机采用外壳悬挂支承结构(既电机外壳可绕支 承轴线转动);
机械设计实验—齿轮传动效率及齿轮疲劳实验
二.实验设备及工作原理
2.电动机的输出功率
2)电动机的输出转矩等于电动机转子与定子之间相互作用 的电磁力矩,与电动机外壳(定子)相联的转矩传感器2提供 的外力矩与作用于定子的电磁力矩相平衡,故转矩传感器测得 的力矩即为电动机的输出转矩T0;电动机转速为n,电动机输 出功率为 P0=n•T0 / 9550 (KW)。
方法。 3、在封闭齿轮实验机上测定齿轮的传动效率。 4、介绍机械功率、效率测定开式实验台,了解一般机械功率、
效率的测试方法。
机械设计实验—齿轮传动效率及齿轮疲劳实验
二.实验设备及工作原理
1、 封闭(闭式)传动系统
1)具有2个完全相同的齿轮箱(悬挂齿轮箱7和定轴齿轮箱 4), 每个齿轮箱内都有2个相同的齿轮相互啮合传动(齿轮9与 9′,齿轮5与5’),两个实验齿轮箱之间由两根轴(一根是用于 储能的弹性扭力轴6,另一根为万向节轴10)相联,组成一个 封闭的齿轮传动系统。
由此计算出封闭系统内传递的功率
机械设计实验—齿轮传动效率及齿轮疲劳实验
二.实验设备及工作原理
4.单对效率为η;
封闭齿轮传动系统内传递的有用功率为P9; 封闭齿轮传动系统内的功率损耗(无用功率)等于电动机输出功率P0, 即:P0=(P9 /η)-P9 η=P9 /(P0+P9)=T9 /(T0+T9 ) 若忽略轴承的效率,系统总效率η包含两级齿轮的传动效率,故单级齿轮
齿轮疲劳试验标准

齿轮疲劳试验标准
齿轮疲劳试验标准有多种,以下提供两种:
1. GB/T :测试目的为模拟齿轮长时间受到交变载荷作用,观察根部是否产生裂纹,并发生断齿现象。
主要通过模拟试验测取轮齿的S-N疲劳强度寿
命曲线,统计分析轮齿的条件疲劳强度均值和样本疲劳强度的标准离差。
该标准为齿轮的设计验证、定型鉴定、批量生产提供评估依据。
2. GB/T:该标准通过齿面点蚀程度来判断齿轮接触疲劳强度试验的失效。
对于表面硬化齿轮,包括渗碳齿轮,当单齿点蚀面积率达到4%或者齿轮副
点蚀面积率达到%,即判定齿面失效。
此外,进行齿轮弯曲疲劳极限安全系数测试时,需要使用专门的试验台架,并根据齿轮材料的实际情况进行设计和制造,真实反映齿轮材料实际的接触和弯曲疲劳特性。
以上内容仅供参考,建议咨询相关行业协会或权威机构,获取最准确的信息。
- 1、下载文档前请自行甄别文档内容的完整性,平台不提供额外的编辑、内容补充、找答案等附加服务。
- 2、"仅部分预览"的文档,不可在线预览部分如存在完整性等问题,可反馈申请退款(可完整预览的文档不适用该条件!)。
- 3、如文档侵犯您的权益,请联系客服反馈,我们会尽快为您处理(人工客服工作时间:9:00-18:30)。
预估,其实现过程如图所示。
该方法已在风电齿轮箱疲劳 试验中使用。
齿轮箱试验台 加载转速扭矩
零件累计疲劳损 伤度 齿轮箱试验台架 损伤度
=
1 齿轮加速疲劳试验
风电齿轮箱加速疲劳试验
4.000E-01 3.500E-01 3.000E-01 2.500E-01 2.000E-01 1.500E-01 1.000E-01 5.000E-02 0.000E+00 1 2 3 4 5 轴承1 轴承2 轴承3 轴承4 轴承5 轴承6 轴承7 轴承8 轴承9
齿轮Βιβλιοθήκη 损伤度 接触0.478 0.012 0.236 0.565
齿轮 弯曲
0.035 0.165 0.324 0.993
损伤度 接触
0.078 0.054 0.113
轴承
1 3 5 7 9
损伤度
0.110 0.101 0.099 0.088 0.045
轴承
2 4 6 8
损伤度
0.113 0.225 0.583 0.052
试验台部分技术参数 额定功率: 2×3300KW 水力测功机功率:双向 7200KW 额定电压: 4.14KV±10% 系统主要技术特点: 变频调速系统采用矢量 控制技术 采用网格技术、数据库 技术 模块设计、易维护 采用统一的组态、变成、 数据管理
齿轮箱性能试验台框图
5 直升机传动系统及其试验平台
用于尾旋翼齿轮箱试验的试验台
RUAG 的MGB齿轮箱试验台: 电缆与齿轮箱上的测量点相连。
兆瓦级机械功率全封闭试验台垂直轴减速器平面布置 兆瓦级机械功率全封闭试验台平行轴减速器平面布置
3 兆瓦级功率全封闭齿轮试验台
3.2 兆瓦级试验台机械加载器 结构独特,性能优良,属过内外首创。
可实现几个千瓦 的无极加载,加载过 程无行程的限制。具 有加载灵敏、稳定等 优点。
4 大功率风电齿轮箱试验台
弯曲
0.178 0.086 0.199
20年设计寿命下轴承疲劳损伤度
试验载荷谱下齿轮损伤度
试验载荷谱下轴承损伤度
2 齿轮系统温度预测
利用传热学和网格法分析技术,分析 齿轮传动系统的拓扑结构,及系统各零部 件间的热量流动关系,创建齿轮传动系统 耦合热分析模型。
减速器内的主要换热情况
节点热平衡方程组
2 齿轮系统温度预测
4 大功率风电齿轮箱试验台
主要技术创新: 解决了双机串、并联运行动 态过程振荡问题。 实现了双机的平滑、可靠运 行。 数据采集系统实现多通道、 多类型的高精度同步采集及 风度的后处理功能。
齿轮箱性能试验台试验现场
5 直升机传动系统及其试验平台
直升机传动系统特点: 高功率密度。 减速比大、传动效率高。 美军“黑鹰”直升机总传 动比为81, 阿帕奇的总传动比为72.1 寿命长、可靠性强。 干运能力强。
美军阿帕奇直升机传动系统原理图
阿帕奇主减速器干运能力为1h、意大利
武装直升机A129干运能力为30min、虎 式直升机干运能力为30min。
美军阿帕奇直升机传动系统
5 直升机传动系统及其试验平台
AS-332超级美洲豹中型运输直升机齿轮箱
Puma旋翼齿轮箱
Puma尾旋翼齿轮箱
直升机减速器试验 齿轮箱试验的内容包括旋翼速度、扭矩、齿轮箱油压、润滑剂温度及 油温。此外,在齿轮箱负载时还将对这些变量进行测试,以测定它们是否 达到极限水平。
齿轮试验方法及装备
1 齿轮加速疲劳试验
目前存在的加速疲劳试验方法有:提高试验加载频率法、删小量 法、线型强化载荷谱法。
线型强化载荷谱法采用 Miner线性累计损伤理论, 提出了加速疲劳寿命试验方 法,实现了在较短时间内齿 轮箱疲劳寿命的试验评价与
线型强化载荷谱法实现过程
齿轮箱载荷 谱
齿轮、轴承应力 循环次数
3 可变中心距功率封闭齿轮试验台
试验齿轮箱中心距变化 时,陪试齿轮箱不发生任何 变化。与活动工作台相连的 陪试齿轮箱可以通过活动工
作台轨道的移动来适应受试
齿轮箱中心距的变化。
A为陪试齿轮箱,B为试验齿轮 箱,T为加载器,M为驱动电机
3 兆瓦级机械功率全封闭齿轮试验台
3.1 试验台结构及工作原理 采用机械功率全封闭结构。机械 功率全封闭式试验台中电动机能耗仅 为封闭功率的10%左右,较电封闭结 构更节能。该技术属于国内首创。