齿轮疲劳试验多变的原因分析
齿轮弯曲疲劳强度试验方法

齿轮弯曲疲劳强度试验方法全文共四篇示例,供读者参考第一篇示例:齿轮在机械设备中起着至关重要的作用,它们通过齿轮传动来实现机械运动,比如汽车的变速箱、风力发电机和其他机械设备都离不开齿轮。
齿轮在长时间运作中会受到各种力的作用,容易发生疲劳断裂,因此对齿轮的疲劳强度进行测试是非常重要的。
本文将介绍一种关于齿轮弯曲疲劳强度试验方法,以帮助读者了解如何对齿轮进行有效的疲劳强度测试。
一、试验原理齿轮在实际工作中常常处于扭转状态,因此齿轮齿面上会受到交替弯曲负载,导致齿轮的疲劳断裂。
齿轮弯曲疲劳强度试验就是通过加载一定应力的齿轮样品,进行一定次数的循环载荷,观察齿轮在经过一定循环次数后是否发生疲劳断裂,从而得到齿轮的弯曲疲劳强度数据。
二、试验步骤1. 制备齿轮样品:根据要测试的齿轮种类和规格,选择合适的齿轮样品进行测试。
确保齿轮样品的质量和尺寸符合要求。
2. 振动应力加载:将齿轮样品安装在试验设备上,施加振动应力加载进行弯曲疲劳试验。
根据所需的循环次数和载荷大小,设定试验参数。
3. 观察齿轮状态:在试验过程中,定期观察齿轮的状态,包括表面裂纹、变形等情况。
一旦发现齿轮有异常情况,立即停止试验,并对齿轮进行检查和修复。
4. 记录数据:记录齿轮样品在每个循环周期后的疲劳情况,包括疲劳寿命、发生裂纹的次数等数据。
5. 分析结果:根据试验数据分析齿轮的疲劳断裂情况,计算出齿轮的弯曲疲劳强度指标,评估齿轮的使用寿命和安全性。
三、试验注意事项1. 选用合适的试验设备和工具,确保试验过程中的准确性和可靠性。
2. 控制试验参数,包括载荷大小、循环次数等,确保试验结果具有可靠性。
3. 在试验过程中定期检查齿轮的状态,及时发现问题并采取措施修复。
4. 根据试验结果对齿轮进行评估和改进,提高其疲劳强度和使用寿命。
通过以上介绍,相信读者已经对齿轮弯曲疲劳强度试验方法有了一定的了解。
要保证齿轮的安全可靠运行,进行疲劳强度测试是非常关键的。
汽车变速器齿轮疲劳寿命试验强化系数计算分析

汽车变速器齿轮疲劳寿命试验强化系数计算分析栾振;卢剑伟;赵方洲;王涛;程建羊【摘要】以某SUV手动变速器齿轮为研究对象,在一般公路和试验场强化道路、山路和高环路上进行了栽荷谱采集.用雨流计数法得到了载荷的分布形式,采用数理统计方法推断和检验了载荷的分布规律,并将采集到的载荷分为8级载荷谱.将此载荷谱施加到变速器齿轮轴系的多体动力学模型中,得到了关键节点的应力.用Miner 理论计算了各挡齿轮在各个工况下的损伤,从而得到了各种试验场路面和变速器总成台架相对于一般道路的强化系数,对汽车耐久性试验的组织实施和汽车试验场的设计提供了重要依据.【期刊名称】《农业装备与车辆工程》【年(卷),期】2019(057)002【总页数】5页(P9-13)【关键词】疲劳可靠性;载荷谱;强化系数;雨流计数法【作者】栾振;卢剑伟;赵方洲;王涛;程建羊【作者单位】230009 安徽省合肥市合肥工业大学汽车与交通工程学院;230009 安徽省合肥市合肥工业大学汽车与交通工程学院;230009 安徽省合肥市合肥工业大学汽车与交通工程学院;230601 安徽省合肥市江淮汽车集团股份有限公司技术中心;230601 安徽省合肥市江淮汽车集团股份有限公司技术中心【正文语种】中文【中图分类】U463.2120 引言汽车道路可靠性试验是考察和评价汽车可靠性的最终技术措施和手段。
为了缩短汽车研发和试验的周期,道路可靠性试验一般都在配备有各类强化道路的汽车试验场进行。
为了使道路可靠性试验里程与设计里程之间有可比性,需要确定各种试验场路面对于一般道路的强化系数。
强化系数指某一汽车零部件在规定条件下达到相同程度的破坏时,该车在一般道路上行驶里程与强化道路上可靠性试验的行驶里程的比值[1],即K=Sp/S。
由于不同零部件的载荷谱不同,同一强化路下不同零部件的强化系数也不相同。
针对试验场强化系数的确定方法,国内外学者进行了大量研究,并取得了很多成果[2-4]。
齿轮弯曲疲劳寿命系数

齿轮弯曲疲劳寿命系数齿轮是机械传动中常见的零件,广泛应用于机械装置和设备中。
作为常规的机械部件,齿轮需要具备极高的稳定性和耐久性,才能够保证其正常运行和服务寿命。
而齿轮弯曲疲劳寿命系数是刻画齿轮性能的一个指标,本文将详细探讨齿轮弯曲疲劳寿命系数的相关内容。
1. 齿轮弯曲疲劳寿命系数的定义齿轮弯曲疲劳寿命系数是指在齿轮传动装置的设计寿命内,齿轮齿根处应力的分布与疲劳寿命之间的关系。
齿轮弯曲疲劳寿命系数越大,即表示齿轮具备更高的耐久性和可靠性,能够承受更大的工作负荷和更长时间的使用寿命。
2. 影响齿轮弯曲疲劳寿命系数的因素齿轮弯曲疲劳寿命系数的大小受到多种因素的影响,主要包括以下几个方面:(1)齿轮材料齿轮材料的物理性能和力学性能对齿轮弯曲疲劳寿命系数的影响非常明显。
一般来说,强度高、韧性好、疲劳寿命长、组织均匀的材料更适合作为齿轮材料,能够提高齿轮弯曲疲劳寿命系数。
(2)齿轮的设计几何参数齿轮的设计几何参数也会对齿轮弯曲疲劳寿命系数产生较大的影响。
齿轮参数的合理设计可以减小齿轮齿根处的应力集中程度,从而提高齿轮弯曲疲劳寿命系数。
(3)负荷条件负荷条件是齿轮弯曲疲劳寿命系数的另一个重要影响因素。
在负荷条件相同的情况下,齿轮弯曲疲劳寿命系数越大,表示齿轮具备更好的承载能力和耐久性。
(4)轴承和润滑条件轴承和润滑条件是影响齿轮弯曲疲劳寿命系数的另一因素。
良好的轴承和润滑条件有助于减少齿轮的磨损和摩擦,降低应力水平,提高齿轮弯曲疲劳寿命系数。
3. 齿轮弯曲疲劳寿命系数的测试方法齿轮弯曲疲劳寿命系数的测试是对齿轮性能进行评估和确认的重要手段。
一般采用模拟试验或数值模拟两种方法进行测试,具体方法如下:(1)模拟试验模拟试验是指利用齿轮模拟器或齿轮试验台等设备进行实物测试的方法。
通过不断重复负荷的作用,观察齿轮的磨损程度和变形情况,推算齿轮弯曲疲劳寿命系数和寿命预测模型。
(2)数值模拟数值模拟是通过建立齿轮弯曲疲劳寿命的有限元模型,采用ANSYS、ABAQUS等有限元软件进行计算、模拟和预测的方法。
变速器总成疲劳试验故障识别及应用
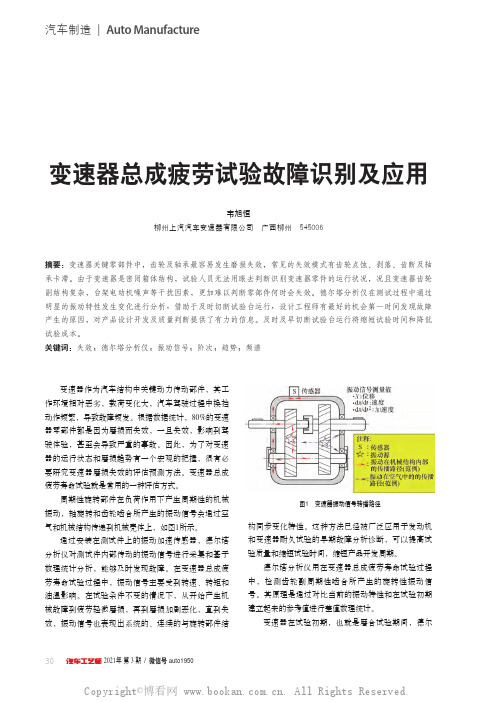
也分为DA和CP报警模式。 DA模式监控变速器内活动件的细微变化趋势,如
齿轮、轴承内外圈及滚动体表面轻微磨损和点蚀;CP 模式监控变速器运行过程中实时振动剧烈变化信号, 如齿轮副轮齿突然崩断,就会触发CP报警。
DA模式中,有多种评价指标来分析整体振动情 况,如各个自振动传感器和转速传感器 的数据,借助快速傅里叶变换将记录到的机械振动信 号转换为频谱。
图3 二挡工况运行趋势指数
微信号 auto1950 / 2021年 第 3 期
31
Copyright©博看网 . All Rights Reserved.
变速器在试验初期,也就是磨合试验期间,德尔
30
2021年 第 3 期 / 微信号 auto1950
Copyright©博看网 . All Rights Reserved.
Auto Manufacture | 汽车制造
塔分析仪会自动采集振动信号,通过傅里叶变换,达 到自动学习次数后,形成含有上下限公差的容限带。 后期总成疲劳试验过程所产生的振动信号如果都分布 在容限带内,则可以判断变速器总成试验是平稳正常 进行。
汽车制造 | Auto Manufacture
变速器总成疲劳试验故障识别及应用
韦旭恒 柳州上汽汽车变速器有限公司 广西柳州 545006
摘要:变速器关键零部件中,齿轮及轴承最容易发生磨损失效,常见的失效模式有齿轮点蚀、剥落、齿断及轴 承卡滞。由于变速器是密闭箱体结构,试验人员无法用眼去判断识别变速器零件的运行状况,况且变速器齿轮 副结构复杂,台架电动机噪声等干扰因素,更加难以判断零部件何时会失效。德尔塔分析仪在测试过程中通过 明显的振动特性发生变化进行分析,借助于及时切断试验台运行,设计工程师有最好的机会第一时间发现故障 产生的原因,对产品设计开发及质量判断提供了有力的信息。及时及早切断试验台运行将缩短试验时间和降低 试验成本。 关键词:失效;德尔塔分析仪;振动信号;阶次;趋势;频谱
齿轮啮合传动时,接触疲劳强度不相等,而弯曲疲劳强度相等
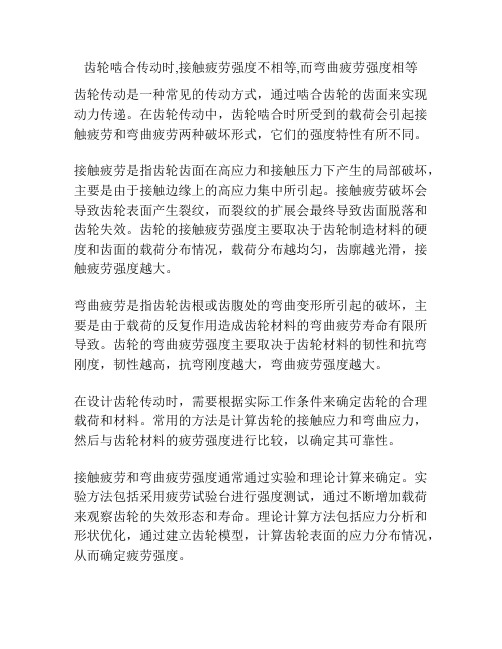
齿轮啮合传动时,接触疲劳强度不相等,而弯曲疲劳强度相等齿轮传动是一种常见的传动方式,通过啮合齿轮的齿面来实现动力传递。
在齿轮传动中,齿轮啮合时所受到的载荷会引起接触疲劳和弯曲疲劳两种破坏形式,它们的强度特性有所不同。
接触疲劳是指齿轮齿面在高应力和接触压力下产生的局部破坏,主要是由于接触边缘上的高应力集中所引起。
接触疲劳破坏会导致齿轮表面产生裂纹,而裂纹的扩展会最终导致齿面脱落和齿轮失效。
齿轮的接触疲劳强度主要取决于齿轮制造材料的硬度和齿面的载荷分布情况,载荷分布越均匀,齿廓越光滑,接触疲劳强度越大。
弯曲疲劳是指齿轮齿根或齿腹处的弯曲变形所引起的破坏,主要是由于载荷的反复作用造成齿轮材料的弯曲疲劳寿命有限所导致。
齿轮的弯曲疲劳强度主要取决于齿轮材料的韧性和抗弯刚度,韧性越高,抗弯刚度越大,弯曲疲劳强度越大。
在设计齿轮传动时,需要根据实际工作条件来确定齿轮的合理载荷和材料。
常用的方法是计算齿轮的接触应力和弯曲应力,然后与齿轮材料的疲劳强度进行比较,以确定其可靠性。
接触疲劳和弯曲疲劳强度通常通过实验和理论计算来确定。
实验方法包括采用疲劳试验台进行强度测试,通过不断增加载荷来观察齿轮的失效形态和寿命。
理论计算方法包括应力分析和形状优化,通过建立齿轮模型,计算齿轮表面的应力分布情况,从而确定疲劳强度。
为了提高齿轮的疲劳强度,可以采取以下措施:1. 优化齿轮的几何形状,比如增大齿距、增加齿数、优化齿廓曲线等,以减小齿轮齿面上的应力集中。
2. 选择高强度、高韧性的材料,比如合金钢、渗碳钢等,以提高齿轮的疲劳强度。
3. 控制齿轮的加工工艺,比如采用精密加工、硬化处理等,以提高齿轮的表面质量和耐磨性。
总之,接触疲劳和弯曲疲劳是齿轮传动过程中两种不同的破坏形式,其强度特性有所不同。
在设计齿轮传动时,应根据实际工作条件和要求,综合考虑接触疲劳和弯曲疲劳强度,选择合适的材料和几何形状,以确保齿轮传动的可靠性和寿命。
齿轮弯曲疲劳强度试验方法
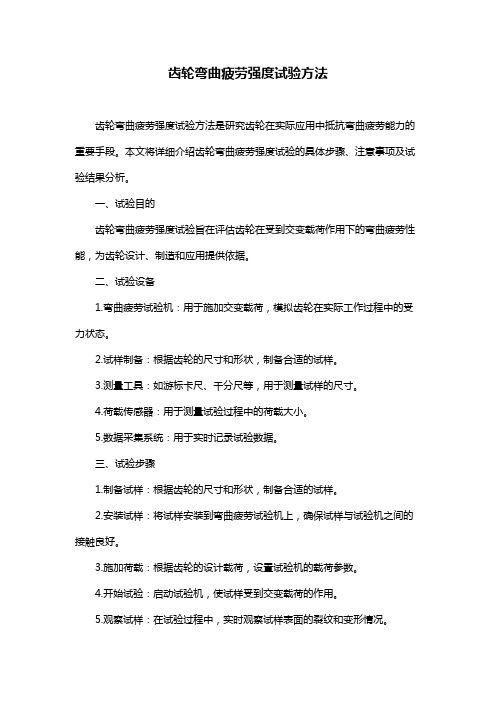
齿轮弯曲疲劳强度试验方法齿轮弯曲疲劳强度试验方法是研究齿轮在实际应用中抵抗弯曲疲劳能力的重要手段。
本文将详细介绍齿轮弯曲疲劳强度试验的具体步骤、注意事项及试验结果分析。
一、试验目的齿轮弯曲疲劳强度试验旨在评估齿轮在受到交变载荷作用下的弯曲疲劳性能,为齿轮设计、制造和应用提供依据。
二、试验设备1.弯曲疲劳试验机:用于施加交变载荷,模拟齿轮在实际工作过程中的受力状态。
2.试样制备:根据齿轮的尺寸和形状,制备合适的试样。
3.测量工具:如游标卡尺、千分尺等,用于测量试样的尺寸。
4.荷载传感器:用于测量试验过程中的荷载大小。
5.数据采集系统:用于实时记录试验数据。
三、试验步骤1.制备试样:根据齿轮的尺寸和形状,制备合适的试样。
2.安装试样:将试样安装到弯曲疲劳试验机上,确保试样与试验机之间的接触良好。
3.施加荷载:根据齿轮的设计载荷,设置试验机的载荷参数。
4.开始试验:启动试验机,使试样受到交变载荷的作用。
5.观察试样:在试验过程中,实时观察试样表面的裂纹和变形情况。
6.记录数据:记录试验过程中的荷载、循环次数等数据。
7.停止试验:当试样出现明显的裂纹或达到预定的循环次数时,停止试验。
四、注意事项1.试样的制备应严格按照齿轮的实际尺寸和形状进行,以保证试验结果的准确性。
2.确保试验机与试样之间的接触良好,避免因接触不良导致的试验误差。
3.在试验过程中,应密切关注试样的裂纹和变形情况,及时记录数据。
4.遵循试验机的操作规程,确保试验安全、顺利进行。
五、试验结果分析1.对比不同齿轮材料的弯曲疲劳强度,为齿轮选材提供依据。
2.分析齿轮设计参数(如模数、齿数等)对弯曲疲劳强度的影响,为优化设计提供参考。
3.研究齿轮制造工艺对弯曲疲劳性能的影响,为改进制造工艺提供指导。
4.通过试验结果,评估齿轮在实际应用中的弯曲疲劳寿命。
总之,齿轮弯曲疲劳强度试验是确保齿轮质量、提高齿轮应用性能的重要手段。
齿轮接触疲劳强度试验
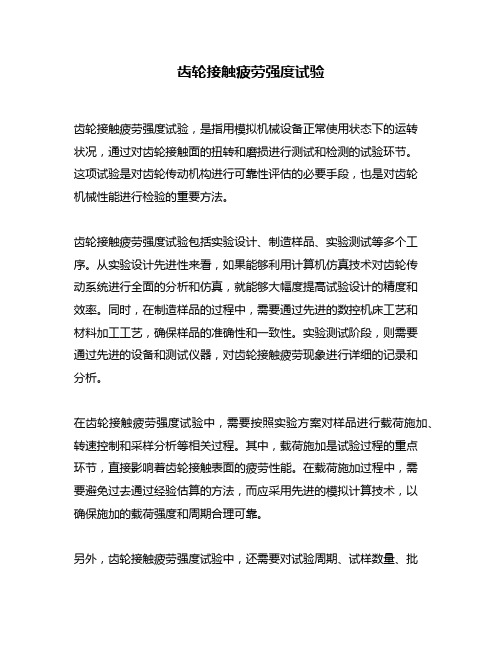
齿轮接触疲劳强度试验
齿轮接触疲劳强度试验,是指用模拟机械设备正常使用状态下的运转
状况,通过对齿轮接触面的扭转和磨损进行测试和检测的试验环节。
这项试验是对齿轮传动机构进行可靠性评估的必要手段,也是对齿轮
机械性能进行检验的重要方法。
齿轮接触疲劳强度试验包括实验设计、制造样品、实验测试等多个工序。
从实验设计先进性来看,如果能够利用计算机仿真技术对齿轮传
动系统进行全面的分析和仿真,就能够大幅度提高试验设计的精度和
效率。
同时,在制造样品的过程中,需要通过先进的数控机床工艺和
材料加工工艺,确保样品的准确性和一致性。
实验测试阶段,则需要
通过先进的设备和测试仪器,对齿轮接触疲劳现象进行详细的记录和
分析。
在齿轮接触疲劳强度试验中,需要按照实验方案对样品进行载荷施加、转速控制和采样分析等相关过程。
其中,载荷施加是试验过程的重点
环节,直接影响着齿轮接触表面的疲劳性能。
在载荷施加过程中,需
要避免过去通过经验估算的方法,而应采用先进的模拟计算技术,以
确保施加的载荷强度和周期合理可靠。
另外,齿轮接触疲劳强度试验中,还需要对试验周期、试样数量、批
次数量等多个因素进行统计分析,以确保得到足够可靠和可行的测试结果。
在试验结果分析过程中,可以通过建立齿轮疲劳数据模型和统计分析模型,对试验结果进行数值化和数学处理,进一步优化试验结果。
总之,齿轮接触疲劳强度试验是对齿轮传动机构进行评估、优化和调整的重要工具,也是检验齿轮机械性能的有效手段。
通过有效的实验设计和多环节的制备、测试与分析过程,可以得到更为准确可信的试验结果,保证齿轮机械产品的质量和性能。
解决设计齿轮传动时齿面接触疲劳强度不够的问题
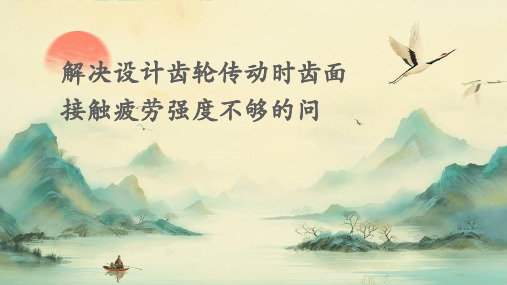
理论研究
深入研究齿面接触疲劳的机理,建立更为精确的理论模型,为设 计提供更为准确的指导。
新材料与新工艺
探索和开发具有更高强度、耐磨性和耐热性的新材料和加工工艺。
智能化设计
利用人工智能和数值模拟技术,实现齿轮传动的智能化设计和优化。
对实际应用的建议
优化设计
01
在设计阶段充分考虑齿面接触疲劳强度,通过优化几何参数和
03
解决策略与方案
材料选择与处理
选用高强度材料
选择具有高强度和耐磨性的材料, 如合金钢、不锈钢等,以提高齿 面的抗疲劳性能。
材料热处理
通过适当的热处理工艺,如淬火、 回火等,改善材料的硬度和韧性, 增强齿面的耐磨性和抗疲劳性能。
表面强化处理
采用喷丸、碾压、渗碳淬火等表面 强化处理技术,提高齿面的硬度和 抗疲劳性能。
解决设计齿轮传动时齿面 接触疲劳强度不够的问
• 问题概述 • 问题原因分析 • 解决策略与方案 • 案例分析 • 结论与建议
01
问题概述
齿面接触疲劳强度的定义
01
齿面接触疲劳强度是指齿轮在接 触应力作用下抵抗疲劳破坏的能 力。
02
齿面接触疲劳强度取决于齿轮材 料的机械性能、热处理方式、表 面处理、齿轮参数以及工作条件 等因素。
优化设计
改进齿形设计
优化齿形参数,减小应力 集中,改善齿面接触状况, 降低接触疲劳应力。
增加润滑设计
合理设计润滑系统,确保 齿轮在传动过程中得到充 分润滑,减少摩擦和磨损。
优化装配设计
确保齿轮装配精度,减小 装配误差,提高齿轮传动 的平稳性和可靠性。
制造工艺改进
精密加工
质量检测与控制
采用先进的加工设备和工艺,提高齿 轮的加工精度和表面光洁度,减小齿 轮的制造误差。
- 1、下载文档前请自行甄别文档内容的完整性,平台不提供额外的编辑、内容补充、找答案等附加服务。
- 2、"仅部分预览"的文档,不可在线预览部分如存在完整性等问题,可反馈申请退款(可完整预览的文档不适用该条件!)。
- 3、如文档侵犯您的权益,请联系客服反馈,我们会尽快为您处理(人工客服工作时间:9:00-18:30)。
齿轮疲劳试验数据多变的原因分析Causes of Variability in Gear Fatigue TestingGregory A.Fett and Michael A .FollisDana Corporation ,Torque Traction Technologies Group【摘要】零件的疲劳试验数据变化很大,高强度表面渗碳硬化零件齿轮更是如此。
长期的大量齿轮疲劳试验数据表明,在相同试验条件下,齿轮的高疲劳寿命与低疲劳寿命比较,比值可达9:1。
本文介绍了一种系统分析方法,以确定引起齿轮疲劳试验数据多变的原因。
本文主要通过准双曲面锥齿轮组的动态疲劳试验研究不同原因对疲劳试验影响的大小,每次试验间隔为6个月。
研究结果表明动态试验设备、热处理、切齿以及齿轮用钢都会对疲劳试验寿命产生一定的影响。
为了研究金相组织与疲劳试验寿命的联系,试验也对几种金相组织因素进行检查。
简介齿轮疲劳试验数据会产生相当大的散差和变化。
在过去30多年驱动桥和变速器工业生产中,测试时间跨度较长的大量试验结果表明,试件的高疲劳寿命VS低疲劳寿命的比值达到9:1是普遍的。
这些试验数据都是在相同试验条件下,测试相同数量的试件得到的。
如果试验测试涉及到多种材料因素,那么在任何给定的应力应变条件下,试验室样品的测试数据比值会有10:1或更大的差别。
基于此种原因,人们很难甚至几乎不可能对两组不同的数据是否真的存在差别作出判断。
试验设计本试验的目的是为了确定齿轮疲劳试验数据变化的潜在原因,并定量分析各种原因对试验数据变化的影响。
试验采用的从动齿轮毛坯均取自同一钢锭,并经过相同的热处理,然后分为三类。
部分毛坯在相同时间内完成切齿加工、渗碳热处理及后续加工,编号为A,动态试验时间间隔为6个月,目的是确定不同时间和试验设备会对试验数据产生多大的变化。
部分齿轮编号为B,与A组试件在同一时间完成切齿加工,但不立即进行渗碳热处理,而是时间间隔6个月进行渗碳热处理及后续加工,然后与A组试件一同进行动态试验,除热处理外,其余工艺与A组试件的相同,目的是确定渗碳热处理对试验数据变化的影响。
C 组齿轮试件分别完成毛坯准备和切齿加工、渗碳热处理以及后续加工等工序,时间间隔为6个月,与A组和B组试件一起进行动态试验,除切齿外,其余工艺基本与B组试件相同,目的是确定切齿对试验数据变化有多大的影响。
最后,D 组试件是随机选择的现生产试件,时间间隔6个月,并与A、B、C组试件一起进行动态试验,选择的每批试件采用相同牌号的材料和热处理工艺,目的是研究包括渗碳用钢在内的多种原因的影响。
为了确定其它因素是否会对试验结果产生影响,试验也对几组试验后的齿轮进行金相组织分析。
数据表1中列出了试验的原始数据,每组试验有5个样品,其中有一组为原始基准试验,与A组一起进行,间隔6个月后,则进行一轮A、B、C、D组齿轮试验。
每组齿轮的试验随机安排,间隔为6个月,以保证试验数据的客观性。
表1中前两组数据是在同一试验机上进行,三、四组数据分别在两个不同试验机上进行,其他试验条件一致。
最低的疲劳寿命为11.82万次,最高的疲劳寿命为49.5万次,比值为4.2:1。
表2列出每组试验数据的平均值和标准差,标准差的范围为12901次~92124次,然而,大部分数据标准差都近似处于35000次~65000次之间,同组最下方列出的数值为全组数据的平均值和标准差。
表格最底部的平均值和标准差的是各组数据组合后计算出的平均值和标准差,A组主要考察的是在其他条件恒定不变时试验设备引起的试验数据变化,B组考察的是试验设备和热处理引起的试验数据变化,C组考察的是试验设备、热处理和切齿引起的试验数据变化,D组是包括材料在内的多种因素引起的试验数据变化。
显而易见,随着每种影响原因的加入,标准差不断增大。
原始基准试验A1的标准差为52555次。
A组所有试验数据的标准差为54928次,A与B组合的标准差为67446次,A、B和C组合的标准方差为75554次,最后,所有组包括D的标准差为84947次,引起标准差较大增长的原因依次为B、C、D,最后是A.为确定每种原因的影响,我们做了以下工作。
首先假设每个试验平均值变化都是由上述四种原因引起,通过正态处理数据,即可消除以上原因的影响,得到与基准试验组A1相同的平均值,并可以确定65个试件的标准差为45971次。
如果排除了试验数据的变化,这一数值即可作为基准的标准差,我们认为以上假设的原因只能影响每组试验的平均值而不影响标准差。
接着,我们考察由于每种原因引起的标准差超过基准标准差的增长,见表3所示。
试验装备引起的标准差从45971次增长54928次,即增长到1.19,占总标准差增长的20%。
我们用相同的逻辑可确定热处理为33%,切齿为18%,材料为27%,以上数据说明引起试验数据变化的最大原因是热处理和材料。
另外我们看看数据的韦布尔分析,表4列出了齿轮的B10、B50、B90寿命,以及每组试验的斜度,齿轮的B50寿命非常接近表1平均寿命的近似值。
表4也列出了组合后韦布尔分析的各项数据,这些数据与表3列出的数据非常相近,在这里,斜度常用于量度变化,而不是标准差。
斜度越陡峭试验数据的变化也越小。
如果采用前文与标准差相同的逻辑,能够看出随着影响原因的加入斜度有所降低。
唯一的例外是A组的斜度大于最初基准组A1的斜度,表示试验设备A 对渗碳齿轮的试验数据变化没有表现出明显的影响,其他三类原因,D会引起试验较大的变化,其次是B和C。
表5列出了一种方差分析方法ANOV A,用于确定我们所看到的疲劳寿命数据的是否差异显著。
如果F值超过了F标准值,则认为数据差异明显。
数据显示A组试件的数据差异不明显,意味着试验设备引起的数据变化不显著。
ANOV A 列出的A组和B组,A组和C组的数据差异明显,这意味着热处理和切齿联同热处理两者都能明显增加试验数据变化。
切齿影响的近似求法是通过比较B组和C组得到,ANOV A表示这些数据也有较明显差异,事实上,基于F值和F标准值分析,切齿是试验变化最主要的影响因素。
列出另外的两组数据是A组和D 组、C组和D组的比较,两者的数据也有明显差异,这也意味着热处理、切齿和渗碳用钢三者的结合与渗碳钢联同热处理组合对试验数据变化的影响近似。
热处理、切齿和渗碳钢是三个最主要影响原因。
接下来的数据是B组中3个试件和C组中3个试件的相互比较,数据没有表现出多大的差异。
B组包含了试验和热处理两种原因,同样,C组也包含了试验、热处理和切齿三种原因。
最后的比较的是所有试件组,很明显,数据暗示试验之间差异明显。
最后,我们比较齿轮的B50寿命的数据,表6列出多组齿轮的B50寿命的平均差,其中包括A,A和B组合,A、B和C组合以及A、B、C和D组合的数据。
正如前面提到的数据,随着每种原因的加入,试验数据变化也随着增大。
另外,表6也列出了B-C(B2-A2、B3-A3、B4-C4)和C-B的B50寿命数据的差异,这两组数据将用于近似分析热处理和切齿因素单独对试验数据变化的影响。
采用相同的逻辑,列出的数据表明试验设备的影响占13%,热处理占19%,切齿占38%,而渗碳用钢占30%,也就是说,对试验数据变化的最大的影响是切齿和用材。
讨论显然,以上所探讨原因都会增加齿轮疲劳试验数据的变化。
依靠上述方法进行数值分析,每种原因影响的准确比例值还存在争议。
独立试验的B50寿命最高为43.333万次,最小为16.7255万次,比值为2.6:1。
前面曾提到单个试样的最大寿命为49.5万次,最小寿命为11.82万次,比值为4.2:1。
以上所有的试验都是在理想的条件下进行的,试验数据的如此变化一至于无法有效应用齿轮疲劳试验数据。
比如,在生产的初始阶段,获得的齿轮B50寿命为43.3万次,后来又得到了16.7万次的试验结果,这时就会怀疑什么地方出现差错,事实上并非如此,所有的试验数据都属于正常变化。
在工业生产中,类似的情况也会导致大量时间和精力的浪费。
相反的事情也有可能发生,就是误导我们相信已经找到提高齿轮寿命的途径。
为有效的应用齿轮疲劳数据,必须通过长期的大量的不同试验,建立起一个好的数据库。
例如,长达20多年的齿轮试验结果表明,本次试验采用齿轮的B50寿命约为27.5万次,并且齿轮的寿命范围在10万次到70万次之间波动,根据这一依据,本次试验得到的试验数据都处于这一范围。
以前,曾采用优质钢进行相同齿轮的试验,最初的试验结果显示疲劳寿命有很大提高,齿轮的B50寿命几乎达到79.9万次,随后进行了第二次验证试验,采用同牌号不同炉号的材料,试验结果仅为27.9万次,非常接近这种齿轮历史的B5寿命。
同样,相同牌号另一炉号的材料,第三次试验结果为34.2万次。
以上结论表明,采用优质钢能明显提高齿轮寿命,然而,后来的试验数据都没能达到最初的试验结果。
通过三个试验数据可共同得出一个较清晰的趋向,即优质钢可以提高齿轮寿命,但试验数据出现了较大交叉。
金相组织的因素假设我们归结出试验数据变化主要是由本试验考察的四种原因引起,但试验数据依然还有一定的变化,前面曾提高试验的标准差为4.5971万次。
本试验的另一目的是确定金相组织特性是否成为试验数据变化的原因,数据都源于试验齿轮组的主动轮失效件。
图1表示齿根有效硬化层深与疲劳寿命的关系,没有发现有什么直接联系。
图2表示表面硬度与疲劳寿命的关系,同样也没有联系。
图3表示的是齿根心部硬度与疲劳寿命的关系,也是没有联系,图4表示晶间氧化深度与疲劳寿命的关系,也没有表现出和疲劳寿命的联系。
图5表示的是表面非马氏体组织与疲劳寿命的关系,这也不是什么重要的影响原因。
检验的金相组织,很明显,没有一项能够对基准试验数据的变化做出合理解释。
结论齿轮疲劳试验数据必然会产生相当大的散差和变化。
本次试验的目的是考察影响疲劳试验的四种原因,以确定每种原因对试验数据变化有多大影响。
三个最主要的原因分别是热处理、切齿以及渗碳齿轮用钢,另外一个原因是试验设备,这些原因都有助于解释试验数据的一些变化。
试验进行了13组齿轮试验,疲劳寿命范围为11.8万次~49.5万次,13组齿轮试验的韦布尔的B50寿命范围为16.255万次~43.3357万次,这些数据都是齿轮疲劳试验产生的一个典型变化,必须考虑到试验数据的变化才能合理利用。
在齿轮疲劳试验中,一组数据仅为另一组数据寿命的一半,并不是意味着什么事情发生改变。
通过长期的多组试验,建立一种必要数据库是非常必要的。
除了本试验研究的四种原因,试验数据依然有一定的变化,通过检查齿轮的几种金相组织,考察是否能够对基准数据的变化提供一个合理的解释。
检验的因素包括齿根有效硬化层深、表面硬度、心部硬度、表面晶间氧化物和非马氏体转变,结果表明,这些因素都无法合理解释这些变化。