齿轮接触疲劳强度试验方法
标准直齿圆柱齿轮齿面接触疲劳强度计算
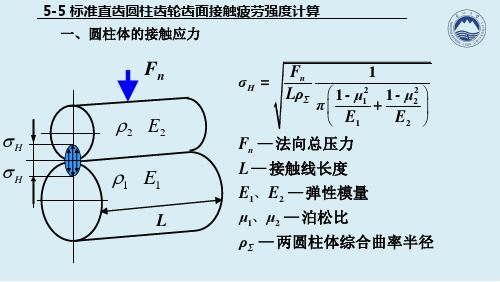
三、标准直齿圆柱齿轮齿面接触疲劳强度
1.齿轮齿面接触疲劳强度条件
H ZH ZE Z
2KT1 bd12
u u
1
[ H
]
2.按齿面接触疲劳强度的设计式
a
u 1
3
KT1
2 a u
ZH ZE Z
H
2
mm
d1
3
2KT1
d
u 1
u
ZH ZE Z
H
2
mm
a
b a
;
d
ห้องสมุดไป่ตู้
b d1
5-5 标准直齿圆柱齿轮齿面接触疲劳强度计算 三、标准直齿圆柱齿轮齿面接触疲劳强度
5-5 标准直齿圆柱齿轮齿面接触疲劳强度计算 一、圆柱体的接触应力
H
Fn 2 E2
σH =
Fn
1
LρΣ
π
1
- μ12 E1
+ 1 - μ22 E2
Fn — 法向总压力
H
1 E1
L — 接触线长度 E1、E2 — 弹性模量
L
μ1、μ2 — 泊松比
ρΣ — 两圆柱体综合曲率半径
5-5 标准直齿圆柱齿轮齿面接触疲劳强度计算
5-5 标准直齿圆柱齿轮齿面接触疲劳强度计算 二、标准直齿圆柱齿轮齿面接触应力 4.齿轮齿面接触应力
弹性系数:ZE
1
[(1 12 ) (1 22 )]
E1
E2
表5 5
节点区域系数:ZH
2
sin cos
齿轮齿面接触应力
H ZH ZE Z
2KT1 u 1 bd12 u
N/mm2
5-5 标准直齿圆柱齿轮齿面接触疲劳强度计算
齿轮啮合传动时,接触疲劳强度不相等,而弯曲疲劳强度相等
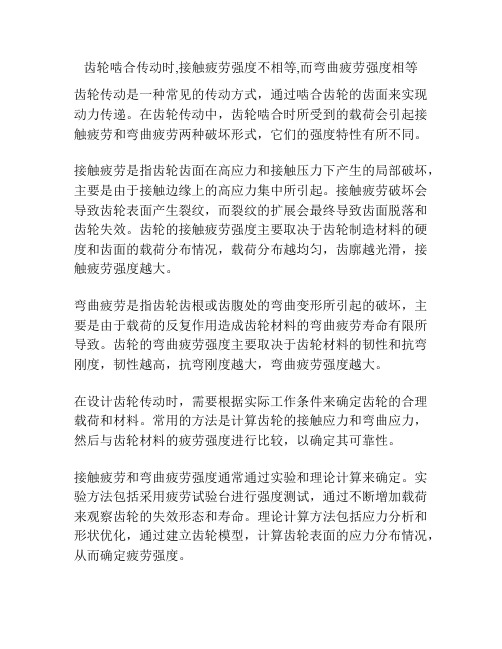
齿轮啮合传动时,接触疲劳强度不相等,而弯曲疲劳强度相等齿轮传动是一种常见的传动方式,通过啮合齿轮的齿面来实现动力传递。
在齿轮传动中,齿轮啮合时所受到的载荷会引起接触疲劳和弯曲疲劳两种破坏形式,它们的强度特性有所不同。
接触疲劳是指齿轮齿面在高应力和接触压力下产生的局部破坏,主要是由于接触边缘上的高应力集中所引起。
接触疲劳破坏会导致齿轮表面产生裂纹,而裂纹的扩展会最终导致齿面脱落和齿轮失效。
齿轮的接触疲劳强度主要取决于齿轮制造材料的硬度和齿面的载荷分布情况,载荷分布越均匀,齿廓越光滑,接触疲劳强度越大。
弯曲疲劳是指齿轮齿根或齿腹处的弯曲变形所引起的破坏,主要是由于载荷的反复作用造成齿轮材料的弯曲疲劳寿命有限所导致。
齿轮的弯曲疲劳强度主要取决于齿轮材料的韧性和抗弯刚度,韧性越高,抗弯刚度越大,弯曲疲劳强度越大。
在设计齿轮传动时,需要根据实际工作条件来确定齿轮的合理载荷和材料。
常用的方法是计算齿轮的接触应力和弯曲应力,然后与齿轮材料的疲劳强度进行比较,以确定其可靠性。
接触疲劳和弯曲疲劳强度通常通过实验和理论计算来确定。
实验方法包括采用疲劳试验台进行强度测试,通过不断增加载荷来观察齿轮的失效形态和寿命。
理论计算方法包括应力分析和形状优化,通过建立齿轮模型,计算齿轮表面的应力分布情况,从而确定疲劳强度。
为了提高齿轮的疲劳强度,可以采取以下措施:1. 优化齿轮的几何形状,比如增大齿距、增加齿数、优化齿廓曲线等,以减小齿轮齿面上的应力集中。
2. 选择高强度、高韧性的材料,比如合金钢、渗碳钢等,以提高齿轮的疲劳强度。
3. 控制齿轮的加工工艺,比如采用精密加工、硬化处理等,以提高齿轮的表面质量和耐磨性。
总之,接触疲劳和弯曲疲劳是齿轮传动过程中两种不同的破坏形式,其强度特性有所不同。
在设计齿轮传动时,应根据实际工作条件和要求,综合考虑接触疲劳和弯曲疲劳强度,选择合适的材料和几何形状,以确保齿轮传动的可靠性和寿命。
减速器试验方法
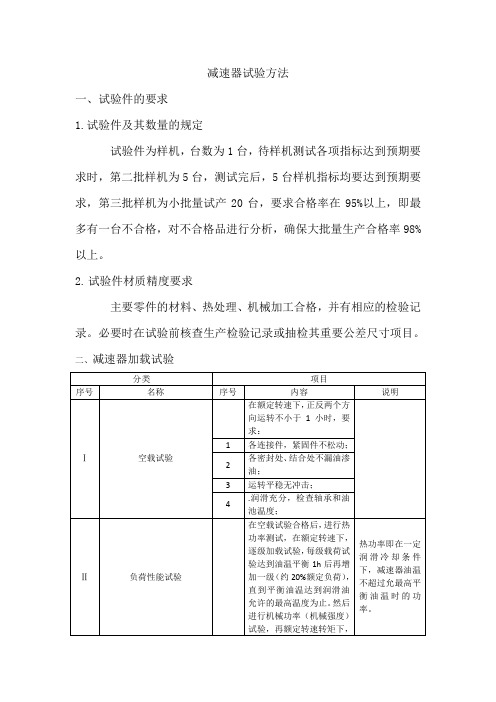
减速器试验方法一、试验件的要求1.试验件及其数量的规定试验件为样机,台数为1台,待样机测试各项指标达到预期要求时,第二批样机为5台,测试完后,5台样机指标均要达到预期要求,第三批样机为小批量试产20台,要求合格率在95%以上,即最多有一台不合格,对不合格品进行分析,确保大批量生产合格率98%以上。
2.试验件材质精度要求主要零件的材料、热处理、机械加工合格,并有相应的检验记录。
必要时在试验前核查生产检验记录或抽检其重要公差尺寸项目。
二、减速器加载试验以上允许工业应用试验代替疲劳寿命试验,但工业应用实际符合必须达到额定负荷,并有准确的日记记录,试验时间不小于3600h。
三、产品质量认证试验产品质量鉴定认证试验按表Ⅰ-Ⅲ各项目进行试验,齿面接触疲劳试验可免做。
四、产品出厂验收试验一般应进行表Ⅰ-Ⅲ各项试验,但负荷性能试验与超载试验允许按实际负荷加载,且负荷试验运转时间允许达到温度平衡为止,不许达到N≥3X106次,批量生产时允许抽样试验,抽样数不小于批量数的10%,如果抽样试验发现不合格品,应再抽试10%,仍有不合格品,应全部试验。
五、测试数据与数据处理1.数据采集试验中采集的数据包括:加载转矩、功率、转速、温度、噪音、震动、齿轮磨损、时间等。
至少没半小时应采集的数据有:输入输出转速、输入输出转矩、功率值、润滑油温度轴承温度、室温(环境温度)。
输入输出转速、输入输出转矩、功率值每次应测试5组,并记录相应的测试时间。
噪音、振动每个负荷档次、每个转速档次测定一次,并记录噪声、振动值及相应的负荷转速与时间。
齿轮磨损、点蚀、胶合、断裂及齿面接触率的变化,一般至少每日观察记录一次,试验正常无损伤、声音无异常,记录时间间隔可较长,反正齿轮出现损伤、声音异常,记录时间应较短。
轴、轴承、箱体再试验中出现异常现象损伤,其种类,润滑油牌号等也应相应记录。
六、减速器传动效率计算减速器总效率=平均输入转矩/平均输出转矩/速比x100%七、试验合格指标1.疲劳寿命试验或工业应用试验合格指标在额定载荷下疲劳寿命试验或工业应用3600h以内的减速器,其合格的指标为:a.齿轮与各部件无断裂损坏。
粉末冶金齿轮齿抗的测量方法

粉末冶金齿轮齿抗的测量方法英文回答:Methods for Measuring the Fatigue Strength of Powder Metallurgy Gear Teeth.Powder metallurgy (PM) gears are increasingly being used in various industrial applications due to their advantages such as high strength, wear resistance, andcost-effectiveness. The fatigue strength of PM gear teethis a crucial property that determines the gear's ability to withstand cyclic loads without failure. Several methods are available to measure the fatigue strength of PM gear teeth, each with its own advantages and limitations.1. Bending Fatigue Test.The bending fatigue test is a widely used method for measuring the fatigue strength of PM gear teeth. In this test, a specimen gear is mounted on a rotating shaft andsubjected to a bending load applied through a meshing gear. The load is applied in cycles until the specimen gear fails due to fatigue. The fatigue strength is determined as the maximum stress amplitude that the gear can withstand for a specified number of cycles without failure.2. Torsional Fatigue Test.The torsional fatigue test is another common method for measuring the fatigue strength of PM gear teeth. In this test, a specimen gear is mounted on a rotating shaft and subjected to a torsional load applied through a meshing gear. The load is applied in cycles until the specimen gear fails due to fatigue. The fatigue strength is determined as the maximum torque amplitude that the gear can withstandfor a specified number of cycles without failure.3. Rolling Contact Fatigue Test.The rolling contact fatigue test is used to measure the fatigue strength of PM gear teeth under rolling contact conditions. In this test, a specimen gear is mounted on arotating shaft and meshed with a mating gear. The gears are subjected to a load that simulates the contact stresses experienced during gear operation. The fatigue strength is determined as the maximum contact stress amplitude that the gears can withstand for a specified number of cycles without failure.4. Ultrasonic Fatigue Test.The ultrasonic fatigue test is a non-destructive method for measuring the fatigue strength of PM gear teeth. Inthis test, a specimen gear is subjected to high-frequency ultrasonic vibrations while a load is applied to the gear tooth. The fatigue strength is determined by monitoring the changes in the ultrasonic response of the gear tooth as the load amplitude increases.5. Finite Element Analysis.Finite element analysis (FEA) can be used to predict the fatigue strength of PM gear teeth. In this method, a computer model of the gear is created and subjected tosimulated loading conditions. The model can be used to calculate the stresses and strains in the gear teeth under various load conditions. The fatigue strength is then estimated based on the calculated stresses and strains using fatigue failure criteria.The choice of fatigue strength measurement method depends on the specific application and requirements. Bending fatigue tests are commonly used for gears subjected to bending loads, while torsional fatigue tests are usedfor gears subjected to torsional loads. Rolling contact fatigue tests are used for gears subjected to rolling contact conditions. Ultrasonic fatigue tests are used for non-destructive evaluation of fatigue strength, while FEA can be used for predicting fatigue strength based on computer simulations.中文回答:粉末冶金齿轮齿抗疲劳强度的测量方法。
齿轮设计中的强度计算方法

齿轮设计中的强度计算方法齿轮作为机械传动中常用的元件,其设计中的强度计算是十分重要的。
强度计算是为了保证齿轮在工作过程中能够承受所受力的作用,不会发生破坏或变形。
本文将介绍齿轮设计中的强度计算方法。
我们需要了解齿轮的受力情况。
齿轮主要受到两种力的作用,一种是齿面上的接触力,另一种是轴向力。
接触力是由于齿轮齿面间的相互作用而产生的,其大小与传动比、输入功率、齿轮材料等因素有关。
轴向力则是由于齿轮的传动力矩而产生的,其大小与传动比、输入功率等因素有关。
在进行强度计算时,首先需要确定齿轮的材料强度。
常用的齿轮材料有铸铁、钢和铜合金等。
不同材料的强度不同,需要根据具体情况选择合适的材料。
接下来,我们来分析齿轮的受力情况。
齿轮的接触力会使齿面产生弯曲应力和接触应力。
弯曲应力是由于齿轮齿面弯曲而产生的,其大小与齿轮的模数、齿轮的参数等因素有关。
接触应力则是由于齿轮齿面间的接触而产生的,其大小与接触面积、接触力、齿轮的参数等因素有关。
在进行强度计算时,我们需要计算齿轮的弯曲强度和接触强度。
弯曲强度是指齿轮在受到弯曲应力作用时能够承受的最大应力值,接触强度是指齿轮在受到接触应力作用时能够承受的最大应力值。
弯曲强度的计算可以使用刘易斯公式或双曲线公式。
刘易斯公式适用于模数较大的齿轮,双曲线公式适用于模数较小的齿轮。
这两种公式都是根据齿轮的几何参数和材料强度来计算弯曲强度的。
接触强度的计算可以使用弗·里兰德公式或哈克公式。
弗·里兰德公式适用于传动比较小的齿轮,哈克公式适用于传动比较大的齿轮。
这两种公式都是根据齿轮的几何参数和材料强度来计算接触强度的。
除了弯曲强度和接触强度的计算外,我们还需要考虑齿轮的疲劳寿命。
疲劳寿命是指齿轮在反复受力下能够工作的时间,其大小与齿轮的材料、强度、工作条件等因素有关。
我们需要通过疲劳寿命计算来确定齿轮是否能够满足使用要求。
齿轮设计中的强度计算方法包括确定材料强度、计算弯曲强度和接触强度,以及考虑疲劳寿命等因素。
齿轮接触疲劳极限表
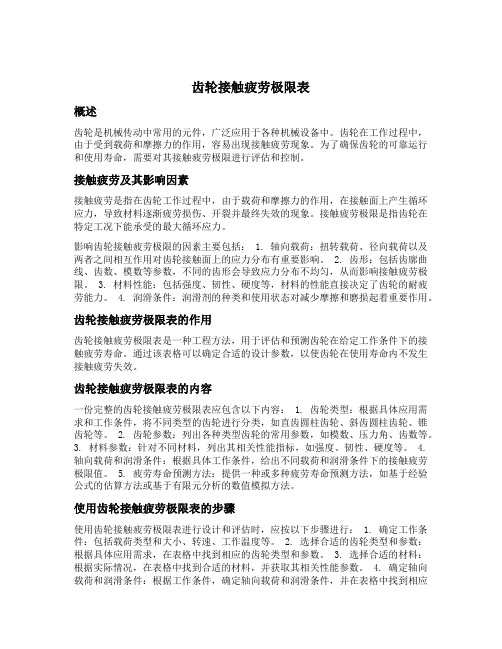
齿轮接触疲劳极限表概述齿轮是机械传动中常用的元件,广泛应用于各种机械设备中。
齿轮在工作过程中,由于受到载荷和摩擦力的作用,容易出现接触疲劳现象。
为了确保齿轮的可靠运行和使用寿命,需要对其接触疲劳极限进行评估和控制。
接触疲劳及其影响因素接触疲劳是指在齿轮工作过程中,由于载荷和摩擦力的作用,在接触面上产生循环应力,导致材料逐渐疲劳损伤、开裂并最终失效的现象。
接触疲劳极限是指齿轮在特定工况下能承受的最大循环应力。
影响齿轮接触疲劳极限的因素主要包括: 1. 轴向载荷:扭转载荷、径向载荷以及两者之间相互作用对齿轮接触面上的应力分布有重要影响。
2. 齿形:包括齿廓曲线、齿数、模数等参数,不同的齿形会导致应力分布不均匀,从而影响接触疲劳极限。
3. 材料性能:包括强度、韧性、硬度等,材料的性能直接决定了齿轮的耐疲劳能力。
4. 润滑条件:润滑剂的种类和使用状态对减少摩擦和磨损起着重要作用。
齿轮接触疲劳极限表的作用齿轮接触疲劳极限表是一种工程方法,用于评估和预测齿轮在给定工作条件下的接触疲劳寿命。
通过该表格可以确定合适的设计参数,以使齿轮在使用寿命内不发生接触疲劳失效。
齿轮接触疲劳极限表的内容一份完整的齿轮接触疲劳极限表应包含以下内容: 1. 齿轮类型:根据具体应用需求和工作条件,将不同类型的齿轮进行分类,如直齿圆柱齿轮、斜齿圆柱齿轮、锥齿轮等。
2. 齿轮参数:列出各种类型齿轮的常用参数,如模数、压力角、齿数等。
3. 材料参数:针对不同材料,列出其相关性能指标,如强度、韧性、硬度等。
4. 轴向载荷和润滑条件:根据具体工作条件,给出不同载荷和润滑条件下的接触疲劳极限值。
5. 疲劳寿命预测方法:提供一种或多种疲劳寿命预测方法,如基于经验公式的估算方法或基于有限元分析的数值模拟方法。
使用齿轮接触疲劳极限表的步骤使用齿轮接触疲劳极限表进行设计和评估时,应按以下步骤进行: 1. 确定工作条件:包括载荷类型和大小、转速、工作温度等。
小齿轮接触疲劳强度极限表

小齿轮接触疲劳强度极限表【原创版】目录1.引言2.接触疲劳强度极限的定义和影响因素3.接触疲劳强度极限的计算方法4.齿轮设计中的应用5.结论正文1.引言在机械传动系统中,齿轮扮演着至关重要的角色。
然而,在长时间的使用过程中,齿轮可能会因为接触疲劳而损坏。
接触疲劳强度极限是齿轮设计中一个关键的参数,直接影响着齿轮的使用寿命和可靠性。
因此,如何计算齿轮的接触疲劳强度极限是一项重要的任务。
2.接触疲劳强度极限的定义和影响因素接触疲劳强度极限是指齿轮在接触应力作用下,能够承受的最大应力值。
接触疲劳强度极限主要受以下因素影响:- 齿轮材料:齿轮材料的硬度和强度直接影响接触疲劳强度极限。
- 齿轮几何参数:包括齿轮直径、齿数、齿宽、齿高、齿根圆半径等,这些参数会影响齿轮的接触疲劳强度极限。
- 载荷条件:包括功率、传动比、转速等,这些条件会影响齿轮的接触疲劳强度极限。
3.接触疲劳强度极限的计算方法计算齿轮的接触疲劳强度极限需要根据上述影响因素选取合适的公式。
一般来说,计算方法可以分为以下步骤:- 根据已知功率、传动比和转速,确定齿轮的载荷条件。
- 选择合适的齿轮材料,并根据材料硬度查取极限接触强度和极限弯曲应力。
- 根据载荷条件和极限应力值,计算齿轮的许用应力值。
- 最后,根据许用应力值和齿轮几何参数,计算出齿轮的接触疲劳强度极限。
4.齿轮设计中的应用在齿轮设计过程中,根据接触疲劳强度极限可以确定齿轮的大小、齿数、齿宽等参数。
此外,接触疲劳强度极限还可以用于检查现有齿轮设计是否合理,如果接触疲劳强度极限小于许用值,则需要重新设计齿轮。
5.结论齿轮的接触疲劳强度极限是齿轮设计中一个关键的参数,直接影响着齿轮的使用寿命和可靠性。
计算接触疲劳强度极限需要考虑齿轮材料、几何参数和载荷条件等因素,并根据许用应力值进行计算。
第七章金属磨损和接触疲劳
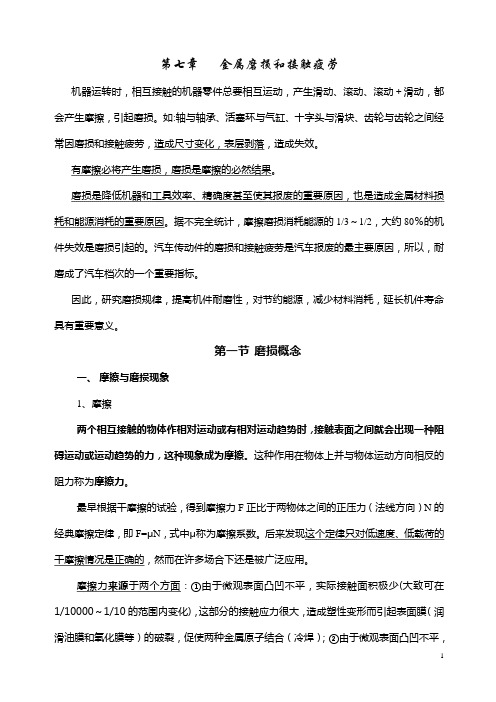
第七章金属磨损和接触疲劳机器运转时,相互接触的机器零件总要相互运动,产生滑动、滚动、滚动+滑动,都会产生摩擦,引起磨损。
如:轴与轴承、活塞环与气缸、十字头与滑块、齿轮与齿轮之间经常因磨损和接触疲劳,造成尺寸变化,表层剥落,造成失效。
有摩擦必将产生磨损,磨损是摩擦的必然结果。
磨损是降低机器和工具效率、精确度甚至使其报废的重要原因,也是造成金属材料损耗和能源消耗的重要原因。
据不完全统计,摩擦磨损消耗能源的1/3~1/2,大约80%的机件失效是磨损引起的。
汽车传动件的磨损和接触疲劳是汽车报废的最主要原因,所以,耐磨成了汽车档次的一个重要指标。
因此,研究磨损规律,提高机件耐磨性,对节约能源,减少材料消耗,延长机件寿命具有重要意义。
第一节磨损概念一、摩擦与磨损现象1、摩擦两个相互接触的物体作相对运动或有相对运动趋势时,接触表面之间就会出现一种阻碍运动或运动趋势的力,这种现象成为摩擦。
这种作用在物体上并与物体运动方向相反的阻力称为摩擦力。
最早根据干摩擦的试验,得到摩擦力F正比于两物体之间的正压力(法线方向)N的经典摩擦定律,即F=μN,式中μ称为摩擦系数。
后来发现这个定律只对低速度、低载荷的干摩擦情况是正确的,然而在许多场合下还是被广泛应用。
摩擦力来源于两个方面:①由于微观表面凸凹不平,实际接触面积极少(大致可在1/10000~1/10的范围内变化),这部分的接触应力很大,造成塑性变形而引起表面膜(润滑油膜和氧化膜等)的破裂,促使两种金属原子结合(冷焊);②由于微观表面凸凹不平,导致一部分阻止另一部分运动。
要使物体继续移动,就必须克服这两部分阻力。
用来克服摩擦力所做的功一般都是无用功,在机械运动中常以热的形式散发出去,使机械效率降低。
减小摩擦偶件的摩擦系数,可以降低摩擦力,即可以保证机械效率,又可以减少机件磨损。
而要求增加摩擦力的情况也很多,在某些情况下却要求尽可能增大摩擦力,如车辆的制动器、摩擦离合器等。
- 1、下载文档前请自行甄别文档内容的完整性,平台不提供额外的编辑、内容补充、找答案等附加服务。
- 2、"仅部分预览"的文档,不可在线预览部分如存在完整性等问题,可反馈申请退款(可完整预览的文档不适用该条件!)。
- 3、如文档侵犯您的权益,请联系客服反馈,我们会尽快为您处理(人工客服工作时间:9:00-18:30)。
实用标准文案
精彩文档
齿轮接触疲劳强度试验方法(GB/T14229-93)
1主题内容与适用范围
本标准规定了测定渐开线圆柱齿轮接触疲劳强度的试验方法,以确定齿轮接触承
载能力所需的基础数据。
本标准适用于钢、铸铁制造的渐开线圆柱齿轮由齿面点蚀损伤而失效的试验。其
它金属齿轮的接触疲劳强度试验可参照使用。
4试验方法
确定齿轮接触疲劳强度应在齿轮试验机上进行试验齿轮的负荷运转试验。当齿面
出现接触疲劳失效或齿面应力循环次数达到规定的循环基数N。而未失效时(以
下简称“越出”),试验终止并获得齿面在试验应力下的一个寿命数据。当试验
齿轮及试验过程均无异常时,通常将该数据称为 “试验点”。根据不同的试验
目的,选择小列不同的试验点的组合,经试验数据的统计处理,确定试验齿轮的
接触疲劳特性曲线及接触疲劳极限应力。
4.1常规成组法
常规成组法用于测定试验齿轮的可靠度-应力-寿命曲线(即R-S-N曲线),求
出试验齿轮的接触疲劳极限应力。
实用标准文案
精彩文档
试验时取4~5个应力级,每个应力级不少于5个试验点(不包括越出点)。最
高应力有中的各试验点的齿面应力循环次数不少于1×106。最高应力级与次高
应力级的应力间隔为总试验应力范围的40%~50%,随着应力的降低,应力间
隔逐渐减少。最低应力级至少有一个试验点越出。
4.2少试验点组合法
少试验点组合法通常用于测定S-N曲线或仅测定极限应力。
试验时试验点总数为7~16个。测定S-N曲线时,应力级为4~10个,每个应
力级取1~4个试验点。
测定极限应力时可采用升降法。
采用正交法进行对比试验时,每个对比因素至少有3个试验点。
5试验条件及试验齿轮
5.1齿轮接触疲劳强度试验按下述规定的试验条件和试验齿轮进行(对比试验的
研究对象除外),上此可确定试验齿轮的接触疲劳极限应力σHlim。
5.1.1试验条件
5.1.1.1试验机
试验应使用功率流封闭式结构的齿轮试验机,试验机的性能校核见表A(补充
件)。试验机的中心距一般为90~150mm,试验齿轮线速度为8~16m/s。试
验机的精度应不低于试验齿轮所要求的精度,试验机应具有以下基本功能:
实用标准文案
精彩文档
a.齿轮断齿时自动停机;
b.有保证齿轮良好润滑的循环喷油润滑系统;
c.有润滑油油墨度控制装置,回油温度控制在60℃以下;
d.有循环次数记录装置,其记录误差不大于±0.1%。
5.1.1.2润滑油
按ZB J17 003进行润滑油的选择的保养。一般情况下试验机连续运转三个月应
进行润滑油的取样检查。
5.1.2试验齿轮
试验齿轮模数的选择应保证在试验中不出现弯曲疲劳断齿,通常取m=3~
8mm。螺旋角β=0°,齿数比u=1.2~1.5(小齿轮为主动轮),试验齿轮副材料相
同,工作齿宽b>0.05a(中心距,mm),表面粗糙度RZ=2~5μm,精度为
GB10095的4~6级,基本齿廓应符合GB1356的规定。
试验齿轮的材料、热处理及加工检测见附录B(补充件)。
5.2齿轮接触疲劳强度试验也可在试验条件和试验齿轮参数与产品齿轮工况和参
数一致或相近的条件下进行。
6接触疲劳失效判据
6.1失效判别方法
实用标准文案
精彩文档
齿轮接触疲劳强度试验是以齿面点蚀损伤程度作为接触疲劳失效的判据。判别方
法有以下两种:
a.单齿点蚀面积率
RS=AS/ASW…………………………(1)
式中:RS——单齿点蚀面积率,%;
AS——试验齿轮单个齿面上点蚀面积之和,mm2;
ASW——试验齿轮单个齿面的工作表面积,mm2。
b.齿轮副点蚀面积率
RT=A1T/A1TW+A2T/A2TW…………………………(2)
式中:RT——齿轮副点蚀面积率,%;
A1T——试验齿轮副主动轮全部点蚀面积之和,mm2;
A2T——试验齿轮副被动轮全部点蚀面积之和,mm2;
A1TW——试验齿轮副主动轮各齿工作表面积之和,mm2;
A2TW——试验齿轮副被动轮各齿工作表面积之和,mm2.
6.2失效判别准则
实用标准文案
精彩文档
6.2.1非表面硬化齿轮,点蚀一般总是在所有齿面上出现。当试验齿轮副的硬度
相等或相近时,它们的点蚀损伤极限为:
RT=2%…………………………(3)
当试验齿轮齿轮副点蚀面积率达到式(3)的点蚀损伤极限时,即判定该齿面失
效。
6.2.2表面硬化齿轮,包括渗碳、渗氮、碳氮共渗、火焰或感应淬火的齿轮,点
蚀一般在少数齿上出现。它们的点蚀损伤极限为:
RS=4%………………………………(4)
或
RT=0.5%…………………………(5)
当试验齿轮点蚀面积率达到式(4)或式(5)的点蚀损伤极限时,即判定该齿
面失效。
6.2.3非表面硬化的试验齿轮循环基数N0=5×107。表面硬化的试验齿轮循环基
数N0≥5×107。当齿面应力循环次数达到循环基数N0,而齿面点蚀损伤速度
未达到点蚀损伤极限时,试验停止,判定该试验点越出。