毕业设计三相异步电动机外文翻译(精)
三相异步交流电机毕业设计书[管理资料]
![三相异步交流电机毕业设计书[管理资料]](https://img.taocdn.com/s3/m/86df0dc23968011ca20091db.png)
学生毕业设计(毕业论文)系别:机电工程专业:数控技术班级:学生姓名:学生学号:设计(论文)题目:三相异步交流电机指导教师:设计地点:起迄日期:毕业设计(论文)任务书专业班级姓名一、课题名称:三相异步电机的设计二、主要技术指标:1.内部由定子和转子构成。
2. 外壳有机座、端盖、轴承盖、接线盒、吊环等组成。
3. 技术要求:采用电压AC380,可以实现正反转。
三、工作内容和要求:1.设计磁路部分:定子铁心和转子铁心。
2 设计电路部分:定子绕组和转子绕组以及电路图。
3 设计机械部分:机座、端子、轴和轴承等。
4.设计电路的正反转和安全控制部分。
5.按照“毕业设计规格”设计毕业报告。
四、主要参考文献:1.[1]王世琨.《图解电工入门》[M]..2.[2]满永奎.《电工学》[M]..3.[3]乔长君.《电机绕组接线图册》[M]..学生(签名)年月日指导教师(签名)年月日教研室主任(签名)年月日系主任(签名)年月日毕业设计(论文)开题报告摘要在费拉里斯和特斯拉发明多相交流系统后,19世纪80年代中期,多沃罗沃尔斯基发明了三相异步电机,异步电机无需电刷和换向器三相异步电机(Triple-phase asynchronous motor)是靠同时接入380V三相交流电源(相位差120度)供电的一类电动机,由于三相异步电机的转子与定子旋转磁场以相同的方向、不同的转速成旋转,存在转差率,所以叫三相异步电机。
作电动机运行的三相异步电机。
三相异步电动机转子的转速低于旋转磁场的转速,转子绕组因与磁场间存在着相对运动而感生电动势和电流,并与磁场相互作用产生电磁转矩,实现能量变换。
与单相异步电动机相比,三相异步电动机运行性能好,并可节省各种材料。
按转子结构的不同,三相异步电动机可分为笼式和绕线式两种。
笼式转子的异步电动机结构简单、运行可靠、重量轻、价格便宜,得到了广泛的应用。
Reese and Tesla invented in AC system. At the mid of 1880s, 多沃罗沃尔Chomsky invented the three-phase asynchronous motors, asynchronous motors without brushes and commutate. Three-phase asynchronous motors (Triple-phase asynchronous motor) is by simultaneously accessing 380V three-phase AC power supply of a class of motors, three-phase asynchronous motor as the rotor and the stator rotating in the same direction, to rotate at different speeds, there turn slip, so called three-phase asynchronous motors.For three-phase asynchronous motors motor is running. Three-phase asynchronous motor rotor speed is lower than the speed of the rotating magnetic field, the magnetic field due to the rotor windings relative motion exists between the induced electromotive force and current, and the magnetic field generated by the interaction with the electromagnetic torque and achieve energy conversion. Compared with single-phase induction motor, Three- phase asynchronous motor running properties, and save a variety of materials. According to the different structure of the rotor, three-phase cage induction motor and the winding can be divided into two kinds. Cage rotor induction motor, simple structure, reliable operation, light weight, cheap, has been widely used目录摘要 (5)第一章电机的分类 (20)按电源分类 (21)按结构及工作原理 (25)按启动与运行方式 (30)按用途分类 (33)按转子的结构 (35)按转速分类 (30)第二章三相异步电机的概述简单介绍 (30)工作原理 (30)电机的参数 (30)启动与运行 (30)第三章三相异步电机的结构磁路部分的结构 (30)电路部分的结构 (30)机械部分的结构 (30)第四章电机的控制电路电机的正反转控制 (30)电机的调速控制 (30)斯沃软件的功能概括 (30)利用仿真软件模拟点动控制 (30)利用仿真软件模拟自锁正反转控制 (30)第五章三相异步电机的特点 (30)第六章致谢参考文献第一章电机的分类按电源分类按工作电源根据电动机工作电源的不同,可分为直流电动机和交流电动机。
毕业设计外文原文+翻译(电力系统)
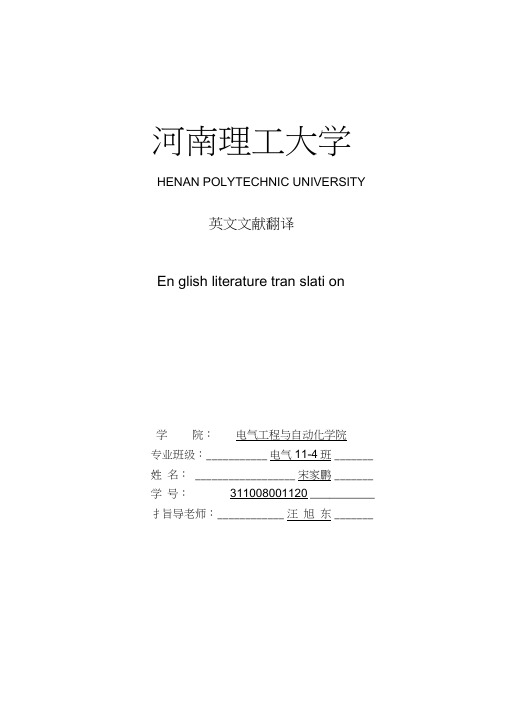
河南理工大学HENAN POLYTECHNIC UNIVERSITY英文文献翻译En glish literature tran slati on学院:电气工程与自动化学院专业班级:___________ 电气11-4班_______ 姓名: __________________ 宋家鹏_______ 学号:311008001120 __________ 扌旨导老师:____________ 汪旭东_______2014年6月5日河南理工大学HENAN POLYTECHNIC UNIVERSITY2.5 对称三相电路在这一部分,我们介绍三相对称电路的一下几个话题:丫连接,相电压,线电压,线电流,△形连接负荷,△ - Y变换,以及等效的相图。
c Ca Ab B图2-10三相Y连接电源带Y连接对称负荷电路图对称Y连接图2-10显示的是一个三相Y连接电源带Y连接对称负荷电路图。
对于Y连接电路,每个相的中性点是连接起来的。
在图2-10中电源中性点标记的是n,而负载中性点标记的是N。
把三相电源假设为理想电源,即阻抗忽略不计。
同时,电源和负载之间线路阻抗,中性点n与N之间的线路阻抗也可忽略不计。
三相负荷是对称的,意味着三相之中任意两相间的阻抗是相同的。
对称相电压在图2-10中,三相电源的终端呗标记为a、b、c,电源相电压标记为E an ,E bn,E cn,当电源的三相电压有相同的幅度,任意两相之间互差120度角时,电源是对称的。
当以E an 作为参考相量时,相电压的幅值是10V,对称三相相电压如下所示:E an=10 0E bn10 120 10 240 (2.5.1 )E cn10 120 10 240河南理工大学HENAN POLYTECHNIC UNIVERSITY图2-11以E an 作为参考的对称正序相电压向量图当E an 超前E bn 120度,E bn 超前E cn 以120度角时,此时的相序称为正相序或 者abc 相序。
三相异步电动机的设计及优化毕业设计开题报告(XXX)

本科生毕业设计(论文)开题报告题目:三相异步电动机的设计及优化(Y160M-4 11kW)学院:信息工程学院系自动化系专业:XXXXXXXXXXXXXXXXXXXX班级:XXX学号:XXX姓名:XXX指导教师:XXX填表日期:2010 年03 月10 日一、选题的依据及意义电能适宜于大量生产、集中管理、远距离运输和自动控制,比其他各种形式的能两更有优越性。
人类对能量利用和控制的能力决定着社会的生产潜能,从而又影响着人类生活方式的进步。
目前,全球每年电能的用量大约为10^4kW·h,并且还在以每年10亿kw·h的速度增长。
电机是将电能从最初的能源形式转换过来的重要桥梁,又是再将大部分电能转换为机械能的装置。
电机在电力工业、工矿企业、农业、交通运输业、国防、科学文化及日常生活等方面都是十分重要的设备。
在电力工业中,将机械能装换为电能的发电机以及将电网电压升高或降低的变压器,都是电力系统中的关键设备。
在很多地方都需要不同特性的电机来驱动和控制。
随着工业企业电气化、自动化、电脑化的发展,还需要众多的各种容量的精密控制电机,作为整个自动控制系统中的重要元件。
电机行业是一个传统的行业。
经过200多年的发展,它已经成为现代生产、生活中不可或缺的核心、基础,是国民经济中重要的一环。
作为劳动密集型产业,我国发展电机制造业有着得天独厚的优势。
到目前为止,我国的电机制造业已经具有一定规模。
统计数据显示,2008年上半年,全行业实现工业总产值180.5亿元,同比增长19.7%。
累计产量6805万千瓦,同比增长11.1%。
在总产量中,大中型电机产量为2878.7万千瓦,增速减缓3.5个百分点;小型交流电机产量为3224.8万千瓦,同比增长5.6%,增速同比减缓8.8个百分点;直流电机产量284.2万千瓦,同比降低20.9%,增速同比减缓21.7个百分点。
上半年全行业实现销售收入178.5亿元,同比增长17.7%。
三相异步变频电机 英语
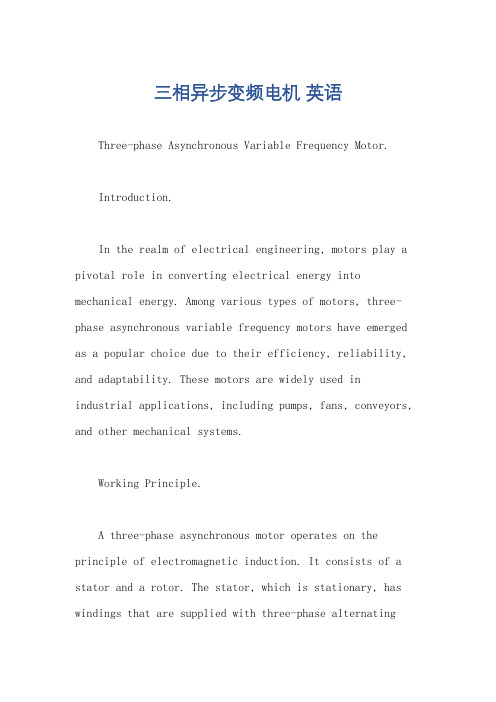
三相异步变频电机英语Three-phase Asynchronous Variable Frequency Motor.Introduction.In the realm of electrical engineering, motors play a pivotal role in converting electrical energy into mechanical energy. Among various types of motors, three-phase asynchronous variable frequency motors have emerged as a popular choice due to their efficiency, reliability, and adaptability. These motors are widely used in industrial applications, including pumps, fans, conveyors, and other mechanical systems.Working Principle.A three-phase asynchronous motor operates on the principle of electromagnetic induction. It consists of a stator and a rotor. The stator, which is stationary, has windings that are supplied with three-phase alternatingcurrent (AC). The rotor, on the other hand, rotates inside the stator.When the three-phase AC supply is given to the stator windings, it creates a rotating magnetic field. Thisrotating magnetic field induces currents in the rotor conductors, which in turn produce their own magnetic fields. The interaction between the stator's rotating magneticfield and the rotor's magnetic fields causes the rotor to rotate.The rotor's speed, however, is slightly less than the synchronous speed of the rotating magnetic field. Thisspeed difference is due to the slip between the rotor and the stator, hence the term "asynchronous".Variable Frequency Control.The frequency of the AC supply to the motor can be varied, allowing for precise control over the motor's speed and torque. Variable frequency control is achieved through the use of a variable frequency drive (VFD) or an inverter.A VFD converts the fixed-frequency AC supply to a variable-frequency output, which can be adjusted as per the motor's requirements. By varying the frequency, the speed of the motor can be controlled. Additionally, the VFD can also control the voltage supplied to the motor, allowingfor further fine-tuning of the motor's performance.Variable frequency control offers several advantages.It enables precise speed control, improves energy efficiency, and reduces mechanical stress on the motor. It also allows for smoother acceleration and deceleration, enhancing the overall performance and reliability of the motor.Applications.Three-phase asynchronous variable frequency motors are widely used in various industrial applications. Some of the common applications include:1. Pumping Systems: These motors are commonly used inpumping systems to control the flow rate and pressure of fluids. By varying the motor's speed, the pump can be adjusted to meet the demand for water or other fluids.2. Fan Applications: In ventilation and cooling systems, variable frequency motors are used to control airflow. By adjusting the motor's speed, the fan can be optimized to maintain a comfortable indoor environment while minimizing energy consumption.3. Conveyor Systems: In material handling applications, conveyor systems often employ variable frequency motors. These motors allow for precise control over the conveyor's speed, ensuring efficient and smooth transportation of materials.4. Machine Tools: Machine tools such as lathes, milling machines, and grinding machines often utilize variable frequency motors for precise speed control and improved machining accuracy.Conclusion.Three-phase asynchronous variable frequency motors play a crucial role in modern industrial applications. Their ability to operate efficiently at variable speeds, combined with the precision control offered by variable frequency drives, makes them an ideal choice for a wide range of mechanical systems. With the increasing demand for energy-efficient and sustainable solutions, these motors are expected to find even more applications in the future.。
异步电动机外文文献翻译中英文
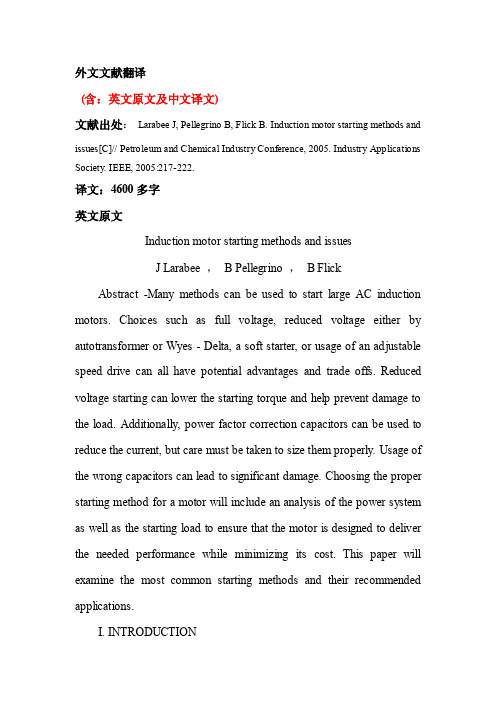
外文文献翻译(含:英文原文及中文译文)文献出处:Larabee J, Pellegrino B, Flick B. Induction motor starting methods and issues[C]// Petroleum and Chemical Industry Conference, 2005. Industry Applications Society. IEEE, 2005:217-222.译文:4600多字英文原文Induction motor starting methods and issuesJ Larabee ,B Pellegrino ,B FlickAbstract -Many methods can be used to start large AC induction motors. Choices such as full voltage, reduced voltage either by autotransformer or Wyes - Delta, a soft starter, or usage of an adjustable speed drive can all have potential advantages and trade offs. Reduced voltage starting can lower the starting torque and help prevent damage to the load. Additionally, power factor correction capacitors can be used to reduce the current, but care must be taken to size them properly. Usage of the wrong capacitors can lead to significant damage. Choosing the proper starting method for a motor will include an analysis of the power system as well as the starting load to ensure that the motor is designed to deliver the needed performance while minimizing its cost. This paper will examine the most common starting methods and their recommended applications.I. INTRODUCTIONThere are several general methods of starting induction motors: full voltage, reduced voltage, wyes-delta, and part winding types. The reduced voltage type can include solid state starters, adjustable frequency drives, and autotransformers. These, along with the full voltage, or across the line starting, give the purchaser a large variety of automotives when it comes to specifying the motor to be used in a given application. Each method has its own benefits, as well as performance trade offs. Proper selection will involve a thorough investigation of any power system constraints, the load to be accelerated and the overall cost of the equipment.In order for the load to be accelerated, the motor must generate greater torque than the load requirement. In general there are three points of interest on the motor's speed-torque curve. The first is locked-rotor torque (LRT) which is the minimum torque which the motor will develop at rest for all angular positions of the rotor. The second is pull-up torque (PUT) which is defined as the minimum torque developed by the motor during the period of acceleration from rest to the speed at which breakdown torque occurs. The last is the breakdown torque (BDT) which is defined as the maximum torque which the motor will develop. If any of these points are below the required load curve, then the motor will not start.The time it takes for the motor to accelerate the load is dependent onthe inertia of the load and the margin between the torque of the motor and the load curve, sometimes called accelerating torque. In general, the longer the time it takes for the motor to accelerate the load, the more heat that will be generated in the rotor bars, shorting ring and the stator winding. This heat leads to additional stresses in these parts and can have an impaction motor life.II. FULL VOL TAGEThe full voltage starting method, also known as across the line starting, is the easiest method to employ, has the lowest equipment costs, and is the most reliable. This method utilizes a control to close a contactor and apply full line voltage to the motor terminals. This method will allow the motor to generate its highest starting torque and provide the shortest acceleration times.This method also puts the highest strain on the power system due to the high starting currents that can be typically six to seven times the normal full load current of the motor. If the motor is on a weak power system, the sudden high power draw can cause a temporary voltage drop, not only at the motor terminals, but the entire power bus feeding the starting motor. This voltage drop will cause a drop in the starting torque of the motor, and a drop in the torque of any other motor running on the power bus. The torque developed by an induction motor varies roughly as the square of the applied voltage. Therefore, depending on the amount ofvoltage drop, motors running on this weak power bus could stall. In addition, many control systems monitor under voltage conditions, a second potential problem that could take a running motor offline during a full voltage start. Besides electrical variation of the power bus, a potential physical disadvantage of an across the line starting is the sudden loading seen by the driven equipment. This shock loading due to transient torques which can exceed 600% of the locked rotor torque can increase the wear on the equipment, or even cause a catastrophic failure if the load can not handle the torques generated by themotor during staring.A. Capacitors and StartingInduction motors typically have very low power factor during starting and as a result have very large reactive power draw. See Fig. 2. This effect on the system can be reduced by adding capacitors to the motor during starting.The large reactive currents required by the motor lag the applied voltage by 90 electrical degrees. This reactive power doesn't create any measurable output, but is rather the energy required for the motor to function. The product of the applied system voltage and this reactive power component can be measured in V ARS (volt-ampere reactive). The capacitors act to supply a current that leads the applied voltage by 90 electrical degrees. The leading currents supplied by the capacitors cancel the lagging current demanded by the motor, reducing the amount ofreactive power required to be drawn from the power system.To avoid over voltage and motor damage, great care should be used to make sure that the capacitors are removed as the motor reaches rated speed, or in the event of a loss of power so that the motor will not go into a generator mode with the magnetizing currents provided from the capacitors. This will be expanded on in the next section and in the appendix.B. Power Factor CorrectionCapacitors can also be left permanently connected to raise the full load power factor. When used in this manner they are called power factor correction capacitors. The capacitors should never be sized larger than the magnetizing current of the motor unless they can be disconnected from the motor in the event of a power loss.The addition of capacitors will change the effective open circuit time constant of the motor. The time constant indicates the time required for remaining voltage in the motor to decay to 36.8% of rated voltage after the loss of power. This is typically one to three seconds without capacitors.With capacitors connected to the leads of the motor, the capacitors can continue to supply magnetizing current after the power to the motor has been disconnected. This is indicated by a longer time constant for the system. If the motor is driving a high inertia load, the motor can changeover to generator action with the magnetizing Current from the capacitors and the shaft driven by the load. This can result in the voltage at the motor terminals actually rising to nearly 50% of rated voltage in some cases. If the power is reconnected before this voltage decays severe transients can be created which can cause significant switching currents and torques that can severely damage the motor and the driven equipment. An example of this phenomenon is outlined in the appendix.Current from the capacitors and the shaft driven by the load. This can result in the voltage at the motor terminals actually rising to nearly 50% of rated voltage in some cases. If the power is reconnected before this voltage decays severe transients can be created which can cause significant switching currents and torques that can severely damage the motor and the driven equipment. An example of this phenomenon is outlined in the appendix.Ⅲ. REDUCED VOL TAGEEach of the reduced voltage methods are intended to reduce the impact of motor starting current on the power system by controlling the voltage that the motor sees at the terminals. It is very important to know the characteristics of the load to be started when considering any form of reduced voltage starting. The motor manufacturer will need to have the speed torque curve and the inertia of the driven equipment when they validate their design. The curve can be built from an initial, or break awaytorque, as few as four other data points through the speed range, and the full speed torque for the starting condition. A centrifugal or square curve can be assumed in many cases, but there are some applications where this would be problematic. An example would be screw compressors which have a much higher torque requirement at lower speeds than the more common centrifugal or fan load. See Fig. 3. By understanding the details of the load to be started the manufacturer can make sure that the motor will be able to generate sufficient torque to start the load, with the starting method that is chosen.A. AutotransformerThe motor leads are connected to the lower voltage side of the transformer. The most common taps that are used are 80%, 65%, and 50%. At 50% voltage the current on the primary is 25% of the full voltage locked rotor amps. The motor is started with this reduced voltage, and then after a pre-set condition is reached the connection is switched to line voltage. This condition could be a preset time, current level, bus volts, or motor speed. The change over can be done in either a closed circuit transition, or an open circuit transition method. In the open circuit method the connection to the voltage is severed as it is changed from the reduced voltage to the line level. Care should be used to make sure that there will not be problems from transients due to the switching. This potential problem can be eliminated by using the closed circuit transition. With theclosed circuit method there is a continuous V oltage applied to the motor. Another benefit with the autotransformer starting is in possible lower vibration and noise levels during starting.Since the torque generated by the motor will vary as the square of the applied voltage, great care should be taken to make sure that there will be sufficient accelerating torque available from the motor. A speed torque curve for the driven equipment along with the inertia should be used to verify the design of the motor. A good rule of thumb is to have a minimum of 10% of the rated full load torque of the motor as a margin at all points of the curve.Additionally, the acceleration time should be evaluated to make sure that the motor has sufficient thermal capacity to handle the heat generated due to the longer acceleration time.B. Solid State or Soft StartingThese devices utilize silicon controlled rectifiers or Scars. By controlling the firing angle of the SCR the voltage that the device produces can be controlled during the starting of the motor by limiting the flow of power for only part of the duration of the sine wave.The most widely used type of soft starter is the current limiting type.A current limit of 175% to 500% of full load current is programmed in to the device. It then will ramp up the voltage applied to the motor until it reaches the limit value, and will then hold that current as the motoraccelerates.Tachometers can be used with solid state starters to control acceleration time. V oltage output is adjusted as required by the starter controller to provide a constant rate of acceleration.The same precautions in regards to starting torque should be followed for the soft starters as with the other reduced voltage starting methods. Another problem due to the firing angle of the SCR is that the motor could experience harmonic oscillating torques. Depending on the driven equipment, this could lead to exciting the natural frequency of the system.C. Adjustable Frequency DrivesThis type of device gives the greatest overall control and flexibility in starting induction motors giving the most torque for an amount of current. It is also the most costly.The drive varies not only the voltage level, but also the frequency, to allow the motor to operate on a constant volt per hertz level. This allows the motor to generate full load torque throughout a large speed range, up to 10:1. During starting, 150% of rated current is typical.This allows a significant reduction in the power required to start a load and reduces the heat generated in the motor, all of which add up to greater efficiency. Usage of the AFD also can allow a smaller motor to be applied due to the significant increase of torque available lower in thespeed range. The motor should still be sized larger than the required horsepower of the load to be driven. The AFD allows a great degree of control in the acceleration of the load that is not as readily available with the other types of reduced voltage starting methods.The greatest drawback of the AFD is in the cost relative to the other methods. Drives are the most costly to employ and may also require specific motor designs to be used. Based on the output signal of the drive, filtered or unfiltered, the motor could require additional construction features. These construction features include insulated bearings, shaft grounding brushes, and insulated couplings due to potential shaft current from common mode voltage. Without these features, shaft currents, which circulate through the shaft to the bearing, through the motor frame and back, create arcing in the bearings that lead to premature bearing failure, this potential for arcing needs to be considered when applying a motor/drive package in a hazardous environment, Division2/Zone2.An additional construction feature of a motor used on an AFD may require is an upgraded insulation system on the motor windings. An unfiltered output signal from a drive can create harmonic voltage spikes in the motor, stressing the insulation of the motor windings.It is important to note that the features described pertain to motors which will be started and run on an AFD. If the drive is only used for starting the motor, these features may not be necessary. Consult with themotor manufacturer for application specific requirements.D. Primary Resistor or Reactor StartingThis method uses either a series resistor or reactor bank to be placed in the circuit with the motor. Resistor starting is more frequently used for smaller motors.When the motor is started, the resistor bank limits the flow of inrush current and provides for a voltage drop at the motor terminals. The resistors can be selected to provide voltage reductions up to 50%. As the motor comes up to speed, it develops a counter EMF (electro-magnetic field) that opposes the voltage applied to the motor. This further limits the inrush currents. As the inrush current diminishes, so does t>e voltage drop across the resistor bank allowing the torque generated by the motor to increase. At a predetermined time a device will short across the resistors and open the starting contactor effectively removing the resistor bank from the circuit. This provides for a closed transition and eliminates the concerns due to switching transients.Reactors will tend to oppose any sudden changes in current and therefore act to limit the current during starting. They will remain shorted after starting and provide a closed transition to line voltage.E .Star delta StartingThis approach started with the induction motor, the structure of each phase of the terminal are placed in the motor terminal box. This allowsthe motor star connection in the initial startup, and then re-connected into a triangle run. The initial start time when the voltage is reduced to the original star connection, the starting current and starting torque by 2 / 3. Depending on the application, the motor switch to the triangle in the rotational speed of between 50% and the maximum speed. Must be noted that the same problems, including the previously mentioned switch method, if the open circuit method, the transition may be a transient problem. This method is often used in less than 600V motor, the rated voltage 2.3kV and higher are not suitable for star delta motor start method.Ⅴ. INCREMENT TYPEThe first starting types that we have discussed have deal with the way the energy is applied to the motor. The next type deals with different ways the motor can be physically changed to deal with starting issues.Part WindingWith this method the stator of the motor is designed in such a way that it is made up of two separate windings. The most common method is known as the half winding method. As the name suggests, the stator is made up of two identical balanced windings. A special starter is configured so that full voltage can be applied to one half of the winding, and then after a short delay, to the second half. This method can reducethe starting current by 50 to 60%, but also the starting torque. One drawback to this method is that the motor heating on the first step of the operation is greater than that normally encountered on across-the-line start. Therefore the elapsed time on the first step of the part winding start should be minimized. This method also increases the magnetic noise of the motor during the first step.IV .ConclusionThere are many ways asynchronous motor starting, according to the constraints of power systems, equipment costs, load the boot device to select the best method. From the device point of view, was the first full-pressure launch the cheapest way, but it may increase the cost efficiency in the use of, or the power supply system in the region can not meet their needs. Effective way to alleviate the buck starts the power supply system, but at the expense of the cost of starting torque.These methods may also lead to increased motor sizes have led to produce the required load torque. Inverter can be eliminated by the above two shortcomings, but requires an additional increase in equipment costs. Understand the limitations of the application, and drives the starting torque and speed, allowing you for your application to determine the best overall configuration.中文译文异步电动机起动的方法作者:J Larabee , B Pellegrino , B Flick摘要:大容量的交流异步电动机有多种启动方法。
三相异步牵引电动机毕业设计

摘要随着电机控制技术的不断发展,在实际中应用越来越多的交流调速系统已经取代了直流调速系统。
由于异步电机是一种复杂的多变量的、强耦合的非线性系统,所以利用计算机仿真的办法构造一个实验系统进行异步电机的分析是一种很好的研究手段。
本文主要首先介绍三相异步牵引电动机结构和构造建立电机数学、物理模型,对比直流电机电磁转矩和异步电动机电磁转矩,结合矢量控制的基本思想和基本概念,完成了对三相交流异步牵引电动机在三相静止坐标和两相静止坐标系上的数学模型,经过坐标转换得到交流牵引电机的模型。
然后通过Matlab/Simulink的模块简化搭建功能完成三相异步牵引电动机最终的仿真模型,并在Mutlab系统环境下实现对电动机的仿真,观察异步电机空载转矩和负载转矩过程中的电流、转速、转矩的变化,对结果与理论结果进行比对分析,证实了该方法的简便直观、高效快捷和真实准确性。
关键词:异步电机;建模;仿真;坐标变换;AbstractWith the development of motor control technology, AC drive system is used more and more in practice has replaced the DC speed regulating system. The asynchronous motor is a strongly coupled nonlinear system is a complex multivariable, using the way of constructing, analysis and computer simulation of an experimental system of asynchronous motor is a very good research tools.This paper first introduces the structure and the structure of three phase a synchronous traction motor mathematical, physical model of motor, compared with DC motor electromagnetic torque and asynchronous motor electro magnetic torque, combined with the basic theory of vector control and the basic concept,the mathematical model in the three-phase static coordinate and two-phase static coordinate system on the three phase asynchronous traction motor, the AC traction the motor model to get the coordinate conversion. Then through the Matlab/Simulink module to simplify the building function to finish the simulation model of the three-phase asynchronous traction motor end, and realize the simulation of the motor in the environment of Mutlab system, variable current,speed, torque of asynchronous motor load torque and load torque in the process, the results were compared with the theoretical results and analysis,confirmed this method simple and intuitive, fast and accurate.KeyWords: Induction motor, Modeling, Simulation, Coordinate transformation目录摘要 (I)Abstract .............................................................................................................................. I I 目录.. (III)1 绪论 (1)1.1研究背景及意义 (1)1.2 国内外研究现状 (1)1.3本论文研究的主要内容 (1)2三相异步电机的构造和工作原理 (2)2.1 三相异步电机的结构和原理 (2)2.1.1三相异步电机的结构 (2)2.1.2三相异步牵引电机工作原理 (2)2.2 三相异步电机的数学模型 (2)2.2.1 三相异步电机在两相静止坐标系上的数学模型 (2)2.2.2 三相异步电机在三相静止坐标系上的数学模型 (3)3 三相牵引电机的建模和仿真 (5)3.1 三相异步牵引电动机模型 (5)3.1.1模型坐标变换 (5)3.1.2建立模型 (5)3.1.3建立s函数以及电机模型 (7)4 仿真结果及其分析 (11)4.1三相输入电流在不同坐标上的波形图 (11)4.2 三相输入电压子在同一坐标下的波形图 (11)4.3 电动机理论输出波形 (12)4.5结果分析 (13)4.6总结 (13)致谢 (14)参考文献 (15)1 绪论1.1 研究背景及意义由于直流调速的局限性和交流调速的优越性,交流异步电动机在实际的需求下得到了很大的发展。
毕业设计(论文)外文资料翻译(学生用)
毕业设计外文资料翻译学院:信息科学与工程学院专业:软件工程姓名: XXXXX学号: XXXXXXXXX外文出处: Think In Java (用外文写)附件: 1.外文资料翻译译文;2.外文原文。
附件1:外文资料翻译译文网络编程历史上的网络编程都倾向于困难、复杂,而且极易出错。
程序员必须掌握与网络有关的大量细节,有时甚至要对硬件有深刻的认识。
一般地,我们需要理解连网协议中不同的“层”(Layer)。
而且对于每个连网库,一般都包含了数量众多的函数,分别涉及信息块的连接、打包和拆包;这些块的来回运输;以及握手等等。
这是一项令人痛苦的工作。
但是,连网本身的概念并不是很难。
我们想获得位于其他地方某台机器上的信息,并把它们移到这儿;或者相反。
这与读写文件非常相似,只是文件存在于远程机器上,而且远程机器有权决定如何处理我们请求或者发送的数据。
Java最出色的一个地方就是它的“无痛苦连网”概念。
有关连网的基层细节已被尽可能地提取出去,并隐藏在JVM以及Java的本机安装系统里进行控制。
我们使用的编程模型是一个文件的模型;事实上,网络连接(一个“套接字”)已被封装到系统对象里,所以可象对其他数据流那样采用同样的方法调用。
除此以外,在我们处理另一个连网问题——同时控制多个网络连接——的时候,Java内建的多线程机制也是十分方便的。
本章将用一系列易懂的例子解释Java的连网支持。
15.1 机器的标识当然,为了分辨来自别处的一台机器,以及为了保证自己连接的是希望的那台机器,必须有一种机制能独一无二地标识出网络内的每台机器。
早期网络只解决了如何在本地网络环境中为机器提供唯一的名字。
但Java面向的是整个因特网,这要求用一种机制对来自世界各地的机器进行标识。
为达到这个目的,我们采用了IP(互联网地址)的概念。
IP以两种形式存在着:(1) 大家最熟悉的DNS(域名服务)形式。
我自己的域名是。
所以假定我在自己的域内有一台名为Opus的计算机,它的域名就可以是。
【精品毕设】机电专业论文英文文献及其中文译文
毕业论文外文文献翻译译文题目:INTEGRATION OF MACHINERY外文资料翻译资料来源:文章名:INTEGRATION OF MACHINERY 《Digital Image Processing》书刊名:作者:Y. Torres J. J. Pavón I. Nieto and J. A.Rodríguez章节:2.4 INTEGRATION OF MACHINERYINTEGRATION OF MACHINERY (From ELECTRICAL AND MACHINERY INDUSTRY)ABSTRACT Machinery was the modern science and technology development inevitable resultthis article has summarized the integration of machinery technology basic outlineand the development background .Summarized the domestic and foreign integration ofmachinery technology present situation has analyzed the integration of machinerytechnology trend of development. Key word:integration of machinery ,technology,present situation ,productt,echnique of manufacture ,trend of development 0. Introduction modern science and technology unceasing development impelleddifferent discipline intersecting enormously with the seepage has caused the projectdomain technological revolution and the transformation .In mechanical engineeringdomain because the microelectronic technology and the computer technology rapiddevelopment and forms to the mechanical industry seepage the integration of machinerycaused the mechanical industry the technical structure the product organizationthe function and the constitution the production method and the management systemhas had the huge change caused the industrial production to enter into quottheintegration of machineryquot by quotthe machinery electrificationquot for the characteristicdevelopment phase. 1. Integration of machinery outline integration of machinery is refers in theorganization new owner function the power function in the information processingfunction and the control function introduces the electronic technology unifies thesystem the mechanism and the computerization design and the software whichconstitutes always to call. The integration of machinery development also has becomeone to have until now own system new discipline not only develops along with thescience and technology but also entrusts with the new content .But its basiccharacteristic may summarize is: The integration of machinery is embarks from thesystem viewpoint synthesis community technologies and so on utilization mechanicaltechnology microelectronic technology automatic control technology computertechnology information technology sensing observation and control technologyelectric power electronic technology connection technology information conversiontechnology as well as software programming technology according to the systemfunction goal and the optimized organization goal reasonable disposition and thelayout various functions unit in multi-purpose high grade redundant reliable inthe low energy consumption significance realize the specific function value andcauses the overall system optimization the systems engineering technology .From thisproduces functional system then becomes an integration of machinery systematic orthe integration of machinery product. Therefore quotintegration of machineryquot coveringquottechnologyquot and quotproductquot two aspects .Only is the integration of machinerytechnology is based on the above community technology organic fusion one kind ofcomprehensivetechnology but is not mechanical technical the microelectronictechnology as well as other new technical simple combination pieces together .Thisis the integration of machinery and the machinery adds the machinery electrificationwhich the electricity forms in the concept basic difference .The mechanicalengineering technology has the merely technical to develop the machineryelectrification still was the traditional machinery its main function still wasreplaces with the enlargement physical strength .But after develops the integrationof machinery micro electron installment besides may substitute for certainmechanical parts the original function but also can entrust with many new functionslike the automatic detection the automatic reduction information demonstrate therecord the automatic control and the control automatic diagnosis and the protectionautomatically and so on .Not only namely the integration of machinery product ishumans hand and body extending humans sense organ and the brains look has theintellectualized characteristic is the integration of machinery and the machineryelectrification distinguishes in the function essence. 2. Integration of machinery development condition integration of machinerydevelopment may divide into 3 stages roughly.20th century 60s before for the firststage this stage is called the initial stage .In this time the people determinationnot on own initiative uses the electronic technology the preliminary achievement toconsummate the mechanical product the performance .Specially in Second World Warperiod the war has stimulated the mechanical product and the electronic technologyunion these mechanical and electrical union military technology postwar transferscivilly to postwar economical restoration positive function .Developed and thedevelopment at that time generally speaking also is at the spontaneouscondition .Because at that time the electronic technology development not yetachieved certain level mechanical technical and electronic technology union alsonot impossible widespread and thorough development already developed the productwas also unable to promote massively. The 20th century 7080 ages for the second stagemay be called the vigorous development stage .This time the computer technologythe control technology the communication development has laid the technology basefor the integration of machinery development . Large-scale ultra large scaleintegrated circuit and microcomputer swift and violent development has provided thefull material base for the integration of machinery development .This timecharacteristic is :①A mechatronics word first generally is accepted in Japanprobably obtains the quite widespread acknowledgment to 1980s last stages in theworldwide scale ②The integration of machinery technology and the product obtainedthe enormous development ③The various countries start to the integration ofmachinery technology and the product give the very big attention and the support.1990s later periods started the integration of machinery technology the new stagewhich makes great strides forward to the intellectualized direction the integrationof machinery enters the thorough development time .At the same time optics thecommunication and so on entered the integration of machinery processes thetechnology also zhan to appear tiny in the integration of machinery the footappeared the light integration of machinery and the micro integration of machineryand so on the new branch On the other hand to the integration ofmachinery systemmodeling design the analysis and the integrated method the integration ofmachinery discipline system and the trend of development has all conducted thethorough research .At the same time because the hugeprogress which domains and so on artificial intelligence technology neural networktechnology and optical fiber technology obtain opened the development vast worldfor the integration of machinery technology .These research will urge theintegration of machinery further to establish the integrity the foundation and formsthe integrity gradually the scientific system. Our country is only then starts fromthe beginning of 1980s in this aspect to study with the application .The State Councilhad been established the integration of machinery leading group and lists as quot863plansquot this technology .When formulated quot95quot the plan and in 2010 developed thesummary had considered fully on international the influence which and possiblybrought from this about the integration of machinery technology developmenttrend .Many universities colleges and institutes the development facility and somelarge and middle scale enterprises have done the massive work to this technicaldevelopment and the application does not yield certain result but and so on theadvanced countries compared with Japan still has the suitable disparity. 3. Integration of machinery trend of development integrations of machinery arethe collection machinery the electron optics the control the computer theinformation and so on the multi-disciplinary overlapping syntheses its developmentand the progress rely on and promote the correlation technology development and theprogress .Therefore the integration of machinery main development direction is asfollows: 3.1 Intellectualized intellectualizations are 21st century integration ofmachinery technological development important development directions .Theartificial intelligence obtains day by day in the integration of machineryconstructors research takes the robot and the numerical control engine bedintellectualization is the important application .Here said quottheintellectualizationquot is to the machine behavior description is in the control theoryfoundation the absorption artificial intelligence the operations research thecomputer science the fuzzy mathematics the psychology the physiology and the chaosdynamics and so on the new thought the new method simulate the human intelligenceenable it to have abilities and so on judgment inference logical thinkingindependent decision-making obtains the higher control goal in order to .Indeedenable the integration of machinery product to have with the human identicalintelligence is not impossible also is nonessential .But the high performancethe high speed microprocessor enable the integration of machinery product to havepreliminary intelligent or humans partial intelligences then is completelypossible and essential. In the modern manufacture process the information has become the controlmanufacture industry the determining factor moreover is the most active actuationfactor .Enhances the manufacture system information-handling capacity to become themodern manufacture science development a key point .As a result of the manufacturesystem information organization and structure multi-level makes the information thegain the integration and the fusion presents draws up the character informationmeasuremulti-dimensional as well as information organizations multi-level .In themanufacture information structural model manufacture information uniform restraintdissemination processing and magnanimous data aspects and so on manufacture knowledgelibrary management all also wait for further break through. Each kind of artificial intelligence tool and the computation intelligence methodpromoted the manufacture intelligence development in the manufacture widespreadapplication .A kind based on the biological evolution algorithm computationintelligent agent in includes thescheduling problem in the combination optimization solution area of technologyreceives the more and more universal attention hopefully completes the combinationoptimization question when the manufacture the solution speed and the solutionprecision aspect breaks through the question scale in pairs the restriction .Themanufacture intelligence also displays in: The intelligent dispatch the intelligentdesign the intelligent processing the robot study the intelligent control theintelligent craft plan the intelligent diagnosis and so on are various These question key breakthrough may form the product innovation the basicresearch system. Between 2 modern mechanical engineering front science differentscience overlapping fusion will have the new science accumulation the economicaldevelopment and societys progress has had the new request and the expectation tothe science and technology thus will form the front science .The front science alsohas solved and between the solution scientific question border area .The front sciencehas the obvious time domain the domain and the dynamic characteristic .The projectfront science distinguished in the general basic science important characteristicis it has covered the key science and technology question which the project actualappeared. Manufacture system is a complex large-scale system for satisfies the manufacturesystem agility the fast response and fast reorganization ability must profit fromthe information science the life sciences and the social sciences and so on themulti-disciplinary research results the exploration manufacture system newarchitecture the manufacture pattern and the manufacture system effectiveoperational mechanism .Makes the system optimization the organizational structureand the good movement condition is makes the system modeling the simulation andthe optimized essential target .Not only the manufacture system new architecture tomakes the enterprise the agility and may reorganize ability to the demand responseability to have the vital significance moreover to made the enterprise first floorproduction equipment the flexibility and may dynamic reorganization ability set ahigher request .The biological manufacture view more and more many is introduced themanufacture system satisfies the manufacture system new request. The study organizes and circulates method and technique of complicated systemfrom the biological phenomenon is a valid exit which will solve many hard nut tocracks that manufacturing industry face from now on currently .Imitating to livingwhat manufacturing point is mimicry living creature organ of from the organizationfrom match more from growth with from evolution etc. function structure and circulatemode of a kind of manufacturing system and manufacturing process. The manufacturing drives in the mechanism under continuously by ones ownperfect raise on organizing structure and circulating modeand thus to adapt theprocess ofwith ability for the environment .For from descend but the last productproceed together a design and make a craft rules the auto of the distance born producesystem of dynamic state reorganization and product and manufacturing the system tendautomatically excellent provided theories foundation and carry out acondition .Imitate to living a manufacturing to belong to manufacturing science andlife science ofquotthe far good luck is miscellaneous to hand overquot it will produceto the manufacturing industry for 21 centuries huge of influence .机电一体化摘要机电一体化是现代科学技术发展的必然结果本文简述了机电一体化技术的基本概要和发展背景。
毕业设计(论文)外文资料翻译【范本模板】
南京理工大学紫金学院毕业设计(论文)外文资料翻译系:机械系专业:车辆工程专业姓名:宋磊春学号:070102234外文出处:EDU_E_CAT_VBA_FF_V5R9(用外文写)附件:1。
外文资料翻译译文;2.外文原文.附件1:外文资料翻译译文CATIA V5 的自动化CATIA V5的自动化和脚本:在NT 和Unix上:脚本允许你用宏指令以非常简单的方式计划CATIA。
CATIA 使用在MS –VBScript中(V5.x中在NT和UNIX3。
0 )的共用部分来使得在两个平台上运行相同的宏。
在NT 平台上:自动化允许CATIA像Word/Excel或者Visual Basic程序那样与其他外用分享目标。
ATIA 能使用Word/Excel对象就像Word/Excel能使用CATIA 对象。
在Unix 平台上:CATIA将来的版本将允许从Java分享它的对象。
这将提供在Unix 和NT 之间的一个完美兼容。
CATIA V5 自动化:介绍(仅限NT)自动化允许在几个进程之间的联系:CATIA V5 在NT 上:接口COM:Visual Basic 脚本(对宏来说),Visual Basic 为应用(适合前:Word/Excel ),Visual Basic。
COM(零部件目标模型)是“微软“标准于几个应用程序之间的共享对象。
Automation 是一种“微软“技术,它使用一种解释环境中的COM对象。
ActiveX 组成部分是“微软“标准于几个应用程序之间的共享对象,即使在解释环境里。
OLE(对象的链接与嵌入)意思是资料可以在一个其他应用OLE的资料里连结并且可以被编辑的方法(在适当的位置编辑).在VBScript,VBA和Visual Basic之间的差别:Visual Basic(VB)是全部的版本。
它能产生独立的计划,它也能建立ActiveX 和服务器。
它可以被编辑。
VB中提供了一个补充文件名为“在线丛书“(VB的5。
KW出口三相异步电机设计毕业设计
可编辑修改毕业设计题目: 30KW出口三相异步电动机的设计精品文档河北科技大学毕业设计成绩评定表目录1 引言 (1)1.1 三相感应电机概述 (1)1.2 国内外电机制造工业发展状况 (2)1.3 出口电机 (2)2 毕业设计课题任务及设计过程 (4)2.1 课题设计任务内容及要求 (4)2.2 设计过程 (4)2.3电磁计算程序 (7)3.1 VB简介 (30)3.2 程序说明 (31)3.3 设计方法 (31)3.4 程序流程图 (34)3.5 计算程序及计算结果 (37)3.6 方案比较及优选 (51)3.7 程序变量对照表 (55)结论 (59)致谢 (60)附图1 定子冲片图附图2 转子冲片、端环图附图3 绕组展开图副本计算机辅助设计1引言电机在国民经济中发挥着巨大的作用,它是一种能把能量或信号进行转换的电磁装置,现已广泛应用于电力工业、机械行业、交通运输等国民经济的各个领域。
从能量转换的角度来看,电机可分为两大类。
第一类是发电机,它把机械能转换为电能,首先通过原动机先把各类一次能源蕴藏的能量转换为机械能,然后通过发电机把机械能转换为电能,再经输配电线路供给用户使用。
第二类是电动机,它把电能转换为机械能,用来驱动各种用途的生产机械和其他装置,以满足人们不同的需求。
本次设计的电机为电动机,根据所应用的场合和电源的不同,电动机有直流电动机、交流同步电动机、交流感应电动机,以及满足不同需求的特种电动机]1[。
三相异步电动机是电动机的一种,它是人们常用的动力工具,广泛应用于各个领域,它结构简单,制造、使用、维护方便,价格便宜,运行可靠,效率较高,具有直流电机所不具有的优势。
随着电机产品国外市场的进一步拓宽,中小型电机在出口数量、品种、产品档次、创汇额上将会有重大突破]2[。
未来出口电机产量增长主要外部原因在于世界经济稳定增长,促进了行业贸易产量的增长。
内因是国内出口退税率改革导致企业加快出口步伐,及国内外资企业规模的不断扩大和数量的快速增加,产品竞争提高,在国内形成巨大的效益,也刺激了出口上升]3[。
- 1、下载文档前请自行甄别文档内容的完整性,平台不提供额外的编辑、内容补充、找答案等附加服务。
- 2、"仅部分预览"的文档,不可在线预览部分如存在完整性等问题,可反馈申请退款(可完整预览的文档不适用该条件!)。
- 3、如文档侵犯您的权益,请联系客服反馈,我们会尽快为您处理(人工客服工作时间:9:00-18:30)。
中文翻译异步电动机具有结构简单、运行可靠、价格低、维护方便等一系列的优点,因此,异步电动机被广泛应用在电力拖动系统中。
尤其是随着电力电子技术的发展和交流调速技术的日益成熟,使得异步电动机在调速性能方面大大提高。
目前,异步电动机的电力拖动已被广泛地应用在各个工业电气自动化领域中。
就三相异步电动机的机械特性出发,主要简述电动机的启动,制动、调速等技术问题。
1 三相异步电动机的机械特性文三相异步电动机的机械特性是指电动机的转速n与电磁转矩Tem之间的关系。
由于转速n与转差率S有一定的对应关系,所以机械特性也常用Tem=f(s的形式表示。
三相异步电动机的电磁转矩表达式有三种形式,即物理表达式、参数表达式和实用表达式。
物理表达式反映了异步电动机电磁转矩产生的物理本质,说明了电磁转矩是由主磁通和转子有功电流相互作用而产生的。
参数表达式反映了电磁转矩与电源参数及电动机参数之间的关系,利用该式可以方便地分析参数变化对电磁转矩的影响和对各种人为特性的影响。
实用表达式简单、便于记忆,是工程计算中常采用的形式。
电动机的最大转矩和启动转矩是反映电动机的过载能力和启动性能的两个重要指标,最大转矩和启动转矩越大,则电动机的过载能力越强,启动性能越好。
三相异步电动机的机械特性是一条非线性曲线,一般情况下,以最大转矩(或临界转差率为分界点,其线性段为稳定运行区,而非线性段为不稳定运行区。
固有机械特性的线性段属于硬特性,额定工作点的转速略低于同步转速。
人为机械特性曲线的形状可用参数表达式分析得出,分析时关键要抓住最大转矩、临界转差率及启动转矩这三个量随参数的变化规律。
2 三相异步电动机的启动小容量的三相异步电动机可以采用直接启动,容量较大的笼型电动机可以采用降压启动。
降压启动分为定子串接电阻或电抗降压启动、Y-D降压启动和自耦变压器降压启动。
定子串电阻或电机降压启动时,启动电流随电压一次方关系减小,而启动转矩随电压的平方关系减小,它适用于轻载启动。
Y-D降压启动只适用于正常运行时为三角形联结的电动机,其启动电流和启动转矩均降为直接启动时的1/3,它也适用于轻载启动。
自耦变压器降压启动时,启动电流和启动转矩均降为直接启动时的l/k2(k为自耦变压器的变比,适合带较大的负载启动。
绕线转子异步电动机可采用转子串接电阻或频敏变阻器启动,其启动转矩大、启动电流小,适用于中、大型异步电动机的重载启动。
软启动器是一种集电机软启动、软停车、轻载节能和多种保护功能于一体的新型电动机控制装置,国外称为Soft Starter。
它的主要构成是串接于电源与被控电动机之间的三相反并联晶闸管及其电子控制电路。
运用串接于电源与被控电动机之间的软启动器,以不同的方法,控制其内部晶闸管的导通角,使电动机输入电压从零以预设函数关系逐渐上升,直至启动结束,赋予电动机全电压,即为软启动。
在软启动过程中,电动机启动转矩逐渐增加,转速也逐渐增加。
软启动器实际上是个调压器,用于电动机启动时,输出只改变电压并没有改变频率。
3 三相异步电动机的调速三相异步电动机的调速方法有变极调速、变频调速和变转差率调速。
其中变转差率调速包括绕线转子异步电动机的转子串接电阻调速、串级调速和降压调速。
变极调速是通过改变定子绕组接线方式来改变电机极数,从而实现电机转速的变化。
变极调速为有级调速,变极调速时的定子绕组联结方式有三种:Y-YY、顺串Y-反串Y、D-YY。
其中Y-YY联结方式属于恒转矩调速方式,另外两种属于恒功率调速方式。
变极调速时,应同时对调定子两相接线,这样才能保证调速后电动机的转向不变。
变频调速是现代交流调速技术的主要方向,它可实现无级调速,适用于恒转矩和恒功率负载。
绕线转子电动机的转子串接电阻调速方法简单,易于实现,但调速是有级的,不平滑,且低速时特性软,转速稳定性差,同时转子铜损耗大,电动机的效率低。
串级调速克服了转子串接电阻调速的缺点,但设备要复杂得多。
异步电动机的降压调速主要用于风机类负载的场合,或高转差率的电动机上,同时应采用速度负反馈的闭环控制系统。
把电压和频率固定不变的工频交流电变换为电压或频率可变的交流电的装置称作“变频器”。
为了产生可变的电压和频率,该设备首先要把电源的交流电变换为直流电(DC,这个过程叫整流。
再把直流电(DC变换为交流电(AC,这个过程叫逆变,把直流电变换为交流电的装置叫逆变器(inverter。
对于逆变为频率可调、电压可调的逆变器我们称为变频器。
变频器输出的波形是模拟正弦波,主要用在三相异步动机的调速,又叫变频调速器。
附录二外文原文Asynchronous motor has a simple structure, reliable operation, low price, convenient maintenance and a series of advantages, therefore, asynchronous motor is widely used in electric drive system. Especially with the development of power electronic technology and AC drive technology becomes more mature, greatly improve the speed performance makes the asynchronous motor. At present, electric drive asynchronous motor has been widely used in various industrial electrical automation. The mechanical properties of three-phase asynchronous motor starting, the main motor starting, braking, speed control technology.The mechanical properties of 1 three-phase asynchronous motorMechanical characteristics of three-phase asynchronous motor is refers to the relationship between the speed of the motor electromagnetic torque of N and Tem. Due tothe speed of N and slip S have a certain relationship, so the mechanical properties arealso commonly used Tem = f (s representation. Electromagnetic torque expression ofthree-phase asynchronous motor has three forms, namely physical expression, parameters and practical expression. Physical expressions reflect the physical nature of electromagnetic torque of asynchronous motor, the electromagnetic torque is generatedby the main flux and rotor active current interaction. Parameter expression reflects the relationship between parameters of electromagnetic torque and power supply parameters and motor, the expression can be used to influence easily analyze the influence of parameter variation on the electromagnetic torque and all kinds of human characteristics. Practical expressions in a simple, easy to remember, is often used in engineering calculation in the form of.The maximum torque of motor and torque are two important indexes reflecting the overload capacity of the motor and starting performance, maximum torque and starttorque motor overload capacity is bigger, stronger, better starting performance.The mechanical characteristic of three-phase asynchronous motor is a nonlinear curve, under normal circumstances, with the maximal torque (or critical slip as a cutoff point, the linear segment for the stable operation region, while the nonlinear section is not stable operating region. Hard characteristic is linear segment inherent mechanicalproperties, the nominal operating point speed slightly lower than the synchronous speed. Shape parameters available expressions man-made mechanical characteristic curve analysis, analysis the key to grasp the maximum torque, starting torque variation ofcritical slip and the three with the parameters of.2 three-phase asynchronous motor startingThree-phase asynchronous motor with small capacity can be used to directly start, cage motor with large capacity can adopt step-down start. Step-down start into stator resistance or reactance step-down start, Y-D step-down start and autotransformer start.The stator resistance or motor step-down start, starting current voltage relations with a reduced, and the starting torque with the square of the voltage is reduced, it is suitable for the starting load. Only applicable to motor start to normal operation for the triangle connection Y-D buck, the starting current and starting torque is reduced to direct startup 1\/3, which is also suitable for the starting load. Autotransformer start, starting current and starting torque is reduced to direct startup l\/k2 (k is the self coupling transformer, suitable for large load starting.The wound rotor asynchronous motor with rotor series resistance or frequency sensitive rheostat starting, the starting torque, small starting current, suitable for heavy load starting, large asynchronous motor.The soft starter is a novel control device for motor motor soft start, soft stop, light load energy saving and various protecting functions in one, called Soft Starter. The main structure is connected in series between the power supply and the controlled motor three-phase inverse parallel thyristor and its electronic control circuit. Through the series ofsoft starter is connected between the power supply and the controlled motor, in different ways, its internal control thyristor conduction angle, so that the motor input voltage from zero to a preset function gradually rise, until the end of the motor start, give full voltage, namely soft start. In the soft start-up process, starting torque motor speed increases gradually, gradually increasing. The soft starter is actually a regulator, for when the motor is started, the output voltage does not change the frequency change.3 speed of three-phase asynchronous motorControl method of the three-phase asynchronous motor with variable speed, variable speed and variable slip speed. The variable slip ratio control includes a rotor winding rotor asynchronous motor series resistance speed control, cascade control and blood pressure control.Variable speed is by changing the stator winding connection mode to change thepole number, so as to realize the change of motor speed. Variable speed is speed-regulation, variable stator winding connection speed of three kinds: Y-YY, Y-, D-YY and Y run. The Y-YY connection is constant torque speed control mode, another two species belong to the constant power control mode. Variable pole speed, should also be on the stator two-phase wiring, so that we can guarantee the speed regulation motor steering. Variable frequency speed control is the main direction of modern AC speed regulation technology, it can realize stepless speed regulation, suitable for constant torque and constant power load. Wound rotor rotor motor series resistance speed control method is simple, easy to implement, but speed is not smooth, level, and low speed characteristics of soft, speed stability is poor, and the rotor copper loss, motor efficiency is low. Cascade speed control to overcome the rotor series resistance speed disadvantage, but the equipment is much more complex. Step-down speed asynchronous motor for fan load, or high slip motor, closed-loop control system should be accompanied by negative feedback of speed. The industrial frequency alternating current voltage and frequency of fixed to variable voltage or frequency of the alternating current. 6。