超大规模集成电路铜互连电镀工艺
巴斯夫创造用于集成电路的先进电镀铜化学品

巴斯夫创造用于集成电路的先进电镀铜化学品巴斯夫创造出一种先进的电镀铜化学品,可满足现今及未来芯片科技的需求。
巴斯夫与IBM 于2007 年6 月开始这一联合开发项目,这项创新的化学品解决方案是其直接成果。
这种解决方案的表现超越了市场上现有的其它化学品。
两家公司正扩展他们的合作计划,以确定量产所需的参数。
相关的技术、化学品和材料预计可于2010 年中期上市供应。
巴斯夫全球电子材料业务部研发部门的资深经理兼该项目负责人Dieter Mayer 表示:我们为这一创新的化学品感到兴奋无比。
巴斯夫与IBM 团队选择了一种新的方式,通过对于沉积铜物理特性的了解来设计分子添加剂系统。
利用巴斯夫与IBM 强大的资源,我们已经克服了在电镀铜方面的主要挑战,朝着制造更小、更快、更可靠芯片的目标又迈进了一步。
实现无缺陷的电导线沉积是成功沉积铜工艺最关键的条件。
在电镀铜沉积工艺中,传统的等向性充填(conformal fill)会在形体的上、下、外围产生同样的铜沉积率,形成接缝及缺陷。
通过采用巴斯夫的化学品可以实现快速的充填,一般称为超填孔(superfill),可以将铜快速的充填至细小的通孔及沟槽,制造出无缺陷的铜导线。
通过超填充的方式,底部的铜沉积率会比顶部及外围更高。
铜导线可显著改善芯片效能,这种高传导性金属的沉积是建构多层互连结构的关键性工艺。
时下最先进的芯片技术被称为32 纳米技术节点,而下一代的22 纳米技术预期将于2011 年推出。
当芯片尺寸越来越小,互连结构日趋复杂,要制造出高性能的芯片就更需要专门的化学知识。
同时,纯熟完善的化学工艺解决方案也是必不可少的。
巴斯夫的电镀铜化学品已经可以应用在32 纳米和22 纳米的芯片技术中,。
半导体技术分享电镀工艺的应用

半导体技术分享 | 电镀工艺的应用电镀是一种常见的制造工艺,其原理是将一薄层金属镀在其他金属表面上。
例如,美国自1982年以来,就一直采用镀有一薄层铜的锌来制作一分硬币。
此外,珠宝和西式餐具的外层也经常使用电镀工艺,从而使其更美观或提高耐磨性和抗腐蚀性。
如今,在电子行业中,电镀工艺还被广泛应用于印刷电路板,连接器以及最近的半导体互连中导电金属的沉积。
在芯片制造的过程中,需要沉积电介质(绝缘)材料层和金属(导电)材料层。
根据不同的材料类型和制作结构,技术人员会使用不同的物理和化学技术。
目前,电镀技术经常被用来创建铜互连和导通孔,以此将集成电路中的元件连接在一起。
而且,相比于物理气相沉积等沉积方法,使用电镀技术沉积的铜具有较低的电阻率和更好的填充特性。
在具体分析芯片制造过程的实例前,我们先来看一个你或许在化学课上做过的黄铜钥匙镀铜的基础电镀实验。
首先,需要将钥匙和铜片都连接到电源上(通常是电池)。
然后,把钥匙和铜片浸没到导电溶液中,并使它们互不接触,从而形成一个完整的电路。
随着电流流动,离子从铜供应源处溶解转移,并在钥匙上沉积。
最后,钥匙被铜层完全覆盖。
同理,这个电镀原理还可应用到半导体工艺中。
将晶圆和铜供应源放置在通常含有硫酸铜和硫酸的电镀液中。
然后,当电流作用时,铜离子开始在晶圆上沉积。
由于电流能提供铜离子还原反应所需的电子,因此通过电流可以直接控制晶圆上沉积的铜量。
另外,溶液温度、溶液流动率和电镀液的化学成分等参数都可以用来控制晶圆上沉积的铜的特性。
互连在创建互连结构时,情况会更为复杂。
如果层间的电介质层中出现铜污染,便会造成严重的后果。
因此,为了防止这种污染,工艺过程的第一步就是沉积扩散阻挡层(Ta/TaN)。
由于铜电镀过程通常不会在电阻较高的扩散阻挡层上成核,所以可以通过使用物理气相沉积法在阻挡层上沉积出非常薄的铜种子层。
之后,采用铜电镀来形成所需厚度的铜膜。
此外,完全填充又深又窄的互连沟槽也是一个挑战。
PCB电镀铜锡工艺资料
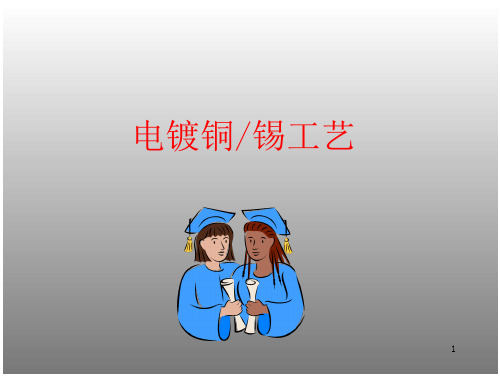
34
电镀铜溶液的控制
n 赫尔槽试验(Hull Cell Test)
n仅高电流密度区烧焦,试片的其它区域仍然正常----Copper Gleam 125T-2(CH) Additive 低 n改正方法:添加1ml/l Copper Gleam 125T-2(CH) Additive
: 濃度太低,Байду номын сангаас液導電性差,鍍液分 散能力差。
濃度太高,降低Cu2+的遷移率,電流 效率反而降低,❹對銅鍍層的延伸 率不利。
: 濃度太低,鍍層出現台階狀的粗糙 鍍層,易出現針孔和燒焦;濃度太 高,導致陽極鈍化,鍍層失去光澤 。
: (後面專題介紹)
11
操作條件對酸性鍍銅效果的影響
溫度
溫度升高,電極反應速度加快,允許電流密度提高,鍍 層沉積速度加快,但加速添加劑分解會增加添加劑消耗,鍍層結 晶粗糙,亮度降低。
31
电镀铜溶液的控制
n 赫尔槽试验 (Hull Cell Test)
阴极-
阳极+
32
电镀铜溶液的控制
n 赫尔槽试验(Hull Cell Test)参数
n — 电流: 2A n — 时间: 10分钟 n — 搅拌: 空气搅拌 n — 温度: 室温
33
电镀铜溶液的控制
n 赫尔槽试验(Hull Cell Test)
28
电镀铜溶液和电镀线的评价
n 热冲击测试
测试步骤
(1) 裁板16""x18"’ (2) 进行钻孔; (3) 经电镀前处理磨刷; (4) Desmear + PTH + 电镀; (5) 经电镀后处理的板清洗烘干; (6) 每片板裁上、中、下3小片100mm x 100mm测试板;
-半导体-大规模集成电路工艺流程(精)

半导体-大规模集成电路工艺流程(精)半导体工艺是制造集成电路的过程。
集成电路是由许多晶体管、电容器、电阻等元件组成的电子电路系统。
集成电路的制造需要经过一系列的工艺过程。
在本文中,我们将介绍大规模集成电路的制造工艺流程。
半导体工艺简介半导体制造工艺分为半导体材料生长、晶圆制备、光刻、蚀刻、沉积、清洗、测试等多个流程。
每个工艺流程都有不同的方法和技术。
半导体是一类电导率介于导体(金属)和绝缘体之间的材料。
在半导体中,当加上电场或加热时,电子就能从电子价带跃迁到空穴价带,并形成电流。
这样的材料有硅(Si)、锗(Ge)、砷化镓(GaAs)等等。
大规模集成电路工艺流程大规模集成电路是由数百万个晶体管、电容器、电阻等元件组成的电路。
在大规模集成电路的制造过程中,大家都会遵循下面这个工艺流程。
晶圆制备晶圆制备是大规模集成电路制造的第一步。
晶圆是半导体材料生长的产物,它们通常由硅(Si)、锗(Ge)、石英等材料制成。
在晶圆制备过程中,首先需要生长一个单晶材料,这可以通过以下两种方法实现:CVD生长法此方法的原理是利用气相反应过程,将气体中的材料(如氯硅烷SiCl4、氯气Cl2)分解,生成单晶硅。
这种方法的优点是能够高效且大规模地生长单晶材料,且可以以低成本制备量生产高质量的晶圆。
CZ法此方法是将高纯度的多晶硅(Si)置于沃尔夫拉姆棒(Tungsten electrode)中,借助热电流电流加热并慢慢拉伸,使得多晶硅逐渐溶解,沉淀成为单晶硅。
这个方法对单晶硅的杂质限制要比CVD法少得多,但晶体生长速度较慢。
光刻和蚀刻光刻和蚀刻是制造晶片的核心工艺。
这一步骤通常是在一个称为掩膜层上完成的,其中包含了一个所需电路的图案。
这个步骤可以通过以下两个步骤的组合来完成。
光刻光刻是将所需的信号电路或功能模块转移到晶片上的过程。
它可以通过将光线通过模板或掩膜光刻到光刻胶层上来实现。
一旦完成了光刻胶层的曝光,就可以模仿模板或掩膜的图案进行开发。
电镀铜和化学镀铜的性能分析和影响因素
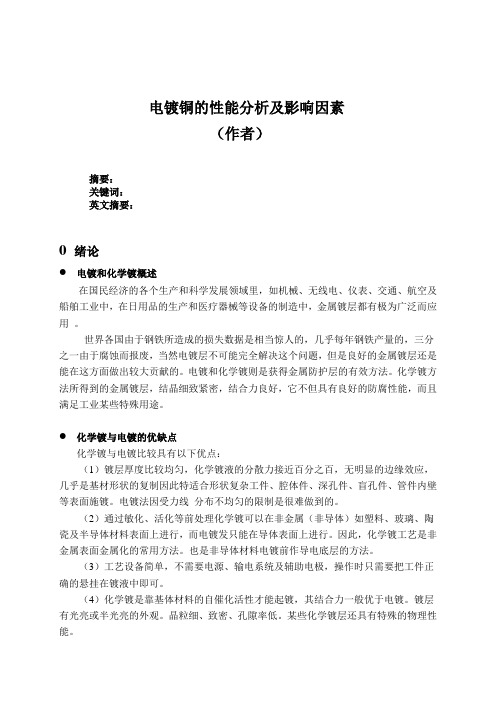
电镀铜的性能分析及影响因素(作者)摘要:关键词:英文摘要:0 绪论●电镀和化学镀概述在国民经济的各个生产和科学发展领域里,如机械、无线电、仪表、交通、航空及船舶工业中,在日用品的生产和医疗器械等设备的制造中,金属镀层都有极为广泛而应用。
世界各国由于钢铁所造成的损失数据是相当惊人的,几乎每年钢铁产量的,三分之一由于腐蚀而报废,当然电镀层不可能完全解决这个问题,但是良好的金属镀层还是能在这方面做出较大贡献的。
电镀和化学镀则是获得金属防护层的有效方法。
化学镀方法所得到的金属镀层,结晶细致紧密,结合力良好,它不但具有良好的防腐性能,而且满足工业某些特殊用途。
●化学镀与电镀的优缺点化学镀与电镀比较具有以下优点:(1)镀层厚度比较均匀,化学镀液的分散力接近百分之百,无明显的边缘效应,几乎是基材形状的复制因此特适合形状复杂工件、腔体件、深孔件、盲孔件、管件内壁等表面施镀。
电镀法因受力线分布不均匀的限制是很难做到的。
(2)通过敏化、活化等前处理化学镀可以在非金属(非导体)如塑料、玻璃、陶瓷及半导体材料表面上进行,而电镀发只能在导体表面上进行。
因此,化学镀工艺是非金属表面金属化的常用方法。
也是非导体材料电镀前作导电底层的方法。
(3)工艺设备简单,不需要电源、输电系统及辅助电极,操作时只需要把工件正确的悬挂在镀液中即可。
(4)化学镀是靠基体材料的自催化活性才能起镀,其结合力一般优于电镀。
镀层有光亮或半光亮的外观。
晶粒细、致密、孔隙率低。
某些化学镀层还具有特殊的物理性能。
电镀也具有其不能为化学镀代替的优点:(1)可以沉积的金属及合金品种远多于化学镀。
(2)价格比化学镀低得多。
(3)工艺成熟,镀液简单、易于控制。
化学镀铜的应用领域及进展铜具有良好的导电、导热性能,质软而韧,有良好的压延性和抛光性能。
为了提高表面镀层和基体金属的结合力,铜镀层常用作防护、装饰性镀层的底层,对局部渗碳工件,常用镀铜来保护不需要渗碳的部位。
1)印刷线路板通孔金属化处理目前化学镀铜在工业上最重要的应用是印刷线路板(PrintedCircuit Board,简称PCB)的通孔金属化过程,使各层印刷导线的绝缘孔壁内沉积上一层铜,从而使两面的电路导通,成为一个整体。
空气污染源对铜互连中电镀铜模拟工艺影响

卒气污染源对制互连中lU镀制模拟工岂的影响边逸军复旦人学研究生院Gamblingat0.13proTechnology图卜3形象的表明了Cu&Low—k的结合是最符合t30nm技术要求的。
1.2铜制程的基本概念传统的半导体工艺采用铝作为金属互联材料(Interconnect),在信号延时上已经受到限制。
人们寻找到了新的材料来满足对电阻的要求,这种材料就是铜。
简单地说,铜工艺就是指以铜作为金属互联材料的一系列半导体制造工艺。
将铜工艺融入集成电路制造工艺可以提高芯片器件密度集成度,提高时钟频率以及降低功耗。
要达到这样的要求就需要对工艺上做出相应的调整。
在器件尺寸缩小到深亚微米以后,尤其是在90纳米或以下的技术产品中,信号延时主要来自互联线。
这一部分可以用以下公式来描述:t2RC=(PL/wt。
)宰(Ke..Lw/t。
)空气污染源埘{}14Ⅱ连中{U镀锕模拟工岂的影I嘞边逸军复旦人学研究生院其中t是指totalsignaldelay,R是指金属连线的电阻,c是指金属连线与介质层的寄生分布电容,P是互联金属的电阻率,L是指长度,w是指长度,t是指厚度,K是相对介电常数,e。
是真空介电常数(如图卜4所示)。
图卜4公式各个参数的定义由公式可见,选用电阻率比较小的金属材料作为互联材料,和选用介电常数比较小的介质材料作为介质材料是降低信号延时、提高时钟频率的两个主要方向。
铜的电阻率为1.7肛Q.cm,铝的电阻率为2.8uQ.cm,所以铜更为优越。
同时由于采用铜线可以降低互联层的厚度,所以同时也降低了上面公式中的电容c。
为了进一步降低t,产业界也在选择比si02的K值更加低的材料(即所谓的lowk材料)。
现有的铝材料(通常选用掺入少量Cu的hlCu合金材料)在器件密度进一步提高的情况下还会出现由电迁移效应引发的可靠性问题。
而铜在这方面比铝也有很强的优越性。
当IC的电流密度超过106A/cm2时,低熔点的材料比高熔点的材料更易于发生电迁移,原因在于前者具有更高的晶界扩散激活能。
_半导体_大规模集成电路工艺流程

_半导体_大规模集成电路工艺流程半导体大规模集成电路工艺流程是指将半导体材料制作成集成电路芯片的一系列步骤。
下面是一个通常的半导体大规模集成电路工艺流程的简要介绍:1.基片选择:半导体晶圆,也称为基片,通常由硅材料制成。
其尺寸通常为8英寸或12英寸。
在工艺开始前,基片的质量和净化程度必须符合要求。
2.清洗和清理:将基片进行多次的清洗和清理,以去除表面的杂质和污染物。
这包括使用化学物质和超纯水以及特殊的清洗设备进行清理。
3.热氧化:将基片暴露在氧气环境中,并通过高温加热使其形成氧化层。
这一步骤通常用于形成绝缘层,并为后续工序提供基础。
4.光刻:使用光刻胶将光学图案转移到基片上。
通过使用遮罩和紫外线曝光,将光刻胶暴露在特定区域。
接着使用化学液浸入光刻胶中,通过光刻胶保护或去除基片区域。
5.刻蚀和腐蚀:使用化学和物理刻蚀技术,通过将基片暴露在特定的化学物质中,去除部分材料。
这是用来改变基片上的形状和结构。
6.沉积:使用化学气相沉积或物理气相沉积技术,在基片上形成新的材料层。
通常使用化学气相沉积来制造金属、多晶硅或氮化硅等材料层。
7.离子注入:通过将特定的离子注入基片中,改变基片的电子性能。
通过操控离子注入的能量和浓度,可以创建P型或N型半导体区域。
8.金属化:在基片上涂覆一层金属,用于连接不同的器件和电路之间的电子。
金属化层可以是铝、铜等金属。
9.封装和测试:将单个芯片切割成独立的芯片,并采用封装技术将芯片封装在塑料或陶瓷封装中。
封装后,进行电气测试,以验证芯片的功能和性能。
以上是一个简要的半导体大规模集成电路工艺流程。
实际的工艺流程可能会更复杂,并根据芯片的种类和设计进行调整。
不同的工艺流程可以实现不同的功能和性能,是制造半导体芯片的关键步骤。
- 1、下载文档前请自行甄别文档内容的完整性,平台不提供额外的编辑、内容补充、找答案等附加服务。
- 2、"仅部分预览"的文档,不可在线预览部分如存在完整性等问题,可反馈申请退款(可完整预览的文档不适用该条件!)。
- 3、如文档侵犯您的权益,请联系客服反馈,我们会尽快为您处理(人工客服工作时间:9:00-18:30)。
超大规模集成电路铜互连电镀工艺摘要:介绍了集成电路铜互连双嵌入式工艺和电镀铜的原理;有机添加剂在电镀铜中的重要作用及对添加剂含量的监测技术;脉冲电镀和化学电镀在铜互连技术中的应用 ;以及铜互连电镀工艺的发展动态。
关键词:集成电路,铜互连,电镀,阻挡层 1.双嵌入式铜互连工艺随着芯片集成度的不断提高,铜已经取代铝成为超大规模集成电路制造中的主流互连技术。
作为铝的替代物,铜导线可以降低互连阻抗,降低功耗和成本,提高芯片的集成度、器件密度和时钟频率。
由于对铜的刻蚀非常困难,因此铜互连采用双嵌入式工艺,又称双大马士革工艺(Dual Damascene),如图1所示,1)首先沉积一层薄的氮化硅(Si3N4)作为扩散阻挡层和刻蚀终止层,2)接着在上面沉积一定厚度的氧化硅(SiO2),3)然后光刻出微通孔(Via),4)对通孔进行部分刻蚀,5)之后再光刻出沟槽(Trench),6)继续刻蚀出完整的通孔和沟槽,7)接着是溅射(PVD)扩散阻挡层(TaN/Ta)和铜种籽层(Seed Layer)。
Ta的作用是增强与Cu的黏附性,种籽层是作为电镀时的导电层,8)之后就是铜互连线的电镀工艺,9)最后是退火和化学机械抛光(CMP),对铜镀层进行平坦化处理和清洗。
图1 铜互连双嵌入式工艺示意图电镀是完成铜互连线的主要工艺。
集成电路铜电镀工艺通常采用硫酸盐体系的电镀液,镀液由硫酸铜、硫酸和水组成,呈淡蓝色。
当电源加在铜(阳极)和硅片(阴极)之间时,溶液中产生电流并形成电场。
阳极的铜发生反应转化成铜离子和电子 ,同时阴极也发生反应,阴极附近的铜离子与电子结合形成镀在硅片表面的铜,铜离子在外加电场的作用下,由阳极向阴极定向移动并补充阴极附近的浓度损耗,如图2所示。
电镀的主要目的是在硅片上沉积一层致密、无孔洞、无缝隙和其它缺陷、分布均匀的铜。
图2 集成电路电镀铜工艺示意图 2. 电镀铜工艺中有机添加剂的作用由于铜电镀要求在厚度均匀的整个硅片镀层以及电流密度不均匀的微小局部区域(超填充区)能够同时传输差异很大的电流密度,再加上集成电路特征尺寸不断缩小,和沟槽深宽比增大,沟槽的填充效果和镀层质量很大程度上取决于电镀液的化学性能,有机添加剂是改善电镀液性能非常关键的因素,填充性能与添加剂的成份和浓度密切相关,关于添加剂的研究一直是电镀铜工艺的重点之一[1,2]。
目前集成电路铜电镀的添加剂提供商有Enthone、Rohm&Haas等公司,其中Enthone公司的ViaForm系列添加剂目前应用较广泛。
ViaForm系列包括三种有机添加剂:加速剂(Accelerator)、抑制剂(Suppressor)和平坦剂(Leverler)。
当晶片被浸入电镀槽中时,添加剂立刻吸附在铜种籽层表面,如图3所示。
沟槽内首先进行的是均匀性填充,填充反应动力学受抑制剂控制。
接着,当加速剂达到临界浓度时,电镀开始从均匀性填充转变成由底部向上的填充。
加速剂吸附在铜表面,降低电镀反应的电化学反应势,促进快速沉积反应。
当沟槽填充过程完成后,表面吸附的平坦剂开始发挥作用,抑制铜的继续沉积,以减小表面的粗糙度。
加速剂通常是含有硫或及其官能团的有机物,例如聚二硫二丙烷磺酸钠(SPS),或3-巯基丙烷磺酸(MPSA)。
加速剂分子量较小,一般吸附在铜表面和沟槽底部,降低电镀反应的电化学电位和阴极极化,从而使该部位沉积速率加快,实现沟槽的超填充。
抑制剂包括聚乙二醇(PEG)、聚丙烯二醇和聚乙二醇的共聚物,一般是长链聚合物。
抑制剂的平均相对分子质量一般大于1000,有效性与相对分子质量有关,扩散系数低,溶解度较小,抑制剂的含量通常远大于加速剂和平坦剂。
抑制剂一般大量吸附在沟槽的开口处,抑制这部分的铜沉积,防止出现空洞。
在和氯离子的配合作用下,抑制剂通过扩散-淀积在阴极表面上形成一层连续抑制电流的单层膜,通过阻碍铜离子扩散来抑制铜的继续沉积。
氯离子的存在,可以增强铜表面抑制剂的吸附作用,这样抑制剂在界面处的浓度就不依赖于它们的质量传输速率和向表面扩散的速率。
氯离子在电镀液中的含量虽然只有几十ppm,但对铜的超填充过程非常重要。
如果氯浓度过低,会使抑制剂的作用减弱;若氯浓度过高,则会与加速剂在吸附上过度竞争。
平坦剂中一般含有氮原子,通常是含氮的高分子聚合物,粘度较大,因此会依赖质量运输,这样在深而窄的孔内与加速剂、抑制剂的吸附竞争中没有优势,但在平坦和突出的表面,质量传输更有效。
沟槽填充完成后,加速剂并不停止工作,继续促进铜的沉积,但吸附了平坦剂的地方电流会受到明显抑制,可以抑制铜过度的沉积。
平坦剂通过在较密的细线条上方抑制铜的过度沉积从而获得较好的平坦化效果,保证了较小尺寸的图形不会被提前填满,有效地降低了镀层表面起伏。
在铜电镀过程中,对填充过程产生影响的主要是加速剂、抑制剂和氯离子,填充过程完成后对镀层表面粗糙度产生影响的主要是平坦剂。
铜电镀是有机添加剂配合作用的结果,它们之间彼此竞争又相互关联。
为实现无空洞和无缺陷电镀,除了改进添加剂的单个性能外,还需要确定几种添加剂同时存在时各添加剂浓度的恰当值,使三者之间互相平衡,才能达到良好的综合性能,得到低电阻率、结构致密和表面粗糙度小的铜镀层。
尽管使用有机添加剂可实现深亚微米尺寸的铜电镀,但往往会有微量的添加剂被包埋在铜镀层中。
对于镀层来说,这些杂质可能会提高电阻系数,并且使铜在退火时不太容易形成大金属颗粒。
图3 电镀铜表面添加剂作用示意图 A= Accelerator S= Suppressor L= Leveler Cl= Chloride Ion 电镀过程中添加剂不断地被消耗,为了保证镀层的品质,需要随时监控添加剂的浓度。
目前主要使用闭环的循环伏安剥离法(Cylic Voltammetric Stripping,CVS)来监测电镀液的有机添加剂含量。
CVS测量仪器的主要提供商是美国ECI 公司。
CVS尽管硬件成本低,但它很难反映出几种添加剂组分浓度同时改变的准确情况,高效液相色谱(High Performance Liquid Chromatography,HPLC) 分析技术有望能替代CVS 。
3.脉冲电镀和化学镀在铜互连中的应用在目前的集成电路制造中,芯片的布线和互连几乎全部是采用直流电镀的方法获得铜镀层。
但直流电镀只有电流/电压一个可变参数,而脉冲电镀则有电流/电压、脉宽、脉间三个主要可变参数,而且还可以改变脉冲信号的波形。
相比之下,脉冲电镀对电镀过程有更强的控制能力。
最近几年,关于脉冲电镀在集成电路铜互连线中的应用研究越来越受到重视[3,4]。
脉冲电镀铜所依据的电化学原理是利用脉冲张驰增加阴极的活化极化,降低阴极的浓差极化,从而改善镀层的物理化学性能。
在直流电镀中,由于金属离子趋近阴极不断被沉积,因而不可避免地造成浓差极化。
而脉冲电镀在电流导通时,接近阴极的金属离子被充分地沉积;当电流关断时,阴极周围的放电离子又重新恢复到初始浓度。
这样阴极表面扩散层内的金属离子浓度就得到了及时补充,扩散层周期间隙式形成,从而减薄了扩散层的实际厚度。
而且关断时间的存在不仅对阴极附近浓度恢复有好处,还会产生一些对沉积层有利的重结晶、吸脱附等现象。
脉冲电镀的主要优点有:降低浓差极化,提高了阴极电流密度和电镀效率,减少氢脆和镀层孔隙;提高镀层纯度,改善镀层物理性能,获得致密的低电阻率金属沉积层。
除了电镀以外,还有一种无需外加电源的沉积方式,这就是化学镀。
化学镀不同于电镀,它是利用氧化还原反应使金属离子被还原沉积在基板表面,其主要特点是不需要种籽层,能够在非导体表面沉积,具有设备简单、成本较低等优点。
化学镀目前在集成电路铜互连技术中的应用主要有:沉积CoWP 等扩散阻挡层和沉积铜种籽层。
最近几年关于化学镀铜用于集成电路铜互连线以及沟槽填充的研究亦成为一大热点,有研究报道通过化学镀同样可以得到性能优良的铜镀层[5,6]。
但是化学镀铜通常采用甲醛做为还原剂,存在环境污染的问题。
4.铜互连工艺发展趋势使用原子层沉积(ALD ,Atomic Layer Deposition)技术沉积阻挡层和铜的无种籽层电镀是目前铜互连技术的研究热点[7]。
在当前的铜互连工艺中,扩散阻挡层和铜种籽层都是通过PVD工艺制作。
但是当芯片的特征尺寸变为45nm或者更小时,扩散阻挡层和铜种籽层的等比例缩小将面临严重困难。
首先,种子层必须足够薄,这样才可以避免在高纵宽比结构上沉积铜时出现顶部外悬结构,防止产生空洞;但是它又不能太薄。
其次,扩散层如果减薄到一定厚度,将失去对铜扩散的有效阻挡能力。
还有,相对于铜导线,阻挡层横截面积占整个导线横截面积的比例变得越来越大。
但实际上只有铜才是真正的导体。
例如,在65nm 工艺时,铜导线的宽度和高度分别为90nm和150nm,两侧则分别为10nm。
这意味着横截面为13,500 nm2的导线中实际上只有8,400 nm2用于导电,效率仅为62.2%[7]。
目前最有可能解决以上问题的方法是ALD和无种籽电镀。
使用ALD技术能够在高深宽比结构薄膜沉积时具有100%台阶覆盖率,对沉积薄膜成份和厚度具有出色的控制能力,能获得纯度很高质量很好的薄膜。
而且,有研究表明:与PVD阻挡层相比,ALD阻挡层可以降低导线电阻[7]。
因此ALD技术很有望会取代PVD技术用于沉积阻挡层。
不过ALD目前的缺点是硬件成本高,沉积速度慢,生产效率低。
此外,过渡金属-钌可以实现铜的无种籽电镀,在钌上电镀铜和普通的铜电镀工艺兼容。
钌的电阻率(~7 μΩ-cm),熔点(~2300℃),即使900℃下也不与铜发生互熔。
钌是贵金属,不容易被氧化,但即使被氧化了,生成的氧化钌也是导体。
由于钌对铜有一定的阻挡作用,在一定程度上起到阻挡层的作用,因此钌不仅有可能取代扩散阻挡层常用的Ta/TaN两步工艺,而且还可能同时取代电镀种籽层,至少也可以达到减薄阻挡层厚度的目的。
况且,使用ALD技术沉积的钌薄膜具有更高的质量和更低的电阻率。
但无种籽层电镀同时也为铜电镀工艺带来新的挑战,钌和铜在结构上的差异,使得钌上电镀铜与铜电镀并不等同,在界面生长,沉积模式上还有许多待研究的问题。
5.结语铜互连是目前超大规模集成电路中的主流互连技术,而电镀铜是铜互连中的关键工艺之一。
有机添加剂是铜电镀工艺中的关键因素,各种有机添加剂相互协同作用但又彼此竞争,恰当的添加剂浓度能保证良好的电镀性能。
在45nm或更小特征尺寸技术代下,为得到低电阻率、无孔洞和缺陷的致密铜镀层,ALD和无种籽电镀被认为是目前最有可能的解决办法。
此外,研究开发性能更高的有机添加剂也是途径之一,而使用新的电镀方式(比如脉冲电镀)也可能提高铜镀层的质量。
参考文献 [1]Tantavichet N, Pritzker M.Effect of plating mode, thiourea and chloride on the morphology of copper deposits produced in acidic sulphate solutions [J]. Electrochimica Acta, 2005, 50: 1849-1861 [2]Mohan S, Raj V. The effect of additives on the pulsed electrodeposition of copper [J]. Transactions of the Institute of Metal Finishing, 2005, 83(4): 194-198 [3]Y. Lee, Y.-S. Jo, Y. Roh. Formation of nanometer-scale gaps betweenmetallic electrodes using pulse/DC plating and photolithography [J]. Materials Science and Engineering C23 (2003): 833-839 [4]Song Tao, D Y Li.Tribological,ÎÒÈ¥mechanical and electrochemical properties of nanocrystalline copper depositsproduced by pulse electrodeposition [J]. Nanotechnology 17 (2006) 65–78 [5]王增林,刘志鹃,姜洪艳等. 化学镀技术在超大规模集成电路互连线制造过程的应用 [J]. 电化学, Vol.12 No.2 May 2006 :125-133 [6]Rajendra K. Aithal, S. Yenamandra andR.A. Gunasekaran, etc. Electroless copper deposition on silicon with titaniumseed layer [J]. Materials Chemistry and Physics 98 (2006) 95–102 [7]45nm铜工艺面临的挑战. Peter Singer, Semiconductor International [J]. Jul. 2004。