铜互连技术
半导体镀膜设备国产化分析报告

全球镀膜工艺市场规模及细分市场
口 全球半导体薄膜沉积市场预计到2025年将达到360亿美元;从2017年到2025年将以复合年增长率 14.1%的速度增加。由于高效能DRAM、AMOLED显示屏以及安装太阳能电站等新兴应用需求的增 加是驱动半导体薄膜沉积市场增长的核心驱动力; 从半导体镀膜细分市场上看,CVD占比最大,市占率达到55%,PVD市占率约24%,其次是ALD 等 其他镀膜设备。
20
20
18
%
16
18 %
14
16
12
%
10
14
8
%
6
12
%
4
10
2
%
0 201
201
201
201
201
2018H 8%
3
4
5
6
7
1
6%
R&D
研发占比
4%
2%
2013-2018年年应用材料毛利率、净利率情况
50
4 5
4 0
35
30
2 5
2 0
15
10
201 3
5
0
2014 201
5
2016 201
7
北方华创硅刻蚀机与国外技术差距
西南电子
西南电子
西南电子
数据来源:北方华创,西南证券整理
镀膜 工艺
三大 工艺
集成电路中不同薄膜的作用
IC中的薄膜类型:
介电质薄膜(SiO2、SiN):用来隔离导电层、作为扩散及离子注入的掩蔽膜,或是防止掺杂物的流 失,或用来覆盖器件免受杂质、水汽或刮伤的损害。
口 多晶硅:MOS器件的栅淀积材料,多层金属导通材料或接触材料。 金属薄膜(铝、铜或金属硅化物):形成低电阻值金属连线。数据来源:,西南证券整理镀膜 工艺
电脑CPU超频的五大危害~电脑DIY小知识

电脑CPU超频的五大危害~电脑DIY小知识1、免费的升级何乐不为中央处理器(CPU)从本质上说是信号处理器,将来自键盘、硬盘或者其它设备的信号由输入针脚送至CPU核心,经过指定变换处理,转换成所需信号,再由输出针脚送至内存,显卡或其它设备。
CPU处理信号的快慢,即CPU性能的高低一直以来是人们关注的焦点,可以说CPU的发展史实际上也是一部CPU的性能增长史。
根据CPU性能=IPC(每时钟周期执行的指令数)×频率(MHz)的公式,单独提升IPC、主频,或同时提升两者都可使处理器的性能得以提升。
因此CPU的内部架构和运行频率一直都是中央处理器的重要特征。
对于消费者来说,无法改变CPU的内部结构设计以提升IPC,因此提高CPU的运行频率就成了人们获得额外性能的唯一方法。
这也就是超频行为的由来和出现的必然性原因。
最早的超频记录为Amiga 500的Motorola芯片从9MHz超到12MHz,英特尔80286从8MHz超到12MHz。
但那时的超频行为是个别技术高手才能做的事情,需要用烙铁更换主板上的晶振来改变频率。
真正超频作为一种大众行为开始普及——几乎人人可做,Intel公司于1998年推出的赛扬300A处理器功不可没。
这款可以轻松将主频和性能提升50%的处理器成为超频史上经典中的经典,也将超频和CPU紧紧联系再一起。
2、超频并非仅仅为了性能此后,超频不仅仅成为一种获得提升性能的有效方法,也成为大众玩家竞相为之的时尚行动。
何种产品好超,可以超到多少等等问题开始各大论坛上的热门话题,甚至于为什么无法超频的问题成为电脑医院的长期客户。
相互攀比的结果进一步刺激了超频行为,进而开始产生各类成绩的排行榜,比如CPU超频幅度排行、SuperPI 百万位成绩排行和3DMark成绩排行榜等等。
还出现了一些以超频为宗旨,企图或者已经混迹于各类排行榜的电脑玩家。
超频行为也成为一部分人满足心理需求的重要手段。
由超频行为逐渐聚集起的庞大消费群体所引发的需求也渐渐衍生出为超频服务的技术、产品和行业。
不同浓度添加剂对铜镑层性能的影响

203 ) 04 3
摘要: 前, 目 随着集成电路规模 的不断发展 , 传统的铝互连技术 已由铜互连技术取代。铜的超填充主要 采用 D m see aa cn 工艺进行电镀 。 电镀液中有机添加剂 ( 在 包括加速剂、 抑制剂和平坦剂 ) 虽然含量很 少,
但对 镀层 性 能的影 响 至关 重要 。本文 以 E t o e公 司的 V a o m系列添加 剂 为例 ,研 究 了不 同添加 剂 n hn iF r
kH. —I … n h
^…
j …
…
- - ^
维普资讯
低介电系数材料的应用技术应运而生。
由于铜在导电方面具备卓越的性能 ,采用铜互 连线的器件在层数上只需达到采用铝互连线的一半
时就 可 以实 现相 同的功能 。 因此 , 当铜互 连工 艺 日趋
i g n .
Ke r : o e t r o n c ; g i d tv s p lepltn ; y wo ds c pp ri e c n e t Or a ca iie ; u s a i gXRD ;e itvt n n d 世纪的时 间里 ,
解槽底部靠近阴极处有一个磁力搅拌子 , 电镀时 , 置 于电解槽下面的磁力搅拌仪产生磁场,驱动搅拌子 匀速转动 , 转速设定为 40转 , , 0 分 这可以使电镀过
程 中阴极 附近 电解 液 中 的 c u离 子 浓 度保 持 正 常 ,
成熟时, 采用铜互连线 的器件将会主宰半导体行业。
c u i r h o p r l t gp o e s T i a e b u t d i g o a h tp f d i v s i a t n c p e l t r ca f e c p e a i r c s . h sp p r sa o t u y n f c e o d t e ’ mp c o p r a — l o t p n i s e y a i o p
集成电路用磷铜阳极及相关问题研究
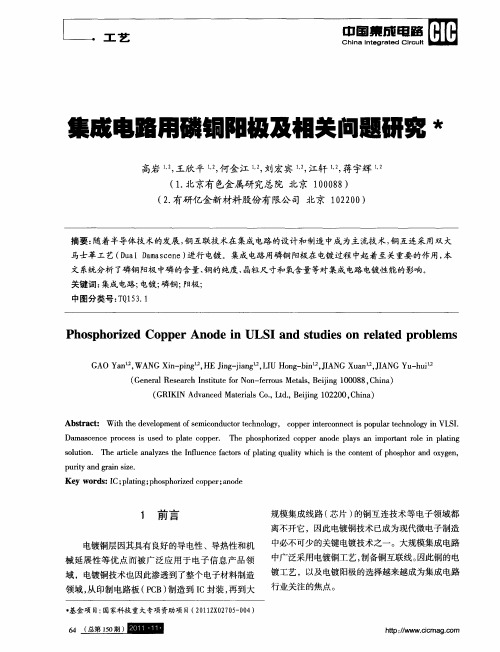
中图分类 号 : Q 3 1 T 1 5.
P o p o ie p e o e i h s h rz d Co p r An d n ULS n t d e n r l t d p o lm s I a d su i so e a e r b e
电镀 成本 。
电镀铜是完成铜填充的主要工艺 ( 1 图 中③ ) , 该工艺要求在制备超微结构刻槽 的铜连线过程 中电 镀铜必须具有很高 的凹槽填充能力 ,因此就对 电镀
过程 中的电镀 阳极 , 电镀液 , 有机添加剂等的要求很
高, 特别是 电镀用磷铜阳极的要求就更高 。 集成电路用磷铜阳极通常是 由高纯磷铜合金构 成; 铜电镀液通常由硫酸铜、 硫酸和水组成 。在 电镀 溶液中,当电源加在带有铜种子层的硅片 (阴极 )
规模集成线路 ( 芯片 ) 的铜互连技术等 电子领域都 离不开它,因此电镀铜技术已成为现代微电子制造 中必不可少的关键 电镀技术之一 。大规模集成电路 中广泛采用 电镀铜工艺, 制备铜互联线 。 因此铜的电
域 ,电镀铜技术也因此渗透到了整个 电子材料制造 镀工艺 ,以及电镀 阳极 的选择越来越成为集成电路 领域 , 印制电路板 ( C ) 从 P B 制造到 I C封装 , 再到大 行业关 注 的焦点 。
磁力搅拌效果好 , 铜磷熔融搅拌均匀 , 自动控制 , 这样制造的铜阳极磷分布均匀 溶解均匀 ,结晶细 致 晶粒细小 , 阳极利用率高 , 有利于镀层光滑光亮 , 减少 了毛刺和粗糙缺陷圆 随着大规模集成电路引入酸『电镀铜技术的发 生 晶圆上的更细线宽、 更小孑 径 、 L 线路 的密集化 和 多层化对铜镀层的要求就越来越严格 镀层的硬度 、 晶粒的精细 小孑 分散能力以及镀层的延展性等物 L 理化学特性要求磷铜阳极的质量更加的精细
浅谈现代集成电路28nm芯片制造工艺A(前端FEOL)

浅谈现代集成电路28nm芯片制造工艺A(前端FEOL) 全球90%以上集成电路都是CMOS工艺制造的,经历了半个多世纪发展进化,芯片集成度从一个芯片包含几十个器件进化到几十亿个器件。
从上世纪60年代MOS器件采用铝栅工艺,70年代采用了硅栅工艺,铝线互连,进化到现代集成电路采用高K金属栅、超低k介质多层铜线互连,以及FD-SOI和FinFET立体结构。
制造工艺也越来越复杂。
下面就纳米级体硅平面型CMOS集成电路工艺流程,展现芯片先进制程不断丰富现代集成电路制造工艺。
1)现将几种先进制程工艺简介如下:50多年发展,集成电路制造过程工艺越来越复杂,先进制程不断完善。
首先为了抑制短沟道效应,提高栅极对沟道的控制能力,提高栅极电容,栅氧化层厚度不断减薄。
对于厚度大于4nm的栅氧化层,SiO2是理想的绝缘体,不会形成栅漏电流。
当纯二氧化硅厚度小于3nm时,衬底的电子以量子形式穿过栅介质进入栅极,形成栅极漏电流。
(量子隧穿)栅极漏电导致功耗增加,IC 发热且阈值电压飘移,可靠性降低。
为提高介质绝缘特性,当特征尺寸达到0.18μm时采用氮氧化硅代替二氧化硅。
特征尺寸进入90nm节点,单纯缩小厚度不能满足器件性能的要求了,于是采用提高氮氧化硅含氮量以增加介电常数k,但SiON厚度低于14Å会严重遂穿,栅极漏电剧增。
45nm节点之后氮氧化硅已经不能满足mos器件正常工作的要求,开始使用高k介质HfO2代替SiON来改善栅极漏电问题,同时采用金属栅解决费米能级钉扎和多晶硅栅耗尽问题。
尽管在0.35μm技术节点开始采用掺杂多晶硅与金属硅化物(WSi)鈷(镍)多晶硅化物栅叠层代替多晶硅栅,降低了多晶硅栅的电阻。
但金属栅电阻要比金属硅化物还要小。
高k金属栅HKMG.采用高k介质材料替代SiO2。
二氧化硅k=3.9,氮氧化硅k=4~7,高K介质(HfO2和,HfSiON)=15~25。
同样等效氧化层厚度时,高k材料的物理厚度是SiO2的3~6倍。
博士论文开题报告-文献综述

学科代码编号文献综述学号:0040509010研究生:王新建导师:吴建生教授姜传海教授研究方向:材料科学论文题目:学科:材料学学院:材料科学与工程系入学时间:2004年9月开题时间:2005年10月20日年月日0 引言 (1)1.大规模集成电路的发展以及铜互连工艺的概述 (2)1.1.大规模集成电路的发展概况 (2)1.2.ULSI中铝互连线的发展 (4)1.3.ULSI中铜互连线工艺的提出、发展及存在的问题 (5)1.3.1.铜互连工艺的提出 (5)1.3.2.铜互连技术的主要问题 (8)2.铜互连的扩散阻挡层的发展现状的概述 (10)3.扩散基本理论以及铜互连薄膜中的二维扩散研究的现状 (12)3.1.Fick扩散定律及扩散系数 (13)3.1.1.Fick第二扩散定律 (13)3.1.2.扩散系数的确定及Arrhenius公式 (14)3.2.薄膜扩散理论 (14)3.2.2.单晶薄膜的扩散动力学理论的研究 (15)3.2.3.多晶薄膜扩散动力学理论的研究 (16)3.3.溶质对晶粒间界扩散的影响 (21)3.3.1溶质在高温时增加晶粒间界扩散 (21)3.3.2溶质在低温时减小晶粒间界的扩散 (22)3.4.铜薄膜中铜原子层间的扩散失效 (22)4.铜互连膜合金化的研究现状 (23)5.本课题的研究思想、研究目标和研究内容及可行性分析 (25)5.1.本课题的研究思想 (25)5.2.研究的内容、研究目标及拟解决的关键问题 (25)6.年度研究计划及预期研究结果 (28)7.目前的初步研究结果 (28)参考文献 (31)0 引言金属化是集成电路一道重要的工序,在集成电路制造工艺中Al是最早使用的内连线材料,然而随着集成电路集成度的不断提高,铝线逐渐不能适应新的要求。
其中电阻率偏高和易产生电迁移失效是Al线的主要不足。
采用Cu作为内连线材料有以下优点:(a) 电阻率低。
Cu的电阻率是1.7 μΩ·cm,比Al的电阻率2.7 μΩ·cm(200℃)低,降低了RC延迟,提高了集成电路的速度。
ALD应用 PPT课件

ALD
厚度的均匀 好 性
薄膜密度
好
台阶覆盖
好
界面质量
好
原料的数目 不好
低温沉积
好
沉积速率
不好
工业适用性 好
MBE 较好 好 不好 好 好 好 不好 较好
CVD Sputter Evapor
好
好
较好
好
好
不好
多变
不好
不好
多变
不好
好
不好
好
较好
多变
好
好
好
好
好
好
好
好
PLD 较好 好 不好 多变 不好 好 好 不好
一.高K介质材料
➢ 集成器件的小型化给当前材料的持续使用带来了严 峻的挑战。在传统的微电子电路,由于二氧化硅介电层 的物理限制,由硅/二氧化硅/金属组成的电容器,将无 法运作。在纳米尺寸的二氧化硅的介电常数(κ)不足 以防止泄漏电流,导致不必要的电容放电。新的更高的 κ材料正在考虑。 1.5-10 nm厚层Zr、Hf和铝硅氧化物, ALD的生长过程产生的电流比SiO2的等效厚度具有更低的 栅极漏。
ALD技术的主要优点
•前驱体是饱和化学吸附,保证生成大面积均匀性的薄膜 •可生成极好的三维保形性化学计量薄膜,作为台阶覆盖和 纳米孔材料的涂层 •可轻易进行掺杂和界面修正 •可以沉积多组份纳米薄片和混合氧化物 •薄膜生长可在低温(室温到400℃)下进行 •固有的沉积均匀性,易于缩放,可直接按比例放大 •可以通过控制反应周期数简单精确地控制薄膜的厚度,形 成达到原子层厚度精度的薄膜 •对尘埃相对不敏感,薄膜可在尘埃颗粒下生长 •排除气相反应 •可广泛适用于各种形状的基底 •不需要控制反应物流量的均一性
微电子技术的发展现状与趋势-张志勇

西北大学信息科学与技术学院 张志勇
1
微电子技术的战略地位与作用 微电子技术的发展历史与现状 微电子技术的发展规律与趋势
2
什么是微电子学或微电子技术?
电
子
微电子学
学
微电子学(Microelectronics )
—— 微型电子学
3
微电子技术的核心—— 集成电路
(Integrated Circuit,缩写IC)
市场
超薄显示器* IC 卡* 地面微波广播* DNA 生物芯片 多用途通讯设备* 半导体设备* 电力交通工具 墙壁式超薄电视* 移动电话* 直接引入工具 ITS 设备 DNA 加工食品 液晶显示器* 仿制品 燃油汽车
销售额 (10 亿美元)
170 165 160 160 155 150 150 145 140 140 140 135 120 115 110
17
微电子技术的发展水平和微电子 产业的规模已经成为衡量一个国 家综合实力强弱的重要标志!
18
微电子技术的发展历史与现状
19
理论推动
▪ 19世纪末20世纪初发现半导体的三个重要 物理效应
– 光电导效应 – 光生伏特效应 – 整流效应
▪ 量子力学 ▪ 材料科学
需求牵引:二战期间雷达等武器的需求
26
发展历史
第一个CPU--Intel 4004
1971年由Intel制造 2000多个晶体管 10μm的PMOS工艺
27
发展历史
Intel 8088
• 1979 年3月
• 16 Bit
•5到
28
Intel 386
• 1985 年10月
• 32 Bit
- 1、下载文档前请自行甄别文档内容的完整性,平台不提供额外的编辑、内容补充、找答案等附加服务。
- 2、"仅部分预览"的文档,不可在线预览部分如存在完整性等问题,可反馈申请退款(可完整预览的文档不适用该条件!)。
- 3、如文档侵犯您的权益,请联系客服反馈,我们会尽快为您处理(人工客服工作时间:9:00-18:30)。
铜互连技术周江涛、周长聘、严玮俊、沈系蒙、陈龙摘要:在集成电路中采用双镶嵌工艺制备互连线,铜作为互连线的材料具有低电阻率和较好的抗电迁移能力等优点,同时存在新的缺陷模式如沟槽缺陷、气泡缺陷、金属缺失等,目前的工作主要是该工艺的完善。
1、引言:铜互连技术指在半导体集成电路互连层的制作中采用铜金属材料取代传统铝金属互连材料的新型半导体制造工艺技术。
由于采用铜互连线可以降低互连层的厚度,使得互连层间的分布电容降低,从而使频率提高成为可能。
另外,在器件密度进一步增加的情况下还会出现由电子迁移引发的可靠性问题,而铜在这方面比铝也有很强的优越性。
铜的电阻率为1.7μΩ•cm,而铝的电阻率为2.8μΩ•cm,所以铜的导电率大大高于铝。
由于采用铜互连线可以降低互连层的厚度,使得互连层间的分布电容降低,从而使频率提高成为可能。
另外,在器件密度进一步增加的情况下还会出现由电子迁移引发的可靠性问题,而铜在这方面比铝也有很强的优越性,铜的熔点为1083℃,铝的熔点为660℃,铜更不容易发生电迁移。
铜互连技术于1998年被引入后,得到了良好的发展,目前已经成为130nm以下节点技术所必须采用的工艺技术。
当前铜互连层已经由原来的6~7层发展到现今的9~10层。
本文将按如下次序介绍:Cu淀积(用于生长籽晶);铜图形化方法--铜图形化有三种方法:镶嵌工艺(damascene), 剥离工艺 , 铜刻蚀;抛光(完成互连制备)。
铜互连工艺简介:Cu的互连工艺最早在1997年9月由IBM提出来的,被称为是镶嵌工艺(也称大马士革)。
并应用于制备微处理器、高性能存储器及数字信号处理器等等。
它采用对介电材料的腐蚀来代替对金属的腐蚀来确定连线的线宽和间距。
镶嵌工艺分为单镶嵌和双镶嵌。
它们的区别就是在于穿通孔和本曾的工艺连线是否是同时制备的。
2、铜籽晶层制备经过一系列布线刻槽和穿通孔加工完毕后,是Cu的淀积过程。
由于铜虽然电阻率和电迁移特性优于铝, 但是也有不如铝的方面。
铜对二氧化硅等材料的粘附性很弱,而且在二氧化硅中的扩散系数很大, 所以铜互连线外面需要有一层DBA P (diffuSion barrier and adheSion promoter) , 简称为阻挡层(barrier) , 阻挡层可为氮化硅(Si3N4 )、氮化钛(T iN )、氮化钨(WN )、钽(Ta) 等。
为了能更好地电度上Cu,需要先做上一层薄薄的Cu籽晶层,它对二氧化硅等材料的粘附性却很强,之后再电度Cu。
目前有多种途径来生长种籽层:(溅射法、化学气相淀积法、原子层淀积法)。
A、溅射法制备种籽层:溅射是物理气相淀积的形式之一,具有工艺简单,能够淀积高熔点的金属和原位溅射刻蚀等优点。
因此溅射是目前集成电路工业铜种籽层最主要的制备方法。
由于铜容易与其他材料发生反应,粘附系数高,因此在填充高宽比大的引线孔和沟槽时,往往会先将洞口上方堵塞,从而在引线孔和沟槽中留下孔洞,无法完全填充,这样势必会对器件造成很大影响。
因此需要采用溅射方法,如准直溅射法和长距离抛镀法,以及离子化物理气相淀积等改善溅射过程的填充能力。
改进方法:准直溅射、长距离抛镀准直溅射的改进与传统溅射方法相比,在溅射靶和衬底之间放置了一块过滤栅格,它只能允许栅格方向的铜原子通过,并将沿其他方向溅射原子过滤,这样就减少铜原子淀积到边墙的可能。
但这种方法的缺点时淀积速率大大降低。
另一种传统改进方法是长距离抛镀。
在长距离抛度中,溅射靶和衬底之间间距拉大,通过减小溅射源的有效尺寸来限制铜原子的入射角度,从而改善台阶覆盖能力。
这个溅射工艺需要较低的压强,才能保证铜原子从溅射靶到衬底的途中不会相互碰撞。
而且靶和衬底间加了上KV的电压,能使金属离子有充分的动能和方向性,改善了填充能力。
长距离抛镀的缺点是淀积速率也比较低。
这种方法也称离子化的物理气相淀积(IPVD)。
目前最有前景的一项IPVD技术基于磁控溅射方法。
金属粒子流从磁控管靶打出,然后通过射频或某种特殊设计的磁控源电离成金属离子。
电子回旋共振(ECR)放电方法在近年来得到应用。
大部分蒸发的铜原子都被电离,这样在溅射靶和衬底之间形成铜蒸汽的等离子体,电势差位50v左右。
比起传统的蒸发方式,ECR能提供更好的填充性。
B、化学气相淀积:铜的化学气相淀积采用有机金属的前驱物来作为淀积铜薄膜的来源。
CVD方法有两个主要问题,首先是前驱物的选择,前驱物必须具有很好的挥发性。
其次反应副产物会影响淀积铜薄膜的纯度。
但CVD可以提供很好的洞孔填充能力和台阶覆盖性,这是CVD比PVD的主要优势。
CVD装置是由一个冷壁的反应器,只有衬底被加热。
在热壁反应器中整个反应腔被加热,但这会导致铜淀积到反应腔壁上。
常用的前驱物是Cu(I)和Cu(II)。
Cu(I)的化合物是Cu(Ln),其中(Ln)为有机团基。
它具有较高的蒸汽压,可以在较低的温度淀积铜,并且不需要借助还原气体反应,为液体,但缺点是在室温下不稳定;Cu(II),它需要借助还原气体才能进行反应,如H2。
它在室温下能稳定存在,是固体,这在控制蒸发和输运上有一定的困难,所以可以将它先溶解在溶剂中,通过控制溶剂的输运进入反应器。
其中反应方程:在铜淀积过程中, 通过用等离子体激发反应物可以使反应更为有效。
CVD方法制备通常可以达到100nm/min。
由于前驱物分子从不同方向进行反应,通常薄膜的保角性很好。
前驱物粘附系数应当小,这样才不会在洞口上发生反应。
当然,前驱物应当具有较大的表面扩散系数。
C、原子层淀积(ALD):是基于交替的饱和表面反应。
在ALD工艺中,前驱物交替进入反应器,每一时刻反应腔只有一种反应物,之间通过惰行气体将多余的反应物和副产物排出,由于表面反应是自限制的,理论上ALD每生长周期里只淀积单个原子层厚的薄膜,虽然速度慢,但实现大面积均匀生长和良好的高形态比台阶覆盖能力,这使得ALD越来越受到关注。
ALD工艺中使用CuCl2做反应物,H2做还原剂。
在上述的这些工艺,ALD工艺结果最好,它可以淀积在氮化物阻挡层上,而且薄膜杂质含量低。
典型的ALD周期是由12秒的反应脉冲和20秒排气脉冲组成。
电阻率随膜厚度的增加而减小。
当淀积的膜厚度为120nm时,电阻率仅为1.78μΩ*cm。
而厚度为20nm时,由于电子界面散射效应,将增大为4.25μΩ*cm。
3、镀铜电镀工艺的主要目的是在晶片上镀一层致密、无孔洞、无缝隙和其他缺陷、分布均匀的铜。
此外,在对大尺寸、空旷区结构进行填充的同时,要能对密集区、高纵宽比结构和微通孔等进行填充。
当然,最好电镀后表面能够尽可能平坦,减少后续。
现有多种沉积铜的工艺,即非电学淀积(物理气相淀积、化学气相淀积)电离-56、电镀和化学镀等。
下面先介绍一下电化学镀铜(ECP)来制备铜互连线:电镀铜通常成本低,产率高,洞孔填充好等优点,而被广泛应用。
在电镀过程中,衬底做阴极,阳极处的溶液提供铜离子,在电场作用下将不断淀积到硅片表面。
最常用的ECP电镀液基于酸性如硫酸,一些碱性也在研制中。
ECP不能直接淀积到绝缘物上,所以先淀积一层导电层。
这一层可以时阻挡层,也可以时CVD或PVD淀积的铜种籽层。
ECP可以分为三个部分:两电极附近的边界层和中间体区。
在边界层中,离子的扩散是通过浓度梯度,而在体区离子的输运是在电场下作用进行。
一般来说,铜离子能够完成的转化为镀膜的铜原子,所以镀膜的速率就可以用电流密度来衡量。
硅片表面镀膜的均匀性主要由电流分布决定。
电压与电流的关系是:当电压较小时,电流随着电压增大而增大。
当电压到一定值后,电流达到上限,这上限电流与系统的质量输运有关。
如果在电极加电压,通过分析电流和时间的关系图,就可以得到ECP中的成核和薄膜生长情况。
使用硫酸钾和硫酸铜混合溶液做电镀液,PH=4。
起初两边界层进行充电,之后电流与时间关系主要由新核的产生与已形成核的生长之间的竞争决定,很多情况下,每个核周围会形成一个离子耗尽扩散区,这区域限制了新核的产生,也限制了已形成核的生长。
如果扩散区之间没有重叠,那么可以用下式描述成核速度:N0为成核点的数量,A为成核速率常数。
当At >> 1时,得到N=N0,称立即成核,即刚开始就有这些核形成,此时电流密度正比时间的1/2次方;当AT << 1时,得到N << N0,称逐步成核,即成核数随时间线性增长,此时电流密度正比时间3/2次。
4、抛光(CMP)铜淀积工艺完成后的下一步关键技术就是采用化学机械抛光技术, 将沟槽以外的多余的铜除去, 留下沟槽中的铜, 实现铜互连技术中铜引线的图形化。
由于金属铜是一种易于氧化和变形的金属, 所以, 很适合采用CMP 方法来对其进行抛光。
表面平整度问题仍然是化学机械抛光技术中的一大难点, 易腐蚀性使得铜在抛光后可能形成凹坑和过腐蚀现象, 使得铜引线的可靠性下降, 可通过改变垫片硬度、调整压力、转速及抛光液的流量和组分比等方法来使其平整度接近理想化。
化学机械抛光后的清洗工艺也是铜CMP 技术中的一步关键步骤, 由于在抛光过程中, 硅片的背面和侧面都有可能沾有含铜的物质, 如果不及时将其去除, 则会直接影响到器件的性能。
另外, 由于铜在空气中容易氧化,而且不能形成自保护层来阻止其进一步氧化和腐蚀。
因此, 当CMP 工艺完成之后, 应立即给铜的表面生长一层保护层,以防止其在空气中的氧化, 目前普遍采用在表面淀积一层Si3N4 或选择性淀积W 的方法作为铜的表面保护层。
A. 平坦化技术图表示了ILD:①未作平坦化;②部分平坦化;③局部平坦化;④全局平坦化之区别。
圆片在具有流动性,能较好地圆滑表面,属于部分平坦化,同时它还能起到钝化作用,在其上光刻/ 刻蚀出接触区,淀积第1 层金属,构成最初的金属互连。
由于金属熔点较低,在淀积金属后不能再采用高温工艺,所以一般首先使用等离子体增强化学气相淀积(PECVD)淀积SiO2、Si3H4 以构成后继的ILD,此时需要平坦化处理介质层;然后刻蚀出通孔(Via),形成与第2 层金属相连用的插塞;最后淀积金属、光刻/ 刻蚀金属,制备出第2 层金属互连。
重复上述过程,即制成多层互连的晶圆。
部分平坦化之法还有回蚀刻(Etch-back)和侧墙等技术。
局部平坦化的特点是在一定范围的硅片表面上实现平坦化,主要技术为旋涂玻璃(SOG)法。
SOG 是一种相当于SiO2 的液相绝缘材料,通过类似涂胶的工艺,将其有效地填满凹槽以实现局部平坦化。
全局平坦化则主要通过化学机械抛光(CMP)来实现,其特点是整个硅片表面上介质层是平整的。
B. CMP 技术CMP是通过圆片和抛光头之间的相对运动来平坦化圆片表面。
在圆片与抛光头之间有研磨液,并同时施加压力(见图3 )。