武钢1#高炉第三代生产操作概要
试析武钢GK1B改造机车显示屏设计

试析武钢GK1B改造机车显示屏设计摘要:将传统的轨道牵引机车由燃油动力变成电动驱动,再让电动机车运营实现绿色环保,为中国的“双碳”战略和低碳经济做出更多重要贡献,助推企业实现高质量发展。
公司紧盯国家“双碳”战略,聚焦工业低碳细分目标,坚持自主创新,打造内燃机车和新能源纯电动轨道牵引机车的精品。
关键词:GK1B改造机车;节能环保型;显示屏设计微机显示屏主界面向司机提供了机车基本运行参数,如机车速度、工况、牵引力、柴油机转速、动力电池SOC、列车管和均衡风缸压力等,并提供机车状态图标指示器,以及机车的故障信息和提示信息。
主界面是微机显示屏操作界面的第一级界面,通过点击主界面下方的附有文字的按钮(或相对应的按键),可以进入下一级操作界面。
为了便于人机交互功能,将主界面进行分区划分为A、B、C、D、E,5个大区,每个大区包含若干个小区,通过对微机显示屏的操作,进入各功能界面,在各功能界面,司机可获取机车的状态、故障等运用信息,并可以在界面上进行机车功能设置、故障复位等操作,以及机车维护等操作。
网络系统界面提供了列车的所以系统的运行状态,可以清晰地查看各个子系统状态。
其中红色表示设备通信故障、绿色表示通信正常。
为了能够满足机车的设计要求,需要规范显示屏设计,先要选型适合的显示屏硬件,然后再定制具体开发规范,最后再编写具体应用软件。
1显示屏的基本情况介绍1.1显示屏的硬件分析GK1B改造机车节能环保型调车机车的显示屏主要是进行复杂控制的设备,同时还可以进行指示操作,这是一个比较系统的设备。
上面显示的过程和数据需要外部操作才可以输入相关信息,在具体操作过程中可以通过按键或者是触屏方式进行相关操作。
GK1B改造机车显示屏应用的是10.4英寸屏幕,具有LED背光功能,其分辨率是81024×768液晶屏,配备了2个网络接口,还有具有 2 路独立CAN 通讯功能,以及1个USB接口。
显示屏的电源是DC24V,防护等级是IP65。
中国高炉情况表

1.4000m3级高炉(4座,17223m3)
宝钢4号 4747
宝钢3号 宝钢2号 宝钢1号
4350
4063
4063
2.3000m3级高炉(5座,16000m3)
武钢5号 3200
沙钢3号 2680
本钢7号 2600
武钢6号 鞍钢新1号 鞍钢新2号
3200
3200
3200
3.2000m3级高炉(35座,82641m3)
包钢3号 2200
包钢4号 2200
涟钢新1号 韶关7号 南京新1号 首钢4号
2200
2200
2200
2100
攀钢5号 2000
宣钢9号 2000
酒钢1号 1800
邯钢7号 昆钢6号 唐钢2号
2000
2000
2000
4.1000m3级高炉(58座,73231m3)
云南玉溪明
湘钢4号
定
首钢2号
1800
重钢5号
1200 广东河源德
润
攀钢2号
1200 山东奥华微
坊
本钢6号 2600
首钢1号 2536
莱钢 2218
安阳9号 2200
天钢1号 2000
济钢8号 1750
海鑫2号 1380
梅山3号 1250
攀钢3号 1200
湘钢新1 号
炉容,m3 厂名,炉
号 炉容,m3 厂名,炉
号 炉容,m3 厂名,炉
首钢迁安1 首钢迁安2
沙钢4号
号
号
2680
2650
鞍钢10
号
鞍钢11号
2650 唐钢3号
2580
2580
2560
研究背景武钢是新中国成立后兴建的...

华 中 科 技 大 学 硕 士 学 位 论 文1 绪论1.1 研究背景武钢是新中国成立后兴建的第一个特大型钢铁联合企业,于1955年开始建设,1958年9月13日建成投产,是中央和国务院国资委直管的国有重要骨干企业。
本部厂区座落在湖北省武汉市东郊、长江南岸,占地面积21.17平方公里。
武钢拥有从矿山采掘、炼焦、炼铁、炼钢、轧钢及配套公辅设施等一整套先进的钢铁生产工艺设备,是我国重要的优质板材生产基地,为我国国民经济和现代化建设作出了重要贡献。
武钢联合重组鄂钢、柳钢、昆钢股份后,已成为生产规模逾4000万吨的大型企业集团,粗钢产量居世界钢铁行业第四位,综合排名居世界500强企业第340位[1]。
经过50年的发展,武钢的产能增长了7倍。
武钢产能的急剧放大相应地增加了对铁矿石的需求量,导致武钢依靠自有矿山的铁矿石供给已经远远无法满足自身的生产需求。
武钢2011年的粗钢产量是3768万吨,随着武钢第三次创业和中西南发展战略的不断推进,在“十二五”规划的末年2015年产能预计会扩大到6000万吨左右,伴随而来的铁矿石年需求量也将攀升至9000万吨以上。
如果武钢不拓展现有矿源,按照矿石对外依存度90%试算,武钢每年需对外购买约7000万吨左右的铁矿石;加之国际市场上的铁矿石主要由必和必拓、力拓和淡水河谷等三大矿业巨头垄断,中国钢铁企业力量相对分散无法形成合力以达到联合采购议价的能力,武钢也不得不接受日益上涨的铁矿石进口价格;并且相比宝钢等其它中国钢铁企业,武钢地处内陆,进口铁矿石运输成本每吨要高出150元左右。
以上种种因素导致了武钢因铁矿石缺乏而面临的巨大的成本压力[2]。
在当前我国钢铁行业加快产业结构调整,加快转变经济发展方式的关键时期,武钢集团大力实施“走出去”战略,充分利用国内和国外两个市场和两种资源[3],加大对海外矿产资源进行开发与投资的力度,力图从根本上解决武钢的铁矿石供应华 中 科 技 大 学 硕 士 学 位 论 文难题。
武钢硅钢片标准

武钢硅钢片标准《一》武钢硅钢标准冷轧无取向电工钢带(片)1、范围本标准规定了无取向电工钢的牌号、公称厚度、叠装系数、磁特性等技术条件。
本标准适合于武汉钢铁股份有限公司生产的冷轧无取向电工钢带(片)。
2、引用标准下列文件中的条款通过在本标准中的引用而构成本标准的条款。
凡是注日期的引用文件,其随后所有的修改单(不包括勘误的内容)或修订版均不适用于本标准,然而,鼓励根据本标准达成协议的各方研究是否可使用这些文件的最新版本。
凡是不注日期的引用文件,其最新版本适用于本标准。
GB/T 228-1987 金属拉伸试验方式GB/T 235-1988 金属反复弯曲试验方法(厚度等于或小于3mm薄板及钢带)GB/T 247-1988 钢板和钢带验收、包装、标志及质量证明的一般规定GB/T 2522-1988 电工钢(带)层间电阻、涂层附着性、叠装系数测试方法GB/T 3076-1982 金属薄板(带)拉伸试验方法GB/T 3655-1992 电工钢片(带)磁、电和物理性能测量方法GB/T 6397-1986 金属拉伸试验试样GB/T 13789-1998 单片面性电工钢片(带)磁性能测量方法3、牌号表示方法为了区别于GB/T2521-1996的同类产品牌号,本标准牌号中的各符号含义表述如下:4、技术要求4.1磁特性4.1.1磁感在5000A/m交变磁场,频率为50HZ时,规定其最小磁感值B5000(峰值)应符合表1的规定。
表1 磁特性和工艺特性产品尺寸、外形及其允许偏差电工钢产品可供规格注:其他尺寸需经供需双方协商。
尺寸及板形公差注:对于宽度>830mm的钢带,允许以不切变状态交货,基宽度允许偏差为+05mm;横向厚度差是指板中心与距边部15mm的厚度差。
典型电磁性能注:检测依据GB/T3655-92或JIS C2550-1986检测试样纵横向各半P15/50指频率为50HZ,磁通密度为1.5T时的损耗B50指磁场强度为5000A/m时的磁通密度,依此类推以上值为典型值而非保证值典型机械性能注:拉伸检测依据GB/T228-1987反复弯曲检测依据JIS C2550叠片系数是指涂敷A涂层时的值以上值为典型值而非保证值表面绝缘涂层表面绝缘涂层宝钢提供A、H、D三种类型的绝缘涂层,用户可根据层间电阻、冲片性、耐氟利昂性、耐热性及其他特性选择一种符合要求的涂层种类。
武刚的战略与结构

武刚的战略与结构1.战略:从专业化到多元化1992年,武汉钢铁(集团)公司从总体战略角度看是一个专业化企业:非钢铁生产收人仅占企业全部收人的4.7%。
但从企业生产组织角度来看,武钢却是一个非专业化生产企业。
当时,武钢有职12.3万人,其中:直接从事钢铁生产(除矿山外)职工仅为2.79万人,占总数的22.7%;非钢铁生产职工从事的工作主要有:(1)社区服务范围内的工作,例如厂区、家属区的保安、交通管理、义务教育、医疗卫生等。
(2)企业内部的生产生活服务工作。
例如,武钢的机械制造系统有职工1万人,固定资产2亿元,其铸造和热处理能力位居中南地区第一名。
但由于仅为武钢自身提供产品,设备利用率很低,机修总厂平均轮班系数仅为1.2,远远低于标准轮班水平。
1992年,武钢开始了“精干主体、分离辅助”的企业改革实践。
其主要做法是:(1)对钢铁生产主体厂及能源、交通运输单位推行了“集中一贯”管理;(2)对生产生活服务单位进行剥离与重组;(3)对内部的事业性单位实行经费包干,在完成内部规定的工作外,可以对外经营。
这项改革实质上是武钢的公司战略开始从专业化转向多元化。
这种战略转变又可分为两个阶段:(1)1992一98年上半年,武钢的多元化战略是自发形成的,“分离辅助”的目的是“精干主体”,提高钢铁生产率,发展武钢的钢铁产业;(2)自1997年下半年开始,武钢的多元化战略进人“自觉”阶段,其目的是通过非钢产业的发展来增强集团公司的整体竞争能力。
武钢多元化经营的“自发”阶段是很有成效的,陆续将16个非钢铁生产的辅助单位从钢铁生产主体中分离出来,按市场经济的原则和行业经营的内在要求,进行生产要素重组,通过实行承包经营或资产经营责任制形式,推动了公司从单一产业向多元产业的转变。
1997年,武钢实现销售收人16O.78亿元,钢产量达到608.79万吨,在全世界大型钢铁企业中排名第29位,创历史最高水平。
武钢非铁产业从业人员6万多人,固定资产重估价值为5O亿元,全年实现销售收人40.30亿元(合外销13.66亿元),占公司销售收人总额的25.O7%。
武钢热轧总厂一分厂翻钢机的设计及应用
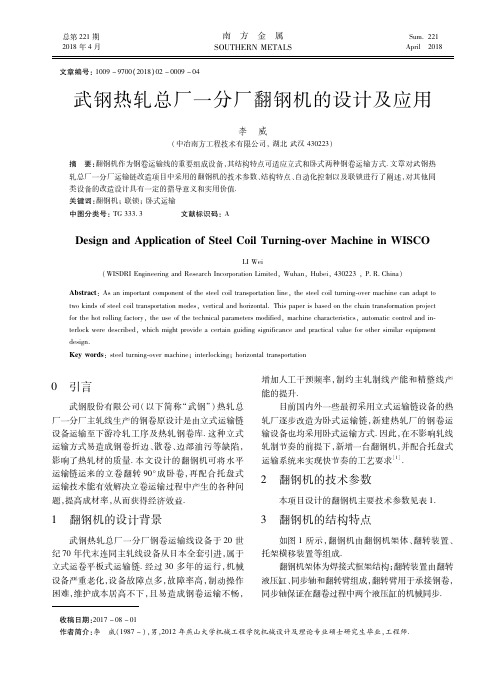
功能 液压缸翻卷 /返回 液压缸翻卷 /返回 翻钢机处于 10号链取卷位 翻钢机处于钢卷车取卷位
托座前进 /后退 翻钢机托座处于后退极限位 翻钢机托座处于钢卷接触位
数量 1 1 1 1 1 1 1
技术参数 DC24 DC24 DC24 DC24 DC24 DC24 DC24
总第 221期
李 威:武钢热轧总厂一分厂翻钢机的设计及应用
项目号 1001.01 1001.01 1001.01 1001.01 1001.02 1001.02 1001.02
代号 YVH2-1 YVH2-2 SBE-1 SBE-2
YVH2 SBE-1 SBE-2
表 2 翻钢机的电气元件清单
名称 电磁阀 电磁阀 接近开关 接近开关 电磁阀 接近开关 接近开关
增加人工干预频率,制约主轧制线产能和精整线产 能的提升.
目前国内外一些最初采用立式运输链设备的热 轧厂逐步改造为卧式运输链,新建热轧厂的钢卷运 输设备也均采用卧式运输方式.因此,在不影响轧线 轧制节奏的前提下,新增一台翻钢机,并配合托盘式 运输系统来实现快节奏的工艺要求[1].
2 翻钢机的技术参数
本项目设计的翻钢机主要技术参数见表 1.
翻钢机架体为焊接式框架结构;翻转装置由翻转 液压缸、同步轴和翻转臂组成,翻转臂用于承接钢卷, 同步轴保证在翻卷过程中两个液压缸的机械同步.
收稿日期:2017-08-01 作者简介:李 威(1987-),男,2012年燕山大学机械工程学院机械设计及理论专业硕士研究生毕业,工程师.
南 方 金 属
10
摘 要:翻钢机作为钢卷运输线的重要组成设备,其结构特点可适应立式和卧式两种钢卷运输方式.文章对武钢热 轧总厂一分厂运输链改造项目中采用的翻钢机的技术参数、结构特点、自动化控制以及联锁进行了阐述,对其他同 类设备的改造设计具有一定的指导意义和实用价值. 关键词:翻钢机;联锁;卧式运输 中图分类号:TG333.3 文献标识码:A
武钢集团公司岗位安全操作规程
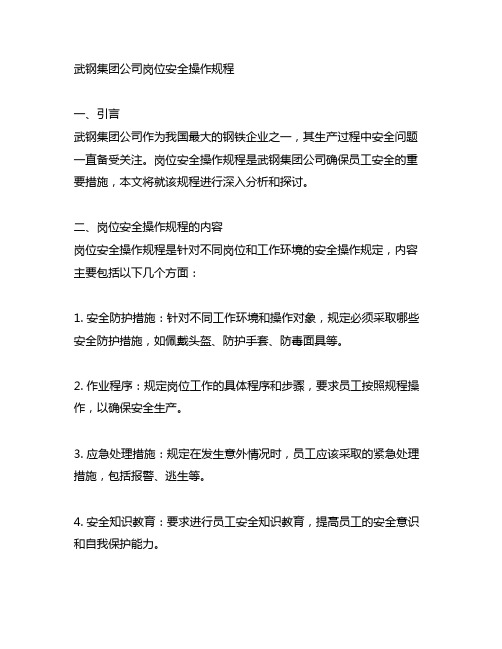
武钢集团公司岗位安全操作规程一、引言武钢集团公司作为我国最大的钢铁企业之一,其生产过程中安全问题一直备受关注。
岗位安全操作规程是武钢集团公司确保员工安全的重要措施,本文将就该规程进行深入分析和探讨。
二、岗位安全操作规程的内容岗位安全操作规程是针对不同岗位和工作环境的安全操作规定,内容主要包括以下几个方面:1. 安全防护措施:针对不同工作环境和操作对象,规定必须采取哪些安全防护措施,如佩戴头盔、防护手套、防毒面具等。
2. 作业程序:规定岗位工作的具体程序和步骤,要求员工按照规程操作,以确保安全生产。
3. 应急处理措施:规定在发生意外情况时,员工应该采取的紧急处理措施,包括报警、逃生等。
4. 安全知识教育:要求进行员工安全知识教育,提高员工的安全意识和自我保护能力。
5. 安全监督检查:对各岗位的安全操作进行监督和检查,发现问题及时纠正,确保规程执行到位。
三、岗位安全操作规程的重要性岗位安全操作规程的制定和执行对于公司的安全生产具有重要意义,体现在以下几个方面:1. 保障员工安全:通过规程的制定,能明确告知员工在工作中应该如何操作,避免因不懂规程而导致的意外伤害。
2. 提高生产效率:规程的执行能够规范生产流程,避免因安全事故导致的生产中断,保证生产不受影响。
3. 降低事故风险:规程的执行能够降低事故的发生概率,保障生产安全。
4. 增强企业形象:公司通过规范的安全操作能够提升企业形象,增加员工的归属感和安全感,从而提高员工的积极性和生产效率。
四、对武钢集团公司岗位安全操作规程的个人观点作为一名从事安全监督工作多年的专家,我对武钢集团公司制定的岗位安全操作规程给予了高度的肯定。
这一规程的制定和执行,为公司安全生产提供了有力的保障,必将对公司的安全生产和可持续发展起到重要的推动作用。
我也建议公司在执行规程的过程中,加强对员工安全意识的培养和规程的宣传,确保规程能够得到全面有效的执行,最大程度地保障员工的安全。
武汉钢铁(集团)公司简介
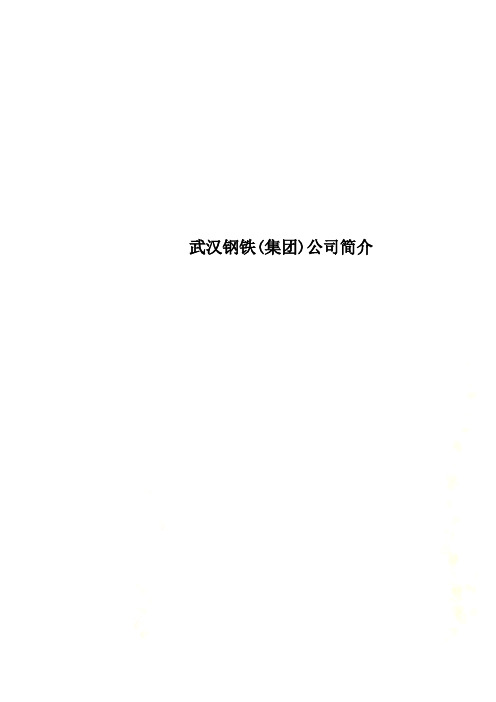
武汉钢铁(集团)公司简介武汉钢铁(集团)公司简介武钢是新中国成立后兴建的第一个特大型钢铁联合企业,于1955年开始建设,1958年9月13日建成投产,是中央和国务院国资委直管的国有重要骨干企业。
本部厂区座落在湖北省武汉市东郊、长江南岸,占地面积21.17平方公里。
武钢拥有从矿山采掘、炼焦(产能吨)、炼铁(产能吨)、炼钢(产能吨)、轧钢及配套公辅设施等一整套先进的钢铁生产工艺设备,是我国重要的优质板材生产基地,为我国国民经济和现代化建设作出了重要贡献。
武钢联合重组鄂钢、柳钢、昆钢后,已成为生产规模近4000万吨的大型企业集团,居世界钢铁行业第四位,2010年,武钢跻身世界500强行列。
武钢现有三大主业,即钢铁制造业、高新技术产业和国际贸易。
钢铁产品主要有热轧卷板、热轧型钢、热轧重轨、中厚板、冷轧卷板、镀锌板、镀锡板、冷轧取向和无取向硅钢片、彩涂钢板、高速线材等几百个品种。
其中,冷轧硅钢片和船板钢获“中国名牌产品”称号,汽车板、桥梁用钢、管线钢、压力容器钢、集装箱用钢、帘线钢、耐火耐候钢、电工系列用钢等优质名牌产品在国内外市场享有广泛的声誉,“武钢牌”被评为全国驰名商标。
近年来,武钢先后获得国家技术创新奖、全国质量管理奖、全国质量效益型先进企业、全国用户满意先进单位、全国企业管理杰出贡献奖、全国文明单位以及中央企业十大典型之一等荣誉称号。
50多年来,武钢历经了三次创业。
1955年10月武钢青山厂区正式破土动工,武钢人开始了第一次创业,迎来了新中国兴建的第一个钢都的诞生。
1974年武钢从原联邦德国、日本引进一米七轧机系统,开创了我国系统引进国外钢铁技术的先河,武钢人开始了第二次创业,走出了一条“质量效益型”发展道路。
2005年以来,武钢以科学发展观为指导,努力推进第三次创业,生产经营和改革发展取得了突出成就:中西南战略扎实推进,本部产能成倍增长,三大品种基地基本形成,自主创新能力大幅提升,“走出去”战略取得突破,内部改革持续深化,相关产业健康发展,节能减排成效显著,企业文化形成特色,职工生活持续改善。
- 1、下载文档前请自行甄别文档内容的完整性,平台不提供额外的编辑、内容补充、找答案等附加服务。
- 2、"仅部分预览"的文档,不可在线预览部分如存在完整性等问题,可反馈申请退款(可完整预览的文档不适用该条件!)。
- 3、如文档侵犯您的权益,请联系客服反馈,我们会尽快为您处理(人工客服工作时间:9:00-18:30)。
武钢1#高炉第三代生产操作概要邹明东张庆喜叶勇董尊敏(武钢炼铁厂)1.1号高炉第三代设计和生产概况1号高炉第三代按照:“优质、低耗、高效、长寿、环保”等炼铁方针,在大修改造设计中采用了一系列新技术、新设备、新工艺。
根据实际生产条件确定改造后的1号高炉第三代改造后的的设计指标为:高炉容积2200m3,利用系数2.0-2.5t/m3.d,风温1200-1250℃,富氧率1-3%,炉顶压力0.25Mpa,熟料率90%。
高炉一代炉役15年(其间无中修)。
高炉所采用的新技术有:无料钟炉顶技术,矮胖型,大炉缸、深死铁层的高炉内型,砖壁合一的薄炉衬结构,铜冷却壁,联合软水密闭循环冷却系统。
炉前渣铁处理系统采用环保型INBA、摆动流嘴和鱼雷罐,热风炉系统采用掺烧转炉煤气和霍戈文高温陶瓷燃烧器。
炉缸直径10.7m,有26个风口和2个铁口。
在以上新设备新工艺中,大炉缸、深死铁层的高炉内型,砖壁合一的薄炉衬结构,铜冷却壁,联合软水密闭循环冷却系统,这些改进直接影响高炉的长寿。
其它新设备新工艺能改善高炉的顺行,利于高炉形成更合理的煤气流分布,从而有利于高炉的长寿。
由于客观条件的限制,1号高炉在上也有不足之处,主要表现在:受场地限制,1号高炉上料系统采用料车上料,与皮带上料相比,其缺点在于:矿石在槽下过筛后经大矿槽皮带→供矿皮带→矿斗→料车→上罐,中间环节多,矿石多次转运易破碎,造成入炉粉末增多,另外由于料车容积相对较小,只有15 m3,高炉的批重最大只能达到40吨左右,严重限制了高炉的上料能力。
炉前系统也存在不很理想的地方:受场地限制,1号高炉INBA系统有2个成渣室,却只有1个转鼓,且最大制渣量为5t/min。
另外,东出铁场配备有7个渣罐位和6个铁罐位,西出铁场只配备有4个渣罐位。
这样,东出铁场的制铁能力、西出铁场的制渣能力受到限制,容易造成憋炉。
1号高炉克服以上不利因素的影响,实现了强化冶炼。
该炉于2001年5月19日点火开炉,开炉初期,由于国内尚无同类型高炉可供参考的成熟的操作经验,高炉操作处于探索期。
通过加强上下部调剂,完善高炉操作,克服原燃料条件的不利影响,高炉逐渐走出了探索期,冶炼水平不断强化,技术经济指标不断优化(1号高炉开炉以来部分技术经济指标见表2)。
其中,2007年平均利用系数达到了2.549t/(m3·d)以上、焦比325.9kg/t、煤比173kg/t的较高水平。
2.铜冷却壁薄炉衬结构高炉的操作规律47武钢1号高炉是我国首座采用铜冷却壁薄炉衬结构的大型高炉。
从炉腹第5段起至炉喉全部为薄炉衬,其中第7、8两段共使用了88块铜冷却壁。
由于铜的导热系数比铸铁高,铜冷却壁表面可以很快地形成渣皮,若操作不当,极易造成炉身粘结。
另外,1号高炉的炉身角和炉腹角偏大(分别为83°27'23"和81°38'28"),对边缘煤气流的上升运动和渣皮的稳定也有不利影响。
当时在国内,1号高炉炉型独特,需要探索其操作特点。
1号高炉投产的前几年,由于没有找到比较合理的操作制度,渣皮经常粘结和脱落,高炉波动频繁,经常出现管道、悬料等。
经过几年的探索和实践,找到了适合铜冷却壁的操作规律,实现了高炉的高产、低耗同时也保证了高炉的长寿。
(1) 改善入炉原燃料条件1号高炉原燃料条件不是特别好。
矿石的配料结构为:烧结+球团+块矿。
烧结矿先后使用过一烧料、四烧料、新二烧料、老二烧料,其主原料为澳大利亚精矿粉,由于其Al2O3的含量偏高,经常引起炉渣的Al2O3含量偏高,有时高达18-19%,对炉渣的流动性极为不利。
球团矿主要为自产球团。
块矿为海南矿+进口块矿。
1号高炉主要使用2号和4号焦炉焦炭,其Μ40为78-80%,Μ10为7-8%。
另外,由于焦炉焦炭缺口大,1号高炉必须使用一部分外购焦。
外购焦含水量高,粉末多,强度低,冶金性能极差,进入高炉后料柱透气性变差,不利于炉况的稳定和顺行。
精料是高炉炼铁的基础,精料的内容是:品位高;成分稳定,粒度均匀;冶金性能良好;炉料结构合理。
搞好精料工作是保证炉况长期稳定顺行实现强化冶炼同时实现长寿的重要手段。
1号高炉开炉10年以来一直坚持精料方针,不断优化炉料结构。
具体做法为:①改进烧结矿质量。
随着烧结厂的逐步改造,1号高炉使用烧结矿由开炉初期的一烧料改为质量较好的四烧料、新二烧料和老二烧料,铁分由55.5%左右提高至57%左右。
转鼓提高至77.5%左右。
<5mm粉末降低至6%以下。
②增加球团矿的使用量,提高熟料率。
1号高炉配料结构变化见表3。
44从表2和表3可以看出,通过改善配料结构,1号高炉入炉炉料熟料率由82-86%提高至89-92%,入炉矿石品位由58%左右提高至59%左右,渣量大幅降低,渣比下降至300kg/t左右,下降了10-20kg/t。
入炉矿石品位提高,渣量降低后有效地改善了料柱的透气性和透液性;熟料率的提高,有效地改善了炉料的冶金性能。
这些都有利于炉况的稳定和顺行。
利于高炉强化和长寿。
搞好过筛管理。
过筛效果差,会使粉末入炉,粉末入炉会使料柱透气性变差,导致风量萎缩,影响炉况的稳定和顺行。
为了减少入炉粉末,1号高炉主要采取了以下措施:①更换筛网。
1号高炉沟下过筛原来使用的是片状的梳齿筛,这种筛子的缺点是筛网易堵,过筛效果差,特别是在大量翻潮焦时,其过筛效果更差,粉末入炉较多。
针对这种状况,1号高炉于2003年逐步对沟下筛子作了改造,将西焦筛、东西焦丁筛及6个大矿槽(主供矿槽)筛中的4个,改为自清理棒条筛,这种筛子的优点在于自清理能力强,筛网不易堵,过筛效果好。
改造后,有效地改善了烧结矿及焦炭的过筛效果,大大减少了入炉粉末。
②控制合理的筛速。
将大矿槽筛速控制在2.5-3.0t/min,焦槽筛速控制在1.8-2.3t/min,既保证了料速的需要,避免了低料线,又保证了筛分效果,减少了入炉粉末。
③合理安排矿槽品种。
将球团矿装入原来备烧结矿的小矿槽,使得球团矿过筛后入炉,减少了球团矿入炉粉末。
④加强对原料系统的日常检查和维护。
要求岗位人员每班检查原料系统的设备,清理槽下筛网,保证过筛效果。
加强对原燃料的质量检查,当原燃料质量发生大的变化时,高炉要及时采取应对措施。
特别在翻潮焦时,要求及时清理筛网,同时补焦量要准。
(2) 装料制度的探索对于无料钟炉顶,其布料方式灵活丰富,布料矩阵的选择是无料钟技术的精髓,是加强高炉操作调剂的重要手段。
1号高炉开炉投产几年来,对铜冷却壁薄炉衬高炉的装料制度进行了大量的探索实践。
在开炉投产初期,1号高炉布料矩阵的最大布料角位为7号,布矿共4个角位,矿焦同角位布料。
生产实践中,煤气利用率不高,CO2含量为17%左右,高炉冶炼强化不够,能耗高。
另外,高炉抗外围影响的能力弱,特别是在原燃料条件恶化时,炉况易波动,经常出现渣皮粘结和脱落,不仅影响了高炉稳定顺行和指标,而且影响了高炉的长寿。
通过摸索,分析其原因在于:1号高炉炉身角和炉腹角偏大,煤气流上升阻力小,边缘煤气流易发展,管道行程多,渣皮不稳定。
炉身温度高,软融带位置高。
在外购焦用量大时,料柱透气性差,风量会大量萎缩,炉身温度又会急剧下降。
因此,高炉在上部调剂上决定抑制边缘煤气流。
一方面,将布料角位不断外移,先后移到8号和9号角位;另一方面,大幅增加边缘布矿量,具体调剂过程见表4。
47从上表可以看出,通过此番调整,1号高炉形成了比较合理煤气流分布,软融带下移,煤气利用率大大提高,CO2含量由17%提高至22.5%。
同时,由于消除了管道行程,炉况的稳定顺行得到了保证,高炉冶炼不断得到强化,利用系数提高到2.5t/(m3·d)以上,经济指标不断优化。
同时形成了稳定的渣皮,大大减少了渣批脱落和粘结,对高炉内衬起到了较好的保护作用,从而有利于高炉的长寿。
(3) 下部调剂下部调剂是上部调剂的基础,上下部调剂合理搭配,才能得到更好的调剂效果,取得更好的技术经济指标。
风口的选择:1号高炉共有26个风口,开炉时全部采用Φ130mm的长风口,其进风面积为0.3449 m2.由于进风面积偏大,风速偏低,鼓风动能不足,中心吹不透,炉缸不活。
配合装料制度抑制边缘煤气流的同时,下部调剂不断缩小进风面积,将Φ130mm的风口逐步部分改为Φ120mm的风口,以开放中心气流。
在具体的调整过程中,将进风面积由0.3449 m2逐步缩小到0.3117 m2。
进风面积缩小后,由于中心气流开放,风量反而增加了。
另外,逐步将长风口改为正常风口,只保留7个长风口,使边缘气流和中心气流分布趋向合理。
合理的热制度与造渣制度:合理稳定的热制度与造渣制度对炉况的稳定顺行十分重要。
在热制度的选择上,1号高炉要求控制[si]在0.35-0.45%范围内,铁水温度大于1490℃。
对于造渣制度的选择,要求炉渣碱度的控制范围为1.11-1.15。
由于武钢烧结矿主要使用澳大利亚精矿粉,Al2O3的含量高,有时炉渣Al2O3的含量高达18-19%,严重影响了炉渣的流动性及料柱的透气性。
针对这种情况,一方面,联系烧结厂,提高烧结矿的碱度由1.75到2.00;另一方面,高炉适当降低烧结矿的配比,增加海南矿配比。
通过以上措施,使炉渣Al2O3的含量控制在15-17%。
(4) 保持好的操作炉型保持好的操作炉型是炉况稳定顺行、优化技术经济指标的的基础,同时也直接关系到高炉的长寿。
影响炉型的因素很多,包括先天设计、材质使用、原燃料条件、煤气流控制、炉温控制、渣铁管理、水冷却系统管理、事故预防等等。
1号高炉采用薄炉衬技术,其设计炉型接近于操作炉型,易于强化冶炼,取得好的技术经济指标。
合理软融带形状和位置的控制。
1号高炉投产以来,进风面积不断缩小,目的是增大风速,增加鼓风动能,活跃中心气流,使软融带尖部上移。
在矩阵的选择上,将布料向边缘平移,同时增加边缘矿焦比,目的是将高温区下移,降低软融带根部的位置,减小炉身粘结的可能。
这样,通过“抑制边缘气流,开放中心气流”,形成倒V字型软融带,降低软融带跟部的位置,既稳定了渣皮,保持了合理的炉型,又改善了间接还原,优化了技术经济指标。
3.长寿生产维护(1) 冷却制度的维护与管理软水参数是否合理将直接关系到操作炉型是否稳定。
软水密闭循环系统设计水量为3740m3/h(武钢1号高炉冷却参数设计值见表5),但由于这一设计水量是建立在利用系数只有2.0-2.5t/m3.d的基础之上的。
而1号高炉冶炼强度逐步提高;今年2月月平均利用系数达2.55t/m3.d;因此,原来设计水量3740m3/h 已远不能满足强化冶炼的生产实际需要,增加水量势在必行。
到2007年1月,1号高炉分三次将水量调为4600m3/h,炉内各段温度趋向正常,炉型处于较为理想的状态,较好地满足了生产需要。