大型铸铁件的铸造工艺设计
超大断面宽厚板坯模铸技术

2021年第1期(总199期)CFHI**************一重技术大型铸锻件是能源装备的核心部件,由于金属凝固的尺寸效应,铸件的规格越大,则疏松缩孔、元素偏析和开裂等铸造缺陷越严重,进而导致锻件质量难以控制,严重影响零部件的服役性能,迫切需要探索新技术解决大型铸锻件的制备难题。
增材制造技术是一种基于“离散-堆积”原理,由数字模型文件驱动的,复杂形状零件的“快速成形”和“快速制造”新技术[1]。
经过近40余年的快速发展,增材制造技术的内涵不断深化、外延不断扩大,从狭义的以激光、电子束等为热源的分层成形技术,向广义的块体组焊、堆焊成形、化学/物理气相沉积等技术延伸,并广泛应用到航天、航空、核电、石化等高端装备领域[2]。
金属构筑成形技术正是基于上述增材制造思想提出的一种变革性的大型锻件制备方法。
传统上采用“模铸制坯+塑性成形”的技术路线来生产大规格、整体、高性能的金属构件,该技术需要大型铸铁模及重型锻造设备,且铸锭质量控制难度大、制造成本较高。
而金属构筑成形技术与建筑行业的1.一重集团大连工程技术有限公司高级工程师,辽宁大连1166001.一重集团大连工程技术有限公司工程师,辽宁大连116600超大断面宽厚板坯模铸技术邢思深1,屈磊1,张亮2摘要:超大断面宽厚板坯是制备大规格锻造坯料的重要基材,此类厚度超过500mm 、锭身无锥度的宽厚板坯只能采用模铸工艺制备。
但因尺寸效应导致凝固过程和铸锭质量极难控制,易出现致密度低、宏观偏析严重、开裂等缺陷。
在合理化锭型设计的基础上,分析在模铸工艺条件下各类锭型的凝固过程和内部质量。
研究结果表明无锥度的锭型设计导致熔池形状呈U 形,不利于铸锭形成自下而上的凝固过程,恶化芯部钢水的补缩条件。
对疏松的计算结果进一步印证这一结论,且厚度越小,疏松缺陷分布范围越广、致密度越差。
大截面宽厚板坯的厚度对应力影响较小。
宽厚板坯的厚度和锥度对C 元素的宏观偏析和V 形偏析没有显著影响,而加快冷却速度可以显著加大成分均匀层的深度,抑制A 形偏析的形成。
铸造成形技术铸造工艺设计

①选择铸件的浇注位置及分型面 ②型芯的数量、形状及其固定方法 ③确定工艺参数(加工余量、起模
斜度、圆角、 收缩率) ④浇冒口、冷铁形状、尺寸及其布
置
铸造工艺图——在零件图上用各种工艺 符号表示出铸造工艺方案的图形
它是制造模样和铸型,进行生产准备 和铸件检验的依据——基本工艺文件。
使型腔和主要芯位于下箱,便于下 芯、合型和检查型腔尺寸。
3.铸造工艺参数的确定
铸造工艺参数包括收缩余量、 加工余量、起模斜度、铸造圆角、 芯头、芯座等。
①收缩余量:
为了补偿收缩,模样比铸件图纸尺寸 增大的数值称收缩余量。收缩余量的大小 与铸件尺寸大小、结构的复杂程度和铸造 合金的线收缩率有关,常常以铸件线收缩 率表示:
工艺 打箱、清理等工艺操作 根据批量大小填写必要条
卡片 过程及要求
件
⑨ 综合整个设计内容
实例分析:
以C6140车 床进给箱体 为例分析毛 坯的铸造工 艺方案如下: 质量约35Kg。
车床进给箱体零件图
该零件没有特殊质量要求的表面, 仅要求尽量保证基准面D不得有明显 铸造缺陷,以便进行定位。
材料:灰铸铁HT150,勿需考虑补缩。
为了便于采用机器造型、尽量 避免活块,故凸台和凹槽均应 用型芯来形成。
为了克服基准面朝上的缺点, 必须加大D面的加工余量。
单件、小批量生产,采用手 工造型,使用活块造型较型芯 更为方便。同时,因铸件的尺 寸允许偏差较大,九个轴孔不 必铸出。
此外,应尽量降低上型高度, 以便利用现有砂箱。
显然,在单件生产条件下,宜 采用方案II或方案III。
在制订铸造工艺方案时,主要应着 眼于工艺上的简化。
1.分型面
三个方案供选择: 方案I:分型面在轴孔 的中心线上。 方案II:从基准面D分 型,铸件绝大部分位于 下型。 方案III:从B面分型, 铸件全部置于下型。
大型铸铁件的铸造工艺设计

大型铸铁件的铸造工艺设计杜瑞祥(天津三达铸造有限公司,天津300251)摘要:通过分析大型铸铁件的特点,认为其浇注工艺设计的主要原则应当是:分散底注、快速浇注和高温浇注;并对各种浇注工艺的优缺点进行了详细分析。
最后用叶片环状支架、压缩机缸体上侧、横梁等大型铸铁件的浇注工艺实例说明采用分散底注的浇注方式,同时适当提高浇注温度和速度,可以提高铸件成品率。
关键词:大型铸铁件;分散底注;快速浇注;高温浇注中图分类号:T G 244+-2文献标识码:A文章编号:1003—8345(2009)05—0043—04C as t i ngM et hodD es i g n of I I ea vy I r on C a s t i ngs D U R ui —xi ang(S anda Foundry Co .Lt d .,Ti anji n300251,C hi n a)A bs t r ac t :Bas edont he anal ys i s ofchar act e r i s t i c s ofhea vy i ID n cast i ngs ,i t7sco nsi d er e d t h att hei r cast i n g m et ho d des i gnpr i nci pl e sho ul dbea s :bo t t o m gat i ngw i t hdi sper sed i ngat es ,f a s t a ndhi gh t e m pe r at ur epo ur i n g .T head vant age sanddi sadV ant ages of V ar i ou s cast i n g m et ho ds w e r eana l yz ed i n det ai l ,and t he cast i n g met ho ds of s o m e hea vy i ron cas t i ngs su ch ast he r i ng —s haped br a cket of bl ades ,t op cyl i nder bl ock a nd c r oss be am of com pr es sor a nds oonw e r e t a kenasexa m pl e st o showt hatiti s pos s i bl et oi ncr eas et her a teof qual i 矗ed cas t i ngsby ad opt i n g bo t t o m gat i ng w i t h di sper sed i ngat e s a nd pr ope r l yi ncr e asi ng po ur i ng t e m pe r at ur e a nd po ur i ngra t e 。
典型铸铁件铸造工艺设计与实例

典型铸铁件铸造工艺设计与实例叙述铸造生产中典型铸铁件一一气缸类铸件、圆筒形铸件、环形铸件、球墨铸铁曲轴、盖类铸件、箱体及壳体类铸件、阀体及管件、轮形铸件、锅形铸件及平板类铸件的铸造实践。
内容涉及材质选用、铸造工艺过程的主要设计、常见主要铸造缺陷及对策等。
第1章气缸类铸件1.1低速柴油机气缸体1.1.1 一般结构及铸造工艺性分析1.1.2 主要技术要求1.1.3 铸造工艺过程的主要设计1.1.4 常见主要铸造缺陷及对策1.1.5 铸造缺陷的修复1.2中速柴油机气缸体1.2.1 一般结构及铸造工艺性分析1.2.2 主要技术要求1.2.3 铸造工艺过程的主要设计1.3空气压缩机气缸体1.3.1 主要技术要求1.3.2 铸造工艺过程的主要设计第2章圆筒形铸件2.1 气缸套2.1.1 一般结构及铸造工艺性分析2.1.2 工作条件2.1.3 主要技术要求2.1.4 铸造工艺过程的主要设计2.1.5 常见主要铸造缺陷及对策2.1.6 大型气缸套的低压铸造2.1.7 气缸套的离心铸造2.2冷却水套2.2.1 一般结构及铸造工艺性分析2.2.2 主要技术要求2.2.3 铸造工艺过程的主要设计2.2.4 常见主要铸造缺陷及对策2.3烘缸2.3.1 结构特点2.3.2 主要技术要求2.3.3 铸造工艺过程的主要设计2.4活塞2.4.1 结构特点2.4.2 主要技术要求2.4.3 铸造工艺过程的主要设计2.4.4 砂衬金属型铸造第3章环形铸件3.1活塞环3.1.1 概述3.1.2 材质3.1.3 铸造工艺过程的主要设计3.2 L形环3.2.1 L形环的单体铸造3.2.2 L形环的筒形铸造第4章球墨铸铁曲轴4.1 主要结构特点4.1.1曲臂与轴颈的连接结构4.1.2 组合式曲轴4.2主要技术要求4.2.1 材质4.2.2 铸造缺陷4.2.3 质量检验4.2.4 热处理4.3铸造工艺过程的主要设计4.3.1 浇注位置4.3.2 模样4.3.3 型砂及造型4.3.4 浇冒口系统4.3.5 冷却速度4.3.6 熔炼、球化处理及浇注4.4 热处理4.4.1 退火处理4.4.2 正火、回火处理4.4.3 调质(淬火与回火)处理4.4.4 等温淬火4.5常见主要铸造缺陷及对策4.5.1 球化不良及球化衰退4.5.2 缩孔及缩松4.5.3 夹渣4.5.4 石墨漂浮4.5.5 皮下气孔4.6大型球墨铸铁曲轴的低压铸造第5章盖类铸件5.1柴油机气缸盖5.1.1 一般结构及铸造工艺性分析5.1.2 主要技术要求5.1.3铸造工艺过程的主要设计5.2空气压缩机气缸盖5.2.1 一般结构及铸造工艺性分析5.2.2 主要技术要求5.2.3 铸造工艺过程的主要设计5.3其他形式气缸盖5.3.1 一般结构5.3.2 主要技术要求5.3.3铸造工艺过程的主要设计第6章箱体及壳体类铸件6.1大型链轮箱体6.2增压器进气涡壳体6.3排气阀壳体6.4球墨铸铁机端壳体6.5球墨铸铁水泵壳体6.6球墨铸铁分配器壳体第7章阀体及管件7.1灰铸铁大型阀体7.2灰铸铁大型阀盖7.3球墨铸铁阀体7.4管件7.5球墨铸铁螺纹管件7.6球墨铸铁管卡箍7.6.1 主要技术要求7.6.2 铸造工艺过程的主要设计7.6.3 常见主要铸造缺陷及对策第8章轮形铸件8.1 飞轮8.2调频轮8.3中小型轮形铸件8.4球墨铸铁轮盘第9章锅形铸件9.1大型碱锅9.2中小型锅形铸件第10章平板类铸件10.1大型龙门铳床落地工作台10.2大型立式车床工作台10.3大型床身中段10.4 大型底座中国机械工业出版社精装16开定价:299元。
大型高铬铸铁护套铸造工艺
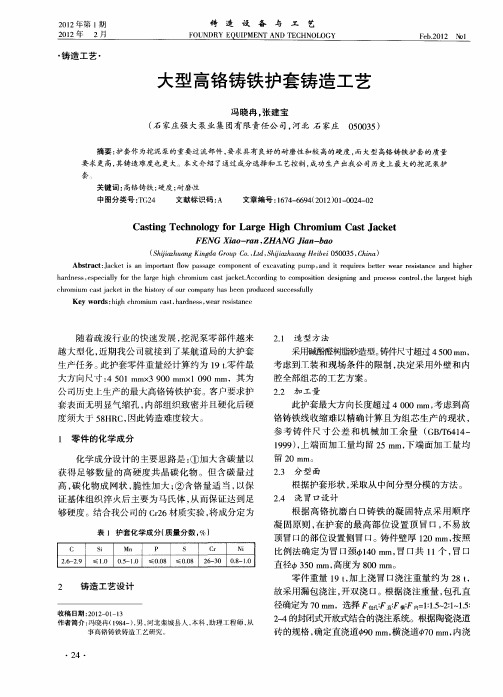
C
【 .- 9 2 6 2. ≤ 10 .
M n
0 5 . .一1 O
P
S lC N r l i
2 3 0.—10 6- 0 8 .
≤ 008 ≤ O 0 . .8
Ab ta t J c e sa mp r n o a s g o o e to x a ai g p mp, n tr q i s b t rwe r r s tn e a d h g e s r c : a k ti n i o t tf w p sa e c mp n n fe c v t u a l n a d i e u r et a e i a c n i h r e e s
摘要 : 护套作 为挖泥泵的重要过 流部件 , 要求具有 良好 的耐磨性 和较 高的硬度 , 而大型高铬铸铁 护套的质量 要 求更高, 其铸造难度也更大。本 文介绍 了通过 成分选择和工艺控制 , 成功生产 出我公 司历史上最大的挖泥泵护
套。
关键词 : 高铬 铸 铁 ; 度 ; 硬 耐磨 性 中 图分 类 号 :G 4 T 2 文 献标 识 码 : A 文章 编 号 :64 6 9 (0 2 o 一 0 4 0 17 — 6 4 2 1 ) l0 2 — 2
随 着疏 浚行 业 的快 速 发展 , 泥 泵零 部件 越 来 挖
21 造 型 方 法 .
越 大 型化 , 近期 我公 司就 接到 了某 航 道局 的 大护 套 生 产任 务 。 此护 套零件 重量 经计算 约 为 1 . 最 9t 零件
大 方 向尺寸 : 0  ̄ 0 i ̄ 9 i,其 为 45 1 mm 39 0ml 10 0ml l l
铸造工艺设计概论

(三)设计内容和程序 铸造工艺设计内容: 1)铸造工艺图 2)铸件(毛坯)图 3)铸型装配图(合箱图) 4)工艺卡及操作工艺规程
此外铸造工艺设计应注意保护环境、 节省能源、最大限度的提高生产效率。 使用保温冒口、湿型、制芯
铸造工艺方案的确定
砂型铸造工艺方案主要包括以下内容: 1)造型方法(机器、手工) 2)造芯方法 3)铸型种类的选择(砂型、金属型) 4)浇注位置 5)分形面选择
第四章
铸造工艺设计
吴士平
主讲
第四章
铸造工艺设计概念
第一节 铸造工艺设计的概念、设计的依据、内 容及程序
一、概念 铸造工艺设计:是根据铸造零件的结构特点、 技术要求、生产批量和生产条件等,确定铸造方 案和工艺参数,绘制铸造工艺图,编制工艺卡等 技术文件的过程。
• 铸造工艺设计的有关文件,是生产准备、 管理和铸件验收的依据,并用于直接指 导生产操作。因此铸造工艺设计的好坏, 对铸件的品质、生产率和成本起着重要 作用。
2、芯头斜度 对垂直芯头,上下芯头都应设有斜度。
3、芯头间隙
4、压环、防压环和积砂槽
(二)芯头承压面积计算 芯头的承压面积应足够大,以保证在金 属液最大浮力的作用下不超过铸型的许 用压应力。 由于砂芯的强度通常都大于铸型的 强度,故只核算铸型的许用压力即可。 芯头的承压面积S应满足下式
(2)零件技术要求 金属材质牌号、金相组织、力学性能 要求、铸件尺寸及重量公差及其它特殊 性能要求,如是否经水压、气压试验等。 铸造工艺设计时应注意尽量满足这些要 求。
(3)产品数量及生产期限 应尽量采用先进技术以保证铸件的质 量及数量,保证生产期限。缩短生产, 周期,获得最大的经济效益。
(二)生产条和生产效率、造型和制芯机种类、 机械化程度、烘干炉和热处理炉的能力 等。 (2)车间原材料的应用情况和供应情况 (3)工人技术水平和生产经验 (4)模具等工艺装备的加工能力和生产经验
大型灰铁铸件的铸造工艺

大型灰铁铸件的铸造工艺
大型灰铁铸件的铸造工艺可以分为以下几个步骤:
1. 模具准备:选择合适的灰铁模具,并进行准备工作,包括清洁、涂抹模脱剂等。
2. 铸型制备:将模具装配到铸造设备上,根据铸件的形状和尺寸,在模具中制备出与铸件相对应的空腔,可以采用砂型、金属型等不同的铸造方式。
3. 熔炼铁水:将铁矿石和其他合金原料放入熔炉中,通过高温熔炼,得到液态的铁水。
4. 铸注铁水:将熔融的铁水倒入预先准备好的铸型中,注意控制铁水的温度和流量,保证铁水充分填充整个铸型空腔。
5. 固化冷却:等到铁水完全填充整个铸型后,放置一段时间,让铁水逐渐固化和冷却,使铸件形成固态。
6. 脱模清理:待铁水完全固化后,拆卸模具,取出铸件。
对于有砂模的铸件,需要清理剩余砂粒和其他杂质。
7. 后处理:根据实际需要,对铸件进行修磨、去毛刺、清除氧化皮等后处理工
序,以提高铸件的精度和表面质量。
需要注意的是,大型灰铁铸件的铸造工艺还需要考虑铁水的浇注方式、冷却方式、铸型材料的选择等因素,以保证铸件的质量和性能。
高铬铸铁衬板铸造工艺的优化设计

根据试 制 时 出现 的铸 造缺 陷 ,改 进时 主要 针对 缩 孔 、 孔 的缺 陷采取 了措施 。 气 ( ) 后 衬板 的外 缘开 设 6个 内浇 道 , 1在 在直 浇道 对
面开设 o 0 的溢流 槽 ,在 中间位 置设 置 o 0 的 4 mm 5 mm
Po u t nT c nq e rd ci e h iu s生 产技 o
高铬铸铁衬板铸造工艺的优化设计
刘 金旺 ( 家庄 强 大泵业 集 团有 限责任 公 司 , 家庄 石 石 00 3 5 0 5)
摘要: 通过改进 内浇道 、 直浇道 、 出气孔 的设计 , 保温冒口的使用 , 以及严格控制生产过程 的各个环节, 品的 产
缩孔 、 气孔废 品大大减 少 , 毛坯 的废 品率 降至 2 %以下。
关键词: 高铬铸铁 ; 衬板; 铸造工艺
中 图分 类号 : G 5 2: T 2 l. 文献 标 识码 : ; B 文章编 号 : 0 6 9 5 ( 0 1 0 — 1 0 — 6 8 2 l )4 2 2 1 我公 司接 到一 个 生 产 高 铬 铸 铁 后 衬 板 备 0 0年 件 的项 目, 衬 板毛 坯 三维 图如 图 1 后 所示 。 该衬 板最 大 直径 o44 14 mm, 7 mm, 孑 直 径 o 6 m 单 面 加 高 6 内 L 94 m,
工余量 8 m, m 铸件重 1Ok 。 lO g 材质为高铬铸铁 , 产品技 术要求十分严格 , 加工面不允许有任何铸造缺陷。
出气孔,并在上砂型上扎出气孔 ,在上平面放置一个 o 6 m 的保 温 冒 口 , 20m 如图 3 。
图 1 后衬 板 毛 坯 三 维 图
1 原铸 造 工艺
- 1、下载文档前请自行甄别文档内容的完整性,平台不提供额外的编辑、内容补充、找答案等附加服务。
- 2、"仅部分预览"的文档,不可在线预览部分如存在完整性等问题,可反馈申请退款(可完整预览的文档不适用该条件!)。
- 3、如文档侵犯您的权益,请联系客服反馈,我们会尽快为您处理(人工客服工作时间:9:00-18:30)。
(快速浇注有利于弥补此弊病);铸铁件下部温度 高,不利于补缩(但对灰铸铁件影响不大)。 1.2 快速浇注
优点:铁液上升速度快,不容易氧化,对型腔 的烘烤时间短,减小涂层开裂、脱落的可能性,可 避免出现浇不足、冷隔缺陷;另外,型腔内气压增 大,迫使气体容易从铸型向外排出,铸件不容易 产生气孔等孔洞类缺陷;还有,由于铸铁件各部 的温度差小,可防止裂纹发生。
iron casting
铸铁件壁厚 /mm <10 10~30 30~50 50~80 >80
系数 S3
4.2 3.8
3.4
3.0
2.6
44 现代铸铁 2009 / 5
能避免裂纹、冷隔类缺陷和气孔、针孔类缺陷。但 浇注温度只能根据铸铁件壁厚及结构形状适当 提高,不是越高越好。
缺点:容易产生粘砂缺陷和冲砂缺陷(分散 内浇口有利于弥补此缺点);特别厚大铸铁件易 造成组织粗大,厚大球铁件有缩孔、缩松倾向;增 大石墨漂浮倾向。
铸件特征 复杂的薄壁铸件
中等复杂铸件 形状简单的厚壁铸件
铸件壁厚 /mm <10 10~15 15~25 10~20 20~30 30~50
50~100 >100
浇注温度 /℃ 1 400~1 420 1 390~1 420 1 380~1 420 1 380~1 420 1 360~1 400 1 350~1 390 1 340~1 380 1 330~1 380
单 的 铸 铁 件 ,宜
过低 使型腔受热烘烤时间长,易引起砂型 采取慢速浇注。 翘起脱落和产生裂纹、冷隔、夹渣等
t3=S3姨3 GL 式中:t3 为浇注时间,单位为 s;GL 为型内金 属液总质量(包括浇、冒口系统质量),单位为 kg; S3 为壁厚系数,与铸铁件的壁厚有关(见表 4)。 1.3 高温浇注 优点:流动性好,可避免由于底注而容易形 成的铸铁件残缺类缺陷,得到轮廓清晰的铸件;
℃,浇注时间 60 s。
(3)横梁
图 5 为横梁,材料牌号为 GGG60 (德国牌
号,相当于我国标准的 QT600),铸件质量 41 000
kg,最小壁厚 50 mm,采用常温固化的呋喃树脂
自硬砂手工造型,内浇道设在底部侧面,浇冒口
质量 9 000 kg,浇注温度 1 390 ℃,浇注时间 50 s。
对于中、大型铸铁件的生产,其实际浇注时 间的长短、浇注速度的快慢,对铸铁件的质量有 直接的影响。依据生产实践,建议灰铸铁件浇注 温度如表 5 所示。
表 5 根据生产实践建议的灰铸铁件浇注温度 Tab.5 Pouring temperature recommended based on
production practice
iron casting
灰铸铁件质量 /kg 5~6 10~50 50~100 100~250 250~500 500~1 000 1 000~5 000 浇注时间 /s 3~4 4~9 9~12 12~20 20~28 28~40 40~85
铸铁件壁厚 /mm <10
系数 S2
1.1
10~20 1.4
砂铁型铸造工艺大批量生产轮毂铸件的优势。介绍覆砂铁型工艺的流程及用于轮毂类铸件生产的机械化和简单机械化
铸造生产线,以两种不同形状、壁厚的轮毂铸件及类似铸件为例,介绍覆砂铁型铸造工艺的应用情况。
关键词:轮毂;覆砂铁型;铸造工艺
中图分类号:TG242
文献标识码:A
文章编号:1003-8345(2009)05-0046-04
式中:t 为浇注时间,单位为 s;GL 为型内金 属液总质量 (包括浇、冒口系统质量),单位为 kg;S 为系数,取决于铸铁件的主要壁厚。
缺点是:如果充型时间过长,金属液在型腔
对于质量小于 1 000 kg 的铸铁件,其浇注时
上升中长时间与空气接触,表面易生成氧化皮 间可按 Dietert 公式计算:
表 1 铸铁件浇注速度的一般原则 Tab.1 General principle to determine pouring rate of iron
castings
S2 为壁厚系数,与铸铁件的壁厚有关(见表 3)。 另外,依据生产实践,建议质量大于 1 000
kg 的灰铸铁件,浇注时间可按下式计算:
表 2 灰铸铁件推荐浇注时间[1] Tab.2 Recommended pouring time of gray iron castings[1]
表 3 系数 S2 和铸铁件壁厚的关系 Tab.3 Relationship between factor S2 and wall thickness of
现代铸铁 2009 / 5 45
球
Nodular Irons & Gray Irons
墨
铸
铁
与
灰 铸
轮毂类铸件覆砂铁型铸造工艺及设备
铁
何芝梅,潘东杰,黄列群,林方夫
(浙江省机电设计研究院有限公司,浙江 杭州 310002)
摘要:对轮毂铸件采用粘土砂湿型铸造、冷硬树脂砂铸造、离心铸造和覆砂铁型铸造的优缺点进行了对比,说明采用覆
浇注速度
对铸铁件质量的影响
原则要求
较高
可使金属液较快充满型腔,能防止浇 (1)薄壁、形状复 不足,减少金属液氧化和铸铁件各部
的温度差,从而避免产生裂纹
杂或具有大水平
过高 对型腔冲刷力增大,易产生冲砂
面 的 铸 铁 件 ,要 采取快速浇注;
较低
能增大铸铁件各部温度差,顶注时能 (2)厚实、形状简 使铸铁件的缩孔集中,利于补缩
用分散底注的浇注方式,同时适当提高浇注温度和速度,可以提高铸件成品率。
关键词:大型铸铁件;分散底注;快速浇注;高温浇注
中图分类号:TG244+.2
文献标识码:A
文章编号:1003-8345(2009)05-0043-04
Casting Method Design of Heavy Iron Castings
1.1 分散底注 图 2 为采用分散底注式浇注系统生产的机
床床身,材料牌号为 GC(密烘灰铸铁 C 级),抗拉 强度相当于我国的 HT300。
优点为:有利于金属液平稳地充满铸型,减 小型、芯的冲击力和紊流现象,防止造成冲砂,避
收稿日期:2009-02-02
修定日期:2009-05-11
作者简介:杜瑞祥(1963.9-),男,汉族,天津人,毕业于天津大学
t1=S1姨3 δGL
缺点:低强度类型的砂型易产生冲砂类缺
式中:t1 为浇注时间,单位为 s;GL 为型内金
陷,但对于树脂砂等强度较高的砂型,影响较小; 属液总质量 (包括浇、冒口系统质量),单位为
浇注系统的截面积有所增大,铸件工艺出品率有 kg;δ 为铸铁件的平均壁厚,单位为 mm;S1 为系
所降低。
大型铸铁件的铸造工艺设计
Nodular Irons & Gray Irons
球
墨
铸
铁
与
ቤተ መጻሕፍቲ ባይዱ
灰
铸
铁
杜瑞祥
(天津三达铸造有限公司,天津 300251)
摘要:通过分析大型铸铁件的特点,认为其浇注工艺设计的主要原则应当是:分散底注、快速浇注和高温浇注;并对各种
浇注工艺的优缺点进行了详细分析。最后用叶片环状支架、压缩机缸体上侧、横梁等大型铸铁件的浇注工艺实例说明采
Casting method and Equipment Used for Resin Sand-Coated Permanent Mould Cast Wheel Hub Castings
HE Zhi-mei, PAN Dong-jie, HUANG Lie-qun, LIN Fang-fu
姨 姨 v=
A+ δ 25.4B
姨2.25GL
式中:v 为浇注速度,单位为 kg/s;δ 为铸铁
件的主要壁厚,单位为 mm;GL 为型内金属液总
质量(包括浇、冒口系统质量),单位为 kg;A、B
为系数,分别取 0.9 和 0.833。
对于质量小于 10 000 kg 的中、大型铸铁件,
其浇注时间可按下式计算:
(4)柴油机曲轴箱
图 6 为柴油机曲轴箱,材料牌号为 GC(密烘
灰铸铁 C 级),铸件质量 29 000 kg,最小壁厚 25
2 大型铸铁件浇注工艺举例
(1)叶片环状支架 图 3 为叶片环状支架图,材料牌号为
GGG40(德国牌号,相当于我国标准的 QT400), 铸件质量 25 800 kg,最小壁厚 80 mm,采用常温 固化的呋喃树脂自硬砂手工造型,内浇道设在底 部侧面,浇冒口质量 4 200 kg,浇注温度 1 380 ℃,浇注时间 50 s。
20~40 1.7
40~80 1.9
文献[2]介绍:对于质量小于 450 kg 的形状 复杂的薄壁铸铁件,其浇注时间可按下面的经验 公式计算:
t=S 姨GL
表 4 系数 S3 和铸铁件壁厚的关系 Tab.4 Relationship between factor S3 and wall thickness of
大型铸铁件的特点是尺寸大,即体积大、质 量重、浇注的铁液多、壁厚相对较厚,形状有的简 单、有的复杂,缺陷种类也繁多,这与铸铁件生产 的每道工序都息息相关(见图 1)。
大型铸铁件的浇注系统设计需要掌握如下 原则:分散底注(分层注入效果最好),快速浇注 (多加出气冒口),高温浇注(加强砂芯排气)。
1 浇注工艺
铸造工艺及设备专业,高级工程师,现主要从事铸造技术及质量
管理的工作。
免气体裹入,减少金属液氧化;同时有利于型腔
现代铸铁 2009 / 5 43
球
Nodular Irons & Gray Irons
墨
铸