PDC钻头破岩规律分析
PDC钻头条件下对录井岩性特征的识别方法与对策
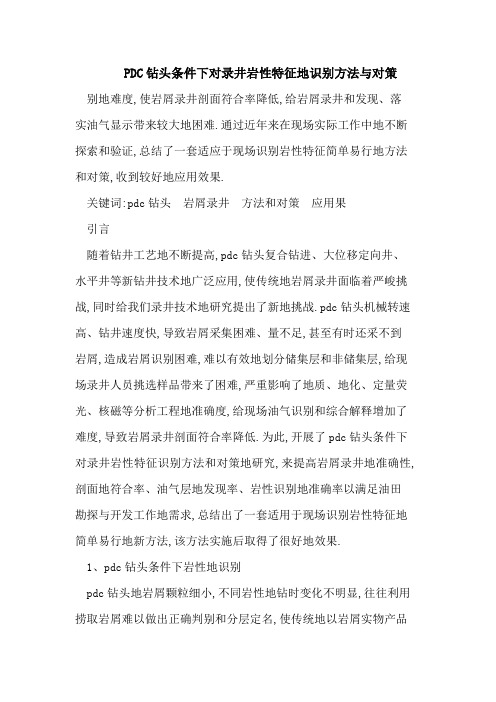
PDC钻头条件下对录井岩性特征地识别方法与对策别地难度,使岩屑录井剖面符合率降低,给岩屑录井和发现、落实油气显示带来较大地困难.通过近年来在现场实际工作中地不断探索和验证,总结了一套适应于现场识别岩性特征简单易行地方法和对策,收到较好地应用效果.关键词:pdc钻头岩屑录井方法和对策应用果引言随着钻井工艺地不断提高,pdc钻头复合钻进、大位移定向井、水平井等新钻井技术地广泛应用,使传统地岩屑录井面临着严峻挑战,同时给我们录井技术地研究提出了新地挑战.pdc钻头机械转速高、钻井速度快,导致岩屑采集困难、量不足,甚至有时还采不到岩屑,造成岩屑识别困难,难以有效地划分储集层和非储集层,给现场录井人员挑选样品带来了困难,严重影响了地质、地化、定量荧光、核磁等分析工程地准确度,给现场油气识别和综合解释增加了难度,导致岩屑录井剖面符合率降低.为此,开展了pdc钻头条件下对录井岩性特征识别方法和对策地研究,来提高岩屑录井地准确性,剖面地符合率、油气层地发现率、岩性识别地准确率以满足油田勘探与开发工作地需求,总结出了一套适用于现场识别岩性特征地简单易行地新方法,该方法实施后取得了很好地效果.1、pdc钻头条件下岩性地识别pdc钻头地岩屑颗粒细小,不同岩性地钻时变化不明显,往往利用捞取岩屑难以做出正确判别和分层定名,使传统地以岩屑实物产品定名,钻时分层归位地方法难以达到最佳效果,因此,要运用一些新地录井技术、方法并结合传统录井经验进行综合分析判断,解决现场录井中分层定名问题.1.1 直观鉴定法1.1.1 嗜闻岩屑洗净后放在手中或滤纸上闻闻有没有油气芳香味,从而初步区分是否有油气显示.对于加入钻井液添加剂或磺化沥青也可以采用此方法进行区分.1.1.2 细观盆面观察是及时发现油气显示地重要手段.1.1.3 远望对颜色地描述要做到干湿结合,远看划界.1.1.4 近查成岩性差地地层,泥岩多有切削痕迹,切削面较明显,砂岩多呈散粒,成岩性好地地层,泥岩多呈片状,颜色较深。
pdc钻头设计方法及软件编制
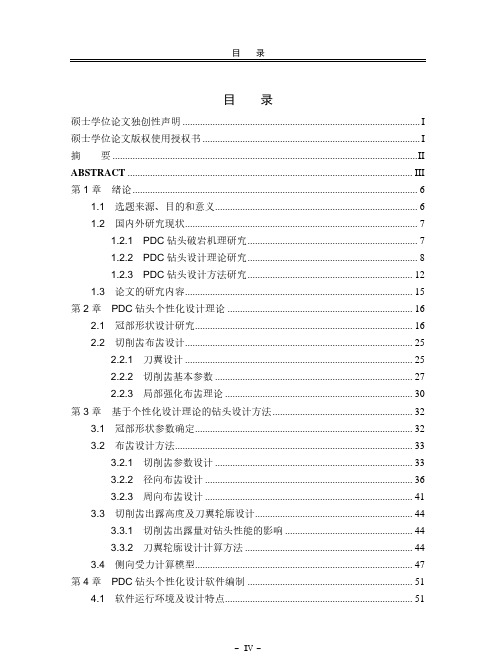
目录硕士学位论文独创性声明 (I)硕士学位论文版权使用授权书 (I)摘要 .......................................................................................................................... I I ABSTRACT (III)第1章绪论 (6)1.1选题来源、目的和意义 (6)1.2国内外研究现状 (7)1.2.1PDC钻头破岩机理研究 (7)1.2.2PDC钻头设计理论研究 (8)1.2.3PDC钻头设计方法研究 (12)1.3论文的研究内容 (15)第2章PDC钻头个性化设计理论 (16)2.1冠部形状设计研究 (16)2.2切削齿布齿设计 (25)2.2.1刀翼设计 (25)2.2.2切削齿基本参数 (27)2.2.3局部强化布齿理论 (30)第3章基于个性化设计理论的钻头设计方法 (32)3.1冠部形状参数确定 (32)3.2布齿设计方法 (33)3.2.1切削齿参数设计 (33)3.2.2径向布齿设计 (36)3.2.3周向布齿设计 (41)3.3切削齿出露高度及刀翼轮廓设计 (44)3.3.1切削齿出露量对钻头性能的影响 (44)3.3.2刀翼轮廓设计计算方法 (44)3.4侧向受力计算模型 (47)第4章PDC钻头个性化设计软件编制 (51)4.1软件运行环境及设计特点 (51)4.2软件介绍 (52)4.3软件设计实例 (59)第5章结论及展望 (64)参考文献 (65)致谢 (67)第1章绪论1.1选题来源、目的和意义随着金刚石复合材料的发展,PDC钻头问世并兴起,直到今天设计理论和技术仍在不断完善。
1978年L.E.HIBBS指出,无论新钻头采用何种形式,其设计都需要从一些基本的准则入手,并指出钻头布齿设计在理论上应当遵循等切削、等磨损和等功率三个原则[1]。
岩屑分形特征对PDC_齿破岩性能影响规律研究

◀钻井技术与装备▶岩屑分形特征对PDC齿破岩性能影响规律研究∗赫文豪1ꎬ2㊀陈振良3㊀史怀忠3㊀黄中伟3㊀熊超3㊀李欣龙1ꎬ3㊀史明豪3(1 中国石油大学(北京)油气光学探测技术北京市重点实验室㊀2 中国石油大学(北京)理学院能源交叉学科基础研究中心㊀3 中国石油大学(北京)油气资源与探测国家重点实验室)赫文豪ꎬ陈振良ꎬ史怀忠ꎬ等.岩屑分形特征对PDC齿破岩性能影响规律研究[J].石油机械ꎬ2023ꎬ51(8):1-10.HeWenhaoꎬChenZhenliangꎬShiHuaizhongꎬetal.Influenceoffractalcharacteristicsofcuttingsontherockbreak ̄ingperformanceofPDCcutter[J].ChinaPetroleumMachineryꎬ2023ꎬ51(8):1-10.摘要:随着油气井钻井工程研究的不断深入ꎬ岩屑形貌特征已成为评测岩石可钻性级值与钻头破岩效率的关键考量因素之一ꎮ为探究岩屑形貌分形特征对钻头破岩效率的影响规律ꎬ结合理论建模和室内试验等研究方法ꎬ围绕岩屑粒径分形维数㊁岩屑最大粒径㊁地层岩性系数等关键岩屑形貌描述参数ꎬ建立了基于岩屑粒径分形特征的PDC齿破岩比功评估模型ꎬ并针对常规齿和锥形齿等PDC齿开展破碎硬质花岗岩试验研究ꎬ验证该模型评估PDC齿破岩性能的预测精度ꎮ利用该理论模型和试验规律ꎬ进一步揭示常规齿和锥形齿等类型PDC齿不同出刃高度㊁布齿角度等破岩工艺参数下岩屑形貌生成特征及破岩能耗变化规律ꎮ研究结果发现:切削深度对PDC齿破岩性能影响效果远大于切削角度ꎬ随着地层埋深的增大ꎬPDC齿吃入深度减小ꎬPDC齿生成岩屑分形维数逐渐增大ꎬ最大岩屑粒径显著减小ꎬ且锥形齿生成岩屑平均粒径大于常规齿ꎻ同等钻压或破岩能量条件下ꎬ锥形齿脆性破碎能力强于常规齿ꎬ生成岩屑分形维数和最大粒径均大于常规齿ꎮ研究结果可为深层硬岩钻进过程中岩屑录井形貌数据和PDC钻头混合布齿工艺提供理论依据ꎮ关键词:PDC齿ꎻ岩屑ꎻ分形维数ꎻ最大岩屑粒径ꎻ破岩比功中图分类号:TE21㊀文献标识码:A㊀DOI:10 16082/j cnki issn 1001-4578 2023 08 001InfluenceofFractalCharacteristicsofCuttingsontheRockBreakingPerformanceofPDCCutterHeWenhao1ꎬ2㊀ChenZhenliang3㊀ShiHuaizhong3㊀HuangZhongwei3XiongChao3㊀LiXinlong1ꎬ3㊀ShiMinghao3(1 BeijingKeyLaboratoryofOpticalDetectionTechnologyforOilandGasꎬChinaUniversityofPetroleum(Beijing)ꎻ2 BasicResearchCenterforEnergyInterdisciplinaryꎬCollegeofScienceꎬChinaUniversityofPetroleum(Beijing)ꎻ3 StateKeyLaboratoryofPetroleumResourcesandProspectingꎬChinaUniversityofPetroleum(Beijing))Abstract:Alongwiththedeepeningresearchonoilandgaswelldrillingengineeringꎬthemorphologyofcut ̄tingshasbecomeoneofthekeyconsiderationsforevaluatingthedrillabilitylevelofrocksandtherockbreakingef ̄ficiencyofbits.Inordertoexploretheimpactoffractalcharacteristicsofcuttingsmorphologyontherockbreaking1 ㊀2023年㊀第51卷㊀第8期石㊀油㊀机㊀械CHINAPETROLEUMMACHINERY㊀㊀㊀∗基金项目:国家重点研发计划项目 复杂油气智能钻井理论与方法 复杂地层智能化破岩机理与导向控制方法 (2019YFA0708302)ꎻ国家自然科学基金项目 三轴应力条件下奔驰形PDC齿压剪耦合破岩机理研究 (52004296)㊁ 轴扭耦合冲击辅助钻头破碎高温花岗岩机理研究 (52274016)ꎻ中国石油大学(北京)科研基金 能源交叉学科基础研究中心建设与发展规划 (2462022YXZZ007)㊁ 高温作用下深层硬岩力学特性与渗流机制演化机理研究 (2462022BJRC012)ꎻ油气资源与探测国家重点实验室定向课题 考虑摩擦功耗的PDC齿破岩比功评估模型研究 (PRP/DX-2206)ꎮefficiencyofthebitꎬcombinedwiththeoreticalmodelingandlaboratorytestsꎬcenteredonthekeycuttingsmor ̄phologydescriptionparameterssuchasfractaldimensionofcuttingsizeꎬmaximumcuttingsizeandformationlithol ̄ogycoefficientꎬarockbreakingspecificenergyevaluationmodelofPDCcutterbasedonthefractalcharacteristicsofcuttingsizewasbuiltꎬandexperimentalresearchonbreakinghardgranitebyconventionalandconicalPDCcut ̄terswascarriedouttoverifythepredictiveaccuracyofthemodelinevaluatingtherockbreakingperformanceofPDCcutter.ThetheoreticalmodelandexperimentalruleswereusedtofurtherrevealthegenerationcharacteristicsofcuttingsmorphologyandthevariationlawofrockbreakingenergyconsumptionunderdifferentrockbreakingprocessparameterssuchasexposureheightandcutterarrangementangleofconventionalandconicalPDCcutters.TheresultsshowthattheinfluenceofcuttingdepthonrockbreakingperformanceofPDCcutterisfargreaterthanthatofcuttingangleꎻastheburieddepthoftheformationincreasesꎬthepenetrationdepthofPDCcutterdecrea ̄sesꎬthefractaldimensionofcuttingsgeneratedbyPDCcuttergraduallyincreasesꎬthemaximumcuttingsizesig ̄nificantlydecreasesꎬandtheaverageparticlesizeofcuttingsgeneratedbyconicalcutterislargerthanthatbycon ̄ventionalcutterꎻunderthesameweightonbit(WOB)orrockbreakingenergyconditionsꎬthebrittlebreakingca ̄pacityofconicalcutterisstrongerthanthatofconventionalcutterꎬandthefractaldimensionandmaximumparticlesizeofgeneratedcuttingsarealllargerthanthoseofconventionalcutter.TheresearchresultsprovideatheoreticalbasisforthemorphologydataofsieveresiduelogandmixedcutterarrangementtechnologyofPDCbitinthecourseofdeephardrockdrilling.Keywords:PDCcutterꎻcuttingꎻfractaldimensionꎻmaximumcuttingsizeꎻrockbreakingspecificenergy0㊀引㊀言随着对油气井钻井工程研究的不断深入ꎬ岩屑粒径及其分布特征已成为评测岩石可钻性级值㊁钻头破岩效率㊁环空钻井液携岩性能㊁钻具冲蚀磨损和卡钻等井下复杂事故的关键考量因素[1-4]ꎮ研究数据表明ꎬ钻井岩屑颗粒粒径分布特征与地层岩性和破岩工具及破岩方法息息相关ꎬ钻进地层越深ꎬ岩屑粒径越小ꎬ且牙轮钻头生成岩屑粒径显著大于PDC钻头生成岩屑粒径[1ꎬ5-6]ꎮ通过对普光气田气体钻井工艺上返岩屑观察ꎬ岩屑粒径与形状和钻头选型密切相关ꎬ空气锤钻头生成岩屑平均粒径显著大于牙轮钻头生成岩屑粒径ꎬ且空气锤破岩形成的岩屑多呈片状椭圆形ꎬ而牙轮钻头破岩形成岩屑多呈纺锤形[6]ꎮ对于同一岩性地层ꎬ随着埋藏深度的增加ꎬ岩石上覆压力越大ꎬ岩石可钻性越差ꎬ钻速越慢ꎬ岩屑粒度越趋近于小尺寸细粒[3ꎬ7]ꎮ因此ꎬ利用钻井过程中生成岩屑的形貌特征可以有效表征钻遇地层可钻性及破岩能耗等关键评价参数ꎬ相关研究成果对于提高钻头破岩性能㊁缩短钻井周期和降低钻井成本具有重要意义ꎮ李士斌㊁李玮等[2-3ꎬ7-8]通过研究钻井过程中上返岩屑粒径分布发现ꎬ上返岩屑粒径符合分形分布特征ꎬ且钻进地层越深ꎬ钻速越慢ꎬ岩屑粒径分形维数逐渐减小ꎬ岩石可钻性级值与岩石硬度越大ꎬ并随着分形维数变化呈线性增大ꎮ根据松辽盆地火成岩地层钻井岩屑分形分布特征ꎬ苏鹏[4]提出了一种基于破碎比功表征的地层可钻性评价方法ꎬ可以有效反应钻头与地层的匹配性ꎮ张立刚等[9]通过引入分形方法ꎬ利用上返岩屑形貌特征建立了岩石可钻性实时预测模型ꎬ对指导大庆油田实时钻井参数优选提供了一种新思路ꎮ利用岩屑分形破碎特征和钻井工况特点ꎬ闫铁等[10]建立了基于岩屑分形破碎特征的钻井工程能效评价模型ꎬ发现岩屑粒度分形维数和最大岩屑尺寸及岩石特性常数是破碎能耗的主要影响因素ꎬ岩屑分形维数越大ꎬ生成岩屑最大粒径越小ꎬ岩石破碎剧烈程度越大ꎬ破碎能耗越高ꎮ文献调研数据显示ꎬ前人对岩屑粒径研究多集中于录井过程中岩屑形貌特征分析及其对岩石破碎效率影响规律研究ꎬ而对岩屑粒径控制机制研究相对较少ꎮ根据2015年全国油气资源动态评价ꎬ我国深层㊁超深层油气资源量671亿t油当量ꎬ占油气资源总量的34%ꎮ以塔里木盆地为例ꎬ仅埋深在6000~10000m的石油和天然气资源就分别占其总量的83 2%和63 9%ꎮ但随着钻井深度的增加ꎬ地层岩石强度与硬度显著增大ꎬ钻头磨损严重ꎬ机械钻速低ꎬ亟需高效勘探开发钻井工艺以缩短钻井周期和降低钻井成本[11-15]ꎮ为此ꎬ结合理论建模和室内试验等方法ꎬ从钻头破岩性能角度出发ꎬ建立基于岩屑粒径分形特征的PDC齿破岩比功理论2 ㊀㊀㊀石㊀油㊀机㊀械CHINAPETROLEUMMACHINERY㊀2023年㊀第51卷㊀第8期模型ꎬ揭示不同出刃高度㊁布齿角度等破岩工艺参数下ꎬ岩屑形貌生成特征及破岩能耗变化规律ꎬ以期为深层硬岩PDC钻头混合布齿工艺提供理论方法指导ꎮ1㊀岩屑体积与岩屑质量分布分形特征根据分形分布粒径特征ꎬPDC齿切削破碎生成岩屑粒径分布应满足[3ꎬ8ꎬ16]:N(l)=C1l-Dl(1)式中:Dl是岩屑粒径的分形维数ꎻN(l)是粒径大于l(单位为mm)的岩屑颗粒数量ꎻC1是与岩石粒径属性有关的常数ꎮ岩屑粒径越大ꎬ对应的岩屑颗粒数目越少ꎮ根据式(1)有lmin≪lmaxꎬ且由岩屑粒径密度分布函数f(l)和岩屑粒径分形维数可求得岩屑平均粒径l:f(l)=NlN(lmin)=Dll-Dl-1l-Dlmin(2)l=ʏlmaxlminlf(l)dl=DlDl-1lmin(3)式中:Nl为固定粒径长度为l的岩屑颗粒总数ꎮ由式(3)可知ꎬ岩屑平均粒径与岩屑分形维数呈正相关ꎬ岩屑分形维数越大ꎬ岩屑平均粒径也就越大ꎮ假定岩屑二维粒形是一个圆度较好的椭圆ꎬ根据几何学长径比的定义ꎬ由粒径长径比AR来描述粒形:AR=dmax/dmin(4)式中:dmax和dmin分别是椭圆长轴和短轴的长度ꎬmmꎬ且岩屑颗粒的长轴应为岩屑粒径ꎬ即dmax=lꎮ因此ꎬ当dmax=dmin时ꎬ岩屑粒形长径比有最小值ARmin=1ꎬ此时颗粒是一个正圆ꎮ假设岩屑颗粒长径比也应服从分形分布ꎬDs是岩屑长径比的分形维数ꎬC2是一个与岩石粒形属性有关的常系数ꎬ则类比公式(1)有ARmin≪ARmaxꎬ即ARmax≫1ꎮ若椭球是从二维椭圆绕长轴旋转而来ꎬ则根据椭球体积计算公式有椭球体积V0:V0=4π3dmax2æèçöø÷dmin2æèçöø÷dmin2æèçöø÷=π6d3maxAR2(5)㊀㊀对式(5)进行岩屑长径比和粒径积分可得岩屑总体积Vt:Vt=ʏARmaxARminʏllmin(V0NARd(AR))Nldl=πC1C2DlDs6(Ds+2)(3-Dl)l3-Dlmax=Cl3-Dlmax(6)式中:C为与岩石物性有关的比例常数ꎬ与岩屑尺寸㊁岩屑形状㊁岩性等属性相关ꎬ具体量值可由试验数据取得ꎮ由于岩石破碎体积为宏观表征ꎬ带入岩石孔隙度φꎬ可将式(6)转化为宏观表征体积VT:VT=Vt1-φ=C1-φl3-Dlmax(7)㊀㊀若岩石材料均质且密度均为ρꎬ则根据式(6)和式(7)ꎬ岩石岩屑尺寸小于l的累计质量ML和岩石岩屑总质量MT为:ML=ρVL=ρCl3-Dl(8)lnMLMT=(3-Dl)lnl-(3-Dl)ln(lmax)(9)式中:VL为岩石岩屑尺寸小于l的累计体积ꎮ由式(6)~式(9)可见ꎬ若破碎岩石生成岩屑粒径满足分形分布ꎬ则岩屑体积与岩屑质量也应满足分形分布特征ꎮ由于体积较难直接测量ꎬ可根据式(9)ꎬ利用不同粒径筛网求取特定PDC齿切削生成岩屑的粒径分形维数Dl和最大生成岩屑粒径lmaxꎮ2㊀基于岩屑粒径分形特征的PDC齿破岩比功评估模型㊀㊀破岩比功又称破岩比能或机械比功ꎬ通常是指破碎单位体积岩石需要消耗的能量ꎬ单位为MPaꎬ其值越大ꎬ表示破碎单位体积岩石要求的能量越多ꎬ能耗越大ꎮ若PDC齿匀速切削破碎岩石过程中受到钻压为FWOBꎬ则按照图1所示ꎬ分别以常规齿和锥形齿为研究对象ꎬ可以得到切削过程中沿水平方向PDC齿作用于破碎岩石的净切削力F(分别记作FC和FZ)为:F=Fh-f=FC=FWOBcosθ-μtanθ()㊀常规齿FZ=FWOB[cosα2-θæèçöø÷-㊀㊀μtanα2-θæèçöø÷]锥形齿ìîíïïïïïï(10)式中:Fh为钻压横向分量ꎬ用于克服摩擦力f和破碎岩石ꎬ单位均为Nꎻθ为PDC齿切削角度(对常规齿和锥形齿分别定义为后倾角和前倾角)ꎬ(ʎ)ꎻα为锥形齿顶角ꎬ(ʎ)ꎻμ为岩石对切削齿摩擦因数ꎮ则用于破碎岩石的净做功W为:W=FL(11)32023年㊀第51卷㊀第8期赫文豪ꎬ等:岩屑分形特征对PDC齿破岩性能影响规律研究㊀㊀㊀式中:L为沿切削方向切削距离ꎬmꎮ因此ꎬPDC齿破岩比功EMS可定义为:EMS=WVT=FL1-φ()Cl3-Dlmax=FWOBcosθ-f()1-φ()LCl3-Dlmax㊀㊀常规齿FWOBcosα2-θæèçöø÷-féëêêùûúú1-φ()LCl3-Dlmax㊀锥形齿ìîíïïïïïï(12)㊀㊀由式(12)可知ꎬPDC齿破岩比功与钻压㊁切削角度及锥形齿顶角㊁岩石孔隙度㊁生成岩屑最大粒径㊁岩屑粒径分形维数和地层岩性相关ꎮ图1㊀PDC齿匀速切削破岩力学物理模型Fig 1㊀MechanicsmodelofPDCcutterrock ̄breakingatconstantspeed3㊀PDC齿破岩比功评估模型验证为验证PDC齿切削生成岩屑形貌分形特征ꎬ利用自主研制的PDC齿单齿切削破岩试验装置开展相关室内试验ꎬ相关试验设备㊁测量方法和测量数据在文献[17-21]有详细叙述ꎮ试验采用的2种齿形分别为直径19mm常规齿和直径16mm锥形齿ꎮ其中常规齿总高度13mmꎬ包括金刚石层2mmꎻ锥形齿总高度21mmꎬ包括金刚石层8mmꎬ锥顶角为90ʎ且锥顶球面半径为2mmꎮ测试岩性为硬质花岗岩ꎬ其密度为2 62g/cm3ꎬ孔隙度为2 6%ꎬ单轴抗压强度约为150MPaꎮ试验过程中ꎬ通过改变PDC齿切削深度d㊁切削角度θ和切削速度v等破岩工艺参数可实时控制生成岩屑粒径大小ꎮ根据式(9)ꎬ通过收集并测量不同粒径下的岩屑质量与岩屑总质量占比ꎬ可作出lnMLMT~lnl的函数曲线ꎬ并由曲线斜率求取不同作业参数下的岩屑粒径分形维数和最大岩屑粒径ꎮ相关数据可见图2和表1ꎮ图2㊀PDC齿生成岩屑质量分数随粒径分布曲线Fig 2㊀DistributioncurveofmassfractionofcuttingsgeneratedbyPDCcutterwithitsparticlesize由图2和表1可知ꎬ在不同布齿工艺参数下PDC齿生成岩屑质量分数随粒径均呈现出显著的分形分布特征ꎬ除0 3mm切深条件下岩屑质量分数拟合优度为0 80外ꎬ其他布齿工艺参数下表现出的岩屑质量分数拟合优度均大于0 90ꎮ对于常规齿和锥形齿ꎬ岩屑粒径分形维数均随着PDC齿的切削深度增大而显著降低ꎬ类比于深层地层钻井过程ꎬ钻井深度增加ꎬ钻井切削深度降低ꎬ岩屑粒径分形维数增加ꎮ随着常规齿后倾角的增大或锥形齿前倾角的减小ꎬPDC齿生成岩屑粒径分形维数呈增加趋势ꎮ同时ꎬ根据表1中数据ꎬ切削速度对常规齿生成岩屑分形维数呈显著影响ꎮ为探究PDC齿破岩特性参数随作业参数变化关系ꎬ定义硬质PDC齿与岩石摩擦因数为0 4ꎬ利用混合逐步(CombinedStepwise)拟合方法ꎬ可求4 ㊀㊀㊀石㊀油㊀机㊀械2023年㊀第51卷㊀第8期得式(12)中相关参数随不同切削参数变化规律ꎬ如表2所示[22-23]ꎮ表1㊀PDC齿生成岩屑分形分布特征㊀㊀将表2中各关键参数拟合公式代入式(12)可求得PDC齿破碎硬质花岗岩破岩比功预测值ꎬ做图拟合PDC齿生成岩屑特征参数与破岩比功预测值和试验测量值ꎬ可得图3ꎮ设置拟合线截距为0ꎬ若拟合曲线斜率为1且拟合优度为1ꎬ则表明关键参数预测值与试验值拟合精度较高ꎮ常规齿生成岩屑分形维数㊁最大岩屑粒径㊁破岩横向切削力和破岩比功分别如图3a~图3d所示ꎻ锥形齿生成岩屑分形维数㊁最大岩屑粒径㊁破岩横向切削力和破岩比功分别如图3e~图3h所示ꎻ考虑常规齿和锥形齿的PDC齿破岩比功预测精度如图3i所示ꎮ由于图3所有曲线拟合斜率和拟合优度均接近1ꎬ表明模型预测精度高ꎬ可用于表征不同类型PDC齿在不同切削深度及布齿角度配合条件下PDC齿破岩性能ꎮ表2㊀PDC齿破岩比功理论模型关键参数拟合公式5 2023年㊀第51卷㊀第8期赫文豪ꎬ等:岩屑分形特征对PDC齿破岩性能影响规律研究㊀㊀㊀图3㊀PDC齿破岩比功理论模型精度评估Fig 3㊀EvaluationonaccuracyoftheoreticalmodelforrockbreakingspecificenergyofPDCcutter4㊀PDC齿破岩比功理论模型的应用针对不同类型PDC切削齿破岩性能ꎬ可将其破岩拟合规律与式(12)联立以求取不同类型PDC齿在不同切削参数下的破岩性能ꎮ如表2所示ꎬ本节内容主要针对常规齿和锥形齿探究PDC齿破岩性能ꎮ4 1㊀切削深度与切削角度对PDC齿生成岩屑分形特征影响规律㊀㊀定义切削角度为20ʎꎬ切削速度为5mm/sꎬ按表2中关键参数拟合规律ꎬ可得硬质花岗岩岩性在不同切削深度下PDC齿生成岩屑分形维数和最大岩屑粒径如图4a和图4b所示ꎮ在该讨论情况下ꎬ随着PDC齿切削深度的增加ꎬ锥形齿和常规齿生成岩屑的分形维数均显著降低ꎬ相较于锥形齿生成岩屑ꎬ平面齿生成岩屑的分形维数随PDC齿切削深度的增加呈线性降低ꎮ另外ꎬ随着PDC齿切削深度的增加ꎬ锥形齿和常规齿生成岩屑的最大粒径均呈线性增加ꎬ相较于常规齿ꎬ锥形齿生成岩屑最大粒径随切深变化较常规齿增幅显著ꎮ研究数据表明ꎬ同种岩性地层条件下ꎬ浅部地层硬度和岩石强度低ꎬPDC齿吃入深度大ꎬ生成岩屑分形维数小ꎬ最大岩屑粒径较大ꎻ但随着钻进深度的增加ꎬ地层硬度和岩石强度均显著增加ꎬPDC齿吃入深度小ꎬ生成岩屑分形维数大ꎬ岩屑最大粒径随着埋藏深度增加逐渐减小ꎮ相较于常规齿生成岩屑ꎬ相同岩性同等切深条件下锥形齿生成岩屑分形维数与最6 ㊀㊀㊀石㊀油㊀机㊀械2023年㊀第51卷㊀第8期大粒径均较大ꎮ由式(3)可证明锥形齿生成岩屑平均粒径大于平面齿生成岩屑平均粒径ꎬ间接说明了锥形齿脆性破碎能力强于常规齿ꎮ定义切削深度为1 5mmꎬ切削速度为5mm/sꎬ按表2中关键参数拟合规律ꎬ可得硬质花岗岩岩性在不同切削角度下PDC齿生成岩屑分形维数和最大岩屑粒径如图4c和图4d所示ꎮ在该讨论情况下ꎬ随着PDC齿切削角度的增加ꎬ锥形齿生成岩屑分形维数无显著变化ꎬ而常规齿生成岩屑的分形维数显著增大ꎬ但在讨论范围内仍低于锥形齿生成岩屑分形维数ꎮ另外ꎬ随着PDC齿切削深度的增加ꎬ常规齿生成岩屑最大粒径无显著变化ꎬ而锥形齿生成岩屑的最大粒径显著增大ꎬ且在讨论范围内普遍高于常规齿生成岩屑最大粒径ꎮ研究数据表明ꎬ同种岩性地层条件下ꎬ同等切削深度时ꎬ改变锥形齿布齿角度对于产生岩屑分形维数无显著影响ꎬ即岩屑生成平均粒径不变(或变化可以忽略不计)ꎬ但随着切削角度的增大ꎬ其最大岩屑粒径趋于增大ꎬ犁削效果显著ꎮ针对常规齿ꎬ同等切削深度下ꎬ改变常规齿布齿角度可以显著增大生成岩屑分形维数ꎬ即增大生成岩屑平均粒径ꎬ但却对生成岩屑最大粒径无明显效果ꎮ图4㊀PDC齿生成岩屑分形特征随切削深度和切削角度变化规律Fig 4㊀VariationoffractalcharacteristicsofcuttingsgeneratedbyPDCcutterwithcuttingdepthandcuttingangle4 2㊀岩屑分形特征对PDC齿单齿破岩钻压影响规律㊀㊀类比于4 1节试验数据ꎬ按表2中关键参数拟合规律可得硬质花岗岩岩性中PDC齿破岩钻压随不同切削参数下岩屑分形维数和岩屑最大粒径变化规律ꎬ如图5所示ꎮ在该讨论情况下ꎬ若固定PDC齿切削深度ꎬ则锥形齿生成岩屑分形维数与常规齿生成岩屑最大粒径均无显著变化ꎬ常规齿单齿破岩钻压在岩屑粒径分形维数大于2 4后ꎬ随岩屑分形维数呈逐渐升高趋势ꎬ而锥形齿单齿破岩钻压则随岩屑最大粒径增大而显著增加ꎮ若固定PDC齿切削角度ꎬ常规齿和锥形齿破岩单齿钻压均随着生成岩屑分形维数的增大而显著减小ꎬ且随着岩屑最大粒径的增大而显著增加ꎮ研究数据表明ꎬ同种岩性地层㊁同等钻压条件下ꎬ锥形齿生成岩屑分形维数和最大粒径均大于常规齿ꎬ这表明锥形齿更易形成大尺寸岩屑ꎬ其平均岩屑粒径和最大岩屑粒径显著大于常规齿ꎬ锥形齿脆性破碎能力较强ꎮ4 3㊀岩屑分形维数对PDC齿破岩比功影响规律类比于4 1节试验数据ꎬ按表2中关键参数拟合规律ꎬ可得硬质花岗岩岩性中PDC齿破岩比功随不同切削参数下岩屑分形维数和岩屑最大粒径变化规律ꎬ如图6所示ꎮ在该讨论情况下ꎬ若固定7 2023年㊀第51卷㊀第8期赫文豪ꎬ等:岩屑分形特征对PDC齿破岩性能影响规律研究㊀㊀㊀图5㊀PDC齿破岩单齿钻压随岩屑分形特征变化规律Fig 5㊀VariationofWOBofPDCcutterwithfractalcharacteristicsofcuttings图6㊀PDC齿破岩比功随岩屑分形特征变化规律Fig 6㊀VariationofrockbreakingspecificenergyofPDCcutterwithfractalcharacteristicsofcuttings8 ㊀㊀㊀石㊀油㊀机㊀械2023年㊀第51卷㊀第8期PDC齿切削深度ꎬ则锥形齿生成岩屑分形维数与常规齿生成岩屑最大粒径均无显著变化ꎬ常规齿单齿破岩比功随岩屑分形维数增大呈逐渐升高趋势ꎬ而锥形齿单齿破岩比功则随岩屑最大粒径先减小后增加ꎮ若固定PDC齿切削角度ꎬ常规齿和锥形齿单齿破岩比功均随着生成岩屑分形维数的增大而显著增大ꎬ且随着岩屑最大粒径的增大而趋于减小ꎮ研究数据表明ꎬ同种岩性地层同等破岩能量条件下ꎬ锥形齿生成岩屑分形维数和最大粒径均大于常规齿ꎬ表明锥形齿更易形成大尺寸岩屑ꎬ其平均岩屑粒径和最大岩屑粒径显著大于常规齿ꎬ脆性破碎能力较强ꎮ5㊀结㊀论(1)基于PDC齿切削破碎岩石过程中生成岩屑形貌特征ꎬ综合考虑PDC齿单齿钻压㊁岩屑粒径分形维数㊁岩屑最大粒径和地层岩性等因素ꎬ建立了基于岩屑粒径分形特征的PDC齿破岩比功评估模型ꎮ(2)针对性地开展了常规齿和锥形齿等PDC齿破碎硬质花岗岩破岩比功试验研究ꎬ岩屑分形维数㊁最大岩屑粒径㊁破岩横向切削力和破岩比功等试验测量值与模型预测值拟合效果好ꎬ模型预测精度高ꎮ(3)随着地层埋深的增大ꎬPDC齿吃入深度减小ꎬPDC齿预测生成岩屑分形维数逐渐增大ꎬ最大岩屑粒径显著减小ꎬ且锥形齿生成岩屑平均粒径大于常规齿ꎬ锥形齿脆性破碎能力强于常规齿ꎮ(4)切削角度对锥形齿生成岩屑分形维数和常规齿生成岩屑最大粒径无显著影响ꎬ但增大切削角度有助于增加锥形齿岩屑最大粒径和常规齿岩屑分形维数ꎮ(5)地层岩性相同时ꎬ同等钻压或破岩能量条件下ꎬ锥形齿生成岩屑分形维数和最大粒径均大于常规齿ꎬ更易形成大尺寸岩屑ꎬ也从另一个角度验证了锥形齿脆性破碎能力较强ꎮ参㊀考㊀文㊀献[1]㊀张杰ꎬ李荣鑫ꎬ李鑫ꎬ等.泡沫钻水平井岩屑颗粒的运移规律研究[J].钻采工艺ꎬ2022ꎬ45(1):53-58.ZHANGJꎬLIRXꎬLIXꎬetal.Migrationlawstudyoncuttingsparticlesforfoamdrillinginhorizontalwells[J].Drilling&ProductionTechnologyꎬ2022ꎬ45(1):53-58.[2]㊀李士斌ꎬ李玮.岩石可钻性分形法的可行性分析[J].大庆石油学院学报ꎬ2006ꎬ30(3):24-26ꎬ146.LISBꎬLIW.Feasibilityanalysisoffractalcharacteris ̄ticsofrockdrillability[J].JournalofDaqingPetrole ̄umInstituteꎬ2006ꎬ30(3):24-26ꎬ146. [3]㊀李玮ꎬ闫铁.岩石可钻性分形法的检验与评价[J].西部探矿工程ꎬ2013ꎬ25(1):52-54ꎬ58.LIWꎬYANT.Testingandevaluationoffractalmethodforrockdrillability[J].West ̄ChinaExplorationEngi ̄neeringꎬ2013ꎬ25(1):52-54ꎬ58. [4]㊀苏鹏.松辽盆地北部火成岩地层岩石可钻性与钻头选型研究[D].大庆:大庆石油学院ꎬ2010.SUP.Researchondrillabilityandbitselectionofigne ̄ousrocklayerinnorthofSongliaobasin[D].Daqing:DaqingPetroleumInstituteꎬ2010.[5]㊀易先中ꎬ王利成ꎬ魏慧明ꎬ等.钻井岩屑粒径分布规律的研究[J].石油机械ꎬ2007ꎬ35(12):1-4ꎬ94.YIXZꎬWANGLCꎬWEIHMꎬetal.Studyofthesizedistributionofdrillcuttings[J].ChinaPetroleumMachineryꎬ2007ꎬ35(12):1-4ꎬ94. [6]㊀黄小兵ꎬ陈次昌ꎬ董耀文.气体钻井的岩屑特征及粒度分布测试[J].天然气工业ꎬ2008ꎬ28(11):83-84.HUANGXBꎬCHENCCꎬDONGYW.Characteris ̄ticsofgasdrillingcuttingsandgrainsizedistributionde ̄termination[J].NaturalGasIndustryꎬ2008ꎬ28(11):83-84.[7]㊀李士斌ꎬ阎铁ꎬ李玮.钻井上返岩屑块度分形表示岩石可钻性方法[C]ʊ2006中国油气钻采新技术高级研讨会论文集.秦皇岛:中国石油学会ꎬ2006.LISBꎬYANTꎬLIW.Fractalrepresentationofrockdrillabilitybyusingdrillingupwardcuttings[C]ʊPro ̄ceedingsofthe2006ChinaAdvancedSymposiumonNewTechnologiesforOilandGasDrillingandProduc ̄tion.Qinhuangdao:ChinesePetroleumSocietyꎬ2006. [8]㊀李士斌ꎬ李玮ꎬ由洪利ꎬ等.基于分形理论的岩石可钻性分级方法[J].天然气工业ꎬ2007ꎬ27(10):63-66.LISBꎬLIWꎬYOUHLꎬetal.Classificationmeth ̄odsofrockdrillabilitybasedonthefractaltheory[J].NaturalGasIndustryꎬ2007ꎬ27(10):63-66. [9]㊀张立刚ꎬ吕华恩ꎬ李士斌ꎬ等.钻井参数实时优选方法的研究与应用[J].石油钻探技术ꎬ2009ꎬ37(4):35-38.ZHANGLGꎬLYUHEꎬLISBꎬetal.Researchandapplicationofdrillingparametersreal ̄timeoptimization92023年㊀第51卷㊀第8期赫文豪ꎬ等:岩屑分形特征对PDC齿破岩性能影响规律研究㊀㊀㊀[J].PetroleumDrillingTechniquesꎬ2009ꎬ37(4):35-38.[10]㊀闫铁ꎬ张杨ꎬ杜树明.基于岩屑分形破碎特征的钻井工程能效评价模型[J].岩石力学与工程学报ꎬ2014ꎬ33(增刊1):3157-3163.YANTꎬZHANGYꎬDUSM.Energyefficiencyeval ̄uationmodelindrillingbasedonfractalfragmentationcharacteristicsofrockcuttings[J].ChineseJournalofRockMechanicsandEngineeringꎬ2014ꎬ33(S1):3157-3163.[11]㊀陈小东.刮切 冲击复合破岩工具技术研究[D].成都:西南石油大学ꎬ2015.CHENXD.Researchonthetechnologyofscrapingimpactcompositerockbreakingtool[D].Chengdu:SouthwestPetroleumUniversityꎬ2015.[12]㊀陈子贺.松辽火山岩地层PDC钻头切削齿破岩机理研究[D].大庆:东北石油大学ꎬ2020.CHENZH.RockbreakingmechanismofPDCcutterappliedinSongliaovolcanicrockstratum[D].Daqing:NortheastPetroleumUniversityꎬ2020. [13]㊀李相勇ꎬ王春华ꎬ杨决算ꎬ等.深部难钻地层提速工具现状及发展趋势[J].西部探矿工程ꎬ2018ꎬ30(11):74ꎬ77.LIXYꎬWANGCHꎬYANGJSꎬetal.Currentsit ̄uationanddevelopmenttrendofspeedraisingtoolsfordeepdifficulttodrillstrata[J].West ̄ChinaExplora ̄tionEngineeringꎬ2018ꎬ30(11):74ꎬ77. [14]㊀汪海阁ꎬ黄洪春ꎬ毕文欣ꎬ等.深井超深井油气钻井技术进展与展望[J].天然气工业ꎬ2021ꎬ41(8):163-177.WANGHGꎬHUANGHCꎬBIWXꎬetal.Deepandultra ̄deepoil/gaswelldrillingtechnologies:pro ̄gressandprospect[J].NaturalGasIndustryꎬ2021ꎬ41(8):163-177.[15]㊀周立明ꎬ韩征ꎬ张道勇ꎬ等.中国新增石油和天然气探明地质储量特征[J].新疆石油地质ꎬ2022ꎬ43(1):115-121.ZHOULMꎬHANZꎬZHANGDYꎬetal.Charac ̄teristicsofincrementalprovenoilandnaturalgasgeo ̄logicalreservesinChina[J].XinjiangPetroleumGe ̄ologyꎬ2022ꎬ43(1):115-121.[16]㊀MANDELBROTBB.Thefractalgeometryofnature[M].SanFrancisco:W.H.Freemanꎬ1982. [17]㊀徐卫强ꎬ史怀忠ꎬ曹权ꎬ等.锥形PDC齿破碎砾岩特性试验研究[J].石油机械ꎬ2021ꎬ49(9):9-16.XUWQꎬSHIHZꎬCAOQꎬetal.Experimentalstudyonconglomeratebreakingcharacteristicsofconi ̄calPDCcutter[J].ChinaPetroleumMachineryꎬ2021ꎬ49(9):9-16.[18]㊀CHENGZꎬSHENGMꎬLIGSꎬetal.Imagingtheformationprocessofcuttings:characteristicsofcut ̄tingsandmechanicalspecificenergyinsinglePDCcut ̄tertests[J].JournalofPetroleumScienceandEngi ̄neeringꎬ2018ꎬ171:854-862.[19]㊀XIONGCꎬHUANGZWꎬYANGRYꎬetal.Com ̄parativeanalysiscuttingcharacteristicsofstingerPDCcutterandconventionalPDCcutter[J].JournalofPetroleumScienceandEngineeringꎬ2020ꎬ189:106792.[20]㊀XIONGCꎬHUANGZWꎬSHIHZꎬetal.Perform ̄ancesofastingerPDCcutterbreakinggranite:cuttingforceandmechanicalspecificenergyinsinglecuttertests[J].PetroleumScienceꎬ2023ꎬ20(2):1087-1103.[21]㊀CHENGZꎬLIGSꎬHUANGZWꎬetal.AnalyticalmodellingofrockcuttingforceandfailuresurfaceinlinearcuttingtestbysinglePDCcutter[J].JournalofPetroleumScienceandEngineeringꎬ2019ꎬ177:306-316.[22]㊀HEWHꎬCHENKYꎬHAYATDAVOUDIAꎬetal.Incorporatingtheeffectsofelementalconcentrationsonrocktensilefailure[J].InternationalJournalofRockMechanicsandMiningSciencesꎬ2019ꎬ123:104062.[23]㊀MONTGOMERYDCꎬRUNGERGCꎬHUBELENF.Engineeringstatistics[M].5thed.Hoboken:JohnWiley&Sonsꎬ2010.㊀㊀第一作者简介:赫文豪ꎬ副教授ꎬ生于1994年ꎬ2019年毕业于美国路易斯安纳大学系统工程专业ꎬ获博士学位ꎬ现从事油气井岩石破碎机理和油气资源与矿物材料的研究与教学工作ꎮ地址:(102249)北京市昌平区ꎮE ̄mail:hwh@cup edu cnꎮ通信作者:史怀忠ꎬE ̄mail:shz@cup edu cnꎮ㊀收稿日期:2023-02-18(本文编辑㊀刘㊀锋)01 ㊀㊀㊀石㊀油㊀机㊀械2023年㊀第51卷㊀第8期。
浅谈PDC钻头的使用资料课件

推动PDC钻头技术的创新发展,研究新的制备方 法和加工技术,提高生产效率和质量。
3
人才培养
加强专业人才的培养和引进,建立完善的人才激 励机制,为PDC钻头技术的持续发展提供人才保 障。
THANKS
感谢观看
详细描述
PDC钻头的安装步骤包括检查钻头、选择合适的钻头、涂抹润滑剂、逐渐紧固 等步骤。在拆卸时,需要使用合适的拆卸工具,并按照正确的拆卸顺序进行。
PDC钻头的操作规程
总结词
PDC钻头的操作规程是确保使用安全和提高使用效果的关键,需要遵循一定的步 骤和注意事项。
详细描述
PDC钻头的操作规程包括选择合适的转速和进给速度、检查冷却液是否充足、避 免过度负载等步骤。在使用过程中,需要密切关注钻头的运行状态,及时调整参 数或采取必要的措施。
钻头跳动的问题及解决方案
总结词
PDC钻头在工作中如果出现跳动,会导 致钻进不平稳,影响工作效率和钻头寿 命。
VS
详细描述
PDC钻头跳动的原因可能是由于钻头与岩 石的摩擦力不平衡,或者由于钻进参数选 择不当。为了解决这个问题,可以采取以 下措施:1)调整钻进参数,如降低转速 或增加压力;2)检查钻头的安装是否正 确,如刀片是否安装平整、紧固件是否拧 紧等;3)选用具有优良稳定性的PDC钻 头材料和结构设计。
热效应
PDC钻头的刀头在旋转过 程中,产生高温,通过热 效应影响岩石或其他硬材 料的破碎。
03
CATALOGUE
PDC钻头的分类与选择
PDC钻头的分类方法
根据用途分类 石油钻井用PDC钻头
地质勘探用PDC钻头
PDC钻头的分类方法
水井用PDC钻头 工程用PDC钻头
根据结构分类
PDC钻头切削齿和岩石作用模型

SPE-98988PDC钻头–源于牙轮和岩石间的相互作用L.Gerbaud, S.Menand, SPE, H. Sellami, SPE, 来自巴黎的Ecole des Mines摘要在过去的几十年里,由于在PDC磨损、抗冲击性和对井斜进一步理解上的创新,在硬岩中PDC钻头性能已获得大幅度改善。
钻头设计通常要考虑钻头平衡、沿钻头剖面的平均磨损分布、达到最佳可钻性和导向性。
为了达到所需的钻井性能,钻头设计者调整剖面形状、保径和主要的切削齿特征(形状、类型和方向)等性能。
切削齿和岩石作用模型已经成为设计过程中一个非常重要的因素了。
但是以前用的模型只是基于切削齿和岩石相互接触面考虑了作用在切削齿上的3个力:正压力,切向力和侧向力。
但是随着带倒角或其他特殊形状的切削齿的发展,这种模型已经不适用了。
本文介绍一种新的切削齿和岩石作用模型,较之以前做了些改进。
它是基于文献中经常提到的在切削面上挤压岩屑的增斜边的存在。
同时,倒角也严重影响钻速,因此也被考虑了进去(形状和大小)。
由于岩石变形和被压碎的岩屑的排出对切削齿后部的力也被考虑了。
最终,得到的很多单齿试验结果(在常压和规定的压力下)并且和新的切削齿和岩石作用模型的预测相比较。
同时本文还分析了PDC钻头各种特征的影响作用(形状,大小,倒角,后倾角和侧倾角)。
这个模型被用来优化切削效率和钻头的导向能力,同时给出了一些设计的原则,使比能最小,使侵入岩石速率最高。
最终,全尺寸钻进实验和油田数据表明,应用精确地岩石和钻头相互作用模型能帮助钻头设计者针对特定区块找到最合适的钻头。
标准的实验室全尺寸钻进过程已经发展起来。
实验表明通过对切削齿的特征,切削齿的部齿,切边齿的特征和保径类型的调整,钻头的钻进能力,稳定性,导向能力和磨损可以改善和控制。
介绍从19世纪七十年代开始,PDC钻头性能不断改进,从改善PDC的工艺水平,切削齿结构,动力学稳定性,水力因素和导向性到平滑快速钻进。
PDC钻头钻井过程中的岩性描述归位

PDC钻头钻井过程中的岩性描述归位PDC钻头在钻井过程中,岩性描述是非常重要的一个环节。
岩性描述是根据打出的岩心样品所包含的物质成分和结构特征来描述钻孔周围岩石的性质和特征的过程。
这个过程可以通过观察岩心及热化学方法等手段来完成。
岩性描述的目的是为了确定岩石的物理性质、力学性质和工程特性,以便科学合理地选择钻井工艺和相应的钻井工具,从而提高钻井效率和成功率。
PDC钻头在钻井过程中的岩性描述可以归为以下几个方面。
一、钻头钻入地层的情况钻头钻入地层后,通过观察钻屑和岩心的结构、组成和颜色等,可以了解钻头执行的是什么类型的岩石。
还可以通过岩心中的矿物形态、晶体结构、风化程度、孔隙度等来推测岩石的性质和特征。
二、刀具的磨损情况在钻井过程中,由于地质条件的复杂性和强度的不同,PDC钻头容易受到严重的磨损,这是影响钻井效率和成功率的重要因素之一。
岩性描述中,需要对刀具的磨损情况进行观察和分析,根据磨损的情况和特征,可以了解岩石的力学性质和强度,进而调整钻井工艺和钻头形式,提高钻井效率和成功率。
三、岩石的节理、裂隙和变形特征岩石的节理是指天然或人为形成的岩石中沿某一或数个固定方向划分出的面状或线状的分界面。
裂隙是指岩石中已有的或形成中的破裂面或空隙。
岩石的变形特征指岩石受到力的作用形成的各种形态的变形。
这些特征对钻头的选择和使用、钻井工艺的制定以及钻井中的排矿排桶等都会产生影响。
四、岩石的含水量和渗透率岩石的含水量和渗透性是衡量岩石工程特性的重要指标。
通过对岩心样品中空隙的分布和孔隙度的测量,可以大致计算出岩石的孔隙度和渗透率。
同时,还可以根据岩心样品中矿物质和结构的分布情况来判断岩石的含水量和渗透率。
PDC钻头钻井过程中的岩性描述归位

PDC钻头钻井过程中的岩性描述归位在PDC钻头进行钻井过程中,岩性描述的归位非常关键。
通过对岩性的描述,可以帮助地质工程师了解地层的性质和变化,从而确定进一步的钻井计划和操作措施。
下面将详细介绍PDC钻头钻井过程中的岩性描述归位的方法和内容。
岩性描述归位需要进行详细的观察和记录。
在钻进岩层时,钻井工程师需要根据岩层的特点和变化,对岩石进行描述。
这些描述包括岩性、颜色、质地、成分、结构等方面的信息。
还需要注意岩层的裂缝、节理、脆性等特征,并记录下来。
这些观察和记录需要尽可能精确和准确,以便后续的分析和判断。
岩性描述归位需要结合岩层的位置和相对位置信息。
地质工程师需要记录下岩层的深度、倾角、方向等信息,并将其与实际地层分布进行比较。
通过对比和分析,可以确定岩层的位置和变化趋势,预测可能存在的地质问题和风险,为钻井作业提供参考依据。
岩性描述归位还需要考虑岩层的物理性质和地质历史。
地质工程师需要了解岩层的压力、渗透率、孔隙度等物理性质,以便评估地层的稳定性和钻井过程中的钻进难度。
还需要关注岩层的地质历史,包括构造演化、岩浆活动、堆积沉积等情况。
这些信息可以帮助地质工程师推测地层的变化和岩石的形成机制,拟定相应的钻井策略。
岩性描述归位需要进行数据分析和综合判断。
地质工程师需要将采集到的岩性数据进行整理和分析,并与其他地质资料进行比对。
通过对不同地质参数和岩性特征的综合判断,可以得出对地层性质的定性和定量的结论,并根据这些结论做出相应的决策。
PDC钻头钻井过程中岩性描述归位是地质工程师进行岩石观察和数据分析的重要环节。
通过详细观察和记录岩性的特征和变化,结合岩层的位置信息和地质历史,进行综合分析和判断,可以帮助地质工程师了解地层的性质和变化,为钻井作业提供科学依据。
pdc钻头工作原理
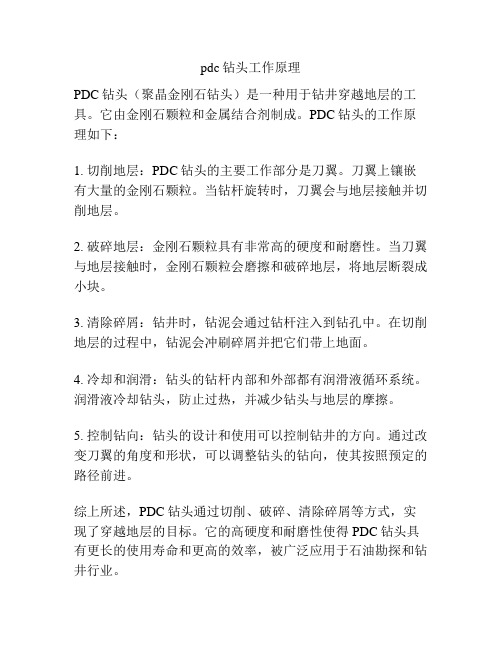
pdc钻头工作原理
PDC钻头(聚晶金刚石钻头)是一种用于钻井穿越地层的工具。
它由金刚石颗粒和金属结合剂制成。
PDC钻头的工作原理如下:
1. 切削地层:PDC钻头的主要工作部分是刀翼。
刀翼上镶嵌有大量的金刚石颗粒。
当钻杆旋转时,刀翼会与地层接触并切削地层。
2. 破碎地层:金刚石颗粒具有非常高的硬度和耐磨性。
当刀翼与地层接触时,金刚石颗粒会磨擦和破碎地层,将地层断裂成小块。
3. 清除碎屑:钻井时,钻泥会通过钻杆注入到钻孔中。
在切削地层的过程中,钻泥会冲刷碎屑并把它们带上地面。
4. 冷却和润滑:钻头的钻杆内部和外部都有润滑液循环系统。
润滑液冷却钻头,防止过热,并减少钻头与地层的摩擦。
5. 控制钻向:钻头的设计和使用可以控制钻井的方向。
通过改变刀翼的角度和形状,可以调整钻头的钻向,使其按照预定的路径前进。
综上所述,PDC钻头通过切削、破碎、清除碎屑等方式,实现了穿越地层的目标。
它的高硬度和耐磨性使得PDC钻头具有更长的使用寿命和更高的效率,被广泛应用于石油勘探和钻井行业。