有机硅涂料(silicone coating)
211181368_耐热线型小分子对有机硅耐温吸波涂层的增韧改性研究
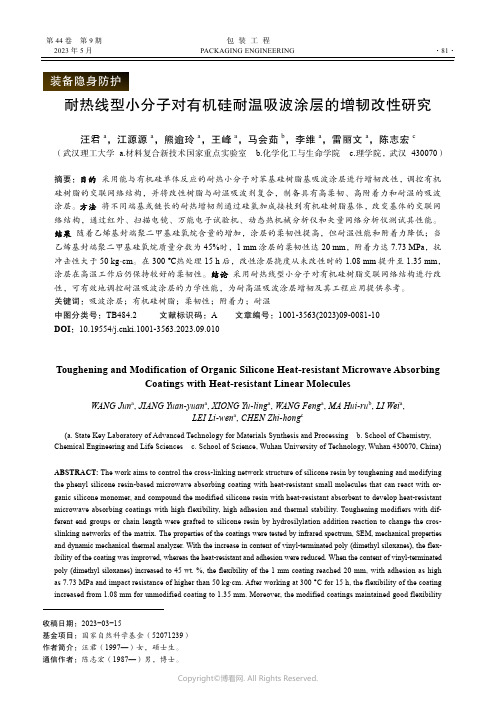
第44卷 第9期 包 装 工 程2023年5月PACKAGING ENGINEERING ·81·收稿日期:2023−03−15基金项目:国家自然科学基金(52071239) 作者简介:汪君(1997—)女,硕士生。
耐热线型小分子对有机硅耐温吸波涂层的增韧改性研究汪君a ,江源源a ,熊逾玲a ,王峰a ,马会茹b ,李维a ,雷丽文a ,陈志宏c(武汉理工大学 a.材料复合新技术国家重点实验室 b.化学化工与生命学院 c.理学院,武汉 430070) 摘要:目的 采用能与有机硅单体反应的耐热小分子对苯基硅树脂基吸波涂层进行增韧改性,调控有机硅树脂的交联网络结构,并将改性树脂与耐温吸波剂复合,制备具有高柔韧、高附着力和耐温的吸波涂层。
方法 将不同端基或链长的耐热增韧剂通过硅氢加成接枝到有机硅树脂基体,改变基体的交联网络结构,通过红外、扫描电镜、万能电子试验机、动态热机械分析仪和矢量网络分析仪测试其性能。
结果 随着乙烯基封端聚二甲基硅氧烷含量的增加,涂层的柔韧性提高,但耐温性能和附着力降低;当乙烯基封端聚二甲基硅氧烷质量分数为45%时,1 mm 涂层的柔韧性达20 mm ,附着力达7.73 MPa ,抗冲击性大于50 kg·cm 。
在300 ℃热处理15 h 后,改性涂层挠度从未改性时的1.08 mm 提升至1.35 mm ,涂层在高温工作后仍保持较好的柔韧性。
结论 采用耐热线型小分子对有机硅树脂交联网络结构进行改性,可有效地调控耐温吸波涂层的力学性能,为耐高温吸波涂层增韧及其工程应用提供参考。
关键词:吸波涂层;有机硅树脂;柔韧性;附着力;耐温中图分类号:TB484.2 文献标识码:A 文章编号:1001-3563(2023)09-0081-10 DOI :10.19554/ki.1001-3563.2023.09.010Toughening and Modification of Organic Silicone Heat-resistant Microwave AbsorbingCoatings with Heat-resistant Linear MoleculesWANG Jun a , JIANG Yuan-yuan a , XIONG Yu-ling a , WANG Feng a , MA Hui-ru b , LI Wei a ,LEI Li-wen a , CHEN Zhi-hong c(a. State Key Laboratory of Advanced Technology for Materials Synthesis and Processing b. School of Chemistry, Chemical Engineering and Life Sciences c. School of Science, Wuhan University of Technology, Wuhan 430070, China) ABSTRACT: The work aims to control the cross-linking network structure of silicone resin by toughening and modifying the phenyl silicone resin-based microwave absorbing coating with heat-resistant small molecules that can react with or-ganic silicone monomer, and compound the modified silicone resin with heat-resistant absorbent to develop heat-resistant microwave absorbing coatings with high flexibility, high adhesion and thermal stability. Toughening modifiers with dif-ferent end groups or chain length were grafted to silicone resin by hydrosilylation addition reaction to change the cros-slinking networks of the matrix. The properties of the coatings were tested by infrared spectrum, SEM, mechanical properties and dynamic mechanical thermal analyzer. With the increase in content of vinyl-terminated poly (dimethyl siloxanes), the flex-ibility of the coating was improved, whereas the heat-resistant and adhesion were reduced. When the content of vinyl-terminated poly (dimethyl siloxanes) increased to 45 wt. %, the flexibility of the 1 mm coating reached 20 mm, with adhesion as high as 7.73 MPa and impact resistance of higher than 50 kg∙cm. After working at 300 °C for 15 h, the flexibility of the coatingincreased from 1.08 mm for unmodified coating to 1.35 mm. Moreover, the modified coatings maintained good flexibility·82·包装工程2023年5月after heat treatment. Modifying the crosslinking networks of silicone resin with heat-resistant small molecules can effec-tively control the mechanical properties of heat-resistant microwave absorbing coatings and provide references for toughening and engineering applications of heat-resistant microwave absorbing coatings.KEY WORDS: microwave absorbing coatings; silicone resin; flexibility; adhesion; heat-resistant随着电子技术的扩展[1],微波探测技术在20世纪后期得到了快速发展[2]。
有机硅:概述二

在有机硅核心分子结构中加入不同分子及化合物能够增强或改变有机硅性质,使其具有令人惊奇的万能用途。
由此产生的材料适应性极强,可以产生 2000 多种不同的形态,如固体、液体、油品、油 脂、半粘软膏、抗泡剂、浸渍剂、脱模剂、硅橡胶等等。
高性能、高保护、多用途,引领生活方式有机硅正改变着我们的现在,描绘着我们的未来源于自然有机硅是一类聚合体的总称,其中包括硅氧烷及硅烷——均为地壳中含量位居第二的天然元素硅的 化合物变体。
以下是部分使用有机硅的重点行业:• 汽车• 航空航天• 建筑• 化妆品• 家用电器• 电子• 食品• 保健• 机械工程• 纸张• 橡胶• 表面涂料• 织物与皮革企业家、消费者及艺术家们都希望通过出色的材料帮助提供创新、经济的解决方案,以满足各行各业的尖端要求。
稳定。
有机硅是非常稳定的化合物,具有出色的抗风雨及老化的特性,并且能够承受极限的温度及气候的变化。
有机硅不会与化学物质发生反应,可以抵抗盐、风、水及辐射等气候的影响,并且具有出色的绝缘性能。
洁净。
有机硅可以与化学物质及材料共用,或是在化学物质及材料上使用,并且通常不会产生有害的副产品或气味。
有机硅可以防水,并且不会促进细菌及真菌的滋生。
使用有机硅制造的产品易于清洁。
在建材方面,有机硅可以防止潮湿及霉菌的损害。
采用有机硅制造的医疗器械易于消毒。
耐用。
有机硅有极强的抗磨损及抗撕裂的性能。
与许多合成材料不同,有机硅在长时间暴露于恶劣环境之后仍可保持其基本的化学及物理性质。
有机硅不但自身非常可靠,还可以延长许多材料的使用寿命。
适应性强、万能用途。
有机硅使用非常方便。
相对而言,其在许多行业中易于生产、易于使用。
有机硅:概述二构建生活的先进化学品有机硅是现代生活的基本构成成分,具有极为宽广的化学及物理特性,从而成为从航空到纺织各个行业用作增强性能的首选材料。
A V O 8 5 1 6有机硅可以用于先进的生产及加工过程,并且常常推动可以简化生产流程的新型技术的产生。
硅胶与硅树脂的区别
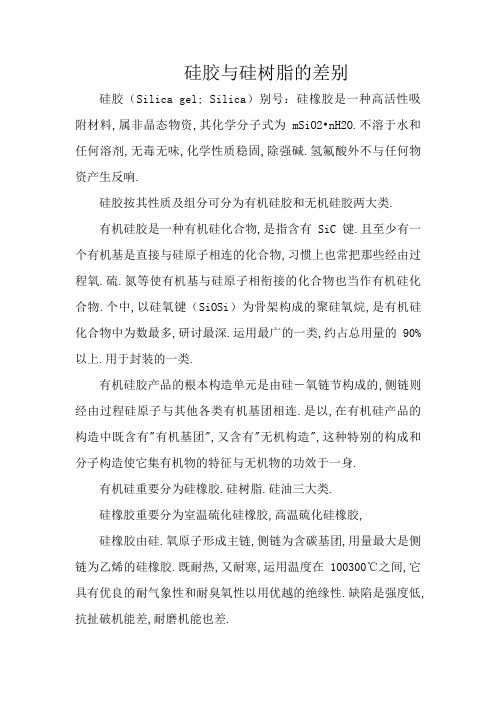
硅胶与硅树脂的差别硅胶(Silica gel; Silica)别号:硅橡胶是一种高活性吸附材料,属非晶态物资,其化学分子式为mSiO2•nH2O.不溶于水和任何溶剂,无毒无味,化学性质稳固,除强碱.氢氟酸外不与任何物资产生反响.硅胶按其性质及组分可分为有机硅胶和无机硅胶两大类.有机硅胶是一种有机硅化合物,是指含有SiC键.且至少有一个有机基是直接与硅原子相连的化合物,习惯上也常把那些经由过程氧.硫.氮等使有机基与硅原子相衔接的化合物也当作有机硅化合物.个中,以硅氧键(SiOSi)为骨架构成的聚硅氧烷,是有机硅化合物中为数最多,研讨最深.运用最广的一类,约占总用量的90%以上.用于封装的一类.有机硅胶产品的根本构造单元是由硅-氧链节构成的,侧链则经由过程硅原子与其他各类有机基团相连.是以,在有机硅产品的构造中既含有"有机基团",又含有"无机构造",这种特别的构成和分子构造使它集有机物的特征与无机物的功效于一身.有机硅重要分为硅橡胶.硅树脂.硅油三大类.硅橡胶重要分为室温硫化硅橡胶,高温硫化硅橡胶,硅橡胶由硅.氧原子形成主链,侧链为含碳基团,用量最大是侧链为乙烯的硅橡胶.既耐热,又耐寒,运用温度在100300℃之间,它具有优良的耐气象性和耐臭氧性以用优越的绝缘性.缺陷是强度低,抗扯破机能差,耐磨机能也差.硅树脂是以硅—氧—硅为主链,硅原子上联接有有机基的交联型的半无机高聚物.具有高度交联网状构造的聚有机硅氧烷,是高度支化的聚合物(与线型硅油比拟较)能固化成固态物.兼具有机树脂及无机材料的双重特征,具有奇特的物理化学机能.硅树脂最终加工成品的机能取决于所含有机基团的数量(即R与Si的比值).一般有适用价值的硅树脂,其分子构成中R与Si 的比值在1.2~1.6之间.一般纪律是,R:Si的值愈小,所得到的硅树脂就愈能在较低温度下固化;R:Si的值愈大,所得到的硅树脂要使它固化就须要在200材250℃的高温下长时光烘烤,所得的漆膜硬度差,但热弹性要比前者好得多.硅树脂还具有卓著的耐潮.防水.防锈.耐寒.耐臭氧和耐候机能,对绝大多半含水的化学试剂如稀矿物酸的耐腐化机能优越,但耐溶剂的机能较差.制备硅树脂的单体是氯硅烷,这些氯硅烷都可经由过程醇解而得到响应的烷氧基硅烷.因为它们没有腐化性,又比响应的氯硅烷具有更大的水解稳固性.易保管.易分别,是普遍运用的单体组分.改变单体中官能基的数量和选择不合的代替基,就可制得不合聚合度.支化度和交联度的高聚物,得到不合机能的产品,以顺应不合的用处.单体中官能团的数量可用单体混杂物的R与Si的比值R/Si 来暗示(R为代替基数目.Si为硅原子数量).以甲基氯硅烷的水解缩合为例:当R/Si>2时,即用(CH3)2SiCl2和(CH3)3SiCl混杂共水解,生成分子量较低的油状聚合物,即硅油.当R/Si=2时,即用纯(CH3)2SiCl2水解缩合,生成高分子量的线型聚合物即后面说的硅橡胶胶粘剂的基料,又称硅生胶.当R/Si<2时,即用(CH3)2SiCl2,CH3SiCl3共水解.或CH3SiCl3,(CH3)2SiCl2和SiCl4共水解缩聚,生成网状构造的聚合物,即硅树脂,恰当改变R/Si的值,可以得到不合性质的含硅聚合物.R/Si小,即三官能或四官能硅氧单元比例高时,固化后,交联度高,硅树脂就硬而脆;而R/Si大,即双官能硅氧烷单元比例高,固化后硅树脂的柔性就好,平日采取的R/Si在1.21.5之间.硅树脂不合于硅油和硅橡胶,固化后的有机硅树脂的玻璃化改变温度(Tg)>200℃,而典范的硅橡胶Tg<60℃.甲基硅树脂的碳含量最低,它有很高的耐热性,硅原子上衔接的甲基基团空间位阻最小,树脂的交联度高.硬度大.热塑性小,作为防水.防潮的胶接剂是很幻想的.但纯甲基硅树脂与颜料等的相容性差,热弹性小,在聚甲基硅氧烷中引入苯基可以改良产品的热弹性与颜料的混溶性,以及对各类物资的胶接性,还可进步其热稳固性.甲基苯基硅树脂的机能,重要取决于两个身分:一是上面说的R/Si,别的还与甲基和苯基的比例(CH3/C6H5)亲密相干.从上述三种硅树脂可以看出:硅原子衔接的有机基团种类对树脂机能影响很大,当为甲基时,可付与硅树脂热稳固性.脱模性.憎水性.耐电弧性;为苯基时,付与树脂氧化稳固性,它在必定规模内可损坏高聚物的结晶性;为乙烯基时,可改良硅树脂的固化特征,并带来偶联性;为四氯苯基时,可改良聚合物的润滑性;当为苯基乙基时,可进步硅树脂与有机物的混溶性;为氨丙基时,可改良聚合物的水溶性,同时带来偶联性;为戊基时,可进步硅树脂的憎水性.是以,可在硅树脂制备进程中引入不合的有机基团. 为改良硅树脂的粘接性,可将硅树脂与聚酯.环氧.酚醛等共聚,有机硅聚酯共聚物可经由过程含羟基的聚酯与含烷氧基的硅烷(或硅氧烷),或与含硅羟基的硅烷(或硅氧烷)进行缩合反响而制得.有机硅环氧共聚物的合成有多种门路,但是工业上采取较多的是以商品环氧树脂为原料,依据不合的运用请求,选择恰当的品种与含烷氧基或羟基的低分子量有机硅树脂进行共缩合反响而制得共聚体.有机硅酚醛共聚物也可用可溶性的有机硅树脂与酚醛树脂进行共缩聚反响来制备,还可用有机乙酰基硅烷与低分子量的酚醛树脂共缩聚而制得.差别:硅橡胶是线性构造的分子补强后硫化交联成立体构造,含有微量端羟基时,抗老化机能不敷好,白炭黑补强的透光性差一些,硅树脂补强的透光性好些;力学机能一般比硅树脂好;弹性大,柔嫩,耐热耐候性好,内应力小,缺陷是,分子链间闲暇大,透气,透氧,透湿性大.粘接强度一般耐温50—200 规模.硅树脂是立体构造分子交联成更大的立体构造,含有微量的端羟基时,抗老化比硅橡胶好的多.硬度大,透光性好,透气透湿,透氧小,,力学机能一般比硅橡胶差.硅树脂具有凸起的耐候性,是任何一种有机树脂所瞠乎其后的,即使在紫外线强烈照耀下,硅树脂也耐泛黄.今朝LED光电市场上所普遍运用的大多半是甲基系有机硅胶,苯基系有机硅胶因为成本较高,只在高请求的范畴中运用.硅胶运用中碰到的各类问题:一.固化后概况起皱.这是因为压缩所引起的,多半情形是因为胶中添加有溶剂型的硅树脂造成,建议换胶.二.消失界面层.这个问题也是因为胶所引起,任何两种不合的材质之间都邑消失界面,解决它的独一方法就是只有采取同类物资想近的道理,许多同伙提出过进步固化温度,或者进行高温下的烧结,这些都是一些忽悠的话,独一能解决的方法,从材料上着手,在不克不及改变别的个材质的时刻,改变硅胶与其的亲合力.三.荧光粉产生沉淀,消除是粉的问题,那消失这种情形的胶只能是室温固化型的,因为在硅胶中为了保持其透光性,折射率等,所以不克不及添加任何的悬浮剂进去,碰到这些问题的同伙门可以测验测验着换成升温固化的产品,可以解决这个问题.四.固化后概况不敷滑腻,这是因为胶碰到S.P等中毒引起,大家好好的清洗下模具等系列对象解决之道无非是改良silicone与被接着体的接着性及匹配性,再合营延伸烘烤时光,以改良今朝接着性问题.。
有机硅产品基础知识

02 章节 PART 有机硅的应用 Application of silicone
硅油产品的应用
硅油的定义和特性
硅油是一种不同聚合度链状结构的聚有机硅氧烷。 硅油一般是无色(或淡黄色),无味、无毒、不易挥发 的液体。具有卓越的耐热性、电绝缘性、耐候性、疏水 性、生理惰性和较小的表面张力,此外还具有低的粘温 系数、较高的抗压缩性,有的品种还具有耐辐射性能。
硅油乳液按照硅氧烷种类分类
非活性硅氧烷类
如:聚二甲基硅 氧烷等
活性硅氧烷类
如:聚甲基氢硅 氧烷乳液,羟基
硅油等
改性硅氧烷类
如:环氧改性硅 油、羟基改性硅 油、聚醚改性硅 油氨基改性硅油
纺织
造纸 皮革
化妆 品
作为纤维油剂、消泡剂、染色牢度增进剂、织物功能整理及风格改 进剂、熔融放置剂及缝纫平滑剂。
可作为防粘纸的防黏剂、纸张的防水剂等。在皮革中可作为润滑剂、 防水剂、抛光剂等。常用的是二甲基硅油乳液和氨基改性有机硅乳 液。
黏接剂:硅树脂型粘结剂有纯硅树脂和改性硅 树脂两种,主要起补强耐热作用。
塑料:主要用在耐热、绝缘、阻燃、抗电弧等 有机硅塑料、半导体组件外壳封包塑料等。
不粘涂料:表面能低,防污好,低毒或无毒硬 度高,耐磨好,光伏应用于纺织、印染、造纸 塑料加工等领域的辊筒、模具、管道、食品机 械内壁的防黏涂层,保险刀的防锈增滑涂层等。
国内品牌 之江 新安 星火 中原 硅宝 回天 白云 天山
在国内建筑领域,密封胶 是以国内品牌为主, 在工业领域,国内品牌开 始进入基础工业。
03 章节 PART 有机硅下游发展
有机硅下游-建筑密封胶
优 势
对目标 客户群
熟悉
竞争
电路保护涂料-FSC-中文技术数据手册说明书

Dip Coating
Ensure that the coating material in the container has been agitated thoroughly and has been allowed to stand for at least 2 hours for all the air bubbles to disperse. Non acrylic conformal coating thinners (DCT) should be used to keep the FSC coating at a suitable viscosity for dipping. DCT is added periodically as the solvent evaporates. The viscosity should be checked using a viscosity meter or "flow cup". The board assemblies should be immersed in the FSC dipping tank in the vertical position, or at an angle as close to the vertical as possible. Connectors should not be immersed in the liquid unless they are very carefully masked. Electrolube Peelable Coating Mask (PCM) is ideal for this application. Leave submerged for approximately 10 seconds until the air bubbles have dispersed. The board or boards should then be withdrawn slowly (1 to 2 Seconds / mm) so that an even film covers the surface. After withdrawing, the boards should be left to drain over the tank or drip tray until the majority of residual coating has left the surface. After the draining operation is complete, the boards should be placed in an air-circulating drying cabinet and left to dry.
有机硅材料
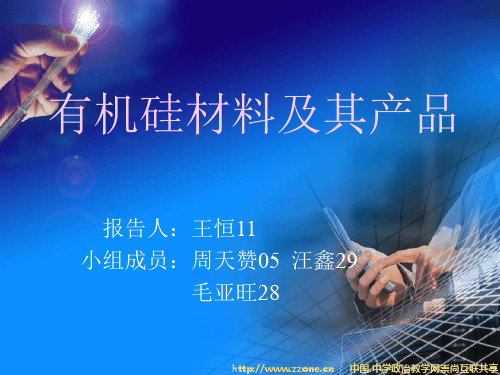
中国.中学政治教学网崇尚互联共享
2 硅酮产品的性能及应用
2.3.5在食品工业的应用 2.3.6在橡胶· 塑胶工业的应用 2.3.7在纤维工业的应用 2.3.8在纸· 纸浆工业的应用 2.3.9在涂料工业的应用
中国.中学政治教学网崇尚互联共享
中国.中学政治教学网崇尚互联共享
1.2.2硅元素和碳元素
H2.1
Li 1.0 Be 1.5 B 2.0 C 2.5 N 3.0 O 3.5 F 4.0
Na 0.9 Mg1.2 Al 1.5 Si 1.8 P 2.1
K 0.8
S 2.5
Cl 3.0
Ca 1.0 Sc 1.3 Ge 1.7 As 2.0 Se 2.4 Br 2.8 Sn 1.7 Sb 1.8 Te 2.1 I 2.4
中国.中学政治教学网崇尚互联共享
2.2.2 硅橡胶(Silicone Rubber)
1.6 耐化学物质性能 溶剂对硅橡胶的作用主要是溶胀和软化,而一旦 溶剂挥发后硅橡胶的大多数原始性能又恢复了, 硅橡胶对乙醇,丙酮等极性溶剂和食用油的耐受 能力相当好,只引起很小的溶胀,机械性能基本 不降低。 硅橡胶对低浓度的酸,碱,盐的耐受能力也较好, 如在10%的硫酸中常温浸渍7天,体积和质量变化 都小于10%,机械性能无变化,但它不耐浓硫酸, 浓碱和四氯化碳,甲苯等非极性溶剂。
有机硅材料及其产品
报告人:王恒11 小组成员:周天赞05 汪鑫29 毛亚旺28
中国.中学政治教学网崇尚互联共享
1.综述
1.1硅的存在 1.2硅酮概述 1.2.1硅元素(Silicon)与硅酮(Silicone) 1.2.2硅元素和碳元素 1.2.3硅酮的物理、化学性质 1.2.4有机硅概述
SKT常见的专业名词解释

•版权所有 ©2010-2020 盛康泰有机硅材料有限公司
有机硅材料具有独特的结构:
盛康泰有机硅材料有限公司
• (1) Si原子上充足的甲基将高能量的聚硅 氧烷主链屏蔽起来; • (2) C-H无极性,使分子间相互作用力十 分微弱; • (3) Si-O键长较长,Si-O-Si键键角大。 • (4) Si-O键是具有50%离子键特征的共价 键(共价键具有方向性,离子键无方向 性)。
•版权所有 ©2010-2020 盛康泰有机硅材料有限公司
•
因为专注,所以专业!
盛康泰有机硅材料有限公司
• •
•
•
•
沈阳化工研究院在有机硅专业迁京后,于20世纪60年代初又成立了有机硅研究室,他 们除了从事多种单体的合成工作外,又首先开发出单组分室温硫化硅橡胶、加成型硅 凝胶和耐烧蚀腻子等。后来此研究室也迁往晨光一厂。 由于搅拌床合成单体的生产效率低、甲基氯硅烷的产量不足制约了有机硅产品的发 展,60年代初,化工部二局杨光启处长拍板决策,在北京化工研究院开设流化床合成 的研究课题。经过探索后,北京化工研究院与上海树脂厂共数十位技术人员和工人师 傅,经6年多努力,在上海建起了由化工部拨款的、我国第一台直径为400mm、生产甲 基氯硅烷的流化床。之后晨光二厂、星火化工厂、吉林电石厂、北京化工二厂等先后 建起直径为400~700mm的流化床,为国家急需的有机硅材料提供出中国人自己生产 的原料。 20世纪80年代初,原国家科委和化工部为使化工新型材料能“寓军于民”、扩大其 应用领域,在北京召开了全国化工新型材料的推广应用会,并组织了化工新型材料全 国7大城市的巡回展览,这使得对新型材料的需求越来越多。“六五”期间,原国家科 委在化工部晨光化工研究院和吉化公司研究院安排了万吨级有机硅的科技攻关项目, 拨给充足的经费,两单位攻克了一批大厂建设所需的关键项目,如晨光院承担的三元 高效催化剂就是其中一例。原国家科委和化工部还组织了有机硅项目的国外考察,了 解与国际的差距。 “七五”期间,化工部决定在星火化工厂建立万吨级有机硅基地。由国家计委拨款建 立、原化工部第六设计院设计的工业性试验装置于1991年12月开始投料试车。化工部 调集了晨光化工研究院一分院的力量,与设计单位会同星火厂职工一起摸索最佳工艺。
电路板保护剂 - Electrolube DCA 改性硅酮绝缘涂料 (SCC3)说明书

DCAModified Silicone Conformal Coating (SCC3)DCA is a flexible, transparent and unique modified silicone conformal coating specifically designed for the protection of electronic circuitry. It has been formulated to meet the highest defence standards in both Europe and the United States. It holds approvals including the British Ministry of Defence (MOD) DEF-STAN 59/47 Issue 4, and Underwriters Laboratories UL746C-QMJU2.•Can be cured at ambient or elevated temperatures; optimum properties achieved by heat curing•Heat-cured coating is resistant to many solvents used within aerospace and automotive industries •Suitable for use at temperature extremes; very wide operating temperature range•Can be reworked using specialist removal product, Electrolube CCRGApprovals RoHS-2 Compliant (2011/65/EU): YesUL746C-QMJU2: Approved File Number: E138403Yes4):(IssueDEF-STAN59/47approvalIPC-CC-830:MeetsNATO Stock Numbers:6850996642823 (DCA05L)(DCA200H)6850992530057PaleStrawLiquid Properties Appearance:ClearDensity @ 20°C (g/ml): 0.97 (Bulk), 0.78 (Aerosol)VOC Content: 63% (Bulk) 73% (Aerosol)<23°C(Bulk),(Aerosol)27°CFlashPoint:Solids content: 37% (Bulk), 27% (Aerosol)Viscosity @ 20°C (mPa s): 180 - 250 (Bulk)Touch Dry: 50 - 55 minutesRecommended Curing Schedule*: 2 Hours @ 20°C followed by:90°Cto120°C@Hours-242*(Maximum Solvent Resistance Achieved @ 120°C; Ambient Curing Schedule: 24 Hours @ 20-25°C)Coverage @ 25 µm: 14.8m² per litre (Bulk), 2.16m² (200ml Aerosol) Cured Film Coating Colour:Colourlessto-70°C+200°COperatingRange:TemperatureUL94V-1Flammability:Thermal Cycling (IPC-CC-830): Meets approvalCoefficient of Expansion: 90ppmkV/mm90DielectricStrength:Dielectric Constant: 3.95 @ 1 MHzInsulation Resistance: 1 x 1015 Ohm (DEF-STAN 59/47)Dissipation Factor (@1 MHz, 25°C): 0.037Moisture Resistance (IPC-CC-830): Meets approvalLifeCode Shelf PackagingDescriptionOrderDCA Conformal Coating 200ml Aerosol DCA200ML 36 MonthsMonths1DCA01L 48BulkLitreMonthsDCA05L 485BulkLitreLitreMonthsDCT01L 361ThinnersConformalCoatingDCT05L 36MonthsBulkLitre5CCRG01L 36BulkMonthsLitreConformal Coating Removal Gel 1Directions for UseDCA can be sprayed, dipped or brushed. The thickness of the coating depends on the method of application (typically 25-75 microns). Temperatures of less than 16°C or relative humidity in excess of 75% are unsuitable for the application of DCA. As is the case for all solvent based conformal coatings, adequate extraction should be used (refer to MSDS for further information).Substrates should be thoroughly cleaned before coating. This is required to ensure that satisfactory adhesion to the substrate is achieved. Also, all flux residues must be removed as they may become corrosive if left on the PCB. Electrolube manufacture a range of cleaning products using both hydrocarbon solvent and aqueous technology. Electrolube cleaning products produce results within Military specification.Spraying – BulkDCA needs to be diluted with the appropriate thinners (DCT) before spraying. The optimum viscosity to give coating quality and thickness depends on the spray equipment and conditions, but normally a dilution ratio of 2:1 (DCA:DCT) is required. Suitable spray viscosity is typically 50-80mPa s. If bulk coating material has been agitated, allow to stand until air bubbles have dispersed. DCA is suitable both for use in manual spray guns and selective coating equipment.The selected nozzle should enable a suitable even spray to be applied in addition to suiting the prevailing viscosity. The normal spray gun pressure required is 274 to 413 kPa (40 - 60 lbs/sq.inch). After spraying, the boards should be placed in an air-circulating drying cabinet following the curing schedule highlighted on page 4/5.Spraying - AerosolWhen applying DCA in aerosol form care must be taken to ensure the can is not shaken before use. Shaking the can will introduce excessive air bubbles and will give a poor coating finish.The can should be held at 45°, and 200mm from the substrate to be coated. The valve should then be depressed when the can is pointing slightly off target and moved at about 100mm/s across the target. To ensure the best coating results are achieved try to use a smooth sweeping motion with small overlap for successive rows.50100150200250161718192021222324252627282930Viscosity(mPas)Temperature (⁰C)Viscosity Change with Temperature -DCA501001502002501:020:110:15:12:11:11:1.51:21:2.51:3Viscosity(mPas)Mix Ratio -DCA:DCTViscosity Chart -DCA:DCTTo ensure penetration of the coating beneath the components and in confined spaces, spray the assembly from all directions to give an even coating. After spraying, the boards should be placed in an air-circulating drying cabinet following the curing schedule highlighted on page 4/5.Dip CoatingEnsure that the coating material in the container has been agitated thoroughly and has been allowed to stand for at least 2 hours for all the air bubbles to disperse.Conformal Coating Thinners (DCT) should be used to keep the DCA coating at a suitable viscosity for dipping (180 – 250mPa s @ 20°C). DCT is added periodically as the solvent evaporates. The viscosity should be checked using a viscosity meter or "flow cup". The board assemblies should be immersed in the DCA dipping tank in the vertical position, or at an angle as close to the vertical as possible. Connectors should not be immersed in the liquid unless they are very carefully masked. Electrolube Peelable Coating Masks (PCM/PCS) are ideal for this application.Leave submerged for approximately 10 seconds until the air bubbles have dispersed. The board or boards should then be withdrawn slowly (1 to 2s/mm) so that an even film covers the surface. After withdrawing, the boards should be left to drain over the tank or drip tray until the majority of residual coating has left the surface. After the draining operation is complete, the boards should be placed in an air-circulating drying cabinet following the curing schedule (shown below).BrushingEnsure that the coating material has been agitated thoroughly and has been allowed to settle for at least 2 hours. The coating should be kept at ambient temperature.When the brushing operation is complete, the boards should be placed in an air-circulating drying cabinet following the curing schedule (shown below).Drying Times and Curing ConditionsThe properties gained from DCA are dependent on the curing schedule employed. It is essential that the coating be allowed a minimum of two hours drying time at ambient temperature prior to any heat curing. This is necessary to allow the solvent system to evaporate.Ambient Ambient curing is via solvent evaporation only. Eliminating the heat curing step will reduce solvent resistance. Other properties, such as resistance to humid and corrosive environments,may also reduce but still meet the requirements of many industry standards. Coated boardsshould be left at room temperature for the solvent to evaporate; extraction is required in thecuring area.Commercial Most commercial users will gain satisfactory performance from this coating by curing for two hours at 90°C after the two-hour ambient cure. This will give limited resistance to solvents. Military If the assemblies are to be used under conditions of high temperature or be exposed to extremes of thermal cycling, the coating should be cured for 12 hours at ambient followed by 24hours at 90°C. For maximum solvent resistance cure at 2 hours at ambient following by 24hours @ 120°C. This curing schedule will give resistance to the more aggressive solvents.It is recommended that the coating be thoroughly cured on circuits, which have design areas of very high impedance that require adjustment after application.InspectionDCA contains a UV trace, which allows inspection of the PCB after coating to ensure complete and even coverage; the stronger the reflected UV light, the thicker the coating layer is. UV light in the region of 375nm should be used for inspection.Revision 2: Jan 2014。
- 1、下载文档前请自行甄别文档内容的完整性,平台不提供额外的编辑、内容补充、找答案等附加服务。
- 2、"仅部分预览"的文档,不可在线预览部分如存在完整性等问题,可反馈申请退款(可完整预览的文档不适用该条件!)。
- 3、如文档侵犯您的权益,请联系客服反馈,我们会尽快为您处理(人工客服工作时间:9:00-18:30)。
有机硅涂料(silicone coating)Research progress of organosilicon coatingsSilicone is the first widely used elements of the organic polymer compound, has excellent performances due to its unique chemical structure, widely used in various fields of national economy, but also plays an important role in the paint industry. Silicone coatings are organosilicon polymer and silicone modified polymer as main film coating material, it has excellent heat resistance, electrical insulation, corona resistance, radiation resistance, moisture resistance and weather resistance, stain resistance, monk water and chemical corrosion resistance and other properties, in recent years in the improvement and application performance of the products have been the rapid development of.1 silicone resin coating made of organic silicon resin film material, mainly heat-resistant, weather resistant silicone anti-corrosion coating, scratch resistant transparent silicone coating, release and moisture-proof coatings and radiation resistant coatings and other varieties.Coating with silicone resin with three methyl chlorosilane (CH3 SiCl3), two methyl two chloro silane [(CH3) 2SiCl2], three (C6H5SiCL3) phenyl chlorosilane, two phenyl chlorosilane two [(C6H5) 2SiCl2] and methyl phenyl chlorosilane CHO two (C6H5) SiCl2 as raw materials for hydrolysis polycondensation prepared. The effect of monomer structure, number and proportion of functional groups on properties of coatings is very important. The types of organic groups connected on silicon atoms also affect the properties of resins. Differentorganic groups can make organosilicon resins exhibit different properties. For example, when the organic group is methyl silicone resin, with thermal stability, releasability, hydrophobicity and arc resistance; for phenyl, given the oxidation stability of silicone resin, crystalline polymer can be destroyed in a certain range;As the vinyl group, the curing property of organosilicon resin can be improved, and coupling property is brought into being; when phenyl ethyl is used, the compatibility of organosilicon resin and organic substance can be improved. The base can be introduced in the siloxane backbone, increase its compatibility with alkyd resin and polyester resin; introducing phenylene and two phenyl ether subunit, biphenyl subunit of aromatic subunit and silicon carbon boron polymers, radiation resistance, the temperature can reach 300 to 500 DEG C; the backbone structure for the Si-N bond is silicone polymer, its thermal stability at 400 deg. In practical application, different organosilicon monomers can be selected according to the requirements, and different organic groups are induced in the organosilicon resin.Chenguang Research Institute of chemical industry with a viscosity of 20 ~ s, 40mPa - hydroxy silicone oil (CH3) and 2SiCl2 methyl triethoxysilane as raw material, control of nR / NSI is 1.3 ~ 1.4, the quality of 2SiCl2 (CH3) and hydroxyl silicone oil ratio was 7O:3O, and the drop of water way at the temperature of 50 1H hydrolysis. Get the methyl silicone resin has good hardness and elasticity, can be used for flame retardant coatings were prepared by metal film resistors. Chinese Academy of sciences so CH3SiCl3 as the main raw material,acetone and xylene as the solvent, soluble trapezoid with narrow molar mass distribution of poly methyl silicone resin was synthesized by the high temperature coating resin with a certain amount of aluminum powder, RTV silicone rubber prepared by 250 DEG C, old 1000 h, its flexibility, oil resistance and resistance have good corrosion resistance. HeFei University of Technology siloxane silicate four functional groups with three functional groups, through strict control of total hydrolysis reaction, the base material is prepared with silicate and silicone polymer properties, the binder and filler and other auxiliary materials according to a certain proportion of organic silicon heat-resisting coating made of.2 modified silicone resin coating while the silicone resin has many excellent properties, but also has some problems: the general need for high temperature (150 ~ 200 DEG C) curing, curing time, the construction of large area is not convenient; adhesion to the substrate, organic solvent resistance, high temperature mechanical strength of the film is not good, the price more expensive etc.. In order to overcome these shortcomings, organic silicone resin was used to modify the organic resin. Modified silicone resin usually has the advantages of two resins, which can make up for some deficiencies in the performance of the two resins, thereby improving performance and expanding application fields. There are two kinds of modification methods, physical mixing and chemical modification. The effect of chemical modification is better than that of physical blending. Chemical modification is mainly on the end or side chain of polysiloxane chain, and then react with other polymers to produce block, graft or interpenetrating polymer networks, thus obtaining newproperties. In the coatings industry, silicone modified organic resins are mainly alkyd resins. Acrylic resin, epoxy resin, etc..2.1 silicone modified alkyd resin coatingSilicone modified alkyd resin coatings is not only an alkyd resin paint film curing at room temperature and physical and mechanical properties, and has the advantages of good heat resistant silicone resin, UV aging resistance and good water resistance characteristics, coating is an excellent comprehensive performance. The first modification was to add the silicone resin directly to the alkyd reaction kettle that reached the end point,The weatherability of alkyd resin is improved greatly. Another modification is to prepare reactive organosilicon oligomers to react with free hydroxyl groups on alkyd resins, and also to use organosilicon oligomers as polyols and alkyd resins for polycondensation. The alkyd resin modified by chemical reaction has better weatherability. Hunan University prepared by alcoholysis hydroxyl alkyd prepolymer and end to hydrolysis or different functional silicone prepolymer prepared by polycondensation reaction synthesis (A B) silicone alkyd type n block copolymer, and the copolymer as base material made of varnish; comprehensive performance of the varnish excellent, not only has the alkyd resin varnish film flexibility, room temperature curing, impact strength and advantages of good adhesion, but also greatly improve the heat resistance, ageing resistance and anti corrosion properties of water medium.2.2 silicone modified acrylic resin coatingSilicone modified acrylic resin coating has excellent weatherability. It has the advantages of light retention, color retention, easy powdering and good gloss. It is widely used for pre coating of metal sheets, painting of machine equipment and weatherproof decoration and decoration of interior and exterior walls of buildings. Silicone modified acrylic resin has two types, solvent and emulsion, of which silicone acrylic latex coating has excellent weatherability, stain resistance, chemical resistance, is an environmentally friendly green paint. Hubei University uses a water-soluble radical initiator, with hydrogen containing silicone oil and butyl acrylate as raw material, the excellent performance of silicone / acrylic emulsion was synthesized by emulsion polymerization method; the emulsion has good acid and alkali. High and low temperature resistance and electrolyte stability, the coatings prepared with it have good weatherability and stain resistance. Ji'nan Chemical Research of acrylate monomer and D4 and vinyl seven methyl siloxane ring four as raw material, by adding a certain amount of grafting agent, using a batch of polyacrylate stable synthesis of polysiloxane emulsion. Sichuan Province Building Materials Industry Research Institute by pre emulsification process, the activity of silicone and acrylate monomer by emulsion copolymerization by organosilicon modified acrylic emulsion coating prepared with the emulsion of stain resistance, excellent comprehensive performance.Fudan University with vinyl silicone monomer and acrylate, methyl acrylate and acrylic acid hydroxy ester monomer polymerization by seed emulsion was stable with excellentproperties of silicone modified acrylate emulsion. Acrylic silicone resin was modified by organosilicon monomer in Zhejiang University, and silicone acrylic emulsion coating was prepared. Polysiloxane polyacrylate interpenetrating network coating synthesis of Chongqing University, the coating is colorless and transparent, high hardness, strong adhesion, acid deposition, heat aging and has good permeability, can be used as anti weathering materials of rock friction moment.HH silicone acrylic resin developed by Shanghai Academy of building research is suitable for the preparation of weather resistant coatings with high weatherability for more than 15 years. HeFei University of Technology with TEOS hydrolysis condensation part to polysiloxane with hydroxyl acrylic resin was prepared by organic silicone modified acrylic resin; the resin in acid and alkali resistance, salt resistance, solvent resistance and impact strength has significantly improved compared with that of pure polysiloxane, and high temperature resistance is obviously improved acrylic resin. Jiangsu architectural materials research and Design Institute introduced a certain amount of organosilicon functional group in the synthesis of acrylic resin, and prepared the solvent modified silicone resin coating with high weatherability. The Chinese Academy of Sciences of Lanzhou Institute of Chemical Physics with hydroxyl terminated poly two methyl siloxane, in two under the action of azo isobutyronitrile, and methacrylic acid (ester) monomers by solution copolymerization, silicon rubber modified acrylic resin, the resin has good heat resistance.2.3 silicone modified epoxy resin coatingThe modification of epoxy resin with organosilicon can not only reduce the internal stress of epoxy resin, but also increase the toughness of epoxy resin and improve its heat resistance. The poly (two siloxane) modified novolac epoxy resin has greatly reduced the internal stress and improved the cracking resistance index of the Institute of chemistry of Chinese Academy of sciences. Wuhan Research Institute of materials protection and the compatibility with epoxy resin and reactive silicone oligomer polycondensation of the prepared silicone modified epoxy resin has advantages of both epoxy resin and silicone resin, not only improve the heat resistance, but also has good corrosion resistance. Two point fourModification of styrene acrylate emulsion with organosilicon modified styrene acrylic emulsion coating can obviously improve its weatherability, gloss, elasticity and durability. Shanghai University of Engineering Science by graft copolymerization of synthetic silicone modified styrene acrylic emulsion has the excellent properties of silicone and acrylic resin coating, good elasticity, the elongation was significantly higher than that of styrene acrylic emulsion coating. Silicone modified styrene acrylate emulsion building coating was prepared by adding a certain amount of organic silicone to styrene acrylic emulsion polymerization in Shanghai traffic science and technology university,The coating has good water resistance, scouring resistance and durability.2.5 silicone modified other resin coatingSilicone modified polyurethane coatings are widely used in Aircraft Skins, large tank surfaces, building roofs and cultural relics protection. The Chinese Academy of Sciences of Lanzhou Institute of Chemical Physics with hydroxyl terminated poly two methyl siloxane and alcohol solution of castor oil modified polyurethane prepolymer was modified, the curing rate of the blend is improved after the film adhesion, hardness, heat resistance is also improved. It also uses organosilicon modified urushiol resin as base material to prepare paint with resistance to boiling water and water vapor permeability. It can be used for corrosion protection of equipment for a long time. Shanghai Research Institute of building science by using epoxy resin, acrylic resin, silicone resin copolymer in the main chain introduced special hydrophilic functional groups made of water soluble epoxy silicone acrylic resin, the resin has excellent physical and mechanical properties, and has good resistance to aging. Anti ultraviolet and anti-corrosion properties. The coatings made of this resin are basically non-toxic, easy to construct, good in coating properties and good in decorative effect. In the research of Chenguang Chemical Research Institute, copolymerization of styrene, methyl methacrylate, acrylonitrile and organosilicon was used to develop a kind of impregnating agent for electronic devices.3 silicone rigid wear-resistant coatingStudy of organosilicon hard coating on silica sol as Q chain components, functional silicon or carbon functional silane to alkyl chain as a T component, in the presence of water, alcohol and acid catalyst by hydrolysis and polycondensation are partof TQ type silicon resin pre silicon containing hydroxyl polymer solution. By adjusting the variety of RSi (OR ') 3 and the ratio of silica sol to the additive, the variety and solvent of the additive, we can make a kind of hard and wear-resistant coating with various properties. The viscosity of organosilicon coating is usually 4~25 m, Pa, s, and the solid content is 20% ~ 30%. After coating on the surface of the substrate, the remaining silicon hydroxyl groups are condensed under heating condition to form a network structure of hardened wear-resistant layer.Silicone reinforced wear-resistant coating is superior to UV curing acrylic resin hardening coating in both wear resistance and weather resistance. Transparent plastics processed by organosilicon stiffening coatings have been widely used as glasses, car lampshades, instrument scales, compact discs and special architectural windows.4 ConclusionWith the further research, development and improvement of new materials, the performance of silicone coating will be more excellent to meet the different needs of different industries or fields. With the improvement of people's life and beautify the demands for living rooms and buildings, silicone coating with excellent weatherability and stain resistant performance in the decoration of building has a broad application prospect; and, with the increasing awareness of environmental protection silicone coatings towards non pollution, green environmental protection development direction.Refractory paint TK-000Product ingredients: refractory paint TK-000 series by silicone resin as the main raw material, the product features: high temperature of 800 DEG, acid and alkali resistance, good blackness, high hardness, good weatherability. Application: metal, iron surface coating. For example the fireplace. Through the international quality standard: SGS non-toxic inspection standard. Viscosity: 65 + 5KU/30 C color the following 2 points: black, light adjustable hardness: H-2H dry conditions: 150 DEG C * 30 'solid content: 54% + 2% adhesion: 100% (iron) leveling: good feeling: good complementary series: silicone special solvent construction method: spraying standard packing: canned note: as the climate is different, that day water should be used in different products, more details please contact the company or the dealer.According to the characteristics of low surface energy and low viscosity of organosilicon polymer itself, it is more suitable for practical application and modified in preparation process. The range of application of modified silicone resin is wider and better, which has been proved by the development trend.The above is from the coating process. Chemical industry press. ISBN7-5025-1434-1/TQ.786) part of the third chapter silicone coating: if you can borrow this book, it might be of greater help to you;Preparation of silicone resin, usually more than two or more than two units for hydrolysis, raw materials in the following article is given. When the hydrolysis conditions are different,the composition of the intermediate product and the amount of the ring formation of the hydrolysis product are often greatly different, even though the formula is the same. Effects of various factors on hydrolysis:1. Influence of pH value of hydrolysis medium(1) acid medium; (2) neutral medium; (3) alkaline medium;2. The influence of water content in hydrolysis medium: the amount of water needed for reaction is lower than that of silane reaction, which forms the gradual hydrolysis and polycondensation reaction, limiting the formation of ring. The hydrolysis of excess water is the opposite.3, the influence of the solvent in the hydrolysis medium4 、 the influence of equipment agitation speed in hydrolysis5, the influence of temperature on hydrolysis, the higher temperature when hydrolysis, the molecular movement of components is intense, the chance of collision with each other is increased, which is beneficial to the growth of CO polycondensation, low temperature,Otherwise.Formulation formulation related factors: depending on the resin type, this factor varies:(1) the average degree of substitution of alkyl hydrocarbons(D.S.); (2) the average mass of% (including SiOx, phenyl, methyl); after a lot of chemists' careful research experience, there is a data range;Modified resin: it has the advantage of two kinds of resin, and makes up for the disadvantage of silicone resin, and makes it more suitable for coating application. General organic silicone modified organic resin: alkyd resin, polyester resin, epoxy resin, acrylic resin, polyurethane resin, phenolic resin and so on;Two methods of modification: cold spelling (physical method); chemical method;。