尺寸链计算 i excel 求解极限公差与统计公差
尺寸链计算及公差分析68页PPT
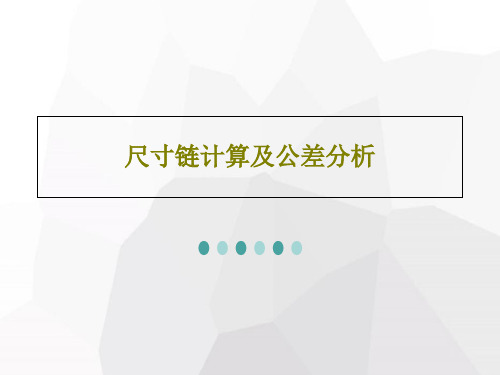
6、法律的基础有两个,而且只有两个……公平和实用。——伯克 7、有两种和平的暴力,那就是法律和礼节。——歌德
8、法律就是秩序,有好的法律才有好的秩序。——亚里士多德 9、上帝把法律和公平凑合在一起,可是人类却把它拆开。——查·科尔顿 10、一切法律都是无用的,因为好人用不着它们,而坏人又不会因为它们而变得规矩起来。——德谟耶克斯
55、 为 中 华 之 崛起而 读书。 ——周 恩来
谢谢!
51、 天 下 之 事 常成 于困约 ,而败 于奢靡 。——陆 游 52、 生 命 不 等 于是呼 吸,生 命是活 动。——卢 梭
53、 伟 大 的 事 业,需 要决心 ,能力 ,组织 和责任 感。 ——易 卜 生 54、 唯 书 籍 不 朽。——乔 特
公差尺寸链计算公式

公差尺寸链计算公式
1.基准尺寸的确定:
在公差尺寸链的计算中,首先需要确定一个基准尺寸,作为其他尺寸的参考。
一般选择与工艺要求相符的零件尺寸作为基准尺寸。
2.公差分配:
公差分配是指根据装配要求和功能要求,按照一定比例将总公差分配到各个零件尺寸上。
公差分配的原则包括:
-公差应按照装配要求和功能要求进行分布,确保装配精度和功能要求的满足。
-尺寸公差应该从初始尺寸向装配间隙依次增大,以确保装配的顺利进行。
-公差应尽量少,以减少成本和缩小尺寸偏差。
在进行公差分配时,一般需要考虑以下几个因素:
-零件功能要求:根据零件在装配中的具体功能、运动和受力情况,确定其尺寸公差的分配。
-装配方式:根据零件的装配方式,如插入、相对位置等,确定其尺寸公差的分配。
-零件尺寸和材料:根据零件的尺寸和材料特性,确定其尺寸公差的分配。
3.最小公差计算:
最小公差是保证装配精度的关键要素,通常根据装配要求和功能要求
向下确定。
最小公差的计算需要考虑以下几个因素:
-装配要求:根据装配的要求和设定的公差限制,确定所需的最小公差。
-装配间隙:根据装配时需要的间隙和松动度,确定所需的最小公差。
-功能要求:根据零件在装配中的具体功能和使用要求,确定最小公差。
以上是公差尺寸链计算的基本原理和步骤。
实际应用中,还需要考虑
诸如公差合理化、商标公差等的因素,以确保设计的合理性和可靠性。
公
差尺寸链计算是一项复杂的工作,需要根据具体情况进行合理的分析和计算,以满足产品的装配和使用要求。
装配尺寸链的计算

d=
,
250.0025
D=
0. .0125
25 ②按尺寸大小分成0四.00组7,列5 表,工件按组涂上不同颜色便于
分组装配.
0.0175
图示为活塞销与活塞销孔的装配,直径为28mm,过盈量为 0.0025~0.0075mm
应用分组装配法必须注意以下几点
1>配合件公差应当相等;公差要向同方向增大;增大的 倍数要等于分组数.
但增加了修配工作,生产效率低,对装配工 人技术要求高。
应用
用于产品结构比较复杂、尺寸链环数较多、 产品精度要求高的单件小批生产的场合。
修配方法
〔1单件修配法 〔2合并加工修配法 〔3 自身加工修配法
应用单件修配法必须注意以下几点
修配环 的选择
〔1易于修配、便于装卸
〔2尽量不选公共环为修配 环
单件修配法解算步骤
固定调整法
选择一个组成环作调整环, 作为调整环的零件是按一
定尺寸间隔制成的一组零 件,装配时根据封闭环超差 的大小,从中选出某一尺寸 等级适当的零件来进行补 偿,从而保证规定的装配精 度.通常使用的调整环有垫 圈、垫片、轴套等.
• 需要计算调整环的各档尺寸及其偏差
要求A0=0.05~0.2mm ,已 知各组成环的基本尺寸为 A1=115mm,
0.52= 0.42+ 0.22+ 0.082+ T42+ 0.082 T4=0.192
中间偏差Δ0=<Δ1+Δ2>-<Δ3+Δ4+Δ5> Δi=<ESi+EIi>/2
Δ4=-0.07
③ 核算封闭环的极限偏差
Δ0=<Δ1+Δ2>-<Δ3+Δ4+Δ5>= <0.2+0.1>-<-0.04-0.070.04>=0.45
尺寸链原理与计算
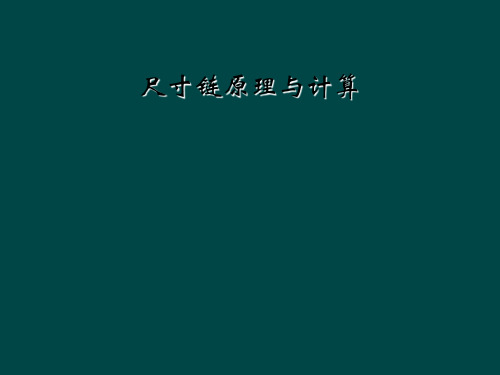
2 i
i 1
-3δ +3δ
反映了封闭环误差与组成环误差间的基本关系。
1. 各环尺寸与公差的计算
(1)各环平均尺寸之间的关系:封闭环的平均尺寸等于增环
的平均尺寸之和与减环平均尺寸之和的差。
m
n1
A0 Ai Ai
i1
im1
(2) 各环公差之间的关系:封闭环的公差等于组成环公差平 方和的平方根。
T0
的。
2.2 封闭环的重要性:
(1) 体现在尺寸链计算中,若封闭环判断错误,则全部分析 计算之结论,也必然是错误的。
(2) 封闭尺寸通常是精度较高,而且往往是产品技术规范或 零件工艺要求决定的尺寸。
在装配尺寸链中,封闭环往往代表装配中精度要求的尺寸; 而在零件中往往是精度要求最低的尺寸,通常在零件图中不予 标注。
(2) 概率解法:又叫统计法。应用概率论原理来进行尺寸键计 算的一种方法。如算术平均、均方根偏差等。
求解尺寸链的情形:
1、已知组成环,求封闭环
2、已知封闭环,求组成环
尺寸链的正计算 尺寸链的反计算
3、已知封闭环及部分组成环,求其余组成环 尺寸链的中
间计算
1.已知组成环,求封闭环 根据各组成环基本尺寸及公差(或偏差),来计算封闭环
A3
A1 A∑
A2
L2
L3 L∑ L4
L1
A1 A∑
A3
L2
L3 L∑ L4
L1
A2
3. 组成环 一个尺寸链中,除封闭环以外的其他各环,都是“组成
环”。按其对封闭环的影响可分为增环和减环。
表示为:Ai 、Li i=1,2,3…… 增环:在尺寸链中,当其余组成环不变的情况下,将某一组 成环增大,封闭环也随之增大,该组成环即称为“增环”。
极值法计算尺寸链的方法

极值法计算尺寸链的方法极值法作为一种常见的计算尺寸链的方法,在机械设计和制造领域具有广泛的应用。
本文将详细介绍极值法的原理和具体计算步骤,帮助读者更好地理解和掌握这一方法。
一、极值法概述极值法是一种基于数学统计原理的计算尺寸链的方法。
它通过分析各尺寸之间的相互关系,确定尺寸链中各尺寸的变动范围,从而计算出合理的尺寸公差。
极值法适用于具有一定数量尺寸的封闭尺寸链,能够确保零件在装配过程中的互换性和功能性。
二、极值法的计算步骤1.确定尺寸链首先,根据零件的装配关系和功能要求,确定尺寸链中各尺寸的名称、数量和顺序。
尺寸链中的尺寸应包括基本尺寸、公差、形位公差等。
2.建立尺寸链模型根据尺寸链中各尺寸的相互关系,建立尺寸链模型。
通常,尺寸链模型可以表示为一个封闭的多边形,各尺寸分别对应多边形的各边。
3.确定尺寸变动范围分析尺寸链中各尺寸的公差,确定各尺寸的变动范围。
变动范围通常包括上极限尺寸、下极限尺寸和基本尺寸。
4.计算封闭尺寸链的公差根据极值法的原理,封闭尺寸链的公差等于尺寸链中各尺寸公差之和。
计算公式如下:封闭尺寸链公差= Σ(各尺寸公差)5.判断尺寸链的合理性比较封闭尺寸链的公差与设计要求的公差,判断尺寸链是否满足设计要求。
若不满足,需对尺寸链进行调整,直至满足设计要求。
6.确定尺寸链中各尺寸的公差根据封闭尺寸链的公差和各尺寸的变动范围,分配各尺寸的公差。
分配公差时,应遵循以下原则:- 尺寸链中各尺寸的公差应相等或相近;- 尺寸链中各尺寸的公差应满足功能要求和加工工艺要求;- 尺寸链中各尺寸的公差应便于测量和检验。
三、总结极值法计算尺寸链的方法具有以下优点:1.简便易行,适用于各种类型的尺寸链;2.能够确保零件在装配过程中的互换性和功能性;3.有助于提高零件的加工质量和降低生产成本。
通过以上介绍,相信读者已经对极值法计算尺寸链的方法有了更深入的了解。
尺寸链计算及公差分析介绍PPT课件

同轴度用A3=0±0.01表示
可编辑课件
6
跳度作为环
a) 尺寸公差可以包含跳度,不需要单独作为一个环。 b) 尺寸公差不能包含跳可度编辑,课跳件 度需要单独作为一个环。 7
尺寸链计算目的
• 保证产品的质量 • 提高生产率,降低成本 • 优化设计
• 以最低的成本,生产出满足质量要求的产品。
可编辑课件
39
例9——计算过程
尺寸链图
已知条件
计算方程组
可编辑课件
40
例9——计算结果
计算结果
计算报告
可编辑课件
41
例10——保险推阻铁解脱击锤瞬间
可编辑课件
42
例10——计算过程
尺寸链图
已知条件
计算方程组
可编辑课件
43
例10——计算结果
计算结果
计算报告
可编辑课件
44
联系人:陈亮 电话:18684815583
A5、A6尺寸 • 求A0尺寸
正计算
可编辑课件
27
例5——箱体装配(计算结果)
结论:该箱体设计 存在一定的问题, 某些情况下会产 生干涉
计算结果
可编辑课件
28
例6——模具设计(结构)
问题: • 根据现有的设计能
否保证66±0.15这 个尺寸?
来自山西平阳机械厂
可编辑课件
29
例6——模具设计(尺寸链)
23
例4——油轮部分拼板焊(尺寸链图)
已知条件:
可编辑课件
24
例4——油轮部分拼板焊(计算结果)
计算结果
可编辑课件
25
例5——箱体装配(结构图)
问题: 检查箱体装配后会不会产 生干涉?(能否正常装 配?)
excel标准公差函数
excel标准公差函数标准公差是衡量产品质量的重要指标之一,它用于描述产品尺寸、形状、位置等方面的偏差范围。
在Excel中,我们可以使用一些函数来计算标准公差,这些函数包括STDEV.P、AVERAGE、MAX、MIN等。
下面我将详细介绍如何使用这些函数来计算产品的标准公差。
首先,我们需要将产品的尺寸数据输入到Excel的工作表中。
假设我们有一个产品的长度数据,我们可以在工作表的一列中输入这些数据。
假设这些数据位于A列,从单元格A2开始。
1.计算平均值要计算产品长度的平均值,我们可以使用AVERAGE函数。
在单元格B2中输入以下公式:=AVERAGE(A2:A1000)其中A2:A1000是包含长度数据的范围。
这个公式将计算A2到A1000单元格中的所有值的平均值。
2.计算标准偏差标准偏差是衡量产品尺寸变化的一种方法。
要计算标准偏差,我们可以使用STDEV.P函数。
在单元格C2中输入以下公式:=STDEV.P(A2:A1000)其中A2:A1000是包含长度数据的范围。
这个公式将计算A2到A1000单元格中的所有值的标准偏差。
3.计算最大偏差最大偏差是产品尺寸在不同批次之间的最大差距。
要计算最大偏差,我们可以使用MAX函数。
在单元格D2中输入以下公式:=MAX(A2:A1000)-MIN(A2:A1000)这个公式将计算A2到A1000单元格中的所有值的最大值减去最小值,得到最大偏差。
4.设置公差范围在标准公差中,通常会设置一个上限值和一个下限值来规定允许的偏差范围。
假设我们的公差范围为±0.1mm。
我们可以使用条件格式来对超出公差范围的数据进行标记。
选择A2到A1000单元格范围,然后按下条件格式按钮,在下拉菜单中选择"新建规则",选择"使用公式确定要格式化的单元格"。
在公式框中输入以下公式:=AND(A2<$B$2-$C$2,A2>$B$2+$C$2)其中B2是平均值单元格的引用,C2是标准偏差单元格的引用。
尺寸链及尺寸链计算
一、尺寸链及尺寸链计算公式1、尺寸链的定义在工件加工和机器装配过程中,由相互联系的尺寸,按一定顺序排列成的封闭尺寸组,称为尺寸链。
尺寸链示例2、工艺尺寸链的组成环:工艺尺寸链中的每一个尺寸称为尺寸链的环。
工艺尺寸链由一系列的环组成。
环又分为:(1)封闭环(终结环):在加工过程中间接获得的尺寸,称为封闭环。
在图b所示尺寸链中,A0是间接得到的尺寸,它就是图b所示尺寸链的封闭环。
(2)组成环:在加工过程中直接获得的尺寸,称为组成环。
尺寸链中A1与A2都是通过加工直接得到的尺寸,A1、A2都是尺寸链的组成环。
1)增环:在尺寸链中,自身增大或减小,会使封闭环随之增大或减小的组成环,称为增环。
表示增环字母上面用--> 表示。
2)减环:在尺寸链中,自身增大或减小,会使封闭环反而随之减小或增大的组成环,称为减环。
表示减环字母上面用<-- 表示。
3)怎样确定增减环:用箭头方法确定,即凡是箭头方向与封闭环箭头方向相反的组成环为增环,相同的组成环为减环。
在图b所示尺寸链中,A1是增环,A2是减环。
4)传递系数ξi:表示组成环对封闭环影响大小的系数。
即组成环在封闭环上引起的变动量对组成环本身变动量之比。
对直线尺寸链而言,增环的ξi=1,减环的ξi=-1。
3.尺寸链的分类4.尺寸链的计算尺寸链计算有正计算、反计算和中间计算等三种类型。
已知组成环求封闭环的计算方式称作正计算;已知封闭环求各组成环称作反计算;已知封闭环及部分组成环,求其余的一个或几个组成环,称为中间计算。
尺寸链计算有极值法与统计法(或概率法)两种。
用极值法解尺寸链是从尺寸链各环均处于极值条件来求解封闭环尺寸与组成环尺寸之间关系的。
用统计法解尺寸链则是运用概率论理论来求解封闭环尺寸与组成环尺寸之间关系的。
5.极值法解尺寸链的计算公式(4)封闭环的中间偏差(5)封闭环公差(6)组成环中间偏差Δi=(ES i+EI i)/2(7)封闭环极限尺寸(8)封闭环极限偏差6.竖式计算法口诀:封闭环和增环的基本尺寸和上下偏差照抄;减环基本尺寸变号;减环上下偏差对调且变号。
尺寸链公差计算案例
尺寸链公差计算案例
假设我们要计算一条尺寸链的公差,该尺寸链包含4个零件距离,它们是A、B、C和D。
首先,我们需要明确每个零件的尺寸和公差。
假设A的尺寸
为10mm,公差为±0.1mm;B的尺寸为15mm,公差为
±0.2mm;C的尺寸为20mm,公差为±0.3mm;D的尺寸为
25mm,公差为±0.1mm。
接下来,我们需要计算每个零件的尺寸范围。
对于A零件来说,其下限是10 - 0.1 = 9.9mm,上限是10 + 0.1 = 10.1mm。
同样地,B的下限是15 - 0.2 = 14.8mm,上限是15 + 0.2 =
15.2mm;C的下限是20 - 0.3 = 19.7mm,上限是20 + 0.3 = 20.3mm;D的下限是25 - 0.1 = 24.9mm,上限是25 + 0.1 = 25.1mm。
然后,我们可以计算尺寸链整体的下限和上限。
下限是各个零件下限之和,即9.9 + 14.8 + 19.7 + 24.9 = 69.3mm;上限是各
个零件上限之和,即10.1 + 15.2 + 20.3 + 25.1 = 70.7mm。
最后,我们可以得到尺寸链的公差范围。
公差是上限减去下限,即70.7 - 69.3 = 1.4mm。
因此,该尺寸链的公差为±1.4mm。
这只是一个简单的尺寸链公差计算案例,实际情况可能更加复杂,需要考虑更多的零件和更多的尺寸限制。
excel正负公差公式
excel正负公差公式
Excel正负公差公式是用来计算数据的正负偏差的一种公式。
正负公差是在测
量或统计数据时用来描述数据与真实值之间的差异的一种指标。
在Excel中,我们
可以使用以下公式来计算正负公差:
1. 计算正公差:
正公差 = 数据值 - 真实值
2. 计算负公差:
负公差 = 真实值 - 数据值
其中,数据值是指我们所测量或统计的数据,真实值是指我们预期的理论值或
标准值。
通过计算正公差和负公差,我们可以直观地了解数据的偏差情况,对数据的准确性进行评估。
使用Excel的公式可以使计算更加自动化和高效。
您可以在Excel的单元格中
输入数据值和真实值,然后在相邻的单元格中使用上述公式进行计算。
在需要计算正公差时,将数据值与真实值相减;在需要计算负公差时,将真实值与数据值相减。
这样,您就可以快速获得正负公差的计算结果。
Excel提供了丰富的函数和工具,使得数据处理和分析变得更加简单。
通过使
用正负公差公式,您可以更好地了解数据的准确度,识别潜在的问题,以便做出相应的调整和改进。
无论是在工作还是学习中,掌握Excel正负公差公式都可以帮助
提高数据处理和分析的能力。
- 1、下载文档前请自行甄别文档内容的完整性,平台不提供额外的编辑、内容补充、找答案等附加服务。
- 2、"仅部分预览"的文档,不可在线预览部分如存在完整性等问题,可反馈申请退款(可完整预览的文档不适用该条件!)。
- 3、如文档侵犯您的权益,请联系客服反馈,我们会尽快为您处理(人工客服工作时间:9:00-18:30)。
尺寸链计算是工程中常用的一种计算方法,它用于求解零件尺寸之间的极限公差和统计公差。
在工程设计和制造中,尺寸的精度和公差是非常重要的,它直接影响着产品的质量和性能。
正确地进行尺寸链计算对于保证产品质量和满足设计要求非常重要。
在本文中,我们将介绍尺寸链计算的基本原理和方法,以及如何在Excel中进行尺寸链计算。
一、尺寸链计算的基本原理
1. 尺寸链概念
在机械设计中,尺寸链是指由多个零件或特征尺寸组成的一系列尺寸之间的关系。
这些尺寸之间的关系可以通过公差来描述,而公差又可以分为极限公差和统计公差。
尺寸链计算就是通过计算这些尺寸之间的公差,来保证零件装配的合理性和可靠性。
2. 极限公差与统计公差
极限公差是指在设计过程中,为了保证零件之间的装配要求而规定的最大和最小尺寸偏差。
统计公差是指在大批量生产中,为了保证产品尺寸的稳定性而规定的公差范围。
进行尺寸链计算时,需要同时考虑极限公差和统计公差。
二、尺寸链计算的方法
1. 传统计算方法
传统的尺寸链计算方法通常是手工计算,需要通过手动的方式将尺
寸链中的所有尺寸和公差进行组合计算。
这种方法存在计算复杂、容
易出错的缺点,效率低下。
2. Excel求解方法
为了提高尺寸链计算的效率和准确性,可以利用Excel软件进行求解。
通过建立尺寸链模型和设置相关的公式,可以实现尺寸链计算的自动化。
Excel具有强大的计算功能和灵活的数据处理能力,非常适合用于尺寸链计算。
三、在Excel中进行尺寸链计算的步骤
1. 建立尺寸链模型
首先需要将尺寸链中的所有尺寸和公差以表格的形式输入到Excel中,并根据尺寸之间的关系建立尺寸链模型。
可以利用Excel的单元格设
置合适的格式和公式,以便后续的计算和分析。
2. 设置公式进行计算
在建立好尺寸链模型后,可以利用Excel的公式功能进行尺寸链计算。
根据零件装配的要求和公差规定,可以设置相应的公式来求解极限公
差和统计公差。
通过调整输入的参数和数据,可以实时得到计算结果。
3. 分析计算结果
最后需要对计算结果进行分析和评估,看是否满足产品的设计要求。
可以通过图表、统计分析等方式展示计算结果,以便进行合理的决策
和调整。
四、尺寸链计算的应用
1. 产品设计
在产品设计阶段,尺寸链计算可以帮助工程师合理确定零件尺寸和
公差,保证产品的装配和使用性能。
2. 工艺规划
在制造工艺规划中,尺寸链计算可以帮助生产部门合理安排工艺流
程和调整设备工艺参数,提高产品的加工精度和稳定性。
3. 质量控制
在产品质量控制过程中,尺寸链计算可以帮助质量管理人员合理制
定检验方案和质量标准,保证产品质量的稳定性。
结语
尺寸链计算是一项重要的工程计算工作,它直接关系到产品的质量和
性能。
通过本文的介绍,希望读者能够了解尺寸链计算的基本原理和
方法,以及如何利用Excel进行尺寸链计算。
在实际工程应用中,合
理地进行尺寸链计算将对产品的设计、制造和质量控制起到重要作用。
三、在Excel中进行尺寸链计算的步骤(续)
4. 精细化调整
一旦得到了尺寸链计算的结果,接下来就需要进行精细化调整。
这
涉及到对零件尺寸和公差的优化,以便在满足装配要求的前提下尽可
能减少成本和提高生产效率。
在Excel中,可以通过设定不同的参数
和条件来进行多次计算和比较,找出最优解。
5. 数据管理与分析
Excel不仅可以完成尺寸链计算,还可以对计算结果进行有效的管理和分析。
通过将计算结果导出到表格、图表或图形中,可以更直观地
展示零件尺寸和公差之间的关系,帮助工程师和决策者做出正确的决定。
Excel还可以进行数据的筛选、分类和汇总,为后续的设计优化和生产控制提供依据。
四、尺寸链计算的应用
1. 新产品开发
在新产品开发过程中,尺寸链计算可以为工程师提供重要参考信息。
通过预先进行尺寸链计算,可以提前预判各零部件装配的可能性,避
免因尺寸偏差而导致的设计错误和制造问题。
尺寸链计算还可以为新
产品的可靠性、易用性和升级性提供技术支持。
2. 工艺改进
在工艺改进中,尺寸链计算可以帮助工程师优化零部件的设计和生产方法,提高制造效率和降低成本。
通过调整零部件尺寸和公差,可以最大程度地减小装配过程中的间隙和摩擦,提高产品的装配精度和性能。
3. 质量管理
尺寸链计算在质量管理中扮演着关键角色。
它可以帮助企业准确判断产品的合格率、产品的稳定性和产品的一致性。
通过不断进行尺寸链计算和分析,可以帮助企业制定更精准的质量控制标准和流程,提高产品的一致性和稳定性,降低不合格品率。
4. 国际标准遵从
因为尺寸链计算是国际通用的一种工程计算方法,符合国际标准,因此在涉及跨国贸易或国际合作领域中具有特别的重要性。
通过进行尺寸链计算,可以保证产品与国际标准的一致性,提高产品的国际竞争力,为产品的国际市场竞争提供技术保障。
五、尺寸链计算的未来发展趋势
1. 自动化与智能化
随着工业4.0的发展和人工智能技术的应用,尺寸链计算将向着自动化和智能化方向发展。
未来,可以通过开发智能软件或利用人工智能算法,实现尺寸链计算的自动化和智能化,最大程度地减少人为错误和提高计算效率。
2. 多学科融合
尺寸链计算需要融合机械、材料、工艺、统计学等多学科知识,因此未来的发展趋势将是多学科融合。
通过与机械设计、材料工程、统计学等学科进行交叉融合,可以不断完善尺寸链计算的理论和方法,更好地适应不同领域的工程实践需求。
3. 数据化管理
未来,尺寸链计算将朝着数据化管理的方向发展。
通过建立和管理尺寸链计算的数据资料库,实现对历史数据的追溯和分析,提高尺寸链计算的智能化和数据化水平,为企业的决策和技术创新提供更多支持。
六、结语
尺寸链计算作为一种重要的工程技术手段,对于保证产品的质量和性能起到了非常重要的作用。
在实际的工程设计、制造和质量控制中,尺寸链计算为工程师提供了一个重要的判断和决策基础。
对尺寸链计算的基本原理、方法和应用进行深入的研究和应用,将对企业的产品
质量和竞争力起到关键作用。
希望通过本文的介绍,读者们能够更加深入地了解和应用尺寸链计算,为企业的发展和产品的提升提供重要支持。